Introduction to High-Temperature Alloys
Understanding What Makes These Materials Special
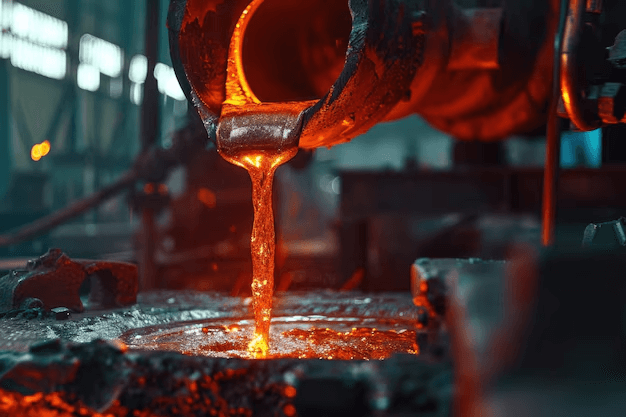
When industries push equipment beyond ordinary limits, many metals struggle to remain stable and reliable. Operations in aerospace turbines, power generation systems, and automotive performance components demand materials that can handle punishing thermal extremes without faltering. Ordinary metals, even those considered robust at moderate temperatures, tend to lose strength, warp, or corrode when exposed to sustained high-heat environments. This can lead to sudden downtime, costly repairs, and safety risks.
Here’s the deal: Proven high-temperature alloys address these challenges head-on. Their specialized compositions, featuring nickel, cobalt, and other heat-resistant elements, create a rugged solution that remains strong and dimensionally stable even at temperatures that would overwhelm standard metals. Choosing these alloys means investing in components that won’t buckle under relentless thermal stress. This choice ultimately enhances operational consistency, reduces unexpected maintenance costs, and boosts overall productivity.
You might be wondering: Why not just reinforce cheaper metals or rely on coatings? The truth is, when conditions demand extreme durability, few alternatives match the endurance and reliability of proven high-temperature alloys. In applications where every minute of downtime cuts into profits, opting for these advanced materials is a strategic move. They deliver peace of mind and allow technicians, managers, and decision-makers to focus on innovation instead of repairs and replacements.
What Are High-Temperature Alloys?
Defining the Core Concepts
High-temperature alloys represent a category of engineered metals designed to perform consistently in environments that approach or exceed the limits of conventional materials. Their compositions typically rely on high concentrations of nickel, cobalt, or iron, along with carefully chosen alloying elements that enhance resistance to heat-induced deformation, corrosion, and oxidation. These specialized mixtures transform ordinary metals into resilient performers that thrive under punishing conditions.
Let’s get real: When your operations involve sustained exposure to temperatures exceeding hundreds of degrees Celsius, ordinary alloys just can’t keep up. High-temperature alloys stand out by maintaining tensile strength, resisting thermal creep, and preserving structural stability. They’re not just about withstanding high temperatures, either. They also offer improved performance in aggressive chemical environments that would rapidly degrade less capable metals.
Typical Temperature Ranges and Key Elements
These alloys often see use in ranges of 600°C to over 1,000°C, conditions commonly found in turbine blades, chemical processing reactors, and advanced automotive engines. To achieve such extremes, their compositions may include elements like chromium for oxidation resistance, aluminum and titanium for precipitation hardening, and molybdenum or tungsten for strengthening.
Here’s the bottom line: At their core, high-temperature alloys are engineered for one purpose—delivering stable, long-lasting performance in conditions that push materials to their absolute limits. Their unique chemistries and metallurgical structures set them apart, making them invaluable resources in industries where failure is not an option. By understanding what these alloys are and what they’re made of, you’re better positioned to appreciate why choosing them can transform tough applications into reliable successes.
Why High-Temperature Alloys Matter in Tough Applications
Handling Extreme Operating Conditions
Industries that rely on equipment subject to extreme heat can’t afford guesswork. Turbines spinning thousands of revolutions per minute inside jet engines or power plants generate immense temperatures. High-speed friction, combustion, and pressure build-ups create a punishing environment that tests metals to their breaking points. Conventional materials, even high-grade steels, lose their strength rapidly as the heat soars.
