Heat-resistant metals are critical components in industries where extreme temperatures are a common challenge. They enable machines, engines, and other equipment to operate effectively in high-heat environments. This article will delve into the various aspects of heat-resistant metals, exploring their properties, types, applications, and the crucial role they play in multiple industries. Ready for the good part? Let’s dive deeper into the world of these specialized metals and uncover why they are indispensable in modern manufacturing.
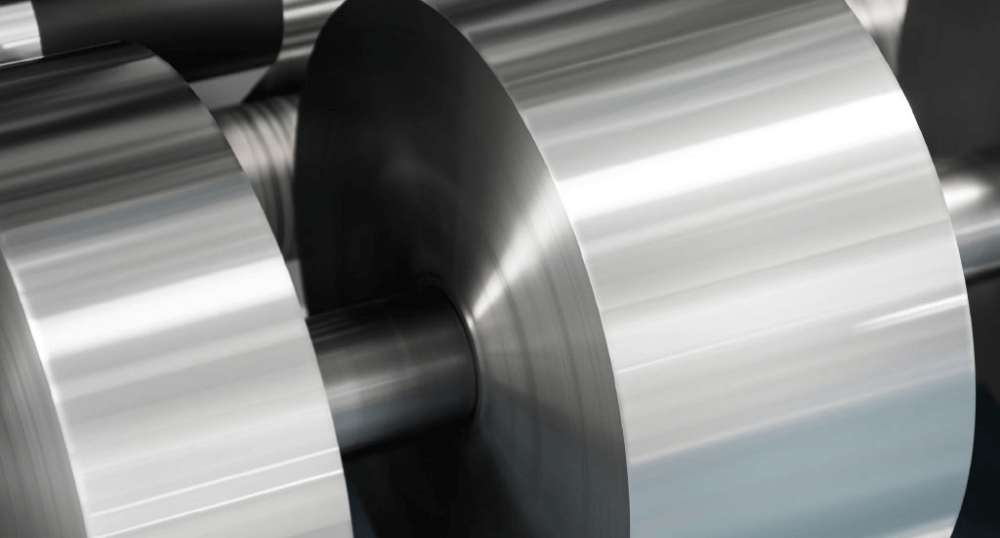
1. Introduction to Heat-Resistant Metals
Heat-resistant metals are materials specifically designed to retain their strength, durability, and structural integrity even at high temperatures. These metals are essential for industries such as aerospace, automotive, and energy production, where components must withstand temperatures that would cause regular metals to degrade quickly. What’s the real story? Heat-resistant alloys like stainless steel, titanium, and nickel-based metals are engineered to handle these extreme conditions without losing performance.
These metals are often used in environments where temperatures exceed 500°C, which can compromise the functionality of standard metals. In the aerospace industry, for example, heat-resistant alloys are used to create turbine blades, engine components, and exhaust systems—parts that experience intense heat during flight. The versatility and reliability of these materials make them invaluable, ensuring the safety, performance, and longevity of critical components.
To fully understand heat-resistant metals, we must first look at their unique properties. These materials are made from specific alloys that combine metals like nickel, chromium, and molybdenum, each contributing to the metal’s heat tolerance. What’s more, these metals also have excellent oxidation resistance, which allows them to maintain their form even in high-oxygen environments.
Here’s the kicker: The high-performance properties of heat-resistant metals are not just about withstanding heat. These metals also provide exceptional strength-to-weight ratios, which are crucial in industries like aviation, where every ounce matters. This combination of features makes heat-resistant metals a perfect fit for demanding applications.
Type of Metal | Common Use | Key Properties |
---|---|---|
Stainless Steel | Automotive, Aerospace | Corrosion-resistant, high temperature tolerance |
Titanium Alloys | Aerospace, Marine | Light, strong, resistant to oxidation |
Nickel Alloys | High-temperature applications | Excellent heat resistance, oxidation resistance |
2. What Makes a Metal Heat-Resistant?
The secret to a metal’s heat resistance lies in its chemical composition and the way it is processed. What’s the real story? Heat-resistant metals are typically made from alloys, which are combinations of two or more metals that enhance specific properties, such as heat resistance, strength, and corrosion resistance. For example, alloys made with nickel or chromium can significantly improve the metal’s ability to resist high temperatures.
