When working with aluminum castings in sand casting, understanding and calculating shrinkage is crucial. Shrinkage occurs when aluminum solidifies and cools, leading to a reduction in volume and potential dimensional inaccuracies in the final product. This article will explore the factors influencing aluminum casting shrinkage, how to calculate it, and the best methods to reduce it for better quality and precision in your sand casting projects.
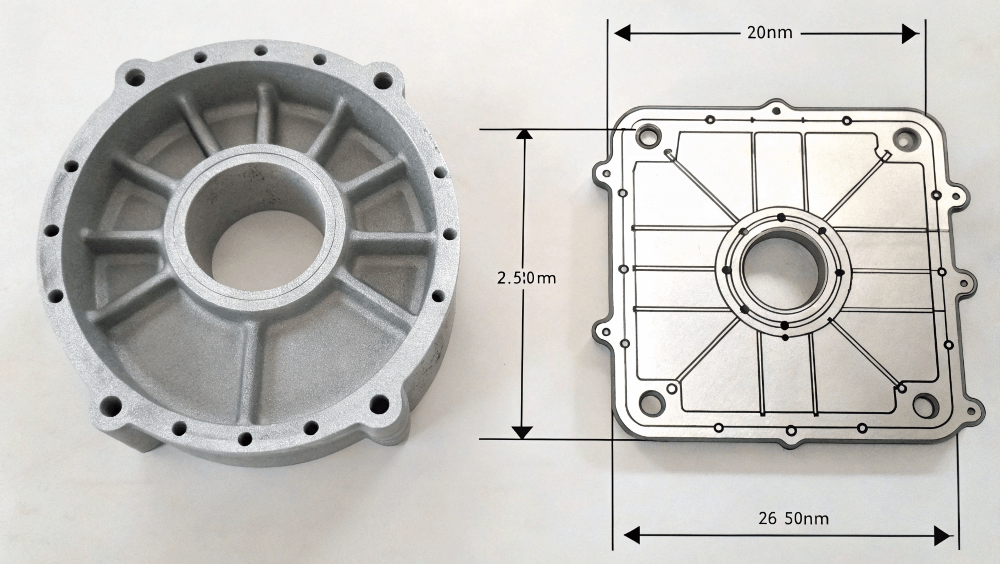
1. What is Aluminum Casting Shrinkage?
Aluminum casting shrinkage is the reduction in volume that occurs when molten aluminum solidifies and cools. This phenomenon happens because metals contract as they cool from their liquid state to their solid form. For aluminum, the shrinkage percentage can vary based on several factors such as the type of aluminum alloy used, the cooling rate, and the design of the casting mold. This shrinkage can lead to dimensional inaccuracies in the final product if not properly accounted for.
But here’s the kicker: If shrinkage is not properly calculated and controlled during the design and casting process, it can result in significant defects like warping, voids, or even cracked components. These defects affect the part’s strength, aesthetic appeal, and overall performance. So, how exactly do we calculate and manage shrinkage in aluminum sand casting? Let’s dive deeper.
Aluminum alloys typically shrink by 1.5% to 2.5% during solidification, depending on the alloy and cooling conditions. The key to accurate shrinkage calculation is to understand the material’s specific shrinkage rate and how it interacts with the mold. In sand casting, the mold material itself also impacts shrinkage, as the heat transfer rate can vary significantly based on the mold’s composition.
Table 1: Typical Shrinkage Rates for Common Aluminum Alloys
Alloy Type | Shrinkage Rate (%) |
---|---|
A356 (Al-Si) | 1.7 |
6061 (Al-Mg-Si) | 1.9 |
356 (Al-Si-Cu) | 2.2 |
2024 (Al-Cu) | 2.4 |
2. Why is Shrinkage Important in Sand Casting?
Shrinkage is a major concern in sand casting because it affects both the dimensional accuracy and the overall quality of the aluminum cast. For manufacturers, ensuring minimal shrinkage is vital to achieving precise, functional parts. If shrinkage is not accounted for in the design phase, it can lead to various issues such as misalignment, improper fit, and reduced strength.
