A356 aluminum casting is widely recognized for its impressive mechanical properties and versatile applications in several industries. In this article, we will explore the features of A356 aluminum, its advantages in investment casting, common uses, challenges faced during the casting process, and the factors that make it a preferred material for engineers and manufacturers. By the end of this guide, you will have a thorough understanding of A356 aluminum casting and how it can benefit your manufacturing needs.
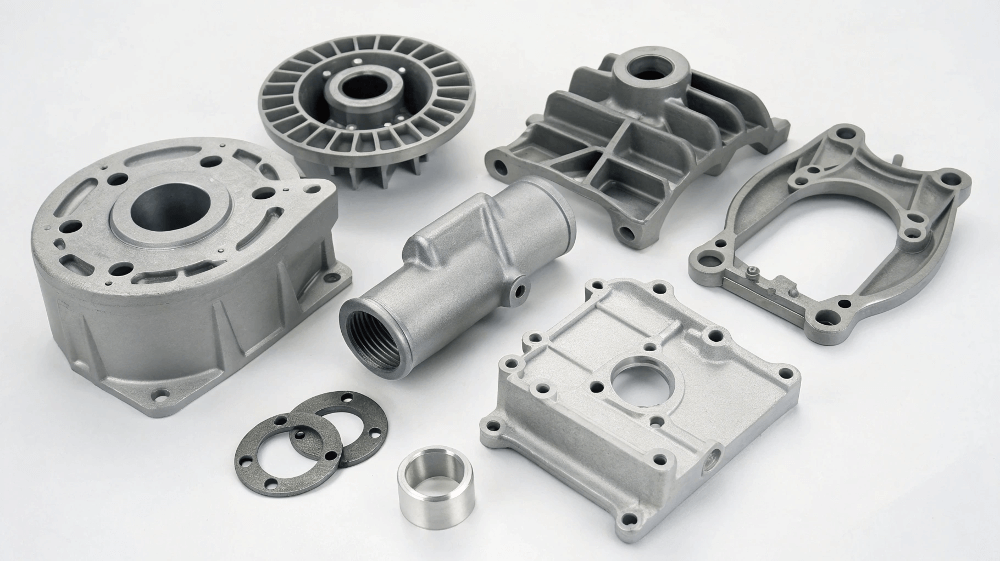
1. Introduction to A356 Aluminum Casting
A356 aluminum alloy is a popular material for investment casting due to its remarkable mechanical properties and versatility. Whether you’re working in the automotive, aerospace, or manufacturing industries, A356 offers strength, lightweight characteristics, and corrosion resistance, making it a go-to choice for many applications. But here’s the kicker: its ability to be precisely cast into complex shapes without compromising structural integrity is what truly sets it apart.
A356 aluminum casting starts with the investment casting process, a technique known for creating intricate and high-precision metal parts. It allows for the production of parts that would be difficult or even impossible to make using traditional machining methods. This process, combined with the material’s unique properties, makes A356 aluminum an ideal choice for industries where precision and reliability are critical.
By the end of this section, you should have a good grasp of what A356 aluminum is and why it’s such a vital part of the manufacturing world.
2. Characteristics of A356 Aluminum Alloy
A356 aluminum alloy is a heat-treatable, high-strength material commonly used for casting parts with a high level of precision. It is made up of primarily aluminum, silicon, and magnesium, which combine to offer a perfect balance of strength and ductility. The alloy’s mechanical properties make it suitable for applications that require both durability and lightness, such as automotive and aerospace components.
A356 aluminum’s composition consists of approximately 7.5-9.5% silicon, 0.2-0.5% magnesium, and the balance being aluminum. This composition gives A356 its excellent castability, ensuring that it can be used in a wide range of casting processes. The material’s melting point is around 1,100°F (593°C), which is relatively low compared to other metals, making it easier to work with in casting.
But here’s the interesting part: A356 aluminum has a tensile strength of about 35,000 psi and an elongation rate of around 8%. This means it can withstand significant stress and deformation before failure, which is why it’s so highly valued in industries where performance under pressure is essential.
Composition | Percentage |
---|---|
Silicon | 7.5-9.5% |
Magnesium | 0.2-0.5% |
Aluminum | Balance |
3. Benefits of Using A356 Aluminum in Investment Casting
Using A356 aluminum for investment casting brings several notable advantages that are important to manufacturers. These benefits range from its strength and durability to its ability to be cast into complex shapes. One of the major reasons for choosing A356 is its excellent corrosion resistance, which makes it ideal for outdoor applications or harsh environments.
