Innovations in Properties of High-Temperature Alloys
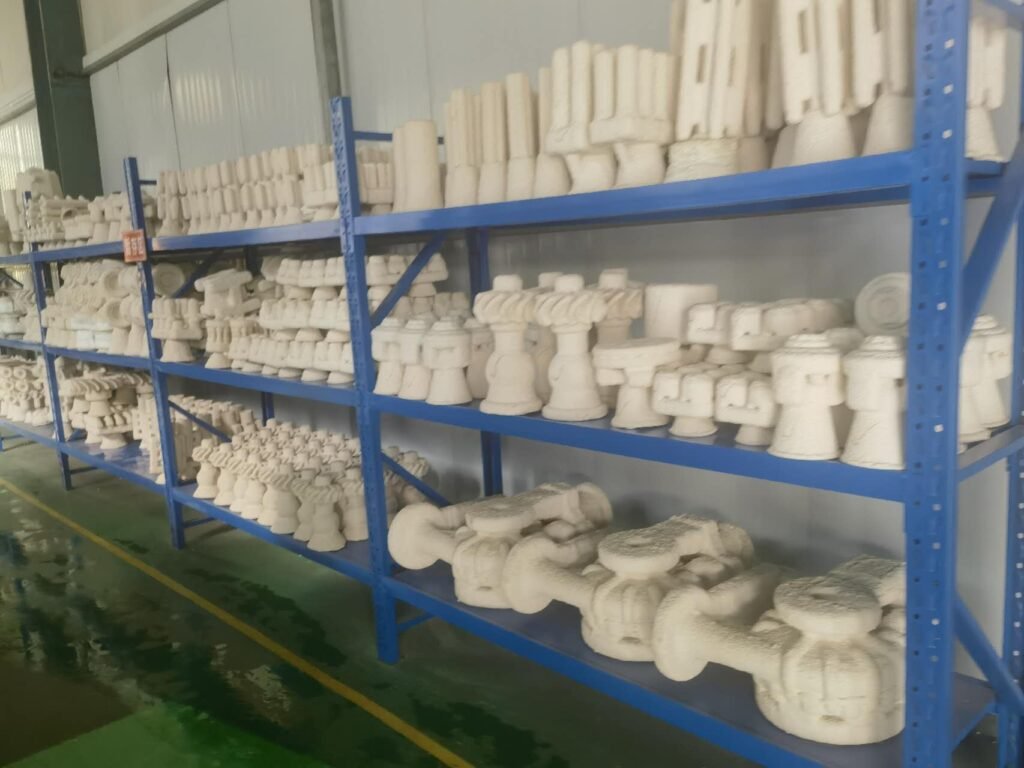
High-temperature alloys play a crucial role in industries requiring materials that can withstand extreme heat, such as aerospace, automotive, and energy production. These alloys have been evolving for years to meet the growing demands of modern engineering, and innovations continue to emerge in their properties. In this article, we will explore the latest advancements in high-temperature alloys, their composition, benefits, and applications, providing an in-depth look at how they are revolutionizing industrial processes.
Basics of High-Temperature Alloys
High-temperature alloys are materials designed to maintain their strength, resistance to corrosion, and structural integrity when exposed to extreme temperatures. These alloys are primarily composed of metals such as nickel, cobalt, and titanium, which are known for their high melting points and robust properties. The key characteristic of high-temperature alloys is their ability to retain mechanical properties at temperatures above 500°C, which would typically cause other materials to degrade or fail.
Common Types of High-Temperature Alloys
The most commonly used high-temperature alloys are nickel-based alloys, which have excellent resistance to oxidation and high-temperature creep. These alloys are primarily used in aerospace and power generation applications, where materials are constantly exposed to high heat and pressure. Cobalt-based alloys, known for their superior resistance to wear and high-temperature corrosion, are often used in turbine engines. Titanium-based alloys, while lighter and more corrosion-resistant, are typically used in applications where weight savings are critical.
These alloys are engineered to withstand extreme stress, thermal cycling, and corrosive environments. In addition to their high melting points, they often feature advanced microstructures that contribute to their mechanical performance at elevated temperatures. The development of such materials has led to significant improvements in efficiency and longevity across several industries.
Alloy Type | Key Properties | Common Applications |
---|---|---|
Nickel-based | High strength, oxidation resistance | Aerospace, gas turbines |
Cobalt-based | Wear resistance, corrosion resistance | Turbine blades, industrial applications |
Titanium-based | Light weight, corrosion resistance | Aircraft components, biomedical implants |
The Role of High-Temperature Alloys in Industry
High-temperature alloys are indispensable in several industries where extreme conditions are a regular challenge. In aerospace, for instance, materials used in jet engines and turbine blades need to withstand temperatures that exceed 1,000°C while maintaining their mechanical properties. Without high-temperature alloys, the efficiency of modern aircraft engines would be compromised.
