Aluminum gravity casting is a widely used manufacturing process that is highly favored for its efficiency and precision. It involves pouring molten aluminum into a mold, where it solidifies under the force of gravity. This method is popular for producing intricate parts with high dimensional accuracy and smooth surfaces. If you’re looking to understand the key aspects of aluminum gravity casting, this article will guide you through its process, advantages, applications, and much more.
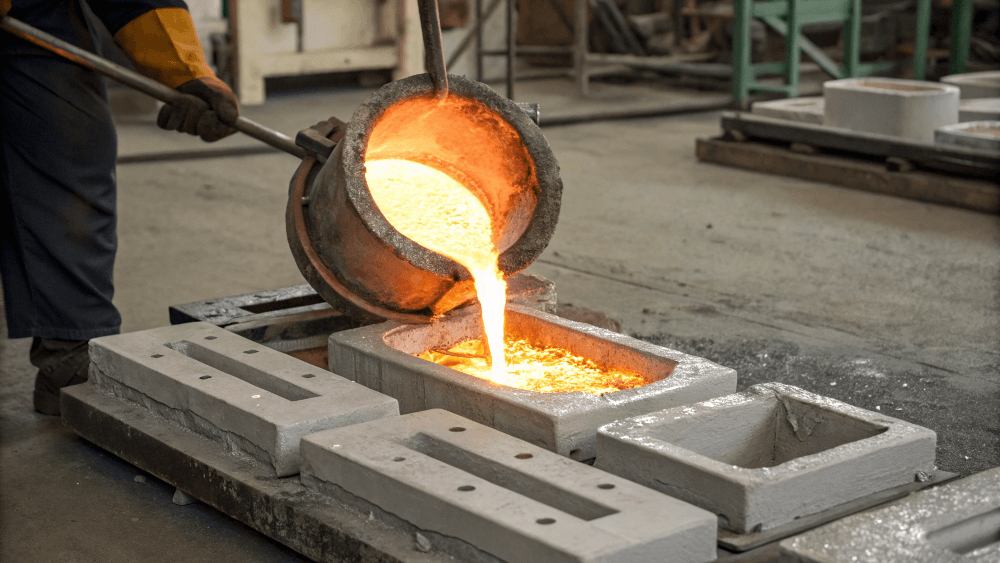
1. What is Aluminum Gravity Casting?
Aluminum gravity casting is a process where molten aluminum is poured into a mold under the influence of gravity. This method is highly favored due to its simplicity and cost-effectiveness, especially for producing large quantities of parts. Ready for the good part? This technique uses gravity as the sole force to fill the mold, which helps avoid the high pressure and speed seen in other casting methods like die casting.
This method is commonly used in a wide range of industries to produce parts with complex geometries that require high precision. Aluminum gravity casting is particularly popular in industries like automotive, aerospace, and electronics, where durability and accuracy are paramount. It can be used to produce components such as engine blocks, transmission cases, and other critical parts that demand high strength and excellent surface finish.
The main advantages of aluminum gravity casting include low production costs compared to other casting methods, the ability to produce parts with a high level of precision, and the capacity to handle high-volume production. Additionally, this process offers excellent surface finishes that are often required for parts that will be used in high-performance applications.
Aluminum gravity casting also allows for the use of different types of molds, including permanent molds made from steel, which are reusable and reduce the cost per part over time. The versatility and scalability of this method make it an attractive option for manufacturers seeking reliable and efficient production.
Table 1: Key Advantages of Aluminum Gravity Casting
Advantage | Description |
---|---|
Cost-effective | Lower setup and operational costs than other casting methods |
Precision | High dimensional accuracy for complex shapes |
Surface finish | Excellent surface quality ideal for high-performance parts |
2. How does Aluminum Gravity Casting Work?
The aluminum gravity casting process is simple but highly effective. What’s the real story? It involves melting aluminum and pouring it into a mold. The molten metal flows into the cavity of the mold, where it cools and solidifies, taking on the shape of the mold. Here’s how it works step-by-step:
- Preparing the Mold: The mold is created from metal or sand, and it is designed to match the exact shape of the part that needs to be produced. The mold is preheated to prevent the molten aluminum from cooling too quickly when it contacts the mold surface.
