Understanding High Temp Alloy Casting
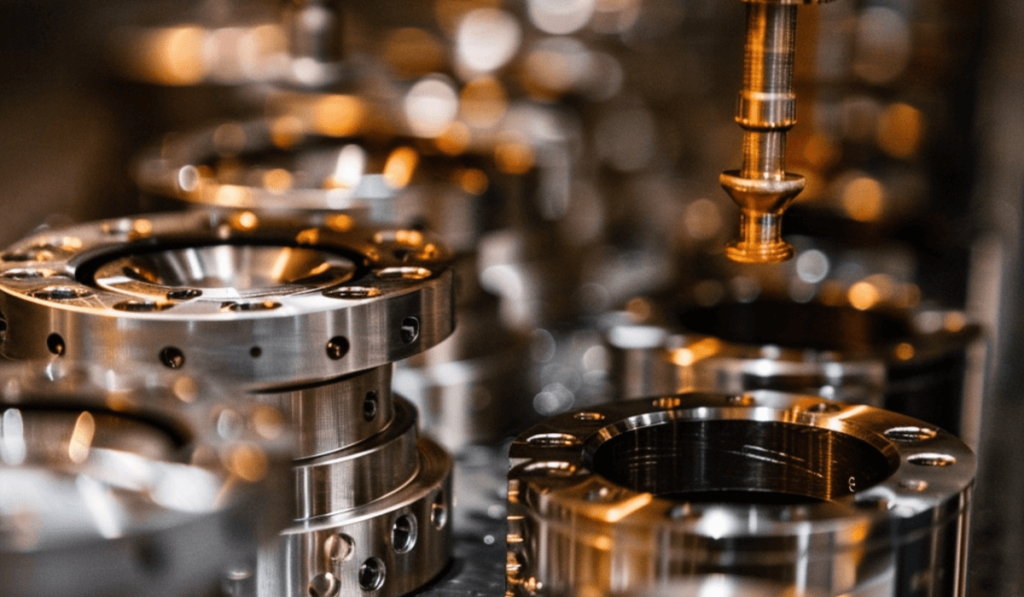
What is High Temp Alloy Casting?
High temperature alloy casting is a cornerstone technology for industries demanding materials capable of withstanding extreme heat, mechanical stress, and corrosive environments. At its core, this process involves shaping high-performance alloys into components specifically engineered to endure such conditions. The materials used are often nickel, cobalt, or iron-based alloys enriched with elements like chromium, molybdenum, and tungsten to enhance their thermal stability and mechanical strength.
This technology plays a pivotal role in advancing innovation in sectors such as aerospace, automotive, and energy production, where equipment is exposed to temperatures exceeding 1,000 degrees Celsius. Why does this matter? Because conventional materials like carbon steel or aluminum would fail under these conditions, leading to catastrophic consequences in critical applications.
Let’s dig deeper into why high temp alloy casting is revolutionary. First, the process allows the design of intricate shapes without compromising material integrity, which is vital for optimizing performance in industrial components. For instance, gas turbine blades—exposed to constant thermal cycling—are manufactured using precision casting techniques to ensure exact specifications are met. But that’s not all. High temp alloys bring unparalleled resistance to oxidation and wear, significantly extending the lifespan of components even in the harshest environments.
Another key feature of this technology is its versatility. It can accommodate a variety of production methods such as investment casting, sand casting, and die casting. Investment casting, in particular, is celebrated for its precision and ability to create complex geometries with minimal waste. Sand casting, while less precise, offers cost-effectiveness for larger components. Each method has its place depending on the specific application, balancing cost, precision, and material performance.
Here’s the kicker: the adoption of high temperature alloy casting doesn’t only promise superior durability but also opens doors for technological breakthroughs in emerging industries like additive manufacturing and green energy. By integrating 3D printing technologies, manufacturers can create high temp alloy components with enhanced designs that were once deemed impossible using traditional methods.
Still, challenges persist. The casting process requires meticulous control of temperature and cooling rates to prevent defects such as porosity or cracking. Manufacturers must also adhere to stringent quality standards, such as those set by ASTM or ISO, to ensure safety and reliability in final products.
Types of Alloys Used in High Temp Casting
High temperature alloy casting thrives on the versatility of its material base, each type catering to specific industrial needs. Let’s break this down:
- Nickel-Based Alloys: The poster child of high temp casting, nickel alloys boast exceptional heat resistance and oxidation protection. Commonly used in aerospace engines and power plant turbines, these alloys endure temperatures above 1,200 degrees Celsius. Why is this significant? Because they maintain their strength even under constant mechanical stress, ensuring operational safety and efficiency.
- Cobalt-Based Alloys: While not as common, cobalt alloys shine in applications demanding superior wear resistance. Think cutting tools and medical implants. Their exceptional corrosion resistance makes them indispensable for environments exposed to harsh chemicals or saline conditions.
