Investment casting tooling is an essential process for producing precise metal parts in industries such as aerospace, automotive, and medical devices. The accuracy and quality of the final product heavily depend on the tooling used during the investment casting process. This article will explore various investment casting tooling techniques, materials, and innovations that ensure high-quality, complex parts. Whether you’re designing tooling from scratch or looking to improve your existing processes, understanding these methods is critical for success in precision casting.
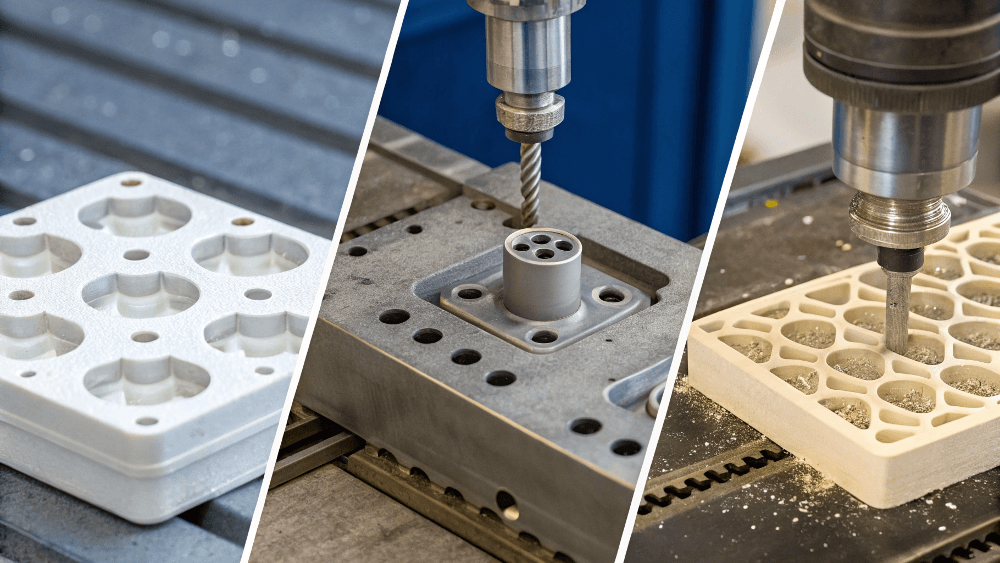
1. Introduction to Investment Casting Tooling
Investment casting tooling refers to the molds, patterns, and core structures used in creating high-precision metal parts through the investment casting process. Without the right tooling, achieving the desired accuracy and complexity in castings is nearly impossible. But here’s the kicker: the tooling directly affects not only the quality of the cast parts but also the cost and time efficiency of the entire casting process.
Tooling plays a vital role in investment casting, where molten metal is poured into a mold that’s been created using the tooling. The mold is often created by first coating a pattern in a ceramic shell and then heating the shell to harden it. The pattern is then melted away, leaving behind an empty mold that can be filled with molten metal. This technique allows for the production of complex shapes that would be difficult or even impossible to achieve using traditional machining methods.
The tooling process begins with creating the pattern, often using materials like wax or plastic. This pattern is then coated with a refractory material to form the mold. But what’s the real story? The precision with which the tooling is created will determine the quality of the final part. That’s why investment casting tooling is crucial for industries that require precision and reliability in their parts.
Table 1: Investment Casting Tooling Overview
Tooling Component | Function | Material Used | Application |
---|---|---|---|
Pattern | Template for the mold | Wax, Plastic | Used to form the mold cavity |
Mold | Container for molten metal | Ceramic, Sand | Holds the molten metal during cooling |
Core | Creates hollow sections in parts | Metal, Sand | Defines internal cavities in cast parts |
2. Key Components of Investment Casting Tooling
Understanding the key components of investment casting tooling helps ensure that each part is made with the highest standards of accuracy. These components include the pattern, mold, and core, each of which serves a critical function in the overall casting process.
The pattern is typically made from materials like wax or plastic, depending on the requirements of the casting. It is used to create the mold cavity. In wax-based patterns, the wax is melted away, leaving behind a hollow cavity into which molten metal is poured. But here’s the twist: in cases where complex geometries are involved, the pattern must be carefully designed and produced to minimize errors and defects in the final casting.
