In the world of manufacturing, stainless steel investment casting stands out as an invaluable method for producing complex and durable components. If you’ve ever faced challenges with precision, cost, or material durability, this process might be the solution you’re seeking.
Stainless steel investment casting offers precision and strength for various industries. It’s a reliable method to create intricate designs, ideal for demanding applications. This article will explore everything you need to know about stainless steel investment casting—from its definition to how it’s used in critical industries.
When it comes to producing high-quality stainless steel components, understanding the intricacies of investment casting can make all the difference. Let’s dive deeper into why this process is crucial and how it works.
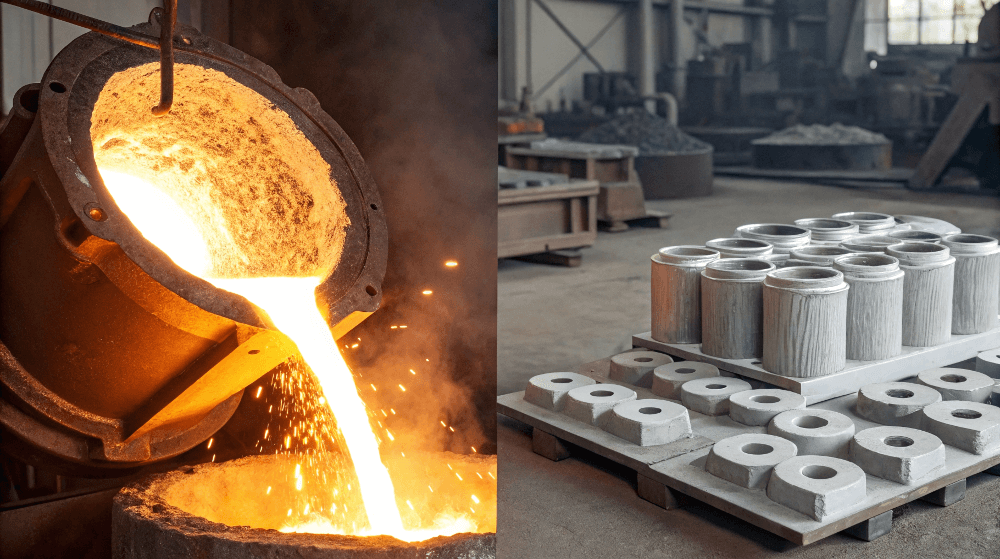
1. What is Stainless Steel Investment Casting?
Stainless steel investment casting is a highly accurate and cost-effective method used to create complex metal parts. If you’ve been struggling to create precision parts that require tight tolerances, this method could be your answer.
In stainless steel investment casting, molten metal is poured into a mold to form intricate components. The technique is known for producing parts with precise details and strength. It is widely used for creating parts in various industries such as aerospace, automotive, and medical devices.
Stainless steel investment casting has been around for centuries. Its flexibility in producing custom shapes and designs makes it an ideal choice for industries that require precision. The technique involves creating a mold from a pattern made of stainless steel, heating it to a liquid state, and then pouring it into the mold. The result is a part that has high dimensional accuracy and strength.
Types of Stainless Steel Used in Investment Casting
Type | Characteristics | Applications |
---|---|---|
Austenitic | High corrosion resistance, ductile | Food processing, medical equipment |
Ferritic | Good resistance to oxidation and corrosion | Automotive, appliances |
Martensitic | High strength, wear resistance | Aerospace, tooling |
2. Why is Stainless Steel Investment Casting Used?
Stainless steel investment casting is an ideal choice for producing complex shapes that other methods can’t match. It provides high precision and reliability, which is why it’s so popular in industries such as aerospace and medical device manufacturing.
Stainless steel’s versatility makes it ideal for casting. It offers durability, resistance to corrosion, and can withstand extreme temperatures. These characteristics make it a go-to material for creating parts that need to endure harsh environments or demanding operational conditions.
In addition to its versatility, stainless steel investment casting also allows manufacturers to reduce waste. Traditional casting methods require additional machining steps, which increase material usage. Investment casting minimizes this by creating more complex shapes directly, reducing the need for excess material.
Benefits of Stainless Steel Investment Casting
Benefit | Description | Impact on Manufacturing |
---|---|---|
Precision | High accuracy in part creation | Reduced need for post-machining |
Durability | Excellent resistance to corrosion and wear | Long-lasting, reliable components |
Cost-Efficiency | Minimal waste and efficient use of materials | Lower overall production costs |
3. How Does Stainless Steel Investment Casting Work?
Stainless steel investment casting involves several key stages. If you’ve been wondering how such precision is achieved, this section will explain the process in detail.