- Melting the Aluminum: Aluminum is melted in a furnace, reaching temperatures around 660°C (1220°F). The molten aluminum is carefully monitored for consistency in temperature and composition.
- Pouring the Aluminum: Once the aluminum reaches the desired temperature, it is poured into the mold. Gravity ensures that the molten metal fills the mold cavity completely. The speed of pouring and mold design are key factors in ensuring the final part is free of defects like air pockets or cold shuts.
- Cooling and Solidification: After the molten aluminum fills the mold, it is left to cool and solidify. This cooling process can take several minutes to an hour depending on the thickness of the part and the material used.
- Removing the Cast: Once the part has cooled and solidified, the mold is removed, and the part is extracted. If necessary, the cast part may undergo post-casting operations such as trimming, surface finishing, or heat treatment.
Aluminum gravity casting is highly efficient, but it requires careful control of variables such as mold temperature, pouring temperature, and cooling time to ensure the best results.
Table 2: Key Steps in Aluminum Gravity Casting
Step | Description |
---|---|
Mold preparation | Create and preheat the mold to match part shape |
Melting aluminum | Heat aluminum to a molten state |
Pouring | Pour molten aluminum into the mold |
Cooling | Allow the aluminum to cool and solidify |
Extraction | Remove the cast part and perform post-processing |
3. What are the Advantages of Aluminum Gravity Casting?
Aluminum gravity casting offers numerous advantages, making it one of the most popular methods in various industries. Here’s the kicker… It combines cost-effectiveness, precision, and versatility in a way that few other casting methods can match. Let’s take a closer look at some of the key benefits:
- Cost-Effective Production: One of the biggest advantages of aluminum gravity casting is its affordability. The cost of production is relatively low, especially when compared to more complex methods like die casting. Additionally, aluminum is a cost-effective material, which further reduces the overall production cost.
- High Precision: Aluminum gravity casting allows for the production of parts with high precision and tight tolerances. The use of gravity to fill the mold ensures that the molten aluminum is evenly distributed, reducing the likelihood of defects. This makes it ideal for parts that require exact measurements, such as engine components or complex brackets.
- Strong Surface Finish: The aluminum gravity casting process produces parts with a smooth surface finish. This is particularly important for parts that will be used in high-performance applications, where surface defects could affect the part’s functionality. The smooth surface also reduces the need for additional finishing processes.
- Ability to Handle Complex Geometries: This casting method can be used to produce complex parts that would be difficult to manufacture using other methods. Aluminum gravity casting can create intricate shapes with internal features, such as hollow cores, which are commonly needed in automotive and aerospace applications.
- Reusability of Molds: Permanent molds made of steel or other durable materials can be reused multiple times. This reduces the cost of producing multiple parts and increases efficiency in high-volume production runs.
In conclusion, aluminum gravity casting provides manufacturers with a combination of cost-efficiency, precision, and versatility that makes it a go-to choice for producing a wide range of high-quality parts.
Table 3: Advantages of Aluminum Gravity Casting
Advantage | Description |
---|---|
Cost-effective | Lower production costs due to reusability of molds |
High precision | Accurate parts with tight tolerances |
Smooth surface finish | Reduced need for additional finishing processes |
4. What Are the Applications of Aluminum Gravity Casting?
Aluminum gravity casting is used in a variety of industries, including automotive, aerospace, and electronics. Ready for the good part? Let’s explore how different industries benefit from aluminum gravity casting.
- Automotive Industry: Aluminum gravity casting is widely used in the automotive industry for manufacturing engine components, transmission cases, and other structural parts. The high strength-to-weight ratio of aluminum makes it ideal for reducing the overall weight of vehicles while maintaining durability.
- Aerospace Industry: In aerospace, aluminum gravity casting is used to produce parts like turbine blades, landing gear components, and structural frames. The high precision required in aerospace applications makes aluminum gravity casting a preferred choice for these critical components.
- Electronics Industry: The electronics industry relies on aluminum gravity casting for producing parts such as housings for electronic devices and components that require thermal management. The excellent thermal conductivity of aluminum makes it ideal for dissipating heat in electronic equipment.
