Introduction
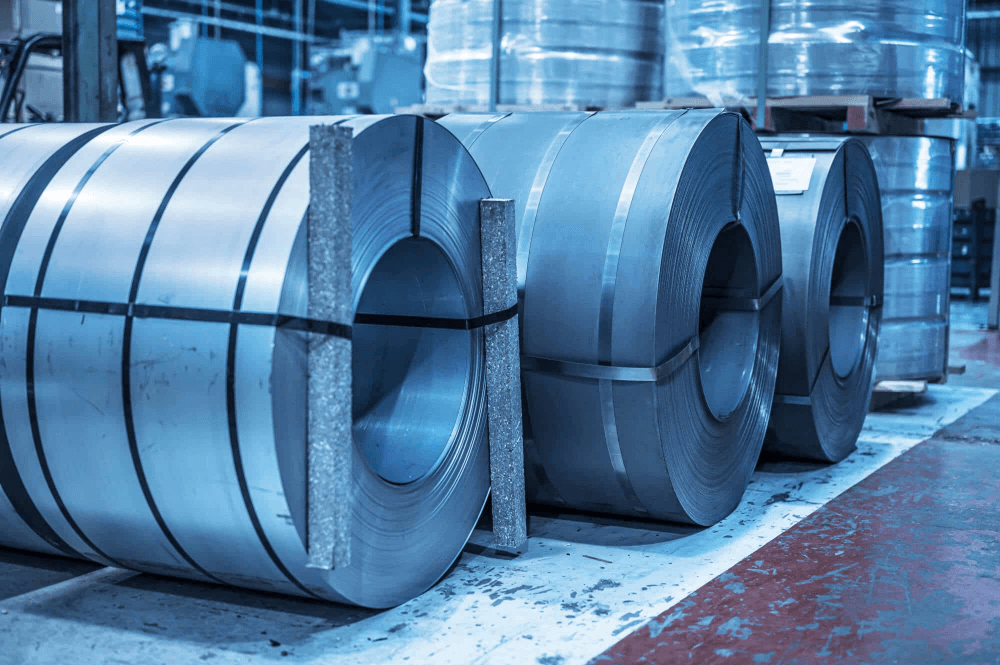
High-temperature alloys are critical materials used in industries that demand superior performance under extreme conditions, such as aerospace, power generation, and automotive sectors. These materials are designed to withstand high thermal stress, oxidation, and mechanical degradation at elevated temperatures. Understanding the properties of high-temperature alloys is essential for industries that require high performance and long-term reliability in challenging environments. In this article, we will explore the key characteristics, applications, and benefits of high-temperature alloys, providing a comprehensive guide for professionals in materials science and engineering.
Definition of High-Temperature Alloys
High-temperature alloys are engineered materials designed to maintain their structural integrity and functionality when exposed to high temperatures, typically exceeding 500°C (932°F). These alloys are primarily composed of metals like nickel, cobalt, and iron, which are combined with various alloying elements to enhance their properties. The key factor that differentiates high-temperature alloys from standard alloys is their ability to resist thermal degradation, oxidation, and creep under extreme conditions.
High-temperature alloys are essential in applications that require materials to operate in environments where temperatures are high and where there is a need for long-term stability. The primary types of high-temperature alloys include:
- Nickel-based alloys: Known for excellent resistance to heat and oxidation, these alloys are commonly used in aerospace and gas turbine applications.
- Cobalt-based alloys: These are highly resistant to wear and corrosion at elevated temperatures, making them suitable for high-stress environments.
- Iron-based alloys: These alloys offer good thermal stability and are used in applications like power generation and industrial machinery.
In addition to their ability to withstand high temperatures, these alloys are also designed for other specific properties such as resistance to corrosion, fatigue, and creep. The overall performance of these alloys depends on the precise combination of the base metal and alloying elements, each of which contributes to different aspects of their high-temperature resistance.
Alloy Type | Base Metal | Key Features | Common Uses |
---|---|---|---|
Nickel | Nickel | High heat resistance, oxidation resistance | Aerospace, turbines, chemical processing |
Cobalt | Cobalt | Wear and corrosion resistance at high temperatures | Aerospace, industrial machinery |
Iron | Iron | Cost-effective, good strength at high temperatures | Power generation, automotive |
Key Applications Across Industries
High-temperature alloys are indispensable in several industries that rely on materials to perform under extreme conditions. The following industries extensively use high-temperature alloys for their operations:
Aerospace
In the aerospace industry, high-temperature alloys are used in components like turbine blades, exhaust systems, and engine parts, where temperatures can reach thousands of degrees Fahrenheit. These alloys are critical for maintaining performance in jet engines, rocket propulsion systems, and other high-altitude and high-speed applications.