Guess what: High-temperature alloys shine here because they’re purpose-built for these conditions. They deliver consistent mechanical properties and strength, enabling critical components to operate safely and efficiently. With the right alloy, you don’t just survive high temperatures—you thrive in them.
Reducing Failures and Downtime
Cascading failures can erupt when a single component warps, cracks, or deforms at elevated temperatures. Equipment downtime means lost productivity, missed deadlines, and repair expenses that stack up quickly. By selecting alloys that reliably hold their shape under heat stress, you minimize risk and reduce sudden disruptions.
You might be asking: Is it worth investing in these materials upfront? Absolutely. Over the operational lifespan, the cost savings from avoiding frequent breakdowns and extending maintenance intervals often more than offset any initial premium.
Maintaining Consistent Performance Over Time
The hallmark of proven high-temperature alloys lies in their ability to deliver uniform results cycle after cycle. They keep tolerances tight, prevent creeping deformation, and resist oxidation, ensuring that tough applications run smoothly. This enables engineers, managers, and other decision-makers to trust their equipment and push operational limits knowing that their chosen materials will hold strong.
Common Types of Proven High-Temperature Alloys
Nickel-Based Superalloys
Nickel-based superalloys frequently appear in turbines and jet engines, where their exceptional combination of heat resistance, strength, and corrosion protection allows them to operate at temperatures approaching 1,000°C. These materials, often formulated with elements like chromium, aluminum, and titanium, strike a balance between toughness and malleability.
Hold on: Their unique crystalline structures remain stable under severe thermal cycling. They resist creep, corrosion, and oxidation better than many alternative metals. This makes them ideal for aerospace, where reliability can literally mean life or death.
Cobalt-Based Alloys
Cobalt alloys excel in applications requiring superior wear resistance at high heat. Chemical processing equipment and certain turbine components benefit from cobalt’s ability to maintain structural stability when exposed to corrosive or oxidizing atmospheres. Although sometimes pricier, their longevity often justifies the investment.
Quick thought: If your environment involves intense chemical interactions or requires materials that maintain hardness even as temperatures rise, cobalt alloys deliver.
Iron-Based Alloys and Emerging Variants
Iron-based high-temperature alloys often provide cost-effective solutions where extreme temperatures are present but slightly lower than the demanding thresholds of nickel or cobalt superalloys. Emerging alloy variants, sometimes integrating cutting-edge elements, continue pushing performance boundaries.
The takeaway: There’s no one-size-fits-all approach. Different alloys suit different conditions, and with guidance from a reputable supplier, you can pinpoint the alloy that best aligns with specific project requirements. The diversity within high-temperature alloys ensures that you’re never stuck without a solution, regardless of how tough your application may be.
Key Properties That Make These Alloys Stand Out
Exceptional Heat Resistance
High-temperature alloys are formulated to resist softening, losing structural integrity, or undergoing phase transformations at elevated temperatures. This inherent resistance comes from carefully balanced compositions and stable microstructures that won’t melt, warp, or otherwise degrade when confronted with intense heat.
Here’s the truth: Without superior heat resistance, components would deform under stress, drastically shortening service life. These alloys secure critical dimensions, support loads, and keep machinery running smoothly.
Corrosion and Oxidation Resistance
Corrosion and oxidation become severe concerns at elevated temperatures. Many metals form scale, lose mass, or suffer embrittlement when exposed to hot, reactive gases. High-temperature alloys incorporate elements like chromium and aluminum that form stable oxide layers, protecting underlying metal from further attack.
Think about it: By minimizing material loss and surface deterioration, these alloys ensure you’re not constantly replacing costly parts.
Strength-to-Weight Ratios and Extended Lifecycles
Many high-temperature alloys maintain impressive strength-to-weight ratios, reducing overall mass while preserving durability. The outcome? More efficient systems, better fuel economy, and reduced load burdens on key components. Over time, their prolonged lifecycles translate into cost savings and less environmental impact.
Bottom line: High-temperature alloys deliver a potent combination of heat resistance, chemical stability, mechanical strength, and longevity. These properties keep your operations humming, cut down on surprises, and help you push your processes further without fear of catastrophic failure.
Applications in Different Industries
Aerospace and Aviation
Jet engines and gas turbines rely heavily on high-temperature alloys to withstand searing combustion temperatures. Turbine blades made from nickel-based superalloys endure countless heating-cooling cycles at blistering speeds without distorting or fracturing.