What’s the real story? If you’re working on a project with strict tolerances, unaccounted shrinkage could force you to rework or scrap entire batches. Not only does this lead to wasted materials and time, but it can also cost you significantly in terms of labor and resources.
Besides dimensional concerns, shrinkage can also cause aesthetic imperfections, such as surface pitting or rough textures. This is particularly problematic in industries where high-quality surface finishes are crucial, such as aerospace, automotive, and medical device manufacturing. Ensuring the right amount of shrinkage compensation can save you from these costly errors.
To mitigate shrinkage, manufacturers must consider factors such as mold design, alloy choice, and cooling techniques during the casting process. Proper shrinkage compensation in both the mold design and the pattern itself can help avoid defects. Without a doubt, understanding shrinkage and accounting for it in your casting design is a critical part of achieving optimal results.
Table 2: Impact of Shrinkage on Dimensional Accuracy
Effect of Shrinkage | Potential Outcome |
---|---|
Excess shrinkage | Dimensional inaccuracies |
Insufficient shrinkage | Warped or cracked parts |
Uneven shrinkage | Surface imperfections |
3. What Are the Causes of Aluminum Casting Shrinkage?
Aluminum casting shrinkage occurs due to a variety of factors, and understanding these factors is key to managing and controlling it effectively. One of the primary causes is the cooling rate. When aluminum cools too quickly, it can cause uneven solidification, leading to localized shrinkage. On the other hand, slow cooling rates can also cause excess shrinkage as the metal has more time to contract.
Ready for the good part? The composition of the aluminum alloy itself plays a significant role in determining the extent of shrinkage. For example, alloys with a higher silicon content generally exhibit lower shrinkage rates, making them easier to manage in sand casting.
Additionally, the design of the mold can affect shrinkage. A poorly designed mold, one that lacks proper ventilation or has improper gating and risers, can cause uneven cooling, which exacerbates shrinkage. The temperature gradient across the mold can lead to sections cooling at different rates, creating stress within the cast.
Another important factor is the quality of the sand used in the mold. Coarse, poorly compacted sand can cause faster cooling, leading to more shrinkage, while finely ground sand can allow for more uniform cooling, reducing the likelihood of excessive shrinkage.
Table 3: Factors Affecting Aluminum Casting Shrinkage
Factor | Effect on Shrinkage |
---|---|
Cooling rate | Faster cooling increases shrinkage |
Alloy composition | Higher silicon content reduces shrinkage |
Mold design | Poor design increases shrinkage |
Sand quality | Coarse sand increases shrinkage |
4. How Can Shrinkage Be Calculated in Sand Casting?
Calculating shrinkage in aluminum sand casting requires understanding the specific shrinkage rate of the alloy being used. This can be done through a straightforward formula:
Shrinkage Percentage = (Initial volume – Final volume) / Initial volume * 100
But wait—calculating shrinkage isn’t just about applying a formula. You’ll need to take into account factors like the specific alloy type, mold conditions, and cooling rates. The equation above can serve as a starting point, but real-world casting requires adjustments based on experimental results.
Here’s where it gets interesting: Shrinkage isn’t uniform across the entire casting. Different parts of the mold cool at different rates, causing some areas to shrink more than others. That’s why precise calculations and a deep understanding of the entire casting process are necessary to minimize shrinkage defects.
A practical example: Let’s assume you are casting a part from A356 aluminum. If the initial volume is 1000 cm³, and after cooling the volume reduces to 980 cm³, the shrinkage rate would be calculated as:
Shrinkage Percentage = (1000 – 980) / 1000 * 100 = 2%
Table 4: Example Shrinkage Calculation
Alloy Type | Initial Volume (cm³) | Final Volume (cm³) | Shrinkage Percentage |
---|---|---|---|
A356 | 1000 | 980 | 2% |
6061 | 1000 | 975 | 2.5% |
2024 | 1000 | 965 | 3.5% |
5. How to Reduce Shrinkage in Sand Casting?
Reducing shrinkage in sand casting starts with careful planning during the design phase. One of the most effective ways to minimize shrinkage is to optimize mold design. A well-designed gating system and risers allow molten metal to flow efficiently and reduce the chances of shrinkage defects.
