In this article, we will explore the intricacies of 4130 carbon steel casting, focusing on its benefits, properties, and uses. 4130 carbon steel, a low-alloy steel that includes chromium and molybdenum, has become a go-to material in various industries such as aerospace, automotive, and defense. This guide will walk you through the composition, properties, applications, and the key benefits of using 4130 carbon steel in casting processes. Whether you are looking to improve your manufacturing processes or seeking to learn more about its advantages, this post will provide all the details you need.
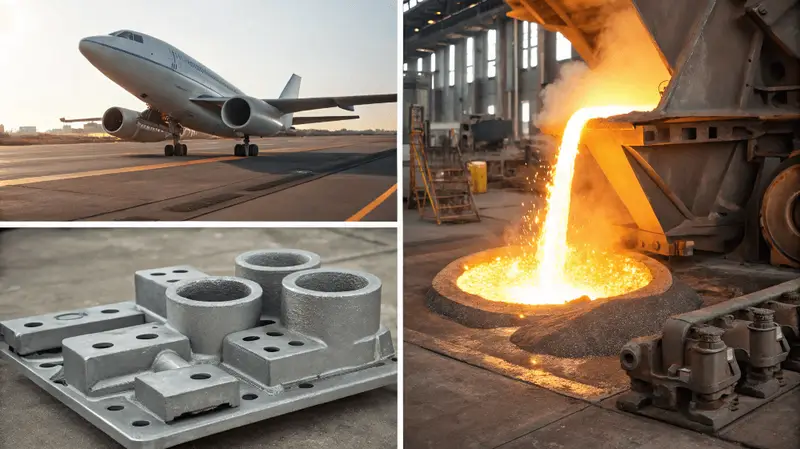
1. Introduction to 4130 Carbon Steel Casting
4130 carbon steel casting has grown in popularity due to its exceptional strength-to-weight ratio and versatility. It’s a popular choice across industries where performance, strength, and corrosion resistance are critical. So, what exactly is 4130 carbon steel? This low-alloy steel contains carbon, chromium, and molybdenum, offering improved strength and toughness compared to regular carbon steel. But here’s the kicker: the alloy also possesses great welding and machining capabilities, making it highly desirable in demanding applications such as aerospace, automotive, and defense.
When casting 4130 steel, manufacturers benefit from its ability to retain its properties even under stress. The casting process allows the material to be molded into complex shapes that are often difficult to achieve with other methods like forging or machining. The adaptability of 4130 steel enables it to meet stringent performance requirements in critical applications, whether in a military fighter jet or high-performance vehicle parts. This flexibility, combined with its high tensile strength, makes it an essential material in industries where performance under pressure is key.
2. Composition of 4130 Carbon Steel
The composition of 4130 carbon steel is a critical factor in its exceptional performance. So, what’s in the mix? The base composition of 4130 steel includes around 0.28% to 0.33% carbon, along with 0.80% to 1.10% chromium and 0.15% to 0.25% molybdenum. These alloying elements significantly enhance the steel’s properties, making it stronger and more durable than regular carbon steel. The addition of chromium increases resistance to oxidation and corrosion, while molybdenum improves the steel’s hardenability and ability to withstand high temperatures.
Here’s the real story: the combination of these elements allows 4130 steel to be heat-treated effectively to increase strength, a crucial factor in many industrial applications. This is why 4130 carbon steel is often chosen over other alloys when high strength-to-weight ratios are required. By varying the percentages of these elements, manufacturers can tailor the steel’s properties for specific purposes. For instance, more chromium could be added for applications requiring greater corrosion resistance, such as in the marine or chemical industries.
The precise control over the composition of 4130 carbon steel is a reason why it stands out in fields like aerospace, where lightweight yet durable materials are paramount. Whether it’s used for structural components or high-stress parts, the alloy’s composition ensures optimal performance across a wide range of conditions.
Composition Element | Percentage Range |
---|---|
Carbon | 0.28% to 0.33% |
Chromium | 0.80% to 1.10% |
Molybdenum | 0.15% to 0.25% |
3. Properties of 4130 Carbon Steel
What makes 4130 carbon steel unique? The properties of 4130 steel are what make it ideal for high-performance applications. It boasts excellent strength, toughness, and weldability. Ready for the good part? It also has excellent machinability, which is essential for producing precision parts. This steel is not just strong—it can also absorb impact without fracturing, making it suitable for use in applications where high fatigue resistance is necessary.
The mechanical properties of 4130 steel include high tensile strength, with a yield strength typically between 95,000 and 120,000 psi. This makes it an attractive option for industries that require components to withstand significant forces. Additionally, its elongation, which refers to how much the material can stretch before breaking, ranges from 15% to 20%. This property enhances its ability to withstand stress and strain in critical components, whether it’s a structural frame or engine component.
