Introduction
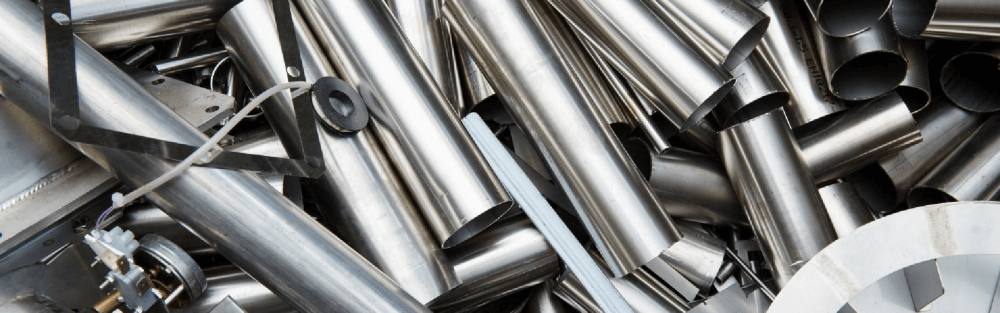
High-temperature alloys are essential materials used across a wide range of industries, from aerospace to power generation. These alloys are designed to withstand extreme heat and demanding mechanical conditions, making them crucial for applications where other materials would fail. However, choosing the right high-temperature alloy for a specific application can be challenging, as it requires understanding the properties that best suit the environment and stresses involved. This article will guide you through the key properties of high-temperature alloys and how to choose the best one for your needs.
What are High-Temperature Alloys?
High-temperature alloys are materials specifically engineered to perform under high heat, often exceeding 500°C. These alloys are commonly made from a variety of metals, such as nickel, cobalt, and iron, combined with other elements like chromium, molybdenum, and tungsten. Each element contributes to the alloy’s ability to resist degradation from heat, oxidation, and corrosion.
These alloys are used in critical applications where standard metals cannot survive the intense conditions, such as in jet engines, gas turbines, and power plants. The primary objective when selecting a high-temperature alloy is to balance the alloy’s ability to resist oxidation, corrosion, and thermal fatigue while maintaining mechanical strength under elevated temperatures.
High-temperature alloys can be classified into different categories, including superalloys, heat-resistant steels, and refractory metals. Superalloys, often made from nickel or cobalt, are particularly notable for their high strength and resistance to heat and corrosion, making them ideal for turbine blades and other critical components exposed to extreme temperatures.
Importance of High-Temperature Alloys in Modern Manufacturing
High-temperature alloys play a critical role in industries that rely on extreme temperature environments. One of the most prominent industries is aerospace, where alloys are used in jet engines and combustion chambers, which operate at temperatures of over 1,000°C. Similarly, power generation industries require high-temperature alloys in turbines, boilers, and heat exchangers, where the materials must withstand both high heat and pressure for prolonged periods.
The automotive industry also utilizes high-temperature alloys in exhaust systems and catalytic converters, where resistance to heat and corrosion is essential. The chemical processing industry also relies on high-temperature alloys for reactors and heat exchangers, where exposure to both high temperatures and aggressive chemicals is a daily concern.
For all these industries, choosing the right alloy can mean the difference between efficient performance and catastrophic failure. Alloys that fail to perform under high heat can lead to costly repairs, production downtime, and even safety hazards. Therefore, understanding the key properties and performance characteristics of these materials is vital for selecting the correct high-temperature alloy.
Thermal Resistance: Why It Matters
Thermal resistance is one of the most crucial properties when choosing a high-temperature alloy. This refers to the alloy’s ability to maintain its structural integrity and functionality at elevated temperatures. As the temperature of an alloy increases, the atoms in the metal vibrate more, which can lead to weakening of the material. The higher the thermal resistance, the better the material can withstand prolonged exposure to heat without failing.
High thermal resistance is particularly important in applications where alloys are subjected to direct flame or extreme temperature gradients, such as in gas turbines or rocket engines. Materials with high thermal resistance can maintain their strength and mechanical properties even when exposed to the intense heat found in these environments.
To evaluate thermal resistance, manufacturers must look at the alloy’s melting point and the temperature at which it can still perform without degrading. Alloys like Inconel and Hastelloy are well-known for their excellent thermal resistance and are often used in extreme applications like aerospace and power generation.
Alloy Type | Melting Point (°C) | Thermal Conductivity (W/m·K) |
---|---|---|
Inconel 718 | 1,300 | 11.4 |
Hastelloy X | 1,300 | 14.5 |
Haynes 230 | 1,410 | 19.5 |
Titanium Alloy | 1,668 | 22.0 |
Oxidation Resistance and Corrosion Resistance
Oxidation and corrosion are two of the biggest threats to high-temperature alloys. At elevated temperatures, materials are more susceptible to reacting with oxygen in the environment, leading to the formation of oxide layers that can weaken the material. Corrosion, on the other hand, is caused by chemical reactions between the alloy and the surrounding environment, which can lead to the degradation of its surface and eventual failure.
