High-temperature alloys play an essential role in many industries, including aerospace, power generation, and chemical processing. However, these materials must endure harsh environmental conditions that can affect their performance over time. Understanding the environmental considerations that impact the properties of high-temperature alloys is critical for making informed decisions during material selection and design. In this article, we will explore the key environmental factors influencing high-temperature alloys, such as temperature extremes, corrosion, oxidation, and contaminants. We will also delve into the challenges of testing these materials and how manufacturers can mitigate the risks associated with their use.
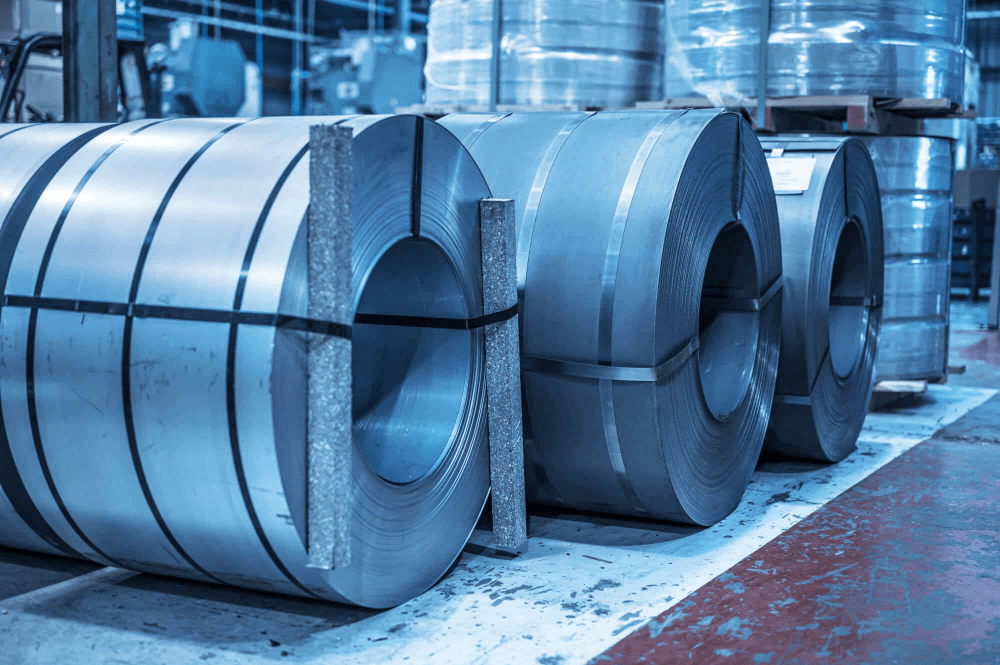
1. Introduction to High-Temperature Alloys
High-temperature alloys are engineered to withstand extreme operating conditions, such as elevated temperatures and corrosive environments. These alloys are commonly used in industries where materials are subjected to thermal stress, including aerospace, power generation, automotive, and chemical industries. Their properties, including strength, hardness, and resistance to corrosion, make them invaluable in these applications.
So, what exactly are high-temperature alloys? These materials are generally composed of a variety of metals, including nickel, cobalt, and iron, and they are designed to maintain their structural integrity and resist degradation at temperatures higher than those of conventional materials. But here’s the kicker: while these alloys are incredibly resilient, environmental factors can still impact their performance. That’s why understanding these influences is crucial for optimizing their application.
For example, when designing turbine blades for a jet engine, engineers need to ensure that the material can withstand not only high temperatures but also oxidation and corrosion from the exhaust gases. This combination of physical and chemical stressors is what makes the environmental considerations for high-temperature alloys so vital.
Table 1: Key Properties of High-Temperature Alloys
Property | Nickel-Based Alloys | Cobalt-Based Alloys | Iron-Based Alloys |
---|---|---|---|
High-Temperature Strength | High | Moderate | Low |
Corrosion Resistance | Excellent | Good | Fair |
Oxidation Resistance | High | High | Moderate |
Thermal Conductivity | Moderate | Low | High |
2. Why Environmental Considerations Matter
High-temperature alloys are designed to perform under harsh conditions, but the environment plays a crucial role in determining how long they last and how well they function. Let’s face it: ignoring environmental factors when choosing materials can lead to catastrophic failures. What’s the real story? Environmental conditions, such as temperature fluctuations, exposure to corrosive gases, and extreme stresses, can cause alloys to degrade, lose their strength, or fail prematurely.
