When it comes to selecting the best properties of heat-resistant metals, the process can seem daunting. The right choice can be a game-changer in industries where performance under high temperatures is crucial, such as aerospace, automotive, and power plants. But here’s the kicker—choosing the correct metal isn’t just about picking one that can handle high heat. It’s about understanding the interplay of properties that will provide the best performance in specific conditions. This guide will walk you through what makes heat-resistant metals stand out and how to select them based on your unique needs.
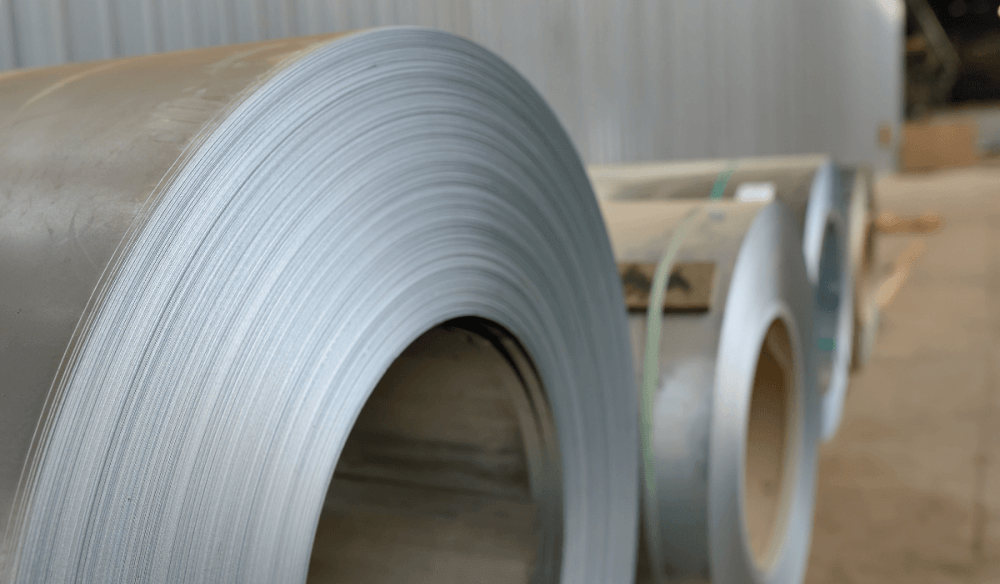
1. Introduction to Heat-Resistant Metals
Heat-resistant metals are indispensable in industries where elevated temperatures are the norm. What’s the real story? These materials withstand thermal stresses that would quickly degrade conventional metals. Whether it’s the strength needed for turbines, or the ability to resist corrosion in chemical reactors, the right heat-resistant metal ensures longevity and reliability.
Heat-resistant metals come with a unique set of characteristics, such as high melting points, stability at elevated temperatures, and the ability to resist oxidation. Ready for the good part? These properties make them vital in manufacturing and engineering, especially when dealing with extreme conditions. The ultimate goal is to select materials that not only resist heat but also maintain their mechanical properties over time, even when exposed to high stress.
Property | Description | Examples |
---|---|---|
High Melting Point | Ability to retain structure at high temperatures | Inconel, Titanium |
Thermal Stability | Ability to endure temperature changes without failure | Stainless Steel |
Oxidation Resistance | Prevents rusting or corrosion under heat | Nickel Alloys |
2. Understanding Heat-Resistant Metal Properties
Heat-resistant metals are characterized by a few key properties that ensure their performance under extreme conditions. Here’s the deal—the more you understand these properties, the better equipped you’ll be to select the right material. First, these metals must have a high melting point, which means they can handle the extreme temperatures typical in industrial applications.
In addition to a high melting point, the best heat-resistant metals need to show thermal stability. This property is crucial because materials can degrade over time when subjected to fluctuations in temperature. What’s the catch? Some metals perform better at certain temperatures, and understanding these variations helps you choose the most reliable option for your specific use case.
