Aluminum castings for structural applications offer numerous benefits across industries. From bridges to buildings, aluminum is a popular choice due to its strength, lightweight properties, and resistance to corrosion. In this article, we’ll explore the importance of aluminum castings for structural applications, how they are manufactured, and the wide range of benefits they bring to the table. Whether you’re in construction, architecture, or manufacturing, understanding how aluminum castings can enhance your projects is crucial. Let’s dive into the world of aluminum castings and see why they are the go-to material for durable and efficient structures.
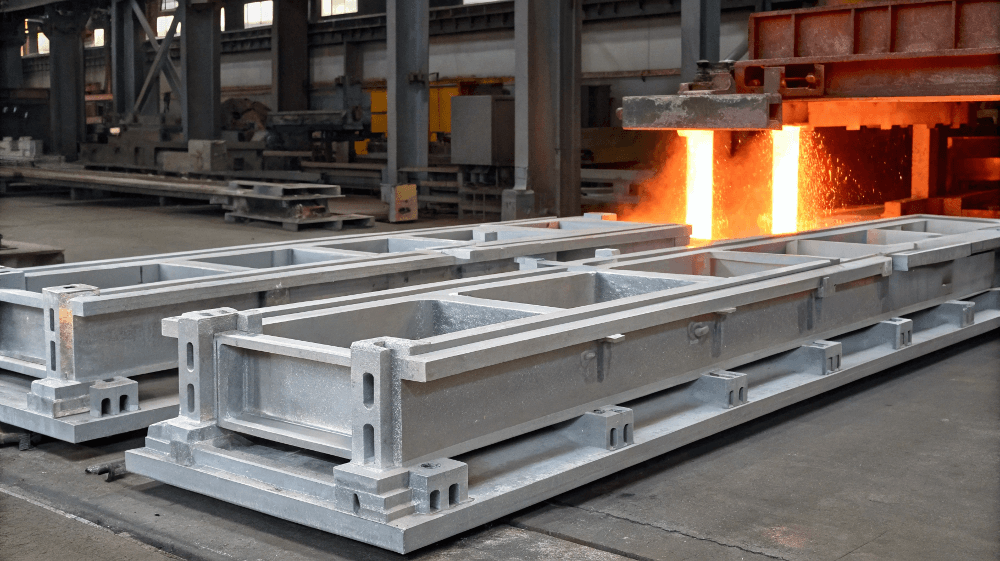
1. Why Are Aluminum Castings Important for Structural Applications?
Aluminum castings are critical in structural applications due to their unique combination of strength, weight, and durability. But here’s the kicker: when combined with the right casting techniques, aluminum can achieve performance levels that rival heavier materials like steel. Aluminum castings allow for the creation of lightweight, corrosion-resistant, and highly durable components. This makes them ideal for a variety of industries, including construction, aerospace, and transportation.
Aluminum’s versatility is one of the key reasons why it’s so commonly used in structural projects. Its low density reduces the overall weight of structures, which in turn decreases transportation costs and makes assembly easier. Moreover, aluminum is highly resistant to corrosion, meaning that structures made from aluminum castings require less maintenance and have a longer lifespan. In environments where metal fatigue is a concern, aluminum stands out as an excellent choice because it can withstand prolonged exposure to harsh conditions without significant degradation.
To put it simply, aluminum castings are essential for projects where weight, durability, and resistance to the elements are top priorities. Whether you’re constructing bridges, building facades, or structural components for airplanes, aluminum is a material you can count on.
Benefit | Explanation |
---|---|
Lightweight | Reduces transportation and handling costs. |
Durability | Resistant to corrosion, reducing the need for maintenance. |
Versatility | Used in a variety of industries, from aerospace to construction. |
2. What Are the Different Types of Aluminum Castings Used in Structures?
Aluminum casting techniques vary based on the complexity and requirements of the structure being built. Ready for the good part? Here’s a breakdown of the different types of aluminum castings that can be used in structural applications.
The three most common types of aluminum castings for structural applications are sand casting, die casting, and permanent mold casting. Sand casting is a popular choice for creating large, complex parts. It involves pouring molten aluminum into a mold made of sand, which is then removed to reveal the final product. This technique is highly flexible and can accommodate various shapes and sizes, making it ideal for custom structural components.
Die casting, on the other hand, is used for producing smaller, high-volume parts with precise dimensions. This method involves injecting molten aluminum under high pressure into a steel mold. Die-cast components are known for their accuracy and smooth surface finish, which makes them well-suited for applications where appearance matters, such as in architectural elements.
