Titanium investment casting is a crucial process for industries requiring high-performance, precision components. However, the casting process can lead to various defects that compromise the quality and functionality of titanium parts. In this article, we will explore the top 5 defects that can occur during titanium investment casting, understand the causes behind them, and discuss practical methods for prevention. Ready to dive into the details? Let’s get started!
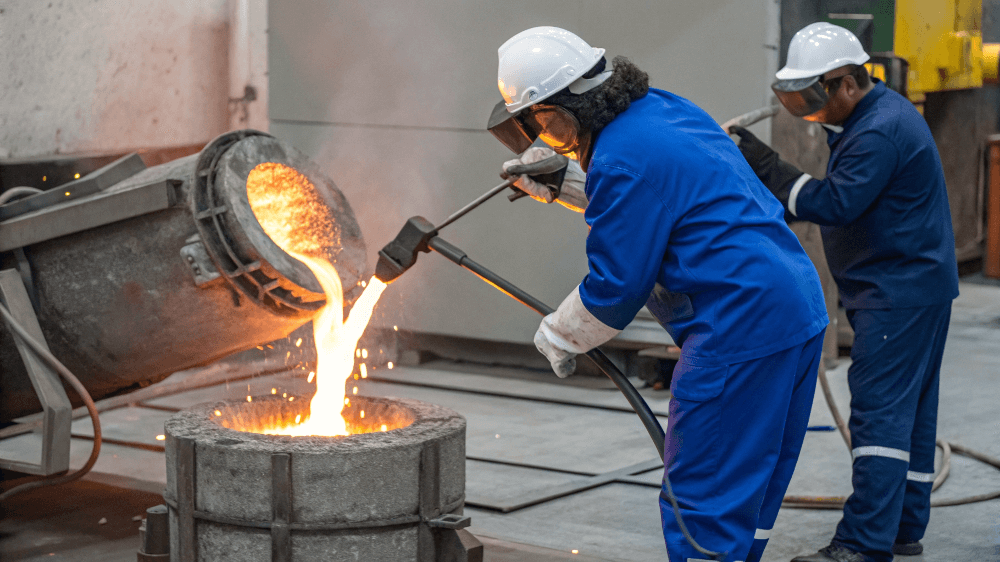
1. Introduction to Titanium Investment Casting Defects
Investment casting, also known as lost wax casting, is a widely used manufacturing process in industries such as aerospace, automotive, and medical devices. Titanium, due to its excellent strength-to-weight ratio, corrosion resistance, and biocompatibility, is often the material of choice. However, despite its many advantages, titanium investment casting can present a variety of challenges.
What’s the real issue here? Defects in the casting process can lead to major operational and safety concerns, not to mention significant financial losses. The most common defects include porosity, cracks, surface finish issues, dimensional inaccuracies, and incomplete filling. These defects can compromise the performance of the final product, making defect-free casting a high priority for manufacturers.
But here’s the kicker: understanding the causes of these defects and taking preventive measures can drastically improve the quality of the castings, saving time and resources. In this section, we’ll look at some of the most frequent defects in titanium investment casting, and why they occur.
Defect Type | Impact on Product | Possible Cause |
---|---|---|
Porosity | Reduced strength and integrity | Poor gating design, air entrapment |
Cracks | Structural failure | Excessive cooling rates, improper stress relief |
Surface finish | Aesthetic and functional issues | Contamination during casting, improper mold preparation |
Dimensional inaccuracies | Misalignment, poor fit | Mold warping, improper tooling |
Incomplete filling | Weak spots, incomplete parts | Low pouring temperature, incorrect gating |
2. Types of Titanium Investment Casting Defects
The defects in titanium investment casting can be broadly categorized into several types, each with its own set of challenges and solutions. Here are the top five:
Porosity in Titanium Castings: Porosity refers to the formation of tiny holes or voids in the cast material, which can significantly reduce the strength of the final product. This defect is often caused by trapped air or gas during the casting process. It can also be the result of improper gating systems, poor mold material, or inadequate pouring temperatures.
Cracks and Fractures: Cracking is one of the most detrimental defects in investment casting. Cracks can occur during the cooling process or as a result of improper stress relief techniques. As the titanium cools, it can contract unevenly, causing fractures if not managed properly.
Surface Finish Issues: The surface finish of titanium castings is crucial for both functional and aesthetic purposes. Poor surface finishes can be caused by contamination in the mold or incorrect casting temperatures. The investment material used for the mold plays a significant role in achieving a smooth surface.
