Heat-resistant metals play an essential role in industries that operate in high-heat environments. These metals must withstand extreme temperatures while maintaining strength, structural integrity, and resistance to wear and tear. But what exactly makes these metals so crucial in modern technology? In this comprehensive guide, we will dive into the properties of heat-resistant metals, their uses, and how to select the right one for your specific needs. Whether you are involved in aerospace, manufacturing, or energy generation, understanding these materials will equip you with the knowledge to make better, more informed decisions.
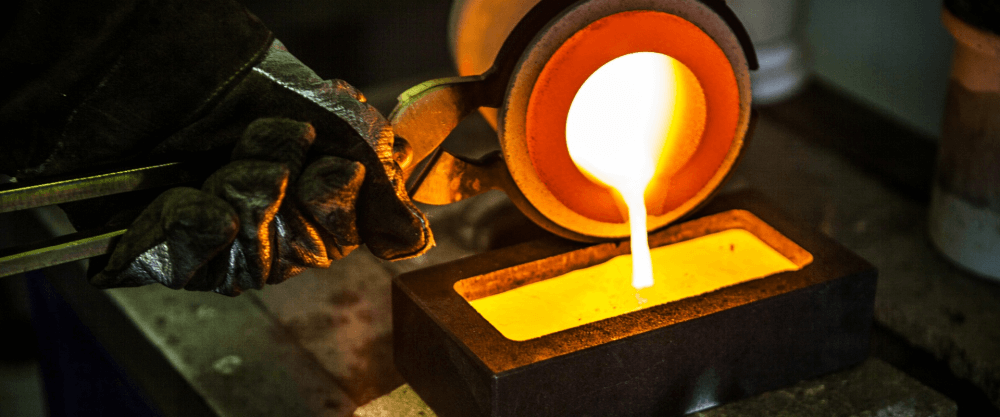
1. What Are Heat-Resistant Metals?
Heat-resistant metals are materials that can endure elevated temperatures without losing their structural integrity, strength, or ability to perform critical functions. Essentially, these metals have the ability to resist the effects of heat, preventing them from becoming brittle, deforming, or deteriorating when exposed to high temperatures.
What’s the real story? Heat-resistant metals are essential in high-performance applications, from engines to turbines, where temperatures can soar to extreme levels. The metals must maintain a balance between thermal expansion and resistance to oxidation and corrosion. Some common examples of these metals include nickel alloys, titanium, and high-performance steel. These metals typically have a high melting point, making them highly resistant to heat-related stresses.
Table: Common Heat-Resistant Metals and Their Properties
Metal Type | Melting Point (°C) | Thermal Conductivity (W/m·K) | Common Applications |
---|---|---|---|
Stainless Steel | 1400–1500 | 16–30 | Automotive, Aerospace |
Nickel Alloys | 1300–1450 | 10–15 | Gas Turbines, Power Generation |
Titanium Alloys | 1668 | 6.7–21 | Aerospace, Industrial Equipment |
High-Temperature Steel | 1370–1550 | 30–50 | Heat Exchangers, Chemical Plants |
Understanding the unique properties of these metals allows industries to pick the best material suited for their specific needs. This is where it gets interesting: heat resistance alone isn’t enough; the material’s other characteristics, like tensile strength, corrosion resistance, and ductility, play an equally important role.
2. Why Are Heat-Resistant Metals Important?
The importance of heat-resistant metals cannot be overstated. These materials serve as the backbone of modern engineering, where the requirement to withstand extreme temperatures is a non-negotiable factor in the design and functionality of critical components. Ready for the good part? Without heat-resistant metals, industries such as aerospace, automotive, and power generation would not be able to achieve the performance and reliability they require.
Heat-resistant metals are used extensively in engines, turbines, boilers, reactors, and many other high-heat environments. Their role is crucial in ensuring the safety, longevity, and efficiency of equipment. In the aerospace industry, for example, turbine blades made from nickel-based alloys must endure temperatures above 1,000°C without failing. But here’s the kicker: if these metals were not heat-resistant, engines and other critical systems would not function effectively, leading to failures and safety hazards.