Property | Description | Examples |
---|---|---|
High Melting Point | Ability to resist deformation at extreme heat | Inconel, Titanium |
Thermal Stability | Resists thermal fatigue, maintaining strength over time | Superalloys |
Corrosion Resistance | Withstands harsh environmental conditions | Ceramic-based Alloys |
3. Why Heat-Resistance Matters in Various Industries
The importance of heat resistance goes beyond just high temperatures—it impacts the efficiency and lifespan of materials used in critical applications. But here’s where it gets interesting—industries such as aerospace, automotive, and energy production rely heavily on heat-resistant metals for their performance. These industries demand materials that can endure prolonged exposure to extreme heat, such as jet engine turbines, rocket parts, or furnace linings.
In the aerospace industry, for example, turbines and engines require alloys that can handle both high temperatures and mechanical stress. What’s the real challenge? The material must perform without degradation or failure, ensuring the safety and efficiency of the entire system. For automotive industries, heat-resistant materials are used in components like exhaust systems and engine blocks, where performance under heat is non-negotiable.
Industry | Use of Heat-Resistant Metals | Example Materials |
---|---|---|
Aerospace | Engine components, turbines | Inconel, Titanium |
Automotive | Exhaust systems, engine blocks | Stainless Steel |
Power Generation | Furnace linings, turbines | Cast Iron, Alloy Steel |
4. Key Properties to Look for in Heat-Resistant Metals
Selecting the right heat-resistant metal isn’t a one-size-fits-all approach. So, what should you look for? The key properties to focus on include high melting points, thermal stability, and oxidation resistance. These properties ensure that the material can withstand high temperatures without deforming or rusting.
The melting point of a material is crucial because it determines the temperature at which the metal will lose its structural integrity. Metals with high melting points, such as titanium and Inconel, are ideal for high-temperature environments. Additionally, oxidation resistance is critical for materials exposed to oxygen at elevated temperatures, as it prevents the material from degrading over time.
Property | Importance | Examples |
---|---|---|
High Melting Point | Resists heat-induced deformation and failure | Inconel, Titanium |
Thermal Stability | Endures temperature changes without structural damage | Alloy Steel, Stainless |
Oxidation Resistance | Protects metal from corrosion in extreme heat conditions | Nickel Alloys |
5. What Types of Heat-Resistant Metals are Available?
There are several types of heat-resistant metals, each with its unique set of properties. Here’s the kicker—the choice of material depends on the specific application and its requirements. Some of the most commonly used heat-resistant metals include Inconel, titanium alloys, and various forms of steel.
Inconel is a superalloy known for its ability to withstand high temperatures while maintaining structural integrity. What’s the real story? It’s commonly used in aerospace and chemical industries. Titanium alloys, on the other hand, are ideal for applications that require high strength-to-weight ratios, such as aerospace components. Nickel alloys are perfect for environments where resistance to corrosion and oxidation is a priority.
Metal Type | Key Properties | Common Applications |
---|---|---|
Inconel | High temperature stability, oxidation resistance | Aerospace, Chemical |
Titanium Alloys | Lightweight, high strength, corrosion resistant | Aerospace, Automotive |
Nickel Alloys | High corrosion and oxidation resistance | Marine, Chemical |
6. How to Assess Heat-Resistance in Metals
Understanding how to assess the heat-resistance of a metal is key to making an informed selection. Here’s the good part—laboratory testing and material characterization are essential methods used to evaluate heat-resistance. These tests include thermal cycling, oxidation tests, and mechanical stress testing at high temperatures.
Laboratory testing helps simulate real-world conditions, providing insight into how a metal will perform over time. Thermal cycling tests expose materials to repeated temperature changes, while oxidation resistance tests simulate exposure to oxygen. Mechanical tests, such as tensile and fatigue tests, ensure the material can handle both high temperatures and stress.
Test Type | Purpose | Key Results |
---|---|---|
Thermal Cycling Test | Simulates repeated temperature fluctuations | Fatigue Resistance |
Oxidation Test | Measures how well metals resist oxidation at high heat | Corrosion Resistance |
Mechanical Stress Test | Tests strength under high heat and mechanical load | Durability under Stress |
7. When to Choose Heat-Resistant Metals for Your Projects
Choosing the right time to use heat-resistant metals is just as important as selecting the right material. What’s the deal? Heat-resistant metals are necessary for projects where temperature control is critical—such as in manufacturing processes, power generation, and aerospace. These metals ensure that machinery and systems perform safely and efficiently in high-temperature environments.