Oxidation resistance is a key factor when selecting an alloy for high-temperature applications. Alloys that have high levels of chromium and aluminum tend to form a protective oxide layer on the surface, which prevents further oxidation and protects the alloy from damage. This makes alloys like Inconel and Hastelloy ideal for high-temperature environments where oxidation resistance is essential.
Corrosion resistance is equally important in industries like chemical processing and power generation, where alloys are exposed to not just heat, but also aggressive chemicals. The presence of elements like molybdenum and tungsten in the alloy composition enhances its resistance to pitting and stress corrosion cracking, making it suitable for such challenging environments.
Alloy Type | Oxidation Resistance (hrs at 1,000°C) | Corrosion Resistance (at 600°C) |
---|---|---|
Inconel 718 | 500 | Excellent |
Hastelloy C-276 | 450 | Excellent |
Monel 400 | 300 | Good |
Titanium Alloy | 700 | Moderate |
Mechanical Properties at Elevated Temperatures
Mechanical properties such as tensile strength, creep resistance, and fatigue resistance are critical when selecting high-temperature alloys. At elevated temperatures, metals can become more ductile, which reduces their strength and ability to bear load. This makes it essential for high-temperature alloys to retain their mechanical properties to ensure the safety and longevity of components.
Tensile strength refers to the material’s ability to resist breaking under tension. At high temperatures, alloys must maintain their tensile strength to prevent failure during operation. Creep resistance, on the other hand, measures the material’s ability to resist gradual deformation over time when subjected to high stress at elevated temperatures. Alloys with high creep resistance can retain their shape and dimensions even after prolonged exposure to high temperatures.
Fatigue resistance is another important mechanical property, as materials that are exposed to repeated thermal and mechanical stresses can fail due to fatigue. Alloys with high fatigue resistance are able to withstand these stresses without cracking or breaking, making them ideal for applications in turbine blades, jet engines, and exhaust systems.
Alloy Type | Tensile Strength (MPa) | Creep Resistance (hrs at 800°C) | Fatigue Resistance (MPa) |
---|---|---|---|
Inconel 718 | 1,240 | 3,000 | 550 |
Hastelloy C-276 | 850 | 1,800 | 450 |
Titanium Alloy | 900 | 1,500 | 400 |
Haynes 230 | 1,300 | 4,500 | 600 |
Temperature Range Considerations
When selecting a high-temperature alloy, one of the most important factors to consider is the temperature range the material will be exposed to. Different alloys are designed to operate effectively within specific temperature ranges, and choosing an alloy that can withstand the maximum expected temperature is essential for ensuring the longevity and performance of components.
For applications in the aerospace industry, for example, materials must be capable of withstanding temperatures exceeding 1,000°C, while alloys used in automotive exhaust systems may only need to resist temperatures up to 800°C. It’s important to match the temperature requirements of the application to the capabilities of the alloy to avoid premature failure.
Some alloys are specifically designed for ultra-high temperatures, such as those used in rocket engines, while others are more suitable for mid-range applications like gas turbines or heat exchangers. By selecting an alloy that is rated for the required temperature range, manufacturers can avoid over-engineering or under-engineering the material, both of which can lead to unnecessary costs or operational failures.
Alloy Type | Operating Temperature Range (°C) | Max. Temperature (°C) |
---|---|---|
Inconel 718 | 700-1,000 | 1,300 |
Hastelloy C-276 | 600-1,000 | 1,050 |
Titanium Alloy | 450-800 | 1,200 |
Haynes 230 | 600-1,100 | 1,410 |
Alloy Composition and Its Impact on Performance
The composition of a high-temperature alloy is a critical factor in determining its overall performance. By altering the proportion of various elements in the alloy, manufacturers can enhance certain properties, such as strength, thermal resistance, and oxidation resistance, to suit specific needs.
For example, adding more chromium to an alloy can significantly improve its oxidation resistance, while increasing the amount of nickel can enhance its strength and thermal stability. Similarly, elements like molybdenum and tungsten can improve the alloy’s resistance to creep and corrosion, making them ideal for applications in harsh environments.
By understanding how each element contributes to the alloy’s performance, manufacturers can better select the right high-temperature alloy for their application. For instance, a high-nickel alloy might be ideal for aerospace components where both high strength and thermal stability are essential, while an alloy with a higher percentage of chromium might be more suitable for chemical processing applications where oxidation resistance is key.