- Iron-Based Alloys: Cost-effective yet reliable, these alloys are often reinforced with chromium and molybdenum to boost heat tolerance. They are widely used in automotive and industrial applications, where moderate high-temperature performance is sufficient.
The choice of alloy depends on the specific operational requirements and cost constraints. For example, aerospace engineers might opt for nickel-based alloys for jet turbines, while automotive manufacturers could lean toward iron-based alloys for exhaust systems. Here’s the deal: matching the right alloy with its intended application is a science, requiring expertise in material properties, thermal dynamics, and engineering design.
Finally, the emergence of superalloys—a hybrid category blending nickel, cobalt, and other elements—has pushed the boundaries of what’s possible in high temp applications. These materials offer unprecedented strength and longevity, albeit at a higher production cost. For industries where failure is not an option, the investment is often justified.
By understanding the nuances of the casting process and the properties of various alloys, industries can harness the full potential of high temp alloy casting.
Industrial Sectors Utilizing High Temp Alloy Castings
Aerospace: Pushing the Boundaries of Flight
The aerospace industry represents one of the most critical and demanding applications for high temperature alloys. Jet engines, the heart of modern aircraft, are exposed to extreme thermal stresses, often exceeding 1,400 degrees Celsius. This environment necessitates materials that can not only withstand the heat but also maintain structural integrity under immense pressure.
Here’s why it matters: High temp alloy castings, particularly nickel-based superalloys, are used extensively in the production of turbine blades and combustion chambers. These components operate in high-stress zones where failure is simply not an option. What makes these alloys indispensable is their ability to resist thermal fatigue and oxidation, ensuring long operational lifespans.
The precision casting process used in aerospace also allows for the creation of intricate geometries optimized for performance. For example, turbine blades often feature complex internal cooling channels designed to reduce thermal load while maintaining efficiency. Without high temp alloy casting, these advanced designs would be impossible to manufacture.
Beyond jet engines, aerospace relies on these materials for auxiliary systems like exhaust nozzles, afterburners, and even space exploration components. High temp alloys are critical for rockets, where materials must endure both the extreme heat of reentry and the cold vacuum of space. What’s the takeaway? The aerospace sector’s reliance on these materials underscores their unmatched performance in critical applications.
Automotive: Driving Innovation and Efficiency
The automotive industry is increasingly adopting high temp alloy casting for high-performance engines, turbochargers, and exhaust systems. Why? It’s all about efficiency. Modern engines are designed to operate at higher temperatures to improve fuel efficiency and reduce emissions, pushing traditional materials beyond their limits.
High temp alloys offer a unique solution by enabling components to withstand extreme operating conditions without deforming or deteriorating. For example, turbocharger housings crafted from nickel-based alloys ensure consistent performance under repeated thermal cycling. And the result? Enhanced vehicle reliability and reduced maintenance costs.
Another significant application is in catalytic converters, where high temp alloys play a role in maintaining structural integrity while facilitating the chemical reactions necessary for emission control. These advancements not only meet stringent environmental regulations but also pave the way for greener automotive technologies.
High-performance racing vehicles also benefit from these materials. Engine components made from high temp alloys reduce weight while increasing durability, providing the competitive edge needed in motorsport.
Energy: Powering the World with Resilience
The energy sector demands materials capable of enduring punishing conditions in power plants, whether they burn fossil fuels, harness nuclear reactions, or utilize renewable sources like concentrated solar power. High temp alloy castings are indispensable in these applications.
In gas and steam turbines, for instance, high temp alloys are used for blades, casings, and other critical components. These turbines often operate at temperatures above 1,000 degrees Celsius, where lesser materials would fail. Why does this matter? Reliable materials directly translate to higher efficiency and lower downtime, both of which are essential for meeting global energy demands.
In the renewable sector, solar thermal plants rely on high temp alloys for heat exchangers and receivers, where materials must endure both extreme heat and corrosive environments. Similarly, nuclear power plants use these materials in reactor cores, where both radiation and high temperatures pose challenges.
High temp alloy casting also supports the transition to cleaner energy. Advanced alloys enable the design of components for hydrogen production and storage, paving the way for future energy solutions. The bottom line: The energy sector’s reliance on these materials underscores their critical role in driving global progress.
Manufacturing: Industrial Strength Redefined
In manufacturing, high temp alloys are the backbone of tools, molds, and machinery exposed to intense heat and mechanical wear. Foundries, in particular, use these materials for furnace linings and crucibles, where temperatures can soar above 1,500 degrees Celsius.
But there’s more: The rise of additive manufacturing has introduced new opportunities for high temp alloy casting. By integrating 3D printing technologies, manufacturers can produce custom components with intricate designs tailored to specific industrial needs. This fusion of traditional and modern techniques is transforming the manufacturing landscape.
These alloys also find use in chemical processing industries, where corrosive environments demand materials with exceptional resistance. Reactors, pipelines, and heat exchangers made from high temp alloys ensure safe and efficient operations, even in the harshest conditions.
