Aluminum casting is a process that transforms molten aluminum into solid objects by pouring it into a mold. The aluminum cools and hardens inside the mold, taking its shape. This method is widely used in various industries due to its ability to create complex, durable, and lightweight components. In this article, we will explore the significance of aluminum casting, how it works, and the three main methods used in this process: sand casting, die casting, and permanent mold casting. Understanding these methods and their applications will provide valuable insights for those in manufacturing and engineering sectors.
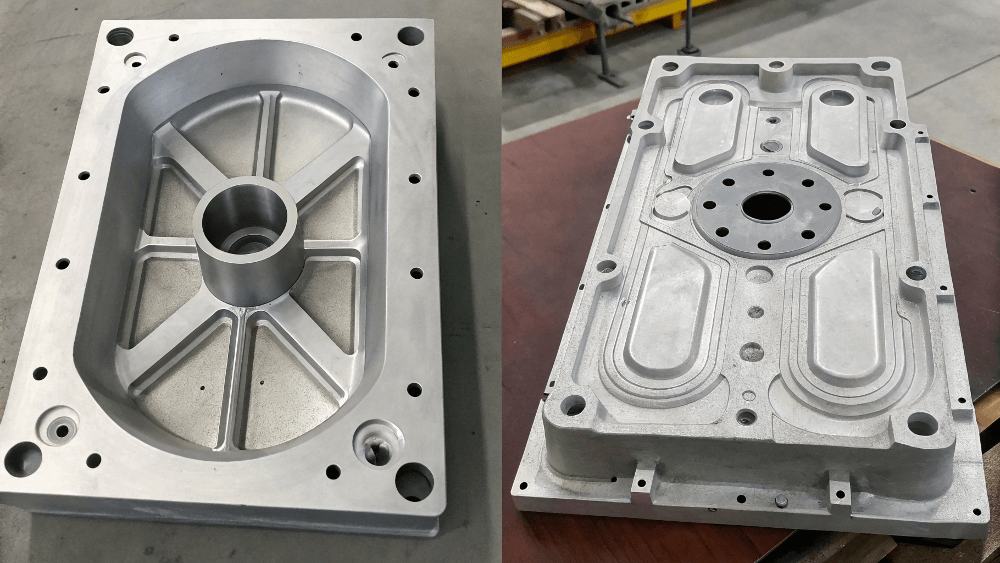
1. What is Aluminum Casting?
Aluminum casting is one of the most widely used methods for producing metal parts in various industries. This manufacturing technique involves melting aluminum, pouring it into a mold, and allowing it to solidify, taking the shape of the mold. The process is highly versatile, offering the ability to create intricate designs and complex structures. But here’s the kicker: aluminum casting has revolutionized industries such as automotive, aerospace, and construction due to its cost-effectiveness and high-quality results.
The history of aluminum casting dates back to the early 19th century. Today, it remains one of the most essential processes for mass production of aluminum parts. Aluminum casting’s benefits extend beyond just creating metal objects; it allows manufacturers to achieve high precision, strength, and cost efficiency in their products. It’s also one of the most eco-friendly methods of production, with recycled aluminum being used in most cases, minimizing environmental impact.
Notably, aluminum casting is a cornerstone in industries that require strong, lightweight, and corrosion-resistant parts, like automotive and aerospace. For instance, car engine blocks, aircraft components, and architectural elements often rely on aluminum casting due to its ability to form complex shapes with minimal material waste. What’s the real story? The aluminum casting process is integral to reducing manufacturing costs while maintaining product integrity.
Applications | Industries | Benefits |
---|---|---|
Engine blocks | Automotive | Lightweight, strong |
Aircraft parts | Aerospace | Corrosion-resistant |
Construction materials | Construction | High precision |
Electrical components | Electronics | Cost-efficient |
2. Why is Aluminum Casting Important?
Why does aluminum casting matter? Well, it’s not just about creating metal objects. Aluminum casting is an essential process in manufacturing for multiple reasons, starting with its ability to produce lightweight and durable parts. These properties make aluminum casting particularly valuable in industries such as automotive, aerospace, and electronics, where performance and durability are critical.