Here’s the scoop: Aviation’s uncompromising safety standards demand flawless performance. High-temperature alloys deliver, helping aircraft engines run reliably while maximizing efficiency.
Power Generation and Energy
Thermal power plants, geothermal systems, and industrial furnaces require materials that endure hot, corrosive conditions. Steam turbines, heat exchangers, and boiler components built from these alloys enhance uptime and prolong service intervals, ultimately lowering operational costs.
You might be curious: Stable, high-performing alloys help power facilities generate more energy from fewer resources, improving sustainability.
Automotive and Transportation
Turbocharger housings, exhaust systems, and other high-heat automotive parts benefit from corrosion-resistant alloys that keep performance consistent. With stricter emissions standards and the pursuit of greater engine efficiency, these materials help meet evolving regulatory demands.
Industrial Equipment and Machinery
Furnaces, chemical reactors, and high-temperature processing units rely on these alloys for durability. By resisting scaling, corrosion, and thermal fatigue, they maintain equipment integrity and reduce unscheduled shutdowns.
In a nutshell: From jet engines to car engines, from power plants to processing plants, the influence of high-temperature alloys is broad and transformative.
Quality Standards & Certifications to Look For
Recognized Industry Standards
When sourcing materials, it’s vital to look for compliance with established standards like ISO or ASTM. These groups set stringent metallurgical criteria and performance benchmarks. Materials passing these evaluations have shown they possess the mechanical properties and chemical composition necessary for their intended use.
Listen up: Without verifiable standards, it becomes guesswork. Reputable suppliers can produce documentation proving their alloys meet recognized parameters.
Industry-Specific Certifications
Sectors like aerospace and defense impose even stricter requirements, subjecting materials to rigorous testing before approving them for critical applications. Components made from certified alloys instill confidence and ensure alignment with strict regulatory frameworks.
Pro tip: Prioritize suppliers who can demonstrate aerospace-grade or energy-sector approvals.
Supplier Qualifications and Documentation
High-quality alloys emerge from careful control of raw materials, melt conditions, heat treatments, and finishing processes. Trustworthy suppliers provide clear material test reports, detailed composition analyses, and traceable records.
Heads up: Always request technical data sheets, mechanical property tables, and performance test results. Having these documents in hand ensures you’re getting what you pay for and that the alloy truly meets the advertised specifications.
Choosing the Right Supplier or Manufacturer
Evaluating Track Records and Expertise
Selecting a supplier goes beyond price. Lengthy experience in producing or distributing high-temperature alloys suggests they’ve encountered and solved complex challenges. A proven track record indicates they understand how to optimize material properties.
Check this out: Research reviews, case studies, and testimonials to gauge supplier reliability.
Technical Support and Customization
Some projects demand alloys fine-tuned for unique operating conditions. Suppliers offering in-house metallurgists, engineers, or technical advisors can recommend alloys that match your thermal profile. They might suggest proprietary blends or certain heat treatments that maximize performance.
Here’s the kicker: Good suppliers aren’t just vendors; they’re partners in innovation.
Global Supply and Logistics
Complex international supply chains risk delays, inconsistent quality, or communication gaps. Reliable global networks mean stable, timely deliveries.
Hint: Consider whether the supplier can provide continuous support, spare parts, and quick adjustments to orders as conditions change.
Designing Components with High-Temperature Alloys
Early Collaboration with Engineers
Bringing metallurgists and design engineers into the discussion from the start helps ensure chosen alloys match the application’s stress, load, and thermal conditions. This proactive approach reduces surprises once components hit the field.
Heads up: Don’t treat material selection as an afterthought. Integrate it early in the design phase.
Precision Casting and Advanced Manufacturing Methods
High-temperature alloys often require specialized casting, forging, or additive manufacturing techniques. Expert manufacturers know how to form complex shapes without compromising internal microstructures.
Considering Operating Conditions and Predicting Performance
Engineers rely on modeling and simulation tools to anticipate how alloys behave over service life. By analyzing thermal gradients, stress distributions, and chemical interactions, they minimize guesswork.
Remember: Careful design and manufacturing decisions pay dividends when equipment endures high temperatures without flinching.
