Understanding High-Temperature Alloys
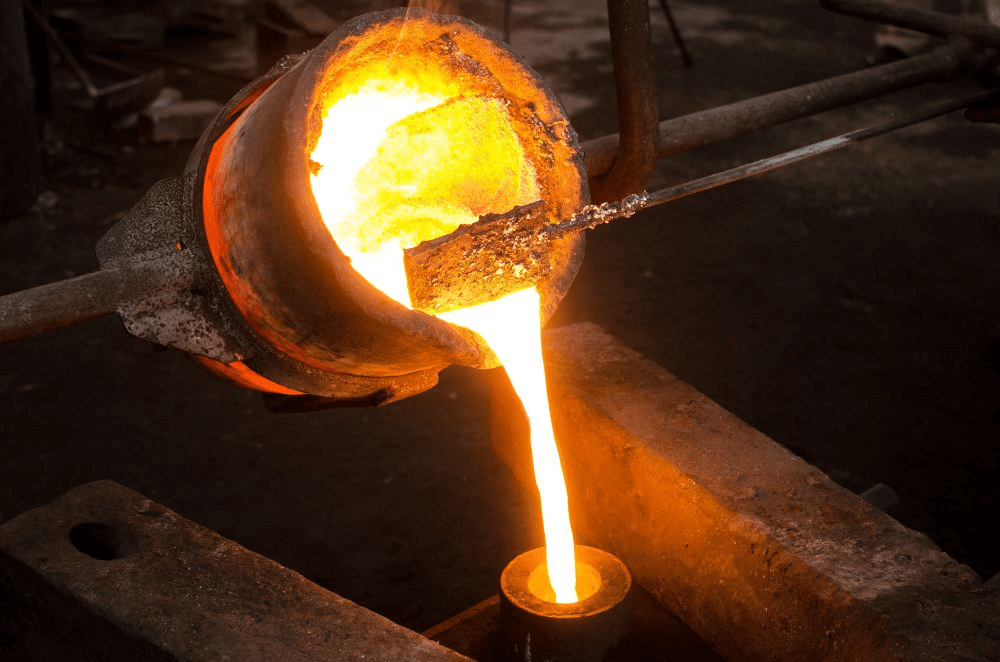
High-temperature alloys are specialized materials designed to perform reliably under extreme conditions. These materials are primarily used in applications where components are exposed to intense heat, high pressure, or corrosive environments. The defining characteristic of high-temperature alloys is their ability to retain strength and resist deformation even when subjected to temperatures that would compromise most other materials. This resilience makes them indispensable in industries such as aerospace, automotive, energy, and even medical technology.
Three main types dominate the landscape: nickel-based, cobalt-based, and iron-based alloys. Nickel-based alloys are the most widely used due to their exceptional heat resistance and durability. These are ideal for jet engines and gas turbines. Cobalt-based alloys excel in resisting wear and corrosion, making them a popular choice in medical implants and industrial applications. Iron-based alloys, often seen as stainless steels, are versatile and cost-effective, catering to various high-temperature scenarios.
The development of high-temperature alloys represents a fascinating intersection of science and engineering. The materials are composed of a primary metal and a range of alloying elements like chromium, molybdenum, and titanium, each contributing unique properties. For example, chromium enhances oxidation resistance, while molybdenum boosts high-temperature strength. These alloys often undergo stringent testing and refinement to ensure they meet the demanding requirements of their applications.
The significance of these materials lies in their unique ability to withstand both thermal and mechanical stresses. Without high-temperature alloys, many modern engineering marvels, such as space exploration vehicles and nuclear reactors, would be impossible. As technology continues to evolve, the demand for more advanced high-temperature alloys is set to grow, pushing the boundaries of what these materials can achieve.
Key Properties of High-Temperature Alloys
High-temperature alloys are revered for their unique set of properties that enable them to thrive in extreme conditions. Understanding these attributes sheds light on why they are indispensable in critical industries. Among their most notable properties is their impressive heat resistance. These alloys can endure temperatures exceeding 1000°C without losing their structural integrity, a feat that makes them ideal for applications like turbine blades and exhaust systems.
Mechanical strength is another cornerstone of their appeal. High-temperature alloys maintain their robustness under heavy loads, even when subjected to high-stress environments. This characteristic is crucial in aerospace applications, where components like engine parts face continuous mechanical strain. Moreover, these materials exhibit exceptional resistance to thermal fatigue, which is the degradation that occurs when materials are repeatedly exposed to fluctuating temperatures.
