1. Introduction: Why High-Temperature Alloys Matter
Defining Advanced High-Temperature Alloys
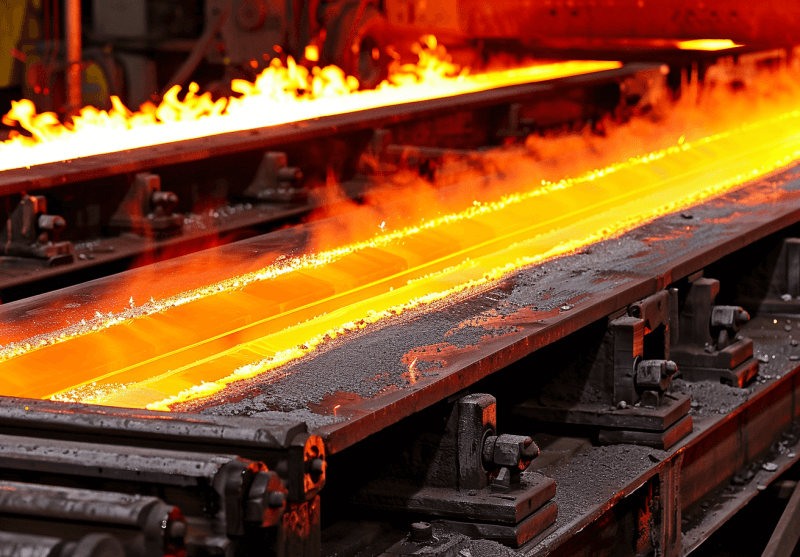
Advanced high-temperature alloys represent specialized metal formulations engineered for intense heat. They maintain structural integrity when temperatures soar. Their compositions enable remarkable strength, corrosion resistance, and dimensional stability.
The Core Purpose and Value
These alloys matter because they help critical projects run longer and more efficiently. Industries facing harsh thermal conditions need materials that will not buckle under stress. By relying on these alloys, projects that deal with turbines, combustion systems, or power plants enjoy fewer breakdowns and longer maintenance intervals. Ultimately, their real value lies in improved reliability, reduced downtime, and greater overall performance.
2. Understanding the Basics of High-Temperature Alloys
What Defines a High-Temperature Alloy?
High-temperature alloys stand apart because they resist extreme thermal environments that would weaken ordinary materials. When conventional steels soften, warp, or corrode, these specialized alloys continue performing. They often combine nickel, cobalt, or iron matrices with elements like chromium or aluminum. Together these blends deliver strength and resilience over wide temperature ranges. By understanding these compositions, engineers and managers can anticipate how materials behave and plan accordingly.
Differentiating from Common Materials
Unlike conventional metals, advanced high-temperature alloys handle punishing conditions with minimal degradation. Where standard steel loses shape under prolonged heat, these specialized alloys hold their form. Resistance to oxidation prevents surfaces from flaking or weakening, ensuring parts last longer. Corrosion resistance further guards key components, helping them withstand moisture, chemicals, and varying operational stresses that would cripple lesser metals.
Tailored for Specialized Applications
High-temperature alloys provide a perfect fit for environments demanding absolute consistency. In fields like aerospace, automotive, or energy, machinery often functions at temperatures that push ordinary metals beyond their limits. By selecting the right alloy grades, engineers sidestep failures related to overheating, brittleness, or distortion. The result is more dependable equipment, smoother operations, and improved safety margins.
Meeting Stringent Industry Standards
The metal industry develops these alloys to conform to stringent performance benchmarks. Their properties undergo rigorous laboratory testing before adoption. Manufacturers issue detailed datasheets outlining mechanical strength, creep resistance, and thermal stability. Engineers rely on these documents when selecting materials. This standardized approach ensures that when a buyer specifies an advanced high-temperature alloy, they receive a product meeting predictable, repeatable, and quantifiable performance criteria.
