Introduction: Understanding Alloy Casting’s Challenges
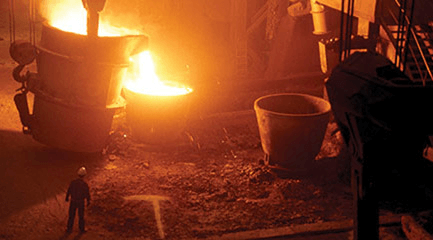
Alloy casting is a cornerstone of modern manufacturing, enabling the production of complex parts for industries like aerospace, automotive, and construction. Yet, like any intricate process, it has vulnerabilities that can compromise quality and efficiency. Understanding these weak points is critical for improving outcomes and reducing costs. This article explores the common flaws in alloy casting, their causes, and practical solutions, offering a roadmap to elevate casting standards. By the end, you’ll have a comprehensive grasp of how to identify and tackle these challenges effectively.
What Is Alloy Casting?
Definition and Types of Alloy Casting
Alloy casting refers to the process of pouring molten metal alloys into molds to form specific shapes as the material solidifies. This technique has been a manufacturing staple for centuries, evolving alongside technological advancements. There are several types of alloy casting, including sand casting, investment casting, die casting, and permanent mold casting. Each serves distinct applications based on material properties and desired part complexity.
Role in Modern Industries
Alloy casting is integral to industries where precision, strength, and customization are essential. In aerospace, it produces lightweight yet robust components. The automotive sector relies on it for engine parts and structural elements. Construction uses it for durable frameworks and tools. The diversity of applications underscores the process’s adaptability and importance.
Why Understanding Weak Points Matters
Despite its advantages, alloy casting is not immune to flaws. Issues like porosity, cracking, and inclusions can undermine product performance and safety. These defects often arise from missteps in design, material selection, or process control. Recognizing these weak points is the first step toward implementing corrective measures, ensuring that cast parts meet or exceed industry standards.
Why Weak Points in Alloy Casting Matter
Impacts on Product Performance
Weak points in alloy casting can significantly affect product integrity. Porosity, for instance, compromises mechanical strength, leading to premature failure. Cracks, often caused by thermal stress, render parts unsuitable for critical applications. These flaws can undermine a product’s ability to withstand operational loads and environmental conditions, making reliability a concern.
Economic Consequences
The financial implications of casting flaws are substantial. Reworking defective parts or scrapping them entirely adds costs and delays. For manufacturers, this translates to wasted materials, increased labor, and lost revenue. Customers also bear the brunt through higher maintenance costs and shorter product lifespans. Addressing weak points proactively can minimize these financial burdens.
Real-World Examples
History provides stark reminders of the consequences of ignoring weak points. In the automotive industry, defective alloy wheels prone to cracking prompted costly recalls. Similarly, failures in cast turbine blades caused significant downtime in power plants. These incidents highlight the importance of understanding and mitigating weak points to safeguard both reputations and operations.
The Anatomy of a Weak Point in Alloy Castings
Common Types of Weak Points
Weak points in alloy castings typically manifest as porosity, inclusions, cracks, and dimensional inaccuracies. Porosity arises from trapped gases or shrinkage, creating voids that weaken the material. Inclusions are foreign particles embedded during solidification, affecting uniformity. Cracks, either hot or cold, compromise structural integrity, while dimensional errors hinder functionality.
Formation During the Casting Process
Each weak point stems from specific process inefficiencies. Porosity often results from inadequate degassing or cooling imbalances. Inclusions occur when slag or dross contaminates the molten alloy. Cracks form due to thermal gradients or residual stresses, and dimensional inaccuracies are linked to poor mold design or thermal expansion miscalculations.
Detection Methods
Identifying weak points requires advanced inspection techniques. Non-destructive testing (NDT) methods like X-ray radiography, ultrasonic testing, and dye penetrant inspection reveal internal and surface defects without damaging the part. Early detection allows manufacturers to rectify flaws before they escalate, ensuring quality and compliance.
Material-Related Weak Points
Alloy Composition Issues
The properties of an alloy depend on its composition. Variations in alloying elements, such as excess carbon in steel or inadequate chromium in stainless alloys, can lead to brittleness or corrosion susceptibility. Maintaining precise composition is essential for achieving desired mechanical and chemical properties.
Impurities and Their Effects
Impurities, including oxides and non-metallic inclusions, disrupt the homogeneity of the alloy. These can act as stress concentrators, reducing fatigue life and strength. Impurities are often introduced during melting or pouring, highlighting the need for stringent quality control measures.
Solutions for Ensuring Material Purity
To prevent material-related weak points, manufacturers employ refining processes such as vacuum degassing and filtration. These techniques remove impurities and gases, ensuring a cleaner melt. Additionally, strict adherence to material specifications and batch testing minimizes variability, producing consistent, high-quality castings.