- Marine Industry: Aluminum gravity casting is used to manufacture parts for the marine industry, including propellers, hull components, and engine components. The resistance to corrosion in saltwater environments is a key advantage of aluminum in marine applications.
Aluminum gravity casting’s ability to handle complex shapes and its superior surface finish make it ideal for a wide range of applications. Its versatility ensures that it continues to be a popular choice for industries that require strong, lightweight, and precision-cast components.
Table 4: Key Applications of Aluminum Gravity Casting
Industry | Common Applications |
---|---|
Automotive | Engine blocks, transmission cases, structural parts |
Aerospace | Turbine blades, landing gear, structural components |
Electronics | Housings, heat dissipation parts |
Marine | Propellers, hull components, engine parts |
5. What is the Difference Between Gravity Casting and Other Casting Methods?
Aluminum gravity casting is often compared to other casting methods like die casting and sand casting. What’s the real story? Let’s break down the differences between these methods to understand when each one is best used.
- Gravity Casting vs. Die Casting: The main difference between gravity casting and die casting lies in the way the molten aluminum is poured into the mold. In gravity casting, the metal is poured into the mold using only gravity, while in die casting, high pressure is used to force the molten metal into the mold. Die casting typically provides a higher level of precision but at a higher cost due to the need for specialized equipment and the use of pressure.
- Gravity Casting vs. Sand Casting: Sand casting uses a mold made from sand, which is then packed around the pattern of the part to be cast. This method is ideal for large parts but is not as precise as gravity casting. Gravity casting, on the other hand, uses permanent molds made of metal, offering better dimensional accuracy and smoother surface finishes.
- Gravity Casting vs. Investment Casting: Investment casting, also known as lost-wax casting, is used for parts that require very high precision and complex geometries. It involves coating a wax pattern with a ceramic shell, melting the wax, and pouring molten metal into the shell. Investment casting is more expensive than gravity casting but provides superior detail and surface finish.
Understanding the differences between these casting methods is crucial when deciding which one to use for a particular project. The choice depends on factors such as the required precision, cost, material properties, and production volume.
Table 5: Comparison of Casting Methods
Casting Method | Description | Precision | Cost | Best for |
---|---|---|---|---|
Gravity Casting | Uses gravity to fill the mold | High | Low | High-volume production, automotive |
Die Casting | Uses pressure to fill the mold | Very High | High | Complex parts, high precision |
Sand Casting | Uses sand molds | Medium | Low | Large parts, simple shapes |
Investment Casting | Uses a wax pattern and ceramic mold | Very High | Very High | Detailed, small parts |
6. What Materials Are Best for Aluminum Gravity Casting?
Choosing the right material for aluminum gravity casting is essential to ensuring the final product performs well in its intended application. But here’s the kicker… The material you select influences the strength, durability, and overall quality of the cast part. Let’s explore which materials are best suited for aluminum gravity casting.
- Aluminum Alloys: Various aluminum alloys can be used in gravity casting, with each offering different properties. The most commonly used alloys include:
- A356: This alloy is known for its excellent casting properties, high strength, and good corrosion resistance.
- A380: A widely used alloy in die casting, A380 is also used in gravity casting for its excellent fluidity and good mechanical properties.
- LM6: LM6 is a high-performance alloy used for applications that require excellent corrosion resistance, such as marine environments.
- Magnesium-Aluminum Alloys: These alloys combine the lightweight properties of magnesium with the strength and durability of aluminum. They are often used in automotive and aerospace applications where weight reduction is a critical factor.
- Aluminum-Silicon Alloys: These alloys are commonly used in aluminum gravity casting due to their excellent fluidity, high wear resistance, and low shrinkage. They are ideal for producing parts with intricate shapes.
Choosing the right material depends on the specific requirements of the casting, such as strength, weight, and corrosion resistance. A proper selection ensures that the final product meets the performance standards of the application.
Table 6: Common Aluminum Alloys Used in Gravity Casting
Alloy | Properties | Common Applications |
---|---|---|
A356 | High strength, excellent corrosion resistance | Automotive components, aerospace parts |
A380 | Excellent fluidity, good mechanical properties | Automotive, electrical housings, transmission cases |
LM6 | High corrosion resistance, excellent casting fluidity | Marine environments, engine parts, offshore components |
Magnesium-Aluminum Alloys | Lightweight, strong, durable | Aerospace, automotive (lightweight parts) |
Aluminum-Silicon Alloys | High wear resistance, low shrinkage, excellent fluidity | Parts requiring complex shapes, automotive engine components |
By carefully selecting the right alloy, manufacturers can ensure that their aluminum gravity castings are tailored to meet the specific demands of the application, whether it’s for strength, weight reduction, or corrosion resistance.
