A356 aluminum investment castings are highly valued in the manufacturing industry, particularly for applications requiring precision, strength, and reliability. This article delves into the various aspects of A356 aluminum investment casting, from its process and material benefits to its broad applications across industries. If you’re considering A356 aluminum for your next project, understanding its capabilities will help you make an informed decision. By the end of this article, you’ll have a thorough grasp of A356 aluminum and how it can benefit your business.
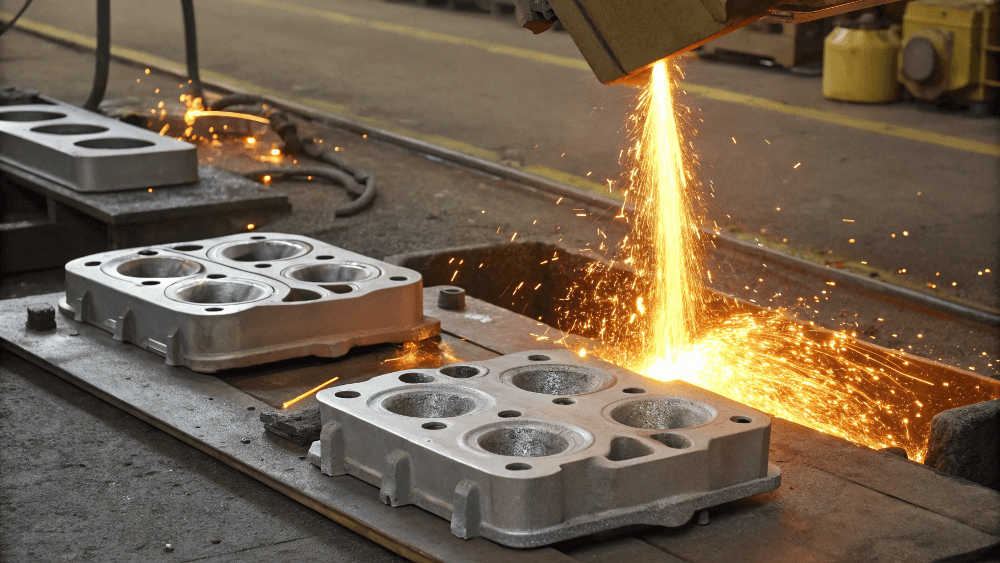
1. Introduction to A356 Aluminum Investment Casting
A356 aluminum investment casting is a precision casting process used to produce highly accurate and detailed parts from aluminum alloys. Known for its excellent strength-to-weight ratio and corrosion resistance, A356 aluminum is a top choice in industries such as aerospace, automotive, and manufacturing. But here’s the kicker: what makes A356 stand out is its versatility, providing the perfect balance of performance, cost-efficiency, and design flexibility.
The A356 aluminum alloy is primarily used for creating complex geometries and thin-walled parts. Its casting process allows for superior surface finishes and intricate designs, which would otherwise be difficult to achieve through traditional methods. The main components of the A356 alloy include silicon, magnesium, and aluminum, all of which contribute to its exceptional properties.
A356 aluminum investment casting is often selected for components that require both durability and light weight, such as engine blocks, turbine parts, and structural components. Manufacturers prefer this alloy because of its consistent performance and easy-to-machine finish. It also provides a higher tensile strength than other common casting alloys, making it the ideal choice for high-stress applications. In the following sections, we’ll explore the specific benefits of A356 aluminum, how it compares to other alloys, and its applications in various industries.
2. Understanding the Benefits of A356 Aluminum
A356 aluminum is known for its unique combination of benefits, making it an optimal choice for investment casting in demanding industries. Ready for the good part? Let’s break down why A356 aluminum shines in terms of strength, corrosion resistance, and casting properties.
One of the primary advantages of A356 aluminum is its high strength-to-weight ratio, which makes it ideal for lightweight applications in aerospace and automotive industries. When compared to other materials, A356 aluminum offers the perfect balance between strength and lightness, ensuring high performance without adding unnecessary weight.
