Stainless steel casting is one of the most important manufacturing processes, offering unique benefits such as strength, durability, and resistance to corrosion. This article will provide a comprehensive guide to stainless steel casting, explaining the process, benefits, types of materials used, common applications, and how it compares to other casting methods. We will also cover how to choose the right supplier and tackle quality control challenges. Whether you are a manufacturer, procurement officer, or involved in the casting industry, this guide will give you the necessary insights to better understand stainless steel casting.
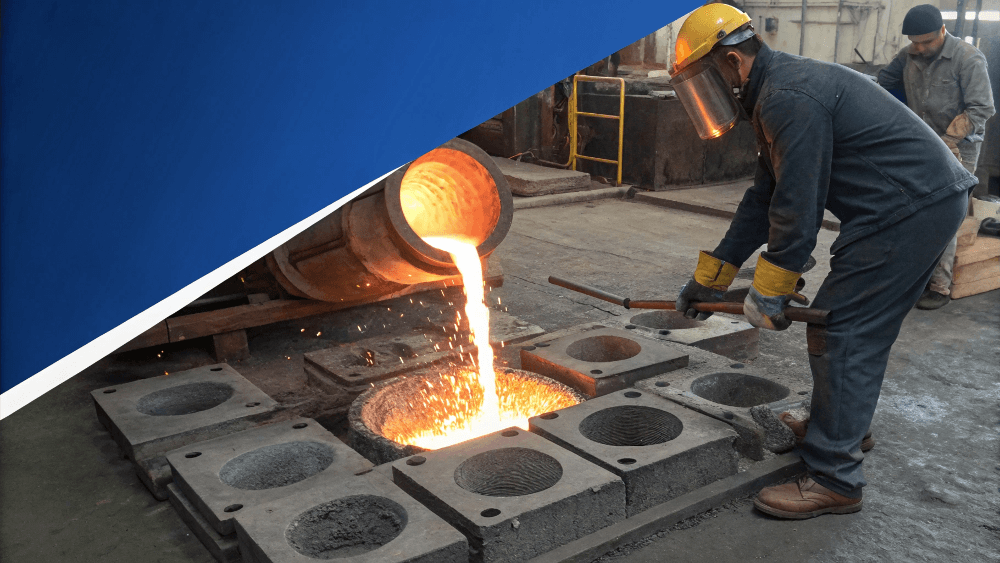
1. Introduction: Understanding Stainless Steel Casting
Stainless steel casting is a critical process used to create parts and products that require high strength and resistance to corrosion. The importance of stainless steel casting cannot be overstated, especially in industries that demand precision and durability. What’s the real story here? Stainless steel castings are essential in sectors such as aerospace, automotive, and medical devices due to their ability to withstand harsh environments and high temperatures. It is a versatile process that enables manufacturers to produce complex geometries and intricate designs.
Ready for the good part? The main goal of this guide is to simplify the stainless steel casting process, explain its advantages, and help you make informed decisions regarding the material, methods, and suppliers. By the end, you will have a solid understanding of how stainless steel casting works and why it is the go-to solution for high-quality manufacturing. Let’s dive deeper into what stainless steel casting actually involves.
Table 1: Types of Stainless Steel Castings
Type of Stainless Steel | Characteristics | Common Applications |
---|---|---|
Austenitic | Non-magnetic, excellent corrosion resistance | Food processing, medical devices |
Ferritic | Magnetic, corrosion resistant | Automotive exhaust systems |
Martensitic | High hardness, good wear resistance | Surgical instruments |
Duplex | Combines austenitic and ferritic properties | Oil and gas industries |
2. What is Stainless Steel Casting?
Stainless steel casting is the process of pouring molten stainless steel into a mold to create a specific shape. This method allows for the production of complex shapes and designs that might be difficult or impossible to achieve through other manufacturing techniques. The casting process involves heating stainless steel until it becomes liquid, then pouring it into a mold and allowing it to solidify. The result is a part that has the desired strength, precision, and surface finish.
What’s the catch here? Stainless steel casting is not just about pouring metal into a mold. There are various types of molds used depending on the application, and the process requires great precision to ensure the final product meets the required standards. This is where the expertise of the casting team becomes crucial.
The process also involves strict temperature control, careful monitoring of the cooling rate, and post-casting treatments to ensure that the casting is free of defects. And this is where stainless steel casting truly shines — it offers a level of detail and complexity that is hard to match in other methods like forging or machining.