Dimensional Inaccuracies: Dimensional control is critical in precision casting. Warping during the cooling phase or improper mold preparation can lead to deviations from the desired dimensions, making the cast part unusable or requiring costly rework.
Incomplete Filling: Incomplete filling occurs when the molten titanium fails to completely fill the mold cavity. This leads to parts that are structurally weak or unfinished. Incomplete filling can result from improper gating, low pouring temperatures, or incorrect metal flow paths.
What’s the real story? These defects not only affect the strength and functionality of titanium castings but also lead to wasted materials, extended production timelines, and increased costs. By understanding the root causes, manufacturers can take corrective actions to improve the process.
Defect | Description | Common Causes |
---|---|---|
Porosity | Voids within the cast material | Air/gas entrapment, improper gating |
Cracks | Fractures in the titanium part | Cooling rates, stress relief issues |
Surface Finish | Rough or uneven surface quality | Mold contamination, improper mold prep |
Dimensional Issues | Inaccurate product dimensions | Mold warping, poor tooling |
Incomplete Filling | Gaps or voids in the casting | Low pouring temperature, wrong gating |
3. Causes of Titanium Investment Casting Defects
Understanding the causes of defects in titanium investment casting is essential for preventing them. Let’s break it down into manageable parts.
Material-Related Causes: The quality of the titanium alloy used plays a critical role in the casting outcome. Impurities in the metal can lead to poor casting quality, while the incorrect composition of the alloy can cause issues like porosity or cracking. Selecting high-quality titanium and ensuring it’s properly melted and alloyed is crucial for successful casting.
Environmental Factors: Temperature and humidity can have a significant impact on the casting process. Titanium is highly sensitive to its environment, and small fluctuations in temperature or moisture levels can affect the final product. For example, excess moisture in the mold material can lead to the formation of gas bubbles, resulting in porosity.
Equipment and Tooling Limitations: The performance of the equipment used in the casting process directly affects the quality of the titanium castings. Poorly maintained or outdated equipment can lead to inconsistent pouring temperatures, inadequate mold preparation, and ultimately defects in the final product. Tooling such as molds, sprues, and risers also play a key role in ensuring the titanium is properly formed.
Human Error: While automation and advanced technology have reduced human error in many industries, it still plays a significant role in investment casting. Factors such as improper mold preparation, incorrect mold assembly, or inadequate post-processing techniques can result in defects.
Inadequate Post-Processing: After casting, titanium parts often undergo heat treatment, polishing, and other finishing processes. Improper post-processing can exacerbate issues like porosity or surface roughness, especially if the casting is not sufficiently stress-relieved or cleaned.
Ready for the good part? By addressing these factors, manufacturers can improve their casting processes and reduce the occurrence of defects.
Cause | Impact on Castings | Examples of Mitigation |
---|---|---|
Material Quality | Impurities, poor alloying | Use high-quality titanium, refine alloying |
Environmental Factors | Inconsistent casting conditions | Control temperature and humidity levels |
Equipment/Tooling | Poor performance of molds, improper temperatures | Regular maintenance, update equipment |
Human Error | Improper procedures, oversight | Enhanced training and automation |
Post-Processing | Surface imperfections, stress issues | Proper heat treatment, thorough cleaning |
4. Impact of Defects on Titanium Investment Castings
What happens when defects occur in titanium investment casting? The consequences are far-reaching and can affect the functionality, safety, and economics of manufacturing.
Functional Consequences: The primary concern with defects in titanium castings is their impact on the final product’s performance. Porosity can weaken the material, making it susceptible to failure under stress. Cracks and fractures can cause catastrophic failure, especially in critical applications like aerospace or medical devices. Dimensional inaccuracies can affect the fit and function of parts, rendering them unusable or causing mechanical failure.
Safety Risks: Defective titanium parts pose significant safety risks, particularly in industries like aerospace, automotive, and healthcare. For example, in aerospace, a small crack or weak point in a titanium component can lead to catastrophic structural failure. In medical devices, compromised titanium implants can result in patient harm.
Economic Implications: The financial impact of defects in titanium investment casting is substantial. Reworking or re-casting defective parts can add significant costs to the manufacturing process. The wasted materials, extended production timelines, and potential delays in product delivery can negatively impact a company’s bottom line.
This is where it gets interesting… addressing defects proactively can save companies time, money, and resources, leading to more reliable products and a stronger reputation in the market.