Heat-resistant metals are designed to retain their strength and integrity even at extreme temperatures. This is accomplished through special alloying elements like chromium, which forms a protective oxide layer on the metal’s surface, preventing oxidation and corrosion. Ready for the good part? These metals are also engineered to avoid thermal expansion, which could otherwise lead to cracks or warping when exposed to heat.
The manufacturing process also plays a crucial role in making a metal heat-resistant. High-performance metals undergo precise processing methods such as forging, casting, and heat treatment. These techniques refine the metal’s microstructure, improving its heat resistance and overall performance. The result is a material that can endure high temperatures without compromising its mechanical properties.
Metal Type | Alloying Elements | Temperature Resistance Range |
---|---|---|
Stainless Steel | Chromium, Nickel | Up to 800°C |
Titanium | Aluminum, Vanadium | Up to 600°C |
Nickel Alloys | Nickel, Molybdenum | 800°C to 1000°C |
3. Types of Heat-Resistant Metals
Heat-resistant metals come in various types, each offering specific benefits depending on the intended application. This is where it gets interesting: Let’s explore some of the most commonly used metals in high-heat environments.
- Stainless Steel – Stainless steel is one of the most widely used heat-resistant metals due to its corrosion resistance and ability to withstand high temperatures. With various grades available, stainless steel is often used in automotive exhaust systems, industrial equipment, and kitchen appliances.
- Titanium Alloys – Titanium alloys are lightweight yet incredibly strong, making them ideal for aerospace applications where weight is crucial. These alloys can resist oxidation at high temperatures, which makes them a favorite for engine components and turbine blades.
- Nickel Alloys – Nickel-based alloys, such as Inconel and Hastelloy, are famous for their excellent high-temperature strength and oxidation resistance. These alloys are used extensively in power plants, chemical processing, and jet engines, where extreme heat is a constant challenge.
Each of these metals has unique properties that make them suitable for specific industries. Here’s the kicker: The choice of metal depends not only on the temperature requirements but also on other factors such as weight, strength, and resistance to environmental factors like moisture and corrosive chemicals.
Metal Type | Best Use Case | Key Advantage |
---|---|---|
Stainless Steel | Automotive, Appliances | Corrosion resistance, cost-effective |
Titanium Alloys | Aerospace | Lightweight, high strength-to-weight ratio |
Nickel Alloys | Power Plants, Chemical Industries | Exceptional high-temperature strength |
4. When Are Heat-Resistant Metals Used?
Heat-resistant metals are used in a variety of industries where high temperatures are common. What’s the real story? These metals are critical in applications where components must endure extreme heat without compromising safety or performance.
- Aerospace – Heat-resistant metals are essential in the aerospace industry. Aircraft engines, especially jet turbines, require components made from heat-resistant alloys to function in high-heat environments. These alloys prevent metal fatigue, corrosion, and thermal degradation, ensuring that engines perform at their best.
- Automotive – The automotive industry also relies heavily on heat-resistant metals. Car engines, exhaust systems, and transmissions are subjected to high temperatures, and using the right alloys ensures that these components can operate efficiently without breaking down prematurely.
- Energy – In the energy sector, heat-resistant metals are used in power plants, particularly in boilers, turbines, and reactors. These metals must withstand high-temperature gases, steam, and corrosive materials to maintain the plant’s performance and safety.
The application of heat-resistant metals is dictated by the specific demands of each industry. Ready for the good part? When you use the right material, you enhance performance, extend the life of components, and reduce overall maintenance costs.
Industry | Application | Metal Type |
---|---|---|
Aerospace | Jet engines, turbines | Titanium alloys, Nickel alloys |
Automotive | Exhaust systems, engines | Stainless steel, Nickel alloys |
Energy | Power plants, reactors | Stainless steel, Nickel alloys |
5. Where Are Heat-Resistant Metals Typically Found?
Heat-resistant metals are found across several industries and locations around the world. Here’s the kicker: These metals are indispensable in sectors like aerospace, automotive, and energy, and they are utilized globally in both manufacturing and high-performance applications.
- Aerospace Manufacturing – Companies in the U.S. and Europe lead the aerospace industry in producing heat-resistant alloys for jet engines and aircraft components. Countries with significant aerospace sectors, such as the United States, China, and Russia, rely on these metals to maintain the performance of their fleets.
