High-temperature alloys are crucial in industries such as aerospace, automotive, and power generation, where extreme heat is a constant challenge. However, many misconceptions about these alloys can lead to improper applications and maintenance issues. This article will address some of the most common myths and provide clarity on their properties, performance, and practical uses. By dispelling these myths, we can improve the understanding and application of high-temperature alloys, ensuring that these materials meet their potential and continue to drive innovation across industries.
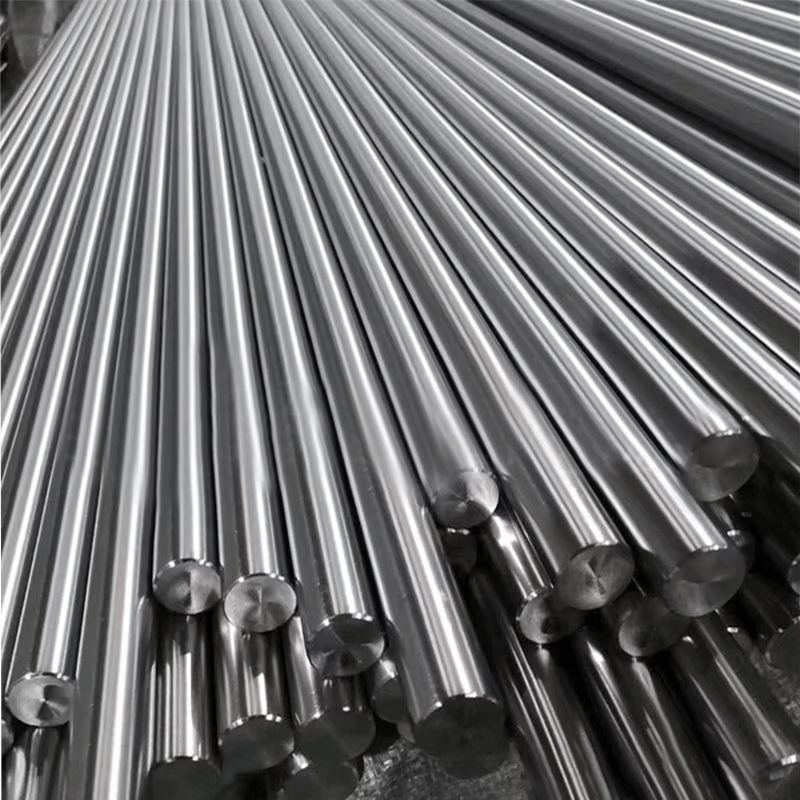
1. Introduction: Understanding High-Temperature Alloys
When discussing high-temperature alloys, it’s easy to assume that these materials are flawless, built to endure any extreme condition without a second thought. But here’s the kicker: there are many misconceptions about their properties that can lead to costly mistakes in the manufacturing process. It’s essential for professionals in industries such as aerospace and power generation to understand what high-temperature alloys are truly capable of.
High-temperature alloys are materials designed to maintain their strength and structural integrity at elevated temperatures. These alloys are engineered to resist thermal expansion, corrosion, and degradation under extreme heat, which makes them indispensable in critical components like turbine blades, engine parts, and reactors. However, common misconceptions can skew perceptions about their limitations and lifespan.
Understanding the true nature of these alloys helps engineers, manufacturers, and procurement managers make informed decisions. What’s the real story behind these materials? Let’s dive into some of the most widespread myths and explore what’s fact and what’s fiction.
Misconception | Reality |
---|---|
High-temperature alloys are indestructible under heat | They can degrade over time due to oxidation, corrosion, and mechanical stress. |
All high-temperature alloys have the same properties | Different alloys have varying properties depending on their composition and intended application. |
High-temperature alloys require no maintenance | Like all materials, they need regular inspection and maintenance to maintain performance. |
High-temperature alloys are always too expensive | Many offer a balance of cost and performance, making them suitable for long-term use. |
2. What Are High-Temperature Alloys?
High-temperature alloys are materials primarily designed to withstand the extreme conditions found in high-stress environments. These alloys are essential when working with machinery and components that are exposed to elevated temperatures, such as those found in turbines, jet engines, and heat exchangers.
