High-temperature alloys are essential in industries requiring materials that can withstand extreme conditions. These materials are used in a wide variety of applications, from aerospace engineering to power generation. With technological advancements, high-temperature alloys have become even more vital, driving innovations in performance, durability, and efficiency. In this article, we’ll explore the latest developments in the properties of high-temperature alloys, focusing on the benefits of these innovations, challenges faced by industries, and how these new materials can revolutionize the way we operate in extreme environments.
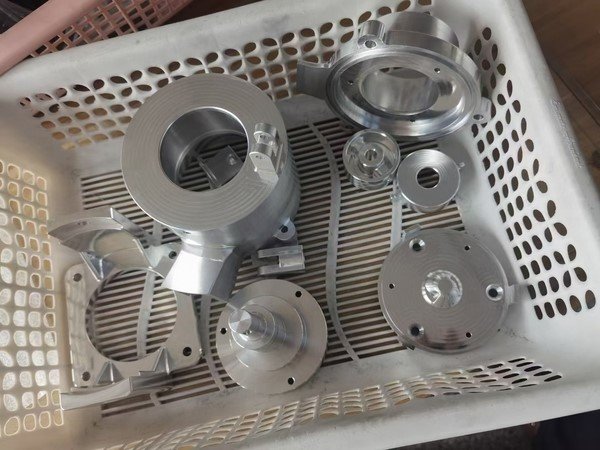
What Are High-Temperature Alloys?
High-temperature alloys are materials specifically designed to retain their strength and resist thermal fatigue, creep, and corrosion in environments with temperatures exceeding 500°C. These alloys are primarily composed of metals like nickel, cobalt, and iron, along with other elements such as chromium, molybdenum, and aluminum to enhance their properties.
High-temperature alloys are used across industries such as aerospace, automotive, chemical processing, and energy production. They are critical in turbines, jet engines, power plants, and high-performance vehicles. The alloys’ ability to withstand extreme thermal and mechanical stresses makes them indispensable in applications where reliability and durability are non-negotiable.
Material | Common Composition | Applications |
---|---|---|
Nickel Alloys | Nickel, chromium, molybdenum | Gas turbines, jet engines |
Cobalt Alloys | Cobalt, chromium, tungsten | Aerospace, petrochemical industries |
Iron-based Alloys | Iron, chromium, nickel | Power plants, industrial machinery |
As technology advances, the demand for high-performance high-temperature alloys increases. Manufacturers and researchers focus on improving these materials’ heat resistance, mechanical properties, and longevity, ensuring that they meet the growing demands of high-tech industries.
Why Are High-Temperature Alloys Important?
High-temperature alloys play an essential role in industries that require materials to perform in extreme heat environments. Their resistance to heat, corrosion, and fatigue is crucial for maintaining the reliability and safety of equipment and systems. Without these specialized materials, high-performance machinery such as jet engines, power turbines, and chemical reactors would not be able to operate efficiently or safely.
In the aerospace industry, for instance, jet engines need to withstand temperatures exceeding 1,000°C. High-temperature alloys ensure that these engines can perform optimally, reducing the risk of failure. Similarly, in power plants, turbines rely on high-temperature alloys to maintain efficiency and prevent thermal degradation, which can lead to costly downtime.
Industry | Key Applications | Challenges |
---|---|---|
Aerospace | Jet engines, gas turbines | Extreme thermal and mechanical stresses |
Power Generation | Turbines, heat exchangers | High temperatures, corrosion |
Chemical Processing | Reactors, heat exchangers | Chemical corrosion, heat resistance |
The innovations in the properties of these alloys directly impact the performance and cost-effectiveness of machinery. As industries evolve, the demand for alloys that can handle higher temperatures and greater stresses continues to rise. This has spurred research into new alloy compositions and treatments that can improve the material’s resistance to heat and fatigue.
The Challenges of High-Temperature Alloys
Despite their advantages, high-temperature alloys come with their own set of challenges. One of the primary concerns is the material’s tendency to degrade over time due to thermal fatigue, oxidation, and corrosion. Under extreme heat, metals can lose their strength, becoming brittle and prone to failure. This is especially problematic in industries like aerospace, where the cost of failure is exceptionally high.
Another significant challenge is the difficulty in manufacturing high-temperature alloys with consistent quality. Achieving the right balance of components to maximize strength, heat resistance, and durability requires precise control over the alloying process. Any variation in the composition can result in performance issues, making quality control a crucial factor in the production of high-temperature alloys.