Here’s the good part: being aware of these factors can help engineers select the right alloys and design better systems that reduce the risk of failure. Take the case of turbine blades used in jet engines. These components are subjected to extremely high temperatures, thermal stresses, and corrosion. If the wrong material is selected, the blades can degrade quickly, leading to engine failure. However, by understanding the environmental factors at play, engineers can choose alloys with better oxidation and corrosion resistance, ensuring the longevity and reliability of the turbine.
Table 2: Environmental Factors Impacting High-Temperature Alloys
Environmental Factor | Impact on Alloy Performance | Consequences |
---|---|---|
High Temperatures | Softening, creep, and oxidation | Reduced lifespan |
Corrosive Gases | Corrosion and cracking | Structural failure |
Thermal Stress | Fatigue and cracking | Material degradation |
Radiation Exposure | Alteration of material structure | Loss of strength |
3. What Are the Key Environmental Factors Affecting High-Temperature Alloys?
When it comes to high-temperature alloys, several environmental factors can affect their performance. These include extreme temperatures, oxidation, corrosion, and the presence of contaminants. What’s the deal? The higher the temperature, the more stress the alloy experiences, and this can lead to changes in its physical properties.
For instance, oxidation occurs when the alloy reacts with oxygen at high temperatures, forming a protective oxide layer. While this layer can protect the material from further degradation, it can also lead to brittleness and failure if it becomes too thick. Similarly, corrosion can occur when alloys are exposed to aggressive chemicals or gases, leading to rust or other forms of degradation. Ready for the good part? By understanding these factors, manufacturers can make better choices about which alloys to use in specific applications, ultimately increasing their lifespan and reducing the risk of failure.
Table 3: Environmental Impact on Alloy Properties
Environmental Factor | Effect on Alloy | Impact on Performance |
---|---|---|
Oxidation | Surface layer formation | Decreased strength |
Corrosion | Material breakdown | Increased wear |
Thermal Fatigue | Expansion and contraction | Cracking and fracture |
Contaminants | Chemical reaction with alloys | Reduced lifespan |
4. When Do Environmental Considerations Become Crucial?
In many cases, the significance of environmental factors becomes apparent only during certain stages of an alloy’s lifecycle. For example, during the manufacturing process, engineers may focus primarily on temperature resistance. However, once the alloy is in use, factors like corrosion resistance and thermal fatigue can become more important. This is where it gets interesting: the lifecycle stage of the alloy dictates which environmental factors will be most impactful.
For example, in the aerospace industry, materials undergo extensive testing during both the manufacturing process and operational phase. It’s not enough to just consider the temperature resistance of an alloy in a laboratory setting; engineers must also account for how the material will perform under real-world conditions, such as exposure to exhaust gases or fluctuating thermal cycles. Without this understanding, there’s a risk that the alloy will fail prematurely, leading to safety hazards and costly repairs.
Table 4: Critical Lifecycle Stages for Alloy Performance
Lifecycle Stage | Environmental Factor | Importance |
---|---|---|
Manufacturing | Temperature resistance | Crucial |
Operational Phase | Corrosion and oxidation | Crucial |
Long-Term Use | Thermal fatigue and stress | Critical |
End-of-Life/Decommission | Degradation due to chemicals | Major consideration |
5. Where Are High-Temperature Alloys Typically Used?
High-temperature alloys are used in a variety of demanding industries, including aerospace, automotive, power generation, and chemical processing. But here’s the kicker: the environment in each of these industries presents its own unique challenges, requiring alloys that can handle specific environmental stressors. Aerospace materials, for example, must resist extreme temperatures, oxidation, and thermal shock. In contrast, alloys used in power generation may need to resist corrosive gases or extreme pressure.
In the aerospace sector, alloys are subjected to not only extreme temperatures but also mechanical stress and radiation. For instance, the turbine blades in jet engines operate at temperatures exceeding 1,000°C and are exposed to high-velocity exhaust gases, requiring alloys with exceptional oxidation resistance and strength. Meanwhile, in power plants, alloys must withstand both high temperatures and corrosive gases, which can lead to erosion and wear over time.