Aerospace and Power Generation
In power generation, particularly in gas turbines and nuclear reactors, high-temperature alloys are used to construct components that must operate at incredibly high temperatures and pressures. These materials are integral to ensuring the efficiency of energy production and reducing the environmental impact of power plants. Similarly, in the automotive industry, high-temperature alloys are used in high-performance engine parts, ensuring that engines can withstand the intense heat generated during operation.
The reliance on high-temperature alloys across these industries cannot be overstated. They are essential for improving energy efficiency, reducing maintenance costs, and increasing the lifespan of critical components. As industries strive for greater performance, the demand for these alloys continues to grow, pushing the boundaries of material science.
Industry | Alloy Usage | Impact |
---|---|---|
Aerospace | Engine turbines, structural parts | Increased efficiency, longer lifespan |
Power Generation | Gas turbines, reactor components | Reduced operational costs, improved energy output |
Automotive | High-performance engines | Enhanced engine durability, better fuel efficiency |
The Need for Innovations in High-Temperature Alloys
As industries demand higher performance from their materials, there is an increasing need for innovations in the properties of high-temperature alloys. Traditional alloys, while reliable, often fall short when exposed to the most demanding conditions. The quest for materials that can withstand higher temperatures, resist oxidation, and maintain their structural integrity over long periods is driving innovation in the field.
Overcoming Existing Limitations
The primary challenge with high-temperature alloys is their tendency to degrade under prolonged exposure to heat. As temperature increases, the alloys may undergo phase transformations, which can reduce their strength and make them more susceptible to wear and fatigue. Advances in alloy composition and processing techniques are essential to overcome these issues. Researchers are exploring new ways to improve the microstructure of alloys, increase their resistance to thermal cycling, and enhance their performance in extreme environments.
Innovations in the alloying process, such as the use of advanced coatings and multi-phase alloys, have already led to notable improvements. These developments help increase the lifespan of components and reduce the frequency of repairs, ultimately saving industries significant amounts of money. The need for high-temperature alloys to perform better under ever more extreme conditions will continue to drive future innovations.
Challenge | Solution | Impact |
---|---|---|
Phase transformation | Improved microstructure design | Enhanced strength and thermal stability |
Oxidation | Advanced coatings, hybrid alloys | Longer component lifespan |
Fatigue | Grain boundary engineering | Reduced maintenance, higher efficiency |
Innovations in Material Composition
Material composition plays a vital role in determining the performance of high-temperature alloys. Traditional alloys typically rely on elements like nickel, cobalt, and chromium to provide the necessary heat resistance and strength. However, as industries push for even higher performance, researchers are turning to new and innovative elements to improve the properties of these alloys.
Additive Manufacturing and Hybrid Alloys
One significant innovation is the development of hybrid alloys, which combine traditional alloying elements with newer, more exotic materials like titanium and niobium. These alloys exhibit enhanced properties, including better oxidation resistance, improved creep strength, and superior thermal stability. Additive manufacturing is also playing a role in developing custom alloys for specific applications, allowing manufacturers to optimize the material composition for particular environments.
The use of advanced materials like rhenium and hafnium is becoming more common in the development of alloys for extremely high-temperature applications. These elements provide exceptional resistance to heat and oxidation, allowing alloys to perform in conditions previously deemed impossible.
Alloy Composition | Key Benefits | Applications |
---|---|---|
Hybrid alloys | Enhanced strength, oxidation resistance | Aerospace, nuclear reactors |
Titanium-based | Lightweight, corrosion-resistant | Aircraft, automotive components |
Rhenium alloys | Superior heat resistance, strength | High-performance turbines |
Enhancing Oxidation Resistance
Oxidation is one of the most significant challenges for high-temperature alloys. When exposed to high heat, alloys can react with oxygen, leading to the formation of oxide layers on the surface. These oxide layers can weaken the material, causing it to degrade over time.
Protective Coatings
Innovations in oxidation resistance often involve the application of protective coatings to the surface of the alloys. Coatings made from materials such as yttrium, cerium, and other rare earth metals have shown promise in preventing oxidation at elevated temperatures. These coatings form a barrier between the alloy and the surrounding environment, significantly extending the lifespan of the material.
Additionally, researchers are exploring the potential of self-healing coatings that can repair themselves when damaged. This innovative approach could further reduce the risk of oxidation and prolong the useful life of high-temperature alloys in challenging environments.
Coating Material | Key Properties | Applications |
---|---|---|
Yttrium-based | Oxidation resistance, high stability | Gas turbines, jet engines |
Cerium-based | Improved corrosion resistance | High-temperature reactors |
Self-healing | Autonomous repair, enhanced durability | Aerospace, power generation |
Improving Thermal Fatigue Resistance
Thermal fatigue occurs when a material is exposed to repeated cycles of heating and cooling, causing it to crack or break down over time. This is a particular concern for components in high-temperature environments, where parts experience constant thermal cycling.