Permanent mold casting is similar to die casting but uses a reusable metal mold, which makes it more cost-effective for high-volume production. This technique is typically used for parts that require superior strength and durability, making it perfect for structural applications.
Casting Method | Key Features | Best Suited For |
---|---|---|
Sand Casting | Flexible, complex shapes | Custom components, large parts |
Die Casting | High precision, smooth finish | Small parts, high volume production |
Permanent Mold Casting | Reusable molds, cost-effective for large runs | High-strength structural parts |
3. How Does Aluminum Compare to Other Materials for Structural Applications?
When choosing materials for structural projects, it’s important to consider strength, weight, cost, and durability. But here’s where it gets interesting: aluminum often outperforms its competitors, such as steel and concrete, in several key areas. Aluminum’s strength-to-weight ratio is one of its most appealing qualities. It is significantly lighter than steel, which makes it easier to transport and install. This lightweight nature can also reduce the overall weight of a structure, which may lead to lower foundation costs.
Aluminum also has a natural resistance to corrosion, making it ideal for outdoor applications or environments where exposure to moisture is common. Unlike steel, aluminum does not rust, which gives it a longer lifespan with less maintenance required. Concrete, while strong, is heavy and may require additional support structures, increasing costs. Moreover, concrete is more susceptible to cracking over time, especially in extreme weather conditions.
When it comes to cost, aluminum is often more affordable than steel in terms of raw material costs. However, the cost of aluminum casting can vary depending on the complexity of the part and the casting process used.
Material | Strength | Weight | Corrosion Resistance | Cost |
---|---|---|---|---|
Aluminum | High strength-to-weight ratio | Lightweight | Excellent (does not rust) | Lower than steel in some cases |
Steel | High, but heavier | Heavy | Susceptible to rust | Higher than aluminum |
Concrete | Strong under compression | Heavy | Prone to cracking | Generally cheaper |
4. How Are Aluminum Castings Manufactured for Structural Use?
The manufacturing process of aluminum castings for structural use is highly detailed and requires precision. This is where the magic happens—because the right techniques ensure that the final product can meet the demanding requirements of structural applications. Aluminum casting starts with the selection of the proper alloy, which will determine the material’s final properties. Once the alloy is chosen, the casting process begins.
There are several stages in the aluminum casting process. First, a mold is created, typically from sand, metal, or another material depending on the casting method chosen. The aluminum is then heated to its molten state and poured into the mold. The molten aluminum fills the cavity of the mold, taking on the desired shape. After cooling, the casting is removed from the mold and undergoes finishing processes, such as cleaning, polishing, and sometimes machining, to achieve the precise dimensions and surface finish needed.
Quality control is an essential aspect of the manufacturing process. Each casting is carefully inspected for defects, such as cracks or porosity, and tested to ensure it meets the strength and durability requirements for structural use.
Casting Step | Description | Importance |
---|---|---|
Mold Creation | The first step in the casting process, where a mold is made. | Essential for shaping the part |
Molten Aluminum Pouring | Aluminum is poured into the mold to form the shape. | Key to achieving the final product’s shape |
Finishing | The casting is cleaned, polished, and machined if necessary. | Ensures precision and surface quality |
5. What Are the Key Benefits of Using Aluminum Castings in Structural Design?
Aluminum castings provide several advantages when used in structural design. What’s the real story? These benefits are not only technical—they can also affect project timelines and cost-efficiency. First, aluminum’s lightweight nature significantly reduces the weight of structural components. This makes it easier to transport, handle, and install parts, which can reduce labor and equipment costs. Additionally, aluminum castings provide a high level of flexibility in design. They can be molded into complex shapes that are difficult or impossible to achieve with other materials.
Another major benefit is the corrosion resistance of aluminum. Unlike steel, which can rust over time, aluminum forms a protective oxide layer that prevents further corrosion. This makes aluminum castings ideal for outdoor applications where exposure to the elements is common. For projects in coastal areas or regions with high humidity, this benefit alone can make a significant difference in the lifespan and maintenance costs of the structure.
Aluminum castings also offer better thermal conductivity compared to other metals, which makes them useful in environments where temperature regulation is important. This can be crucial for certain building designs, such as those in temperature-sensitive industries or for structures requiring energy efficiency.
