Choosing the right steel for your project is crucial, especially when comparing options like 4130 and 4140 steel. Both of these steels are alloy steels with unique properties and applications that cater to different industries. In this article, we will explore the key differences between 4130 and 4140, their uses, and how to decide which is best for your needs. So, if you’ve been wondering whether 4130 or 4140 is right for you, let’s dive in and explore all the details. Ready for the good part?
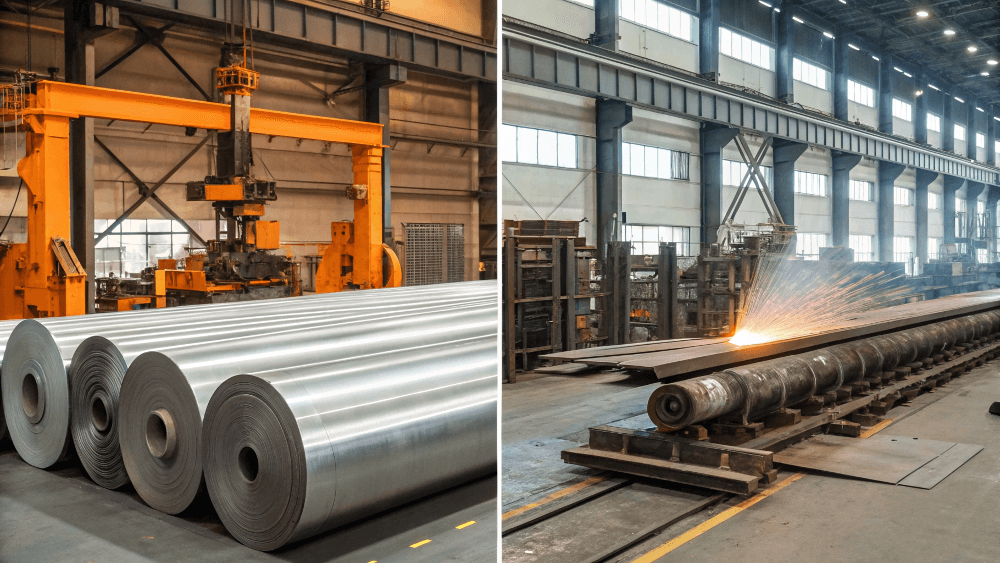
1. Introduction: Understanding the Key Differences Between 4130 and 4140 Steel
When choosing between 4130 and 4140 steel, it’s essential to understand the differences in composition, mechanical properties, and their applications in various industries. These two steels, although similar, have different characteristics that make them better suited for specific purposes. But here’s the kicker: Even though they both fall under the category of alloy steels, their chemical compositions are different, leading to varying mechanical properties.
4130 steel is a low-alloy steel containing chromium and molybdenum, which enhances its toughness and strength. On the other hand, 4140 steel contains more carbon and is typically alloyed with chromium, molybdenum, and sometimes vanadium. This makes 4140 steel a more robust material with higher tensile strength, which is ideal for heavy-duty applications.
In this section, we’ll take a closer look at what makes these two types of steel distinct. What’s the real story? Let’s dive into the specifics and compare 4130 and 4140 steel.
Property | 4130 Steel | 4140 Steel |
---|---|---|
Chemical Composition | Low carbon (0.28–0.33%), Chromium, Molybdenum | Higher carbon (0.38–0.43%), Chromium, Molybdenum, Vanadium |
Tensile Strength | 95,000 psi | 150,000 psi |
Common Applications | Aerospace, automotive, general manufacturing | Automotive, heavy machinery, construction |
2. What is 4130 Steel?
4130 steel, often referred to as chromoly steel, is a low-alloy steel known for its excellent balance of strength and toughness. Ready for the good part? The composition of 4130 includes approximately 0.30% carbon, with small amounts of chromium and molybdenum. These alloying elements enhance the steel’s resistance to wear, improve its hardenability, and increase its ability to withstand high temperatures.