This is where it gets interesting: The cooling rate of the casting also plays a crucial role. By controlling the cooling process—whether through controlled furnace cooling or modifying the mold material—you can reduce the likelihood of excessive shrinkage. For example, using sand with a finer grain size allows for a more controlled cooling process and reduces the risk of shrinkage.
Additionally, choosing the right alloy for your application can significantly impact shrinkage. As mentioned earlier, alloys with a higher silicon content tend to have lower shrinkage rates. Choosing a higher-quality alloy may result in a more precise cast with fewer shrinkage-related issues.
What’s the real story here? Minimizing shrinkage isn’t just about design and material choice—it’s also about effective process management. Continuous monitoring and testing throughout the casting process help identify potential shrinkage issues early and correct them before they cause defects.
Table 5: Methods for Reducing Shrinkage in Sand Casting
Method | Impact on Shrinkage |
---|---|
Optimized mold design | Reduces shrinkage defects |
Controlled cooling rates | Prevents uneven shrinkage |
Use of higher silicon alloys | Reduces shrinkage |
6. What Are the Common Methods to Correct Shrinkage After Casting?
Even with meticulous planning, shrinkage can still occur after the casting process. While it’s preferable to minimize shrinkage during the initial casting, corrections can still be made once the casting has cooled. The most common methods to correct shrinkage include re-machining, welding, and adding filler material.
What’s the real story? Shrinkage correction is often necessary when there are voids or deformations that can’t be fixed simply by altering the design. Re-machining involves removing excess material from the surface of the casting to achieve the desired dimensions. However, this method can be costly and time-consuming, especially for large or complex castings.
Another technique involves welding or adding filler material to areas that have experienced significant shrinkage. While this method can correct dimensional issues, it is often used when the shrinkage is localized or affects a non-critical area. However, it’s not always ideal for high-precision parts, as it can introduce additional stress to the material.
Lastly, adding extra metal during the casting process is a technique that many manufacturers use. Risers and gating systems can be used to provide additional material to accommodate shrinkage as it occurs. These methods ensure that shrinkage does not result in voids or misalignments in the final product.
Table 6: Methods of Shrinkage Correction After Casting
Method | Description | Ideal Usage |
---|---|---|
Re-machining | Removing excess material via machining | For achieving precise dimensions |
Welding and filler material | Adding material to fill voids | For localized shrinkage correction |
Risers and gating | Adding extra metal during casting | To accommodate shrinkage during solidification |
7. How Does Alloy Composition Affect Shrinkage in Sand Casting?
The composition of the aluminum alloy plays a significant role in determining how much shrinkage will occur during the casting process. Certain alloys, such as those with higher silicon content, typically experience less shrinkage because silicon helps prevent the formation of gas pockets and reduces the metal’s overall contraction.
But here’s the kicker: Alloying elements also affect the solidification point of the aluminum, which directly influences how it behaves during cooling. For example, aluminum alloys with a higher percentage of copper tend to shrink more than those with higher silicon levels. This is because copper has a higher tendency to form a solid structure faster, resulting in increased volume contraction.
Choosing the right alloy for your specific application can help reduce shrinkage and improve the final product’s quality. For example, choosing alloys with a lower tendency to shrink can help reduce the overall need for shrinkage compensation. On the other hand, some alloys, like those with a high copper content, may require more rigorous mold and process design to ensure that the final cast is up to standard.
Table 7: Shrinkage in Aluminum Alloys by Composition
Alloy Type | Shrinkage Rate (%) | Key Composition Elements |
---|---|---|
A356 | 1.7 | Silicon, Magnesium, Iron |
6061 | 1.9 | Magnesium, Silicon, Copper |
2024 | 2.4 | Copper, Magnesium, Manganese |
7075 | 2.0 | Zinc, Magnesium, Copper |
8. What Role Does Mold Design Play in Shrinkage Control?
Mold design is a crucial factor in controlling shrinkage during aluminum sand casting. A poorly designed mold can cause uneven cooling rates, leading to areas of the casting shrinking at different rates. This can result in warping, cracks, or voids in the final product. One of the most effective ways to control shrinkage is by designing a mold that allows for uniform cooling.