Next, the mold is created, often from a ceramic material that provides the necessary heat resistance. The mold must be capable of withstanding the high temperatures of the molten metal without deforming. The mold is also designed with enough strength to prevent any fractures or defects during the cooling process.
Finally, cores are used to form internal cavities within the cast parts. These cores are often made from a material that can withstand the heat of molten metal but can later be removed once the casting process is completed. Whether sand cores or metal cores, their design is crucial for forming parts with complex internal structures.
Table 2: Common Materials for Tooling Components
Tooling Component | Material Options | Key Properties |
---|---|---|
Pattern | Wax, Plastic, Foam | Easy to melt or remove, customizable |
Mold | Ceramic, Silica, Sand | Heat resistant, durable |
Core | Sand, Metal | Strong under heat, can create hollow sections |
3. Types of Investment Casting Tooling
Investment casting tooling can be categorized into different types based on the complexity of the part being cast. Each type serves a specific need and comes with its own set of advantages and limitations.
One common type of tooling is traditional tooling, which involves the use of wax patterns and ceramic molds. This method is widely used for parts with relatively simple geometries. However, when it comes to more complex shapes, the tooling must be more advanced. This is where custom tooling comes into play, particularly for parts with intricate internal structures or very fine details.
What’s the real story? For example, aerospace components often require advanced tooling because of their intricate shapes and precise measurements. These parts demand the highest standards of tooling design and production. This is where technology like 3D printing has made a significant impact, as it allows for the creation of more complex patterns and molds that would otherwise be very difficult to produce using traditional methods.
The choice between conventional tooling and advanced tooling depends on several factors, such as the complexity of the part, the material being used, and the overall cost of production. But here’s the kicker: choosing the right tooling for the job ensures better part quality and greater efficiency in the manufacturing process.
Table 3: Traditional vs. Advanced Tooling
Type of Tooling | Characteristics | Common Applications |
---|---|---|
Traditional Tooling | Simple designs, wax-based patterns | Automotive, standard machinery |
Advanced Tooling | Complex designs, often 3D printed | Aerospace, medical devices, precision parts |
4. Materials Used in Investment Casting Tooling
The materials used in investment casting tooling are crucial to the overall success of the process. These materials must meet the requirements of both the molten metal and the cast part itself. For example, the pattern material must be able to withstand the heat of the molten metal while being easily removed once the mold has hardened.
But here’s the twist: the material selection for the tooling is not always straightforward. Different casting requirements call for different tooling materials, and the wrong choice can lead to costly mistakes or defective parts. For example, some metals require higher melting points, which in turn may require more heat-resistant tooling materials.
One common material used for tooling is wax, especially for patterns. Wax is easy to melt and is ideal for creating highly detailed patterns. After the wax is removed, the mold is created by coating the pattern in a heat-resistant material, such as ceramic. The mold must then be capable of withstanding the high temperatures of the molten metal without cracking or deforming.
Another important material used in tooling is ceramic, which forms the mold for casting. The ceramic material must be capable of handling high temperatures and is often used for more complex parts requiring greater precision. In addition, some advanced tooling methods use metals or composite materials for molds and cores, especially when parts need to be durable and reusable over several casting cycles.
Table 4: Tooling Material Comparison
Material Type | Common Uses | Properties |
---|---|---|
Wax | Pattern creation | Easily melts away, cost-effective |
Ceramic | Mold construction | Heat-resistant, durable |
Metal | Core and advanced molds | Strong, heat-resistant, reusable |
5. The Role of Tooling in Precision and Accuracy
Precision is key in industries such as aerospace, automotive, and medical device manufacturing. But here’s the kicker: the quality of the tooling is the biggest determinant of part accuracy. Tooling defects or inaccuracies can lead to costly rework, delays, or the need for entirely new parts.
When it comes to precision, even small discrepancies in tooling can cause significant issues with the final casting. For example, if the mold design isn’t precise, it can lead to misalignment, shrinkage, or deformation in the final part. These issues are especially problematic in industries where even a small flaw can result in a failure during operation.
Tooling accuracy impacts not only the functionality of the part but also the time and cost of production. When tooling is accurate, parts are made faster and with fewer defects, leading to reduced costs and improved product quality. On the other hand, inaccurate tooling can result in delays, rework, and wasted materials.