Table 2: Stainless Steel Casting Process Steps
Step | Description |
---|---|
Melting | Stainless steel is melted at high temperatures |
Molding | Liquid metal is poured into a pre-formed mold |
Cooling | Metal solidifies in the mold to form the casting |
Finishing | Castings are cleaned, inspected, and tested |
3. Types of Stainless Steel Used in Casting
The choice of stainless steel for casting significantly affects the material’s performance and suitability for specific applications. Stainless steel is available in several grades, each with its own unique properties. Here’s where things get interesting. The most commonly used types of stainless steel for casting include:
- Austenitic Stainless Steel: This is the most commonly used type due to its excellent corrosion resistance and good mechanical properties. It is widely used in industries like food processing and medical devices.
- Ferritic Stainless Steel: Known for its resistance to stress corrosion cracking, ferritic stainless steel is commonly used in automotive applications, especially for exhaust systems.
- Martensitic Stainless Steel: This type is characterized by high hardness and wear resistance, making it ideal for applications that require strength and durability, such as surgical instruments and knives.
- Duplex Stainless Steel: Combining the advantages of both austenitic and ferritic grades, duplex stainless steel is highly corrosion-resistant and is commonly used in the oil and gas industry.
But here’s the kicker — the choice of stainless steel grade impacts not only the casting process but also the final product’s cost and performance. For example, using a more specialized grade might increase the material cost but can offer superior durability or resistance in certain environments.
Table 3: Comparison of Stainless Steel Grades for Casting
Stainless Steel Grade | Corrosion Resistance | Hardness | Common Uses |
---|---|---|---|
Austenitic | High | Medium | Food, medical, chemical processing |
Ferritic | Medium | Low to medium | Automotive, architectural |
Martensitic | Medium to high | High | Surgical instruments, valves |
Duplex | Very high | High | Oil, gas, chemical processing |
4. The Stainless Steel Casting Process
The stainless steel casting process is a fascinating combination of metallurgy and engineering. The process typically starts with designing a mold based on the desired product shape. Then, molten stainless steel is poured into the mold and allowed to cool. As the metal cools, it solidifies and forms the final product. There are several techniques used in stainless steel casting, each with specific advantages depending on the project requirements.
What’s the real story? While the basic process seems straightforward, there are several factors that can influence the success of the casting. For example, the temperature of the molten metal must be carefully controlled to prevent defects like porosity or cracks. Similarly, the cooling rate must be optimized to ensure that the metal solidifies evenly, which affects the material properties of the final product.
In addition to traditional methods, advanced technologies such as 3D printing are making their way into the stainless steel casting process. This can allow for even more precise and complex designs, reducing the need for post-casting modifications. These technological advancements are revolutionizing the casting industry.
Table 4: Common Stainless Steel Casting Techniques
Technique | Description | Advantages |
---|---|---|
Sand Casting | Uses sand molds to form the castings | Low cost, ideal for complex shapes |
Investment Casting | Uses a ceramic shell for high-precision parts | High accuracy, smooth surface finishes |
Die Casting | Uses metal molds for high-volume production | Fast production, suitable for mass production |
Lost Foam Casting | Uses a foam pattern that evaporates in the mold | Ideal for intricate parts, reduces material waste |
5. Benefits of Stainless Steel Casting
Stainless steel casting offers a range of benefits that make it the preferred choice for many industries. For starters, stainless steel is known for its strength and corrosion resistance, which is critical in applications like aerospace, automotive, and medical device manufacturing. What’s the kicker here? Stainless steel also performs well at high temperatures, making it ideal for components that will be exposed to heat, such as engine parts or heat exchangers.
Furthermore, stainless steel castings are extremely durable, which means they require less maintenance and have a longer service life. This can translate to significant cost savings over time, especially in industries where parts are subjected to harsh conditions. The versatility of stainless steel casting allows manufacturers to produce complex parts in a wide range of shapes and sizes, which would be difficult or expensive to produce using other methods.
Ready for the good part? Stainless steel casting also offers great flexibility in terms of material composition, enabling manufacturers to tailor the alloy properties to meet specific performance requirements. Whether you need increased strength, better corrosion resistance, or improved wear resistance, stainless steel casting can be optimized for the job.
Table 5: Benefits of Stainless Steel Casting
Benefit | Description |
---|---|
Strength | Excellent strength-to-weight ratio |
Durability | Long service life with minimal maintenance |
Corrosion Resistance | Resistant to rust, oxidation, and other forms of corrosion |
High-Temperature Performance | Performs well in extreme heat environments |
6. Common Applications of Stainless Steel Castings
Stainless steel castings have a wide variety of applications, making them essential in many industries. From automotive parts to industrial equipment, stainless steel castings are used for products that need to withstand extreme conditions. But here’s the kicker — the versatility of stainless steel casting means it can be used in almost any industry. In the automotive sector, stainless steel castings are used for exhaust systems, engine components, and structural parts. In aerospace, stainless steel castings are found in turbine blades, fuel nozzles, and landing gear.