Enhancing Project Longevity and Efficiency
Ultimately, understanding the basics sets the foundation. By grasping what these alloys are, how they differ, and why they excel under heat, decision-makers gain confidence. They know these alloys can withstand critical loads without succumbing to deformation. By investing time in learning fundamental properties, buyers ensure the chosen material aligns with their operational goals. Such informed decisions lead directly to projects that run longer, demand fewer repairs, and achieve more stable results.
3. Key Properties that Make High-Temperature Alloys Stand Out
Heat Resistance Under Stress
One standout characteristic is the remarkable ability to maintain mechanical integrity when subjected to extreme temperatures. While ordinary materials lose hardness or melt, advanced alloys retain tensile strength and rigidity. This stability ensures components keep working under intense operational heat. When a turbine blade spins at blistering speeds in a furnace-like chamber, these alloys preserve critical shape and precision.
Corrosion and Oxidation Shield
Another hallmark is how well these alloys resist corrosion and oxidation. Heat often accelerates chemical reactions, leaving less robust metals riddled with pits or weakened by oxide layers. By contrast, high-temperature alloys have compositions that form stable protective films, effectively sealing surfaces against chemical attack. This resilience reduces the frequency of replacements and prolongs service life.
Enhanced Mechanical Strength
High-temperature alloys also exhibit formidable mechanical strength. Even when heavily stressed and heated, they hold up over extended periods. Their robust crystal structures, carefully engineered grain boundaries, and precise elemental distributions add up to parts that remain strong when exposed to fluctuating loads. This strength under challenging conditions means equipment can be pushed further without risking catastrophic failure.
Fatigue Life and Creep Resistance
Long-term stability is crucial. Components often operate continuously at elevated temperatures. Over time, normal metals creep or deform. High-temperature alloys, however, are designed to resist such slow deformation. They maintain dimensional accuracy, ensuring critical tolerances remain intact. With reduced creep and higher fatigue life, machines run more reliably, facing fewer unplanned outages.
Balanced Thermal Conductivity
Some alloys effectively manage heat flow, distributing thermal loads more evenly. Balanced conductivity helps prevent localized hot spots. Without these troublesome areas, equipment experiences less thermal stress. Controlled heat flow reduces chances of cracks or microscopic faults forming over time. Project managers appreciate these features since they translate to predictable performance, extended intervals between overhauls, and fewer emergency repairs.
Stable Microstructure at Elevated Temperatures
High-temperature alloys maintain stable microstructures even when hot. Instead of grain boundaries weakening or precipitates dissolving, they remain intact. This stability ensures consistent mechanical behavior throughout the alloy’s life cycle. Reliable structures translate directly into machines that perform their intended functions hour after hour, shift after shift, without the worrisome drift in properties often seen with less specialized materials.
4. Industries and Applications: Where High-Temperature Alloys Shine
Aerospace Engineering and Turbine Technology
Aerospace turbines spin in unimaginable heat, pushing engines to their design limits. High-temperature alloys ensure blades retain shape and strength. They keep jet engines efficient, reduce maintenance intervals, and enhance flight safety. These alloys enable parts like turbine disks, combustor liners, and exhaust nozzles to survive extended operational cycles.
Power Generation and Energy Sector
In power plants, gas turbines and boiler tubes face relentless thermal and mechanical stress. High-temperature alloys ensure critical components endure massive temperature gradients without failing. This reliability translates into consistent power output, fewer shutdowns, and longer operational life. As energy producers seek higher efficiency and lower emissions, these alloys become the backbone of their improvements.
Automotive Performance Enhancements
Advanced engines and turbochargers rely on these alloys to handle the intense heat of combustion. By using high-temperature alloys in exhaust manifolds or turbocharger housings, automotive manufacturers improve engine efficiency. Reduced thermal fatigue means less downtime and improved reliability, allowing for vehicles that run cooler, produce more consistent power, and require less intensive servicing.
Oil, Gas, and Petrochemical Equipment
Refineries, drilling platforms, and petrochemical processing plants confront harsh conditions. Superheated fluids, corrosive media, and constant mechanical loads demand robust materials. High-temperature alloys meet these demands, ensuring pumps, valves, and piping maintain structural integrity. Operators appreciate how these materials reduce the frequency of part replacements and help mitigate costly, unexpected failures.