But here’s the twist: in addition to creating accurate parts, tooling also needs to provide consistent results over time. This means that tooling materials must be durable enough to withstand repeated use without degrading in quality. With the right tooling, manufacturers can ensure that every part produced meets the required specifications.
Table 5: Tooling Accuracy and Its Impact on Production
Impact | Consequence | Result |
---|---|---|
Tooling Accuracy | High precision in mold and pattern | Reduced defects, better part quality |
Tooling Inaccuracy | Misalignment, deformation, shrinkage | Rework, delays, increased costs |
6. Steps in the Investment Casting Tooling Process
Investment casting tooling involves several critical steps to ensure the creation of precise parts. The process begins with designing the part and selecting the right material. Once the part is designed, the tooling team creates the pattern, which is often made from materials like wax, plastic, or foam.
What’s the real story? The pattern is then coated in a ceramic shell, which is heated to harden. Once the shell is hardened, the pattern is removed, leaving behind a hollow mold cavity. Afterward, molten metal is poured into the mold, where it cools and solidifies to form the desired part.
But here’s the kicker: this process can involve several iterations. After the first casting, the tooling may need to be adjusted or repaired to ensure it meets the required specifications. Tooling adjustments are particularly important for parts with tight tolerances or complex geometries.
The final step in the process involves inspecting the cast part to ensure it meets the necessary quality standards. This includes checking for defects, such as cracks, voids, or misalignment. If defects are found, the tooling may need to be adjusted and the part recast. Once the part passes inspection, it’s ready for use or further processing.
Table 6: Tooling Process Breakdown
Step | Description | Material Used |
---|---|---|
Design | Creating part design | CAD software, material selection |
Pattern Creation | Building pattern based on design | Wax, plastic, foam |
Mold Creation | Coating pattern with ceramic shell | Ceramic, silica |
Casting | Pouring molten metal into mold | Various metals |
Inspection | Verifying part quality | N/A |
7. Designing Tooling for Complex Castings
Designing tooling for complex castings requires careful consideration of part geometry, material properties, and production requirements. But here’s the kicker: the more complex the part, the more precise and intricate the tooling design must be.
For parts with intricate internal structures, such as aerospace components, the tooling must be designed to form these internal cavities accurately. This is where advanced techniques, such as 3D printing, come into play. 3D printing allows for the creation of highly detailed patterns that would be difficult to achieve with traditional methods.
What’s the real story? 3D-printed tooling can significantly reduce the time and cost associated with creating complex molds. It also allows for greater flexibility in design, enabling manufacturers to experiment with new shapes and structures without the risk of costly tooling errors.
Moreover, tooling for complex castings often requires the use of multiple cores or inserts to define the internal cavities. This makes the tooling more difficult to design and requires close collaboration between the design team and the casting engineers. But here’s the twist: when done correctly, complex tooling can yield parts that are lighter, stronger, and more efficient.
Table 7: Complex Tooling Design Considerations
Consideration | Impact | Solution |
---|---|---|
Part Geometry | Complex shapes require intricate tooling | Use 3D printing for intricate patterns |
Internal Structures | Requires precise core placement | Multiple cores and inserts |
Material Properties | Affect tooling material choice | Use heat-resistant materials for tooling |
8. Tooling Maintenance and Longevity
Tooling maintenance is critical for ensuring that molds and patterns maintain their accuracy and functionality over time. Regular maintenance helps prevent defects, extends tooling life, and ensures that parts continue to meet quality standards.
What’s the real story? Tooling can degrade over time due to wear and tear, high temperatures, and repeated use. This can lead to inaccuracies in the final castings, resulting in costly rework or delays. By properly maintaining tooling, manufacturers can ensure that the tooling remains in optimal condition and continues to produce high-quality parts.
Maintenance typically involves inspecting the tooling for signs of damage, such as cracks or wear marks. Any issues found are addressed promptly to prevent them from affecting the casting process. Tooling may also need to be cleaned or lubricated to prevent material build-up, which can affect the quality of the mold.
But here’s the kicker: maintaining tooling isn’t just about fixing issues when they arise—it’s also about preventing problems before they happen. Proactive maintenance schedules and regular inspections are key to keeping tooling in top condition and avoiding production disruptions.
