Heat resistant metals are essential in industries that deal with high-temperature environments, ranging from aerospace to automotive applications. These metals are specially designed to maintain their strength, durability, and functionality even when subjected to extreme heat. In this article, we will explore the various types of heat resistant metals, their properties, applications, and how to select the right one for your needs. Let’s dive into the world of heat resistant metals and discover what makes them essential for high-performance industries.
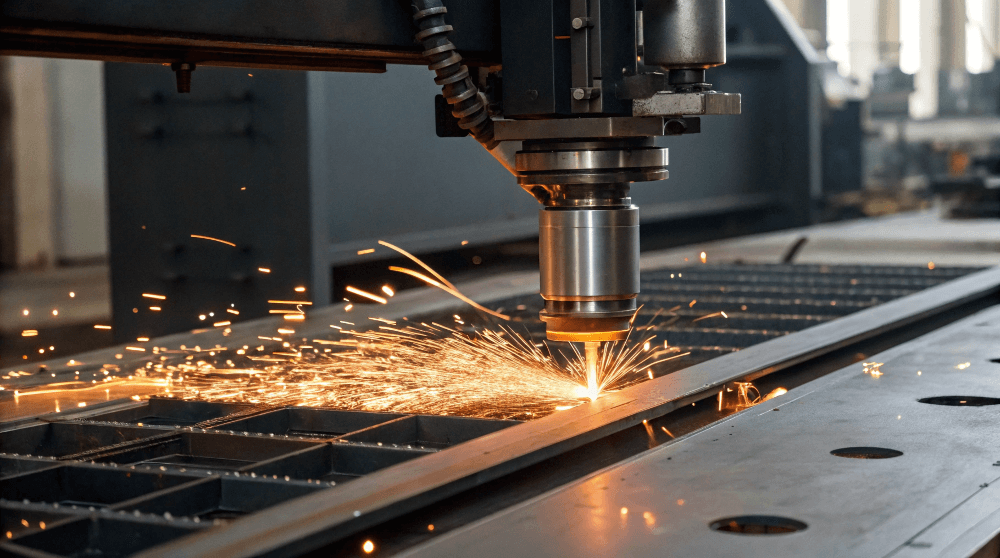
1. Introduction to Heat Resistant Metals
When it comes to high-temperature applications, choosing the right material can make or break the success of a project. Heat resistant metals play a crucial role in industries that demand strength and durability under extreme conditions. These metals are designed to withstand intense heat without losing their structural integrity, making them indispensable for manufacturing processes, machinery, and infrastructure in sectors like aerospace, automotive, and industrial manufacturing.
But here’s the kicker – heat resistant metals come in various forms, each offering unique properties that make them suitable for different high-temperature applications. While some metals can handle extreme heat better than others, selecting the ideal metal for your project involves understanding the specific requirements of the application, such as temperature resistance, corrosion resistance, and overall strength.
The key takeaway here is that high-performance heat resistant metals ensure longevity, reliability, and safety in applications that demand maximum performance. Whether you’re working with engines, turbines, or power plants, understanding how heat resistant metals function and their properties is the first step toward selecting the right material.
Metal Type | Maximum Temperature (°F) | Common Applications | Cost Range (per kg) |
---|---|---|---|
Stainless Steel | 1,200 | Automotive, Food Processing | Low-Medium |
Titanium Alloys | 1,800 | Aerospace, Marine | High |
Nickel Alloys | 2,000+ | Power Generation, Aerospace | High |
2. Key Properties of Heat Resistant Metals
Heat resistant metals are engineered to handle extreme conditions without compromising their mechanical properties. Let’s break down the critical properties that make these metals effective in high-temperature applications.
Ready for the good part? Heat resistant metals are primarily defined by their ability to resist thermal degradation. These metals must maintain their strength, elasticity, and resistance to oxidation under intense heat. This is especially important for components that operate in environments like jet engines or industrial furnaces.
Among the most crucial properties of heat resistant metals are:
- Thermal Stability: Heat resistant metals can withstand high temperatures without undergoing significant changes in their physical properties. This ensures that they remain stable and reliable even under extreme heat exposure.
