The Problem at Hand: Why Extreme Performance Environments Demand High-Temperature Alloys
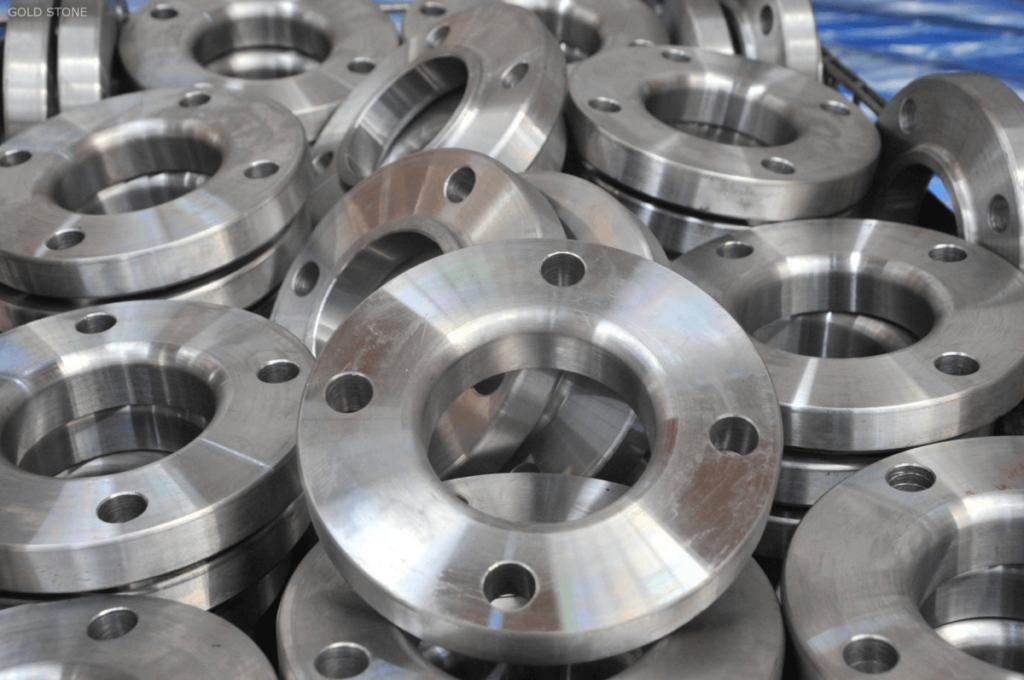
In environments where the stakes are high—like aerospace, energy production, or automotive industries—materials must endure not only extreme temperatures but also stress, corrosion, and wear. High-temperature alloys are engineered specifically for such conditions, offering unparalleled strength, resistance, and reliability. This article explores the top high-temperature alloys, diving deep into their properties, applications, and innovations that make them indispensable for modern engineering.
What Are High-Temperature Alloys?
Definition: Characteristics of High-Temperature Alloys
High-temperature alloys are specialized materials designed to perform in environments where temperatures soar above 500°C (932°F). These alloys consist of metals like nickel, cobalt, and iron, often combined with other elements to achieve superior properties. They are known for their remarkable strength, resistance to deformation, and ability to maintain structural integrity under thermal stress.
Key Properties: Strength, Thermal Stability, Oxidation Resistance
One defining characteristic of high-temperature alloys is their thermal stability. Unlike ordinary materials, these alloys resist softening or weakening at elevated temperatures, which is crucial in applications such as turbine engines. Oxidation resistance is another vital property, ensuring that the alloy forms a protective oxide layer rather than degrading over time. Furthermore, these alloys exhibit exceptional tensile strength and creep resistance, allowing them to handle sustained stress without permanent deformation.
Examples of High-Temperature Alloys
Nickel-based alloys like Inconel and Hastelloy dominate the field, prized for their high melting points and resistance to extreme environments. Cobalt-based alloys are also notable for their wear and corrosion resistance. Meanwhile, iron-based superalloys serve as cost-effective options for applications that don’t require the highest heat resistance.
Understanding these characteristics lays the foundation for exploring why high-temperature alloys are indispensable across industries.
Why Are High-Temperature Alloys Critical?