Benefit | Explanation |
---|---|
Lightweight | Reduces handling and transportation costs. |
Corrosion Resistance | Aluminum doesn’t rust, offering better longevity. |
Flexibility in Design | Can be molded into complex shapes, reducing design limitations. |
6. How Do Aluminum Castings Contribute to Energy Efficiency in Structures?
Aluminum castings are an excellent choice for improving energy efficiency in structural applications. Here’s the deal: aluminum not only provides mechanical strength but also offers superior thermal conductivity and insulation, which are essential in creating energy-efficient buildings. Because aluminum is highly reflective, it can help reduce energy costs in structures by reflecting heat away from buildings in warmer climates. This can reduce cooling costs, especially when aluminum is used in roofing materials and exterior elements. Additionally, aluminum’s natural resistance to corrosion means less maintenance is needed over time, which contributes to the long-term energy efficiency of the structure.
Moreover, aluminum’s excellent ability to conduct heat can be leveraged in heating systems. For example, aluminum castings can be used in components for energy-efficient heating systems such as radiators, where their conductivity helps distribute warmth evenly throughout a building. This reduces the need for excessive energy consumption, contributing to a greener, more sustainable structure.
Another key factor is the recyclability of aluminum. Recycled aluminum requires only a fraction of the energy needed to produce new aluminum, making it an environmentally friendly material choice for energy-efficient buildings. The use of recycled aluminum castings in structural components further enhances the sustainability of the project.
Benefit | Explanation |
---|---|
Thermal Conductivity | Helps regulate temperatures and reduces energy consumption. |
Reflectivity | Reduces cooling costs by reflecting heat in warm climates. |
Recyclability | Aluminum can be recycled with minimal energy consumption. |
7. What Are the Common Applications of Aluminum Castings in Structural Projects?
Aluminum castings are used in a wide array of structural applications. Ready for the good part? Let’s explore the numerous industries where aluminum castings shine the brightest. One of the most common uses for aluminum castings in structural projects is in the construction of bridges. Aluminum is favored for bridge components like beams, supports, and connectors because of its lightweight properties and resistance to corrosion. This is particularly important in areas that experience extreme weather conditions, such as coastal or high-humidity regions.
Aluminum castings are also widely used in the aerospace industry, where lightweight materials are essential. Aircraft components, such as engine parts, landing gear, and structural supports, often rely on aluminum castings for their strength-to-weight ratio. The ability to cast complex shapes allows for the creation of lightweight yet strong components that contribute to the overall efficiency and safety of the aircraft.
Another critical application is in architectural design, where aluminum castings are used in facades, window frames, and other structural elements. These applications benefit from aluminum’s versatility, as it can be cast into intricate designs that add aesthetic value without compromising strength or durability.
Application | Industry | Benefits |
---|---|---|
Bridges | Civil Engineering | Lightweight, durable, corrosion-resistant components. |
Aerospace Components | Aerospace | High strength-to-weight ratio, precision castings. |
Architectural Design | Architecture/Construction | Intricate designs, strong, and durable for facades. |
8. How to Choose the Right Aluminum Casting for Your Structural Needs?
Choosing the right aluminum casting for your structural project is a critical decision that impacts both the design and performance of the final structure. What’s the real story? Let’s break it down: selecting the appropriate casting process depends on several factors, such as the complexity of the part, the required strength, and the overall project budget. For instance, if you’re working on a project that requires high precision and smooth surface finishes, die casting is likely your best option. On the other hand, if you need a cost-effective solution for large, complex parts, sand casting might be more suitable.
Size is another important consideration. Larger structural components, like beams and supports, may require sand casting due to its ability to create large molds. For smaller parts, such as those used in aerospace or automotive applications, permanent mold casting or die casting may be a better fit due to their ability to produce more detailed and precise parts.
When selecting aluminum alloys for casting, the specific mechanical properties needed for the project should be considered. Different aluminum alloys offer varying levels of strength, hardness, and resistance to corrosion, so it’s essential to choose an alloy that aligns with the requirements of the structure.
Casting Type | Best For | Key Features |
---|---|---|
Die Casting | High-precision, small parts | Accuracy, smooth surface finish |
Sand Casting | Large, complex components | Flexibility in design, cost-effective |
Permanent Mold Casting | High-volume production | Durability, good strength-to-weight ratio |
9. What Are the Challenges in Working with Aluminum Castings in Structural Projects?
While aluminum castings offer many advantages, there are challenges involved in working with them in structural projects. Here’s where it gets interesting: one of the main challenges in aluminum casting is dealing with complex designs. Unlike steel or concrete, aluminum is not as easy to shape or modify once the casting is complete. Therefore, it’s important to plan and design carefully to avoid costly revisions. Complex geometries or intricate details may require more time and specialized equipment, adding to the overall cost of the project.
Another challenge is ensuring the consistency and quality of the castings. Aluminum can be prone to defects such as porosity, cracks, and shrinkage during the casting process, which can affect the structural integrity of the final product. To mitigate these risks, it’s crucial to work with a skilled foundry that follows rigorous quality control processes and uses advanced technologies to monitor and address potential defects during production.