- Corrosion Resistance: Many high-temperature environments also involve corrosive elements, like acids or gases. Heat resistant metals must resist such chemical reactions to ensure that the material doesn’t degrade prematurely.
- Strength and Toughness: As temperature increases, materials can become brittle and lose their mechanical strength. Heat resistant metals are designed to retain their strength even in high-temperature environments, making them essential for load-bearing components.
What’s the real story? These properties combined ensure that heat resistant metals can function in harsh conditions without deteriorating over time.
Property | Importance | Example Materials |
---|---|---|
Thermal Stability | Prevents degradation at high temps | Stainless Steel, Titanium Alloys |
Corrosion Resistance | Prevents material breakdown in harsh environments | Nickel Alloys, Inconel |
Strength and Toughness | Retains structural integrity under stress | Titanium Alloys, Stainless Steel |
3. Types of Heat Resistant Metals
There are several types of heat resistant metals, each suited for different high-temperature applications. The choice of material depends on various factors such as temperature, environment, and mechanical stress. Let’s take a closer look at the most commonly used heat resistant metals:
- Stainless Steel: Stainless steel is one of the most widely used heat resistant metals. It offers excellent strength, oxidation resistance, and can operate at temperatures up to 1,200°F (649°C) depending on the alloy. Stainless steel is frequently used in industries like food processing, automotive, and chemical plants.
- Titanium Alloys: Titanium is known for its high strength-to-weight ratio and its ability to withstand extreme temperatures. Titanium alloys are commonly used in aerospace applications due to their excellent heat resistance and corrosion resistance.
- Nickel-Based Alloys: Nickel-based alloys are ideal for extreme environments, particularly in the aerospace and power generation industries. These alloys can handle temperatures exceeding 1,800°F (982°C) and are resistant to both high heat and corrosive gases.
But here’s where it gets interesting – these metals can also be combined in various alloys to enhance their properties. For instance, Inconel, a nickel-chromium alloy, is renowned for its ability to withstand high temperatures and aggressive environments, making it essential in turbine engines.
Metal Type | Maximum Temperature (°F) | Common Uses | Key Property |
---|---|---|---|
Stainless Steel | 1,200 | Automotive, Food Processing | Oxidation Resistance |
Titanium Alloys | 1,800 | Aerospace, Marine | Strength-to-Weight Ratio |
Nickel-Based Alloys | 1,800+ | Power Generation, Aerospace | Corrosion Resistance |
4. Factors to Consider When Choosing Heat Resistant Metal
Selecting the right heat resistant metal for your project can be tricky, but considering several factors will help guide your decision. Here’s what you need to keep in mind:
- Temperature Range: The first consideration is the maximum temperature the material will be exposed to. Each metal has a specific temperature threshold, and exceeding that limit can cause irreversible damage.
- Mechanical Properties: Aside from heat resistance, metals must also retain their strength and elasticity under stress. Mechanical properties like tensile strength, yield strength, and toughness are essential to consider when selecting a metal.
- Corrosion Resistance: In high-temperature environments, metals often come into contact with corrosive chemicals, gases, or moisture. Selecting a metal with good corrosion resistance ensures longer lifespan and reliability.
- Cost: Heat resistant metals can be expensive, especially those used in high-performance applications like aerospace. Cost considerations must balance performance needs with budget constraints.
Ready for the good part? Many industries face the challenge of sourcing the most cost-effective heat resistant materials. While some may prioritize performance, others may need to consider budget constraints. Understanding the trade-offs between cost and performance is critical when choosing the right material for a specific application.
Factor | Consideration | Example Materials |
---|---|---|
Temperature Range | Must withstand high heat | Titanium Alloys, Inconel |
Mechanical Properties | Ability to retain strength and elasticity | Nickel Alloys, Stainless Steel |
Corrosion Resistance | Ability to resist chemical reactions | Stainless Steel, Inconel |
Cost | Balance between performance and budget | Stainless Steel (Low), Titanium Alloys (High) |
5. Applications of Heat Resistant Metals
Heat resistant metals are used in a wide range of industries. Here’s a look at some of the most critical applications:
- Aerospace: In the aerospace industry, heat resistant metals are used in engine components, turbine blades, and heat shields. These materials must withstand the intense heat produced during flight while maintaining structural integrity.