Mold Design and Its Impact
Influence of Mold Geometry
The mold dictates the final shape and quality of the casting. Poorly designed molds can lead to defects such as shrinkage cavities, warping, or incomplete fills. Complex geometries increase the likelihood of such flaws, especially if cooling is uneven.
Common Design Errors
Mistakes in mold design often stem from neglecting material properties and cooling behavior. Sharp corners or abrupt thickness changes create stress concentrations, leading to cracks or distortion. Inadequate gating and riser systems exacerbate these issues by hindering proper flow and solidification.
Advances in Mold-Making Technology
Modern mold-making leverages computer-aided design (CAD) and simulation tools to predict and mitigate potential issues. Techniques like 3D printing enable rapid prototyping of complex molds, enhancing precision. These innovations reduce trial-and-error iterations, improving efficiency and quality.
Casting Process Parameters
Importance of Temperature Control
Temperature plays a pivotal role in casting success. Overheating the alloy can cause excessive oxidation, while underheating results in incomplete fills. Maintaining the ideal temperature ensures proper flow and solidification, minimizing defects.
Cooling Rate and Its Role
The cooling rate determines the microstructure of the alloy, directly impacting mechanical properties. Rapid cooling can induce residual stresses, while slow cooling risks coarser grain structures. Achieving a balanced cooling rate is critical for optimal performance.
Case Study: Parameter Mismanagement
In one instance, an aluminum casting plant experienced frequent porosity issues due to inconsistent furnace temperatures. Implementing automated controls eliminated these defects, demonstrating the importance of precise parameter management in avoiding weak points.
Porosity: The Silent Culprit
Causes of Porosity
Porosity originates from gas entrapment, shrinkage, or improper feeding. During solidification, dissolved gases may form bubbles, while inadequate riser systems fail to compensate for volume shrinkage. Both scenarios create voids that compromise strength.
Types of Porosity
Porosity can be classified into gas porosity, shrinkage porosity, and micro-porosity. Gas porosity appears as rounded voids, shrinkage porosity manifests as irregular cavities, and micro-porosity consists of tiny dispersed voids visible only under magnification.
Minimization Techniques
Preventing porosity requires meticulous process control. Degassing molten alloys, optimizing mold design, and maintaining appropriate pouring temperatures are effective strategies. Real-time monitoring using sensors ensures adherence to best practices, minimizing this pervasive issue.
Inclusions and Impurities
Sources of Inclusions
Inclusions often arise from slag, dross, or refractory material entering the molten metal. Mishandling during pouring or insufficient filtration exacerbates the problem. These contaminants disrupt the alloy’s uniformity, weakening the final product.
Effects on Mechanical Properties
Inclusions act as stress concentrators, reducing fatigue resistance and toughness. They compromise weldability and can cause aesthetic flaws, diminishing the part’s marketability. Addressing inclusions is critical for both functional and visual quality.
Effective Filtration Methods
Filtration systems, such as ceramic foam filters, trap inclusions before the alloy enters the mold. Coupled with slag removal techniques, these systems ensure cleaner melts. Regular equipment maintenance and operator training further mitigate contamination risks.
Causes of Cracking in Alloy Castings
Cracking, a prevalent defect in alloy casting, arises from factors like thermal gradients, improper alloy composition, and stress concentrations during cooling. Hot cracks occur when alloys are still partially molten, while cold cracks develop in solidified materials under residual stress. Uneven cooling and rapid temperature changes exacerbate these issues.
Differentiating Hot and Cold Cracks
Hot cracks often appear along grain boundaries due to insufficient ductility during solidification. Conversely, cold cracks result from external forces or contraction stresses acting on brittle materials. Identifying the type is critical to addressing its root cause and implementing corrective measures.
Prevention Strategies
To minimize cracking, manufacturers can optimize cooling rates and use heat-treatable alloys. Stress-relief treatments and careful mold design also play vital roles in distributing thermal loads evenly. Employing simulation software helps predict and mitigate cracking risks, ensuring a more robust casting process.
Machining Allowances and Casting Tolerances
Challenges of Achieving Precision
Precision in alloy casting is essential but often hampered by shrinkage, deformation, or inconsistent mold dimensions. Improper machining allowances lead to excess material removal, affecting strength and fit. Accurate tolerances ensure parts meet functional and aesthetic requirements.
Common Errors in Tolerance Settings
Manufacturers sometimes underestimate shrinkage or overcompensate for machining, resulting in under- or oversized components. Failing to account for alloy-specific behaviors during solidification exacerbates these inaccuracies.