7. How to Set Up a Successful Aluminum Gravity Casting Operation?
Setting up a successful aluminum gravity casting operation requires careful planning and consideration of various factors. Here’s the deal… The setup process involves everything from selecting the right equipment to ensuring that the production flow is smooth and efficient. Below are key steps in setting up your operation:
- Selecting the Right Equipment: Choosing the correct machinery for aluminum gravity casting is critical for the quality of the finished product. The basic equipment needed includes a furnace to melt the aluminum, mold-making equipment, a pouring system, and cooling stations. Each piece of equipment must be capable of handling the temperatures and volumes required for aluminum casting.
- Mold Design and Materials: A successful operation begins with a good mold. The design of the mold must account for the shape, dimensions, and material properties of the aluminum part being cast. Molds made from durable materials like steel or iron are common in gravity casting. These molds are reusable and capable of withstanding high temperatures without warping or degradation.
- Temperature Control: Maintaining proper temperature control is vital for achieving consistent quality in the cast parts. Both the aluminum and the mold must be heated to the correct temperatures before pouring the molten aluminum. Temperature fluctuations can cause defects like cold shuts, porosity, or weak spots in the final product.
- Skilled Workforce: Having a skilled workforce is crucial. Operators must be trained in all aspects of the casting process, from mold preparation to monitoring the molten metal temperature and pouring it accurately. Proper training reduces errors and ensures that the parts produced meet required specifications.
- Post-Casting Operations: After the aluminum has cooled and solidified, post-casting processes such as trimming, finishing, and quality inspection are necessary. These operations ensure that any excess material is removed and that the part meets the desired surface finish and dimensional accuracy.
The key to success in aluminum gravity casting lies in ensuring that each step is carefully managed, from mold design to post-casting inspections. By investing in the right equipment and workforce, manufacturers can achieve optimal results.
Table 7: Key Steps in Setting Up Aluminum Gravity Casting
Step | Description |
---|---|
Selecting Equipment | Choose the right furnace, mold-making tools, and pouring system |
Mold Design | Design molds that can withstand high temperatures and ensure dimensional accuracy |
Temperature Control | Maintain consistent temperatures for both aluminum and molds to prevent defects |
Skilled Workforce | Train workers on proper casting techniques to minimize errors |
Post-Casting Operations | Perform trimming, finishing, and quality control checks to ensure part accuracy |
8. What Are the Costs Involved in Aluminum Gravity Casting?
The costs of aluminum gravity casting can vary depending on factors such as mold material, production volume, and part complexity. What’s the real story? Understanding the cost structure is important for manufacturers to determine whether this process is the right fit for their needs. Let’s break down the key cost components involved in aluminum gravity casting:
- Initial Setup Costs: Setting up an aluminum gravity casting operation requires significant initial investment. This includes purchasing the necessary equipment like furnaces, pouring systems, and mold-making tools. Depending on the scale of the operation, this initial cost can be substantial.
- Mold Costs: The cost of creating molds is another significant expense. Steel and iron molds are commonly used because they are durable and reusable. While these molds are more expensive than sand molds, their ability to withstand multiple uses over time makes them more cost-effective in the long run.
- Material Costs: Aluminum is the primary material used in gravity casting. The cost of aluminum can fluctuate based on market conditions, so manufacturers need to account for this when calculating production costs. Additionally, the use of specific aluminum alloys can add to the cost, depending on the alloy’s properties.
- Operational Costs: Once the operation is set up, the ongoing costs include energy to power the furnace, labor costs, and maintenance of equipment. These costs can be minimized by optimizing the production process, such as reducing energy consumption and improving production efficiency.
- Post-Casting Costs: After the casting is complete, there are additional costs for post-casting operations such as trimming, finishing, and quality control. These processes ensure that the final product meets the required specifications, but they also add to the overall cost of production.