One of the main advantages of 4130 steel is its versatility. It is widely used in industries such as aerospace, automotive, and manufacturing. The steel’s low carbon content provides high weldability, making it easy to shape, fabricate, and work with. Here’s where it gets interesting: 4130’s ability to resist corrosion and its cost-effectiveness make it an attractive option for many applications, particularly when weight savings and strength are critical.
In the aerospace industry, 4130 is commonly used in the production of aircraft parts such as frames, landing gear, and wing struts. Its high strength-to-weight ratio is beneficial for reducing weight while maintaining durability. Similarly, in the automotive industry, 4130 is used for making roll cages, structural components, and high-performance parts.
Feature | 4130 Steel |
---|---|
Carbon Content | 0.28-0.33% |
Molybdenum Content | 0.15-0.25% |
Chromium Content | 0.80-1.10% |
Applications | Aerospace, automotive, manufacturing |
3. What is 4140 Steel?
4140 steel is a medium-carbon alloy steel known for its exceptional toughness, high strength, and fatigue resistance. But here’s the kicker: It’s not just stronger than 4130, it also has greater wear resistance, making it the go-to choice for heavy-duty applications. The steel is typically alloyed with chromium and molybdenum, which improve its hardenability and resistance to heat.
What sets 4140 apart from 4130 is its higher carbon content, which gives it superior strength after heat treatment. This makes 4140 ideal for applications in industries such as heavy machinery, automotive, and construction. What’s the real story? While 4130 is more suitable for lightweight applications, 4140 excels in heavy-duty environments where toughness and wear resistance are paramount.
In the automotive industry, 4140 is used for gears, shafts, and other high-stress components. It is also commonly used in the construction industry for equipment that undergoes constant wear and tear, such as drill bits, impact tools, and machinery parts. The increased carbon content also allows for better heat treatment, improving the material’s hardness and fatigue resistance.
Feature | 4140 Steel |
---|---|
Carbon Content | 0.38-0.43% |
Molybdenum Content | 0.15-0.25% |
Chromium Content | 0.80-1.10% |
Applications | Heavy machinery, automotive, construction |
4. Key Differences Between 4130 and 4140 Steel
To make the right choice between 4130 and 4140 steel, understanding the key differences is crucial. This is where it gets interesting… While both steels have similar alloying elements, 4140 steel has a higher carbon content, making it stronger and more durable than 4130. The differences in their composition lead to noticeable variations in mechanical properties like tensile strength, hardness, and fatigue resistance.
One of the most important differences between 4130 and 4140 steel is the carbon content. 4140 steel has a higher carbon percentage, typically ranging from 0.38% to 0.43%, compared to 4130’s 0.28% to 0.33%. This higher carbon content contributes to better wear resistance, making 4140 ideal for applications subjected to high stress, pressure, and abrasion.
In addition to carbon content, the inclusion of vanadium in some 4140 steels enhances its toughness and stability during high-temperature applications. This makes 4140 a better choice for high-strength applications where fatigue resistance is essential. On the other hand, 4130 is favored in applications where weight is a concern, and moderate strength is sufficient.
Property | 4130 Steel | 4140 Steel |
---|---|---|
Carbon Content | 0.28-0.33% | 0.38-0.43% |
Alloying Elements | Chromium, Molybdenum | Chromium, Molybdenum, Vanadium |
Strength (Tensile) | 95,000 psi | 150,000 psi |
Hardness (Rockwell C) | 28-32 | 30-35 |
5. How 4130 and 4140 Steel Perform in Various Industries
Both 4130 and 4140 steel are used across a wide range of industries, each steel offering specific advantages based on the application. But here’s the kicker: Understanding where and why each steel is used can help you make an informed decision based on your project’s needs.
In the aerospace industry, 4130 steel’s lightweight nature and strong properties make it the material of choice for producing parts like wing struts and other structural components. The low carbon content and ability to withstand high temperatures without losing strength are key factors that make 4130 ideal for this application.