Impact Area | Consequence | Example |
---|---|---|
Functionality | Weakened material, failure | Aerospace, medical applications |
Safety | Structural or patient harm | Aircraft parts, medical implants |
Economics | Increased costs, delays | Rework, extended lead times |
5. Detecting Titanium Investment Casting Defects
Detecting defects early in the casting process can save manufacturers from costly rework and delays. There are several techniques available to identify defects in titanium investment castings.
Visual Inspection: This is the most straightforward method of detecting defects. A trained eye can spot surface flaws, cracks, or incomplete fills by simply examining the cast parts. However, this method has its limitations, particularly with internal defects like porosity or cracks that are not visible to the naked eye.
Non-Destructive Testing (NDT): NDT methods are crucial for detecting internal defects without damaging the part. Techniques such as X-ray inspection, ultrasonic testing, and dye penetrant testing allow manufacturers to identify issues like porosity or cracks. These methods are highly effective but require specialized equipment and skilled technicians.
Advanced Scanning Technologies: Emerging technologies, such as 3D scanning and laser-based systems, are increasingly being used to detect defects in titanium castings. These methods can identify dimensional inaccuracies, surface finish issues, and even internal flaws with high precision. The data gathered can also be used for real-time quality control during the casting process.
So, what’s the takeaway here? Detecting defects early in the process is key to minimizing the impact of casting flaws and ensuring high-quality output.
Detection Method | Defects Detected | Advantages |
---|---|---|
Visual Inspection | Surface flaws, cracks | Quick, cost-effective |
Ultrasonic Testing | Internal cracks, voids | No damage to part |
X-ray Inspection | Porosity, structural flaws | High precision, non-invasive |
3D Scanning | Dimensional issues | Real-time quality control |
6. Preventing Porosity in Titanium Investment Castings
Porosity is one of the most common defects in titanium investment casting. It refers to the formation of small holes or voids in the cast material, which can weaken the final part. Preventing porosity involves addressing several key factors during the casting process.
Proper Gating and Riser Design: The gating system directs the molten titanium into the mold, while the risers allow air to escape as the metal flows. An inefficient gating system can trap air in the mold, leading to porosity. A well-designed system ensures that the molten metal flows smoothly and consistently, reducing the risk of air entrapment.
Control of Pouring Temperature and Speed: If the pouring temperature is too low, the titanium may solidify too quickly, trapping gas bubbles. Conversely, if the temperature is too high, the metal can become too fluid, increasing the chance of air entrapment. Controlling the pouring speed is equally important; too fast, and air may get trapped, too slow, and you risk uneven filling.
Use of High-Quality Raw Materials: Contaminants in the raw titanium material can introduce impurities that lead to porosity. Using high-quality, properly prepared materials is crucial for ensuring a successful cast.
Now here’s the deal: by optimizing these factors, manufacturers can significantly reduce the occurrence of porosity and produce stronger, more reliable parts.
Prevention Method | Key Benefits | Implementation Examples |
---|---|---|
Gating and riser design | Smooth molten flow, reduced air entrapment | Proper mold configuration |
Control of pouring temperature | Consistent fill, reduced risk of porosity | Use of temperature-controlled equipment |
Use of high-quality materials | Clean, pure titanium | Source materials from trusted suppliers |
7. Preventing Cracks and Fractures in Titanium Castings
Cracks and fractures are critical defects in titanium investment casting, especially in applications where structural integrity is paramount. These issues can arise during the cooling process or due to improper heat treatment. So, how can manufacturers prevent cracks from forming?
Techniques for Stress Relief During Casting: One of the primary causes of cracking in titanium castings is residual stress. This stress can build up during the cooling phase, causing parts to crack. To mitigate this, manufacturers often use stress relief techniques, such as slow cooling or controlled cooling chambers. Stress relief treatments help to reduce internal stresses, ensuring a more stable casting.
Preheating and Post-Casting Heat Treatment: Preheating the mold or the titanium material before casting can reduce thermal shock, which can lead to cracks. Similarly, post-casting heat treatment helps to relieve any residual stresses that remain in the part after cooling. Heat treatments, like annealing, also improve the mechanical properties of the castings, making them less prone to cracking.
Control of Cooling Rates: Rapid cooling can cause significant stress, leading to cracking. By controlling the cooling rates through slow and consistent cooling, manufacturers can reduce the risk of cracks. Implementing controlled cooling methods ensures that the titanium solidifies in a uniform manner, reducing the chances of thermal stress-related fractures.