Oxidation and corrosion resistance further elevate the performance of these alloys. In environments rich in oxygen or harsh chemicals, most metals would degrade quickly. However, high-temperature alloys, often fortified with elements like chromium and aluminum, form a protective oxide layer that shields them from corrosion. This property ensures longevity in applications such as chemical processing plants and power generation equipment.
The ability to retain mechanical properties during thermal cycling is another vital aspect. Thermal cycling involves rapid heating and cooling, which can cause materials to expand and contract, leading to stress and eventual failure. High-temperature alloys are designed to accommodate such changes without significant performance losses.
In essence, the properties of high-temperature alloys are a testament to their advanced engineering and material science. Their ability to withstand heat, mechanical stress, and corrosive environments makes them a linchpin in modern industrial and technological advancements, ensuring safety, reliability, and efficiency.
What Is High-Temperature Alloy Casting?
High-temperature alloy casting is a sophisticated manufacturing process that involves shaping molten high-temperature alloys into precise components. Unlike standard casting, this method is tailored to handle alloys that require exceptionally high melting points and specific cooling profiles. The process is integral to creating parts that must endure the harshest conditions, such as turbine blades in jet engines or components in nuclear reactors.
The fundamental principle of casting remains the same: molten metal is poured into a mold where it solidifies into the desired shape. However, the casting of high-temperature alloys demands a higher level of precision and control. The alloys used in this process are engineered for their specific properties, including thermal stability and resistance to mechanical and chemical stresses. Consequently, every stage, from melting to cooling, is carefully monitored to ensure the integrity and performance of the final product.
A key distinction in high-temperature alloy casting is the use of specialized molds. These molds are often made from advanced refractory materials that can withstand extreme heat without degrading. Moreover, the design of the mold must account for factors like shrinkage and the prevention of defects such as porosity or cracks. Precision engineering in mold creation is critical to achieving the desired outcome.
The significance of high-temperature alloy casting lies in its ability to produce components with intricate shapes and superior performance. This process supports innovation in industries where conventional materials and methods fall short. From aerospace and automotive to energy production, the versatility and reliability of high-temperature alloy casting are indispensable for advancing technology and meeting the challenges of extreme environments.
The Science Behind Casting High-Temperature Alloys
Casting high-temperature alloys is as much a scientific endeavor as it is an industrial process. At its core, the science involves managing the complex interactions between heat, metal, and the environment to produce high-performance components. The journey begins with understanding the melting points of the alloys involved. High-temperature alloys, often with melting points exceeding 1200°C, require precise temperature control to ensure uniformity in the molten metal.
Chemical composition plays a pivotal role in determining the behavior of the alloy during casting. Alloying elements like chromium, nickel, and cobalt not only influence the alloy’s properties but also dictate how it reacts to heat and cooling. For instance, some elements might segregate during cooling, potentially leading to weak spots if not properly managed. Thus, achieving a homogenous mixture is crucial, and this is often accomplished through techniques like electromagnetic stirring.
Heat transfer and cooling rates are another critical aspect of the science. Rapid cooling, or quenching, can lock the alloy’s microstructure in place, enhancing certain properties like hardness. Conversely, controlled slow cooling may be used to achieve a fine-grain structure that enhances toughness and reduces brittleness. Balancing these rates is a meticulous task that directly impacts the quality of the final product.
The casting environment also requires careful control. The presence of oxygen, for example, can lead to oxidation, compromising the material’s surface and performance. To mitigate this, vacuum casting or inert gas environments are often employed. These controlled settings help maintain the purity of the alloy and prevent unwanted reactions.
By blending metallurgical principles with cutting-edge technology, the science of casting high-temperature alloys enables the production of components that meet exacting specifications. This scientific rigor ensures that the end products not only perform well but also stand the test of time in the most demanding applications.
Tools and Equipment in High-Temperature Alloy Casting
The successful casting of high-temperature alloys hinges on the use of specialized tools and equipment designed to withstand and manipulate extreme conditions. At the heart of this process is the induction furnace, a device capable of achieving the high temperatures required to melt these advanced alloys. Unlike traditional furnaces, induction furnaces use electromagnetic fields to generate heat, ensuring uniform melting and reducing contamination risks.
Molds are another cornerstone of the casting process. These molds are typically made from refractory materials such as ceramics or graphite, chosen for their ability to endure intense heat without degrading. The design of the mold must be precise, accounting for factors like shrinkage and thermal expansion to ensure that the final product matches its intended dimensions. Advanced manufacturing techniques, including 3D printing, are increasingly being used to create intricate mold designs.
Cooling systems are equally vital in high-temperature alloy casting. These systems control the rate at which the alloy solidifies, a factor that directly impacts the material’s microstructure and properties. Water-cooled or air-cooled setups are common, and in some cases, a combination of both is used to achieve the desired cooling profile.