- Automotive Production – Major automotive manufacturing hubs in Germany, Japan, and the U.S. use heat-resistant metals extensively in engine components and exhaust systems. These metals are necessary for meeting the performance standards required by modern vehicles.
- Power Generation – Power plants worldwide rely on heat-resistant metals to maintain safe and efficient operations. In regions like the Middle East, where energy production is vital, heat-resistant alloys are essential for maintaining the performance of high-temperature industrial machinery.
What’s the real story? The global distribution of heat-resistant metals shows how essential they are for critical industries worldwide. Their presence is a sign of their importance in driving innovation and safety.
Industry | Key Countries | Metal Type Used |
---|---|---|
Aerospace | USA, Russia, China | Titanium alloys, Nickel alloys |
Automotive | Germany, Japan, USA | Stainless steel, Nickel alloys |
Energy | Middle East, USA, Russia | Stainless steel, Nickel alloys |
6. Why Are Heat-Resistant Metals So Crucial for Industrial Applications?
Heat-resistant metals are vital for industries where heat can cause material failure, machinery breakdowns, or safety risks. Ready for the good part? These metals prevent performance degradation and ensure the continued operation of critical systems.
- Durability – Heat-resistant alloys are designed to resist oxidation, corrosion, and other forms of degradation in high-heat environments. This ensures that industrial equipment performs at optimal levels for longer periods, minimizing the need for repairs or replacements.
- Safety – Components that operate in high-temperature environments must be able to withstand extreme conditions without compromising safety. Heat-resistant metals ensure that machinery and equipment remain stable, reducing the risk of failures that could cause accidents or costly downtime.
- Cost-Efficiency – Using heat-resistant metals can save money in the long run. Although these materials may be more expensive initially, their durability and ability to withstand harsh conditions reduce the need for frequent replacements and maintenance, ultimately lowering operational costs.
This is where it gets interesting: The performance of heat-resistant metals in these applications has a direct impact on the success of businesses. The more durable and reliable these materials are, the more efficient the operation becomes, leading to higher productivity and profitability.
Application | Benefit | Result |
---|---|---|
Aerospace | Durability in jet engines | Reduced maintenance, enhanced safety |
Automotive | Heat resistance in exhaust systems | Longer lifespan, reduced repairs |
Energy | Resilience in power plants | Reduced downtime, lower operational costs |
7. How Heat-Resistant Metals Are Manufactured
The manufacturing of heat-resistant metals involves specialized techniques to create alloys that can withstand high temperatures. Here’s the kicker: The production process itself determines the final properties of the material, such as strength, resistance, and durability.
- Alloying – The first step in creating heat-resistant metals is alloying. This process involves mixing metals such as nickel, chromium, and molybdenum to create a substance with enhanced properties like heat tolerance, oxidation resistance, and strength at high temperatures.
- Forging and Casting – Once the metal has been alloyed, it is formed into the desired shape through forging or casting. These methods use intense heat to shape the metal, ensuring that the final product can withstand the temperatures it will be exposed to in real-world applications.
- Heat Treatment – The metal undergoes heat treatment processes like annealing or quenching to further refine its strength and heat resistance. These processes are essential for ensuring that the metal retains its form and functionality at high temperatures.
Process | Description | Purpose |
---|---|---|
Alloying | Mixing metals like nickel and chromium | Create heat-resistant properties |
Forging and Casting | Shaping metal through heat and pressure | Ensure durability and form |
Heat Treatment | Applying controlled heating/cooling | Enhance strength and performance |
8. The Role of Heat-Resistant Metals in Aerospace and Aviation
Heat-resistant metals play a crucial role in the aerospace and aviation industries. Ready for the good part? These metals ensure the safety and performance of critical components like engines and turbines.
- Jet Engine Components – Jet engines operate at extremely high temperatures, and the materials used must be able to withstand heat without losing strength or stability. Titanium and nickel-based alloys are the most commonly used metals in turbine blades, ensuring engines run efficiently and safely.
- Turbine Blades – Turbine blades are subjected to both high temperatures and immense pressure. Heat-resistant metals such as Inconel alloys provide the necessary strength and oxidation resistance, preventing turbine blades from deteriorating in flight.
- Aerospace Safety – The safety of passengers and crew relies on the performance of heat-resistant metals in aerospace components. These metals ensure that critical systems like fuel lines, exhaust systems, and control systems function optimally, even under intense heat.