Ready for the good part? The inclusion of risers and gating systems can help direct molten metal flow to areas that are prone to shrinkage. A riser acts as a reservoir for molten metal and ensures that the metal flows into the mold as it cools, compensating for the shrinkage that occurs during solidification.
Gating systems also play a critical role. They control how molten metal enters the mold and helps prevent turbulence, which can lead to poor surface finishes or internal defects. Proper placement of these systems can help reduce the likelihood of shrinkage defects and ensure that the casting cools uniformly.
The design of the mold material itself also influences how shrinkage is managed. Mold materials that allow for faster cooling may reduce shrinkage, but they can also increase the risk of thermal cracking or premature solidification. Therefore, selecting the right mold material and designing it to match the specific casting process is essential for controlling shrinkage.
Table 8: Mold Design Considerations for Shrinkage Control
Mold Design Feature | Effect on Shrinkage |
---|---|
Risers and Gating Systems | Ensures uniform metal flow |
Mold material composition | Impacts cooling rate and shrinkage |
Mold wall thickness | Thicker walls reduce shrinkage risk |
9. How to Optimize Cooling Rates for Minimal Shrinkage?
Controlling cooling rates is one of the most effective ways to reduce shrinkage in sand casting. When aluminum cools too quickly, it can result in uneven contraction and cause defects like cracks or warping. On the other hand, slow cooling rates can also result in excessive shrinkage. The key lies in finding the right balance.
What’s the real story here? By carefully managing the cooling rate, manufacturers can minimize thermal gradients within the mold, which reduces the risk of shrinkage. Cooling is influenced by factors such as mold material, ambient temperature, and even the casting’s geometry. A casting with thinner walls may cool faster than one with thicker walls, leading to higher shrinkage in the thinner areas.
To optimize cooling rates, many manufacturers use techniques such as cooling channels within the mold. These channels allow the mold material to absorb heat more evenly, promoting uniform solidification. Additionally, external cooling methods such as air jets or liquid cooling can be used to control the cooling rate during casting.
For example, in high-performance applications where dimensional accuracy is critical, controlled cooling systems that use both external and internal cooling methods are often employed to minimize shrinkage.
Table 9: Methods for Optimizing Cooling Rates in Sand Casting
Cooling Method | Impact on Shrinkage |
---|---|
Cooling channels | Promotes uniform cooling |
External air cooling | Controls surface cooling |
Liquid cooling | Reduces shrinkage in thicker sections |
10. What Are the Risks of Not Accounting for Shrinkage in Sand Casting?
Failing to account for shrinkage in aluminum sand casting can result in a variety of costly issues, both during the casting process and after production. One of the primary risks is dimensional inaccuracy, which can cause parts to not fit properly in their intended applications. For example, in industries such as aerospace or automotive manufacturing, dimensional accuracy is critical for functionality and safety.
But wait, there’s more: Shrinkage-related issues can also affect the structural integrity of the cast part. For instance, if a casting shrinks unevenly, it may experience warping, which compromises its strength and durability. This is especially critical in parts subjected to high-stress conditions.
Additionally, not accounting for shrinkage can lead to excessive rework or even the scrapping of parts. This not only wastes valuable materials but also impacts production timelines, leading to delays and increased labor costs. In some cases, poorly cast parts may need to be remade entirely, leading to further delays and financial losses.
To prevent these issues, manufacturers must incorporate shrinkage compensation into the design phase, regularly monitor the casting process, and use the appropriate shrinkage rate for the alloy and mold material. Failure to do so can result in costly defects and delays in the production process.
Table 10: Risks of Not Accounting for Shrinkage
Risk | Consequence |
---|---|
Dimensional inaccuracies | Poor fit or failure to meet specifications |
Uneven shrinkage | Warped or weak parts |
Increased rework or scrap | Wasted materials and production delays |
11. How Do Modern Casting Technologies Help Reduce Shrinkage?
Modern casting technologies have significantly improved the ability to manage and reduce shrinkage in aluminum sand casting. One of the most impactful innovations is the use of casting simulation software, which allows manufacturers to predict and correct shrinkage issues before casting begins. This software analyzes the cooling process in real time, helping engineers adjust the mold design and cooling rates for optimal results.