Power Generation
Power plants, especially those that use gas turbines and steam turbines, require alloys that can endure high thermal stresses over long periods. High-temperature alloys are used in turbine blades, heat exchangers, and other vital components of power generation systems. These alloys ensure efficiency and durability, even in environments with fluctuating temperatures.
Automotive and Industrial Machinery
In automotive engines and industrial machinery, high-temperature alloys are used to manufacture exhaust systems, valve components, and other parts that are exposed to heat during operation. These alloys help to improve engine performance and lifespan while maintaining safety under harsh conditions.
Oil and Gas Sector
High-temperature alloys also play a significant role in the oil and gas industry, where drilling equipment, pipelines, and valves must withstand extreme temperatures and pressures. The materials’ corrosion resistance and durability are essential for ensuring that equipment can handle the demanding environment of oil extraction and transportation.
Industry | Key Applications | Temperature Range |
---|---|---|
Aerospace | Turbine blades, exhaust systems | 600–1200°C |
Power Generation | Turbines, heat exchangers | 600–1000°C |
Automotive | Exhaust systems, engine components | 200–600°C |
Oil and Gas | Drilling equipment, valves | 400–800°C |
Core Properties of High-Temperature Alloys
High-temperature alloys exhibit several core properties that make them suitable for use in extreme environments. These properties are essential for maintaining their functionality and durability under high thermal stress.
High Thermal Stability
High-temperature alloys are designed to maintain their structural integrity at elevated temperatures. These materials can retain their strength and resist thermal expansion, ensuring that critical components do not warp or deform in hot conditions. The alloys are formulated with materials that allow them to withstand prolonged exposure to heat without losing their mechanical properties.
Creep Resistance
Creep is the gradual deformation of a material under constant stress over time, especially at elevated temperatures. High-temperature alloys are designed with specific elements such as titanium, molybdenum, and tungsten, which improve their ability to resist creep. This property is crucial in applications like turbines, where parts are subjected to sustained high temperatures and stresses.
Oxidation and Corrosion Resistance
At high temperatures, metals can oxidize and corrode quickly, leading to failure. High-temperature alloys are formulated to resist oxidation and corrosion, even in aggressive environments. Alloying elements like chromium, aluminum, and silicon form protective oxide layers on the surface of the material, preventing further degradation.
Mechanical Strength
In addition to thermal stability, high-temperature alloys must maintain their mechanical strength at elevated temperatures. These alloys are designed to endure both tensile and shear stresses, ensuring they do not fail under the conditions typical of high-temperature applications.
Property | Description | Alloying Elements |
---|---|---|
Thermal Stability | Ability to maintain strength at high temperatures | Nickel, Cobalt, Chromium |
Creep Resistance | Resistance to deformation under stress at high temperatures | Molybdenum, Tungsten, Titanium |
Oxidation Resistance | Ability to resist degradation from heat and oxygen | Chromium, Aluminum, Silicon |
Mechanical Strength | Strength at high temperatures under stress | Nickel, Iron, Cobalt |
Metallurgical Composition and Structure
The metallurgical composition of high-temperature alloys is a key factor that influences their performance under extreme conditions. These alloys are made up of a variety of elements, each contributing to specific characteristics like heat resistance, strength, and stability.
Phases and Microstructures
The microstructure of high-temperature alloys is crucial for their performance. Most high-temperature alloys exhibit multiple phases, such as the gamma (γ) phase and the gamma prime (γ’) phase in nickel-based alloys. These phases contribute to the material’s strength and stability at high temperatures.
Alloying Elements
Alloying elements are added to high-temperature alloys to enhance specific properties. For example, nickel provides excellent thermal stability, while chromium enhances corrosion resistance. Other elements like molybdenum, titanium, and tungsten improve the material’s resistance to creep and oxidation.
Heat Treatment Processes
High-temperature alloys undergo various heat treatment processes, such as aging, solution treatment, and stress-relieving, to optimize their microstructure for specific applications. These processes allow manufacturers to tailor the material’s properties, ensuring optimal performance in high-heat environments.