But here’s the kicker: aluminum casting is not just lightweight; it’s also cost-effective. Aluminum is relatively inexpensive compared to other metals like steel, and the casting process itself is efficient. This makes it an ideal choice for mass production. Additionally, aluminum casting reduces the environmental impact of manufacturing by allowing the use of recycled aluminum. So, aluminum casting isn’t just an industrial workhorse—it’s an eco-friendly solution as well.
The benefits extend beyond just cost and weight. Aluminum casting also allows for intricate designs that would be impossible with other methods, such as forging or machining. This precision is particularly important in the production of parts for industries that rely on tight tolerances, such as automotive and aerospace. With aluminum casting, manufacturers can achieve exact shapes with minimal material waste, which further improves cost-effectiveness. What’s the real story? Aluminum casting helps companies deliver high-performance, durable products that meet the specific demands of various industries.
Advantage | Description | Industries Benefiting |
---|---|---|
Cost-effective | Lower material costs | Automotive, Electronics |
Lightweight | Reduces the overall weight of parts | Aerospace, Automotive |
Durability | Increased product longevity | Aerospace, Construction |
Precision | High accuracy in complex designs | Automotive, Electronics |
3. What Are the Main Types of Aluminum Casting?
What types of aluminum casting are commonly used? Aluminum casting can be done using several methods, each with its strengths and suitability for different applications. The three most popular aluminum casting methods are sand casting, die casting, and permanent mold casting. Let’s break each one down.
Sand Casting is one of the oldest and most widely used aluminum casting methods. This process involves creating a mold from a mixture of sand, clay, and water, then pouring molten aluminum into the mold. Sand casting is ideal for larger parts and is particularly useful when dealing with low to medium production volumes. Its main advantage is the ability to produce complex parts at a low cost, making it suitable for applications such as engine blocks and other large components.
Die Casting is another method commonly used for aluminum casting. In this method, molten aluminum is injected under high pressure into a steel mold or die. Die casting is perfect for high-volume production and is used in the manufacturing of smaller parts with high precision. The process results in smooth, well-defined parts that require minimal finishing. Die casting is commonly used for parts in industries such as automotive, electronics, and consumer products.
Permanent Mold Casting involves pouring molten aluminum into a reusable mold made of metal, typically steel or iron. This method is used for parts requiring high strength and precision, especially in smaller quantities. Permanent mold casting is ideal for producing thin-walled parts and is commonly used in the aerospace and automotive industries for components such as transmission cases and gearbox housings.
Casting Method | Best For | Key Benefits |
---|---|---|
Sand Casting | Large, complex parts | Low cost, flexibility in design |
Die Casting | High-volume, precise parts | High accuracy, smooth surface |
Permanent Mold Casting | Small, intricate parts | Strength, precision, repeatability |
4. How Does Sand Casting Work?
Let’s get into the details of sand casting. This is a process that involves creating a mold from a mixture of sand and clay, which is compacted to form a cavity into which molten aluminum is poured. Sand casting is an excellent option for larger parts and components that need to be produced in lower quantities, making it cost-effective and highly versatile. Ready for the good part? The sand used in this process is highly adaptable, allowing it to create molds for even the most intricate designs.
The sand casting process starts with the creation of a pattern, which is a replica of the object being cast. This pattern is placed in a mold box, and the sand mixture is packed around it. Once the mold is created, molten aluminum is poured into the cavity. After the aluminum solidifies, the mold is broken away, revealing the cast part. The main advantage of sand casting is its ability to produce complex shapes with a high degree of detail, and it’s particularly useful for low to medium production volumes.
However, sand casting also has limitations. For instance, it tends to produce parts with rougher surfaces compared to die casting. These parts may require additional finishing processes, such as grinding or machining, to meet the desired surface quality. Nevertheless, sand casting remains a highly popular choice for industries that require large parts and are working with limited production runs.
Step | Description | Outcome |
---|---|---|
Pattern Creation | Replica of the part being cast | Precise design replication |
Mold Formation | Sand and clay mixture packed around pattern | Mold ready for pouring |
Pouring Molten Aluminum | Aluminum poured into the mold cavity | Initial cast formed |
Cooling and Solidifying | Aluminum cools and hardens | Solidified part ready for finishing |
5. How Does Die Casting Work?
Die casting is a fast, high-precision method of aluminum casting. The process involves injecting molten aluminum into a steel mold under high pressure. The key difference between die casting and other methods is the use of pressure to force the aluminum into the mold, ensuring highly accurate and smooth parts. This is where it gets interesting: die casting allows for extremely tight tolerances and a high level of precision, which is why it’s favored in industries like automotive and electronics for producing small, complex components.