Handling and transporting large aluminum castings can also pose logistical challenges. Due to the weight of the parts and the precision required, careful handling and proper transportation methods must be implemented to avoid damage to the components before they are installed in the structure.
Challenge | Explanation |
---|---|
Complex Designs | Intricate shapes may require specialized equipment and time. |
Quality Control | Risks of porosity, cracks, and shrinkage can compromise quality. |
Logistics | Proper handling and transportation are crucial for large parts. |
10. How Can You Ensure Quality and Durability in Aluminum Castings for Structural Use?
Ensuring the quality and durability of aluminum castings for structural use involves a combination of selecting the right materials, working with experienced manufacturers, and employing stringent quality control measures. This is where it gets interesting: the first step in ensuring quality is choosing the right aluminum alloy for the project. Different alloys have varying levels of strength, durability, and corrosion resistance, so selecting one that aligns with the specific needs of the project is critical.
Once the alloy is chosen, the casting process must be carefully monitored to minimize defects. Advanced techniques such as X-ray inspection and ultrasonic testing can help identify internal flaws in the casting, ensuring that the parts meet the required strength and integrity standards. Additionally, post-casting treatments such as heat treatment, anodizing, or painting can enhance the durability and appearance of the castings, making them more resistant to environmental factors such as moisture and UV radiation.
Finally, it’s important to work with a reliable and experienced supplier who can provide high-quality castings that meet industry standards. Whether it’s through certifications or customer testimonials, it’s essential to verify that the manufacturer has a proven track record of delivering quality aluminum castings for structural applications.
Quality Measure | Explanation |
---|---|
Material Selection | Choosing the right alloy ensures the casting’s strength and resistance. |
Advanced Testing | Using technologies like X-ray inspection to detect internal flaws. |
Post-Casting Treatments | Heat treatments, anodizing, and painting improve durability. |
11. What Role Does Aluminum Casting Play in Sustainable Building Practices?
Aluminum casting plays a crucial role in sustainable building practices. You might be wondering: how does aluminum contribute to environmental sustainability? First, aluminum is highly recyclable. In fact, nearly 75% of all aluminum ever produced is still in use today, which helps reduce the environmental impact of new aluminum production. By using recycled aluminum for casting, structural projects can significantly lower their carbon footprint and promote sustainability.
Moreover, aluminum’s energy efficiency properties, such as its ability to reflect heat, can help reduce energy consumption in buildings. This, in turn, lowers the overall environmental impact of the structure. When combined with green building practices, such as using aluminum castings for energy-efficient windows, roofing, and structural elements, the benefits are magnified.
Finally, aluminum’s long lifespan reduces the need for repairs and replacements, further contributing to sustainability. Structures made with aluminum castings require less maintenance, meaning fewer resources are needed for upkeep.
Sustainability Benefit | Explanation |
---|---|
Recyclability | Aluminum can be recycled indefinitely with minimal energy input. |
Energy Efficiency | Reflective properties help reduce energy consumption in buildings. |
Durability | Long lifespan reduces the need for repairs and replacements. |
12. How Do Aluminum Castings Perform Under Extreme Weather Conditions?
Aluminum castings are known for their excellent performance under extreme weather conditions. What’s the real story? Aluminum’s resistance to both high and low temperatures makes it ideal for use in a variety of climates. Unlike other materials, such as steel, which can expand or contract significantly in response to temperature changes, aluminum maintains its shape and integrity under most weather conditions.
In cold climates, aluminum retains its strength and does not become brittle, making it suitable for use in regions that experience freezing temperatures. In hot climates, aluminum’s low coefficient of thermal expansion allows it to resist heat-related deformation. Furthermore, aluminum’s natural resistance to corrosion ensures that it will withstand the effects of moisture, humidity, and salt in coastal regions without deteriorating.
This makes aluminum an ideal material for structural applications in areas with extreme weather conditions, such as bridges, outdoor buildings, and coastal infrastructure.
Weather Condition | Aluminum Performance |
---|---|
Cold | Resists brittleness and maintains strength. |
Heat | Resists heat-induced deformation and retains structural integrity. |
Moisture/Coastal | Highly resistant to corrosion from salt and humidity. |
13. What Are the Future Trends in Aluminum Casting for Structural Applications?
Aluminum casting continues to evolve, and future trends point toward even more innovation in materials and manufacturing processes. Let’s take a look ahead: one of the key trends is the development of new aluminum alloys with enhanced properties. These alloys will offer improved strength, better resistance to high temperatures, and even better performance in extreme environments, which will expand the range of applications for aluminum castings.