What’s the real story? The steel’s ability to resist wear and tear also plays a vital role. In corrosive environments, 4130 steel holds its own due to its resistance to oxidation, but it is worth noting that it is not immune to corrosion, especially in highly aggressive environments. So, when deciding if 4130 carbon steel is right for your needs, it’s essential to consider environmental factors like exposure to moisture or chemicals.
Property | Value |
---|---|
Tensile Strength | 95,000 to 120,000 psi |
Elongation | 15% to 20% |
Corrosion Resistance | Moderate (dependent on environmental factors) |
4. Common Applications of 4130 Carbon Steel
4130 carbon steel is used in various applications, especially in industries where high strength and low weight are critical. This includes everything from aerospace parts to high-performance racing cars. Let’s dive into some of the most prominent uses for 4130 steel. First, in aerospace, 4130 steel is often used in aircraft frames, landing gear components, and structural elements due to its strength and fatigue resistance. What’s the key takeaway? Its strength-to-weight ratio is ideal for aerospace applications, where minimizing weight while maintaining structural integrity is essential.
In the automotive industry, 4130 is commonly used in the manufacturing of roll cages, chassis, and suspension components. Ready for the interesting part? This material’s combination of toughness and light weight makes it perfect for motorsport applications, where performance under high stress is critical. Additionally, 4130 is also used in making machine parts that require precise tolerances and durability, such as gears and shafts.
In the military and defense sectors, 4130 steel is used to fabricate weapons systems, armor, and other defense technologies. Its resilience under extreme stress makes it highly valuable in military-grade equipment. The versatility of 4130 carbon steel is evident in its broad range of applications. It serves industries that rely on materials capable of withstanding rigorous conditions, all while maintaining strength and flexibility.
Industry | Common Applications |
---|---|
Aerospace | Aircraft frames, landing gear |
Automotive | Roll cages, chassis, suspension components |
Military | Weapons systems, armor, defense equipment |
5. Benefits of Using 4130 Carbon Steel for Casting
Why should you consider 4130 carbon steel for your casting needs? The benefits are significant. First and foremost, it offers an excellent balance between strength and weight. This means parts made from 4130 carbon steel can endure high loads without adding excessive weight. Think of it this way: in the aerospace or automotive industries, where weight savings can lead to substantial improvements in performance, using 4130 steel is a game-changer.
But here’s the kicker: 4130 carbon steel is also relatively easy to weld and machine compared to other high-strength alloys. This reduces manufacturing time and costs, making it a cost-effective option for complex casting applications. Furthermore, 4130 offers good resistance to oxidation and wear in moderate environments, which is a plus in industries like automotive or oil and gas.
Another advantage of 4130 steel is its excellent formability when heat-treated. It can be molded into intricate shapes, making it ideal for parts with complex geometries. Whether you are manufacturing high-precision components or durable structural parts, 4130 provides the flexibility to meet a range of needs.
Benefit | Description |
---|---|
Strength-to-weight ratio | Ideal for lightweight but durable parts |
Ease of welding and machining | Reduces manufacturing costs |
Corrosion resistance | Moderate resistance, suitable for many industries |
Formability | Ideal for casting complex shapes |
6. Comparing 4130 Carbon Steel to Other Steel Alloys
When comparing 4130 carbon steel to other steel alloys, it’s clear why it is such a popular choice in high-performance industries. Let’s start by comparing 4130 to 1045 steel. While 1045 steel is a medium-carbon steel known for its hardness, it lacks the alloying elements that give 4130 its unique properties. 4130 steel offers superior toughness and is more resistant to fatigue, making it a better option for high-stress applications.
But here’s where 4130 really shines: when compared to 4140 steel, another popular alloy, 4130 has a slightly lower tensile strength but offers improved machinability. This is a key factor when choosing materials for components that require intricate shaping or those that will undergo additional machining after casting. In aerospace, for instance, where precision is paramount, the ease of working with 4130 can save time and costs.
So, what’s the key takeaway here? When you need a material that combines strength, machinability, and fatigue resistance, 4130 carbon steel stands out as an optimal choice. Whether you are comparing it to 1045 or 4140, the combination of properties that 4130 offers is hard to beat.
Comparison | 1045 Steel | 4130 Steel | 4140 Steel |
---|---|---|---|
Tensile Strength | Lower | Moderate | Higher |
Machinability | Low | High | Moderate |
Fatigue Resistance | Moderate | High | High |
7. 4130 Carbon Steel Casting Process
The casting process for 4130 carbon steel involves several critical steps, each of which contributes to the final product’s quality. It all starts with selecting the right mold material. To get the best results, a high-quality sand or shell mold is often used. These molds ensure that the steel is cast with minimal imperfections. After preparing the mold, the 4130 steel is heated until it melts, usually at temperatures around 2,500°F (1,370°C). Once melted, the liquid steel is poured into the mold to form the desired shape.