4140 steel, on the other hand, is widely used in automotive manufacturing for its higher strength and toughness. It is used in the production of high-stress components like gears, shafts, and axles. The superior fatigue resistance of 4140 ensures that automotive parts can withstand the harsh conditions they are subjected to, including high temperatures and pressure.
In heavy machinery and construction, 4140 is commonly used in applications that require high strength and resistance to impact. This includes equipment like drill bits, hammers, and construction machinery parts. 4130 is not typically used for these types of applications due to its lower tensile strength and wear resistance.
Industry | 4130 Steel Applications | 4140 Steel Applications |
---|---|---|
Aerospace | Aircraft parts, wing struts | – |
Automotive | Roll cages, structural components | Gears, shafts, axles |
Heavy Machinery | – | Drill bits, hammers, construction tools |
6. Choosing the Right Steel for Your Project
Choosing between 4130 and 4140 steel depends largely on the requirements of your project. What’s the real story? Here’s how you can make an informed choice.
If your project requires a steel that is lightweight yet strong enough for general manufacturing applications, 4130 may be the better choice. Its balance of strength and toughness makes it ideal for components that don’t face extreme stress or wear.
However, if you need a steel that can handle heavy-duty applications with high stress, abrasion, and fatigue, 4140 should be your go-to. The higher carbon content and enhanced properties of 4140 make it ideal for parts that require durability and wear resistance, such as automotive components or heavy machinery parts.
Consideration | 4130 Steel | 4140 Steel |
---|---|---|
Strength | Moderate | High |
Toughness | Moderate | High |
Applications | Aerospace, automotive | Automotive, heavy machinery |
Cost | More affordable | More expensive |
7. Heat Treatment and Its Effects on 4130 and 4140 Steel
Heat treatment plays a crucial role in enhancing the mechanical properties of both 4130 and 4140 steel. What’s the real story? Heat treatment can significantly improve the hardness, strength, and fatigue resistance of these steels, making them suitable for demanding applications. However, the heat treatment process and its effectiveness vary depending on the carbon content and alloying elements in the steel.
For 4130 steel, heat treatment is often used to increase its hardness and improve its tensile strength. Common methods like annealing, normalizing, and quenching are applied to achieve the desired properties. When heat-treated, 4130 becomes stronger and more resistant to impact and wear. However, because of its relatively low carbon content, it does not achieve the same high hardness levels as 4140 steel.
4140 steel, on the other hand, responds much more effectively to heat treatment due to its higher carbon content. The additional alloying elements like chromium and molybdenum allow for more thorough hardening during heat treatment. Here’s where it gets interesting: After heat treatment, 4140 exhibits superior wear resistance and toughness, which is essential for heavy-duty applications like manufacturing gears and shafts.
Heat Treatment Process | 4130 Steel | 4140 Steel |
---|---|---|
Normalizing | Increases toughness | Increases strength |
Quenching | Moderate hardness | High hardness and strength |
Annealing | Improves workability | Improves toughness |
8. Corrosion Resistance of 4130 and 4140 Steel
Corrosion resistance is another important consideration when choosing between 4130 and 4140 steel. But here’s the kicker: Both steels have good resistance to corrosion in certain environments, but they perform differently in harsher conditions.
4130 steel, with its lower carbon content, generally has good resistance to corrosion, particularly in mild to moderate environments. However, it’s not as corrosion-resistant as 4140 steel in extreme conditions. In applications where the steel is exposed to high humidity, chemicals, or marine environments, additional surface treatments such as galvanizing or coating may be necessary to protect 4130 steel from rust and corrosion.
4140 steel, due to its higher carbon content and alloying elements like chromium, offers better resistance to corrosion in harsh environments. Chromium, a key alloying element, enhances the steel’s ability to resist rust and oxidation. This is where it gets interesting… When exposed to high temperatures and aggressive conditions, 4140 steel performs much better, especially in industries like oil and gas or construction, where steel components are regularly exposed to corrosive substances.