Chemical Processing and Beyond
Even outside traditional heavy industries, any sector dealing with elevated temperatures benefits. Chemical processing, furnaces, medical sterilization equipment, or advanced manufacturing lines rely on alloys that keep their shape and strength under punishing heat. The uniform performance and corrosion resistance reduce maintenance cycles, keep quality consistent, and help businesses maintain profit margins.
Ensuring Competitive Edges Across Industries
By integrating high-temperature alloys, enterprises stay ahead. They can design systems that operate at higher temperatures for improved efficiency or produce better-quality goods in shorter timeframes. This versatility and adaptability let companies respond to evolving market demands. Whether it’s making cleaner power, faster jets, or more durable manufacturing equipment, high-temperature alloys empower projects to reach goals once considered impossible.
5. Selecting the Right Alloy for Your Project
Assessing Operational Conditions
Choosing the right alloy starts with knowing your project’s precise demands. Consider temperature ranges, mechanical loads, and exposure to corrosive agents. Will the material face steady high heat or fluctuating spikes? By clarifying operating conditions, you narrow the candidate list. Careful examination of datasheets and consultation with metallurgists helps match the alloy’s capabilities to the project’s realities.
Material Expertise and Professional Guidance
Don’t tackle selection alone. Professionals with metallurgical backgrounds can assess subtle differences between alloys. They understand complex trade-offs: one alloy excels in extreme temperatures, another offers better oxidation resistance. Tapping expert knowledge ensures fewer surprises down the line. Their input can reveal overlooked factors, like how certain elements improve weldability or alter long-term maintenance schedules.
Testing, Validation, and Pilot Runs
Before full-scale implementation, consider small pilot trials. Test candidate alloys in controlled conditions. Evaluate wear, corrosion, and mechanical properties after simulating real operational cycles. Such experiments validate your choice, ensuring that when you scale up, you do so confidently. These tests also guide design tweaks that optimize performance.
Balancing Costs and ROI
Advanced alloys may command a higher initial price. Yet, weighing upfront expense against long-term savings often justifies the investment. Durable materials reduce frequent part replacements, minimize downtime, and improve overall equipment efficiency. By calculating life-cycle costs, managers see that a slightly higher procurement cost pales compared to the reduction in maintenance, repairs, and lost production time.
Negotiating Supply Chain Reliability
Even if you find the perfect alloy, you must ensure stable supply. Confirm supplier credibility, lead times, and inventory practices. A reliable source keeps your production schedule intact. Securing consistent material availability prevents expensive last-minute substitutions or project delays. Successful sourcing strategies align supply reliability with the chosen alloy’s technical merits, delivering a smoother path toward project success.
6. Composition and Microstructure: The Science Behind the Alloys
Elemental Contributions
High-temperature alloys gain their properties from a carefully chosen blend of elements. Nickel imparts excellent strength at heat, chromium adds corrosion resistance, aluminum enhances oxidation stability. Each ingredient modifies microstructures, affecting how the alloy behaves when stressed or heated. Understanding these elemental roles helps engineers predict how materials respond to harsh conditions.
Microstructure: Grains, Phases, and Precipitates
Beneath the surface lies a tapestry of grains, boundaries, and microscopic phases. Stable microstructures resist transformation under thermal stress. Grain sizes affect strength, while carbide precipitates can block dislocations, improving creep resistance. Metallurgists tweak compositions and heat treatments so that the final alloy emerges with optimal grain structures. These microstructural features determine if components last hours or decades under relentless heat.
Tailored for Specific Applications
By adjusting alloy compositions, manufacturers produce variants optimized for niche applications. Need exceptional oxidation resistance at 1,000°C? Increase certain elements. Require a ductile alloy for intricate shapes? Adjust heat treatments. This customization ensures you get exactly what your project demands, avoiding compromises that lead to premature failure or performance dips.
Heat Treatment and Aging
The process does not end after casting. Controlled heating and cooling cycles, known as heat treatments, manipulate microstructures to achieve target properties. Aging treatments prompt specific precipitates to form, boosting strength or altering corrosion behavior. This tuning process guarantees alloys meet stringent specification requirements, giving engineers control over final mechanical and chemical properties.