Advanced Cooling Techniques
To improve thermal fatigue resistance, researchers are focusing on advanced cooling techniques and microstructural optimization. The use of cooling channels, thermal barrier coatings, and advanced casting techniques helps to reduce the thermal stresses that cause fatigue. Additionally, fine-tuning the alloy’s microstructure by adjusting the grain size and phase distribution has been shown to improve fatigue resistance.
These innovations are essential for applications like turbine blades and engine components, which experience constant thermal cycling. By enhancing the materials’ ability to resist thermal fatigue, industries can extend the life of their components and reduce maintenance costs.
Cooling Technique | Benefit | Applications |
---|---|---|
Thermal barrier coatings | Improved fatigue resistance | Gas turbines, jet engines |
Cooling channels | Reduced thermal stress | Power generation, automotive |
Microstructural optimization | Enhanced strength and resistance | Aerospace, industrial equipment |
Advancements in High-Temperature Strength
High-temperature alloys must maintain their strength and structural integrity at elevated temperatures. Without this ability, critical components would fail prematurely, leading to catastrophic consequences in industries like aerospace and energy production.
Strengthening Mechanisms
Recent advancements in high-temperature strength involve the development of new strengthening mechanisms within the alloys themselves. Researchers are focusing on the role of intermetallic compounds and precipitate phases, which help maintain strength at high temperatures. Innovations in grain boundary engineering have also shown promising results in improving the overall strength of high-temperature alloys.
By controlling the distribution and size of precipitates within the alloy, manufacturers can create materials that retain their strength and resistance to deformation even under extreme heat. These advancements are particularly important for components like turbine blades and heat exchangers, where high strength is essential for maintaining performance under challenging conditions.
Strengthening Mechanism | Key Benefit | Applications |
---|---|---|
Intermetallic compounds | Increased strength at high temperatures | Gas turbines, aerospace |
Precipitate phases | Improved resistance to deformation | Power generation, automotive |
Grain boundary engineering | Enhanced strength and stability | Industrial machinery, reactors |
Improving Creep Resistance in High-Temperature Alloys
Creep is the gradual deformation of a material under constant stress at high temperatures. This phenomenon is a major concern for materials used in high-temperature environments, as it can lead to permanent deformation and failure of components.
Microstructure and Creep Resistance
To improve creep resistance, researchers are focusing on developing alloys with fine-grained structures and stable phases. By optimizing the microstructure, manufacturers can reduce the rate of creep and extend the service life of components exposed to high temperatures and stress.
Innovations in creep-resistant alloys have led to significant improvements in the performance of materials used in turbine engines, power plants, and other critical applications. These advancements help ensure that components maintain their shape and strength under long-term stress, preventing costly breakdowns and extending operational lifetimes.
Alloy Type | Key Benefit | Applications |
---|---|---|
Fine-grained alloys | Enhanced creep resistance | Gas turbines, nuclear reactors |
Stable phase alloys | Reduced deformation over time | Aerospace, power generation |
Impact of Additive Manufacturing on High-Temperature Alloys
Additive manufacturing, or 3D printing, is revolutionizing the production of high-temperature alloys. This technology allows manufacturers to create complex geometries that were previously impossible with traditional manufacturing methods.
Custom Alloys for Specific Applications
Additive manufacturing enables the creation of custom high-temperature alloys tailored to specific industrial needs. By using 3D printing, manufacturers can optimize the material composition and design for specific applications, ensuring maximum performance in extreme conditions.
This technology also allows for rapid prototyping and shorter production times, making it easier to develop new materials and bring them to market quickly. The flexibility and efficiency of additive manufacturing are driving innovations in high-temperature alloys, opening up new possibilities for industries that rely on advanced materials.
Technology | Key Benefit | Applications |
---|---|---|
Additive manufacturing | Custom alloy production | Aerospace, automotive, power generation |
Rapid prototyping | Faster development of new alloys | Engineering, R\&D |
Role of Nanotechnology in High-Temperature Alloys
Nanotechnology is playing an increasingly important role in the development of high-temperature alloys. By manipulating materials at the nanoscale, researchers can enhance their properties and performance in extreme conditions.
Nanoparticles and Alloy Properties
Nanoparticles are being integrated into high-temperature alloys to improve their resistance to wear, oxidation, and thermal degradation. These tiny particles can help create more stable microstructures and enhance the overall durability of the alloy. The addition of nanoparticles can also improve the strength-to-weight ratio, making the alloys more suitable for high-performance applications in aerospace and automotive industries.
Nanotechnology offers exciting possibilities for the future of high-temperature alloys. As research in this area continues, we can expect to see even more innovative materials that perform better and last longer under extreme conditions.