Another standout feature of A356 aluminum is its excellent corrosion resistance, especially in harsh environments. This makes it particularly suitable for parts exposed to extreme conditions, such as those in marine, automotive, and industrial machinery. A356 aluminum also withstands high temperatures better than many other alloys, maintaining its structural integrity in heat-intensive applications.
Additionally, A356 aluminum offers superior casting properties, including excellent fluidity and the ability to cast thin walls, which enhances its usability for intricate designs. The alloy also responds well to heat treatment, allowing manufacturers to achieve the desired mechanical properties, such as increased strength and durability. This makes A356 aluminum an attractive choice for components that require a precise combination of strength, lightweight design, and high corrosion resistance.
Table: Benefits of A356 Aluminum Investment Casting
Property | A356 Aluminum | Other Aluminum Alloys |
---|---|---|
Strength-to-Weight Ratio | High | Moderate |
Corrosion Resistance | Excellent (ideal for harsh environments) | Good |
Casting Capabilities | Superior fluidity, thin-walled parts | Limited |
Temperature Resistance | High (resistant to heat) | Moderate |
3. A356 Aluminum vs. Other Aluminum Alloys
When it comes to choosing the right material for investment casting, A356 aluminum frequently stands out. But what’s the real story? How does it stack up against other aluminum alloys commonly used in manufacturing?
Let’s start by comparing A356 aluminum with A380 aluminum. A380 is often chosen for its ease of casting and excellent fluidity, but it doesn’t offer the same level of strength-to-weight ratio as A356 aluminum. While A380 is perfect for large, complex parts, it tends to be heavier and less durable under high-stress conditions compared to A356.
Next, we have A319 aluminum, which is often used for engine blocks and similar components. While A319 offers good strength, it is not as resistant to corrosion as A356, which is a significant drawback in applications that require long-lasting durability, especially in marine and high-temperature environments. Additionally, A356 is better suited for thin-walled parts, while A319 tends to be used for thicker, more rigid components.
So, what’s the final verdict? A356 aluminum is an ideal choice for parts that require both precision and durability, especially in applications where corrosion resistance and lightweight properties are critical. While other alloys like A380 and A319 have their merits, A356 offers a superior balance for more demanding applications.
Table: Comparison of A356, A380, and A319 Aluminum Alloys
Alloy | Strength-to-Weight Ratio | Corrosion Resistance | Casting Fluidity | Ideal Applications |
---|---|---|---|---|
A356 | High | Excellent | Superior | Aerospace, Automotive |
A380 | Moderate | Good | Excellent | Complex, large parts |
A319 | Moderate | Fair | Good | Engine blocks, machinery |
4. The A356 Aluminum Casting Process
So, how does the A356 aluminum casting process actually work? This section takes you through the steps involved, ensuring you understand how such precision is achieved.
Investment casting, also known as the lost wax process, is used for casting A356 aluminum. This process begins with creating a pattern of the desired part, typically using wax or a similar material. The pattern is then coated with a ceramic shell, creating a mold. The wax is melted away, leaving behind a precise mold cavity. Once the mold is prepared, molten A356 aluminum is poured into the cavity.
What’s the real story behind this process? It’s all about precision. The investment casting process allows manufacturers to create complex parts with a high degree of detail and accuracy. The mold can handle intricate features like undercuts, thin walls, and fine details. This method ensures that the final product is dimensionally accurate, which is a huge advantage for industries requiring strict specifications.
However, there are some challenges to consider. For example, the casting process requires careful temperature control to prevent defects such as cracks, porosity, and warping. If the aluminum is poured at the wrong temperature, the resulting parts may have structural weaknesses that compromise their performance. That’s why working with experienced foundries is critical for ensuring high-quality results.
Table: A356 Aluminum Investment Casting Process Steps
Step | Description |
---|---|
Pattern Creation | Create a detailed pattern (usually wax) |
Shell Coating | Apply a ceramic shell around the pattern |
Wax Removal | Melt away the wax to leave the mold |
Molten Aluminum | Pour molten A356 aluminum into the mold |
Cooling & Finishing | Allow the casting to cool, then finish |
5. Applications of A356 Aluminum Investment Casting
A356 aluminum investment casting is widely used in several industries due to its exceptional properties. Ready for the good part? Let’s take a deeper dive into its primary applications across different sectors.