Challenge | Impact | Solution |
---|---|---|
Thermal Fatigue | Reduced strength, cracking | Develop alloys with higher creep resistance |
Oxidation and Corrosion | Material degradation | Apply protective coatings, new alloy compositions |
Manufacturing Consistency | Variability in material properties | Improve control during the alloying process |
Addressing these challenges is key to advancing the properties of high-temperature alloys. Researchers are exploring new materials and manufacturing techniques that can mitigate these issues while ensuring that the alloys retain their exceptional performance under extreme conditions.
Recent Innovations in High-Temperature Alloys
Recent innovations in high-temperature alloys have focused on improving their resistance to extreme temperatures, enhancing mechanical properties, and extending the lifespan of the materials. One notable development is the use of superalloys, which are alloys that combine multiple elements to improve heat resistance and mechanical strength.
These superalloys are composed of a complex mixture of nickel, cobalt, and chromium, along with elements like rhenium and tantalum. The result is a material that can withstand extremely high temperatures while maintaining structural integrity. The aerospace and energy sectors are already benefiting from these innovations, with new superalloys being used in jet engine turbines and high-performance gas turbines.
Innovation | Material | Benefit |
---|---|---|
Superalloys | Nickel, cobalt, rhenium, tantalum | Higher heat resistance, better strength retention |
Coated Alloys | Ceramic, metallic coatings | Improved corrosion and oxidation resistance |
Additive Manufacturing | 3D printed alloys | Complex geometries, faster production |
Additionally, the development of coated high-temperature alloys has provided solutions to the issue of corrosion and oxidation. By applying protective coatings to the surface of these alloys, manufacturers can extend the material’s service life, reducing maintenance and replacement costs. Additive manufacturing, or 3D printing, has also revolutionized the production of high-temperature alloys. This technology allows for the creation of intricate designs that would be difficult or impossible to achieve with traditional methods, making it a game-changer for industries that require high-precision components.
How Innovations in Alloy Composition Are Improving Performance
Innovations in alloy composition have significantly contributed to improving the performance of high-temperature alloys. By adjusting the proportion of elements such as aluminum, titanium, and zirconium, manufacturers can enhance the alloy’s resistance to high temperatures and thermal degradation. For example, adding titanium improves the strength of the alloy at elevated temperatures, while aluminum can increase resistance to oxidation.
Researchers are also experimenting with novel alloy combinations to create materials that offer superior performance under extreme conditions. One promising area of research involves using rare-earth elements to further enhance the heat resistance and durability of high-temperature alloys. These elements have unique properties that can improve the alloy’s ability to withstand extreme heat without losing its mechanical strength.
Element | Effect on Alloy | Application |
---|---|---|
Titanium | Increases strength at high temperatures | Aerospace, power generation |
Aluminum | Enhances oxidation resistance | Turbines, reactors |
Rare-earth Elements | Improves heat resistance and durability | Jet engines, gas turbines |
These advancements are crucial for applications in industries like aerospace, where components are exposed to extreme heat and pressure. The continuous improvement of alloy composition ensures that high-temperature alloys can meet the ever-growing demands of these industries.
Advancements in Heat Resistance and Durability
Heat resistance is one of the most critical properties of high-temperature alloys, and recent advancements have significantly improved this characteristic. New alloy compositions are being developed that can withstand temperatures far higher than previous generations of materials. This is particularly important in industries like aerospace and power generation, where components must endure extreme temperatures for extended periods.
One of the key advancements in heat resistance is the development of alloys with higher melting points. These alloys are able to maintain their strength and integrity at temperatures that would cause older materials to degrade. Additionally, improvements in the cooling techniques used in high-temperature environments are helping to extend the life of these alloys.
Development | Benefit | Industry Impact |
---|---|---|
Higher melting points | Enhanced heat resistance | Aerospace, power generation |
Advanced cooling techniques | Reduced material degradation | Gas turbines, jet engines |
Thermal barrier coatings | Improved material longevity | Industrial reactors, turbines |
Thermal barrier coatings are another innovation that has helped improve the durability of high-temperature alloys. These coatings protect the underlying alloy from direct exposure to extreme temperatures, reducing wear and tear on the material. As these innovations continue to evolve, high-temperature alloys will be able to withstand even more extreme environments, further pushing the boundaries of technology.
Improved Creep Resistance in High-Temperature Alloys
Creep is the slow, time-dependent deformation of materials under constant stress at elevated temperatures. This phenomenon can cause significant damage to high-temperature alloys, leading to material failure. To combat this, researchers have focused on improving the creep resistance of high-temperature alloys through new alloy compositions and heat treatments.
Alloying elements such as molybdenum, tungsten, and niobium are being incorporated into high-temperature alloys to improve their creep resistance. These elements help to strengthen the material’s microstructure, reducing the rate of deformation over time. This is especially important in applications where components are exposed to constant stress, such as in turbines or reactors.