What’s the real story? Stainless steel castings are also heavily used in the food processing industry, where sanitary conditions are essential. Medical devices such as surgical instruments and implants also rely on stainless steel casting for their strength and biocompatibility. The ability to create customized, complex shapes makes stainless steel casting a go-to method for manufacturing parts in these high-demand fields.
Table 6: Common Applications of Stainless Steel Castings
Industry | Common Applications | Importance |
---|---|---|
Automotive | Exhaust systems, engine components | Durability, heat resistance |
Aerospace | Turbine blades, landing gear | High strength, ability to withstand heat |
Medical Devices | Surgical instruments, implants | Biocompatibility, strength |
Food Processing | Pumps, valves, conveyors | Sanitation, corrosion resistance |
7. Stainless Steel Casting vs Other Casting Methods
When it comes to manufacturing, choosing the right casting method is crucial for ensuring that the final product meets the required specifications. So, what makes stainless steel casting stand out from other methods like aluminum casting or iron casting? For one, stainless steel is known for its superior corrosion resistance and strength, which makes it ideal for applications that require durability in extreme environments.
Ready for the good part? Stainless steel casting also offers better wear resistance and higher temperature performance compared to aluminum or iron castings. While aluminum casting is ideal for lighter, less durable applications, stainless steel is better suited for high-performance environments. Iron casting, on the other hand, is often more affordable but doesn’t offer the same level of corrosion resistance or strength.
Table 7: Comparison of Stainless Steel Casting vs Other Methods
Casting Method | Strength | Corrosion Resistance | Temperature Performance |
---|---|---|---|
Stainless Steel | High | Excellent | Excellent |
Aluminum | Medium | Good | Good |
Iron | Low | Moderate | Poor |
8. Common Defects in Stainless Steel Castings
While stainless steel casting offers numerous advantages, it is not without its challenges. Common defects in stainless steel castings include porosity, shrinkage, and cracks. These issues can arise during the cooling and solidification process, and they can affect the integrity of the final product. But here’s the kicker — understanding these defects and knowing how to avoid them can save you time and money in the long run.
What’s the real story? Porosity, which refers to the presence of tiny air pockets in the metal, can occur when the metal cools too quickly or the mold is not properly vented. Shrinkage, on the other hand, happens when the metal contracts as it cools. Cracks may form if the metal is cooled too rapidly or exposed to excessive stress. Fortunately, many of these issues can be minimized by carefully controlling the casting process, such as optimizing the mold design and cooling rate.
Table 8: Common Defects in Stainless Steel Castings
Defect | Cause | Solution |
---|---|---|
Porosity | Rapid cooling, poor venting | Adjust cooling rate, improve mold design |
Shrinkage | Metal contraction during cooling | Use proper gating and riser systems |
Cracks | Excessive cooling, high stress | Control cooling rate, reduce stress on metal |
9. Quality Control in Stainless Steel Casting
Quality control is essential in stainless steel casting to ensure that the final product meets the required specifications. The process involves rigorous testing, including visual inspection, dimensional measurement, and mechanical testing. Non-destructive testing (NDT) methods such as ultrasonic testing and X-ray inspection are also commonly used to detect internal defects that may not be visible to the naked eye.
Ready for the good part? The key to high-quality stainless steel castings lies in maintaining consistent casting practices, using the right materials, and ensuring that all tests are properly conducted. Quality assurance should start with the design phase and continue through to the final inspection, ensuring that the parts meet industry standards and customer requirements.
Table 9: Common Quality Control Methods in Stainless Steel Casting
Quality Control Method | Description | Application |
---|---|---|
Visual Inspection | Checking for surface defects | Initial inspection |
Dimensional Measurement | Verifying the size and shape of the casting | Ensures accuracy |
Non-Destructive Testing | Using techniques like ultrasonic or X-ray | Detects internal defects |
10. Cost Considerations in Stainless Steel Casting
While stainless steel casting offers numerous advantages, it can also be more expensive compared to other casting methods. The cost of stainless steel casting is influenced by several factors, including the material cost, labor costs, and the complexity of the casting. What’s the kicker here? While stainless steel casting may cost more upfront, the long-term benefits in terms of durability and performance often outweigh the initial investment. For example, in industries that require parts to withstand extreme conditions, stainless steel casting can save money in maintenance and replacements over time.