In the automotive industry, A356 aluminum is commonly used for manufacturing engine components, such as cylinder heads, intake manifolds, and water pumps. Its strength-to-weight ratio makes it ideal for high-performance vehicles, where minimizing weight without sacrificing strength is critical.
In aerospace, A356 aluminum’s ability to withstand high temperatures and its lightweight nature make it an excellent choice for producing turbine blades, structural components, and other parts subject to extreme conditions. The precision provided by investment casting ensures that parts meet the tight tolerances required for aviation components.
Additionally, A356 aluminum is widely used in the general industrial sector for making brackets, housings, and custom parts. Its versatility and ability to handle complex geometries have made it a go-to material for prototyping and custom fabrication in industries ranging from industrial equipment to defense.
But here’s the kicker: as technology advances, the applications for A356 aluminum investment casting continue to expand. New techniques and innovations in casting processes are allowing manufacturers to create even more complex and lightweight parts for emerging technologies, such as electric vehicles and renewable energy systems.
Table: Key Applications of A356 Aluminum Investment Casting
Industry | Common Applications | Benefits |
---|---|---|
Automotive | Engine components, manifolds | Lightweight, durable |
Aerospace | Turbine blades, structural parts | High-temperature resistance, precision |
General Industrial | Brackets, custom parts | Versatile, cost-effective |
6. Why Choose A356 Aluminum for Your Casting Needs?
What makes A356 aluminum such a popular choice? It’s the perfect balance of performance and cost. This section outlines why choosing A356 aluminum for investment casting is a smart move for your business.
One of the most compelling reasons to choose A356 aluminum is its strength and durability. Unlike other aluminum alloys, A356 maintains its structural integrity under high-stress conditions and high temperatures. This is why it is a preferred choice for industries that rely on high-performance parts, such as aerospace and automotive.
A356 aluminum is also highly cost-effective compared to other alloys, especially when you consider its overall performance and versatility. While there are other alloys that may perform similarly in one area, A356 aluminum is often the best option when looking for a balance of durability, weight reduction, and cost-efficiency.
Additionally, the casting process is highly efficient, allowing for minimal material waste. The intricate shapes that can be achieved through investment casting reduce the need for secondary machining, further driving down production costs.
Table: Advantages of Choosing A356 Aluminum
Benefit | Explanation |
---|---|
Strength & Durability | Withstands high stress and temperature |
Cost-Effective | Competitive pricing for high performance |
Efficient Casting | Less material waste, reduced machining |
7. The Role of A356 Aluminum in Modern Manufacturing
A356 aluminum plays a pivotal role in modern manufacturing, thanks to its ability to meet the growing demand for lightweight, durable, and precise parts. So, what’s the real story? A356 aluminum is the backbone of many advanced manufacturing processes, allowing companies to push the boundaries of what’s possible.
As industries move toward greener technologies and electric vehicles, A356 aluminum’s lightweight properties are in higher demand than ever before. Manufacturers are under increasing pressure to produce parts that meet stricter environmental standards while maintaining high performance. A356 aluminum meets these needs perfectly, helping manufacturers build products that are both eco-friendly and highly functional.
This material is also playing a major role in the advancement of manufacturing technologies. Investment casting techniques are evolving, and A356 aluminum is at the forefront of these changes. New casting methods allow for even more intricate designs and faster production times, which is helping industries reduce costs while improving product quality.
Table: A356 Aluminum’s Role in Modern Manufacturing
Trend | Impact on Manufacturing | Benefits |
---|---|---|
Electric Vehicles | Lightweight, cost-effective parts | Improved fuel efficiency, reduced weight |
Eco-Friendly Design | Meets environmental standards | Reduced carbon footprint |
8. Material Properties of A356 Aluminum
A356 aluminum is known for its impressive material properties, which make it a prime candidate for investment casting. So, why should you care about these properties? Understanding these characteristics will help you make better decisions when selecting materials for your next project.