For example, in power generation, materials used for turbine blades must not only endure extreme heat but also maintain their structural integrity for years. Ready for the next step? In aerospace, heat-resistant metals are chosen for components like jet engine turbines, where failure due to heat exposure is unacceptable.
Application Area | When to Use Heat-Resistant Metals | Material Example |
---|---|---|
Aerospace | Jet engine components, turbine blades | Inconel, Titanium |
Power Generation | Turbines, furnace linings | Alloy Steel, Cast Iron |
Automotive | Exhaust systems, brake parts | Stainless Steel |
8. Where to Source High-Quality Heat-Resistant Metals
When sourcing heat-resistant metals, choosing a reputable supplier is essential. What’s the catch? Not all suppliers provide metals with the same specifications or quality standards. To ensure you’re getting the best material for your project, you need to carefully evaluate potential suppliers.
Look for suppliers who offer detailed technical sheets for their materials. But here’s the kicker—don’t settle for just the first supplier you find. Compare prices, materials, and testing procedures to ensure that the metal you’re purchasing meets your specific needs.
Supplier Factor | Importance | Key Considerations |
---|---|---|
Material Certification | Ensures metals meet international standards | ASTM, ISO |
Supplier Reputation | Trusted history of providing quality materials | Industry Reviews |
Pricing | Fair pricing based on material quality and demand | Competitive Pricing |
9. How Heat-Resistant Metals Are Processed and Manufactured
The manufacturing process of heat-resistant metals plays a significant role in their overall performance. This is where it gets interesting—metals undergo specific treatments, such as casting, forging, and heat treatments, to enhance their resistance to heat and stress.
For example, Inconel is often produced through powder metallurgy, which allows for greater control over its composition and properties. What’s the takeaway? The processing method you choose impacts the final properties of the metal and its suitability for particular applications.
Processing Method | Impact on Metal Properties | Material Example |
---|---|---|
Powder Metallurgy | Allows precise control over material composition | Inconel |
Forging | Enhances mechanical strength and fatigue resistance | Stainless Steel |
Casting | Produces complex shapes, used for high-performance parts | Nickel Alloys |
10. Heat-Resistant Metals vs. High-Temperature Alloys: What’s the Difference?
Heat-resistant metals and high-temperature alloys are often used interchangeably, but they aren’t the same thing. What’s the difference? Heat-resistant metals are designed specifically to perform under high-heat conditions, while high-temperature alloys are a subset of heat-resistant materials with added elements to further improve performance under extreme conditions.
High-temperature alloys often contain additional elements like molybdenum or tungsten to increase strength and resistance to thermal degradation. Here’s the kicker—depending on your project needs, you may choose a standard heat-resistant metal or a more specialized high-temperature alloy to meet specific performance goals.
Type | Characteristics | Key Differences |
---|---|---|
Heat-Resistant Metals | Resist heat and maintain strength at high temperatures | Basic properties |
High-Temperature Alloys | Contain additional elements for enhanced thermal resistance | Greater performance |
11. Factors That Influence the Selection of Heat-Resistant Metals
Selecting heat-resistant metals requires a thorough understanding of several factors. What’s the catch? Budget, material availability, environmental conditions, and the specific mechanical requirements of your project all influence the choice of material.
For instance, a high-performance aerospace component may require a titanium alloy with superior strength-to-weight ratios, while an industrial furnace lining might benefit from a more affordable but equally reliable steel alloy.
Factor | Influence on Selection | Examples |
---|---|---|
Budget | Determines which material is affordable while meeting needs | Stainless Steel, Titanium |
Environment | Materials resistant to oxidation or corrosion in extreme environments | Nickel Alloys |
Mechanical Requirements | Strength and durability under stress or weight | Inconel, Superalloys |
12. Common Mistakes to Avoid When Selecting Heat-Resistant Metals
Selecting the wrong heat-resistant metal can lead to costly failures. What should you avoid? One common mistake is choosing a material based on price alone. Here’s the kicker—this can often lead to performance issues down the line. It’s crucial to balance cost with the necessary properties and performance standards.