By carefully managing these costs, manufacturers can ensure that aluminum gravity casting remains a cost-effective method for producing high-quality parts, especially in high-volume production.
Table 8: Cost Breakdown of Aluminum Gravity Casting
Cost Component | Description |
---|---|
Initial Setup | Investment in equipment such as furnaces and molds |
Mold Costs | Costs of creating and maintaining durable, reusable molds |
Material Costs | Price of aluminum and any alloys used in casting |
Operational Costs | Costs for energy, labor, and equipment maintenance |
Post-Casting Costs | Expenses for trimming, finishing, and quality control |
9. What Are the Challenges in Aluminum Gravity Casting?
Like any manufacturing process, aluminum gravity casting comes with its own set of challenges. This is where it gets interesting… While it’s known for its precision and cost-effectiveness, manufacturers must navigate several potential obstacles to achieve consistent, high-quality results.
- Defects in Castings: One of the most common issues in aluminum gravity casting is the formation of defects such as porosity, cold shuts, or misruns. These defects can occur if the molten aluminum does not fill the mold correctly or cools too quickly. To mitigate this, it’s important to control the pouring speed, mold temperature, and aluminum temperature.
- Mold Wear: Over time, molds used in gravity casting can experience wear and tear due to the high temperatures and pressure involved in the process. This can lead to dimensional inaccuracies or surface defects. Regular maintenance and proper mold design can reduce the frequency of mold replacement.
- Temperature Control: Maintaining consistent temperature is crucial for ensuring the quality of the casting. Fluctuations in temperature can lead to defects like shrinkage or cracking. Effective temperature control during the melting, pouring, and cooling phases is essential to produce high-quality castings.
- Material Variability: The quality of aluminum alloys can vary, and impurities in the material can lead to defects in the final product. Proper material sourcing and quality control are necessary to avoid these issues. Manufacturers need to ensure that the aluminum used meets the required standards for strength, durability, and surface finish.
- High Setup Costs: While the operational costs of aluminum gravity casting can be low, the initial setup costs for equipment and molds can be high. This may be a barrier for smaller manufacturers or companies looking to produce small volumes of parts. However, for high-volume production, the cost per part decreases significantly over time.
By addressing these challenges with careful planning, training, and quality control measures, manufacturers can optimize their aluminum gravity casting processes for better results.
Table 9: Common Challenges in Aluminum Gravity Casting
Challenge | Description |
---|---|
Defects in Castings | Issues like porosity and cold shuts due to pouring problems |
Mold Wear | Mold degradation over time affecting part accuracy |
Temperature Control | Inconsistent temperatures causing defects |
Material Variability | Impurities in aluminum leading to quality issues |
High Setup Costs | Significant initial investment for equipment and molds |
10. How Does Aluminum Gravity Casting Ensure High-Quality Products?
The key to ensuring high-quality products in aluminum gravity casting lies in maintaining strict control over the process. What’s the real story? It’s about precision, consistency, and attention to detail at every step of the casting process.
- Accurate Mold Design: The mold is the foundation of the casting process. A well-designed mold ensures that the aluminum flows evenly into the cavity, reducing the risk of defects. Modern mold design software allows manufacturers to simulate the casting process and optimize mold geometry before production begins.
- Temperature Management: Proper temperature management throughout the casting process is crucial for achieving high-quality results. By controlling the temperature of the molten aluminum, mold, and cooling process, manufacturers can avoid issues like shrinkage, cracks, or surface defects.
- Post-Casting Inspections: After the aluminum part has solidified, post-casting operations such as visual inspection, dimensional checks, and surface finish evaluations are performed. These inspections ensure that the part meets the required quality standards and any defects are identified and addressed before the part is delivered.
- Quality Control Systems: Many manufacturers implement automated quality control systems to monitor the casting process in real-time. These systems use sensors and cameras to detect potential issues during the casting, allowing for immediate corrections.
- Use of High-Quality Materials: The use of high-quality aluminum alloys is another factor that ensures the final product is strong, durable, and performs well under stress. By selecting the right materials and ensuring their quality through rigorous testing, manufacturers can produce high-quality castings that meet or exceed industry standards.