Applications Overview: Where Performance Meets Necessity
High-temperature alloys are critical in industries where failure can lead to catastrophic outcomes. In aerospace, these materials are used in jet engines, turbine blades, and exhaust systems, where temperatures can exceed 1,000°C (1,832°F). In power plants, they ensure the efficiency and safety of gas and steam turbines. Automotive manufacturers rely on these alloys in turbochargers and exhaust systems to withstand intense thermal cycling.
Performance Requirements: Beyond Heat Resistance
It’s not just heat resistance that makes these alloys vital. Their ability to handle mechanical stress and corrosive environments is equally important. For instance, in the energy sector, components must resist oxidation and wear while maintaining high strength over decades of use. Similarly, in nuclear reactors, materials face not only high temperatures but also radiation exposure, requiring a combination of toughness and radiation resistance.
Long-Term Reliability and Cost Efficiency
While high-temperature alloys are more expensive upfront, their durability and performance lead to long-term cost savings. By reducing maintenance, downtime, and failures, these materials prove to be invaluable investments. Their role in ensuring safety and efficiency makes them irreplaceable in high-stakes applications.
Key Factors in Selecting High-Temperature Alloys
Chemical Composition: The Role of Core Elements
The performance of a high-temperature alloy depends heavily on its chemical composition. Nickel, for instance, enhances heat resistance and corrosion protection. Cobalt adds wear resistance, making it ideal for high-stress applications like jet turbines. Iron-based alloys, though less heat-resistant, are more economical and suitable for moderately high temperatures.
Manufacturing Compatibility: Tailoring to Techniques
Selecting an alloy also depends on its compatibility with manufacturing processes. For example, nickel-based alloys are well-suited for casting and forging but can also be used in additive manufacturing, enabling precise, complex shapes. Advances in 3D printing have further expanded the possibilities, allowing engineers to design components with optimized weight and performance.
Balancing Cost and Performance
Not all applications require the highest-grade alloys. Cost-effective options, such as iron-based superalloys, can meet performance needs in less demanding environments. Understanding the specific requirements—such as temperature, load, and exposure conditions—helps engineers select the most appropriate and economical material.
Overview of Leading High-Temperature Alloy Families
Nickel-Based Alloys: Dominating the Field
Nickel-based alloys, such as Inconel, are the gold standard for high-temperature applications. These materials offer unmatched thermal stability and are often used in jet engines and power plants. Hastelloy, another nickel-based alloy, excels in resisting both high temperatures and corrosive environments.
Cobalt-Based Alloys: For Extreme Wear and Corrosion Resistance
Cobalt-based alloys like Stellite are renowned for their wear and corrosion resistance. These materials are ideal for medical implants and cutting tools, where longevity under stress is paramount. Their ability to maintain strength at elevated temperatures makes them indispensable in aerospace and energy applications.
Iron-Based Superalloys: Affordable Alternatives
Iron-based superalloys, such as stainless steels, provide a balance between cost and performance. While they may not match the heat resistance of nickel or cobalt alloys, they are widely used in less extreme environments, such as automotive components and industrial machinery.
The Science Behind High-Temperature Resistance
Material Science Principles: Phase Stability and Grain Boundaries
High-temperature alloys owe their properties to advanced material science. Phase stability ensures that the alloy maintains its structure under thermal stress, while carefully engineered grain boundaries enhance creep resistance. These factors prevent deformation and failure over prolonged use.
Heat Treatment Processes: Enhancing Microstructural Properties
Heat treatment is a crucial step in optimizing high-temperature alloys. Techniques like solution annealing and precipitation hardening fine-tune the material’s microstructure, improving strength and thermal stability. These processes allow manufacturers to tailor alloys for specific performance needs.
Understanding these scientific principles is key to unlocking the full potential of high-temperature alloys in engineering applications.
Aerospace Industry: Pushing the Limits
Jet Turbines: Where High-Temperature Alloys Shine
In aerospace, jet turbines represent the pinnacle of engineering where high-temperature alloys are indispensable. Turbine blades, often made from nickel-based superalloys like Inconel, operate in environments exceeding 1,200°C (2,192°F). These alloys resist thermal fatigue, oxidation, and creep, ensuring safety and performance. Additionally, single-crystal superalloys eliminate grain boundaries, significantly enhancing high-temperature durability and efficiency.