Table: Industries That Rely on Heat-Resistant Metals
Industry | Common Applications | Metal Types Used |
---|---|---|
Aerospace | Jet engines, turbine blades | Nickel Alloys, Titanium |
Power Generation | Gas turbines, nuclear reactors | High-Temperature Steel, Stainless Steel |
Automotive | Engine parts, exhaust systems | Stainless Steel, Titanium |
Manufacturing | Heat exchangers, furnaces | High-Temperature Steel |
By using heat-resistant metals, these industries can improve both the safety and longevity of their equipment. What’s the real story? Heat resistance enables a broad range of high-performance applications that drive technological advancements.
3. Types of Heat-Resistant Metals
Heat-resistant metals come in various types, each tailored to different applications based on factors like temperature resistance, corrosion resistance, and mechanical properties. You might be wondering: what are the best types of heat-resistant metals available today?
Stainless Steel
Stainless steel is one of the most common and versatile heat-resistant metals, widely used in applications ranging from household items to industrial machinery. It resists oxidation and corrosion, making it ideal for high-temperature environments. Stainless steel is used in everything from kitchen appliances to exhaust systems in cars and aircraft.
Nickel Alloys
Nickel alloys are known for their exceptional resistance to high temperatures and corrosion. These alloys are widely used in aerospace, power generation, and chemical processing industries. Nickel-based alloys offer excellent strength and can perform at temperatures exceeding 1,300°C.
Titanium Alloys
Titanium alloys have a high strength-to-weight ratio and are highly resistant to corrosion. Their properties make them ideal for aerospace applications, where both strength and lightweight materials are necessary. Titanium is also used in power generation and military applications due to its impressive heat resistance.
High-Temperature Steel
High-temperature steel, particularly chromium and molybdenum steels, are designed to withstand very high temperatures. These materials are used extensively in industrial applications such as heat exchangers, power plants, and refineries.
Table: Key Types of Heat-Resistant Metals
Metal Type | Key Characteristics | Applications |
---|---|---|
Stainless Steel | High corrosion resistance, durable | Aerospace, Automotive, Appliances |
Nickel Alloys | Superior heat resistance, oxidation-resistant | Gas Turbines, Power Plants |
Titanium Alloys | Lightweight, strong, corrosion-resistant | Aerospace, Military |
High-Temperature Steel | Strong at high temperatures, resistant to wear | Heat Exchangers, Boilers |
Each of these metals has unique properties that make them suitable for specific high-heat applications. This is where it gets interesting: while some are better suited for high-stress mechanical applications, others are designed for corrosion resistance at elevated temperatures.
4. How Do Heat-Resistant Metals Work?
Understanding how heat-resistant metals work is key to choosing the right one for your applications. What’s the real story? Heat-resistant metals are engineered with specific alloys designed to handle extreme temperatures without compromising their mechanical properties.
The Science Behind Heat Resistance
Metals lose their strength as temperatures increase, but heat-resistant metals have a high melting point and maintain strength at high temperatures. The primary mechanism behind heat resistance is the unique atomic structure of these metals, which prevents thermal expansion and the degradation of their crystal structure.
Oxidation Resistance
Heat-resistant metals are often alloyed with elements such as chromium, which form a protective oxide layer on the metal’s surface. This oxide layer prevents further oxidation and corrosion, even when exposed to extreme temperatures. Here’s the kicker: the ability of a metal to resist oxidation is just as crucial as its ability to withstand heat.
Thermal Conductivity
Heat-resistant metals often have low thermal conductivity, meaning they do not easily transfer heat. This characteristic helps prevent heat from spreading through the metal, ensuring that the material remains stable at high temperatures.
Table: Key Mechanisms of Heat Resistance
Mechanism | Description | Example Metals |
---|---|---|
High Melting Point | Prevents material from melting at high temperatures | Titanium, Nickel Alloys |
Oxidation Resistance | Prevents rust and deterioration by forming protective oxide layers | Stainless Steel, Nickel Alloys |
Low Thermal Conductivity | Limits heat transfer and maintains stability under extreme conditions | High-Temperature Steel, Titanium |
Each of these properties plays an essential role in the effectiveness of heat-resistant metals. What’s the real story? Without these mechanisms, the metals wouldn’t be able to perform efficiently in high-heat environments.
