Stainless steel castings are essential in many industries due to their strength, durability, and resistance to corrosion. But how does the casting process work, and why are these castings so critical?
Stainless steel castings offer a variety of benefits across industries. From aerospace to food processing, their durability and resistance make them a preferred choice. This article explores everything you need to know about stainless steel castings.
Understanding how stainless steel castings are made, why they are important, and how to choose the right materials and suppliers will help you in making informed decisions for your business. Keep reading to learn more!
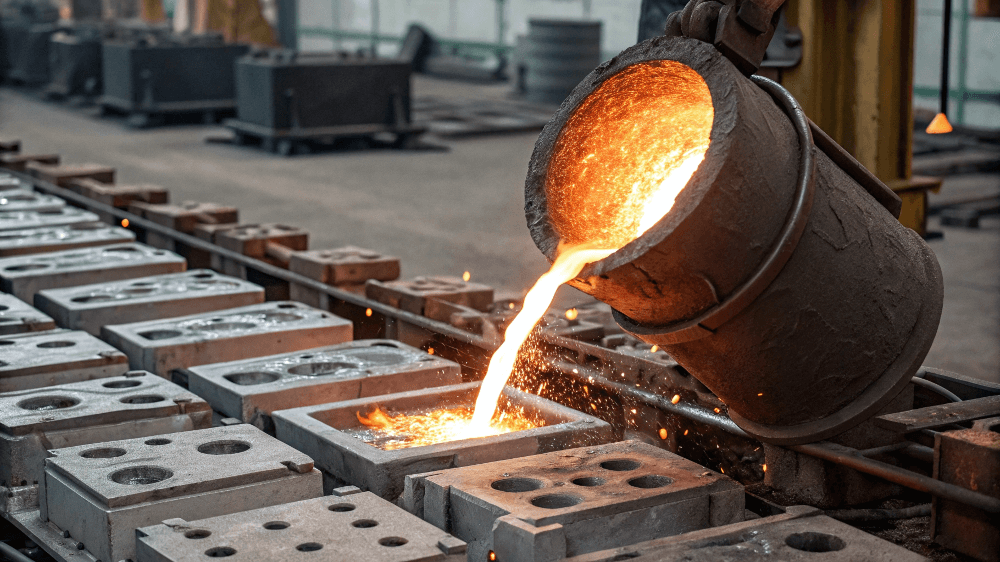
1. What Are Stainless Steel Castings?
Stainless steel castings have become an integral part of various manufacturing processes, and they are found in almost every major industry. But what exactly makes them so special? Let’s break it down.
Stainless steel casting is a process in which molten stainless steel is poured into molds to form complex shapes. It is known for its high strength, resistance to corrosion, and ability to withstand high temperatures. Castings are used in everything from automotive parts to industrial machinery.
Why are stainless steel castings so important?
They offer the flexibility to produce precise, durable parts that can endure harsh environments. Unlike forged parts, castings can have intricate designs, making them perfect for both simple and complex components.
Types of Stainless Steel Used for Castings
Stainless steel castings are available in several different types, each designed for specific applications. The most common include:
Type of Stainless Steel | Properties | Common Applications |
---|---|---|
Austenitic Stainless Steel | Excellent corrosion resistance | Food processing, marine |
Ferritic Stainless Steel | High-temperature resistance, magnetic | Automotive exhaust systems |
Martensitic Stainless Steel | Strong and wear-resistant | Cutting tools, industrial parts |
Benefits of Stainless Steel Castings
Stainless steel castings are favored for their unique properties such as:
- Corrosion resistance: Stainless steel is highly resistant to rust, making it ideal for use in marine or chemical industries.
- Strength: Castings made from stainless steel are durable and capable of withstanding extreme conditions.
- Flexibility in design: The casting process allows manufacturers to create parts with complex shapes that would be difficult to achieve with other methods.
2. Why Are Stainless Steel Castings Important?
Have you ever wondered why stainless steel castings are so critical in industries like aerospace, automotive, and construction? Let’s take a closer look at their key role.
Stainless steel castings play a vital role in manufacturing parts that require strength, precision, and durability. They are essential in a variety of industries, ensuring that the parts produced can withstand extreme conditions.