Spacecraft Applications: Beyond Earth’s Atmosphere
Spacecraft components demand materials that endure extreme heat during atmospheric reentry and freezing temperatures in space. High-temperature alloys, such as those used in thermal protection systems and engine nozzles, provide the required strength and thermal stability. Innovations like cobalt-based alloys in rocket propulsion systems further highlight their versatility in handling extreme thermal cycles.
Challenges and Innovations in Aerospace Alloys
The aerospace sector continuously pushes the boundaries of alloy technology. Lightweight, high-strength alloys are critical for improving fuel efficiency and payload capacities. Research into novel materials, including oxide dispersion-strengthened (ODS) alloys, aims to enhance thermal resistance and reduce weight, meeting the ever-growing demands of modern aviation and space exploration.
Automotive Applications
Turbochargers: Managing Intense Thermal Cycles
Turbochargers in internal combustion engines represent a prime example of high-temperature alloy use in automotive engineering. These components face rapid temperature fluctuations, often exceeding 1,000°C (1,832°F). Nickel-based alloys provide the heat resistance necessary to prevent deformation and maintain efficiency. Their ability to withstand oxidation ensures longevity, even in high-performance vehicles.
Electric Vehicles: A New Frontier for High-Temperature Alloys
The rise of electric vehicles (EVs) introduces new applications for high-temperature alloys. Electric motors and battery packs generate significant heat during operation. Cobalt-based alloys play a critical role in thermal management systems, while nickel-based alloys are employed in battery connections and structural components, enhancing durability and safety.
Balancing Performance and Cost in the Automotive Industry
Automakers constantly seek ways to balance performance with cost-effectiveness. Advances in alloy production techniques, such as powder metallurgy, enable the creation of cost-efficient yet high-performing materials. As the industry shifts towards sustainability, recyclable high-temperature alloys are gaining traction, reducing environmental impact without compromising performance.
Energy Sector
Nuclear Power Plants: Unyielding Under Radiation and Heat
Nuclear reactors pose unique challenges, requiring materials that can withstand intense radiation and temperatures above 700°C (1,292°F). Alloys like Incoloy and Hastelloy provide exceptional radiation resistance and maintain structural integrity over decades of operation. Their role in reactor pressure vessels and heat exchangers underscores their critical importance in the energy sector.
Oil and Gas: Withstanding High-Stress Environments
In the oil and gas industry, high-temperature alloys are vital for drilling, refining, and transport operations. Cobalt-based alloys, with their superior wear and corrosion resistance, are used in drill bits and valves. Meanwhile, nickel-based alloys ensure durability in refinery furnaces and pipelines, where extreme heat and corrosive substances are commonplace.
Renewable Energy: Expanding the Role of High-Temperature Alloys
As renewable energy gains momentum, high-temperature alloys are finding applications in solar thermal plants and wind turbines. These materials enhance efficiency and reliability, enabling renewable technologies to compete with traditional energy sources. Innovations in high-temperature alloys will be instrumental in achieving global sustainability goals.
Medical Applications
Prosthetics and Implants: Meeting Rigorous Demands
In the medical field, high-temperature alloys are not just about heat resistance but also biocompatibility and longevity. Cobalt-chromium alloys, for example, are widely used in joint implants and dental prosthetics. These materials endure repeated sterilization cycles without degrading, ensuring safety and durability for patients.
Heat-Resistant Surgical Tools
Surgical tools made from high-temperature alloys can withstand the intense heat of autoclave sterilization. Nickel-based alloys are particularly valued for their resistance to corrosion and wear, making them ideal for precision instruments that require long-term reliability.
Innovations in Medical Alloys
The development of additive manufacturing techniques has revolutionized the medical industry. High-temperature alloys can now be 3D-printed into custom implants, perfectly tailored to individual patients. These innovations not only improve patient outcomes but also expand the possibilities of high-temperature alloys in healthcare.