5. When Should Heat-Resistant Metals Be Used?
Knowing when to use heat-resistant metals is just as important as understanding their properties. Ready for the good part? Heat-resistant metals are often used in high-performance applications where traditional metals would fail under extreme conditions.
High-Temperature Environments
Industries that involve high temperatures, such as aerospace and power generation, require materials that can withstand the heat without deteriorating. Turbines, engines, and reactors are prime examples of components that require heat-resistant metals.
Critical Components
In industries like automotive and manufacturing, heat-resistant metals are used for critical components like exhaust systems, heat exchangers, and furnace parts. But here’s the kicker: if these components were made from traditional metals, they would break down quickly, leading to costly repairs and replacements.
High-Performance Applications
Heat-resistant metals are also used in high-performance applications like military technology, where both strength and heat resistance are required. Aircraft, missiles, and rockets rely heavily on heat-resistant materials to maintain structural integrity at extreme speeds and altitudes.
Table: When to Use Heat-Resistant Metals
Application Area | Metal Types Used | Example Products |
---|---|---|
Aerospace | Nickel Alloys, Titanium | Turbine Blades, Engine Parts |
Automotive | Stainless Steel, Titanium | Exhaust Systems, Engine Blocks |
Power Generation | High-Temperature Steel, Stainless Steel | Heat Exchangers, Boilers |
Military Technology | Titanium, Nickel Alloys | Aircraft, Rocket Engines |
Heat-resistant metals are essential when high temperatures could cause regular metals to fail. This is where it gets interesting: in many cases, these metals are the difference between operational success and failure.
6. Where Are Heat-Resistant Metals Used?
Heat-resistant metals find applications in a wide range of industries. You might be wondering: where exactly are these metals used?
Aerospace
In the aerospace industry, heat-resistant metals are used for turbine blades, engine components, and other high-temperature areas. These metals help engines maintain performance even in extreme conditions.
Power Generation
Gas turbines and nuclear reactors rely heavily on heat-resistant metals. These metals ensure that turbines remain efficient and durable even when operating at temperatures above 1,000°C.
Automotive
In automotive applications, heat-resistant metals are used for components like exhaust systems, engine blocks, and turbochargers. These parts are exposed to extreme heat and must maintain strength and durability.
Industrial Manufacturing
Industrial sectors such as chemical processing, refineries, and manufacturing plants use heat-resistant metals in equipment like furnaces, reactors, and heat exchangers to prevent failure during high-temperature operations.
Table: Key Applications of Heat-Resistant Metals
Industry | Applications | Metal Types Used |
---|---|---|
Aerospace | Turbine Blades, Engines | Titanium, Nickel Alloys |
Power Generation | Gas Turbines, Reactors | High-Temperature Steel, Stainless Steel |
Automotive | Exhaust Systems, Engine Parts | Stainless Steel, Titanium |
Manufacturing | Heat Exchangers, Furnaces | High-Temperature Steel |
By understanding where heat-resistant metals are used, industries can better select the materials needed for specific applications. What’s the real story? These metals are indispensable in critical industries that depend on high-heat environments.
7. How to Choose the Right Heat-Resistant Metal
Choosing the right heat-resistant metal is crucial for ensuring the success of your project. But here’s the kicker: choosing the wrong material can lead to failure, costing your company time and money.
Key Considerations
When selecting a heat-resistant metal, consider factors such as temperature range, mechanical properties, and corrosion resistance. Each metal offers different advantages depending on the application, so it’s essential to match the material to your specific needs.
Temperature Requirements
If the operating temperature is above 1,000°C, then nickel alloys and high-temperature steel might be the best options. For applications where weight is a concern, titanium alloys may be a better choice due to their strength-to-weight ratio.
Durability and Corrosion Resistance
Certain metals, like stainless steel, offer excellent corrosion resistance at high temperatures, making them ideal for environments where oxidation and rust are concerns.
