Introduction
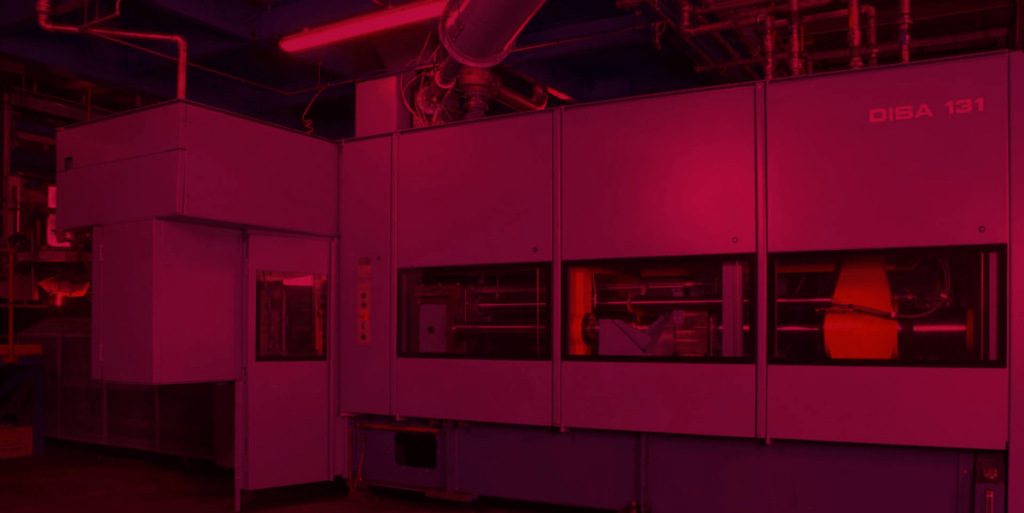
High-temperature alloy casting has transformed modern industries, providing unparalleled durability and heat resistance in critical applications. Imagine jet engines withstanding extreme heat or gas turbines powering cities without a hitch—this is the magic of these alloys. Designed for environments that demand exceptional strength and resilience, high-temperature alloy casting enables complex designs and superior performance. Whether you’re in aerospace, automotive, or renewable energy, understanding its applications can help streamline production and enhance product reliability. This guide dives into the key properties, industries, and innovations of high-temperature alloy casting, explaining why it remains a cornerstone of advanced manufacturing today.
What Is High-Temperature Alloy Casting?
High-temperature alloy casting involves molding metals like nickel, cobalt, and titanium into components that endure extreme thermal and mechanical stress. These alloys are meticulously engineered to resist deformation, corrosion, and oxidation even under harsh conditions. This casting process allows manufacturers to create intricate shapes that standard materials can’t achieve.
The materials used in this process are critical. Nickel-based alloys dominate due to their excellent thermal stability, followed by cobalt alloys known for their strength and oxidation resistance. Other metals, such as titanium, enhance the versatility of high-temperature casting. These materials offer an ideal balance between weight and performance, making them perfect for high-stakes applications.
The process also incorporates precision. Advanced techniques, including investment casting, deliver unmatched accuracy, essential for industries where tolerances are minimal. The ability to form complex geometries ensures efficiency in production and performance. For example, turbine blades with internal cooling passages are made possible by this level of detail.
Overall, high-temperature alloy casting is not merely a manufacturing technique. It’s a fusion of science and engineering, ensuring components survive and thrive in environments where failure isn’t an option. From jet engines to medical implants, this process offers a blend of innovation and reliability that few others can match.
Historical Evolution of High-Temperature Alloy Casting
The history of high-temperature alloy casting is closely tied to advancements in aerospace and industrial engineering. It began with the advent of aviation in the early 20th century. As aircraft engines grew more powerful, traditional materials couldn’t withstand the heat and stress, prompting engineers to develop specialized alloys.
The 1940s marked a breakthrough with nickel-based alloys during World War II. These materials revolutionized the performance of jet engines, allowing them to operate at higher temperatures and efficiencies. The development of investment casting during this era further enhanced precision and scalability, setting the stage for widespread adoption.