Comparing High-Temperature Alloys to Other Materials
Stainless Steel vs. High-Temp Alloys
Stainless steel may resist oxidation and corrosion at moderate temperatures, but it often softens and loses strength well before reaching the elevated zones where high-temperature alloys excel. While stainless can be cost-effective, it struggles in truly severe conditions.
Here’s the scoop: High-temperature alloys pick up where stainless steel leaves off. They’re engineered for extremes, bridging the gap between what’s “just good enough” and what’s truly optimal.
Ceramics and Composites
Ceramics and advanced composites handle very high temperatures but can be brittle and challenging to machine. High-temperature alloys strike a balance, offering formability, ductility, and predictable mechanical properties.
Food for thought: High-temp alloys often provide a more user-friendly solution, especially for dynamic or rotating parts.
Traditional Carbon Steels
Carbon steels may do fine at room temperature but become unreliable once temperatures surge. Choosing carbon steel for high-heat zones invites deformation and frequent part replacements. High-temperature alloys deliver stability and longevity, ultimately improving reliability.
Cost Factors and Return on Investment (ROI)
Initial Investment vs. Lifetime Value
High-temperature alloys sometimes carry a higher upfront cost. However, their extended service life, reduced maintenance, and minimized downtime frequently offset that initial expenditure. Over time, these savings add up, making the total cost of ownership more attractive.
Think about it: Fewer replacements and less downtime translate into long-term financial gains.
Energy Efficiency and Operational Benefits
By maintaining stable performance, these alloys can improve system efficiency. A more efficient turbine or engine can extract extra value from fuel or other energy sources, trimming costs in the long run.
Justifying the Choice
Decision-makers often perform cost-benefit analyses to quantify these advantages. While the sticker price might appear high, the operational improvements, safety enhancements, and reduced failure rates can justify the investment.
The bottom line: Choosing high-temperature alloys isn’t just a technical decision—it’s a strategic financial one that can yield substantial returns over an asset’s life.
Real-World Case Studies & Success Stories
Aerospace Applications
Jet engines demand materials that hold shape under repeated thermal shocks and high-speed operations. Nickel-based superalloys have allowed aerospace engineers to push engine temperatures higher, increasing thrust and efficiency without compromising safety.
Here’s an example: Certain commercial jet engine turbines run reliably for tens of thousands of flight hours thanks to carefully selected alloys.
Power Plant Upgrades
When older power plants upgrade critical components with high-temperature alloys, forced outages decline, leading to more consistent energy output. Over years, this reliability improvement pays for itself.
Automotive Innovations
High-performance cars featuring advanced turbochargers leverage these alloys for optimal exhaust flow at high heat. This contributes to improved engine responsiveness and compliance with stringent emission standards.
Bottom line: In every domain, from rockets to racecars, proven high-temperature alloys enable feats that once seemed out of reach.
Ensuring Long-Term Performance & Maintenance
Regular Inspections and Non-Destructive Testing
Heat-induced stress can accumulate over time, so periodic checks and maintenance strategies ensure components remain fit for purpose. Non-destructive tests detect early signs of wear, cracks, or oxidation before catastrophic failures occur.
Remember: Proactive maintenance saves money and protects equipment.
Replacement vs. Refurbishment
Well-chosen alloys maintain integrity longer, reducing the need for expensive component replacements. When refurbishments are necessary, applying protective coatings or performing precision machining can extend component life further.
Predictive Maintenance and Data Analytics
Modern systems can monitor temperature, vibration, and stress in real-time. Advanced analytics predict when maintenance should occur, optimizing schedules and preventing downtime.
Guess what: High-temperature alloys combined with smart maintenance practices create a winning formula—extended service life, fewer emergencies, and steady productivity.
Emerging Technologies and Future Trends in High-Temperature Alloys
Advanced Alloy Development
Metallurgists continually experiment with new elemental blends seeking even greater temperature resilience and mechanical properties. Ongoing research could push operational limits higher, enabling performance that today seems impossible.
Pay attention: Tomorrow’s alloys may incorporate novel elements or techniques that redefine what’s achievable.
Nanostructures and 3D Printing
Additive manufacturing allows complex shapes to be produced with minimal waste. Combining this technology with advanced alloys could create lightweight, heat-resistant components for specialized industries.