Alloying Element | Primary Function | Common Alloys Used In |
---|---|---|
Nickel | Heat resistance, thermal stability | Inconel, Hastelloy |
Chromium | Oxidation and corrosion resistance | Incoloy, Haynes alloys |
Molybdenum | Creep resistance, strength | Waspaloy, Udimet |
Titanium | High-temperature stability, strength | Ti-6Al-4V |
Advantages of Using High-Temperature Alloys
High-temperature alloys offer several advantages that make them indispensable in industries requiring durability and performance under extreme conditions.
Extended Service Life
Due to their excellent resistance to thermal degradation, oxidation, and creep, high-temperature alloys provide extended service life compared to conventional materials. This reduces the need for frequent maintenance and replacement, leading to cost savings over time.
Design Flexibility
High-temperature alloys can be customized for a wide range of applications, from turbine blades to exhaust systems. Their versatility allows engineers to design components that meet specific temperature, pressure, and mechanical stress requirements.
Performance Under Extreme Conditions
These alloys are specifically designed to perform well in environments with high thermal cycles, mechanical stresses, and aggressive chemicals. Their ability to withstand such conditions ensures reliable performance in critical industries like aerospace and power generation.
Reduced Downtime in Industrial Settings
The durability of high-temperature alloys reduces the risk of component failure and extends the operational life of machinery. This translates to fewer repairs, less downtime, and more efficient production processes.
Advantage | Description | Key Industries |
---|---|---|
Extended Service Life | Reduced maintenance and replacement costs | Aerospace, Power Generation |
Design Flexibility | Customization for various applications | Automotive, Industrial Machinery |
Performance Under Extreme Conditions | Reliability in harsh environments | Oil & Gas, Aerospace |
Reduced Downtime | Fewer repairs and longer operational life | Manufacturing, Energy |
Challenges and Limitations
While high-temperature alloys provide many benefits, they also come with some challenges and limitations that need to be addressed.
High Cost and Resource Constraints
The raw materials used to manufacture high-temperature alloys, such as nickel and cobalt, are expensive and can significantly increase the cost of production. The complex manufacturing processes involved in creating these alloys also add to the overall cost.
Processing Complexity
The production of high-temperature alloys requires specialized equipment and methods. These processes can be time-consuming and require high levels of expertise to ensure the material’s properties are optimized for specific applications.
Potential Issues in Large-Scale Production
Manufacturing high-temperature alloys in large quantities can present challenges in maintaining consistency and quality control. Variations in alloy composition or processing methods can lead to inconsistent performance, which is problematic for critical applications.
Design Trade-offs
Engineers often have to make trade-offs when selecting high-temperature alloys. Balancing properties such as ductility, weldability, and strength at elevated temperatures can be challenging, and the choice of alloy must be optimized based on the specific needs of the application.
Challenge | Impact | Possible Solutions |
---|---|---|
High Cost | Increases the price of the final product | Optimizing material use, sourcing alternatives |
Processing Complexity | Requires specialized equipment and expertise | Advanced manufacturing techniques |
Quality Control Issues | Variability in alloy composition | Rigorous testing and inspection processes |
Design Trade-offs | Balancing properties like strength and ductility | Tailoring alloys for specific needs |
Common Manufacturing Methods
High-temperature alloys are produced using various manufacturing methods, each with its advantages and limitations. These methods determine the final properties and suitability of the alloy for specific applications.
Investment Casting
Investment casting, also known as lost-wax casting, is a popular method for producing complex shapes with high precision. This method is widely used for creating parts like turbine blades and engine components made from high-temperature alloys.
Forging and Rolling
Forging and rolling are traditional methods used to shape high-temperature alloys into components that require directional strength. These processes help align the grain structure of the material, enhancing its strength and durability.
Powder Metallurgy
Powder metallurgy is a process that involves compressing metal powders into shapes and then heating them to form solid components. This method allows for precise control over the material’s composition and microstructure, making it ideal for producing high-performance alloys.
Additive Manufacturing (3D Printing)
Additive manufacturing, or 3D printing, is a rapidly emerging technology used to produce high-temperature alloys in complex shapes. This method is especially useful for prototyping and creating customized components for industries like aerospace and automotive.
Manufacturing Method | Key Features | Common Applications |
---|---|---|
Investment Casting | High precision, complex shapes | Turbine blades, engine components |
Forging and Rolling | Directional strength, large-scale production | Aerospace, automotive |
Powder Metallurgy | Fine control over composition and microstructure | Aerospace, medical devices |
Additive Manufacturing | Complex geometries, rapid prototyping | Aerospace, automotive |
Quality Control and Testing
Ensuring the quality of high-temperature alloys is critical to their performance in extreme environments. Manufacturers rely on several testing methods to verify that alloys meet the required standards.