Predictable Performance and Long-Term Stability
When every grain and precipitate is accounted for, materials behave predictably. Engineers can reliably forecast how an alloy will respond to thermal cycling, mechanical loads, or corrosive media. This predictability underpins safe design margins, allowing equipment to be pushed closer to operational limits. The result is machinery that not only survives intense conditions but thrives within them, producing consistent results and lowering operational risks.
7. Challenges in Working with High-Temperature Alloys
Machinability and Fabrication Hurdles
While their robust properties deliver performance benefits, high-temperature alloys are harder to machine and shape. Conventional cutting tools wear quickly, and welding requires specialized processes. Engineers must adapt fabrication methods, sometimes employing advanced tool materials, slower feed rates, or preheating steps. Although challenging, these measures ensure parts retain critical properties after manufacturing.
Supply Chain Complexities
High-temperature alloys often have more intricate supply chains. Raw materials may be sourced globally, adding logistical complexity. Lead times can be longer, and batch-to-batch consistency must be monitored. Without careful planning and reliable suppliers, unexpected delays can cascade into missed production deadlines. Overcoming these challenges requires strong supplier relationships and proactive inventory management.
Initial Cost Considerations
The sticker price of these alloys can be significantly higher than standard metals. Decision-makers might balk at initial costs. Yet the challenge lies in understanding long-term value. Early investments offset future losses by reducing part failures and maintenance overhead. Explaining the return on investment to stakeholders helps secure buy-in despite the higher upfront expense.
Ensuring Operator Proficiency
Technicians and fabricators must learn specialized handling procedures. Lack of skill can compromise final part quality. Training and equipment upgrades help navigate these complexities. Investing in operator expertise lowers scrap rates, ensures safe handling, and maintains the alloy’s integrity through each production step.
Balancing Performance with Practicality
Designers must weigh increased performance against practical constraints. If an alloy’s machinability proves too difficult, or if its supply chain strains lead times, another suitable option might be needed. The challenge involves finding a sweet spot that aligns with both technical demands and project realities. Skilled decision-making and a willingness to consider trade-offs ensure a balanced, feasible solution that still harnesses many of these alloys’ advantages.
8. Solutions and Best Practices for Handling These Alloys
Advanced Machining Techniques
To tame these tough materials, professionals rely on specialized cutting tools and coatings that withstand extreme hardness. High-pressure coolant systems, precision machining centers, and well-optimized tool paths reduce tool wear. The result is cleaner cuts, fewer defects, and a production line that keeps pace with schedule demands.
Skilled Welding and Joining Methods
Welding advanced alloys involves careful control of heat input, filler materials, and post-weld treatments. Operators must follow precise procedures, often informed by supplier recommendations or engineering handbooks. With correct welding techniques, joints remain strong and corrosion-resistant. This ensures assemblies stay intact under high-temperature conditions.
Partnering with Knowledgeable Suppliers
Choosing an experienced supplier can streamline everything. Reputable vendors advise on material selection, share machining tips, and troubleshoot unexpected issues. They maintain quality control systems that guarantee consistent alloy batches. A strong supplier relationship means a stable supply of materials and immediate technical support when the unexpected arises.
Quality Assurance and Non-Destructive Testing
Regular inspections confirm parts meet design standards. Techniques like ultrasonic testing, X-ray imaging, or eddy current inspections uncover hidden flaws. By identifying issues early, teams correct them before catastrophic failures occur. Sustained quality assurance programs maintain confidence, ensure parts perform as promised, and help extend component life.
Training and Continuous Improvement
Investing in operator education pays off. Skilled staff understand alloy behavior and adjust their work accordingly. Training sessions, workshops, and documentation empower the workforce. Continuous improvement cycles—where lessons learned inform future projects—lead to better handling methods, lower defect rates, and long-term gains in productivity. Over time, what once posed formidable challenges becomes routine, predictable, and manageable.