By integrating these quality control measures throughout the process, aluminum gravity casting ensures that the final product is both precise and reliable.
Table 10: Quality Control Measures in Aluminum Gravity Casting
Control Measure | Description |
---|---|
Accurate Mold Design | Use of simulation software and optimal mold geometry |
Temperature Management | Control of molten aluminum, mold, and cooling temperatures |
Post-Casting Inspections | Visual, dimensional, and surface inspections after casting |
Automated Quality Control | Real-time monitoring of the casting process with sensors |
High-Quality Materials | Ensuring the use of high-grade aluminum alloys for durability |
11. What is the Role of Temperature in Aluminum Gravity Casting?
Temperature control plays a crucial role in the aluminum gravity casting process. Here’s the deal… Both the molten aluminum and the mold need to be at specific temperatures for the casting to be successful. Let’s explore the role temperature plays in producing high-quality castings.
- Melting Temperature: The aluminum must be heated to its melting point, which is around 660°C (1220°F). If the aluminum is not sufficiently melted, it will not flow into the mold correctly, resulting in an incomplete or defective casting.
- Mold Temperature: The temperature of the mold is just as important as the molten aluminum. If the mold is too cold, the molten metal will cool too quickly, leading to incomplete filling or cold shuts. If the mold is too hot, the aluminum may solidify too early, causing defects in the casting.
- Cooling Rate: After the molten aluminum fills the mold, it needs to cool and solidify. The cooling rate is carefully controlled to avoid issues like cracking or shrinkage. Cooling is typically done at a steady, controlled rate to ensure uniform solidification.
By maintaining optimal temperatures throughout the casting process, manufacturers can reduce defects and improve the overall quality of the cast part.
Table 11: Temperature Control in Aluminum Gravity Casting
Temperature Type | Optimal Range | Impact on Casting |
---|---|---|
Melting Temperature | 660°C (1220°F) | Ensures complete melting of aluminum |
Mold Temperature | 150°C – 250°C | Prevents premature cooling and cold shuts |
Cooling Rate | Controlled and gradual | Prevents cracks and shrinkage in the cast part |
12. How Do You Optimize Aluminum Gravity Casting for Efficiency?
Optimizing aluminum gravity casting for maximum efficiency is key to ensuring both high-quality results and cost-effectiveness. This is where it gets interesting… There are several strategies you can implement to improve efficiency in the casting process while maintaining the desired quality of the cast parts. Let’s dive into these strategies:
- Mold Design Optimization: The design of the mold plays a critical role in ensuring efficient casting. A well-designed mold not only ensures that the molten aluminum flows smoothly into the cavity but also helps in maintaining the correct cooling rate. Optimized mold designs can reduce the risk of defects, like misruns or cold shuts, and can lead to faster and more consistent production.
- Automation: Automating the casting process can significantly improve efficiency. By using automated systems for tasks like mold preparation, molten metal pouring, and quality inspections, manufacturers can reduce human error and increase the speed of production. Automation can also help in maintaining consistency, which is essential for producing high-quality parts.
- Temperature Control Systems: Implementing advanced temperature control systems can improve efficiency in aluminum gravity casting. These systems monitor and control the temperature of both the molten metal and the mold to ensure that they remain within optimal ranges. This reduces the chances of defects caused by temperature fluctuations and increases the overall throughput of the casting process.
- Efficient Cooling Systems: Cooling is a crucial phase of aluminum gravity casting. By using advanced cooling techniques, such as forced air or water-cooling systems, manufacturers can reduce the cooling time, which in turn speeds up production. Optimized cooling systems also help ensure the quality of the castings by preventing thermal gradients and uneven solidification.
- Streamlined Post-Casting Operations: Post-casting operations, such as trimming, finishing, and quality inspection, can be time-consuming. By streamlining these operations with automated trimming and more efficient finishing processes, manufacturers can cut down on production time. Additionally, advanced inspection technologies, like in-line sensors or automated visual inspection systems, can speed up the quality control process and reduce labor costs.
By focusing on these strategies, manufacturers can achieve a more efficient aluminum gravity casting process, ultimately lowering costs and increasing production volumes while maintaining high-quality standards.