Ready for the good part? High-temperature alloys are typically made from a combination of metals such as nickel, cobalt, and iron, along with additional elements like chromium, molybdenum, and aluminum to enhance specific properties. These alloys are known for their resistance to oxidation and creep, a phenomenon where materials gradually deform under stress at high temperatures.
It’s important to note that not all high-temperature alloys are created equal. For example, nickel-based alloys are often used in high-temperature environments because of their excellent heat resistance. On the other hand, cobalt-based alloys offer superior wear resistance. Understanding these differences is crucial when selecting the right alloy for a particular application.
3. Why Are High-Temperature Alloys Crucial?
High-temperature alloys play a pivotal role in ensuring the safety and efficiency of industrial processes, especially in sectors like aerospace, automotive, and power generation. But here’s the thing: they’re not just about withstanding heat; they also need to maintain structural integrity under mechanical stress. Without high-temperature alloys, the performance of jet engines, gas turbines, and reactors would be significantly compromised.
What’s the real story? These alloys are specifically engineered to function in harsh environments where other materials might fail. Their ability to resist high-temperature oxidation, corrosion, and mechanical deformation makes them indispensable in components that operate at extreme temperatures. These properties not only enhance the lifespan of the components but also contribute to the safety and reliability of critical infrastructure.
For example, in the aerospace industry, high-temperature alloys ensure that turbine blades and exhaust systems can withstand the intense heat generated during flight. Similarly, in power plants, these alloys are used in the construction of heat exchangers and reactors, which are constantly exposed to high temperatures.
Alloy Type | Key Application | Advantages |
---|---|---|
Nickel-based alloys | Turbine blades, jet engines | High heat resistance, excellent creep resistance |
Cobalt-based alloys | High-performance machinery | Superior wear resistance, oxidation resistance |
Iron-based alloys | Heat exchangers, reactors | Cost-effective, good resistance to oxidation |
4. Common Misconceptions About High-Temperature Alloys
What’s the catch? One of the biggest misconceptions about high-temperature alloys is the belief that they are invincible under extreme heat. While it’s true that these alloys can withstand higher temperatures than many materials, they are not immune to degradation. Over time, high temperatures can cause oxidation, material fatigue, and other forms of wear.
Another common misconception is that all high-temperature alloys are essentially the same. In reality, different alloys are designed for different applications, and their properties vary depending on their composition. For instance, alloys made from nickel are often chosen for their excellent heat resistance, while cobalt-based alloys offer superior wear resistance.
Some people also assume that high-temperature alloys require no maintenance. But here’s where it gets interesting: just like any material exposed to high-stress conditions, these alloys require regular inspection and maintenance to ensure they continue to perform as expected.
Misconception | Impact on Use | Why It’s Incorrect |
---|---|---|
High-temperature alloys are indestructible | Leads to neglect in maintenance | These alloys degrade over time and need regular inspection. |
All high-temperature alloys are the same | Incorrect alloy selection | Different alloys offer unique benefits for different applications. |
High-temperature alloys require no maintenance | Can lead to failures and unexpected downtime | Even the best alloys need regular upkeep to maintain performance. |
5. What Makes High-Temperature Alloys Different from Other Alloys?
High-temperature alloys stand apart from other types of alloys due to their unique ability to retain strength and resist deformation at elevated temperatures. Unlike standard alloys, which may become soft or lose structural integrity when exposed to heat, high-temperature alloys are designed to maintain their properties even under extreme conditions.
Ready for the good part? High-temperature alloys typically include additional elements such as molybdenum, tungsten, or niobium, which improve their ability to withstand high heat and mechanical stress. For example, nickel-based alloys are often used in aerospace applications due to their excellent resistance to heat and corrosion, while cobalt-based alloys are chosen for their wear resistance in industrial machinery.