9. Integrating High-Temperature Alloys Into Existing Systems
Evaluating Compatibility and Retrofits
Before upgrading established equipment, engineers must determine compatibility. Can existing housings, couplings, or seals handle the new alloy’s properties? Will dimensional changes be needed? By running simulations or small-scale tests, teams confirm that retrofitting won’t introduce unforeseen issues. Proper planning ensures a smooth transition that enhances rather than disrupts operations.
Adjusting Manufacturing Processes
Incorporating advanced alloys might demand tweaks to production lines. Machine tools need reconfiguration; operators require training in new cutting techniques. Scheduling changes ensure that machining processes align with complex fabrication steps. Though initially challenging, these adaptations pay dividends over time. Once settled, the new processes become second nature, stabilizing quality and productivity.
Aligning with Industry Standards
Adherence to recognized standards and certifications sets a baseline for performance. Complying with norms like ASME or ASTM instills confidence in customers and regulatory bodies. It assures everyone that upgraded components meet proven benchmarks. Standardized alloy grades and documented testing protocols simplify integration. They also provide a common language, making it easier to communicate expectations across supply chains.
Communication Between Teams
Implementing new materials involves collaboration across departments. Engineers, procurement specialists, maintenance crews, and quality assurance teams all play roles. Transparent communication ensures everyone understands why the change is happening, what benefits it brings, and how their work might evolve. Unified teamwork prevents silos and ensures a smoother adoption period.
Achieving Long-Term Operational Gains
Once integrated, high-temperature alloys deliver their full benefits. Equipment runs more efficiently with fewer breakdowns. Operators notice improved reliability and confidence grows in system performance. As production stabilizes and maintenance intervals stretch, companies realize tangible value. Over time, the decision to integrate these alloys proves a cornerstone of ongoing project optimization and competitiveness.
10. Real-World Case Studies and Success Stories
Aerospace Turbine Efficiency Gains
In one aerospace project, engineers replaced standard steel turbine blades with nickel-based high-temperature alloys. The result? Extended blade life, reduced maintenance intervals, and improved fuel efficiency. The upgrade allowed the engine to operate closer to its design limits without sacrificing reliability. Fewer unexpected stoppages cut operational costs and boosted customer satisfaction.
Power Plant Longevity
A power generation facility swapped conventional heat-resistant steels with advanced alloys in boiler tubes. Operating temperatures rose without tube failures. Downtime plummeted as routine inspections found fewer cracks. This improved the plant’s output and bottom line. The alloys’ corrosion resistance also minimized scaling, reducing cleaning expenses. Over time, these changes justified the initial investment.
Automotive Turbochargers That Last
A leading automotive manufacturer experimented with high-temperature alloys in turbocharger housings. Traditional materials struggled with the relentless heat of exhaust gases. After switching, turbochargers retained shape and strength longer, improving engine response. Customers enjoyed vehicles with fewer performance issues and longer service intervals. Word spread, enhancing the brand’s reputation.
Oil and Gas Reliability
A refinery integrated cobalt-based alloys into critical valve assemblies. Despite exposure to corrosive fluids and scorching conditions, valves remained functional well past their expected service life. Reduced part replacements and lower downtime made project schedules more predictable. This reliability earned client trust and set the stage for wider alloy adoption throughout the facility.
Cross-Industry Validation
These success stories show that advanced alloys do more than survive harsh environments—they thrive. Whether refining oil, powering turbines, or propelling aircraft, their durability and stability translate into real business value. Over time, these examples encourage other companies to follow suit, recognizing that advanced high-temperature alloys are not just engineering curiosities but practical tools for sustained competitive advantage.
11. The Role of Research and Development in Alloy Innovation
Ongoing Material Science Advances
Materials scientists continually push boundaries. They experiment with new element combinations, refining alloy recipes for even greater heat tolerance. This research aims for lighter yet stronger alloys capable of handling unprecedented temperature extremes. Such advances create a steady pipeline of improved materials, ensuring future projects benefit from cutting-edge technology.