Alloy Type | Main Elements | Key Properties |
---|---|---|
Inconel 718 | Nickel, Chromium, Iron | High strength, oxidation resistance |
Hastelloy C-276 | Nickel, Molybdenum, Chromium | Corrosion resistance, high-temperature performance |
Titanium Alloy | Titanium, Aluminum, Vanadium | Strength, fatigue resistance |
Haynes 230 | Nickel, Chromium, Molybdenum | High-temperature strength, oxidation resistance |
Environmental Factors to Consider
Environmental factors play a significant role in the performance of high-temperature alloys. The presence of aggressive chemicals, moisture, and varying atmospheric conditions can all affect the integrity of the alloy over time. For example, alloys used in chemical processing environments may need to withstand not only high temperatures but also exposure to corrosive chemicals.
Similarly, alloys used in marine environments must resist saltwater corrosion in addition to high heat. Pressure also affects high-temperature alloys, especially in deep-sea or underground applications. The combination of heat, pressure, and chemicals requires selecting alloys that are specifically formulated for these tough environments.
Manufacturers need to evaluate all environmental factors when choosing the right alloy for a given application. By selecting materials that are tailored to withstand specific environmental conditions, they can ensure longer service life and minimize the risk of material failure.
Alloy Type | Environmental Conditions | Recommended Applications |
---|---|---|
Inconel 718 | High heat, oxidation | Aerospace, power generation |
Hastelloy C-276 | Corrosive chemicals | Chemical processing, marine |
Titanium Alloy | High heat, corrosion | Aerospace, automotive exhaust |
Haynes 230 | High heat, oxidation | Gas turbines, aerospace |
Cost vs. Performance: Striking the Balance
When selecting a high-temperature alloy, balancing cost and performance is a critical decision. Premium alloys, such as those used in aerospace or nuclear industries, offer superior performance but come at a higher cost. On the other hand, less expensive alloys may still provide adequate performance for lower-stress applications but might not last as long in extreme environments.
Manufacturers must weigh the potential benefits of longer-lasting, higher-performance alloys against the initial cost savings from using more affordable options. In some cases, using a premium alloy may be the best choice if it prevents costly repairs, downtime, or safety risks down the road. However, for applications where performance demands are lower, a more affordable alloy might suffice.
By understanding the specific requirements of the application and considering the long-term costs associated with material performance, manufacturers can make a more informed decision.
Alloy Type | Cost (per kg) | Performance Benefits | Best for Applications |
---|---|---|---|
Inconel 718 | $40 | High strength, thermal resistance | Aerospace, turbines |
Hastelloy C-276 | $60 | Corrosion resistance, durability | Chemical processing |
Titanium Alloy | $30 | High strength, light weight | Automotive, aerospace |
Haynes 230 | $50 | High temperature resistance | Gas turbines, aerospace |
Alloy Testing and Analysis: What to Look For
Testing and analysis are essential for ensuring the right alloy is selected for the job. Manufacturers must test the material’s mechanical properties, such as tensile strength, creep resistance, and fatigue resistance, under the specific temperature and environmental conditions they will face.
Common tests include tensile tests, which determine the material’s ability to resist deformation under tension, and creep tests, which measure its resistance to slow deformation at high temperatures. Oxidation tests are also crucial for assessing how well an alloy will perform in high-heat, oxidizing environments.
In addition to mechanical testing, alloy certification and standards play an important role in ensuring that the material meets the required specifications for quality and reliability. These certifications verify that the alloy has passed rigorous testing and is suitable for use in demanding applications.
Test Type | Purpose | Common Testing Standards |
---|---|---|
Tensile Test | Measure strength under tension | ASTM E8, ISO 6892 |
Creep Test | Measure resistance to deformation | ASTM E139, ISO 204 |
Oxidation Test | Measure resistance to oxidation | ASTM B829, ISO 15081 |
Fatigue Test | Measure resistance to repeated stress | ASTM E606, ISO 1099 |
Understanding Alloy Certifications and Standards
Alloy certifications and industry standards are essential when selecting high-temperature alloys for demanding applications. These certifications ensure that the materials have been tested and meet specific performance and safety criteria. Many industries require that alloys meet recognized international standards to ensure quality and consistency.
Standards like ASTM (American Society for Testing and Materials), ISO (International Organization for Standardization), and ASME (American Society of Mechanical Engineers) provide guidelines for the testing and performance of high-temperature alloys. Alloys that meet these standards have undergone rigorous testing to verify their suitability for high-temperature applications.
Alloy certifications also give manufacturers confidence that the materials they are using meet safety and quality expectations. Whether working in aerospace, automotive, or chemical processing, using certified alloys ensures the reliability of components in harsh conditions.