Defense and Marine: Strength Under Pressure
In defense and marine applications, high temp alloys provide unmatched durability and resistance to extreme environments. Naval vessels, for instance, rely on these materials for engine components and exhaust systems exposed to high thermal and mechanical stresses.
High temp alloys are also critical in military aviation, where materials must perform under both high-speed and high-temperature conditions. Here’s the twist: These materials don’t just endure—they enhance performance, ensuring that critical systems remain operational in the most challenging scenarios.
In the marine sector, high temp alloy castings are used in desalination plants, where components face continuous exposure to saline environments. Their superior corrosion resistance ensures long-term reliability, reducing maintenance costs and improving operational efficiency.
Key Factors to Identify the Right Application
Understanding Operational Requirements
High temperature alloys aren’t a one-size-fits-all solution. Selecting the right alloy depends on understanding the specific operational conditions it will face. Temperature ranges, mechanical loads, and environmental factors like corrosion all influence material choice. Here’s why: A misstep in alloy selection can lead to catastrophic failure, especially in high-stakes applications like aerospace or energy production.
For example, applications in high-oxidation environments might prioritize chromium-enriched alloys for their superior resistance. Meanwhile, industries requiring wear-resistant materials, such as mining or manufacturing, might opt for cobalt-based alloys. The key takeaway: Knowing your application’s unique demands is essential for making the right material choice.
Material Testing and Certifications
Certifications like ASTM and ISO standards are non-negotiable in industries that prioritize safety and performance. Rigorous material testing ensures that high temp alloys meet these standards, guaranteeing reliability. Common tests include creep testing for high-stress environments and thermal fatigue testing for components subject to temperature cycling. Why does this matter? It builds confidence in the material’s ability to perform as expected.
Key Factors to Identify the Right Application
Understanding Operational Requirements
High temperature alloys aren’t a one-size-fits-all solution. Selecting the right alloy depends on understanding the specific operational conditions it will face. Temperature ranges, mechanical loads, and environmental factors like corrosion all influence material choice. Here’s why: A misstep in alloy selection can lead to catastrophic failure, especially in high-stakes applications like aerospace or energy production.
For example, applications in high-oxidation environments might prioritize chromium-enriched alloys for their superior resistance. Meanwhile, industries requiring wear-resistant materials, such as mining or manufacturing, might opt for cobalt-based alloys. The key takeaway: Knowing your application’s unique demands is essential for making the right material choice.
Material Testing and Certifications
Certifications like ASTM and ISO standards are non-negotiable in industries that prioritize safety and performance. Rigorous material testing ensures that high temp alloys meet these standards, guaranteeing reliability. Common tests include creep testing for high-stress environments and thermal fatigue testing for components subject to temperature cycling. Why does this matter? It builds confidence in the material’s ability to perform as expected.
Challenges in High Temp Alloy Casting
Production Challenges
Manufacturing high temp alloys is a complex process that demands precise control over variables such as temperature, cooling rates, and alloy composition. One major hurdle is porosity, which occurs when gas gets trapped during solidification, weakening the material. Advanced casting techniques, like vacuum casting, address this issue by minimizing exposure to air during the process.
Another challenge is cracking, which can occur due to thermal stress during cooling. This problem is particularly prevalent in larger components, where uneven cooling rates are more likely. What’s the solution? Techniques like directional solidification help control the microstructure, enhancing the material’s ability to resist stress.
Material Availability
The reliance on rare and expensive elements, such as cobalt and tungsten, poses another significant challenge. Supply chain disruptions, geopolitical factors, and resource scarcity can drive up costs, making high temp alloys less accessible to smaller manufacturers. Recycling and developing alternative alloys with similar properties are promising solutions to this issue.
Maintenance and Lifecycle
While high temp alloys offer exceptional durability, they are not immune to wear and tear. Components exposed to repeated thermal cycling or corrosive environments eventually degrade. Regular maintenance, combined with advancements in surface coatings, helps extend the lifecycle of these materials, reducing overall costs.
FAQs
What are the main advantages of high temp alloy castings?
High temp alloy castings offer exceptional heat resistance, mechanical strength, and corrosion resistance. These properties make them indispensable in critical applications across aerospace, automotive, energy, and more.
What industries benefit most from high temp alloys?
Industries like aerospace, energy, automotive, and manufacturing rely heavily on these materials. Emerging sectors such as renewable energy and advanced computing are also increasingly adopting high temp alloys.
How are high temp alloys tested for performance?
Rigorous testing methods, such as creep testing and thermal fatigue analysis, ensure these materials meet industry standards. Certifications like ASTM and ISO validate their reliability and safety.
What challenges do manufacturers face with high temp alloys?
Key challenges include production issues like porosity and cracking, material scarcity, and lifecycle management. Advanced casting techniques and recycling initiatives are helping overcome these barriers.
What does the future hold for high temp alloy applications?
The future looks promising, with growing demand in lightweighting, renewable energy, and advanced technologies like hydrogen systems and AI cooling.