Ready for the good part? By implementing these strategies, manufacturers can significantly reduce the likelihood of cracks and fractures in titanium castings, leading to more reliable and durable parts.
Prevention Method | Key Benefits | Examples of Application |
---|---|---|
Stress relief techniques | Reduces internal stresses, prevents cracks | Controlled cooling chambers |
Preheating and post-casting heat treatment | Minimizes thermal shock, improves properties | Annealing, furnace cooling |
Controlled cooling rates | Reduces thermal stresses, prevents fractures | Slow cooling techniques |
8. Ensuring Accurate Dimensional Control in Titanium Castings
Dimensional accuracy is critical in titanium investment casting, especially for parts that must fit precisely in assemblies. Any deviations from the specified dimensions can lead to improper fits, misalignments, and costly rework. Let’s look at how manufacturers can ensure better dimensional control.
Implementing Tighter Tolerances During Mold Preparation: One of the first steps in ensuring accurate dimensions is to prepare the mold with tight tolerances. The mold must be designed with precise measurements, ensuring that the final casting will meet the desired specifications. Using high-quality mold materials and advanced manufacturing techniques ensures the mold maintains its shape throughout the casting process.
Calibration and Maintenance of Equipment: Accurate dimensions also depend on the equipment used in the casting process. Molds, injection systems, and temperature control equipment all need to be regularly calibrated and maintained. By keeping equipment in top condition, manufacturers can prevent dimensional inconsistencies and ensure that each casting is made to the correct specifications.
Impact of Mold Material Selection on Casting Precision: The material selected for the mold can greatly affect the dimensional accuracy of the titanium castings. For example, molds made from high-performance ceramics or metals can withstand the high temperatures of the molten titanium and provide better precision during the solidification process. Choosing the right mold material is essential for achieving high-precision castings.
What’s the real story? Accurate dimensional control is essential for meeting tight industry standards and ensuring the performance of the final product. Manufacturers who prioritize dimensional accuracy in their casting processes will see fewer defects and a higher quality output.
Method | Benefits | Application Examples |
---|---|---|
Tight tolerances during mold preparation | Ensures accurate casting dimensions | High-precision mold design |
Calibration and maintenance of equipment | Prevents dimensional inconsistencies | Regular checks on molds, temperature controls |
Selection of appropriate mold materials | Enhances dimensional precision | Use of high-performance ceramics |
9. Achieving a Smooth Surface Finish
The surface finish of titanium castings is an essential aspect of both their functionality and aesthetic quality. Castings with rough or uneven surfaces are often subject to increased wear and reduced performance. How can manufacturers improve surface finish?
Polishing and Cleaning Techniques Post-Casting: After the casting process, the surface of the titanium part is often rough and may contain residues from the mold material. Polishing techniques, such as abrasive blasting or using polishing wheels, can smooth out the surface, making it more aesthetically pleasing and reducing surface roughness. Cleaning the parts thoroughly is essential to remove any contaminants that could affect the final finish.
Role of Investment Materials in Surface Quality: The investment material used for the mold significantly affects the surface quality of the castings. If the mold material is too coarse, it will transfer texture to the casting, leading to a rough surface. Using high-quality investment materials, such as fine silica or other specialized coatings, can help achieve a smoother, more uniform surface.
Heat Treatment Methods for Improved Finish: Heat treatment plays an important role in improving the surface finish of titanium castings. Certain heat treatments can help reduce surface imperfections caused by casting. Techniques like solution treating and aging not only enhance the surface but also improve the mechanical properties of the material, ensuring the casting is both durable and smooth.
This is where it gets interesting… A high-quality surface finish doesn’t just improve the appearance of the titanium casting but also enhances its overall performance by reducing friction and wear.
Method | Benefits | Examples of Application |
---|---|---|
Polishing and cleaning techniques | Smooth surface, reduced imperfections | Abrasive blasting, polishing wheels |
Investment material selection | Improved surface quality | Fine silica, advanced coatings |
Heat treatment methods | Enhanced finish, improved properties | Solution treating, aging |
10. Best Practices for Quality Control in Titanium Investment Casting
Quality control is a vital part of the titanium investment casting process. Ensuring that each part meets the required standards can save manufacturers time and money. Let’s explore the best practices for maintaining high-quality casting.