Emerging Innovations
3D Printing with High-Temperature Alloys
Additive manufacturing has unlocked new potentials for high-temperature alloys. Complex geometries, previously unattainable through traditional methods, can now be achieved with 3D printing. This technology enables lighter, stronger components for aerospace, automotive, and energy applications.
Advanced Coatings: Enhancing Surface Properties
To further extend the lifespan of high-temperature alloys, advanced coatings are being developed. Thermal barrier coatings (TBCs), for instance, protect turbine blades from extreme heat and oxidation, allowing them to operate at higher temperatures and efficiencies.
Future Developments: Beyond Current Alloys
Research into high-entropy alloys and refractory metal composites promises even greater thermal and mechanical performance. These next-generation materials could redefine the limits of high-temperature applications, paving the way for breakthroughs in engineering and technology.
Key Industry Challenges
Corrosion and Oxidation: Continuous Threats
Despite their impressive properties, high-temperature alloys are not immune to challenges. Prolonged exposure to high temperatures can lead to oxidation, which degrades material integrity. Alloy coatings and proper maintenance are crucial to mitigating these effects.
Sustainability and Recycling
The production of high-temperature alloys involves significant energy and resource consumption. Recycling these materials poses a challenge, as maintaining their high-quality properties is difficult. However, advancements in recycling technologies offer hope for more sustainable practices.
Cost vs. Performance Dilemmas
High-performance alloys often come with a hefty price tag, limiting their accessibility. Balancing cost with performance remains an ongoing challenge, especially in industries with tight budget constraints. Collaborative research between manufacturers and industries is critical to overcoming these barriers.
Best Practices for Alloy Maintenance
Inspection Techniques: Ensuring Structural Integrity
Regular inspections are essential for detecting early signs of wear, corrosion, or deformation in high-temperature alloys. Techniques such as ultrasonic testing and thermal imaging provide valuable insights into the health of components, preventing catastrophic failures.
Repair and Coating Methods
Surface treatments like thermal spraying and laser cladding can extend the lifespan of high-temperature alloys. These methods restore damaged components, reducing the need for costly replacements and ensuring consistent performance in demanding environments.
Preventive Maintenance: A Proactive Approach
Implementing a robust maintenance schedule minimizes the risk of unexpected failures. Regular cleaning, proper storage, and adherence to operational guidelines are simple yet effective measures to maintain the longevity of high-temperature alloys.
FAQs and Common Myths
Are High-Temperature Alloys Corrosion-Proof?
While highly resistant, high-temperature alloys are not completely immune to corrosion. Their performance depends on the environment and the presence of protective coatings.
How Do High-Temperature Alloys Compare to Ceramics?
Ceramics excel in heat resistance but lack the mechanical strength and toughness of high-temperature alloys, making the latter more versatile in engineering applications.
Can High-Temperature Alloys Be Recycled?
Yes, but the process is complex and often involves a loss in quality. Ongoing advancements aim to make recycling more efficient and sustainable.
Comparison Chart
Alloy Type | Max Temp (°C) | Key Properties | Common Applications |
---|---|---|---|
Nickel-Based Alloys | 1,200+ | High strength, corrosion resistance | Jet engines, power turbines |
Cobalt-Based Alloys | 1,150 | Wear resistance, biocompatibility | Medical implants, cutting tools |
Iron-Based Alloys | 800-1,000 | Cost-effective, versatile | Automotive components, industrial use |
Conclusion
High-temperature alloys are the backbone of modern engineering, enabling advancements in aerospace, automotive, energy, and medical industries. Their unique properties make them indispensable for extreme environments, ensuring safety, efficiency, and reliability. As innovations continue to expand their capabilities, high-temperature alloys will remain pivotal in shaping the future of technology.
FAQ Section
What are the most heat-resistant alloys available today?
Nickel-based superalloys like Inconel and Hastelloy are among the most heat-resistant, withstanding temperatures above 1,200°C.
Which industries rely most on high-temperature alloys?
Aerospace, energy, automotive, and medical industries are the primary users due to their demanding performance requirements.
How does alloy selection impact product lifecycle costs?
Using the right high-temperature alloy can reduce maintenance and replacement costs, offering long-term savings despite higher initial investment.