Another trend is the increasing use of 3D printing and additive manufacturing in aluminum casting. This technology allows for the creation of more complex and intricate designs while reducing waste and production costs. As 3D printing technology advances, aluminum casting will become even more versatile and cost-effective.
Finally, the growing demand for sustainable building practices will continue to drive the use of aluminum castings, particularly in green construction projects. Aluminum’s recyclability and energy-efficient properties align perfectly with the goals of sustainable architecture and construction.
Trend | Impact on Aluminum Casting |
---|---|
New Alloys | Improved performance in extreme conditions and applications. |
3D Printing | Enables complex designs, reduces material waste, and cuts costs. |
Sustainability | Increased demand for energy-efficient and recyclable materials. |
14. What Are the Costs Involved in Using Aluminum Castings for Structural Applications?
The cost of aluminum castings can vary depending on several factors, such as the size, complexity, and volume of parts required. Here’s where it gets interesting: generally, aluminum castings are cost-effective compared to other materials like steel or concrete. The initial raw material costs for aluminum can be higher, but aluminum’s lightweight nature reduces transportation and handling costs, and its corrosion resistance results in lower maintenance costs over the long term.
For small parts or high-precision components, die casting may be the most cost-efficient option due to its ability to produce parts quickly and accurately. For larger, less complex parts, sand casting is often the most affordable option, although it may take longer to produce.
In the long run, the durability and low maintenance costs of aluminum castings can offset the initial investment. Additionally, the ability to recycle aluminum means that the environmental and financial costs of production are reduced over time.
Cost Factor | Explanation |
---|---|
Material Costs | Aluminum’s initial cost may be higher than steel or concrete. |
Transportation | Lightweight aluminum reduces transportation costs. |
Maintenance | Aluminum’s durability leads to lower long-term maintenance expenses. |
15. How Can You Find Reliable Suppliers for Aluminum Castings in Structural Projects?
Finding a reliable supplier for aluminum castings is essential for ensuring quality and performance in your structural projects. You might be wondering: how do you find the best suppliers? Start by looking for manufacturers with a proven track record of delivering high-quality castings that meet industry standards. Check their certifications and ask for customer references to verify their credibility.
It’s also important to consider the supplier’s expertise in producing castings for your specific type of application. Whether you’re working on a large infrastructure project or a smaller architectural component, you need a supplier that understands the unique requirements of your project. Moreover, reliable communication and fast lead times are essential for meeting deadlines and ensuring the timely delivery of parts.
Finally, working with a supplier that offers post-sale support, including warranty and replacement services, can help mitigate potential risks and ensure that you receive high-quality castings that perform as expected.
Supplier Factor | Explanation |
---|---|
Proven Track Record | Look for experienced suppliers with industry certifications. |
Expertise in Applications | Ensure the supplier understands your specific casting requirements. |
Communication and Support | Timely communication and post-sale services are critical. |
Conclusion
Aluminum castings for structural applications offer unmatched benefits in terms of strength, weight, durability, and cost-efficiency. Whether you’re building bridges, constructing buildings, or working in aerospace, aluminum castings provide the flexibility and reliability needed to meet the challenges of modern construction. By choosing the right casting method, material, and supplier, you can ensure that your project benefits from all that aluminum has to offer. As the industry moves toward more sustainable and energy-efficient solutions, aluminum castings will continue to play a pivotal role in shaping the future of structural design.
FAQ Section
Q1: What are aluminum castings for structural applications?
Aluminum castings are molded aluminum products used in structural applications like bridges, buildings, and aircraft components. These castings are highly durable, lightweight, and resistant to corrosion.
Q2: How does aluminum casting work?
In the aluminum casting process, molten aluminum is poured into a mold to form a specific shape. Once it cools, it solidifies into the desired structure, ready for use in construction or other applications.
Q3: Why should I use aluminum instead of steel or concrete for structural projects?
Aluminum is lightweight, corrosion-resistant, and cost-effective. It’s ideal for projects where weight reduction and durability are crucial. It outperforms steel and concrete in terms of long-term performance, especially in harsh environments.
Q4: How do aluminum castings contribute to energy efficiency?
Aluminum’s excellent thermal conductivity helps regulate temperatures more efficiently, making it a good choice for energy-efficient buildings and structures. Additionally, its insulating properties can contribute to reducing energy consumption in buildings.
Q5: What are the common challenges when using aluminum castings in structural applications?
Common challenges include handling complex designs, ensuring consistent quality, and managing transport and installation logistics for large aluminum components. However, these can be mitigated with careful planning and quality control.