The Role of Standardization in Casting Processes: One of the key strategies in ensuring consistent quality is standardization. By establishing clear and standardized procedures for every step of the casting process, manufacturers can minimize the risk of defects and maintain high levels of consistency. Standardization also helps in training workers and ensuring that each part meets the same high-quality standards.
Routine Inspections and Audits: Regular inspections and audits are crucial for detecting defects early in the process. Using both manual inspections and automated systems can help identify issues such as surface defects or dimensional inaccuracies. Routine checks ensure that any deviations from the desired standards are caught before the casting moves to the next stage.
Collaboration with Suppliers for Defect Prevention: A successful casting process relies heavily on the quality of the raw materials. Collaborating with suppliers to ensure that high-quality titanium and investment materials are used is essential for preventing defects. Regular communication with suppliers and setting clear quality expectations can help avoid material-related issues.
What’s the catch here? By implementing these quality control measures, manufacturers can reduce the number of defective parts and improve the overall efficiency of their casting operations.
Best Practice | Benefit | Example of Application |
---|---|---|
Standardization of processes | Consistent quality, reduced defects | Standard operating procedures |
Routine inspections and audits | Early defect detection | Regular manual and automated checks |
Supplier collaboration | Ensures quality of materials | Ongoing communication with suppliers |
11. Troubleshooting Common Defects in Titanium Investment Casting
Troubleshooting defects in titanium investment casting is an essential skill for manufacturers. When defects arise, it’s important to systematically analyze the issue and implement solutions. Let’s break down how to troubleshoot the most common defects.
Step-by-Step Troubleshooting for Porosity: If porosity is detected, start by evaluating the gating system to ensure it’s designed properly for smooth metal flow. Check the pouring temperature and speed to ensure they are within the optimal range. If material impurities are suspected, inspect the raw titanium for contaminants.
Addressing Cracks and Fractures: When cracks occur, the first step is to check the cooling rate. If it’s too fast, the titanium may cool unevenly, leading to stress cracks. Implementing slower cooling rates and checking for adequate heat treatment can prevent future cracking.
Dealing with Surface Finish Issues: Rough surface finishes can often be linked to improper mold preparation. If the mold surface is too coarse, it will transfer to the casting. Ensuring the mold is prepared with fine, high-quality materials can mitigate this issue.
But here’s the kicker… addressing defects as soon as they’re detected not only prevents delays but also improves the quality of the final product. Having a systematic troubleshooting approach ensures that problems are resolved quickly and efficiently.
Defect | Troubleshooting Step | Suggested Solution |
---|---|---|
Porosity | Evaluate gating, pouring process | Optimize gating design, adjust pouring temperature |
Cracks | Inspect cooling rate and heat treatment | Slow cooling, proper stress relief |
Surface Finish Issues | Examine mold preparation | Use fine mold materials, refine process |
12. Innovations in Titanium Investment Casting Technology
Technology continues to advance, and these innovations are revolutionizing the titanium investment casting process. Let’s explore the emerging trends and technologies that are shaping the future of this industry.
Emerging Casting Techniques: New casting methods, such as 3D printing and additive manufacturing, are making it easier to produce intricate titanium parts with fewer defects. These technologies allow for more precise control over the casting process, minimizing the risks of porosity, cracking, and dimensional inaccuracies.
Automation in Investment Casting: Automation is transforming the casting industry. Automated systems can control pouring temperatures, monitor mold integrity, and perform inspections, greatly reducing human error. With the integration of artificial intelligence and machine learning, these systems can predict defects before they occur, allowing manufacturers to take proactive measures.
Material Science Advances: Advances in material science are enabling the development of stronger, more heat-resistant titanium alloys that are easier to cast. These new materials help reduce defects like porosity and cracks, providing a higher yield of quality titanium parts.
This is where it gets interesting… by embracing these innovative technologies, manufacturers can significantly reduce the occurrence of defects, while also improving the overall efficiency and precision of the casting process.
Innovation | Impact | Example |
---|---|---|
3D printing | Increased precision, fewer defects | Complex, intricate parts |
Automation | Reduced human error, consistent quality | AI-driven casting systems |
Advances in material science | Stronger alloys, reduced defects | New titanium alloys with better casting properties |
13. Case Studies of Titanium Investment Casting Defects
Real-world examples provide valuable insights into the challenges and solutions in titanium investment casting. Let’s take a look at some case studies that highlight the issues and their resolutions.