The die casting process starts with the preparation of a mold, which consists of two parts—usually made of steel. These molds are designed to withstand the high pressure applied during the injection process. Once the mold is ready, molten aluminum is injected into it at high pressure. After cooling and solidification, the mold is opened, and the finished part is removed. The key benefit of die casting is its ability to produce parts with thin walls and smooth surfaces, requiring minimal post-casting processing.
Die casting is ideal for high-volume production, where consistency and precision are paramount. However, it does have some limitations, such as high initial tooling costs and the potential for defects such as air pockets or trapped gases. Despite these challenges, die casting remains a popular choice for industries looking to produce high-precision parts efficiently.
Step | Description | Outcome |
---|---|---|
Mold Preparation | Steel molds are prepared for injection | Ready for high-pressure injection |
High-Pressure Injection | Molten aluminum injected into the mold | High-precision part creation |
Cooling and Solidifying | Aluminum cools and hardens | Final part removal from the mold |
Post-Casting Processing | Minor finishing processes | Clean, smooth part for use |
6. How Does Permanent Mold Casting Work?
Permanent mold casting, also known as gravity die casting, uses a reusable mold made from metal, usually steel or iron. This method is ideal for creating parts that require a high level of detail, strength, and repeatability. Ready for the good part? Permanent mold casting allows manufacturers to produce complex parts in small quantities while ensuring high-quality results.
The process starts by preparing a metal mold, which is often machined to create precise cavities. Once the mold is ready, molten aluminum is poured into it under gravity, allowing the metal to fill the cavity. After the aluminum cools and solidifies, the mold is removed, and the casting is extracted. This method offers a number of advantages, including the ability to produce parts with thinner walls compared to sand casting. It is ideal for producing smaller, intricate parts, such as those used in the automotive and aerospace industries.
Although permanent mold casting is a cost-effective alternative to die casting, it is typically used for lower-volume production. The molds used in this process can be expensive to make, but their reusable nature helps reduce overall costs over time. However, permanent mold casting may not be suitable for parts with very complex geometries or those that require high-volume production.
Step | Description | Outcome |
---|---|---|
Mold Preparation | Metal molds are prepared and machined | Accurate cavity creation |
Pouring Molten Aluminum | Aluminum poured into the mold cavity | Part shaped in the mold |
Cooling and Solidifying | Aluminum solidifies in the mold | Part removed from the mold |
Post-Casting Processing | Minor finishing and cleaning | Ready-for-use high-strength part |
7. What Materials Are Used in Aluminum Casting?
When it comes to aluminum casting, the materials used play a significant role in determining the quality and performance of the final product. But here’s the kicker: aluminum alloys are the most commonly used materials in the casting process, and choosing the right alloy is crucial for achieving the desired properties of the cast part. Let’s break down the main types of aluminum alloys used in casting and how they impact the final product.
Aluminum casting alloys are typically divided into two main categories: wrought alloys and casting alloys. Casting alloys are specifically designed for casting processes like sand casting, die casting, and permanent mold casting. These alloys are formulated to ensure that the aluminum flows easily into molds and solidifies efficiently. Common casting alloys include the 1xx.x, 2xx.x, 3xx.x, 5xx.x, and 7xx.x series. Each series has its unique properties, making them suitable for different applications.
For example, the 3xx.x series, which includes alloys like A356 and A380, is widely used in die casting due to its excellent fluidity and strength. A356 is commonly used for aerospace components, while A380 is used for automotive and electrical applications. On the other hand, the 2xx.x series, including alloys like A201, is used in high-strength applications where durability is crucial, such as engine blocks and high-performance parts.
What’s the real story? The right choice of alloy ensures that the final product meets the performance requirements of its intended application. Whether you need corrosion resistance, high strength, or excellent casting fluidity, selecting the right aluminum alloy is key to a successful casting process.