Component | Material Used | Purpose |
---|---|---|
Jet engines | Titanium alloys | High heat resistance, lightweight |
Turbine blades | Nickel alloys | High-temperature strength, oxidation resistance |
Fuel lines | Stainless steel | Durability, corrosion resistance |
9. The Automotive Industry and Heat-Resistant Metals
Heat-resistant metals are just as important in the automotive industry, where they ensure that engines, exhaust systems, and other critical components function properly under high heat. What’s the real story? Automotive manufacturers rely heavily on these materials to maintain performance and prevent breakdowns.
- Engine Components – The engine is the heart of any vehicle, and heat-resistant metals are used to ensure that components like pistons, valves, and cylinder heads can handle the extreme temperatures created during combustion.
- Exhaust Systems – Exhaust systems must endure high temperatures and corrosive gases. Stainless steel is commonly used in exhaust pipes and catalytic converters, as it can withstand the heat and prevent rust.
- Heat Shields and Brakes – Heat shields protect sensitive components from the intense heat generated by the engine, while heat-resistant metals are used in brake systems to ensure they perform reliably even under high-stress conditions.
Component | Material Used | Application |
---|---|---|
Engine | Nickel alloys, Stainless steel | Durability, heat resistance |
Exhaust | Stainless steel | Corrosion resistance |
Brakes | Heat-resistant alloys | Ensure safety and performance |
10. Heat-Resistant Metals in the Energy Industry
The energy industry is another sector that relies heavily on heat-resistant metals. Here’s the kicker: These metals are used in applications such as power plants, nuclear reactors, and gas turbines, where high temperatures are the norm.
- Power Plant Equipment – Boilers, turbines, and reactors must operate efficiently at high temperatures. Stainless steel and nickel-based alloys are used in these systems to withstand extreme heat without losing their structural integrity.
- Nuclear Reactors – In nuclear reactors, materials are subjected to intense heat and radiation. Heat-resistant metals such as Inconel alloys are essential for keeping the reactors safe and functional under these harsh conditions.
- Gas Turbines – Gas turbines, used in both power plants and aircraft engines, operate at incredibly high temperatures. Heat-resistant alloys like nickel-based alloys help these turbines perform reliably without degradation over time.
Application | Metal Used | Purpose |
---|---|---|
Power plants | Stainless steel, Nickel alloys | Heat resistance, durability |
Nuclear reactors | Inconel alloys | High-temperature and radiation resistance |
Gas turbines | Nickel alloys | Prevent degradation, ensure performance |
11. Challenges of Working with Heat-Resistant Metals
Despite their advantages, working with heat-resistant metals comes with its own set of challenges. What’s the real story? These metals are often more difficult to source, process, and manufacture than other types of metals.
- Cost – Heat-resistant metals are often more expensive than standard metals due to their complex production processes and specialized materials. The high cost can be a barrier for businesses, especially those working with tight budgets.
- Availability – Some heat-resistant alloys are rare or difficult to source, which can delay production and lead to supply chain issues. Companies may face challenges in securing the necessary materials in a timely manner.
- Manufacturing Complexity – The production of heat-resistant metals requires specialized equipment and expertise. Processes like forging and casting require precise control to ensure the final product meets the necessary performance standards.
Challenge | Impact | Solution |
---|---|---|
Cost | Increased production expenses | Invest in long-term durability |
Availability | Supply chain delays | Source from multiple suppliers |
Manufacturing complexity | Risk of defects | Use specialized equipment and skilled labor |
12. Advancements and Innovations in Heat-Resistant Metal Technology
The world of heat-resistant metals is constantly evolving. This is where it gets interesting: New advancements in alloying techniques and manufacturing processes are pushing the boundaries of what these metals can do.
- New Alloys – Researchers are developing new alloys that can withstand even higher temperatures, offering improved strength and resistance to thermal fatigue. These advanced alloys have the potential to revolutionize industries like aerospace and energy.
- Additive Manufacturing – Additive manufacturing techniques, like 3D printing, are being used to create custom components from heat-resistant metals. This allows for greater precision and the ability to produce complex shapes that were previously impossible.
- Nanotechnology – Nanotechnology is also being explored as a way to enhance the properties of heat-resistant metals. By manipulating materials at the molecular level, scientists are improving the durability and heat resistance of these metals.