Table 8: Tooling Maintenance Checklist
Maintenance Task | Frequency | Purpose |
---|---|---|
Inspect for cracks | Weekly | Prevent tooling failure |
Clean and lubricate | Monthly | Ensure smooth operation |
Check alignment | Every production run | Maintain part accuracy |
9. Costs Involved in Investment Casting Tooling
Investment casting tooling can be costly, particularly for complex parts or high-volume production. However, understanding the cost structure helps manufacturers make more informed decisions about tooling investment and resource allocation.
What’s the real story? The costs associated with tooling can vary depending on factors like part complexity, material selection, and the type of tooling required. Custom tooling, for example, tends to be more expensive than traditional tooling, as it requires more time and expertise to design and manufacture.
The cost of tooling also depends on the quantity of parts being produced. High-volume production often justifies the investment in high-quality tooling, as the cost per part decreases with larger quantities. On the other hand, low-volume production may benefit from lower-cost tooling options, such as 3D-printed patterns, to keep costs manageable.
But here’s the kicker: while tooling costs are a significant consideration, they are often outweighed by the benefits of producing high-quality parts with minimal defects. The right tooling can save money in the long run by reducing rework, improving part accuracy, and ensuring faster production cycles.
Table 9: Tooling Cost Breakdown
Tooling Type | Cost Range | Suitable For |
---|---|---|
Traditional Tooling | Low to moderate | Standard parts, low-volume |
Custom Tooling | High | Complex parts, high-volume |
3D-Printed Tooling | Moderate | Complex or prototype parts |
10. Tooling Innovations in the Investment Casting Industry
The investment casting industry has seen significant advancements in tooling technology over the past few years. From the use of 3D printing to the development of more durable materials, these innovations are transforming the way tooling is designed, produced, and maintained.
One major innovation is the use of 3D printing for creating patterns and molds. 3D printing offers manufacturers a way to produce highly complex and detailed parts that would be difficult or impossible to achieve using traditional tooling methods. In fact, 3D-printed tooling can help streamline production, reduce waste, and speed up time to market.
What’s the real story? 3D printing is particularly useful for creating prototypes or small batches of parts that require intricate designs. By reducing tooling lead times and minimizing material waste, 3D printing can significantly cut costs in these applications. Additionally, the ability to rapidly iterate designs allows manufacturers to fine-tune their tooling without incurring high costs.
But here’s the kicker: tooling innovations don’t stop with 3D printing. New materials, such as high-performance ceramics and advanced composites, are being developed to withstand higher temperatures and longer production cycles, increasing the durability and lifespan of tooling.
Table 10: Emerging Tooling Technologies
Technology | Description | Benefit |
---|---|---|
3D Printing | Printing of molds and patterns | Reduces lead times, allows for complex designs |
Advanced Materials | New composites and ceramics | Increases durability, withstands high temperatures |
Automation | Automated tooling production | Reduces labor costs, increases efficiency |
11. Choosing the Right Tooling Supplier
When selecting a tooling supplier, it’s essential to consider several factors that can affect the quality, cost, and efficiency of the tooling. A reliable supplier should have experience with your industry and be able to provide tooling that meets your specific requirements.
What’s the real story? The right tooling supplier will offer more than just products—they will also provide valuable support and guidance throughout the tooling design and production process. They should be able to work with your engineering team to develop customized solutions for your casting needs.
A good supplier will also have a track record of producing high-quality tooling that meets the required standards. They should be transparent about their processes, timelines, and pricing, and they should be able to offer a warranty or guarantee on their tooling. This ensures that if there are any issues with the tooling, they can be addressed promptly.
But here’s the kicker: choosing the right supplier is about building a long-term relationship. A good tooling supplier will be a partner in your success, helping you improve efficiency, reduce costs, and produce better-quality parts.
Table 11: Key Considerations When Choosing a Tooling Supplier
Consideration | Importance | What to Look For |
---|---|---|
Experience | High | Industry-specific knowledge, past projects |
Customization | High | Ability to design tooling for unique needs |
Support | Moderate | Ongoing support during tooling production |
Cost | Moderate | Competitive pricing without compromising quality |
12. The Future of Investment Casting Tooling
The future of investment casting tooling is bright, with new technologies and materials emerging that promise to revolutionize the process. These innovations are helping manufacturers produce parts more efficiently, at a lower cost, and with greater precision.
What’s the real story? In the future, we can expect to see more widespread use of 3D printing for tooling production. This technology will allow for faster production times, more intricate designs, and greater flexibility in tooling design. Additionally, advanced materials will continue to improve the performance and longevity of tooling, further reducing downtime and maintenance costs.