Post-war industrialization saw high-temperature alloys branching into other sectors. The automotive industry began using them for turbochargers, while the energy sector adopted them for turbines in power plants. By the 1970s, their role in nuclear energy solidified their reputation as indispensable materials for extreme environments.
In recent decades, advancements in computational modeling and additive manufacturing have pushed these alloys to new heights. Modern techniques allow engineers to predict performance under stress, reducing development time and costs. Today, high-temperature alloys are at the forefront of innovation, underpinning industries from aerospace to renewable energy.
The evolution of high-temperature alloy casting reflects humanity’s relentless pursuit of efficiency and reliability. Each milestone represents not just technological progress but a commitment to solving complex challenges in engineering and manufacturing.
Key Properties That Make It Stand Out
High-temperature alloy casting stands out for its unique combination of properties that cater to the most demanding industrial applications. These alloys are designed to withstand thermal stress, resist corrosion, and maintain mechanical stability under extreme conditions.
Thermal resistance is one of the most critical properties. These alloys maintain their structural integrity at temperatures exceeding 1,000°C, making them ideal for jet engines, gas turbines, and industrial furnaces. Their ability to endure such conditions without deformation ensures long-term reliability and safety.
Corrosion resistance adds another layer of utility. High-temperature environments often involve exposure to aggressive chemicals or oxidizing agents. Alloys like Inconel and Hastelloy are engineered to resist such damage, extending the lifespan of components in harsh environments.
Mechanical stability is equally important. These alloys can handle significant mechanical loads without cracking or warping, even at elevated temperatures. This is vital for components like turbine blades, which experience intense centrifugal forces during operation.
Finally, the casting process itself enhances these properties. Techniques like vacuum casting and directional solidification minimize impurities and align grain structures for optimal performance. These methods ensure each component meets stringent quality standards, offering peace of mind in critical applications.
Overall, the combination of thermal resistance, corrosion resistance, and mechanical stability, coupled with advanced casting techniques, makes high-temperature alloy casting a cornerstone of modern engineering. It delivers performance and reliability that few materials can match.
Industries Where High-Temperature Alloy Casting Shines
High-temperature alloy casting has found its way into various industries, each leveraging its unique properties to overcome specific challenges. From aerospace to automotive, these alloys are indispensable.
In aerospace, they form the backbone of jet engines, which operate under extreme heat and stress. Components like turbine blades and combustion chambers rely on these materials for their unmatched strength and thermal resistance. The result is safer, more efficient aircraft capable of long-haul flights.
The automotive industry uses high-temperature alloys in turbochargers and exhaust systems. These components must withstand high heat generated by internal combustion engines while maintaining lightweight characteristics. This application not only improves vehicle performance but also reduces emissions.
In the energy sector, high-temperature alloys are critical for gas turbines and nuclear reactors. Their ability to resist thermal and chemical stress ensures uninterrupted power generation. Renewable energy applications, such as wind turbines, also benefit from these materials’ durability and resistance to wear.
Medical and defense industries are no exception. From surgical tools to military-grade equipment, these alloys provide the reliability needed in high-stakes environments. Their biocompatibility makes them suitable for medical implants, ensuring long-term performance within the human body.
The versatility of high-temperature alloy casting across these industries underscores its importance. It’s a testament to the adaptability and reliability of these materials in tackling some of the toughest engineering challenges.
Aerospace Applications
Aerospace represents one of the most significant applications of high-temperature alloy casting. Aircraft engines, in particular, demand materials that can endure extreme temperatures, high stress, and corrosive environments.
Turbine blades are a prime example. These components operate in the hottest part of the engine, where temperatures can exceed 1,500°C. High-temperature alloys ensure these blades maintain their shape and performance, enabling fuel-efficient and reliable flights.
Another critical application is combustion chambers. These parts must withstand intense heat and pressure while maintaining structural integrity. High-temperature alloys provide the necessary resilience, ensuring safety and efficiency in flight.
The aerospace industry also benefits from the precision offered by high-temperature alloy casting. Investment casting allows manufacturers to create intricate geometries with minimal tolerances, essential for optimizing engine performance.