Standard | Relevant Industry | Key Requirements |
---|---|---|
ASTM B829 | Aerospace, Power Generation | Tensile strength, oxidation resistance |
ISO 15081 | Chemical Processing | Corrosion resistance, high-temperature performance |
ASTM E139 | Aerospace, Automotive | Creep resistance, fatigue resistance |
ASME BPVC | Power Generation | High-temperature resistance, mechanical properties |
Aerospace Industry: The Need for Superalloys
The aerospace industry is one of the primary sectors that rely heavily on high-temperature alloys, particularly superalloys. Superalloys are alloys designed to withstand extreme temperatures and stresses, making them ideal for use in jet engines, turbines, and other high-performance applications.
These alloys typically feature high amounts of nickel and cobalt, which provide superior strength and resistance to thermal degradation. In jet engines, for example, turbine blades need to operate at temperatures exceeding 1,000°C without losing strength or integrity. Superalloys, such as Inconel and Hastelloy, are ideal for these applications due to their exceptional resistance to both high heat and oxidation.
Alloy Type | Properties Required | Application Example |
---|---|---|
Inconel 718 | High strength, thermal stability | Jet engines, turbine blades |
Hastelloy X | Oxidation resistance, high strength | Aerospace engines |
Haynes 230 | High-temperature resistance | Gas turbines, aerospace |
Titanium Alloy | Lightweight, high strength | Aerospace, structural components |
Automotive and Power Generation: Durability and Performance
High-temperature alloys are widely used in the automotive and power generation industries for applications like exhaust systems, catalytic converters, and turbine blades. In these environments, alloys must not only resist high temperatures but also perform under constant mechanical stress, pressure, and exposure to chemicals.
The automotive industry, for instance, requires alloys that can withstand temperatures as high as 800°C in exhaust systems. High-temperature alloys, such as stainless steel and titanium, are ideal for this purpose due to their corrosion resistance and ability to maintain strength at elevated temperatures.
In the power generation sector, turbine blades and heat exchangers need to endure extremely high temperatures and pressures. Materials like Inconel and Hastelloy are often chosen due to their superior mechanical properties and resistance to thermal degradation.
Alloy Type | Temperature Range (°C) | Application | Industry |
---|---|---|---|
Inconel 718 | 700-1,000 | Turbines, heat exchangers | Power generation |
Titanium Alloy | 450-800 | Exhaust systems, catalytic converters | Automotive |
Haynes 230 | 600-1,100 | Turbines, aerospace | Aerospace, Power generation |
Hastelloy X | 1,100-1,300 | High-stress components | Power generation |
Heat Exchangers and Chemical Processing: Corrosion Resistance and Strength
Heat exchangers and chemical reactors are critical components in many industrial processes, and they rely on high-temperature alloys to operate efficiently. These systems often deal with both high temperatures and exposure to aggressive chemicals, making material selection a complex process.
High-temperature alloys used in these applications must have excellent resistance to corrosion and oxidation, as well as the ability to maintain mechanical strength at elevated temperatures. Hastelloy and Inconel, for example, are often used in chemical reactors due to their resistance to corrosion from acids and other reactive chemicals.
Alloy Type | Resistance Required | Application | Industry |
---|---|---|---|
Hastelloy C-276 | Corrosion, oxidation | Chemical reactors, heat exchangers | Chemical processing |
Inconel 625 | Oxidation, thermal stability | Heat exchangers | Power generation |
Titanium Alloy | Corrosion, fatigue resistance | Chemical processing | Heat exchangers |
Haynes 230 | High temperature, oxidation | High-temperature reactors | Chemical processing |
Conclusion
When selecting the right high-temperature alloy for your application, it’s essential to consider the specific properties required for your environment. From thermal and oxidation resistance to mechanical strength and corrosion resistance, each factor plays a critical role in ensuring that the alloy performs optimally. By understanding the various properties and how they contribute to alloy performance, you can make an informed decision that ensures the longevity and reliability of your components.
FAQ Section
1. What is the maximum temperature high-temperature alloys can withstand?
The maximum temperature varies depending on the alloy, but materials like Inconel 718 can withstand temperatures up to 1,300°C.
2. Can high-temperature alloys be used in low-temperature environments?
Yes, high-temperature alloys can perform well in low-temperature environments, but they are specifically designed for high-heat conditions.
3. What’s the difference between superalloys and standard high-temperature alloys?
Superalloys have enhanced strength, oxidation, and creep resistance, making them suitable for extreme environments, such as aerospace.
4. How do I know when an alloy has failed under high temperatures?
Signs of failure include cracks, deformation, or loss of mechanical properties such as strength and fatigue resistance.
5. Are high-temperature alloys expensive?
High-temperature alloys tend to be more expensive than standard alloys due to their advanced properties and the specialized manufacturing processes required.