Additionally, advanced inspection tools play a crucial role in ensuring quality. X-ray and ultrasonic testing equipment are used to detect internal defects such as voids or cracks, which could compromise the performance of the cast component. These tools enable manufacturers to identify and address issues early in the production process, saving time and resources.
Emerging technologies are continually enhancing the capabilities of casting tools and equipment. From automation and robotics to machine learning algorithms for defect prediction, these innovations are making the process more efficient and reliable. Together, these tools and technologies ensure that high-temperature alloy casting meets the stringent demands of modern industries.
Steps in the High-Temperature Alloy Casting Process
The process of high-temperature alloy casting is a meticulously orchestrated series of steps, each critical to achieving the desired quality and performance. It begins with designing the mold, a stage where precision is paramount. Using CAD (Computer-Aided Design) software, engineers create molds that accommodate the complex shapes and tolerances required. Material selection for the mold is equally crucial, often involving ceramics or other refractory materials that can withstand extreme temperatures.
Next comes the melting stage, where the high-temperature alloy is heated in an induction furnace until it reaches a molten state. During this phase, maintaining a uniform temperature is essential to ensure homogeneity in the alloy. Impurities are removed through processes like slag skimming or vacuum refining, further enhancing the material’s quality.
The molten metal is then poured into the mold in a controlled environment to prevent oxidation or contamination. Techniques such as vacuum pouring or inert gas atmospheres are often employed to achieve this. The pouring speed and angle are carefully regulated to avoid turbulence, which could introduce defects like porosity.
Cooling and solidification follow, a stage that has a profound impact on the alloy’s microstructure. Controlled cooling is achieved using advanced cooling systems that manage heat dissipation at precise rates. This step ensures that the alloy attains the desired mechanical and thermal properties.
Finally, the finishing process involves removing the cast from the mold, cleaning it, and performing any necessary machining. Heat treatments may also be applied to enhance specific properties such as strength or toughness. Quality control inspections, including non-destructive testing, ensure that the final product meets all specifications and is free from defects.
Types of Casting Techniques Used
High-temperature alloy casting employs several specialized techniques, each tailored to meet specific requirements and applications. The choice of technique depends on factors such as the complexity of the part, the volume of production, and the desired material properties. Among these, investment casting—commonly known as the lost-wax process—stands out as one of the most precise methods. In this technique, a wax pattern of the part is created, coated with a ceramic shell, and then melted away to leave a cavity for molten metal. This method is ideal for producing intricate and detailed components, such as turbine blades, with exceptional dimensional accuracy.
Another widely used method is sand casting, which is more suited for high-volume production. Sand molds, typically made from silica sand mixed with binders, offer flexibility and cost efficiency for producing larger components. Despite its lower precision compared to investment casting, sand casting excels in creating durable parts for automotive and industrial applications.
Die casting is another approach, leveraging high-pressure techniques to inject molten metal into steel molds. This method allows for rapid production and is often chosen for smaller, highly detailed parts. Die casting is particularly advantageous when manufacturing components that require consistent quality across large batches.
For high-temperature alloys sensitive to oxidation, vacuum casting is a preferred choice. By removing air from the casting environment, this method prevents unwanted chemical reactions, ensuring superior material integrity. Vacuum casting is often used in aerospace and energy sectors, where even minor impurities could compromise performance.
Each of these techniques has unique strengths, making them indispensable in manufacturing high-performance components. By carefully selecting the appropriate method, manufacturers can balance cost, efficiency, and quality to meet the demands of specific applications, ensuring the reliability of the final product in its operational environment.
Challenges in High-Temperature Alloy Casting
Casting high-temperature alloys is fraught with challenges that demand innovative solutions and meticulous attention to detail. One of the primary hurdles is managing thermal stresses during the cooling phase. As the molten alloy solidifies, it contracts, which can lead to cracking or warping if not carefully controlled. Advanced cooling systems and simulation tools are often employed to predict and mitigate these stresses.
Another significant challenge is defect prevention, particularly issues like porosity, inclusions, and micro-cracks. These defects can compromise the structural integrity and performance of the cast component. To address this, manufacturers use techniques such as vacuum casting to minimize contamination and non-destructive testing to detect internal flaws early in the process.
The complexity of material behavior under high temperatures adds another layer of difficulty. High-temperature alloys often exhibit unique characteristics, such as segregation of alloying elements during cooling. This phenomenon can create weak spots if not managed properly. Controlling the cooling rate and using advanced alloy compositions are strategies used to counteract these issues.