What’s the real story here? It’s the combination of elements that makes high-temperature alloys so effective. The carefully engineered compositions allow these alloys to thrive in environments that would cause standard alloys to fail. This ability to perform under stress and heat is what sets them apart and makes them so valuable across various industries.
Element | Property | Application |
---|---|---|
Nickel | Heat resistance, corrosion resistance | Aerospace, power generation |
Cobalt | Wear resistance, oxidation resistance | Industrial machinery, turbine blades |
Molybdenum | High-temperature strength, creep resistance | Jet engines, gas turbines |
6. The Truth Behind Their Durability
High-temperature alloys are often thought of as indestructible, but here’s the kicker: their durability is not limitless. Like all materials, high-temperature alloys have a finite lifespan and can degrade over time. Factors such as heat exposure, oxidation, and mechanical stress can all contribute to the eventual failure of these materials.
What’s the real story? The key to maximizing the durability of high-temperature alloys lies in proper material selection, design, and regular maintenance. Regular inspections are necessary to identify signs of wear and prevent catastrophic failure. For example, turbine blades used in jet engines may begin to show signs of oxidation or fatigue after years of service, requiring replacement or repair.
But here’s the good news: when maintained properly, high-temperature alloys can last for many years, ensuring reliable performance in the most demanding environments. Ensuring the right balance of materials, design, and maintenance is key to their longevity.
Factor | Impact on Durability | Best Practices |
---|---|---|
Heat exposure | Accelerates oxidation and fatigue | Regular inspection, material selection |
Mechanical stress | Leads to deformation, fatigue | Design for stress tolerance, maintenance |
Corrosion | Affects long-term performance | Use corrosion-resistant alloys, coatings |
7. How Do High-Temperature Alloys Respond to Stress?
High-temperature alloys are specifically designed to withstand the stresses encountered in high-temperature environments. But here’s where it gets interesting: stress doesn’t just refer to mechanical forces, but also the continuous exposure to extreme heat, which can cause materials to deform over time. The phenomenon known as creep can cause high-temperature alloys to gradually change shape under constant stress.
What’s the real story? Over time, even the strongest high-temperature alloys will begin to show signs of creep and fatigue if exposed to sustained stress. This can lead to material deformation, which compromises the alloy’s strength and performance. However, when properly designed and maintained, high-temperature alloys can resist these effects for extended periods, making them ideal for critical applications such as turbine blades and exhaust systems.
What’s the takeaway? It’s not just about heat resistance; it’s also about understanding how these materials perform under stress over time. Engineers must carefully consider both the temperature and mechanical forces that the alloys will be subjected to in order to choose the right material for each application.
Stress Factor | Impact on Alloy Performance | Preventive Measures |
---|---|---|
High temperature | Increases risk of oxidation and creep | Material selection, cooling techniques |
Mechanical forces | Can cause deformation and fatigue | Proper design, stress testing |
Continuous exposure | Leads to long-term degradation | Regular maintenance, inspections |
8. Why Aren’t High-Temperature Alloys Always the Best Choice?
While high-temperature alloys are indispensable in certain applications, they are not always the best choice for every situation. Here’s the kicker: when selecting materials for specific applications, cost, performance, and availability must all be considered. Sometimes, alternatives like ceramics, composites, or even other metals may offer better value or performance for the given conditions.
What’s the real story? High-temperature alloys are often more expensive than alternative materials. In applications where cost is a major concern and the temperature extremes are not as severe, other materials may perform just as well at a lower cost. However, for mission-critical components like those found in jet engines or nuclear reactors, high-temperature alloys remain the best choice due to their unmatched performance under extreme conditions.
It’s all about balance: understanding the application requirements and the trade-offs between cost, performance, and material longevity.
Material | Advantages | Limitations |
---|---|---|
High-temperature alloys | Heat resistance, durability | Higher cost, maintenance requirements |
Ceramics | High temperature resistance | Brittle, challenging to manufacture |
Composites | Lightweight, good thermal performance | Limited heat resistance, cost |
9. How Are High-Temperature Alloys Manufactured?
The manufacturing process for high-temperature alloys is both complex and critical to ensuring the final product meets the required specifications. But here’s the kicker: the process varies depending on the type of alloy and the specific application. Methods such as casting, forging, and powder metallurgy are commonly used to produce high-temperature alloys, each offering unique benefits for different types of components.