Table 12: Optimization Strategies for Aluminum Gravity Casting
Optimization Strategy | Description |
---|---|
Mold Design Optimization | Improve flow and cooling rates by designing better molds |
Automation | Use automated systems for pouring, molding, and quality checks |
Temperature Control Systems | Monitor and control the temperature of the metal and mold |
Efficient Cooling Systems | Reduce cooling time using advanced forced-air or water-cooling systems |
Streamlined Post-Casting Operations | Use automation for trimming, finishing, and inspection processes |
13. What Are the Environmental Impacts of Aluminum Gravity Casting?
As with any industrial process, aluminum gravity casting has environmental implications. But here’s the kicker… With the growing push for sustainability in manufacturing, it’s crucial for manufacturers to adopt practices that minimize the environmental impact of their operations. Let’s look at the environmental factors associated with aluminum gravity casting:
- Energy Consumption: Aluminum gravity casting requires significant energy to melt the aluminum, which can have a large carbon footprint depending on the energy source. However, using renewable energy sources or more energy-efficient furnaces can help reduce the environmental impact of this process.
- Waste Generation: The casting process generates waste in the form of scrap metal, defective castings, and excess material from post-casting processes like trimming and finishing. Recycling these materials is crucial for minimizing waste. Many manufacturers collect scrap aluminum and reprocess it for reuse in future casting operations.
- Water Use: Aluminum gravity casting often involves the use of cooling systems that rely on water, which can lead to high water consumption. Implementing water recycling systems can help reduce water usage and minimize environmental impact.
- Air Emissions: The process of melting aluminum can release pollutants such as carbon monoxide, volatile organic compounds (VOCs), and other emissions. Manufacturers can mitigate these emissions by installing filtration and ventilation systems to capture harmful gases before they are released into the atmosphere.
- Sustainable Practices: To minimize the environmental footprint, manufacturers can adopt sustainable practices, such as using recycled aluminum in their casting process, optimizing energy use, and reducing material waste. This not only benefits the environment but can also help reduce production costs in the long run.
By focusing on sustainability and minimizing environmental impact, aluminum gravity casting manufacturers can ensure that they meet environmental regulations while also contributing to the global effort for a cleaner, more sustainable manufacturing industry.
Table 13: Environmental Impact of Aluminum Gravity Casting
Environmental Impact | Description |
---|---|
Energy Consumption | High energy usage for melting aluminum; can be reduced with efficient furnaces and renewable energy |
Waste Generation | Scrap metal and defective castings, but recyclable for reuse |
Water Use | Significant water usage for cooling; recycling systems can help reduce this |
Air Emissions | Pollutants released during melting; can be minimized with filtration and ventilation |
Sustainable Practices | Using recycled materials and energy-efficient technologies to reduce environmental impact |
14. How Can You Improve the Durability of Aluminum Castings?
Aluminum gravity castings are known for their strength and durability, but there are several ways to enhance the longevity of the parts produced. This is where it gets interesting… Let’s look at how manufacturers can improve the durability of aluminum castings to ensure they perform well under challenging conditions.
- Choosing the Right Material: The choice of aluminum alloy has a significant impact on the durability of the final part. For example, alloys with higher silicon content, such as A356, offer better wear resistance and are ideal for applications involving high-stress components like engine blocks. Manufacturers should choose the appropriate alloy based on the mechanical properties required for the application.
- Heat Treatment: Heat treatment can improve the strength and hardness of aluminum castings. By subjecting the cast parts to processes like solution heat treatment and aging, manufacturers can increase the part’s resistance to deformation and fatigue. This is particularly important for aluminum castings used in automotive or aerospace applications.
- Surface Finishing: The surface finish of the casting also affects its durability. Parts with rough or uneven surfaces are more prone to wear and corrosion. Applying surface treatments like anodizing or coating can improve the corrosion resistance of aluminum castings, especially in harsh environments like marine or chemical applications.
- Design for Durability: The design of the part itself plays a critical role in its longevity. Components should be designed to withstand the forces and stresses they will encounter during their service life. Incorporating features like ribs for added strength or thicker sections in high-stress areas can improve the part’s overall durability.
- Regular Maintenance: To maintain the durability of aluminum castings over time, regular maintenance is essential. This includes inspecting parts for signs of wear, cleaning components, and replacing any damaged parts before they fail.