Case Study 1: A major aerospace company faced significant issues with porosity in their titanium castings. After thorough analysis, it was found that the pouring temperature was too low, and the gating system was not optimal. By adjusting the pouring temperature and redesigning the gating system, the company reduced porosity by 75%, resulting in a much higher yield of quality parts.
Case Study 2: An automotive manufacturer encountered cracks in titanium castings used for critical engine components. The cause was traced to rapid cooling during the casting process. By implementing controlled cooling rates and post-casting stress relief treatments, the company was able to eliminate cracks and improve part integrity.
Case Study 3: A medical device company struggled with surface finish issues in titanium castings. They switched to higher-quality investment materials and improved mold preparation. As a result, the company achieved smoother surface finishes and reduced the need for post-processing.
These case studies demonstrate that by addressing defects systematically, manufacturers can significantly improve the quality of their titanium investment castings.
Case Study | Issue | Solution | Outcome |
---|---|---|---|
Aerospace | Porosity | Optimized pouring temperature and gating | 75% reduction in porosity |
Automotive | Cracks | Controlled cooling and stress relief | No cracks, improved integrity |
Medical | Surface Finish | Better investment material and mold prep | Smoother finish, reduced post-processing |
14. The Role of Post-Processing in Minimizing Defects
Post-processing plays a key role in eliminating or reducing defects after the casting is complete. From heat treatments to polishing, these processes ensure that titanium castings meet the required specifications.
Post-Casting Heat Treatments: Heat treatments, such as annealing and solution treatment, help relieve residual stresses and improve the mechanical properties of the titanium. These treatments reduce the likelihood of cracking and improve the overall strength of the casting.
Polishing and Surface Finishing: After casting, titanium parts often need to be polished or ground to achieve the desired surface finish. This post-processing step is essential for eliminating rough surfaces, improving aesthetics, and reducing wear and tear on the parts.
Impact of Surface Coatings: Surface coatings, such as anodizing or plasma spraying, can be applied to improve the corrosion resistance and wear resistance of titanium castings. These coatings not only enhance the appearance but also extend the life of the parts, making them suitable for harsh environments.
So, what’s the deal? Proper post-processing can turn a good casting into a great one, ensuring that the final part meets both functional and aesthetic standards.
Post-Processing Step | Purpose | Example of Application |
---|---|---|
Heat treatments | Relieves stresses, improves strength | Annealing, solution treatment |
Polishing and finishing | Improves surface quality | Abrasive blasting, grinding |
Surface coatings | Enhances corrosion resistance | Anodizing, plasma spraying |
15. Conclusion: How to Achieve High-Quality Titanium Investment Castings
To sum up, achieving high-quality titanium investment castings requires careful attention to detail throughout the entire process. From preventing defects like porosity and cracks to ensuring accurate dimensional control and smooth surface finishes, every step plays a critical role in producing reliable and durable titanium parts.
By understanding the common defects and implementing the prevention and detection methods outlined in this article, manufacturers can significantly improve the quality of their titanium castings. Investing in high-quality materials, advanced technologies, and proper post-processing methods is essential for achieving optimal results.
The key takeaway here? Continuous improvement and a systematic approach to quality control are the best ways to ensure the success of titanium investment casting operations. With the right strategies in place, manufacturers can minimize defects and produce parts that meet the highest standards of quality and performance.
Key Takeaway | Action Required | Expected Outcome |
---|---|---|
Prevent defects early | Optimize design and processes | Fewer defects, higher-quality parts |
Invest in technology and training | Embrace new technologies, improve training | Increased precision and efficiency |
Focus on post-processing | Implement proper heat treatments and finishing | Superior final products |
FAQ Section
Q1: What are the most common defects in titanium investment casting?
Titanium investment casting defects commonly include porosity, cracks, fractures, incomplete filling, surface finish issues, and dimensional inaccuracies.
Q2: How do you prevent porosity in titanium investment casting?
Preventing porosity can be achieved by optimizing gating and riser designs, controlling pouring speed and temperature, and using high-quality materials.
Q3: How can cracks be prevented in titanium castings?
Cracks can be prevented by stress relief techniques, controlling cooling rates, and employing proper heat treatment before and after casting.
Q4: What technologies are used to detect titanium investment casting defects?
Non-destructive testing methods such as X-ray inspection, ultrasonic testing, and visual inspection are commonly used to detect defects in titanium castings.
Q5: What impact do titanium investment casting defects have on industries?
Defects can lead to functional failures, safety risks, economic losses, and delays in production, which significantly impact industries relying on titanium castings.