What makes stainless steel castings so useful?
They provide the perfect combination of strength, flexibility, and resistance to wear and tear. These characteristics make stainless steel castings ideal for high-performance applications like engine components, industrial equipment, and medical devices.
Applications of Stainless Steel Castings
Industry | Common Uses | Materials Used |
---|---|---|
Automotive | Engine parts, exhaust systems | 304, 316 stainless steel |
Aerospace | Turbine blades, structural components | 310, 410 stainless steel |
Medical | Surgical instruments, implants, prosthetics | 316L stainless steel |
Food Processing | Machines, equipment parts | 304, 316 stainless steel |
Benefits in Manufacturing
Stainless steel castings are incredibly versatile and provide multiple benefits to manufacturers. They allow for the creation of complex shapes and structures, providing manufacturers with a cost-effective solution that meets the requirements of various applications.
3. How Are Stainless Steel Castings Made?
Have you ever wondered how stainless steel turns into castings? Let’s dive into the process.
The process of stainless steel casting involves several stages, starting with creating molds and ending with quality inspection. This detailed process ensures that the parts produced are of the highest quality and precision.
Step-by-Step Process of Stainless Steel Casting
Step | Description |
---|---|
Pattern Making | Create a pattern that mirrors the final shape of the part. |
Mold Preparation | Place the pattern into a mold cavity and pack it with sand. |
Melting and Pouring | Melt the stainless steel in a furnace and pour it into the mold. |
Cooling and Solidification | Let the molten metal cool and solidify in the mold. |
Finishing | Break away the mold and clean the casted parts. |
Key Considerations in the Casting Process
- Mold quality: The quality of the mold directly impacts the final casting’s precision.
- Material choice: The right type of stainless steel must be selected for the intended application.
- Cooling time: Cooling time can affect the strength and durability of the final product.
Factors Affecting the Casting Process
Several factors can influence the success of a stainless steel casting project, including temperature, mold material, and cooling rates. Manufacturers must carefully control these variables to achieve the desired result.
4. What Types of Stainless Steel Are Used for Castings?
The choice of stainless steel plays a crucial role in the success of the casting. What types of stainless steel should you consider for your next casting project?
Stainless steel castings come in different grades, each designed for specific applications. Understanding the unique properties of each grade can help you select the right material for your needs.
Common Stainless Steel Grades Used in Castings
Grade | Properties | Common Uses |
---|---|---|
304 | Excellent corrosion resistance, easy to weld | Food processing, medical |
316 | Highly resistant to chlorides | Marine, chemical processing |
410 | Strong, wear-resistant | Valves, pumps |
2205 | Excellent strength and corrosion resistance | Oil & gas, chemical plants |
Choosing the Right Stainless Steel
The choice of material should be guided by factors like temperature resistance, corrosion exposure, and mechanical requirements. Stainless steel grades like 304 or 316 are common in industries that demand high corrosion resistance, such as food processing or marine.
5. What is the Stainless Steel Casting Process?
Now that we’ve covered the basics, let’s break down the actual casting process in more detail. How does molten stainless steel become a finished part?
The stainless steel casting process involves multiple stages, each of which must be performed with precision to ensure the highest quality product. Let’s look at each stage more closely.
Detailed Process of Stainless Steel Casting
Step | Description | Key Considerations |
---|---|---|
Pattern Making | A replica of the part is created in the desired material. | Material durability, design complexity |
Preparing the Mold | The pattern is placed in the mold cavity, and the mold is packed with sand. | Mold size, precision |
Melting the Stainless Steel | The stainless steel is melted in a furnace to a molten state. | Temperature control |
Pouring the Metal | Once molten, the steel is poured into the mold to form the shape. | Pouring speed, mold integrity |
Cooling and Solidification | The cast metal cools and solidifies to create the final part. | Cooling rate, mold type |
Finishing Touches | After solidification, the mold is broken away, and finishing processes like polishing are done. | Surface quality, inspection |
6. How Do Stainless Steel Castings Affect Product Durability?
Stainless steel castings are known for their excellent durability, but how exactly do they affect the longevity of a product? Let’s explore.