What’s the real story? The key to producing high-quality high-temperature alloys lies in controlling the composition and processing conditions. Each step, from alloying the metals to shaping and finishing the parts, must be carefully controlled to achieve the desired properties.
Let’s break it down: whether it’s through casting for larger, intricate components or powder metallurgy for high-precision parts, the manufacturing process is crucial to ensure the material performs as intended under extreme conditions.
Manufacturing Method | Key Benefits | Applications |
---|---|---|
Casting | Suitable for large, complex parts | Turbine blades, reactor components |
Forging | Improved material strength, structural integrity | Engine parts, shafts |
Powder metallurgy | High precision, reduced waste | Aerospace components, small parts |
10. How to Select the Right High-Temperature Alloy for Your Needs?
Choosing the right high-temperature alloy can be a daunting task, but here’s the kicker: with the right knowledge and guidance, it’s easier than you think. Understanding the specific needs of your application is the first step in selecting the right alloy.
What’s the real story? Consider factors like the operational temperature, mechanical stress, and corrosion resistance requirements. For example, in aerospace applications, the alloy must resist both high temperatures and the corrosive effects of jet fuel. In contrast, industrial machinery might prioritize wear resistance over heat resistance.
Here’s the deal: the key is matching the material properties with the specific demands of the application. Consulting with material experts and conducting tests are crucial steps in making the right decision.
Factor | Consideration | Examples |
---|---|---|
Temperature resistance | How well does the alloy withstand heat? | Nickel alloys for aerospace |
Corrosion resistance | Will the material be exposed to corrosive substances? | Cobalt alloys for industrial applications |
Strength | How much mechanical stress will the alloy endure? | High-strength alloys for turbine blades |
11. The Role of High-Temperature Alloys in Aerospace and Defense
In the aerospace and defense industries, high-temperature alloys are indispensable. But here’s the kicker: these alloys must not only withstand extreme heat but also perform reliably under continuous stress, vibration, and corrosive environments. From turbine blades to exhaust systems, high-temperature alloys ensure the safety and efficiency of aircraft engines and defense machinery.
What’s the real story? In the aerospace industry, turbine blades must endure temperatures exceeding 1,000°C while maintaining their structural integrity. High-temperature alloys, such as nickel-based and cobalt-based alloys, are essential for these demanding applications due to their ability to resist oxidation, creep, and fatigue.
Here’s the good news: when engineered properly, these alloys enable aircraft to perform safely and efficiently, even in the harshest environments. From fighter jets to commercial airliners, high-temperature alloys are critical to the advancement of aerospace technology.
Application | Alloy Type | Function |
---|---|---|
Turbine blades | Nickel-based alloys | High temperature resistance, structural integrity |
Exhaust systems | Cobalt-based alloys | Wear resistance, corrosion resistance |
Aerospace engines | Iron-based alloys | Cost-effective, good high-temperature performance |
12. Environmental Considerations: How High-Temperature Alloys Perform in Different Conditions
High-temperature alloys must be capable of performing in a wide range of environmental conditions, including exposure to high humidity, saltwater, and corrosive gases. But here’s the kicker: environmental factors can significantly impact the performance and lifespan of these alloys. For example, alloys used in offshore oil rigs or chemical plants must withstand harsh conditions such as high salt content and chemical exposure.
What’s the real story? The performance of high-temperature alloys is not just about temperature resistance; environmental factors like moisture, corrosive gases, and chemical exposure play a huge role. Alloys that perform well in one environment may not be as effective in another.
Here’s the deal: for industries that operate in corrosive environments, selecting high-temperature alloys with enhanced corrosion resistance, such as those with chromium or molybdenum, can significantly increase the lifespan and reliability of components.