Table 10: Factors Affecting the Cost of Stainless Steel Casting
Factor | Impact on Cost |
---|---|
Material Quality | High-quality alloys increase costs |
Complexity of Design | Complex molds and shapes raise costs |
Production Volume | Larger volumes reduce per-unit costs |
11. Innovations in Stainless Steel Casting Technology
The world of stainless steel casting has seen numerous innovations in recent years. From advancements in mold technology to the integration of 3D printing, new techniques are helping manufacturers create more precise and complex castings with greater efficiency. What’s the real story? These innovations have the potential to drastically reduce production times, improve the quality of castings, and lower costs.
Ready for the good part? 3D printing, for example, allows for the creation of molds with intricate details and designs that were previously difficult to achieve. The use of automated processes and robotics in the casting process is also helping to increase efficiency and consistency, leading to higher-quality products and reduced production costs.
Table 11: Innovations in Stainless Steel Casting
Innovation | Description | Benefit |
---|---|---|
3D Printing | Creating complex molds using 3D printers | Enables intricate designs and faster production |
Automation | Using robots and automated systems | Increases precision and reduces labor costs |
Advanced Materials | New alloys and coatings | Improves durability and performance |
12. How to Choose the Right Stainless Steel Casting Supplier
Choosing the right supplier is crucial for ensuring that you receive high-quality stainless steel castings that meet your specifications. What’s the real story? A good supplier should have a proven track record in the industry, a commitment to quality, and the capability to meet your production deadlines. Start by looking at the supplier’s certifications, experience, and customer reviews. What’s the kicker here? It’s also essential to ask for samples or prototypes to test the quality before committing to a large order.
Ready for the good part? Ask potential suppliers about their production capabilities, quality assurance practices, and post-casting services, such as finishing and inspection. The right supplier will not only provide high-quality products but also help you streamline your manufacturing process.
Table 12: Key Factors When Choosing a Supplier
Factor | Importance |
---|---|
Certifications | Ensures adherence to industry standards |
Experience | Demonstrates reliability and expertise |
Customer Reviews | Provides insight into product quality and service |
Post-Casting Services | Ensures proper finishing and quality control |
13. Environmental Considerations in Stainless Steel Casting
As the world becomes more focused on sustainability, the environmental impact of manufacturing processes, including stainless steel casting, is coming under scrutiny. Ready for the good part? Stainless steel casting can be environmentally friendly if manufacturers adopt the right practices. For example, many foundries now focus on recycling metal scrap to reduce waste and minimize the carbon footprint.
But here’s the kicker — modern stainless steel casting methods are increasingly being designed to use less energy and produce fewer emissions. By adopting eco-friendly practices and utilizing recycled materials, the industry can reduce its environmental impact while still producing high-quality castings.
Table 13: Environmental Practices in Stainless Steel Casting
Practice | Impact on Environment |
---|---|
Recycling Metal Scrap | Reduces waste and conserves resources |
Energy-efficient Processes | Lowers energy consumption and emissions |
Sustainable Sourcing | Reduces reliance on non-renewable resources |
14. Conclusion: The Future of Stainless Steel Casting
As industries continue to evolve, the demand for high-quality, durable components will keep growing. What’s the real story here? Stainless steel casting will remain a vital manufacturing method, particularly as technological advancements continue to improve the casting process. The future looks promising, with innovations such as 3D printing and automation playing a key role in enhancing efficiency and precision.
Ready for the good part? By staying informed about the latest trends and technologies, you can ensure that your manufacturing processes remain competitive and efficient. Stainless steel casting offers unmatched versatility, durability, and strength, making it a top choice for industries worldwide.
Table 14: Trends Shaping the Future of Stainless Steel Casting
Trend | Description |
---|---|
3D Printing | Allows for more complex designs and faster production |
Automation | Increases precision and reduces labor costs |
Eco-friendly Practices | Reduces environmental impact through recycling and energy efficiency |
FAQ Section
Q1: What is stainless steel casting?
Stainless steel casting is the process of pouring molten stainless steel into a mold to create a part with specific shapes and properties, ideal for industries that require durable and corrosion-resistant materials.
Q2: How does the stainless steel casting process work?
The stainless steel casting process involves melting the material, pouring it into a mold, and allowing it to cool. The part is then removed, cleaned, and inspected for quality.
Q3: What are the main benefits of stainless steel casting?
The main benefits include strength, corrosion resistance, high-temperature performance, and the ability to produce complex shapes and designs that are often difficult to achieve with other methods.
Q4: What are some common defects in stainless steel castings?
Common defects include porosity, shrinkage, and cracks, often caused by improper cooling or mold design. These defects can be mitigated with careful quality control during the casting process.
Q5: How can I ensure high-quality stainless steel castings?
High-quality castings can be ensured by selecting a reliable supplier, using quality materials, optimizing the mold and cooling process, and performing rigorous quality control tests.