Stainless steel castings contribute significantly to product durability due to their corrosion resistance and high strength. These qualities make stainless steel castings ideal for parts that need to withstand harsh conditions such as extreme temperatures, chemicals, and wear.
How does durability differ across various applications?
The lifespan of stainless steel cast parts can vary based on factors like environmental exposure, the grade of stainless steel used, and the manufacturing process. Parts exposed to moisture or corrosive environments benefit greatly from stainless steel’s inherent resistance to rust and degradation.
Factors Affecting Durability
Factor | Description | Impact on Durability |
---|---|---|
Corrosion Resistance | Stainless steel’s ability to resist rust and corrosion. | Protects parts in humid or salty environments. |
Mechanical Strength | The strength of stainless steel at high temperatures and stress. | Enhances performance in industrial and aerospace applications. |
Finishing Processes | Post-casting treatments like polishing or coating. | Affects surface durability, reduces wear. |
How Durability Impacts Industries
- Automotive: Parts subjected to high mechanical stress benefit from stainless steel’s durability, ensuring long-lasting performance.
- Marine: Castings exposed to saltwater environments need high corrosion resistance, making stainless steel ideal for use in shipbuilding.
- Food Processing: Equipment needs to be durable and resistant to harsh cleaning chemicals, making stainless steel an excellent choice.
7. What Are the Common Applications of Stainless Steel Castings?
What makes stainless steel castings so useful across multiple industries? Let’s dive into the most common applications.
Stainless steel castings are used in a broad range of industries due to their versatility, strength, and ability to withstand harsh conditions. From aerospace components to food processing machinery, their applications are wide-reaching.
Where are these castings typically applied?
Stainless steel castings are used in high-performance environments that require strength, precision, and durability. This includes industries such as aerospace, automotive, medical, and manufacturing.
Applications in Various Industries
Industry | Common Uses | Material Grades |
---|---|---|
Aerospace | Turbine blades, structural components, fasteners | 310, 316 stainless steel |
Automotive | Engine blocks, pumps, exhaust systems | 304, 410 stainless steel |
Food Processing | Equipment parts, storage tanks | 304, 316 stainless steel |
Oil & Gas | Valves, pipe fittings, pressure vessels | 2205, 2507 duplex stainless steel |
Key Benefits in Applications
- Aerospace: Stainless steel castings help produce lightweight, durable components that can withstand extreme stress and temperatures.
- Medical Devices: Castings used in surgical instruments and implants provide the strength and biocompatibility needed for critical medical procedures.
- Oil & Gas: Castings for offshore platforms and pipelines need to endure the harshest environmental conditions, and stainless steel is the perfect material.
8. What Are the Challenges in Stainless Steel Casting?
Although stainless steel castings are a popular choice, they come with challenges. Let’s look at some of the key hurdles in the casting process.
While stainless steel castings offer many advantages, manufacturers often face challenges related to defects, material selection, and cost. These challenges can impact the overall quality of the product and increase production time and expenses.
What challenges should manufacturers be aware of?
Common issues such as porosity, cracking, and dimensional inaccuracies can occur during the casting process. However, these challenges can be managed with proper quality control, material selection, and casting techniques.
Common Issues in Stainless Steel Casting
Issue | Description | Solution |
---|---|---|
Porosity | Tiny holes or voids within the casting, caused by trapped gases. | Adjust pouring technique, use vacuum casting. |
Cracking | Cracks that form due to thermal stresses. | Control cooling rates, use appropriate alloys. |
Dimensional Inaccuracy | Parts that do not meet the desired dimensions. | Improve mold design, use precise measurement tools. |
How to Overcome These Challenges
- Quality Control: Regular inspections during the casting process can help identify defects early.
- Material Selection: Choosing the right stainless steel grade can prevent common casting problems.
- Skilled Workforce: Experienced technicians and engineers can troubleshoot and correct defects effectively.
9. How Do You Ensure Quality in Stainless Steel Castings?
Ensuring that stainless steel castings meet the required specifications is vital. What measures can be taken to guarantee quality?