Mold design and durability also pose challenges. The molds must withstand extreme temperatures without degrading, while maintaining precise dimensions. Wear and tear on molds can lead to inconsistencies in production, necessitating frequent replacements or the use of more durable materials.
Finally, the economic and environmental aspects of high-temperature alloy casting cannot be overlooked. The energy-intensive nature of the process contributes to higher production costs and environmental impact. Manufacturers are increasingly adopting energy-efficient technologies and recycling practices to address these concerns, striving for a balance between performance and sustainability.
Overcoming these challenges requires a combination of technological advancements, skilled craftsmanship, and rigorous quality control, ensuring that the final products meet the high standards demanded by their applications.
Innovations in Alloy Casting
The field of high-temperature alloy casting is continuously evolving, driven by technological advancements and the need for more efficient processes. One of the most transformative innovations is the integration of artificial intelligence (AI) and machine learning. These technologies enable manufacturers to predict potential defects, optimize process parameters, and improve overall production efficiency. For example, AI can analyze data from previous casting runs to identify patterns and recommend adjustments for better results.
Another groundbreaking development is the use of additive manufacturing, or 3D printing, in mold and pattern creation. This technology allows for the rapid production of complex and customized molds, reducing lead times and costs. Additionally, additive manufacturing can produce intricate geometries that were previously impossible with traditional methods, opening new possibilities for design and performance.
Advanced coating technologies for molds have also made a significant impact. By applying specialized coatings, manufacturers can extend the lifespan of molds and enhance their thermal resistance. This reduces the frequency of mold replacements and improves the overall efficiency of the casting process.
The advent of robotics and automation has revolutionized many aspects of alloy casting. Robotic systems can handle tasks such as pouring molten metal and removing finished parts with greater precision and consistency than manual operations. Automation not only improves productivity but also enhances worker safety by minimizing exposure to hazardous conditions.
Lastly, the use of Internet of Things (IoT) technologies is enabling real-time monitoring and control of casting processes. Sensors embedded in equipment provide continuous data on temperature, pressure, and other critical parameters, allowing for immediate adjustments to ensure optimal conditions.
These innovations are shaping the future of high-temperature alloy casting, making it more efficient, reliable, and capable of meeting the demands of increasingly complex applications.
Applications of High-Temperature Alloy Castings
High-temperature alloy castings play a pivotal role in numerous industries, thanks to their ability to withstand extreme conditions and deliver exceptional performance. In the aerospace sector, these castings are indispensable for components such as jet engine turbine blades, which operate under intense heat and stress. The ability of high-temperature alloys to retain strength and resist oxidation ensures the safety and efficiency of modern aircraft.
In the automotive industry, high-temperature alloys are used in turbochargers, exhaust manifolds, and other engine components. These parts must endure high temperatures and corrosive environments while maintaining optimal performance. The use of these advanced materials enhances fuel efficiency and reduces emissions, aligning with the industry’s push toward sustainability.
The energy sector is another major beneficiary, particularly in gas turbines and nuclear reactors. High-temperature alloys enable power generation systems to operate at higher efficiencies by withstanding the extreme heat and pressures involved. In renewable energy, components like heat exchangers and solar thermal systems also rely on these alloys for durability and reliability.
Medical and industrial applications further highlight the versatility of high-temperature alloy castings. In the medical field, cobalt-based alloys are commonly used for prosthetics and surgical instruments due to their biocompatibility and resistance to wear. In industrial settings, these materials are found in machinery parts, chemical processing equipment, and tools exposed to harsh operating conditions.
From enhancing the performance of cutting-edge technology to ensuring safety and durability in everyday applications, high-temperature alloy castings are a cornerstone of modern innovation. Their widespread use underscores their importance in advancing industries and meeting the challenges of the future.
Quality Control in High-Temperature Alloy Casting
Ensuring the quality of high-temperature alloy castings is a rigorous process that combines advanced technology and meticulous attention to detail. One of the primary methods used is non-destructive testing (NDT), which allows for the inspection of components without compromising their integrity. Techniques such as X-ray radiography and ultrasonic testing are employed to detect internal defects like voids, cracks, and inclusions. These methods ensure that only flawless components proceed to the next stage of production.
Metallurgical analysis is another critical aspect of quality control. By examining the microstructure of the alloy, manufacturers can verify that the material properties meet the required specifications. This analysis often includes assessing grain size, phase distribution, and the presence of any unwanted impurities or segregations.
Dimensional accuracy is equally important, particularly for components that must fit precisely within larger assemblies. Coordinate measuring machines (CMMs) and laser scanning technologies are commonly used to measure and verify dimensions against design specifications. Any deviations are corrected through machining or adjustments to the casting process.