Steel Type | Corrosion Resistance | Common Applications |
---|---|---|
4130 Steel | Moderate | Aerospace, automotive |
4140 Steel | High | Heavy machinery, construction |
9. Machining 4130 and 4140 Steel
Machining 4130 and 4140 steel requires a specific set of techniques to achieve the desired finish and dimensions. Ready for the good part? While both types of steel are machinable, 4140 steel is generally more challenging to machine due to its higher carbon content and toughness.
When machining 4130 steel, it’s relatively easy to achieve a clean cut and smooth surface finish. Its low carbon content allows it to be machined with standard tools, making it an excellent choice for applications that require precision machining. It is often used for creating intricate parts with fine tolerances, such as aerospace components and automotive parts.
On the other hand, 4140 steel, due to its higher strength and carbon content, can be more difficult to machine. It often requires specialized tooling, such as carbide inserts, to handle the toughness of the material. Here’s where it gets interesting: Despite being harder to machine, the superior toughness and wear resistance of 4140 steel make it ideal for components that will experience heavy wear, such as gears and shafts.
Steel Type | Machinability | Recommended Tools |
---|---|---|
4130 Steel | Easy to machine | Standard tooling |
4140 Steel | Harder to machine | Carbide inserts, high-speed steel tools |
10. Cost Comparison: 4130 vs 4140 Steel
Cost is an essential factor to consider when selecting materials for a project. What’s the real story? In terms of raw material costs, 4130 steel is generally more affordable than 4140 due to its lower carbon content and simpler alloying elements. However, when considering the long-term benefits of using 4140 for more demanding applications, the higher upfront cost can be justified by its superior strength, wear resistance, and durability.
In applications where moderate strength is required and cost-efficiency is a priority, 4130 steel offers a great balance of performance and price. It is commonly used in general manufacturing and automotive applications where high strength is not the primary concern.
4140 steel, on the other hand, is more expensive but offers better performance for heavy-duty applications that require high strength and toughness. It is commonly used in industries like automotive manufacturing, heavy machinery, and aerospace, where the cost is outweighed by the material’s durability and ability to withstand extreme conditions.
Steel Type | Material Cost | Performance vs Cost |
---|---|---|
4130 Steel | Lower | Great balance for general manufacturing |
4140 Steel | Higher | Superior strength, ideal for heavy-duty applications |
11. Welding 4130 and 4140 Steel
Welding 4130 and 4140 steel requires different approaches due to their varying carbon content and alloying elements. But here’s the kicker: 4130 steel is relatively easy to weld, while 4140 steel requires more precise techniques to prevent cracking and ensure strong welds.
For welding 4130 steel, it’s important to preheat the material to reduce the risk of cracking, especially when working with thicker sections. Standard welding processes like TIG (Tungsten Inert Gas) or MIG (Metal Inert Gas) welding are typically used for 4130 steel. Here’s where it gets interesting: 4130 steel’s low carbon content makes it less prone to heat-affected zone (HAZ) cracking during welding, making it easier to work with for general welding applications.
4140 steel, with its higher carbon content, requires more care when welding. Preheating and post-weld heat treatment are often necessary to reduce the risk of cracking and distortion. Special attention should be paid to the cooling rate to avoid hardness issues in the welded area. The higher strength of 4140 steel after welding makes it suitable for high-stress applications, where weld quality is critical for structural integrity.
Steel Type | Welding Difficulty | Recommended Welding Process |
---|---|---|
4130 Steel | Easy | TIG, MIG, Preheating for thicker sections |
4140 Steel | Difficult | Preheat, Post-weld heat treatment, TIG, MIG |
12. 4130 vs 4140 Steel: Strength and Toughness
When it comes to choosing between 4130 and 4140 steel, one of the most significant factors is the material’s strength and toughness. What’s the real story? 4140 steel is superior in terms of strength and toughness, making it ideal for heavy-duty applications where durability is paramount.
4130 steel, while strong, is not as tough as 4140 steel and is better suited for applications that require moderate strength and a lighter material. It performs well in industries like aerospace and automotive, where strength-to-weight ratio is more important than sheer toughness.