Non-Destructive Testing (NDT)
Non-destructive testing methods like ultrasonic testing, X-ray inspection, and dye penetrant testing are used to detect internal defects and surface flaws in high-temperature alloys. These methods allow for thorough inspection without damaging the material.
Mechanical Property Testing
Mechanical testing, such as tensile, impact, and hardness tests, is conducted at elevated temperatures to assess the alloy’s ability to withstand stress and maintain its mechanical properties under high heat.
Thermal Fatigue and Stress Rupture Testing
Thermal fatigue testing is used to simulate the effects of repeated heating and cooling cycles on high-temperature alloys. Stress rupture testing measures the material’s ability to resist failure when subjected to high stresses at elevated temperatures.
Metallographic Examinations
Metallographic examinations involve analyzing the microstructure of high-temperature alloys under a microscope. This process helps identify grain structures, phase formations, and other microstructural features that contribute to the alloy’s performance.
Testing Method | Purpose | Relevant Industries |
---|---|---|
Non-Destructive Testing | Detects internal and surface defects | Aerospace, automotive |
Mechanical Property Testing | Assesses strength, toughness, and hardness | Power generation, oil and gas |
Thermal Fatigue Testing | Simulates temperature cycling effects | Aerospace, automotive |
Metallographic Examinations | Analyzes microstructure and phases | Industrial machinery, aerospace |
Selecting the Right High-Temperature Alloy
Selecting the appropriate high-temperature alloy for a specific application requires careful consideration of several factors. These include the operating environment, cost, and performance requirements.
Operating Environment Factors
The operating temperature, pressure, and chemical environment all play a critical role in determining which alloy is best suited for a particular application. For example, alloys used in jet engines must withstand extreme temperatures and high mechanical stresses, while those used in power plants may need to resist corrosion from steam or gases.
Cost-Benefit Analysis
While high-temperature alloys offer superior performance, they also come at a higher cost due to the expensive raw materials and complex manufacturing processes. A cost-benefit analysis can help determine whether the higher upfront cost is justified by the long-term benefits of using high-performance alloys.
Availability and Lead Times
The availability of specific high-temperature alloys and their lead times for production can be crucial factors in selecting the right material. In some cases, longer lead times may delay critical projects, so it’s important to balance material availability with production schedules.
Future Upgrades
Consideration should also be given to potential future upgrades in the system or process. As technology evolves, new materials or alloy formulations may provide better performance, and selecting an alloy with a longer lifespan can help reduce the need for frequent replacements.
Selection Factor | Consideration | Impact on Choice |
---|---|---|
Operating Environment | Temperature, pressure, chemical exposure | Selection of suitable alloys |
Cost-Benefit Analysis | Initial investment vs. long-term performance | Balancing cost with reliability |
Availability and Lead Time | Material availability and production time | Impact on project timelines |
Future Upgrades | Potential advancements in material technology | Impact on long-term sustainability |
Emerging Trends in Alloy Development
The development of high-temperature alloys continues to evolve, driven by advances in materials science and manufacturing technologies. Some of the key trends shaping the future of high-temperature alloys include:
Advanced Materials Research
Researchers are constantly working to improve the performance of high-temperature alloys by introducing new materials and alloys that can withstand even higher temperatures or provide better resistance to corrosion and oxidation.
Environmental Concerns
With increasing awareness of environmental issues, there is a growing demand for alloys that have a smaller carbon footprint. Innovations in alloy formulations are aimed at improving energy efficiency while minimizing the environmental impact of production processes.
Next-Generation Manufacturing Techniques
Emerging manufacturing techniques, such as 3D printing and hybrid manufacturing methods, offer greater precision and faster production times for high-temperature alloys. These technologies enable the creation of more complex shapes and components, which are increasingly in demand in industries like aerospace.
Innovations in Heat Treatment
New heat treatment processes are being developed to enhance the properties of high-temperature alloys. These processes aim to improve the alloys’ strength, creep resistance, and thermal stability, making them even more suitable for extreme applications.