Sustainability and Recycling
As environmental concerns grow, the push to recycle and reclaim valuable alloys intensifies. High-temperature alloys, with their premium cost, are prime candidates for recovery programs that reduce resource consumption and waste.
Heads up: Future alloys must not only withstand heat but also align with global sustainability goals, making responsible sourcing and recycling a key part of the conversation.
Conclusion & Next Steps
Reinforcing the Main Message
Why choose proven high-temperature alloys for tough applications? Because their exceptional heat resistance, strength, corrosion protection, and longevity translate into safer, more efficient operations. They maintain structural integrity when others can’t, enabling industries to push performance boundaries with confidence.
Here’s the deal: By investing in these specialized materials, you gain peace of mind, reduce disruptions, and unlock operational efficiencies.
Encouraging Action
Consider evaluating your current materials. If they’re falling short in high-heat conditions, consulting a trusted supplier or metallurgist can guide you toward the right alloys. The result? Longer equipment life, better return on investment, and fewer headaches down the line.
Remember: The best time to upgrade is before breakdowns occur. Take the next step and secure your operations against the heat.
Frequently Asked Questions (FAQ)
What industries benefit most from high-temperature alloys?
Aerospace, power generation, automotive, chemical processing, and industrial manufacturing sectors all rely on these alloys. Whenever harsh thermal conditions, aggressive chemicals, or high mechanical loads occur, these materials provide reliable solutions. Their presence ensures stable performance even in environments where standard metals fail.
How do high-temperature alloys compare in cost to standard metals?
They’re often pricier upfront, but they deliver savings over their service life. Longer lifecycles, reduced downtime, fewer part replacements, and improved system efficiency frequently offset the initial investment. For critical applications, the choice can lead to substantial long-term financial gains.
Why are nickel-based superalloys so popular?
Nickel-based superalloys excel because they combine high-temperature strength, corrosion resistance, and structural stability. They endure extreme conditions common in jet turbines and industrial gas turbines. Their ability to maintain mechanical integrity under heavy thermal stress has earned them a prestigious spot in demanding industries.
Can I use high-temperature alloys for smaller, less critical parts?
Yes. Although they shine in high-stakes applications, these alloys can also enhance performance in smaller components. The key is matching the material’s properties to the operational requirements. Even relatively minor parts that encounter heat or chemical exposure benefit from improved durability and stability.
How do I ensure I’m choosing the right alloy for my application?
Consulting with experienced suppliers or metallurgists is crucial. They consider the operating environment, chemical exposure, thermal cycling patterns, and mechanical loads to recommend an optimal alloy. Asking for technical documentation, certifications, and test results provides further assurance you’re making the right choice.
Are there any environmental advantages to using these alloys?
Yes. Longer component lifespans mean fewer replacements and less waste. Improved efficiency in power and energy systems reduces fuel consumption and emissions. Additionally, many high-temperature alloys can be recycled at end-of-life, further decreasing their environmental footprint and contributing to sustainable practices.
Do I need special manufacturing methods for these alloys?
Many high-temperature alloys require specialized casting, forging, or machining techniques due to their unique properties. Expert manufacturers understand these challenges and adapt processes accordingly. Some emerging additive manufacturing methods also hold promise, enabling more intricate shapes and reducing material waste.
Can high-temperature alloys handle sudden thermal shocks?
Yes, proven alloys are designed to tolerate rapid temperature fluctuations. Their stable microstructures and balanced compositions enable them to resist cracking or deformation, even when confronted with abrupt transitions from hot to cooler conditions. This resilience helps maintain reliability during unpredictable operations.
What kind of maintenance do high-temperature alloy components need?
While these alloys are robust, routine inspections and non-destructive testing help identify early wear or damage. Protective coatings, precise refurbishments, and predictive maintenance strategies further extend component life. Regular checks ensure the investment continues delivering value over an extended operational period.
Will future alloys push temperature limits even higher?
Research is ongoing, and new alloys with enhanced stability, nanostructures, or novel element additions may soon enter the market. These next-generation materials could redefine what’s possible, enabling even hotter, more efficient operations. Advances in additive manufacturing and sustainability will likely shape the next era of high-temperature alloys.