This alloy’s strength-to-weight ratio is another significant benefit. A356 aluminum castings offer exceptional strength while being lightweight, which is particularly important in industries such as automotive and aerospace, where reducing weight is crucial for efficiency and performance. Additionally, A356 offers good thermal conductivity, which is an essential feature for applications that deal with heat-sensitive components.
But here’s the real kicker: A356 aluminum castings are cost-effective for large production runs, making them an ideal choice for mass-manufactured parts. The ability to produce high-quality components at a lower cost while maintaining high strength and durability ensures that A356 aluminum remains a top contender in many industries.
Benefit | Description |
---|---|
Strength-to-Weight Ratio | Offers high strength while remaining lightweight |
Corrosion Resistance | Ideal for use in harsh environments |
Cost-Effectiveness | Lower production costs for high-volume runs |
4. The Investment Casting Process for A356 Aluminum
The investment casting process for A356 aluminum involves several stages, beginning with the creation of a pattern that is then coated with a mold. The process is highly precise, allowing for intricate designs and shapes to be produced without the need for machining or additional finishing. This is where it gets interesting: unlike traditional casting methods, investment casting offers unparalleled precision and surface finish, which is why it’s so widely used for high-precision parts.
After the pattern is created, it is coated with a ceramic shell, and the mold is heated to remove any residual wax. This leaves behind a hollow shell that can withstand the high temperatures of molten aluminum. The mold is then filled with molten A356 aluminum, which is allowed to cool and solidify. After cooling, the mold is broken, revealing the finished part.
But what truly sets investment casting apart is its ability to produce parts with complex geometries, high precision, and tight tolerances, making it suitable for a wide range of industries.
Casting Process Step | Description |
---|---|
Pattern Creation | Create a pattern from wax or another material |
Molding | Coat pattern with ceramic shell |
Melting and Pouring | Pour molten A356 aluminum into the mold |
Cooling and Finishing | Allow cooling, then break the mold and finish the part |
5. Applications of A356 Aluminum Investment Castings
A356 aluminum castings are used in a variety of industries, where their strength, lightweight properties, and corrosion resistance make them indispensable. For example, in the automotive industry, A356 is commonly used to produce engine components, such as cylinder heads and intake manifolds. These parts need to withstand high pressures and temperatures, which A356 aluminum can handle with ease.
In aerospace, A356 is utilized for manufacturing aircraft components that require both strength and lightness. The alloy’s ability to resist corrosion from exposure to the elements makes it ideal for parts that must endure extreme environmental conditions. Additionally, consumer electronics manufacturers use A356 for parts like heat sinks and casings, where thermal conductivity and structural integrity are critical.
Ready for the good part? A356 aluminum is also popular in industrial machinery, where its reliability and durability make it the go-to material for components that face heavy wear and tear. The versatility of A356 in a variety of industries makes it a highly sought-after material for investment casting.
Industry | Applications |
---|---|
Automotive | Engine parts like cylinder heads and manifolds |
Aerospace | Aircraft parts such as structural components |
Consumer Electronics | Heat sinks, casings, and enclosures |
Industrial Machinery | Components exposed to heavy wear and tear |
6. Common Challenges in A356 Aluminum Casting
While A356 aluminum casting offers numerous benefits, it’s not without its challenges. One of the most common issues is the occurrence of surface imperfections, such as porosity. This can result from trapped gases or impurities in the mold, which can weaken the final part. To combat this, manufacturers must carefully control the casting process and ensure proper mold preparation.
Another challenge is shrinkage and distortion during cooling. A356 aluminum, like all metals, experiences some contraction as it cools, and if not managed properly, this can lead to dimensional inaccuracies or warping. One solution to this problem is using advanced simulation software to predict and correct these issues before casting.
But what’s the real story? Despite these challenges, A356 aluminum casting is still a top choice due to its ability to produce complex, high-precision components. With the right processes in place, these issues can be mitigated, ensuring that the final products meet industry standards.