- Automotive: The automotive industry uses heat resistant metals for engine parts, exhaust systems, and catalytic converters. These components are exposed to high temperatures during operation, and metals must withstand these conditions without degrading.
- Industrial Manufacturing: High-temperature furnaces, heat exchangers, and other equipment in industrial manufacturing rely on heat resistant metals to operate efficiently. These metals are also used in power generation facilities and steel mills, where temperatures can reach several thousand degrees.
But here’s the kicker – the versatility of heat resistant metals goes beyond these industries. In addition to the above, heat resistant metals are crucial for food processing, oil and gas drilling, and even medical applications like surgical tools and implants.
Industry | Application | Common Materials |
---|---|---|
Aerospace | Engine parts, turbines, heat shields | Titanium Alloys, Inconel |
Automotive | Exhaust systems, catalytic converters | Stainless Steel, Inconel |
Industrial Manufacturing | High-temperature furnaces, heat exchangers | Nickel Alloys, Stainless Steel |
6. The Role of Alloying in Enhancing Heat Resistance
Alloying is a critical process that enhances the heat resistance of metals. By combining different elements with the base metal, manufacturers can improve properties such as strength, oxidation resistance, and overall heat resistance. Let’s break down how alloying works:
- Chromium: Adding chromium to metals such as steel increases oxidation resistance, making them less likely to rust or corrode at high temperatures.
- Molybdenum: Molybdenum enhances the strength of metals at elevated temperatures, particularly in nickel-based alloys.
- Vanadium: Vanadium is added to steel to improve its hardness and resistance to wear at high temperatures.
What’s the real story? Alloying not only improves heat resistance but also increases the overall performance of the metal in demanding applications. These tailored alloys make it possible to use heat resistant metals in a wide range of industrial sectors, each with specific performance requirements.
Alloying Element | Function | Impact on Material |
---|---|---|
Chromium | Increases oxidation resistance | Prevents rust and degradation |
Molybdenum | Increases high-temperature strength | Enhances strength at elevated temperatures |
Vanadium | Increases hardness | Improves resistance to wear at high temperatures |
7. Heat Resistant Metal Manufacturing Techniques
Manufacturing heat resistant metals requires advanced techniques to ensure that the metals maintain their integrity during the production process. Common manufacturing techniques include:
- Casting: In casting, molten metal is poured into molds to form specific shapes. This is a common method for producing complex components made from heat resistant metals.
- Forging: Forging involves shaping metal using compressive forces, typically at high temperatures. This process increases the strength of the metal and ensures that it can withstand high thermal stresses.
- Heat Treatment: Heat resistant metals are often subjected to heat treatment processes such as annealing, hardening, or tempering to improve their properties. This ensures that the metal can withstand high temperatures without losing its mechanical properties.
This is where it gets interesting – selecting the right manufacturing process can greatly affect the performance of heat resistant metals. It’s essential to choose the appropriate method based on the desired material properties and the application at hand.
Manufacturing Method | Application | Key Benefits |
---|---|---|
Casting | Producing complex shapes | Cost-effective, flexible |
Forging | Shaping with compressive forces | Increased strength and toughness |
Heat Treatment | Enhancing heat resistance | Improves durability and strength |
8. Heat Resistance vs. Thermal Conductivity: What’s the Difference?
It’s essential to differentiate between heat resistance and thermal conductivity when selecting heat resistant metals. Let’s take a look at both:
- Heat Resistance: Heat resistance refers to a material’s ability to withstand high temperatures without significant degradation. This is a key property of heat resistant metals, as they are designed to maintain their mechanical strength under extreme heat.
- Thermal Conductivity: Thermal conductivity refers to a material’s ability to transfer heat. While some applications require metals with low thermal conductivity, others benefit from metals with high conductivity to transfer heat efficiently.