Collaborative Efforts in Innovation
Academic labs, industry consortia, and research institutes often collaborate. Sharing knowledge speeds innovation. Researchers pool data, test new alloys in pilot programs, and distribute findings. Companies save time and resources by tapping into this shared pool of expertise. Collaborative frameworks also encourage standardization, making it easier for industries worldwide to adopt new materials.
Computational Modeling and Predictive Tools
Modern R\&D relies on sophisticated modeling techniques. Computers simulate alloy behavior at atomic scales, predicting outcomes before actual testing. This accelerates the discovery process, guiding researchers toward promising formulations. Predictive modeling reduces trial-and-error costs, ensuring that by the time alloys reach the market, they’re already fine-tuned for performance.
Sustainable and Eco-Friendly Innovations
As environmental concerns grow, R\&D efforts also focus on sustainability. Researchers seek alloys that meet performance goals while using fewer scarce elements or reducing energy-intensive manufacturing steps. Minimizing environmental impact broadens these alloys’ appeal. Over time, innovations result in greener production chains, aligning high-temperature alloys with global eco-friendly directives.
Setting Future Standards
Emerging alloys eventually shape future industry standards. As more facilities adopt next-generation materials, benchmarks shift. What was once considered extraordinary performance becomes the new normal. Companies that monitor and adopt R\&D findings maintain competitive edges and continuously improve their operational results. Ultimately, research and development guide high-temperature alloys toward fresh frontiers of utility and efficiency.
12. Evaluating Suppliers and Partnering for Success
Criteria for Selecting Reliable Suppliers
When scouting suppliers, look beyond price. Check their certifications, technical expertise, and track record. Trusted suppliers must consistently provide alloys within required specifications. They should have a documented history of quality assurance and a willingness to share material data. This transparency builds a solid foundation for long-term cooperation.
Communication and Technical Support
The best suppliers act as partners. They answer questions promptly, help troubleshoot unexpected issues, and offer guidance. Good communication bridges knowledge gaps, ensuring you understand material properties and fabrication guidelines. A responsive supplier makes the difference between a smooth alloy integration and a frustrating experience.
Auditing Facilities and Verifying Standards
Visiting supplier facilities or reviewing audit reports verifies their claims. Inspecting production lines, quality control procedures, and inventory management practices reveals their operational maturity. Certified suppliers often maintain strict quality management systems like ISO 9001, which confirm their capabilities. Such diligence reassures that when you place an order, you receive top-grade alloys.
Negotiating Contract Terms
Long-term partnerships often involve negotiating favorable pricing or guaranteed delivery timelines. Establishing clear terms helps prevent misunderstandings. Locking in stable supply agreements ensures consistent project progress. As trust builds, suppliers may offer priority access to new alloys, early samples, or custom formulations tuned exactly to your specifications.
Strategic Relationships for Ongoing Improvement
When both parties collaborate closely, everyone benefits. Suppliers gain insights into customer needs, guiding product development. Clients gain early access to new materials and timely technical advice. Over time, these relationships evolve into strategic alliances that drive improvements, enhance product quality, and secure competitive advantages in complex markets.
13. Life Cycle Considerations: Maintenance, Inspection, and Repair
Proactive Maintenance and Scheduled Inspections
Even the toughest alloys require supervision. Scheduling regular inspections ensures parts haven’t developed microcracks or surface defects. By detecting issues early, you prevent costly breakdowns. Maintenance crews replace worn components before failures occur, minimizing downtime. Over time, proactive attention saves money and keeps operations flowing steadily.
Non-Destructive Testing Methods
Techniques like ultrasonic testing or radiography reveal hidden flaws without damaging parts. By scanning components at intervals, technicians gather data on wear rates. This feedback shapes maintenance schedules and guides decisions on when to repair or replace. A data-driven approach builds confidence in asset longevity and ensures equipment remains reliable.
Balancing Repairs and Replacements
Sometimes, minor defects can be repaired rather than scrapping entire parts. Skilled technicians can weld cracks or restore worn surfaces. However, if damage extends too far, replacing the component may be wiser. Judicious repair strategies minimize waste and expense. Understanding when repairs suffice versus when replacements are essential ensures operational continuity.