But here’s the kicker: sustainability is also becoming a key factor in the future of investment casting tooling. As manufacturers face increasing pressure to reduce waste and carbon footprints, there will be a greater focus on using recyclable and environmentally friendly materials in tooling production.
Table 12: Future Tooling Trends
Trend | Impact | Benefit |
---|---|---|
3D Printing | Faster production, complex designs | Reduces lead time, lowers costs |
Advanced Materials | Durable, heat-resistant materials | Longer tooling lifespan, better performance |
Sustainability | Eco-friendly materials | Reduces waste, lowers carbon footprint |
13. Common Problems with Investment Casting Tooling
While investment casting tooling can be highly effective, there are a few common issues that manufacturers face. These include tooling defects, misalignment, and material degradation, all of which can affect the quality of the final part.
What’s the real story? Tooling defects often occur due to poor design or material choices. For example, a mold that doesn’t hold its shape can lead to misaligned castings, which results in parts that don’t meet specifications. Additionally, improper cooling or heating of the tooling can cause cracks, leading to defects in the final casting.
The best way to avoid these problems is to carefully inspect tooling before production begins. Regular maintenance and timely repairs can also help mitigate the risk of defects. But here’s the kicker: when problems arise, it’s crucial to address them quickly to avoid costly delays and rework.
Table 13: Common Tooling Problems and Solutions
Problem | Cause | Solution |
---|---|---|
Misalignment | Poor mold design | Improve mold alignment, use precision tools |
Cracks | Improper heating or cooling | Regular inspections, correct temperature control |
Material Degradation | Wear and tear from use | Regular maintenance, use of durable materials |
14. Quality Control and Testing in Tooling
Ensuring that investment casting tooling meets quality standards is essential for producing high-quality cast parts. Quality control and testing are an integral part of the tooling process, helping to identify and correct issues before production begins.
What’s the real story? Quality control involves inspecting tooling for defects and verifying that it meets the required specifications. Testing can include checking for alignment, strength, and durability. But here’s the kicker: implementing strict quality control procedures not only improves part quality but also reduces the risk of costly production delays.
For example, tooling may undergo stress tests to ensure that it can withstand the high temperatures of molten metal without warping. It may also be tested for dimensional accuracy to ensure that the final parts match the design specifications.
Table 14: Quality Control Testing for Tooling
Test Type | Purpose | Frequency |
---|---|---|
Dimensional Accuracy | Ensure tooling meets specifications | Before each production run |
Strength Test | Check durability under stress | After each tooling modification |
Alignment Test | Ensure mold and pattern alignment | During routine inspections |
15. Conclusion
Investment casting tooling is crucial to the success of the casting process, ensuring high-quality, precise parts are produced efficiently. The choice of tooling, materials, and design methods can significantly impact the cost, accuracy, and longevity of the parts being cast. By selecting the right tooling and maintaining it properly, manufacturers can achieve the desired results while minimizing downtime and defects. So, whether you’re designing new tooling or refining existing processes, understanding these techniques will help ensure your investment casting projects are successful.
FAQ Section
Q1: What is investment casting tooling?
Investment casting tooling refers to the molds, patterns, and core structures used to create high-precision metal parts through the investment casting process. These components are essential for producing complex shapes and ensuring the desired accuracy in final cast parts.
Q2: How does investment casting tooling work?
Investment casting tooling works by creating a pattern that is coated with a ceramic shell to form a mold. Once the pattern is removed, molten metal is poured into the mold, where it cools and solidifies into the desired part.
Q3: What materials are used in investment casting tooling?
Common materials used in investment casting tooling include wax for patterns, ceramic for molds, and metals or sand for cores. The material selection depends on factors like the type of casting, temperature requirements, and part complexity.
Q4: Why is tooling maintenance important in investment casting?
Tooling maintenance is important to ensure the tooling remains accurate and functional over time. Regular maintenance prevents defects, reduces wear and tear, and helps extend the tooling’s lifespan, ensuring consistent part quality.
Q5: What challenges can occur during the investment casting tooling process?
Challenges can include misalignment, material degradation, and defects in the tooling design. These issues can result in defects in the final casting, delays in production, and increased costs. Proper maintenance and regular inspections are key to avoiding these problems.