The chemical composition of A356 aluminum includes approximately 7-9% silicon, which improves its fluidity during the casting process. The alloy also contains magnesium, which enhances its strength and makes it more resistant to corrosion. The combination of these elements gives A356 aluminum its impressive mechanical properties.
In addition to its chemical makeup, A356 aluminum is known for its physical properties. It has a low density, which contributes to its lightweight nature, while its high tensile strength ensures that parts made from A356 can handle significant stress without failing. This combination makes it ideal for use in demanding applications where both strength and weight reduction are crucial.
Table: Material Properties of A356 Aluminum
Property | Value |
---|---|
Chemical Composition | 7-9% Silicon, Magnesium |
Density | Low (ideal for lightweight parts) |
Tensile Strength | High (withstands significant stress) |
9. How to Choose the Right Foundry for A356 Aluminum Investment Casting
Choosing the right foundry is crucial for getting the best results when working with A356 aluminum investment casting. What’s the real story here? Selecting a reliable foundry ensures that your parts are manufactured to the highest quality standards.
Look for foundries with experience in investment casting and a track record of producing high-quality A356 aluminum components. The best foundries will offer quick turnaround times and ensure that the casting process is carefully controlled to avoid defects like porosity or warping.
Another key factor to consider is the foundry’s quality control processes. A reputable foundry will use advanced inspection methods, such as X-ray and ultrasonic testing, to ensure the integrity of the cast parts. Look for certifications that indicate the foundry follows strict industry standards and guidelines.
Table: Factors to Consider When Choosing a Foundry
Factor | Importance |
---|---|
Experience | Ensures the foundry can handle A356 aluminum |
Turnaround Time | Quick delivery for time-sensitive projects |
Quality Control | Prevents defects and ensures part integrity |
Certifications | Ensures compliance with industry standards |
10. Post-Casting Processes for A356 Aluminum
Once A356 aluminum has been cast, it undergoes several post-casting processes that enhance its mechanical properties and surface finish. What happens next? After casting, the part must be properly cooled, heat-treated, and finished to meet the desired specifications.
Heat treatment is often used to improve the strength and hardness of A356 aluminum. Depending on the application, parts can be treated to achieve various properties, such as increased tensile strength or improved corrosion resistance.
Surface finishing is another critical step. This can involve processes like shot blasting, polishing, or anodizing to improve the surface finish and provide a protective layer. These processes not only enhance the part’s appearance but also increase its longevity and resistance to environmental factors.
Table: Post-Casting Processes for A356 Aluminum
Process | Description |
---|---|
Heat Treatment | Improves strength and hardness |
Surface Finishing | Enhances appearance and resistance |
Machining | Final adjustments for precision |
11. Quality Control and Testing of A356 Aluminum Castings
To ensure the highest quality standards, A356 aluminum castings undergo a rigorous testing and quality control process. But here’s the kicker: without proper testing, even the best casting methods can result in defective parts.
The most common testing methods used for A356 aluminum include X-ray inspection and ultrasonic testing to detect internal defects. These non-destructive tests ensure that parts are free from cracks, porosity, or other structural issues that could compromise their performance.
Another key quality control process is dimensional inspection. Parts are measured against the original specifications to ensure they meet the required tolerances. Parts that do not pass inspection are either reworked or discarded, ensuring that only the highest-quality parts make it to the final customer.
Table: Quality Control and Testing Methods for A356 Aluminum
Test | Purpose |
---|---|
X-ray Inspection | Detects internal defects (cracks, porosity) |
Ultrasonic Testing | Detects flaws and voids in the casting |
Dimensional Inspection | Ensures parts meet required tolerances |
12. Cost Considerations for A356 Aluminum Investment Casting
When evaluating whether A356 aluminum investment casting is the right choice, cost is always a critical consideration. Let’s break down the factors that affect the price of A356 aluminum castings.