Trend | Description | Potential Impact |
---|---|---|
Advanced Materials | New alloys with superior properties | Increased performance and durability |
Environmental Concerns | Developing alloys with a lower environmental impact | Reduced carbon footprint |
Next-Generation Manufacturing | Using advanced manufacturing methods like 3D printing | Improved precision and customization |
Innovations in Heat Treatment | New heat treatment techniques to enhance properties | Better performance in extreme conditions |
Maintenance and Lifecycle Considerations
Maintaining high-temperature alloys is crucial to ensuring they continue to perform optimally throughout their lifecycle. Regular maintenance and inspection schedules help identify potential issues before they lead to failures.
Inspection Schedules
High-temperature alloys used in critical applications should be inspected regularly to check for signs of degradation or wear. Inspection schedules should be tailored to the specific alloy and its operating conditions, ensuring that components are replaced or repaired before they fail.
Repair Techniques
When high-temperature alloys develop issues like cracks or wear, repair techniques such as welding and surface coating can be used to restore their integrity. Special attention must be given to the material properties during repair to ensure that the repairs do not compromise the alloy’s performance.
Long-Term Cost Savings
The durability of high-temperature alloys leads to long-term cost savings. By reducing the need for frequent replacements and minimizing the risk of equipment failure, businesses can achieve a high return on investment by using these advanced materials.
End-of-Life Recycling
At the end of their service life, high-temperature alloys can often be recycled, recovering valuable alloying elements like nickel and cobalt. Recycling helps to reduce the environmental impact of these materials and ensures that valuable resources are not wasted.
Maintenance Aspect | Consideration | Impact on Performance |
---|---|---|
Inspection Schedules | Regular checks for wear and degradation | Prevents failures and reduces downtime |
Repair Techniques | Methods like welding and surface coatings | Restores material integrity |
Long-Term Cost Savings | Reduced maintenance and replacement costs | Higher ROI over time |
End-of-Life Recycling | Recovery of valuable materials | Reduces environmental impact |
Industry-Specific Case Studies
High-temperature alloys are used across various industries that require materials to perform under challenging conditions. Let’s explore some real-world examples of high-temperature alloys in action:
Aerospace Turbine Blades
In the aerospace industry, turbine blades are critical components that must withstand extreme temperatures and stresses. Nickel-based high-temperature alloys are commonly used for turbine blades due to their excellent heat resistance and ability to maintain mechanical strength under high stress. These alloys ensure the efficient operation of jet engines and improve fuel efficiency.
Power Plant Boilers
Power plants rely on high-temperature alloys in their boilers to maintain efficiency and reduce energy loss. Alloys used in these applications must resist both thermal fatigue and corrosion, as they are exposed to high temperatures and reactive gases. The use of high-performance alloys helps to improve the reliability of power generation systems.
Automotive Exhaust Systems
High-temperature alloys are also used in automotive exhaust systems, where components like exhaust manifolds and turbochargers are exposed to extreme temperatures. These alloys help improve engine performance by maintaining structural integrity under high heat and preventing corrosion from exhaust gases.
Oil & Gas Drilling Components
In the oil and gas industry, high-temperature alloys are used for drilling components that must perform under extreme downhole conditions. The alloys provide the strength and corrosion resistance needed to endure the high-pressure and high-temperature environments encountered during drilling operations.
Industry | Key Applications | Temperature Range |
---|---|---|
Aerospace | Turbine blades, exhaust systems | 600–1200°C |
Power Generation | Turbines, heat exchangers | 600–1000°C |
Automotive | Exhaust systems, engine components | 200–600°C |
Oil and Gas | Drilling equipment, valves | 400–800°C |
Frequently Asked Questions (FAQ)
What Are the Typical Temperature Ranges for High-Temperature Alloys?
High-temperature alloys are generally designed to operate at temperatures ranging from 500°C to 1200°C, depending on the alloy and the application.
How Do Alloying Elements Like Chromium or Nickel Impact Performance?
Chromium enhances oxidation resistance, while nickel provides thermal stability, both of which are critical for high-temperature applications.
Can High-Temperature Alloys Be Welded?
Yes, many high-temperature alloys can be welded, but specialized techniques are required to maintain their integrity during the welding process.
Are There Any “One-Size-Fits-All” Solutions?
No, high-temperature alloys must be selected based on the specific temperature, pressure, and chemical environment of the application.
How Much Do These Alloys Cost?
High-temperature alloys are typically more expensive than standard materials due to their specialized properties and the use of rare metals like nickel and cobalt.
Conclusion
High-temperature alloys are essential for industries that require performance under extreme conditions, offering unmatched durability and efficiency across applications.