Environment | Challenges | Alloy Selection |
---|---|---|
Offshore oil rigs | Saltwater corrosion, high humidity | Cobalt-based alloys, corrosion-resistant alloys |
Chemical plants | Exposure to harsh chemicals, heat | Nickel-based alloys, high-temperature alloys with chemical resistance |
Aerospace | High altitude, extreme heat | Nickel-based alloys, fatigue-resistant alloys |
13. The Future of High-Temperature Alloys
The future of high-temperature alloys looks promising, but here’s the kicker: the demand for better performance, sustainability, and efficiency is pushing the boundaries of material science. Researchers are constantly working to develop alloys that can withstand even higher temperatures and harsh environments while being more cost-effective and environmentally friendly.
What’s the real story? Future innovations may include alloys that are lighter, stronger, and more resistant to degradation over time. New alloy compositions, such as those that incorporate advanced ceramics or composites, are being explored for their potential to outperform current materials in certain applications.
Here’s the good news: advances in material science are opening up exciting possibilities for high-temperature alloys, and we can expect to see even more efficient and durable alloys in the years to come.
Innovation | Potential Benefits | Application |
---|---|---|
Lightweight alloys | Reduced weight, increased fuel efficiency | Aerospace, automotive |
Composite materials | Higher strength, enhanced performance | Jet engines, power generation |
Sustainable alloys | Reduced environmental impact, cost-effective | Power plants, chemical industries |
14. Case Study: The Misconceptions that Led to Failures in High-Temperature Alloy Use
In some cases, misconceptions about high-temperature alloys have led to major failures. But here’s where it gets interesting: understanding the true properties of these materials could have prevented costly mistakes. For example, a company may have chosen a nickel-based alloy for a high-temperature application without realizing it wasn’t the best option due to environmental conditions such as high moisture or corrosion.
What’s the real story here? By understanding the specific limitations of each alloy type, engineers can make more informed decisions, avoiding mistakes that could lead to equipment failure or safety hazards. Regular inspections, proper maintenance, and material selection based on the application are essential to preventing such failures.
Failure Example | Contributing Factors | Solution |
---|---|---|
Turbine failure | Incorrect alloy selection, neglecting environmental factors | Proper material testing, tailored alloy selection |
Exhaust system failure | Lack of regular maintenance, incorrect alloy for environment | Routine inspections, use of corrosion-resistant alloys |
15. Conclusion: Setting the Record Straight About High-Temperature Alloys
High-temperature alloys are essential in industries that demand high performance and reliability. But here’s the kicker: understanding the truth about these alloys and dispelling common misconceptions can make all the difference in selecting the right material for your applications. By choosing the correct high-temperature alloy and following best practices for maintenance and inspection, industries can avoid costly mistakes and improve the lifespan of their components.
What’s the real story? High-temperature alloys are not invincible, and they require careful selection, regular maintenance, and environmental consideration. With the right knowledge and application, these alloys continue to drive innovation and performance in sectors that rely on extreme heat resistance.
Q1: What are high-temperature alloys?
High-temperature alloys are materials designed to withstand extreme heat while maintaining their strength and structural integrity. They are used in industries like aerospace, automotive, and power generation.
Q2: Why are high-temperature alloys important?
High-temperature alloys are critical in applications where materials are exposed to extreme temperatures. They ensure the safe and efficient operation of engines, turbines, and reactors by maintaining their properties under heat and stress.
Q3: How are high-temperature alloys made?
High-temperature alloys are typically made using casting, forging, or powder metallurgy processes. These methods ensure the final product has the desired properties for specific high-temperature applications.
Q4: What’s the lifespan of high-temperature alloys?
The lifespan of high-temperature alloys depends on factors like temperature, stress, and exposure to corrosive elements. With proper maintenance, these alloys can last for many years, but they still require regular inspection and upkeep.
Q5: How do I select the right high-temperature alloy?
Selecting the right high-temperature alloy involves understanding the specific requirements of the application, including temperature, corrosion resistance, and mechanical stress. It’s essential to consult experts and conduct material tests for optimal alloy selection.