Innovation | Description | Impact |
---|---|---|
New Alloys | High-performance alloys with improved heat resistance | Increased temperature tolerance |
Additive Manufacturing | 3D printing of custom components | Greater precision, reduced waste |
Nanotechnology | Manipulating materials at the molecular level | Enhanced strength and durability |
13. Cost of Heat-Resistant Metals: Is It Worth the Investment?
While heat-resistant metals come with a higher upfront cost, the long-term benefits often outweigh the price. What’s the real story? These metals offer significant value in industries where performance, safety, and longevity are paramount.
- Long-Term Savings – Using heat-resistant metals can reduce the need for frequent repairs and replacements. This long-term cost savings can offset the initial investment, especially in high-performance sectors.
- Increased Reliability – With the ability to withstand extreme temperatures, heat-resistant metals contribute to the overall reliability of machinery, reducing downtime and increasing productivity.
- Preventing Failures – The use of these metals can prevent catastrophic failures that could lead to safety issues, environmental damage, or costly legal claims. Their durability ensures the continued safe operation of critical systems.
Benefit | Explanation | Long-Term Effect |
---|---|---|
Long-term savings | Reduced need for maintenance | Offset initial cost |
Increased reliability | Prevent downtime and failures | Improved productivity |
Preventing failures | Safety and performance | Avoid costly legal claims |
14. Environmental Impact and Sustainability of Heat-Resistant Metals
As industries strive to be more environmentally responsible, heat-resistant metals are also evolving to be more sustainable. Here’s the kicker: These metals are being designed not just for performance, but also with the environment in mind.
- Sustainable Sourcing – Many companies are now focusing on sourcing materials from sustainable mines or recycling old metal components to reduce their environmental footprint.
- Recyclability – Heat-resistant metals like stainless steel and aluminum are highly recyclable, which helps reduce waste and energy consumption during production. The recycling process also lowers the demand for new raw materials.
- Reduced Carbon Footprint – By using heat-resistant metals in energy-efficient applications, industries can reduce their overall carbon footprint. These materials contribute to the development of greener, more sustainable technologies.
Sustainability Effort | Explanation | Benefit |
---|---|---|
Sustainable sourcing | Using responsibly sourced materials | Reduces environmental impact |
Recyclability | Reusing heat-resistant metals | Minimizes waste, saves energy |
Reduced carbon footprint | Lower energy consumption | Contributes to greener technologies |
15. Conclusion: The Future of Heat-Resistant Metals in Industrial Applications
Heat-resistant metals will continue to be indispensable for industries that operate in high-temperature environments. What’s the real story? Their reliability, performance, and cost-effectiveness ensure they will remain at the forefront of technological innovation in aerospace, automotive, and energy sectors.
As manufacturing techniques improve and new alloys are developed, the potential applications for heat-resistant metals will only grow. The future is bright for these materials, and as industries evolve, so too will the metals that power them.
Ready for the good part? With continuous advancements in materials science, heat-resistant metals will remain a key player in ensuring the safety, efficiency, and sustainability of critical systems in the world’s most demanding environments.
FAQ Section
Q1: What are heat-resistant metals?
Heat-resistant metals are specialized alloys designed to retain their strength and durability in extreme temperatures. These metals prevent degradation, ensuring long-lasting performance in high-heat environments like aerospace, automotive, and energy industries.
Q2: How do heat-resistant metals work?
These metals work by utilizing specific alloying elements, such as nickel or chromium, that enhance the metal’s resistance to heat, oxidation, and thermal fatigue. This allows the metals to maintain their structural integrity at temperatures that would normally cause standard metals to fail.
Q3: What types of metals are heat-resistant?
Common heat-resistant metals include stainless steel, titanium alloys, and nickel-based alloys. These metals are chosen for their ability to withstand extreme temperatures without losing performance or structural integrity.
Q4: Why are heat-resistant metals important for industries?
Heat-resistant metals are crucial for industries where machinery and components must function in high-temperature environments. They ensure the reliability, safety, and efficiency of equipment, reducing maintenance costs and preventing failures.
Q5: When are heat-resistant metals used in industrial applications?
These metals are used whenever high temperatures are a factor, such as in jet engines, power plants, and automotive engines. They are essential for maintaining performance in extreme conditions where other metals would degrade.