Element | Effect on Creep Resistance | Application |
---|---|---|
Molybdenum | Strengthens microstructure, improves creep resistance | Gas turbines, power plants |
Tungsten | Increases high-temperature strength | Aerospace, energy generation |
Niobium | Enhances resistance to thermal fatigue | Chemical processing, aerospace |
By enhancing creep resistance, these innovations are helping to extend the lifespan of critical components in industries like aerospace, power generation, and chemical processing. These improvements are reducing the need for frequent replacements, saving both time and money for businesses in these industries.
Alloy Coatings and Surface Treatments
Alloy coatings and surface treatments have become essential in enhancing the properties of high-temperature alloys. By applying a thin protective layer to the surface of the alloy, manufacturers can improve resistance to oxidation, corrosion, and wear. These coatings are particularly valuable in industries where components are exposed to harsh environments, such as high-temperature gas turbines or chemical reactors.
Recent advancements in coating technologies include the development of ceramic and metallic coatings that offer superior protection. These coatings can withstand extreme temperatures and are highly resistant to corrosion and oxidation. The use of these coatings has significantly improved the performance and longevity of high-temperature alloys in various applications.
Coating Type | Benefit | Application |
---|---|---|
Ceramic coatings | Excellent oxidation and corrosion resistance | Gas turbines, aerospace |
Metallic coatings | Enhanced wear resistance | Power plants, industrial machinery |
Thermal barrier coatings | Protects against extreme temperatures | Jet engines, reactors |
The application of these coatings not only improves the durability of high-temperature alloys but also enhances their performance, making them more cost-effective in the long term.
The Role of Additive Manufacturing (3D Printing) in High-Temperature Alloys
Additive manufacturing, commonly known as 3D printing, is revolutionizing the production of high-temperature alloys. This technology allows manufacturers to create complex, custom-designed components that would be difficult or impossible to achieve using traditional manufacturing methods. In the context of high-temperature alloys, 3D printing enables the creation of intricate geometries that optimize the material’s performance in high-heat environments.
3D printing also allows for faster production times and reduced material waste, making it a cost-effective alternative to traditional manufacturing techniques. Industries like aerospace and automotive are already benefiting from this technology, with manufacturers using 3D-printed high-temperature alloy components in jet engines, turbines, and other high-performance systems.
Technology | Benefit | Industry Impact |
---|---|---|
3D Printing | Custom designs, faster production | Aerospace, automotive |
Metal Additive Manufacturing | Reduced material waste, faster production | Energy, aerospace |
Complex Geometries | Optimized performance in high-heat environments | Jet engines, turbines |
The use of additive manufacturing in the production of high-temperature alloys represents a significant shift in how these materials are designed, produced, and used across industries.
Environmental Considerations in Alloy Development
As industries continue to push for more sustainable practices, the development of environmentally friendly high-temperature alloys has become a priority. Researchers are exploring ways to reduce the carbon footprint of alloy production and improve the sustainability of these materials throughout their lifecycle.
Innovations in alloy development include the use of recycled materials and the reduction of harmful emissions during the manufacturing process. Additionally, there is a growing focus on creating alloys that require fewer raw materials or that can be recycled more efficiently. These advancements are helping industries meet environmental regulations while still maintaining the high performance required for critical applications.
Innovation | Environmental Benefit | Application |
---|---|---|
Recycled Materials | Reduces raw material consumption | All industries using high-temperature alloys |
Reduced Emissions | Minimizes environmental impact of production | Manufacturing, aerospace |
Sustainable Alloy Production | Lowers carbon footprint | Automotive, power generation |
These environmentally conscious innovations are shaping the future of high-temperature alloys, making them more sustainable without sacrificing performance.
Economic Impact of Advancements in High-Temperature Alloys
The advancements in high-temperature alloys not only improve material performance but also have significant economic benefits. By developing alloys with better heat resistance, durability, and creep resistance, industries can reduce maintenance costs, increase efficiency, and extend the lifespan of critical components.
In industries like aerospace and power generation, where equipment failure can be costly, these innovations lead to fewer replacements and less downtime. This results in long-term savings for businesses while ensuring that operations remain efficient and reliable.
Economic Benefit | Impact | Industry Example |
---|---|---|
Reduced Maintenance Costs | Lower long-term operational costs | Aerospace, power plants |
Extended Equipment Lifespan | Fewer replacements, less downtime | Manufacturing, automotive |
Improved Efficiency | Higher productivity, lower costs | Energy, chemical processing |
As high-temperature alloys continue to evolve, the economic advantages for industries that rely on these materials will only increase, driving further innovation in material science.