Alloy Series | Common Alloys | Properties | Applications |
---|---|---|---|
1xx.x | 1050, 1100 | High corrosion resistance, excellent workability | Electrical, food processing |
2xx.x | A201, A202 | High strength, good wear resistance | Engine blocks, performance parts |
3xx.x | A356, A380 | Excellent fluidity, good castability | Automotive, aerospace |
5xx.x | A5052, A5083 | Corrosion resistance, good weldability | Marine, architectural |
7xx.x | A7075, A7050 | High strength, excellent machinability | Aerospace, military |
8. What Are the Key Steps in the Aluminum Casting Process?
The aluminum casting process involves several key steps that are critical to producing high-quality castings. Ready for the good part? Each step must be carefully controlled to ensure the final product meets all specifications, whether it’s for an automotive part, aerospace component, or industrial machine. Let’s go through the primary stages of the aluminum casting process.
The process begins with the preparation of the mold. Depending on the casting method being used, this step can involve creating sand molds, preparing die molds, or setting up permanent molds. The mold must be carefully designed to accommodate the molten aluminum and ensure that it solidifies into the desired shape.
Once the mold is ready, the next step is pouring the molten aluminum into the mold cavity. The aluminum must be heated to a high temperature, typically around 1,200 to 1,300 degrees Fahrenheit, to achieve the right viscosity for pouring. The molten aluminum is then poured into the mold, filling the cavity and taking the shape of the mold.
After pouring, the next phase is cooling and solidification. The aluminum needs to cool and harden inside the mold, which can take anywhere from a few minutes to several hours, depending on the size and complexity of the casting. Once the aluminum has fully solidified, the mold is removed, and the casting is cleaned and inspected for defects.
Finally, post-casting processes are performed to finish the part. This includes removing any excess material, deburring sharp edges, and sometimes machining the part to achieve the desired surface finish or dimensional accuracy. The casting is then inspected for defects, such as porosity or surface imperfections.
Step | Description | Purpose |
---|---|---|
Mold Preparation | Creation of mold using sand, metal, or other materials | To form the cavity for pouring |
Pouring Molten Aluminum | Heating aluminum and pouring it into the mold | To shape the casting |
Cooling and Solidification | Allowing the aluminum to cool and harden | To solidify the molten aluminum |
Post-Casting Processing | Cleaning, deburring, and machining | To finish the part and remove defects |
9. What Are the Common Defects in Aluminum Casting?
What’s the catch with aluminum casting? While the process can produce high-quality, durable parts, there are also potential defects that can compromise the final product. Let’s dig into the most common defects in aluminum casting and how they can be prevented or corrected.
Porosity is one of the most common defects in aluminum casting. It occurs when gas bubbles are trapped inside the aluminum as it solidifies, leading to holes or voids in the part. Porosity can be caused by several factors, such as improper pouring techniques, high moisture in the mold, or contamination of the aluminum. The result? Weakened parts that might not meet strength or performance standards.
Shrinkage is another common issue. As aluminum cools and solidifies, it contracts, and if the mold isn’t designed to accommodate this shrinkage, the casting may end up with gaps or voids. This can affect the part’s strength and appearance. To combat shrinkage, manufacturers can adjust the mold design or use additives that help reduce the contraction during cooling.
Cold shuts and hot tears are other defects that occur due to improper pouring temperatures. Cold shuts happen when the aluminum doesn’t flow smoothly into the mold, while hot tears occur when the part is cooling too quickly. Both defects can be minimized by controlling pouring temperatures and ensuring the mold is heated correctly.
What’s the real story? The key to producing defect-free aluminum castings is quality control at every stage of the process, from mold preparation to post-casting inspections. By identifying potential issues early on, manufacturers can minimize defects and ensure high-quality parts.
Defect | Cause | Solution |
---|---|---|
Porosity | Trapped gas, improper pouring | Use proper pouring techniques, degas the aluminum |
Shrinkage | Aluminum contraction during cooling | Adjust mold design, use additives to reduce shrinkage |
Cold Shuts | Poor flow of molten aluminum | Ensure proper pouring temperature |
Hot Tears | Rapid cooling of aluminum | Control cooling rates, preheat molds |
10. How Do You Choose the Right Aluminum Casting Method?
Choosing the right aluminum casting method depends on a variety of factors. Ready for the good part? It’s not just about selecting a casting process—it’s about aligning the method with the specific needs of your project. Here are the key factors to consider when making this decision.