Heat treatments, such as annealing or quenching, are also subjected to stringent quality checks to ensure they achieve the desired mechanical properties. These treatments play a crucial role in enhancing strength, toughness, and resistance to wear.
Finally, adherence to international standards, such as ISO and ASTM, provides an additional layer of assurance. Compliance with these standards ensures that the castings meet global benchmarks for safety, reliability, and performance, making them suitable for critical applications in aerospace, automotive, and energy sectors.
Environmental and Economic Considerations
The high-temperature alloy casting industry faces significant environmental and economic challenges. The process is energy-intensive, requiring large amounts of heat to melt and process alloys, which contributes to high operational costs and carbon emissions. To address these issues, manufacturers are increasingly turning to energy-efficient technologies, such as induction furnaces, which consume less power compared to traditional methods.
Recycling and reusing materials are also gaining traction as a means to reduce waste and lower production costs. By reclaiming scrap metal and re-melting it into new castings, manufacturers can minimize material wastage and lessen their environmental footprint. This practice not only conserves resources but also reduces the need for mining and refining raw materials, which are both energy-intensive and environmentally harmful.
Another consideration is the cost of raw materials, which can fluctuate due to market conditions and geopolitical factors. High-temperature alloys often contain rare and expensive elements like cobalt and molybdenum, making cost management a critical aspect of the industry. Strategies such as optimizing alloy compositions and sourcing alternative materials are being explored to mitigate these challenges.
Manufacturers are also adopting sustainable practices to align with global environmental regulations and customer expectations. These include implementing waste heat recovery systems, using eco-friendly binders in molds, and investing in research to develop greener alloys.
Balancing performance, cost, and sustainability is a complex but essential task for the high-temperature alloy casting industry. By embracing innovation and adopting responsible practices, the industry can continue to thrive while minimizing its impact on the planet.
Future Trends in High-Temperature Alloy Casting
The future of high-temperature alloy casting is set to be defined by innovation and adaptation to emerging technologies. One of the most exciting trends is the development of superalloys, which push the boundaries of performance by incorporating advanced elements and manufacturing techniques. These materials promise enhanced strength, thermal resistance, and durability, opening new possibilities for aerospace, energy, and automotive applications.
Additive manufacturing is also poised to play a transformative role. By integrating 3D printing with traditional casting methods, manufacturers can create complex components with greater efficiency and less waste. This hybrid approach is expected to revolutionize the design and production of high-performance parts, enabling greater customization and faster turnaround times.
Robotics and automation are becoming increasingly prevalent in casting facilities, improving precision and consistency while reducing labor costs. Automated systems can perform tasks such as mold preparation, metal pouring, and quality inspections with unmatched accuracy, enhancing overall productivity.
The integration of smart technologies, such as IoT and AI, is another major trend. Real-time data collection and analysis allow manufacturers to monitor and optimize every aspect of the casting process, from temperature control to defect detection. These advancements ensure higher quality and reduce the likelihood of errors, leading to cost savings and improved customer satisfaction.
Finally, the focus on sustainability will continue to drive innovation. Research into alternative materials, energy-efficient processes, and waste reduction techniques will shape the future of the industry, ensuring it meets the demands of a rapidly changing world while minimizing its environmental impact.
Frequently Asked Questions (FAQ)
What industries benefit most from high-temperature alloy casting?
Industries such as aerospace, automotive, energy, and medical fields rely heavily on high-temperature alloy casting for components that must perform in extreme conditions.
How does the cost of high-temperature alloys compare to other materials?
High-temperature alloys are more expensive due to their advanced properties and the inclusion of rare elements. However, their durability and performance often justify the higher cost.
What are the common defects in this casting process, and how are they mitigated?
Defects like porosity, cracks, and inclusions are common. These are mitigated using techniques like vacuum casting, non-destructive testing, and precise control of process parameters.
Can high-temperature alloy castings be recycled?
Yes, scrap metal from high-temperature alloys can be recycled and reused, reducing waste and conserving resources.
What advancements are shaping the future of this industry?
Innovations like superalloys, additive manufacturing, robotics, and AI-driven processes are transforming high-temperature alloy casting, making it more efficient and sustainable.
Conclusion
High-temperature alloy casting is a cornerstone of modern manufacturing, enabling the creation of components that withstand extreme conditions. Through meticulous processes, advanced technologies, and a commitment to quality, this industry supports innovations across critical sectors. By embracing future trends and sustainable practices, high-temperature alloy casting will continue to thrive, pushing the boundaries of what’s possible in engineering and material science.