Table: Choosing the Right Heat-Resistant Metal
Application | Temperature Range (°C) | Recommended Metals |
---|---|---|
High-Temperature Furnaces | 500–1,200 | High-Temperature Steel, Stainless Steel |
Aerospace Turbines | 800–1,200 | Titanium, Nickel Alloys |
Chemical Processing | 300–600 | Stainless Steel, Nickel Alloys |
This is where it gets interesting: a well-chosen heat-resistant metal can significantly improve the performance and longevity of your components, saving money and ensuring operational success.
8. Advantages of Using Heat-Resistant Metals
The benefits of using heat-resistant metals go far beyond just durability. What’s the real story? These metals offer enhanced performance, safety, and long-term savings.
Improved Durability
Heat-resistant metals are designed to last longer in high-temperature environments, reducing the need for frequent replacements. This durability translates into cost savings over time.
Safety and Reliability
When used in critical applications, heat-resistant metals help prevent accidents caused by material failure. Here’s the kicker: using heat-resistant metals in components that are exposed to extreme heat ensures that the system remains safe and functional.
Enhanced Performance
In industries like aerospace and automotive, heat-resistant metals contribute to improved performance by maintaining structural integrity at high speeds and temperatures.
Table: Advantages of Heat-Resistant Metals
Advantage | Description |
---|---|
Durability | Longer lifespan in high-heat environments |
Safety and Reliability | Reduces risks of failure, ensuring operational safety |
Enhanced Performance | Improves efficiency in high-performance applications |
This is where it gets interesting: by investing in heat-resistant metals, industries can ensure that their equipment operates reliably and efficiently over time.
9. Challenges and Limitations of Heat-Resistant Metals
Despite their numerous advantages, heat-resistant metals come with their own set of challenges. You might be wondering: what are the limitations of these metals?
High Cost
The materials used to create heat-resistant metals are often more expensive than regular metals due to the alloys and manufacturing processes involved. This can make heat-resistant metals less cost-effective for some applications.
Processing Difficulties
Certain heat-resistant metals, like titanium alloys, can be challenging to process and fabricate. But here’s the kicker: while these materials are difficult to work with, they offer exceptional benefits when used in the right applications.
Environmental Concerns
The production and use of heat-resistant metals often involve energy-intensive processes, which can have environmental impacts. The mining and extraction of raw materials also contribute to pollution and resource depletion.
Table: Challenges of Heat-Resistant Metals
Challenge | Description |
---|---|
High Cost | Expensive to produce and process |
Processing Difficulties | Can be hard to machine and fabricate |
Environmental Impact | Mining and production can be resource-intensive |
Ready for the good part? Despite these challenges, the benefits of heat-resistant metals far outweigh their limitations when used in the right applications.
10. How Are Heat-Resistant Metals Made?
The production of heat-resistant metals involves several complex processes. What’s the real story? These metals are typically alloyed with specific elements to enhance their ability to withstand high temperatures and resist oxidation.
Alloying Process
To create heat-resistant metals, manufacturers mix base metals with other elements like chromium, nickel, or titanium. This process alters the metal’s properties, enhancing its resistance to high temperatures and corrosion.
Casting and Fabrication
Once the alloys are created, the metals are cast into molds or fabricated into specific shapes for use in various industries. But here’s the kicker: heat-resistant metals often require specialized equipment and processes to ensure their quality and performance.
Advanced Techniques
Some metals, like titanium, require advanced manufacturing techniques such as powder metallurgy or electron beam welding to achieve the desired properties.
Table: Manufacturing Process for Heat-Resistant Metals
Step | Process Description | Metal Types Involved |
---|---|---|
Alloying | Mixing base metals with additives | Nickel Alloys, Stainless Steel |
Casting and Fabrication | Shaping and forming the metal into required parts | High-Temperature Steel, Titanium |
Advanced Techniques | Using specialized techniques for hard-to-process metals | Titanium Alloys, Nickel Alloys |
What’s the real story? The advanced techniques used in manufacturing heat-resistant metals help achieve optimal properties for specific applications.