Another technological advancement is the use of advanced mold materials that promote more consistent cooling. These materials help reduce temperature gradients across the mold, leading to more uniform shrinkage. Additionally, automated systems that control the flow of molten metal into the mold can help reduce turbulence and ensure a more controlled cooling process.
Lastly, innovations in 3D printing have revolutionized mold design. 3D-printed molds allow for more complex and precise designs, which can help eliminate hot spots and other areas prone to shrinkage. This results in better quality castings with fewer defects.
Table 11: Modern Technologies for Reducing Shrinkage
Technology | Impact on Shrinkage Reduction |
---|---|
Casting simulation software | Predicts and corrects shrinkage |
Advanced mold materials | Promotes uniform cooling |
3D-printed molds | Reduces hot spots and shrinkage |
12. How to Ensure Consistent Results in Shrinkage Calculations?
When working with aluminum casting shrinkage, achieving consistent results is key to maintaining quality and minimizing errors in production. To ensure this, manufacturers often turn to advanced software tools that predict shrinkage based on a range of variables, including alloy type, mold conditions, and cooling rates. These tools can simulate the casting process in detail, helping engineers identify potential shrinkage issues before they occur.
But here’s the kicker: Even the best software models need to be calibrated and validated with real-world data. Therefore, consistent results can only be achieved through ongoing testing, evaluation, and adjustment. For example, running multiple casting trials and comparing the results with predicted shrinkage rates can help refine the model and ensure greater accuracy in future projects.
In addition, employing quality control processes, such as regular inspections and dimensional checks during production, ensures that shrinkage is accounted for throughout the casting process. By monitoring the casting as it is being made, manufacturers can spot shrinkage-related defects early and make necessary adjustments before it becomes a bigger issue.
Lastly, feedback loops between engineering and production teams help ensure that shrinkage calculations align with actual results. This ongoing dialogue and iterative process help refine the casting procedures and reduce the margin for error.
Table 12: Methods for Ensuring Consistent Shrinkage Results
Method | Description |
---|---|
Software simulation | Predicts shrinkage based on material, mold, and cooling rates |
Calibration and validation | Regular comparison between predictions and real-world data |
Ongoing quality control checks | Identifies shrinkage-related defects early in production |
Feedback loops between teams | Ensures adjustments are made based on real-world results |
13. What Tools and Techniques Can Help With Shrinkage Measurement?
Accurately measuring shrinkage is essential for ensuring that aluminum castings meet their design specifications. Several tools and techniques are available to measure shrinkage at various stages of the casting process. One of the most common tools used is a micrometer, which allows engineers to measure the dimensional changes in the casting as it cools. Micrometers can provide highly accurate measurements down to the micrometer level, making them ideal for assessing the precise amount of shrinkage that has occurred.
Ready for the good part? Other non-destructive testing (NDT) methods, such as ultrasonic testing, are also used to measure shrinkage and internal defects in aluminum castings. This technique uses high-frequency sound waves to detect changes in material density, which can help identify areas where shrinkage may have caused voids or cracks.
Additionally, some manufacturers use digital image correlation (DIC) techniques, which involve taking high-resolution images of the casting during cooling to monitor changes in shape and size. This provides a detailed, real-time measurement of shrinkage that can help fine-tune casting processes and improve the overall quality of the product.
Table 13: Tools and Techniques for Measuring Shrinkage
Tool/Technique | Description | Best Used For |
---|---|---|
Micrometer | Provides accurate dimensional measurements | Measuring shrinkage in final castings |
Ultrasonic Testing | Uses sound waves to detect density changes | Identifying internal shrinkage defects |
Digital Image Correlation (DIC) | Captures high-resolution images of the casting | Real-time shrinkage measurement during cooling |
14. How Does Sand Casting Compare to Other Casting Methods in Shrinkage?
Aluminum sand casting is one of the oldest and most widely used casting methods, but how does it compare to other methods in terms of shrinkage? One of the primary advantages of sand casting is its ability to produce large, complex parts at a relatively low cost. However, it also comes with challenges, particularly in controlling shrinkage.