Table 5: Applications of High-Temperature Alloys in Different Industries
Industry | Specific Use | Environmental Challenge |
---|---|---|
Aerospace | Turbine blades, exhaust systems | High temperatures, oxidation |
Power Generation | Steam turbines, reactors | Corrosive gases, high pressure |
Automotive | Engine components, exhaust systems | Thermal stress, oxidation |
Chemical Processing | Heat exchangers, reactors | Corrosion, aggressive chemicals |
6. The Impact of Temperature on Alloy Properties
High-temperature alloys are designed to withstand extreme heat, but high temperatures affect more than just the strength of these materials. They can also alter the thermal expansion and contraction of the alloy, potentially leading to thermal fatigue. But here’s the kicker: at high temperatures, alloys are also more susceptible to oxidation, which can degrade the surface and reduce the material’s overall strength.
For example, metals like nickel-based alloys exhibit excellent resistance to thermal fatigue and thermal expansion. However, when exposed to temperatures exceeding their critical limits, they begin to soften, leading to changes in their strength, hardness, and resistance to further degradation. Ready for the good part? The higher the temperature, the more susceptible alloys are to these changes. That’s why engineers must carefully consider both the maximum operating temperature and the thermal cycling conditions when selecting materials for high-temperature applications.
Table 6: Temperature Effects on Alloy Properties
Temperature Range | Effect on Alloy Properties | Consequences |
---|---|---|
Below 500°C | Minimal change in properties | Stable performance |
500°C – 800°C | Moderate softening | Decreased strength |
800°C – 1000°C | Significant oxidation | Loss of integrity |
Above 1000°C | Severe thermal fatigue | Cracking and failure |
7. Corrosion Resistance in High-Temperature Alloys
Corrosion is one of the most significant challenges faced by high-temperature alloys, especially when exposed to aggressive environments such as high humidity or corrosive gases. What’s the deal? When alloys come into contact with these elements, they can form rust or other types of corrosion, which weaken the material over time.
In high-temperature environments, corrosion occurs due to chemical reactions between the material and gases like sulfur, chlorine, or oxygen. But here’s the kicker: corrosion resistance is crucial to the longevity and performance of high-temperature alloys. For example, coatings or surface treatments are often used to improve the alloy’s resistance to corrosion. By selecting alloys with the right chemical composition and protective coatings, manufacturers can minimize the risk of corrosion and extend the life of critical components.
Table 7: Corrosion Resistance of Common High-Temperature Alloys
Alloy Type | Corrosion Resistance | Common Applications | Ideal Operating Conditions |
---|---|---|---|
Nickel-Based Alloys | Excellent | Aerospace, power plants | High temperatures, oxidative environments |
Cobalt-Based Alloys | Good | Chemical processing | High heat, moderate corrosive exposure |
Iron-Based Alloys | Fair | Automotive, general industrial | Low to medium temperature, low corrosive environments |
8. How Do High-Temperature Alloys Resist Oxidation?
Oxidation occurs when high-temperature alloys react with oxygen in the air, forming an oxide layer on the surface. This oxide layer can help protect the material from further degradation, but it can also cause brittleness if it becomes too thick. What’s the real story? The alloy’s ability to resist oxidation is key to ensuring its longevity and effectiveness under extreme conditions.
Ready for the good part? Engineers often choose alloys with a high content of elements like chromium and aluminum, which promote the formation of a thin, protective oxide layer. This layer prevents further oxidation from occurring, extending the alloy’s useful life. For example, chromium-based alloys exhibit excellent oxidation resistance, which is why they are commonly used in jet engine components. However, over time, even the most resistant alloys can experience oxidation if exposed to harsh conditions for extended periods.