4140 steel, on the other hand, is commonly used in applications where toughness is essential, such as construction equipment, automotive components, and heavy machinery. Ready for the good part? Its ability to withstand impact and high-stress conditions makes it the material of choice for parts that endure continuous wear and tear.
Steel Type | Tensile Strength | Toughness (Charpy Impact) |
---|---|---|
4130 Steel | 95,000 psi | Moderate |
4140 Steel | 150,000 psi | High |
13. Fatigue Resistance of 4130 and 4140 Steel
Fatigue resistance is a critical factor in determining the longevity of steel components under cyclic loading conditions. Here’s where it gets interesting: 4140 steel outperforms 4130 steel when it comes to fatigue resistance, making it a better choice for high-stress applications like gears and shafts.
4130 steel has good fatigue resistance in moderate applications but can fail under heavy, cyclic loads. In contrast, 4140 steel’s higher strength and hardness, combined with its superior toughness, make it more resistant to fatigue. This is why 4140 steel is preferred in industries that require components to withstand repeated loading and unloading cycles without failure.
Steel Type | Fatigue Strength | Application |
---|---|---|
4130 Steel | Moderate | Aerospace, automotive |
4140 Steel | High | Heavy machinery, automotive |
14. Environmental Considerations and Sustainability of 4130 and 4140 Steel
Both 4130 and 4140 steel have environmental considerations related to their production and use. But here’s the kicker: When it comes to sustainability, choosing the right steel can help reduce environmental impact, especially in industries like manufacturing and construction.
4130 steel, with its lower carbon content, is generally easier to recycle and has a smaller environmental footprint during production. It’s used in applications where weight and strength are critical, and its production process is less energy-intensive compared to 4140 steel.
4140 steel, while stronger and tougher, requires more energy to produce due to its higher carbon content and alloying elements. However, the added strength and durability of 4140 steel can reduce the need for frequent replacements, making it a more sustainable option in the long run for heavy-duty applications.
Steel Type | Environmental Impact | Sustainability Factor |
---|---|---|
4130 Steel | Lower | Easier to recycle |
4140 Steel | Higher | Longer-lasting, reducing replacement needs |
15. Conclusion: Which Steel is Right for Your Needs?
In conclusion, both 4130 and 4140 steel have their strengths and weaknesses, and the right choice depends on your project’s specific requirements. What’s the real story? If you need a steel that offers a great balance of strength, toughness, and cost-effectiveness for general manufacturing, 4130 is an excellent option. However, if your project demands higher strength, durability, and resistance to wear, 4140 is the way to go.
When deciding between the two, consider factors such as the application, strength requirements, and environmental conditions. Ultimately, the choice between 4130 and 4140 steel comes down to the balance between performance, cost, and application needs.
FAQ Section
Q1: What is the main difference between 4130 and 4140 steel?
4130 steel has a lower carbon content and is often used in aerospace and automotive applications where strength-to-weight ratio is crucial. 4140 steel has a higher carbon content and is stronger, making it suitable for heavy-duty applications like gears and machinery parts.
Q2: How does heat treatment affect 4130 and 4140 steel?
Heat treatment increases the hardness and strength of both 4130 and 4140 steel. 4140 steel, with its higher carbon content, responds better to heat treatment, offering increased hardness and wear resistance compared to 4130.
Q3: Which steel is better for automotive parts?
4140 steel is generally preferred for automotive parts because of its higher strength and durability. It is commonly used for making gears, shafts, and other high-stress components.
Q4: Can 4130 and 4140 be welded easily?
Both 4130 and 4140 can be welded, but care must be taken during the process to prevent cracking. Pre-heating and post-weld heat treatment are recommended, especially for thicker sections.
Q5: Which steel is more cost-effective, 4130 or 4140 steel?
4130 steel is typically more cost-effective than 4140 due to its lower carbon content and simpler alloying elements. However, for applications requiring higher strength and durability, 4140 may offer better long-term value.