From commercial jets to military aircraft, high-temperature alloys play a pivotal role in advancing aerospace technology. Their ability to combine strength, durability, and precision makes them an irreplaceable component of modern aviation.
Automotive Use Cases
In the automotive industry, high-temperature alloy casting has revolutionized performance and efficiency. Turbochargers are a standout application, leveraging these alloys to withstand the intense heat and pressure generated during operation. This results in better fuel efficiency and enhanced engine power.
Exhaust systems also benefit significantly. Components like catalytic converters and manifolds require materials that resist corrosion and high temperatures. High-temperature alloys meet these demands, ensuring longevity and reliability.
Beyond performance, these materials contribute to environmental sustainability. By enabling more efficient combustion and reducing emissions, high-temperature alloys support stricter environmental regulations.
The automotive sector’s reliance on these alloys reflects their unmatched ability to enhance both performance and sustainability. They represent a perfect blend of innovation and practicality in modern vehicle design.
Energy Sector Applications
High-temperature alloys are indispensable in the energy sector, particularly in power generation. Gas turbines, for example, operate at extreme temperatures to maximize efficiency. High-temperature alloys ensure these turbines maintain their performance and reliability over extended periods.
Nuclear reactors also rely on these materials. The alloys provide resistance to radiation and heat, ensuring the safety and longevity of critical components. In renewable energy, wind and solar power systems use high-temperature alloys for their durability and corrosion resistance.
The energy sector’s adoption of high-temperature alloys underscores their critical role in ensuring efficiency and reliability. As global energy demands grow, these materials will remain at the forefront of innovation, driving sustainability and technological advancement.
Medical Applications
High-temperature alloy casting is increasingly valuable in the medical field, particularly for implants and surgical tools. Materials like cobalt-chromium alloys offer exceptional biocompatibility, ensuring they can safely integrate with the human body. This makes them ideal for prosthetics, joint replacements, and dental implants.
Surgical instruments also benefit from these materials’ properties. Precision, durability, and resistance to wear are crucial for tools like scalpels, forceps, and endoscopic equipment. High-temperature alloys ensure these tools maintain their sharpness and effectiveness through repeated sterilization cycles.
Additionally, high-temperature alloys are advancing biomedical devices. Pacemakers, defibrillators, and other critical devices rely on these materials to withstand the body’s corrosive environment while maintaining functionality. Innovations in additive manufacturing further enhance the ability to customize these devices for individual patients.
By offering strength, biocompatibility, and precision, high-temperature alloys are transforming medical technology. They enable improved patient outcomes and the development of innovative solutions for complex medical challenges.
Emerging Technologies Leveraging High-Temperature Alloys
Emerging technologies are expanding the applications of high-temperature alloys. Space exploration, for instance, relies heavily on these materials. Rockets and spacecraft components endure extreme thermal and mechanical stresses during launch and reentry. High-temperature alloys provide the resilience needed for these missions.
Additive manufacturing, or 3D printing, is another area of growth. High-temperature alloys are being used to create complex, lightweight structures that were previously impossible to manufacture. This is particularly beneficial in aerospace and automotive sectors, where weight reduction is critical.
Hypersonic technology represents a cutting-edge application. Vehicles traveling at hypersonic speeds generate immense heat due to air friction. High-temperature alloys ensure these vehicles maintain their structural integrity, paving the way for advancements in defense and transportation.
These emerging technologies highlight the versatility and importance of high-temperature alloys. As industries push the boundaries of innovation, these materials will continue to play a pivotal role in achieving new milestones.
Benefits of High-Temperature Alloy Casting
High-temperature alloy casting offers numerous benefits, making it a preferred choice across industries. One of the primary advantages is its ability to withstand extreme heat, ensuring components remain functional under intense conditions.
Another significant benefit is durability. High-temperature alloys resist wear, corrosion, and fatigue, reducing the need for frequent replacements. This translates to lower maintenance costs and improved operational efficiency.
The precision offered by high-temperature alloy casting is equally valuable. Complex geometries can be achieved with high accuracy, enabling better performance and design flexibility. This is particularly important in industries like aerospace and medical technology, where tolerances are critical.