Ensuring the quality of stainless steel castings is a multi-step process that requires strict adherence to standards and procedures. The entire production process, from design to finishing, must be closely monitored to ensure the highest quality products.
What practices should manufacturers adopt to ensure quality?
From raw material inspection to final product testing, each stage in the casting process contributes to the overall quality. Manufacturers must implement rigorous testing methods to confirm that castings meet the necessary mechanical and chemical properties.
Quality Control Measures
Measure | Description | Why It’s Important |
---|---|---|
Material Testing | Inspecting the raw stainless steel before casting. | Ensures the steel’s properties meet standards. |
Visual Inspection | Checking for surface defects and inconsistencies. | Detects issues like cracks or voids. |
Dimensional Testing | Measuring the final part to ensure proper fit. | Confirms that the casting matches specifications. |
Ensuring Compliance with Industry Standards
In industries where safety and precision are critical, like aerospace and medical, compliance with international standards (such as ASTM or ISO) ensures that stainless steel castings perform as expected.
10. What Are the Key Advantages of Stainless Steel Castings Over Other Materials?
Why should manufacturers choose stainless steel castings over other materials like aluminum or iron?
Stainless steel castings are preferred for their superior properties, including strength, corrosion resistance, and durability. They outperform many other materials in harsh environments, providing long-lasting performance.
What makes stainless steel a better choice than other materials?
Unlike aluminum or iron, stainless steel offers high resistance to corrosion, better high-temperature performance, and superior mechanical strength. This makes it ideal for critical applications like aerospace and industrial equipment.
Comparison of Stainless Steel with Other Materials
Material | Strength | Corrosion Resistance | Temperature Resistance | Weight |
---|---|---|---|---|
Stainless Steel | High | Excellent | High | Medium |
Aluminum | Moderate | Poor | Moderate | Light |
Iron | Moderate | Poor | Low | Heavy |
Where Stainless Steel Castings Excel
- Automotive: Stainless steel is durable, making it ideal for engine components and exhaust systems.
- Marine: The corrosion resistance of stainless steel makes it the best choice for ship parts exposed to seawater.
11. How is the Cost of Stainless Steel Castings Determined?
What factors influence the cost of stainless steel castings?
The cost of stainless steel castings is determined by various factors, including the material used, the complexity of the design, and the manufacturing process. Understanding these cost factors is essential for budget planning and sourcing decisions.
How can manufacturers manage casting costs effectively?
By selecting the right material, optimizing production processes, and managing waste, manufacturers can reduce costs while maintaining high-quality standards.
Key Factors in Cost Determination
Factor | Impact on Cost |
---|---|
Material Choice | High-grade stainless steel costs more than standard grades. |
Design Complexity | More intricate designs increase mold and finishing costs. |
Production Volume | Higher production volumes can reduce per-unit costs. |
Managing Casting Costs
- Material Optimization: Choosing the right grade of stainless steel can help reduce unnecessary expenses.
- Efficient Production: Streamlining the casting process to reduce waste and improve efficiency helps lower overall costs.
12. What Are the Environmental Considerations of Stainless Steel Castings?
As industries become more environmentally conscious, what are the environmental impacts of stainless steel casting, and how can they be mitigated?
Stainless steel casting, while offering many benefits, also has environmental considerations such as energy consumption, waste, and emissions. However, advancements in technology and sustainable practices are helping reduce these impacts.
What can manufacturers do to improve sustainability?
By adopting green manufacturing practices, using recycled materials, and reducing energy consumption, manufacturers can minimize the environmental footprint of stainless steel castings.
Sustainable Practices in Stainless Steel Casting
Practice | Description | Environmental Benefit |
---|---|---|
Recycling Materials | Reusing stainless steel scrap and casting waste. | Reduces material waste and energy consumption. |
Energy Efficiency | Implementing energy-efficient furnaces and equipment. | Lowers greenhouse gas emissions. |
Waste Management | Managing waste by recycling or reusing sand molds. | Reduces landfill waste and pollution. |
The Future of Sustainable Casting
As environmental regulations become stricter, manufacturers must innovate to reduce waste and energy consumption, ensuring that stainless steel casting remains a sustainable process for years to come.