But here’s where it gets interesting – balancing these two properties is essential in certain applications. For instance, in heat exchangers, high thermal conductivity is necessary, but in turbine blades, heat resistance takes precedence over thermal conductivity.
Property | Importance | Application |
---|---|---|
Heat Resistance | Prevents degradation at high temps | Jet engines, power plants |
Thermal Conductivity | Transfers heat efficiently | Heat exchangers, cooling systems |
9. Innovations in Heat Resistant Materials
The field of heat resistant materials continues to evolve as technology advances. Let’s explore some of the innovations in this space:
- Nanotechnology: Recent developments in nanotechnology have led to the creation of advanced coatings that enhance the heat resistance of metals. These coatings can prevent oxidation, corrosion, and other forms of degradation at high temperatures.
- Advanced Alloys: Scientists are continually developing new alloy combinations to improve the performance of heat resistant metals. These alloys can withstand higher temperatures and more aggressive environments than traditional materials.
- 3D Printing: Additive manufacturing, or 3D printing, has opened new possibilities for creating complex heat resistant metal components. This technology allows for the precise control of material properties and geometry.
Ready for the good part? Innovations in heat resistant materials are pushing the boundaries of what’s possible, enabling industries to meet the demands of increasingly extreme environments.
Innovation | Description | Example Materials |
---|---|---|
Nanotechnology | Advanced coatings for heat resistance | Nano-coatings for stainless steel |
Advanced Alloys | New combinations for higher temperatures | Titanium alloys, Inconel |
3D Printing | Precision control of material properties | 3D printed titanium, Inconel |
10. Heat Resistant Metals in Extreme Conditions
Heat resistant metals are essential in some of the most extreme environments on Earth. Here’s how these metals are used in conditions that push them to their limits:
- Space: Heat resistant metals are crucial in space exploration, where components must endure extreme temperatures during reentry and while orbiting the Earth.
- Nuclear Power: In nuclear reactors, heat resistant metals must handle temperatures over 1,000°F (537°C) while remaining stable in the presence of radiation.
- Deep-Sea: Submarine and underwater drilling equipment rely on heat resistant metals to withstand both high pressures and high temperatures found in the deep ocean.
What’s the real story? Heat resistant metals are a game-changer in extreme environments, where failure is not an option. Their ability to withstand the harshest conditions ensures safety and reliability in these critical industries.
Extreme Condition | Key Challenges | Material Requirements |
---|---|---|
Space | Extreme temperatures during reentry | Titanium alloys, Inconel |
Nuclear Power | High temperatures and radiation | Stainless steel, Inconel |
Deep-Sea | High pressure and temperature | Nickel alloys, titanium |
11. Challenges and Limitations of Heat Resistant Metals
While heat resistant metals are indispensable, they come with their own set of challenges and limitations:
- High Costs: Many heat resistant metals, especially superalloys like Inconel, come with a high price tag due to the raw materials and manufacturing processes required.
- Brittleness: Some heat resistant metals can become brittle under certain conditions, which may limit their applications in highly stressed environments.
- Availability: Sourcing heat resistant metals, particularly rare alloys, can be difficult, especially for industries with specialized needs.
But here’s the kicker – overcoming these challenges requires careful material selection and understanding the specific needs of the application. It’s crucial to weigh the benefits of heat resistance against the limitations of cost, availability, and mechanical properties.
Challenge | Impact | Potential Solutions |
---|---|---|
High Costs | Expensive raw materials and manufacturing | Use cost-effective alloys like stainless steel |
Brittleness | Material failure under stress | Select tougher alloys like titanium |
Availability | Difficulty sourcing rare alloys | Stockpiling or sourcing from multiple suppliers |
12. How to Maintain and Care for Heat Resistant Metals
Heat resistant metals require regular maintenance to ensure they continue to perform at their best. Proper care can significantly extend the lifespan of these materials and prevent premature degradation. Here’s how to maintain heat resistant metals:
- Cleaning: Regular cleaning prevents the buildup of corrosive substances, which can degrade the metal’s surface. Use non-abrasive cleaning methods to avoid damaging the metal.