By implementing these techniques, manufacturers can produce aluminum gravity castings that are not only durable but also reliable for long-term use in demanding applications.
Table 14: Methods for Improving Durability of Aluminum Castings
Method | Description |
---|---|
Choosing the Right Material | Select aluminum alloys with higher wear resistance for strength |
Heat Treatment | Use solution heat treatment and aging to improve strength and hardness |
Surface Finishing | Apply coatings or anodizing to enhance corrosion resistance |
Design for Durability | Incorporate design features that enhance part strength and longevity |
Regular Maintenance | Perform inspections and maintenance to extend the part’s service life |
15. What are the Future Trends in Aluminum Gravity Casting?
The aluminum gravity casting industry is evolving, and you might be wondering what trends will shape its future. Technological advancements, new materials, and innovations in casting techniques are driving the future of aluminum gravity casting. Let’s explore some of these trends:
- Automation and Smart Manufacturing: As the demand for high-quality, high-volume production increases, manufacturers are turning to automation and smart technologies to improve the efficiency of their operations. Automation can help reduce the risk of human error, improve consistency, and increase production rates. Smart manufacturing technologies, such as sensors and real-time monitoring systems, can enhance quality control and allow manufacturers to optimize the casting process.
- Advanced Materials: Researchers are constantly developing new materials and alloys that can improve the performance of aluminum castings. For example, new aluminum alloys with improved strength, heat resistance, and wear resistance are being developed for use in demanding applications like electric vehicles and aerospace.
- Sustainability Innovations: With the growing demand for environmentally friendly manufacturing practices, aluminum gravity casting is becoming more sustainable. Manufacturers are exploring ways to reduce energy consumption, recycle aluminum scrap more efficiently, and use renewable energy sources in the casting process. Sustainability is becoming a key driver in the industry, and companies are embracing these practices to reduce their carbon footprint.
- 3D Printing and Additive Manufacturing: 3D printing and additive manufacturing technologies are being explored as complementary tools to aluminum gravity casting. These technologies allow manufacturers to create molds and patterns with high precision, reducing the time and cost associated with mold design. Additionally, 3D printing can be used to produce small-batch or customized aluminum castings.
- Customization and On-Demand Production: The demand for customized and on-demand production is growing. Manufacturers are looking for ways to produce smaller batches of highly customized aluminum castings without sacrificing efficiency or quality. This trend is driving innovations in both casting techniques and production methods.
In conclusion, the future of aluminum gravity casting looks promising, with new technologies and innovations that will improve efficiency, quality, and sustainability. Manufacturers who embrace these trends will be well-positioned to remain competitive in the evolving marketplace.
Table 15: Future Trends in Aluminum Gravity Casting
Trend | Description |
---|---|
Automation and Smart Manufacturing | Use of automation and real-time monitoring to improve efficiency and consistency |
Advanced Materials | Development of new alloys with improved performance characteristics |
Sustainability Innovations | Adoption of green technologies to reduce environmental impact |
3D Printing and Additive Manufacturing | Using 3D printing for mold production and customized parts |
Customization and On-Demand Production | Increasing demand for smaller, customized production runs |
FAQ Section
Q1: What is Aluminum Gravity Casting?
Aluminum gravity casting is a method of pouring molten aluminum into a mold under the influence of gravity to form a solidified part. It is known for its precision and cost-effectiveness.
Q2: How does Aluminum Gravity Casting work?
In this process, molten aluminum is poured into a mold using gravity. It fills the cavity, cools, and solidifies to take the shape of the mold, producing a part that meets specific dimensions and surface finishes.
Q3: What are the advantages of Aluminum Gravity Casting?
Aluminum gravity casting is cost-effective, produces parts with high precision, provides excellent surface finishes, and is ideal for producing complex parts in high volumes.
Q4: What are the key applications of Aluminum Gravity Casting?
It is widely used in the automotive, aerospace, electronics, and marine industries for making critical parts such as engine components, turbine blades, housings, and more.
Q5: How do I choose the right material for Aluminum Gravity Casting?
Choosing the right material depends on factors such as strength, weight, and corrosion resistance. Common materials include aluminum alloys like A356, A380, and LM6, which provide a balance of durability and performance.