Guidelines for Accurate Tolerances
To address these challenges, incorporate precise measurements during mold design and solidification modeling. Use advanced simulation tools to predict shrinkage and deformation. Establishing realistic machining allowances tailored to each alloy ensures quality and dimensional accuracy in the final product.
Post-Casting Treatments
Importance of Post-Casting Processes
Post-casting treatments like heat treatments, surface finishing, and defect repairs enhance the strength, durability, and appearance of alloy castings. Neglecting these steps often leaves flaws that compromise product performance.
Common Post-Casting Methods
Heat treatments such as annealing relieve internal stresses and refine grain structures, improving toughness. Surface finishing removes roughness, while non-destructive inspections identify and address hidden defects. Together, these processes ensure a robust and visually appealing end product.
Avoiding Mistakes in Post-Casting
Errors during post-casting, such as uneven heat treatment or excessive material removal during finishing, can introduce new defects. Following strict procedural guidelines and using automated systems for uniform results minimizes these risks, enhancing product quality.
Environmental Factors Affecting Alloy Casting
Role of External Conditions
External factors like humidity, temperature, and contamination can affect alloy casting. High humidity introduces moisture, leading to defects like porosity or oxide formation. Contaminants in the workspace compromise material purity.
Effects of Oxidation
Oxidation occurs when molten alloys react with oxygen, forming unwanted surface layers. These layers weaken bonds and introduce inclusions, compromising mechanical properties and appearance.
Controlled Environments for Consistency
Maintaining clean, climate-controlled casting environments mitigates these risks. Advanced equipment, such as inert gas chambers or vacuum systems, minimizes oxidation. Regular cleaning of molds and tools ensures consistent quality across production runs.
Advanced Technologies in Identifying Weak Points
Emerging Non-Destructive Testing Methods
Modern non-destructive testing (NDT) methods, including digital X-rays, ultrasonic scanning, and dye penetrants, revolutionize defect detection. These technologies provide detailed insights into internal structures without damaging the casting.
Artificial Intelligence in Defect Analysis
AI-powered systems analyze data from NDT techniques, identifying patterns and predicting weak points with high accuracy. Machine learning models optimize process parameters by correlating defects with specific casting conditions.
Future of Quality Assurance
Integrating NDT and AI streamlines defect detection and prevention. These innovations enable real-time monitoring and adaptive adjustments, reducing waste and improving overall casting reliability.
Best Practices for Avoiding Weak Points
Comprehensive Quality Control Checklist
A robust quality control system ensures every stage of alloy casting meets stringent standards. Key steps include verifying material composition, monitoring mold design, controlling temperatures, and performing post-casting inspections.
Collaboration and Training
Collaboration among engineers, technicians, and quality inspectors fosters a proactive approach to defect prevention. Regular training programs keep staff updated on the latest techniques and standards, promoting a culture of excellence.
Benefits of Proactive Measures
By addressing potential issues before production, manufacturers reduce defects, improve efficiency, and enhance customer satisfaction. Investing in quality control yields long-term benefits, including cost savings and reputation enhancement.
Conclusion: Strengthening Alloy Casting
Alloy casting is a dynamic and essential process, but it is not without challenges. Weak points like porosity, cracking, and inclusions threaten product integrity, efficiency, and profitability. However, by understanding their causes and implementing preventative measures, manufacturers can overcome these vulnerabilities. Advanced technologies such as NDT and AI, coupled with robust quality control practices, provide the tools necessary to ensure high standards. As industries continue to demand superior performance and precision, investing in improved alloy casting processes is not just beneficial—it’s essential. For those committed to excellence, the path to stronger, defect-free castings begins with vigilance, innovation, and a dedication to quality.
FAQ Section
What are the main causes of porosity in alloy casting?
Porosity typically results from gas entrapment during solidification, shrinkage due to improper feeding systems, or contamination in the molten alloy.
How can mold design prevent weak points?
Optimized mold design ensures even cooling, minimizes stress concentrations, and facilitates proper metal flow, reducing the risk of defects like warping or cracks.
Which technologies are best for detecting defects in castings?
Non-destructive testing methods, such as X-ray radiography, ultrasonic testing, and dye penetrants, are highly effective for identifying internal and surface defects.
What industries benefit most from improved alloy casting?
Sectors like aerospace, automotive, construction, and medical devices rely heavily on high-quality castings for performance-critical applications.
How does temperature control improve casting outcomes?
Maintaining precise temperatures during pouring and cooling ensures uniform solidification, reducing defects like porosity and thermal stresses.
This comprehensive article offers in-depth insights into alloy casting’s vulnerabilities, ensuring manufacturers and stakeholders have the knowledge to enhance their processes.