Environmental benefits are also noteworthy. By improving efficiency and reducing emissions, high-temperature alloy components support sustainable practices. Whether in power generation or automotive applications, these materials contribute to greener solutions.
Overall, the benefits of high-temperature alloy casting extend beyond performance and reliability. They offer cost savings, sustainability, and the ability to meet the most demanding engineering challenges.
Challenges and Limitations
Despite its advantages, high-temperature alloy casting has challenges. One of the primary issues is cost. The materials used, such as nickel and cobalt, are expensive, making the process less accessible for budget-constrained projects.
Manufacturing complexities also pose a challenge. Achieving the precision required for advanced applications demands specialized equipment and expertise. This can increase production time and costs, limiting scalability.
Another limitation is the availability of raw materials. Many high-temperature alloys rely on rare metals, making supply chain stability a concern. This can lead to fluctuations in cost and availability.
Alternative materials and technologies further complicate the landscape. While high-temperature alloys offer unparalleled performance, advancements in ceramics and composites present competitive options in certain applications.
Understanding these challenges is essential for making informed decisions. By addressing cost, manufacturing, and material availability, industries can better leverage the benefits of high-temperature alloy casting while mitigating its limitations.
Trends in High-Temperature Alloy Casting
The field of high-temperature alloy casting is evolving rapidly, driven by technological advancements and market demands. Artificial intelligence and machine learning are being integrated into the casting process, optimizing design and reducing defects. These innovations enhance efficiency and product quality.
Sustainability is another key trend. Researchers are developing eco-friendly alloys that reduce environmental impact without compromising performance. This aligns with global efforts to achieve greener manufacturing practices.
Additive manufacturing is transforming how high-temperature alloys are utilized. 3D printing allows for greater customization and complexity, opening new possibilities in aerospace, automotive, and medical applications. This technology also reduces waste, further supporting sustainability goals.
Global market growth reflects these trends. As industries recognize the value of high-temperature alloys, investment in research and development continues to rise. Emerging markets are also contributing to the expansion, driving innovation and competition.
By staying ahead of these trends, industries can harness the full potential of high-temperature alloy casting. The future promises exciting developments that will redefine what’s possible in manufacturing and engineering.
Choosing the Right Supplier
Selecting the right supplier is crucial for leveraging the benefits of high-temperature alloy casting. Key factors to consider include experience, technological capability, and certifications. A reliable supplier should demonstrate expertise in handling complex projects and delivering consistent quality.
Evaluating the supplier’s infrastructure is equally important. Advanced equipment and adherence to international standards ensure precision and reliability. This is particularly critical for industries like aerospace and medical technology, where even minor deviations can have significant consequences.
Cost transparency and after-sales support also play a role. A good supplier should offer competitive pricing without compromising quality and provide robust support for troubleshooting and maintenance.
Establishing a strong partnership with the right supplier can enhance production efficiency and product performance. It’s a decision that impacts not just immediate outcomes but long-term success as well.
Conclusion
High-temperature alloy casting is indispensable for industries requiring exceptional durability, precision, and thermal resistance. From aerospace to medical technology, these materials enable innovation and reliability in the most demanding environments. By understanding their applications, benefits, and challenges, businesses can make informed decisions to enhance performance and sustainability. For expert guidance or to explore cutting-edge solutions, reach out to professionals specializing in high-temperature alloy casting today.
FAQ
What temperatures can high-temperature alloys withstand?
They can endure temperatures exceeding 1,000°C, depending on the specific alloy and application.
How does high-temperature alloy casting differ from other methods?
It allows for greater precision and durability, particularly in complex geometries and extreme environments.
Is it cost-effective for small-scale projects?
The high initial cost may limit its viability for smaller projects, but the durability and reliability often offset the expense.
Can it be used in 3D printing?
Yes, additive manufacturing is increasingly leveraging high-temperature alloys for customized, complex designs.
What maintenance do components made of these alloys require?
Proper maintenance involves regular inspections and adherence to manufacturer guidelines to ensure long-term performance.