- Inspection: Regular inspections can help identify early signs of wear or damage. Pay close attention to signs of oxidation or fatigue, particularly in high-stress areas.
- Storage: Store heat resistant metals in dry, temperature-controlled environments to prevent unnecessary exposure to moisture or extreme temperatures.
What’s the real story? Taking care of heat resistant metals is just as crucial as selecting the right material in the first place. Proper maintenance ensures longevity, performance, and cost-effectiveness.
Maintenance Tip | Action | Benefits |
---|---|---|
Cleaning | Use non-abrasive methods | Prevents corrosion and surface damage |
Inspection | Regularly check for wear and oxidation | Identifies early signs of degradation |
Storage | Store in dry, controlled conditions | Prevents premature wear and ensures longevity |
13. How to Choose the Right Heat Resistant Metal for Your Project
Choosing the right heat resistant metal for your project can seem daunting, but breaking down the selection process into manageable steps makes it easier. Here’s how to go about it:
- Assess the Operating Conditions: What temperatures and stresses will the metal be exposed to? This will help narrow down your options.
- Consider the Material’s Strength: Ensure the metal can withstand mechanical stress, fatigue, and thermal expansion in your specific application.
- Cost vs. Performance: Balance the need for high performance with the available budget. Don’t forget to factor in long-term maintenance costs.
Ready for the good part? With the right approach, choosing the right heat resistant metal becomes a straightforward task that delivers long-lasting, cost-effective results.
Selection Criteria | Consideration | Example Materials |
---|---|---|
Operating Conditions | Temperature and stress levels | Titanium alloys, Inconel |
Material Strength | Mechanical and thermal strength | Nickel alloys, Stainless steel |
Cost vs. Performance | Balance between cost and longevity | Stainless steel (low), Inconel (high) |
14. Environmental Impact of Heat Resistant Metals
The production and use of heat resistant metals have environmental implications, especially when considering their extraction, manufacturing, and disposal. Here’s a closer look:
- Resource Extraction: Mining for metals such as titanium and nickel can have significant environmental impacts, including habitat disruption and pollution.
- Manufacturing: The energy-intensive processes used to create heat resistant metals can contribute to high carbon emissions.
- Recycling: Recycling heat resistant metals is a sustainable way to reduce waste and conserve resources. Many high-performance alloys are recyclable, but the process can be complex.
But here’s where it gets interesting – industries are working to mitigate the environmental impact of heat resistant metals by developing more sustainable practices and recycling methods.
Environmental Impact | Concern | Solutions |
---|---|---|
Resource Extraction | Habitat disruption and pollution | Sustainable mining practices |
Manufacturing | High energy consumption | Use of renewable energy sources |
Recycling | Complex recycling processes | Improved recycling technologies |
15. Conclusion and Final Thoughts
Heat resistant metals are essential for a wide range of industries, ensuring that critical components perform reliably under extreme conditions. Understanding the different types of metals, their properties, and how to select the right material is key to success in high-temperature applications. Remember, choosing the right heat resistant metal involves considering factors like temperature tolerance, mechanical strength, and corrosion resistance. With the right approach and proper maintenance, these metals will deliver long-term performance and reliability in some of the most demanding environments.
FAQ Section
Q1: What is heat resistant metal?
Heat resistant metals are materials that can withstand high temperatures without degrading in strength or structure. These metals are essential for environments that expose them to extreme heat.
Q2: How does heat resistance affect metal performance?
Heat resistance allows metals to maintain their integrity and mechanical properties under high temperatures, preventing failure or deformation in harsh environments.
Q3: What are the best types of heat resistant metals for aerospace?
Titanium alloys, Inconel, and certain types of stainless steel are commonly used in aerospace due to their high-temperature stability and corrosion resistance.
Q4: Can heat resistant metals be used in food processing?
Yes, metals like stainless steel are commonly used in food processing due to their ability to withstand high temperatures and prevent contamination.
Q5: Are heat resistant metals recyclable?
Yes, many heat resistant metals, such as stainless steel and titanium alloys, can be recycled, though the process may be more complex due to the need for maintaining material properties.