First, consider the production volume. Sand casting is typically used for low to medium production volumes, making it ideal for prototype parts or low-run orders. On the other hand, die casting is better suited for high-volume production, especially when precise parts with smooth surfaces are needed. Permanent mold casting is somewhere in between, offering both precision and efficiency for moderate production runs.
Another key factor is the part complexity. If you need intricate details, complex shapes, or fine features, die casting and permanent mold casting are the go-to choices. Sand casting, while versatile, may not provide the same level of precision. It’s also important to consider material properties. Different casting methods may be better suited for different alloys, so understanding the material requirements is crucial.
The cost of tooling and molds is also a significant consideration. Sand casting is generally the least expensive option, followed by permanent mold casting, with die casting being the most expensive due to the high initial tooling costs. However, die casting’s efficiency in high-volume production may offset its higher upfront costs.
Factor | Sand Casting | Die Casting | Permanent Mold Casting |
---|---|---|---|
Production Volume | Low to medium | High | Moderate |
Part Complexity | Moderate | High | High |
Material Suitability | Versatile | Excellent for specific alloys | Ideal for small, intricate parts |
Cost | Low | High | Moderate |
11. How Do Aluminum Castings Compare to Other Metals?
What sets aluminum castings apart from other metals? While aluminum is a popular choice for casting, it’s essential to compare it with other materials like steel and iron. This comparison helps determine which material is best suited for different applications. Let’s dive into the differences between aluminum and its counterparts.
Aluminum has a significant advantage when it comes to weight. It’s much lighter than steel and iron, making it ideal for applications where weight is a critical factor, such as in the aerospace and automotive industries. Steel, on the other hand, is much stronger than aluminum, making it more suitable for heavy-duty applications where strength is paramount.
In terms of cost, aluminum is more affordable than steel but slightly more expensive than iron. However, aluminum casting’s ability to be recycled easily can reduce long-term costs, making it an environmentally friendly choice. Corrosion resistance is another area where aluminum excels. Unlike steel, aluminum does not rust, making it a better option for outdoor or marine applications.
What’s the real story? While aluminum may not be the best choice for every application, its combination of light weight, corrosion resistance, and cost-effectiveness make it a top contender for many industries, especially when compared to steel and iron.
Metal Type | Weight | Strength | Corrosion Resistance | Cost |
---|---|---|---|---|
Aluminum | Lightweight | Moderate | Excellent | Moderate |
Steel | Heavy | High | Prone to rust | Low |
Iron | Heavy | High | Prone to rust | Low |
12. What Are the Benefits of Using Aluminum Castings in Manufacturing?
Why should manufacturers use aluminum castings? Aluminum casting offers a number of significant advantages in production processes, especially in industries that require lightweight, durable, and high-precision parts. What’s the kicker here? Aluminum castings combine performance, cost-effectiveness, and sustainability in a way that few other materials can match.
One of the primary benefits of aluminum castings is their lightweight nature. This makes them an ideal choice for industries like automotive and aerospace, where reducing weight can lead to better fuel efficiency and overall performance. Aluminum also has excellent corrosion resistance, ensuring that cast parts maintain their integrity even in harsh environments, such as marine or industrial settings.
Another key advantage is cost-effectiveness. Aluminum casting can be a more affordable option compared to other methods, such as machining or forging. It also allows for more complex part designs, which can reduce the need for additional processes like welding or assembly. Recycling is another environmental benefit of aluminum casting, as recycled aluminum retains nearly the same properties as virgin aluminum, reducing the need for new materials.
Benefit | Description | Industries Benefiting |
---|---|---|
Lightweight | Reduces overall part weight | Automotive, Aerospace |
Corrosion Resistance | Protects parts in harsh environments | Marine, Industrial |
Cost-Effective | Lower production costs and less material waste | Automotive, Electronics |
Sustainability | Recyclable material reduces environmental impact | Manufacturing, Consumer Products |
13. What Are the Challenges of Aluminum Casting?
Even though aluminum casting offers several advantages, it does come with its set of challenges. Ready for the good part? Understanding these challenges can help manufacturers optimize the casting process and avoid costly mistakes. Let’s explore some of the common difficulties encountered in aluminum casting.