Table 8: Oxidation Resistance of High-Temperature Alloys
Alloy Type | Oxidation Resistance | Benefits | Limitations |
---|---|---|---|
Chromium-Based Alloys | High | Excellent for high-heat applications | Prone to cracking under thermal shock |
Aluminum-Based Alloys | Moderate | Effective in moderately high temperatures | Less suitable for extreme environments |
Nickel-Based Alloys | High | Widely used in aerospace | May require additional coatings for maximum resistance |
9. Effects of Contaminants on Alloy Properties
Contaminants, both external and internal, can have a significant impact on the performance of high-temperature alloys. The presence of contaminants such as sulfur or chlorine can react with the material, causing it to degrade over time. But here’s the kicker: not only external contaminants can affect alloy properties, but internal contamination during the manufacturing process can also play a significant role.
For example, impurities in the raw materials used to produce the alloy can weaken the final product. Ready for the good part? Ensuring the purity of the raw materials and controlling the manufacturing environment is essential to maintaining the high-performance capabilities of the alloy. By doing so, manufacturers can prevent contamination-related failures and extend the lifespan of their products.
Table 9: Common Contaminants and Their Effects on Alloys
Contaminant | Effect on Alloy | Impact on Performance |
---|---|---|
Sulfur | Formation of sulfides | Reduced strength and corrosion resistance |
Chlorine | Chlorine-induced corrosion | Severe material degradation in harsh environments |
Oxygen | Oxidation | Loss of strength and ductility |
Nitrogen | Formation of nitrides | Hardness increase but reduced toughness |
10. The Role of Alloy Composition in Environmental Resistance
Alloy composition plays a critical role in how well high-temperature alloys can withstand environmental stressors. The key elements in the alloy determine its resistance to factors like oxidation, corrosion, and thermal fatigue. What’s the deal? By carefully selecting alloying elements, engineers can design materials that are optimized for specific environmental conditions.
For example, nickel-based alloys are often chosen for high-temperature applications due to their excellent strength and oxidation resistance. On the other hand, cobalt-based alloys are used in applications where higher resistance to thermal fatigue and corrosion is needed. Ready for the good part? The composition of the alloy not only impacts its resistance to environmental stressors but also affects its overall performance, making the selection of the right alloy essential to ensuring long-lasting and reliable results.
Table 10: Alloy Composition and Its Impact on Performance
Alloy Type | Composition Elements | Environmental Resistance | Applications |
---|---|---|---|
Nickel-Based Alloys | Nickel, Chromium, Molybdenum | Excellent oxidation and thermal resistance | Aerospace, power generation |
Cobalt-Based Alloys | Cobalt, Chromium, Tungsten | High thermal fatigue resistance | Chemical processing, turbines |
Iron-Based Alloys | Iron, Carbon, Manganese | Moderate corrosion resistance | Automotive, general manufacturing |
11. Challenges in Testing and Measuring Alloy Resistance to Environmental Factors
Testing high-temperature alloys for their ability to withstand environmental conditions is no easy feat. What’s the real story? Manufacturers must simulate real-world conditions as accurately as possible, which can be challenging due to the complex interactions between the alloy and its environment. From temperature fluctuations to exposure to corrosive gases, the testing process must account for a wide range of variables.
Ready for the good part? Innovations in testing techniques are making it easier to predict how alloys will perform under harsh conditions. New technologies, such as advanced thermal cycling tests and environmental simulation chambers, are allowing engineers to assess alloy performance in a more controlled, repeatable way. By using these techniques, manufacturers can ensure that their high-temperature alloys will perform as expected in real-world applications.
Table 11: Testing Methods for High-Temperature Alloys
Test Method | Purpose | Application |
---|---|---|
Thermal Cycling Test | Simulate thermal stress | Aerospace, automotive |
Corrosion Resistance Test | Assess reaction to corrosive gases | Power generation, chemical processing |
Oxidation Test | Measure oxidation resistance | Aerospace, high-performance engineering |
12. Environmental Impact of Manufacturing High-Temperature Alloys
The production of high-temperature alloys is energy-intensive and often results in significant environmental impacts. Ready for the good part? As the demand for these materials grows, manufacturers are facing increasing pressure to adopt more sustainable practices. High-temperature alloys often require a significant amount of energy to produce, which can result in a high carbon footprint.
For example, nickel-based alloys are typically produced through smelting processes that release greenhouse gases. But here’s the kicker: many manufacturers are exploring ways to reduce the environmental impact of alloy production by implementing more energy-efficient practices and using cleaner technologies. This includes adopting alternative energy sources and improving the recycling rates of alloy components.