Who Is Leading the Innovation in High-Temperature Alloys?
The development of high-temperature alloys is driven by leading manufacturers, research institutions, and industry experts. Companies specializing in material science, such as General Electric, Rolls-Royce, and Siemens, are at the forefront of innovation in high-temperature alloys.
In addition to these industry giants, academic research institutions are contributing significantly to advancements in alloy development. Collaboration between industry and academia is essential for advancing the properties of these materials and finding new solutions to the challenges faced by industries.
Organization | Contribution | Focus Area |
---|---|---|
General Electric | Development of superalloys for turbines | Aerospace, energy |
Rolls-Royce | High-performance alloys for jet engines | Aerospace |
Siemens | Innovation in turbine materials | Power generation |
These leaders in innovation are shaping the future of high-temperature alloys, ensuring that industries have access to the materials they need to perform at the highest levels.
Where Are High-Temperature Alloys Used Most Effectively?
High-temperature alloys are used across a range of industries, but their most critical applications are in aerospace, power generation, and chemical processing. In aerospace, these alloys are used in jet engines and gas turbines, where components must withstand extreme temperatures and pressures. In power generation, high-temperature alloys are used in turbines, boilers, and heat exchangers, where durability and heat resistance are essential.
Chemical processing industries also rely on high-temperature alloys for reactors and heat exchangers. These industries require materials that can withstand not only extreme temperatures but also corrosive chemicals and mechanical stresses.
Industry | Applications | Importance |
---|---|---|
Aerospace | Jet engines, gas turbines | Extreme temperature and pressure resistance |
Power Generation | Turbines, heat exchangers | Durability, heat resistance |
Chemical Processing | Reactors, heat exchangers | Resistance to heat and corrosion |
These industries benefit most from the innovations in high-temperature alloys, ensuring that their systems remain reliable and efficient.
What Are the Future Prospects for High-Temperature Alloys?
The future of high-temperature alloys is promising, with continued advancements in material science. Research is focused on developing alloys that can withstand even higher temperatures and more extreme environments. The use of additive manufacturing is also expected to grow, allowing for the creation of more complex and optimized components.
In the future, we can expect to see high-temperature alloys that are even more resistant to heat, corrosion, and fatigue, enabling industries to push the boundaries of performance and efficiency.
Innovation | Future Impact | Potential Application |
---|---|---|
Additive Manufacturing | Custom designs, faster production | Aerospace, automotive |
Advanced Alloy Compositions | Higher temperature and stress resistance | Energy, aerospace |
Sustainable Alloy Production | Lower environmental impact | Manufacturing, power generation |
These advancements will further enhance the role of high-temperature alloys in modern industry, ensuring that they remain a key material in high-performance applications.
Conclusion: The Ongoing Importance of High-Temperature Alloys and Future Innovations
In conclusion, the ongoing innovations in the properties of high-temperature alloys are vital to industries that rely on materials capable of withstanding extreme conditions. As technology continues to evolve, so too will the properties of these alloys, ensuring that they can meet the growing demands of industries such as aerospace, power generation, and chemical processing. With advancements in alloy composition, manufacturing techniques, and environmental sustainability, high-temperature alloys will continue to play a crucial role in shaping the future of industrial performance.
FAQ Section
- What are the most common applications of high-temperature alloys?
High-temperature alloys are primarily used in industries such as aerospace, power generation, and chemical processing. They are essential in components like jet engines, turbines, and reactors, where they must withstand extreme temperatures and mechanical stresses. - Why are high-temperature alloys important in extreme environments?
These alloys are crucial because they can retain strength and resist thermal degradation, corrosion, and oxidation in environments with temperatures exceeding 500°C. Their durability ensures the reliability and safety of critical systems, such as engines and turbines. - How do alloy compositions affect the performance of high-temperature alloys?
The composition of high-temperature alloys determines their heat resistance, strength, and durability. By adjusting the proportion of elements like nickel, chromium, and titanium, manufacturers can optimize alloys for specific applications that require enhanced performance in high-heat conditions. - What advancements in high-temperature alloys have occurred recently?
Recent advancements include the development of superalloys with improved heat resistance and strength, the application of thermal barrier coatings, and the integration of additive manufacturing to create more complex, efficient components. - How does additive manufacturing contribute to the production of high-temperature alloys?
Additive manufacturing, or 3D printing, allows for the creation of custom-designed, complex components with high-temperature alloys. This technology enables faster production, reduced material waste, and the ability to produce intricate geometries that optimize the performance of these materials in extreme conditions.