Extending Service Life and ROI
Careful life cycle management prolongs component service life. By employing advanced alloys, you start with a higher baseline quality. With proper maintenance, these parts last even longer. This extended lifespan improves return on investment. Businesses find themselves scheduling fewer emergency repairs and benefiting from steadier, more predictable operations.
Continual Improvement Cycles
Feedback loops close the circle. Lessons learned from inspections inform future material choices. If certain areas consistently show wear, engineers may select an alloy variant better suited for that environment. Over time, continuous refinements lead to components that not only last longer but also cost less in terms of downtime and repairs. Ultimately, managing life cycles with care amplifies the advantages advanced alloys bring.
14. Cost-Benefit Analysis and ROI for Using High-Temperature Alloys
Calculating Total Life Cycle Costs
A straightforward cost comparison may mislead. Although advanced alloys cost more upfront, consider downstream savings. Fewer part failures mean reduced downtime. Lower maintenance frequencies cut labor and repair bills. Improved efficiency can raise production outputs. By summing these gains over the component’s lifespan, managers often find the high upfront price pays for itself multiple times.
Justifying the Investment to Stakeholders
Not everyone immediately sees the value. Presenting a well-prepared cost-benefit analysis helps secure stakeholder approval. Charts comparing alternative materials highlight fewer repairs, extended equipment life, and better operational stability. By framing these metrics as measurable returns, decision-makers understand that investing in high-temperature alloys represents sound financial strategy.
Quantifying Improvements and Savings
Precise data strengthens the case. Track maintenance hours saved, replacement cycles avoided, and performance boosts achieved. This quantitative evidence demonstrates how advanced alloys contribute to profitability. Over time, these metrics accumulate into compelling proof. Numbers give credibility, reinforcing the idea that these materials yield tangible benefits, not just theoretical gains.
Long-Term Competitive Advantage
Securing better materials helps businesses outpace competitors still using subpar metals. By running equipment at higher temperatures or pushing operational boundaries, companies produce more output with less downtime. This translates into market advantages, as customers prefer reliable suppliers who deliver consistently. Over time, enhanced reputation and customer loyalty yield even greater returns.
Informed Strategic Decisions
Armed with a thorough ROI calculation, leaders approach future projects more confidently. They know that paying extra for advanced alloys sets the stage for durability and reduced headaches. This foresight shapes procurement strategies, encourages innovation, and leads enterprises toward sustainable growth. Over multiple project cycles, investing in quality materials establishes a track record of steady performance and financial stability.
15. Conclusion and Next Steps
Embracing Next-Generation Materials
In today’s competitive environment, advanced high-temperature alloys offer a golden opportunity. Projects that integrate these materials reap benefits in reliability, efficiency, and lifespan. Managers who commit realize fewer maintenance surprises and smoother schedules. This investment transforms how teams approach thermal challenges, raising performance bars and meeting or exceeding demanding project goals.
Consulting Experts and Starting Trials
For readers considering a shift, consulting material specialists or partnering with seasoned suppliers can streamline transitions. Running pilot tests confirms that the chosen alloy aligns perfectly with operational needs. This proactive approach sets the stage for seamless integration, fostering confidence in long-term results. Making incremental changes can yield lasting positive impacts.
FAQ
Q: Are advanced high-temperature alloys suitable for only extreme applications?
A: While they excel in very hot conditions, even moderate environments benefit from their durability and stability.
Q: How can I confirm the right alloy choice?
A: Study datasheets, consult experts, and consider small-scale tests. This ensures that the selected alloy meets exact requirements.
Q: Will these alloys dramatically raise project costs?
A: Initially they may cost more, but long-term savings in downtime, maintenance, and efficiency often outweigh the upfront expense.
Q: Can I retrofit current equipment with these materials?
A: Yes, but careful planning and testing help ensure compatibility. Adjusting fabrication processes and consulting specialists prevents issues.
Q: Do suppliers offer technical support?
A: Reputable suppliers provide guidance, answer questions, and help ensure that chosen alloys meet your project’s unique challenges.