13. How Do Stainless Steel Castings Compare to Other Manufacturing Techniques?
What makes stainless steel casting superior compared to forging, machining, or welding?
Stainless steel casting offers unique advantages over other manufacturing methods like forging and machining. It provides flexibility in design, precision, and cost-efficiency, especially for complex parts.
What makes casting stand out?
Casting allows manufacturers to produce complex shapes without the need for extensive machining, reducing labor costs and material waste. Moreover, castings are ideal for creating intricate parts that would be difficult to achieve with forging or welding.
Comparison of Casting with Other Techniques
Technique | Pros | Cons |
---|---|---|
Casting | High precision, low waste, complex shapes | Longer production times |
Forging | Stronger parts, fewer defects | Higher material costs, limited shapes |
Machining | High precision, flexibility | High material waste, costly |
Welding | Good for large parts, strong joints | Limited to specific shapes and sizes |
Choosing the Right Manufacturing Technique
Each technique has its strengths, but stainless steel casting remains the go-to choice for producing complex, durable parts efficiently.
14. What Are the Future Trends in Stainless Steel Casting?
What does the future hold for stainless steel castings?
The future of stainless steel casting looks promising, with advancements in technology pushing the limits of what is possible. Innovations in automation, 3D printing, and material science are expected to drive new applications and efficiencies.
How is the casting industry evolving?
New casting technologies and digital solutions are expected to reduce production times, improve quality, and minimize costs, making stainless steel castings even more competitive.
Emerging Trends in Stainless Steel Casting
Trend | Description |
---|---|
3D Printing | Using additive manufacturing to produce intricate parts with less waste. |
Automation | Increased use of robotics and AI in the casting process to improve efficiency and consistency. |
Advanced Materials | Developing new alloys and coatings to enhance performance in extreme conditions. |
Adapting to New Challenges
The stainless steel casting industry is poised for innovation, allowing manufacturers to meet evolving demands while maintaining high quality and performance.
15. How Can You Choose the Right Stainless Steel Casting Supplier?
Choosing the right supplier is crucial to ensuring quality and reliability. What should you look for when selecting a stainless steel casting supplier?
Selecting a reliable supplier is key to getting high-quality stainless steel castings delivered on time. You need to evaluate suppliers based on their experience, certifications, and ability to meet your specific requirements.
What makes a supplier stand out?
Look for a supplier who has experience in your industry, understands your needs, and offers transparent communication. Certifications and a track record of consistent delivery also indicate a reliable partner.
Key Factors in Selecting a Supplier
Factor | Description | Why It’s Important |
---|---|---|
Experience | Supplier’s experience in producing stainless steel castings. | Ensures understanding of specific industry needs. |
Certifications | ISO, ASTM, and other quality certifications. | Guarantees product quality and consistency. |
Customer Service | Supplier’s ability to respond to inquiries and address concerns. | Ensures smooth communication and reliability. |
Building a Long-Term Relationship with Your Supplier
Establishing a strong relationship with a stainless steel casting supplier can result in better pricing, reliability, and long-term business success.
Conclusion
Stainless steel castings are an essential part of many industries, offering strength, durability, and corrosion resistance. The casting process, though intricate, ensures that high-quality parts are produced to meet the needs of industries ranging from aerospace to food processing.
FAQ Section
Q5: How can I ensure the quality of stainless steel castings?
Ensuring quality involves inspecting the casting process, selecting the right materials, and adhering to strict quality control standards.
Q1: What is stainless steel casting?
Stainless steel casting is a process where molten stainless steel is poured into molds to form complex shapes and components.
Q2: How does the stainless steel casting process work?
The process involves creating a pattern, preparing the mold, melting and pouring the stainless steel, cooling, and finishing the part.
Q3: Why is stainless steel used for castings?
Stainless steel offers excellent corrosion resistance, strength, and durability, making it ideal for critical applications.
Q4: What are the benefits of stainless steel castings?
Stainless steel castings provide durability, resistance to corrosion, and the ability to create complex shapes, making them versatile in various industries.