One challenge is the initial tooling cost, especially for high-precision methods like die casting. These molds can be expensive to create, and in some cases, the initial investment may be prohibitively high for small or low-volume production runs. However, the high efficiency of die casting in large-scale production can offset this cost over time.
Another challenge is defect prevention. As discussed earlier, defects like porosity, shrinkage, and surface imperfections can occur during the casting process. These defects can compromise the quality of the final part, leading to additional costs for rework or scrap. Implementing strict quality control measures, using advanced techniques, and employing experienced staff can help mitigate these issues.
Handling and transport of cast parts can also present challenges. Aluminum castings, especially those with complex shapes, may require special handling to avoid damage. Additionally, transporting large aluminum castings can be costly and require careful planning to ensure that the parts reach their destination in good condition.
Challenge | Description | Solution |
---|---|---|
Tooling Costs | High initial mold costs, especially for die casting | Offset costs with high-volume production |
Defect Prevention | Issues like porosity and shrinkage | Implement quality control measures |
Handling and Transport | Risk of damage during transportation | Use specialized packaging and handling |
14. What is the Future of Aluminum Casting?
Looking ahead, what does the future hold for aluminum casting? The future of aluminum casting is bright, with exciting innovations on the horizon. The technology behind aluminum casting is evolving rapidly, driven by advancements in automation, digitalization, and sustainability. Ready for the good part? These advancements promise to make aluminum casting even more efficient, environmentally friendly, and cost-effective.
One major trend is the increasing use of automation in the aluminum casting process. Robots and automated systems are already being used to handle repetitive tasks like mold handling, pouring, and part removal. This reduces labor costs and increases production efficiency. Additionally, 3D printing technology is beginning to play a role in aluminum casting by enabling manufacturers to create complex molds or even entire parts without the need for traditional casting methods.
Sustainability is also a key factor shaping the future of aluminum casting. With a growing emphasis on recycling and reducing environmental impact, more manufacturers are adopting green practices in their casting operations. This includes using recycled aluminum as a primary material, which reduces the need for raw mining and helps lower the overall carbon footprint.
Future Trend | Description | Impact |
---|---|---|
Automation | Increased use of robots and automation in casting | Higher efficiency and reduced labor costs |
3D Printing | Integration of 3D printing for molds and parts | More complex designs and reduced material waste |
Sustainability | Increased focus on recycling and eco-friendly practices | Reduced environmental impact, lower carbon footprint |
15. Conclusion
In conclusion, aluminum casting remains a cornerstone of modern manufacturing, offering numerous benefits across industries that require durable, lightweight, and high-precision parts. From automotive to aerospace, the flexibility and cost-effectiveness of aluminum casting make it an essential process for producing high-quality components. However, the casting process does come with its challenges, such as tooling costs and potential defects, but these can be mitigated with proper planning and quality control.
What’s the real story? The future of aluminum casting looks promising, with innovations in automation, 3D printing, and sustainability set to revolutionize the industry. Whether you’re in automotive, aerospace, or another manufacturing field, understanding aluminum casting’s methods, materials, and advantages can help you make informed decisions that lead to better products and more efficient production processes.
FAQ Section
Q1: What is aluminum casting?
Aluminum casting is a manufacturing process where molten aluminum is poured into a mold to create metal parts. These parts are used across various industries, including automotive, aerospace, and construction.
Q2: How does die casting work?
Die casting involves injecting molten aluminum into a steel mold under high pressure. This results in highly precise parts with smooth surfaces, ideal for high-volume production.
Q3: What are the advantages of aluminum casting?
Aluminum casting provides lightweight, durable, and cost-effective solutions. It also allows for the creation of intricate designs with minimal material waste, making it ideal for mass production.
Q4: What are the main types of aluminum casting methods?
The three main types are sand casting, die casting, and permanent mold casting. Each method is used depending on the complexity, volume, and precision required for the parts.
Q5: What are common defects in aluminum casting?
Common defects include porosity, shrinkage, and surface imperfections. These defects can be minimized with proper techniques and quality control during the casting process.