What’s the real story here? While sand casting is effective for many applications, other casting methods like die casting and investment casting are often better at controlling shrinkage. Die casting, for example, uses high pressure to inject molten metal into a mold, which results in less shrinkage because the metal is forced into the mold quickly and under pressure. This method is often used for high-volume production of smaller, more precise parts.
On the other hand, investment casting allows for more intricate designs and tighter tolerances. It’s commonly used in industries like aerospace, where dimensional accuracy is critical. This method typically results in less shrinkage because the mold is made from a ceramic shell that can withstand higher temperatures, reducing the risk of metal contraction during solidification.
However, sand casting remains a valuable method, especially for larger parts or those that don’t require the ultra-precise tolerances of die or investment casting. By using the right techniques, sand casting can achieve good control over shrinkage, although it requires more careful design and process management.
Table 14: Comparison of Shrinkage Control Across Casting Methods
Casting Method | Shrinkage Control | Ideal Use Case |
---|---|---|
Sand Casting | Moderate control | Larger parts, cost-effective production |
Die Casting | High control, minimal shrinkage | High-volume production of smaller parts |
Investment Casting | Very high control | Parts requiring high precision and fine details |
15. What Are the Best Practices for Minimizing Shrinkage in Sand Casting?
Minimizing shrinkage in sand casting requires a combination of careful design, material selection, and process optimization. To get started, ensure that your mold design is optimized to promote uniform cooling. This includes properly placing risers and gating systems to direct molten metal flow efficiently and avoiding turbulent flow that could lead to defects.
But here’s the kicker: Using higher-quality sand and ensuring that it is compacted properly can significantly reduce shrinkage. Sand with a finer grain size and appropriate moisture content can help control cooling rates and reduce thermal gradients within the mold.
Choosing the right alloy for your specific casting application is another important consideration. Alloys with a higher silicon content, for example, tend to shrink less, making them ideal for applications where dimensional accuracy is important. Additionally, adjusting the cooling rate and applying external cooling methods can help ensure that the aluminum solidifies evenly, further reducing shrinkage.
Lastly, ongoing process monitoring and adjustments based on real-time data can help improve the consistency and quality of the casting process. Using advanced simulation software and digital tools can help predict and manage shrinkage more effectively, ensuring that your aluminum castings meet the highest quality standards.
Table 15: Best Practices for Minimizing Shrinkage in Sand Casting
Best Practice | Impact on Shrinkage |
---|---|
Optimized mold design | Ensures uniform cooling |
High-quality sand | Reduces thermal gradients |
Use of higher silicon alloys | Minimizes shrinkage |
Cooling rate control | Ensures even solidification |
Conclusion
In conclusion, aluminum casting shrinkage is a significant challenge in sand casting, but it is one that can be managed with careful planning and the right techniques. By understanding the factors that contribute to shrinkage, such as alloy composition, mold design, and cooling rates, manufacturers can take proactive steps to minimize shrinkage and ensure high-quality castings.
From selecting the appropriate materials and alloys to optimizing mold design and using advanced technologies, there are several ways to reduce shrinkage and improve the overall quality of aluminum castings. By incorporating best practices into the casting process and utilizing modern tools for monitoring and measurement, manufacturers can produce precise, high-performance parts that meet the highest standards of quality.
FAQ Section
Q1: What is aluminum casting shrinkage?
Aluminum casting shrinkage refers to the reduction in volume as molten aluminum cools and solidifies, which can lead to dimensional inaccuracies in the final product.
Q2: How does shrinkage affect sand casting?
Shrinkage in sand casting can result in poor dimensional accuracy, surface imperfections, and can ultimately cause defects that require costly rework or scrapping of parts.
Q3: What factors contribute to shrinkage in aluminum castings?
Factors such as cooling rate, alloy composition, mold design, and the quality of the sand used all play significant roles in determining the amount of shrinkage in aluminum castings.
Q4: How can I prevent shrinkage defects in aluminum castings?
By optimizing mold design, controlling the cooling process, selecting the right alloy, and continuously monitoring the casting process, you can minimize shrinkage defects.
Q5: Are there advanced technologies that can reduce shrinkage in sand casting?
Yes, modern technologies such as improved mold materials, advanced cooling systems, and casting simulation software help reduce shrinkage and improve the quality of aluminum castings.