Once the casting has cooled, it is removed from the mold and undergoes cleaning and inspection. At this stage, any imperfections or rough edges are smoothed out. What’s the real story here? The cooling process is critical in determining the properties of the cast steel. If the cooling is too fast, the steel could become brittle; too slow, and it could remain too soft. That’s why managing the cooling rate is key to achieving the right balance of strength and ductility.
For larger or more complex parts, additional machining or heat treatment may be required. Heat treatment helps further refine the steel’s properties, ensuring that the final product meets the necessary specifications for its application.
Step | Description |
---|---|
Mold preparation | High-quality sand or shell mold to reduce imperfections |
Melting | Heat the steel to around 2,500°F (1,370°C) |
Pouring | Pour liquid steel into the mold to form the part |
Cooling | Controlled cooling to ensure optimal properties |
Post-casting | Cleaning, inspection, and possible machining |
8. Factors Affecting the Quality of 4130 Carbon Steel Castings
The quality of 4130 carbon steel castings can be influenced by several factors. One of the most important is the composition of the alloy itself. Even small deviations from the desired mix of carbon, chromium, and molybdenum can affect the material’s properties. So, what can go wrong? If the alloy is not properly mixed, the steel may exhibit inconsistent properties, such as weak spots or brittleness in areas that should be strong.
Another key factor is the casting process itself. Issues like improper mold design, contamination, or incorrect pouring temperatures can lead to defects like porosity, cracks, or other imperfections. That’s why precise control over every step of the casting process is critical to achieving high-quality results.
Ready for the good part? Heat treatment can also play a significant role in the final quality of the casting. Proper heat treatment helps ensure that the steel has the right balance of hardness, toughness, and fatigue resistance. However, improper or inconsistent heat treatment can lead to undesirable characteristics, such as uneven hardness or brittleness.
Factor | Impact on Quality |
---|---|
Alloy composition | Inconsistent properties if not properly mixed |
Casting process | Contamination or incorrect temperatures can cause defects |
Heat treatment | Ensures desired hardness and toughness if done correctly |
9. Heat Treatment of 4130 Carbon Steel Castings
Heat treatment is one of the most important processes for enhancing the properties of 4130 carbon steel castings. So, how does it work? Heat treatment typically involves heating the material to a specific temperature and then cooling it at a controlled rate. The two most common types of heat treatment for 4130 steel are annealing and tempering.
Annealing involves heating the steel to a high temperature and then slowly cooling it to remove internal stresses and soften the material. This process improves the steel’s machinability and formability. Ready for the interesting part? Tempering is done after hardening to reduce brittleness while maintaining strength. This process is critical in ensuring that the material has the right combination of toughness and strength for its intended use.
The key takeaway is that heat treatment allows manufacturers to customize the properties of 4130 carbon steel castings for specific applications. Whether you’re making automotive parts or aerospace components, the right heat treatment process ensures the steel is optimized for its intended function.
Heat Treatment | Purpose |
---|---|
Annealing | Softens the material, improves machinability |
Tempering | Reduces brittleness, increases toughness |
10. Challenges in 4130 Carbon Steel Casting
Casting 4130 carbon steel can present several challenges, primarily due to the material’s high alloy content and tendency to form certain defects. What are the key challenges? One of the most common issues is porosity, where small gas pockets form within the cast steel. This can weaken the material and compromise its integrity.
Another challenge is controlling the cooling rate during the casting process. If the steel cools too quickly, it can form cracks or become too brittle. On the other hand, if the cooling process is too slow, the steel may not achieve the desired hardness. So, what’s the key to overcoming these challenges? It all comes down to precise control over the alloy composition, casting temperature, and cooling rate.
Welding can also present challenges when working with 4130 steel. Due to its high carbon content, the material is more prone to cracking during welding. To address this, manufacturers must use specialized welding techniques, such as preheating the material or using low hydrogen electrodes.
Challenge | Impact |
---|---|
Porosity | Weakens material, reduces integrity |
Cooling rate | Can cause cracks or insufficient hardness |
Welding | Prone to cracking during the welding process |
11. Welding 4130 Carbon Steel Castings
Welding 4130 carbon steel castings requires careful consideration of the steel’s properties. Ready for the good part? While 4130 carbon steel is weldable, its high carbon content can lead to cracking if not handled properly. So, how do you avoid these issues? Preheating the material before welding is often essential to prevent cracking. Additionally, using the correct type of filler material, such as low hydrogen electrodes, helps minimize the risk of defects.
The real key to welding success with 4130 steel lies in managing the heat input during the welding process. Too much heat can cause distortion, while too little can result in weak welds. So, it’s critical to strike the right balance to ensure strong, durable welds.