Nanotechnology Component | Key Benefit | Applications |
---|---|---|
Nanoparticles | Enhanced strength and oxidation resistance | Aerospace, automotive, industrial equipment |
Nano-coatings | Improved surface durability | Power generation, reactors |
Environmental Sustainability of High-Temperature Alloys
As industries strive for greater efficiency, there is also a growing emphasis on sustainability. High-temperature alloys play a key role in reducing energy consumption and minimizing waste in various applications.
Sustainable Manufacturing Practices
The development of more environmentally friendly high-temperature alloys is a priority for many industries. Innovations in alloy composition and manufacturing processes are helping reduce the environmental impact of these materials. Additionally, the recycling and reuse of high-temperature alloys are becoming more common, ensuring that valuable resources are not wasted.
Sustainable practices in the production of high-temperature alloys not only benefit the environment but also help reduce operational costs in the long term. As the demand for sustainable materials grows, we can expect to see continued innovation in this area.
Sustainable Practice | Benefit | Applications |
---|---|---|
Alloy recycling | Reduced resource waste | Aerospace, automotive, power generation |
Eco-friendly manufacturing | Lower environmental impact | Industrial machinery, reactors |
Cost-Effectiveness of Innovations in High-Temperature Alloys
As with any innovation, cost-effectiveness is a key factor in the adoption of new high-temperature alloys. Manufacturers need to balance performance improvements with the costs of research, development, and production.
Long-Term Savings
While advanced alloys may have a higher upfront cost, the long-term savings resulting from increased durability, reduced maintenance, and improved efficiency can outweigh these initial expenses. For industries like aerospace and power generation, where the cost of failure is high, investing in high-performance alloys is a cost-effective choice in the long run.
By adopting innovations in high-temperature alloys, companies can reduce downtime, lower repair costs, and improve the overall efficiency of their operations, leading to significant financial benefits over time.
Cost Factor | Benefit | Applications |
---|---|---|
Upfront cost | Improved performance and durability | Aerospace, automotive, power generation |
Long-term savings | Reduced maintenance and downtime | Industrial equipment, reactors |
Challenges in Research and Development of High-Temperature Alloys
While innovations in high-temperature alloys have come a long way, there are still many challenges to overcome. The research and development process for new materials can be time-consuming, expensive, and fraught with obstacles.
Overcoming Barriers in Material Development
One of the key challenges in developing new high-temperature alloys is the difficulty in predicting how materials will behave under extreme conditions. Research in this field requires a combination of experimentation, simulation, and real-world testing to ensure that the materials can meet the rigorous demands of industry.
Another challenge is the cost of testing and manufacturing new alloys. However, as the demand for these materials grows, investments in R\&D are expected to increase, helping accelerate the development of new high-performance alloys.
Challenge | Solution | Impact |
---|---|---|
High development cost | Investment in R\&D and testing | Accelerated innovation |
Material testing | Simulation and real-world trials | Improved material reliability |
The Future of High-Temperature Alloys
The future of high-temperature alloys is bright, with ongoing research and development pushing the boundaries of material science. As industries continue to evolve and demand even higher performance, the role of high-temperature alloys will only increase.
Emerging Trends
The integration of artificial intelligence and machine learning in alloy design is one of the most exciting trends in the field. These technologies can help accelerate the discovery of new materials and optimize existing alloys for specific applications. As new technologies and manufacturing methods emerge, we can expect even more advancements in the properties of high-temperature alloys, making them more efficient, durable, and cost-effective than ever before.
Emerging Trend | Key Benefit | Applications |
---|---|---|
Artificial intelligence | Optimized material design | Aerospace, automotive, power generation |
Advanced manufacturing | Faster development and testing | Industrial machinery, reactors |
Conclusion: The Path Forward for High-Temperature Alloys
The advancements in high-temperature alloys represent a significant step forward in materials science. As industries continue to evolve, these alloys will play an essential role in ensuring the longevity, efficiency, and safety of critical components. The future of high-temperature alloys looks promising, with innovations in composition, manufacturing, and sustainability leading the way.
FAQ Section
- What are high-temperature alloys used for?
They are primarily used in aerospace, power generation, automotive, and chemical processing industries where materials are exposed to extreme heat. - What are the most common high-temperature alloys?
Nickel-based, cobalt-based, and titanium-based alloys are the most widely used for high-temperature applications. - How does additive manufacturing impact high-temperature alloys?
Additive manufacturing allows for the creation of custom alloys and optimized designs, improving performance and reducing production time. - What challenges do researchers face in developing high-temperature alloys?
High costs, testing limitations, and the complexity of predicting material behavior under extreme conditions are key challenges. - How will high-temperature alloys evolve in the future?
Continued advancements in material composition, manufacturing technologies, and AI optimization are expected to improve performance and efficiency.