Table 12: Environmental Impact of Alloy Production
Production Stage | Environmental Impact | Mitigation Strategy |
---|---|---|
Mining Raw Materials | Habitat destruction, emissions | Sustainable mining practices |
Smelting and Refining | Greenhouse gas emissions | Energy-efficient technologies |
Alloy Processing | Energy consumption, waste | Recycling and waste reduction |
13. Future Trends in High-Temperature Alloy Development
The development of high-temperature alloys is an ongoing process, driven by advances in materials science and manufacturing technologies. What’s the deal? Researchers and manufacturers are constantly working to improve the performance of these alloys by enhancing their resistance to environmental stressors, such as oxidation and corrosion.
Ready for the good part? Emerging technologies like nanotechnology and additive manufacturing are making it possible to create alloys with better performance characteristics and more sustainable production methods. By harnessing these innovations, manufacturers can create alloys that meet the growing demands of industries like aerospace, power generation, and automotive, while also reducing their environmental impact.
Table 13: Future Trends in Alloy Development
Trend | Description | Impact on Performance |
---|---|---|
Nanotechnology | Enhanced material properties | Improved strength, oxidation resistance |
Additive Manufacturing | 3D printing for alloy parts | Customization, waste reduction |
Green Manufacturing | Sustainable alloy production | Lower carbon footprint |
14. Case Studies of High-Temperature Alloys in Extreme Environments
High-temperature alloys are put to the test in some of the most extreme environments on Earth. Take the aerospace industry, for example, where turbine blades are exposed to extreme heat, pressure, and thermal cycling. Ready for the good part? These components rely heavily on the properties of high-temperature alloys to ensure they perform safely and reliably.
Aerospace engineers use a combination of nickel-based alloys and cobalt-based alloys to create turbine blades that can withstand the harsh conditions inside jet engines. By carefully selecting the right materials, manufacturers can ensure the components remain strong and reliable throughout their operational life. This is just one example of how high-temperature alloys are used in extreme environments to perform essential functions.
Table 14: Aerospace Case Study: Turbine Blade Material Performance
Alloy Type | Temperature Range (°C) | Application | Performance |
---|---|---|---|
Nickel-Based Alloys | 800-1,100 | Turbine blades | High oxidation resistance |
Cobalt-Based Alloys | 700-1,000 | Turbine blades | Excellent thermal fatigue resistance |
Iron-Based Alloys | 400-800 | General components | Moderate performance in high temperatures |
15. Conclusion: Balancing Performance and Environmental Considerations
As industries continue to demand higher performance from their materials, understanding the environmental considerations for high-temperature alloys becomes even more important. The right alloy selection can make all the difference in ensuring the longevity and reliability of critical components.
By choosing alloys that are resistant to oxidation, corrosion, and thermal fatigue, manufacturers can extend the lifespan of their products while also ensuring they can withstand the harshest environments. Ready for the good part? With continuous advancements in alloy development and testing methods, the future looks promising for high-temperature alloys, and industries can look forward to even better performance and sustainability.
FAQ Section
Q1: What are high-temperature alloys?
High-temperature alloys are materials designed to withstand extreme temperatures, often above 500°C. They are used in industries like aerospace, power generation, and automotive, where materials face thermal and mechanical stress.
Q2: How do environmental factors impact high-temperature alloys?
Environmental factors such as temperature, oxidation, corrosion, and contaminants can degrade the performance of high-temperature alloys, leading to material failure or reduced efficiency.
Q3: Why is corrosion resistance important for high-temperature alloys?
Corrosion resistance is crucial because exposure to aggressive gases or chemicals can cause alloys to degrade, reducing their strength and lifespan, especially in high-heat environments.
Q4: How are high-temperature alloys tested for environmental resistance?
High-temperature alloys are tested through simulated conditions like thermal cycling, corrosion exposure, and oxidation tests to evaluate their performance in real-world environments.
Q5: What are the future trends in high-temperature alloy development?
Future trends include innovations like nanotechnology and additive manufacturing, which improve alloy performance and sustainability while reducing the environmental impact of production.