Additionally, not considering the environment where the material will be used can lead to corrosion or other failures. So, what’s the solution? Always ensure the material selected meets the demands of both temperature and environmental exposure.
Mistake | Explanation | Solution |
---|---|---|
Prioritizing Cost | Choosing cheaper materials that don’t meet performance standards | Focus on properties first |
Ignoring Environmental Conditions | Not factoring in corrosive or extreme environments | Consider environmental tests |
Underestimating Longevity | Not considering the long-term durability of metals under stress | Use lifecycle assessments |
13. How to Compare Heat-Resistant Metals for Your Specific Needs
Comparing heat-resistant metals effectively can be overwhelming. Here’s the secret—start by gathering the technical specifications for each material and compare them against your needs. Look at things like melting point, oxidation resistance, and thermal stability.
It’s also wise to conduct your own tests, particularly when working in environments with unusual temperature fluctuations. Ready for the good part? This hands-on comparison ensures that you select the right metal based on real-world performance, not just theoretical properties.
Metal Type | Melting Point (°C) | Thermal Stability (°C) | Oxidation Resistance |
---|---|---|---|
Inconel | 1300 | High | Excellent |
Titanium | 1600 | Moderate | Good |
Stainless Steel | 1375 | High | Moderate |
14. The Future of Heat-Resistant Metals and Technological Advancements
As industries evolve, so do the materials used to withstand extreme conditions. But here’s the kicker—the future of heat-resistant metals involves advanced alloys, composites, and manufacturing processes. Innovations in materials science continue to push the boundaries of what’s possible, introducing metals that perform better and last longer under higher temperatures.
Emerging technologies, such as 3D printing, are making it possible to manufacture complex components from heat-resistant metals, reducing material waste and increasing design flexibility. What’s the takeaway? These advancements will continue to improve the performance and applications of heat-resistant metals across industries.
Technology | Impact on Heat-Resistant Metals | Potential Benefits |
---|---|---|
3D Printing | Custom manufacturing of complex heat-resistant components | Reduced waste, flexibility |
Advanced Alloys | Increased resistance to oxidation and temperature fluctuations | Longer lifespan, better performance |
15. Conclusion
In conclusion, selecting the best properties of heat-resistant metals is a critical step in ensuring the performance and durability of materials used in high-temperature environments. What’s the bottom line? Understand the key properties, select based on the specific demands of your project, and always test the material for real-world performance. This comprehensive guide has equipped you with the knowledge to make informed decisions and choose the right heat-resistant metal for your needs.
FAQ Section
Q1: What are heat-resistant metals?
Heat-resistant metals are alloys and materials designed to withstand high temperatures without losing their strength or structural integrity. These metals are essential in environments where extreme heat exposure is constant, such as in engines or power plants.
Q2: How do I choose the best heat-resistant metal for my project?
To choose the best heat-resistant metal, consider factors like the material’s melting point, thermal conductivity, oxidation resistance, and mechanical strength. Evaluate the specific needs of your project, such as the temperature range and environmental conditions.
Q3: Why are nickel alloys commonly used for high-temperature applications?
Nickel alloys are known for their superior resistance to heat, corrosion, and oxidation. These qualities make them ideal for high-temperature environments like jet engines and power turbines, where other metals might fail.
Q4: What industries commonly use heat-resistant metals?
Industries such as aerospace, automotive, energy production, and manufacturing rely on heat-resistant metals. These materials are used in turbine blades, exhaust systems, and heat exchangers, where high temperatures and extreme conditions are prevalent.
Q5: How are heat-resistant metals tested for their properties?
Heat-resistant metals are tested through various methods, including thermal cycling tests, oxidation resistance tests, and mechanical testing under high temperatures. These tests help determine a material’s durability and performance under real-world conditions.