11. Maintenance and Care of Heat-Resistant Metals
Maintaining heat-resistant metals is essential for extending their lifespan and ensuring they continue to perform at high levels. Ready for the good part? Regular care and maintenance can help prevent deterioration, oxidation, and failure due to heat exposure.
Cleaning and Inspection
Regular cleaning and inspection of components made from heat-resistant metals are essential for preventing buildup of debris and ensuring the materials remain intact. Special care must be taken to avoid damaging protective oxide layers.
Preventing Corrosion
One of the key maintenance tasks is preventing corrosion, which can degrade the metal’s performance over time. But here’s the kicker: using proper coatings and protective layers can help mitigate the effects of corrosion.
Table: Maintenance Practices for Heat-Resistant Metals
Practice | Description |
---|---|
Regular Cleaning | Ensuring that metals remain free from contaminants |
Corrosion Prevention | Using protective coatings to prevent rust and oxidation |
Inspection | Regular checks for signs of wear and damage |
Proper maintenance of heat-resistant metals is essential for keeping systems running efficiently. This is where it gets interesting: a little care goes a long way in extending the life of your equipment.
12. The Future of Heat-Resistant Metals
As industries continue to push the boundaries of performance, the demand for advanced heat-resistant metals is expected to rise. What’s the real story? In the coming years, new developments in materials science are likely to result in even more efficient and durable heat-resistant metals.
Research and Development
Scientists are continuously researching new alloys and manufacturing techniques to improve the performance of heat-resistant metals. But here’s the kicker: these innovations promise to make heat-resistant metals even more effective in extreme environments.
Emerging Applications
As new technologies emerge, heat-resistant metals will become increasingly important in sectors such as renewable energy, advanced manufacturing, and deep space exploration.
Table: Emerging Trends in Heat-Resistant Metals
Trend | Description |
---|---|
New Alloys | Development of advanced heat-resistant alloys |
Advanced Manufacturing | Use of cutting-edge techniques like 3D printing for heat-resistant metals |
New Applications | Expansion into renewable energy and space exploration |
Ready for the good part? As the technology continues to evolve, heat-resistant metals will play an even larger role in shaping the future of high-performance industries.
13. Conclusion
Heat-resistant metals are indispensable in modern technology, ensuring that critical systems operate efficiently in high-temperature environments. What’s the real story? By understanding the properties, applications, and challenges of these metals, industries can make informed decisions that drive performance, safety, and cost-efficiency.
Key Takeaways:
- Heat-resistant metals are essential in industries such as aerospace, automotive, and power generation.
- Choosing the right material depends on factors like temperature range, mechanical properties, and corrosion resistance.
- The future of heat-resistant metals holds promising advancements in alloys and manufacturing technologies.
What’s the real story? Understanding the role of heat-resistant metals can give your business a competitive edge in industries that rely on high-performance materials.
FAQ Section
Q1: What are heat-resistant metals?
Heat-resistant metals are alloys specifically designed to withstand high temperatures without losing their mechanical properties. They are used in environments where metals are exposed to extreme heat, such as in engines or industrial furnaces.
Q2: How do heat-resistant metals work?
Heat-resistant metals work by utilizing specific alloys and chemical compositions that resist thermal expansion, oxidation, and maintain strength at high temperatures. These metals are often designed to have high melting points and low thermal conductivity to reduce the effects of heat.
Q3: Why is heat resistance important in metals?
Heat resistance is essential for ensuring that metal components do not deform, corrode, or fail in high-temperature environments. Industries like aerospace and manufacturing rely on these metals to ensure that their machinery operates effectively and safely under extreme heat.
Q4: What are some examples of heat-resistant metals?
Examples of heat-resistant metals include stainless steel, titanium alloys, nickel alloys, cobalt alloys, and high-temperature steel. Each of these has unique properties that make them suitable for specific high-heat applications.
Q5: How can I choose the right heat-resistant metal for my application?
Choosing the right heat-resistant metal depends on factors like the temperature range, environmental conditions, required strength, and resistance to corrosion. Understanding these factors and consulting with experts will help ensure the best choice for your specific needs.