Challenge | Solution |
---|---|
Surface Imperfections | Proper mold preparation and gas management |
Shrinkage and Distortion | Use of simulation software to predict and correct |
7. How to Choose a Reliable A356 Aluminum Casting Supplier
Choosing the right supplier for A356 aluminum investment casting is crucial to ensuring that the parts meet your specifications. One of the first steps is assessing the supplier’s experience and expertise in producing A356 castings. You want to work with a supplier who understands the complexities of the material and has a proven track record in the industry.
But here’s where it gets interesting: a reliable supplier should also offer transparency in pricing and lead times. It’s important to ensure that the supplier is capable of meeting your delivery deadlines and is open about any potential delays. In addition, quality control is a key factor—ensure that the supplier follows stringent testing procedures to ensure that every part meets the necessary standards.
Ready for the good part? Make sure to ask for references or case studies from the supplier’s past clients to verify their reputation and reliability.
Criteria | Why It’s Important |
---|---|
Experience | Ensures knowledge of A356 casting intricacies |
Transparency in Pricing | Helps with accurate budgeting and planning |
Quality Control | Guarantees consistent part quality |
8. Quality Control and Testing of A356 Aluminum Castings
When it comes to A356 aluminum investment casting, quality control is non-negotiable. The casting process can introduce defects that, if left unchecked, can compromise the part’s integrity. Common quality control measures include visual inspections, dimensional checks, and material testing. These steps ensure that the parts conform to the required specifications and meet industry standards.
A356 castings are also subjected to various mechanical tests, including tensile, hardness, and fatigue tests. These tests help manufacturers determine the material’s strength, durability, and performance under different stress conditions. For instance, a tensile test will reveal the maximum stress the material can endure before breaking, while a hardness test will assess the alloy’s resistance to indentation.
What’s the real story? By implementing rigorous quality control measures, manufacturers can ensure that A356 aluminum castings maintain their high performance and reliability across various applications.
Test | Purpose |
---|---|
Tensile Test | Determines maximum stress the material can withstand |
Hardness Test | Measures material’s resistance to indentation |
Fatigue Test | Assesses performance under repeated stress |
9. Cost Factors in A356 Aluminum Investment Casting
The cost of A356 aluminum investment casting can vary depending on several factors, including the complexity of the part, the size of the production run, and the supplier’s pricing structure. Larger production runs tend to bring down the per-part cost, making A356 a cost-effective option for high-volume manufacturing.
One of the key cost considerations is the mold. Investment casting requires a high-quality mold to ensure precise and defect-free parts. While the initial cost of creating the mold can be expensive, the long-term cost savings from reduced material waste and labor costs often outweigh this upfront investment.
But here’s the kicker: the quality of the final part can also affect cost. High-quality A356 castings require more precise production techniques, which may increase the overall cost. However, the durability and performance of these castings often make the extra cost worthwhile in industries where quality is paramount.
Cost Factor | Impact on Cost |
---|---|
Production Run Size | Larger runs reduce per-part cost |
Mold Creation | High-quality molds increase initial costs |
Part Quality | High-quality parts require more precise production |
10. Heat Treatment and Post-Casting Processes for A356 Aluminum
Heat treatment is a critical step in enhancing the mechanical properties of A356 aluminum castings. The process typically involves solution heat treating the material, followed by aging to improve its strength. This treatment helps to relieve internal stresses and enhance the casting’s overall durability.
After the casting is heat treated, post-casting processes such as machining, polishing, and surface finishing may be required to meet the final specifications. These processes help ensure that the part not only performs well but also meets the desired aesthetic standards.
But here’s where it gets interesting: post-casting processes can also help to eliminate any imperfections that may have occurred during the casting or heat treatment processes, ensuring that the final part meets all required specifications.
Process | Purpose |
---|---|
Heat Treatment | Improves strength and relieves internal stresses |
Post-Casting Finishing | Enhances part appearance and ensures dimensional accuracy |
11. Innovations in A356 Aluminum Casting Technology
As industries evolve, so does the technology used in A356 aluminum casting. One of the most significant innovations is the advancement of casting automation, which has improved the efficiency, precision, and consistency of the process. Automated systems can now handle complex casting tasks with little to no human intervention, reducing the risk of errors and increasing production speeds.
Additionally, new materials and coatings are being developed to improve the surface quality of A356 aluminum castings. These innovations help to reduce the occurrence of defects such as porosity and surface roughness, which are common challenges in casting.