Additionally, post-weld heat treatment can help relieve residual stresses in the material, ensuring that the final welded part retains its desired mechanical properties. In many applications, such as aerospace and automotive, the integrity of the weld is just as important as the properties of the base material.
Welding Consideration | Best Practice |
---|---|
Preheating | Reduces risk of cracking |
Filler material | Use low hydrogen electrodes |
Heat input | Balance heat for strong, durable welds |
12. 4130 Carbon Steel Casting in Aerospace
Aerospace applications demand materials that can withstand extreme conditions without sacrificing performance. 4130 carbon steel is a perfect fit for these requirements. What’s the real story? The strength and durability of 4130 steel make it ideal for aerospace applications, especially where weight reduction is crucial without compromising strength. Common uses include structural components like wing spars, landing gear, and aircraft frames.
In addition to its high tensile strength, 4130 steel is resistant to fatigue, a key factor in the high-stress environment of aerospace. Ready for the kicker? Its excellent machinability means that it can be precisely shaped to meet the tight tolerances required in aerospace manufacturing. Moreover, 4130’s ability to withstand both high and low temperatures makes it a reliable material for use in a wide range of aerospace environments, from high-altitude conditions to extreme temperature shifts during flight.
Aerospace Application | Use of 4130 Carbon Steel |
---|---|
Aircraft frames | Strong, lightweight construction |
Landing gear | Fatigue-resistant, durable |
Structural components | Precision manufacturing, high strength |
13. Cost Considerations for 4130 Carbon Steel Castings
When considering 4130 carbon steel for your casting needs, it’s important to factor in the cost. What’s the breakdown? While 4130 steel may be more expensive than other materials like 1045 or 4140, its superior performance and versatility often make it a cost-effective choice in the long run. By reducing the need for expensive replacements or repairs due to material failure, 4130 can offer significant cost savings, particularly in high-performance applications.
The initial investment in 4130 carbon steel casting may be higher, but the material’s durability, ease of machining, and reduced need for maintenance make it a worthwhile investment for critical applications. So, how does it compare to other materials in terms of cost? 4130 offers a balance of performance and cost, often beating out higher-cost alternatives in the aerospace and automotive industries.
Material | Cost | Benefits |
---|---|---|
4130 Carbon Steel | Higher initial cost | Durability, strength, versatility |
1045 Carbon Steel | Lower cost | Good for basic applications, less durable |
4140 Steel | Higher cost | Higher tensile strength, tougher than 4130 |
14. Best Practices for Manufacturing 4130 Carbon Steel Castings
Manufacturing 4130 carbon steel castings requires careful attention to several factors to ensure the best results. What are the best practices? First and foremost, it’s crucial to control the casting temperature and cooling rate to avoid defects such as cracks or porosity. Properly managing the mold and using the right alloy composition are also critical to achieving high-quality results.
Moreover, proper heat treatment is essential to ensure that the steel meets the required strength and toughness standards. Whether you are manufacturing automotive parts or aerospace components, following industry-standard best practices ensures that each casting meets its performance requirements.
Best Practice | Description |
---|---|
Control casting temperature | Prevent defects like cracks or porosity |
Manage cooling rate | Achieve the desired strength and toughness |
Use the correct alloy composition | Ensure optimal material properties |
15. Conclusion
To sum up, 4130 carbon steel casting is a remarkable material that combines strength, toughness, and machinability. Its composition, properties, and versatility make it ideal for demanding applications in aerospace, automotive, and other industries. The material’s benefits, including its cost-effectiveness, ease of welding, and machining, make it an optimal choice for manufacturers seeking durable, high-performance parts. So, if you’re looking to enhance the performance of your products or improve your manufacturing processes, 4130 carbon steel casting could be the perfect solution.
FAQ Section
Q1: What is 4130 carbon steel?
4130 carbon steel is a low-alloy steel that contains carbon, chromium, and molybdenum. It is used for its strength, toughness, and versatility in various industries, including aerospace and automotive.
Q2: How does the casting process for 4130 carbon steel work?
The casting process involves melting the 4130 alloy, pouring it into molds, and cooling it to solidify. The process allows the creation of complex shapes while retaining the steel’s high strength.
Q3: Why is 4130 carbon steel commonly used in aerospace?
4130 carbon steel is used in aerospace due to its strength-to-weight ratio, resistance to fatigue, and machinability. It is ideal for structural components and parts that require high performance under stress.
Q4: What are the main advantages of using 4130 carbon steel for casting?
4130 carbon steel offers excellent strength, machinability, and resistance to fatigue. It also has a good balance between performance and cost, making it ideal for critical applications.
Q5: What are some common challenges when casting 4130 carbon steel?
Challenges include controlling the alloy composition, managing the cooling rate, and preventing defects like porosity and cracking. Proper heat treatment and quality control help overcome these issues.