The initial cost of raw material for A356 aluminum can fluctuate depending on the market. However, the real cost often comes from the investment casting process itself, which requires specialized molds and precision equipment. While the upfront cost might be higher than traditional casting methods, the final product often requires less post-processing, making it a cost-effective option in the long run.
Other cost factors include tooling costs and labor costs. Highly skilled labor is required to operate the complex machinery involved in investment casting, and tooling costs can add up depending on the complexity of the design.
Table: Cost Factors for A356 Aluminum Investment Casting
Factor | Impact on Cost |
---|---|
Raw Material | Market fluctuations affect pricing |
Casting Process | Specialized equipment and molds increase cost |
Labor & Tooling | Skilled labor and complex tooling add to the expense |
13. Future Trends in A356 Aluminum Investment Casting
The future of A356 aluminum investment casting is bright, with continued innovation expected across various industries. Ready for the good part? Let’s explore the trends shaping the future of this material.
One key trend is the growing demand for electric vehicles and the role A356 aluminum plays in reducing vehicle weight. The lightweight nature of A356 aluminum helps manufacturers improve fuel efficiency and reduce emissions. As electric vehicle technology advances, A356 aluminum’s role in automotive manufacturing will only become more significant.
Additionally, advances in casting technology are enabling manufacturers to produce even more complex and lightweight parts. The future of A356 aluminum looks promising, with increased use in everything from aerospace components to renewable energy systems.
Table: Future Trends in A356 Aluminum Investment Casting
Trend | Impact on Industry |
---|---|
Electric Vehicles | Increased demand for lightweight parts |
Casting Innovation | More complex, lightweight, and efficient parts |
14. Environmental Considerations in A356 Aluminum Casting
As industries focus on sustainability, environmental considerations are becoming more important. What’s the real story? A356 aluminum is already a relatively eco-friendly material due to its recyclability and the reduced energy consumption of its casting process.
A356 aluminum can be recycled multiple times without losing its properties, making it a sustainable option for manufacturers. Moreover, the investment casting process itself is more efficient than traditional methods, generating less waste and using fewer raw materials.
Manufacturers can also reduce their carbon footprint by adopting green practices in the casting process, such as using energy-efficient equipment and minimizing emissions. As sustainability becomes a greater priority, A356 aluminum’s role in reducing environmental impact will continue to grow.
Table: Environmental Benefits of A356 Aluminum
Benefit | Explanation |
---|---|
Recyclability | Can be recycled without losing properties |
Efficiency | Investment casting generates less waste |
Green Practices | Adoption of energy-efficient techniques |
15. Conclusion
In summary, A356 aluminum investment casting offers exceptional benefits, including high strength, excellent corrosion resistance, and a superior casting process. Whether you are in the automotive, aerospace, or industrial sector, A356 aluminum provides the perfect combination of performance and cost-efficiency.
Ready to get started? A356 aluminum investment casting is a highly versatile solution for your casting needs. By choosing the right foundry and utilizing the material’s properties, you can ensure high-quality, durable parts for even the most demanding applications.
FAQ Section
Q1: What is A356 Aluminum?
A356 aluminum is a high-strength alloy commonly used in investment casting due to its excellent corrosion resistance and ability to withstand high temperatures.
Q2: How does A356 aluminum investment casting work?
The process involves creating a mold by coating a pattern with a ceramic shell, then pouring molten A356 aluminum into the mold to create precise parts.
Q3: What are the benefits of using A356 aluminum in casting?
A356 aluminum offers a high strength-to-weight ratio, excellent corrosion resistance, and superior casting properties, making it ideal for demanding applications.
Q4: Can A356 aluminum be used in high-temperature environments?
Yes, A356 aluminum is known for its ability to withstand higher temperatures, making it ideal for use in applications like engine components and exhaust systems.
Q5: How do I ensure the quality of A356 aluminum castings?
Quality can be ensured through rigorous testing, such as ultrasonic and X-ray inspection, and by working with reliable, experienced foundries that follow industry standards.