What’s the real story? These innovations are making A356 aluminum casting even more efficient and cost-effective, ensuring that manufacturers can continue to produce high-quality parts without breaking the bank.
Innovation | Benefit |
---|---|
Casting Automation | Increases efficiency and reduces human error |
New Coatings | Improves surface quality and reduces defects |
12. Sustainability and Environmental Impact of A356 Aluminum Casting
Sustainability is becoming an increasingly important consideration in all industries, and A356 aluminum casting is no exception. The material itself is highly recyclable, making it an eco-friendly choice for manufacturers looking to reduce their carbon footprint. A356 castings can be recycled multiple times without losing their properties, contributing to a circular economy.
In addition, the casting process itself can be made more sustainable by optimizing energy use and minimizing material waste. Manufacturers are continually seeking ways to improve energy efficiency in the casting process, which not only reduces costs but also benefits the environment.
But here’s the kicker: the lightweight nature of A356 aluminum also helps to reduce fuel consumption in vehicles and machinery, further lowering the overall environmental impact.
Sustainability Factor | Impact |
---|---|
Recycling | Reduces material waste and conserves resources |
Energy Efficiency | Reduces energy consumption and operating costs |
13. Comparing A356 Aluminum with Other Materials for Casting
When it comes to investment casting, A356 aluminum offers several advantages over other materials such as steel and iron. Unlike steel, A356 aluminum is significantly lighter, making it an ideal choice for applications where weight is a concern, like automotive and aerospace industries.
While iron is often used for casting large components, it is heavier and more prone to corrosion than aluminum. A356 aluminum, on the other hand, provides excellent corrosion resistance, making it more suitable for outdoor or marine applications.
What’s the real story? When selecting the right material for casting, A356 aluminum’s combination of strength, lightness, and corrosion resistance makes it a clear winner in many industries.
Material | Advantages |
---|---|
A356 Aluminum | Lightweight, corrosion-resistant, strong |
Steel | Strong, but heavier and prone to corrosion |
Iron | Suitable for large parts but lacks corrosion resistance |
14. Future Outlook for A356 Aluminum Casting
The demand for lightweight materials is expected to grow, making A356 aluminum an even more attractive option for manufacturers in the future. As industries continue to prioritize sustainability and efficiency, A356 aluminum’s recyclability and energy-saving properties will only increase its appeal.
Moreover, the ongoing advancements in casting technology, such as 3D printing and advanced mold materials, will enable even more complex and precise parts to be produced using A356 aluminum. These innovations will ensure that A356 aluminum casting remains at the forefront of manufacturing for years to come.
Future Trend | Impact |
---|---|
Lightweight Materials | Increasing demand for energy efficiency and performance |
Advanced Casting Technologies | Enabling more complex, high-precision components |
15. Conclusion
A356 aluminum casting is a powerful material choice for manufacturers across various industries. With its exceptional strength-to-weight ratio, corrosion resistance, and versatility, it’s clear why A356 aluminum is a preferred choice for high-performance components. From automotive to aerospace, A356 aluminum continues to shine as an essential material in the manufacturing world.
For those looking to make the most of A356 aluminum casting, the key lies in selecting the right supplier, ensuring quality control, and staying updated with the latest industry trends. Ready for the good part? Now that you know the advantages and applications of A356 aluminum, it’s time to explore how it can fit into your production needs.
FAQ Section
Q1: What is A356 aluminum?
A356 aluminum is a heat-treatable alloy known for its high strength and excellent castability, commonly used in investment casting for parts requiring precision and durability.
Q2: How does the A356 aluminum investment casting process work?
The process involves creating a wax pattern, coating it with a ceramic shell, removing the wax, and then pouring molten A356 aluminum into the mold to form the desired part.
Q3: What industries use A356 aluminum castings?
A356 aluminum is used in automotive, aerospace, industrial machinery, and consumer electronics industries due to its strength, lightweight properties, and resistance to corrosion.
Q4: What are the common challenges in casting A356 aluminum?
Surface imperfections, shrinkage, and distortion are common challenges, which can be mitigated with proper quality control and advanced casting techniques.
Q5: How can I choose the best supplier for A356 aluminum investment casting?
Look for a supplier with proven experience, quality control procedures, transparent pricing, and reliable delivery times to ensure consistent, high-quality results.