The process begins with creating a model or pattern from the stainless steel. This pattern is then coated in a fine material that hardens to form the mold. After the mold is prepared, molten stainless steel is poured into the mold, which is then cooled and solidified. Once the part cools, the mold is broken, revealing the cast component.
The entire process ensures that intricate designs can be reproduced with great accuracy. Stainless steel’s natural properties, such as strength and resistance to corrosion, further enhance the effectiveness of the casting. This method is also cost-effective, especially for high-volume production runs.
Stages of Stainless Steel Investment Casting
Stage | Description |
---|---|
Pattern Creation | Crafting the model, usually from wax or metal. |
Mold Creation | Coating the pattern with a fine material and hardening it. |
Pouring and Solidifying | Molten stainless steel is poured into the mold to form the part. |
Breaking the Mold | After cooling, the mold is broken to reveal the cast part. |
4. What Are the Benefits of Stainless Steel Investment Casting?
The benefits of stainless steel investment casting are numerous, particularly when it comes to precision and durability.
Precision is one of the key advantages. Stainless steel investment casting is capable of creating intricate parts with tight tolerances, reducing the need for additional machining. The material properties of stainless steel, such as corrosion resistance and strength, make it suitable for industries that demand long-lasting and durable components.
Another benefit of this casting method is the ability to create parts with minimal waste. Unlike other methods, investment casting allows manufacturers to create complex designs without the need for excessive material.
Comparing Benefits: Stainless Steel Investment Casting vs. Other Methods
Feature | Stainless Steel Investment Casting | Traditional Casting Methods |
---|---|---|
Precision | High, with minimal machining required | Moderate, requires more post-processing |
Material Waste | Minimal, high material efficiency | Higher, due to extra machining steps |
Durability | Excellent, resistant to corrosion and wear | Good, but less resistant |
5. What Are the Different Types of Stainless Steel Investment Castings?
Not all stainless steels are the same. Different types offer unique advantages depending on the intended application.
Austenitic stainless steel, for example, is known for its excellent corrosion resistance and is widely used in food processing and medical equipment. On the other hand, martensitic stainless steel provides high strength and wear resistance, which makes it a popular choice in the aerospace industry.
The type of stainless steel used in investment casting directly impacts the final product’s performance. Knowing which material to choose can help ensure the component meets specific requirements.
Comparison of Stainless Steel Types
Type | Properties | Best Uses |
---|---|---|
Austenitic | Excellent corrosion resistance, ductile | Medical, food processing |
Ferritic | Oxidation resistance, magnetic | Automotive, heating applications |
Martensitic | Strong, wear-resistant | Aerospace, tooling |
6. What Industries Benefit from Stainless Steel Investment Casting?
Stainless steel investment casting is used in several industries that require durable, precise, and reliable parts. Whether you’re in the aerospace, automotive, or medical sector, this casting technique offers multiple benefits that other methods can’t match.
Stainless steel’s strength, resistance to corrosion, and flexibility make it an ideal material for various high-performance applications. Industries such as aerospace and automotive depend on stainless steel investment casting for its ability to produce complex parts with high precision and low material waste.
For example, in the aerospace industry, investment casting is used to create turbine blades and other vital components. These parts need to withstand extreme temperatures and mechanical stresses. In the medical field, it’s used for making surgical tools, implants, and diagnostic devices, where precision and biocompatibility are essential.
Common Applications of Stainless Steel Investment Casting
Industry | Application Examples | Key Benefits |
---|---|---|
Aerospace | Turbine blades, structural components | High strength, temperature resistance |
Automotive | Engine components, exhaust systems | Durability, wear resistance |
Medical | Surgical tools, implants, diagnostic devices | Precision, biocompatibility |
Food Processing | Valves, pumps, food-grade equipment | Corrosion resistance, hygiene |
7. What Are the Key Challenges in Stainless Steel Investment Casting?
While stainless steel investment casting offers several advantages, it does come with its own set of challenges. Understanding these challenges can help manufacturers address potential issues before they arise.
One of the main challenges in stainless steel investment casting is controlling the temperature during the pouring process. If the molten metal is too hot or too cold, it can affect the quality of the cast, leading to defects such as cracking or porosity. Another challenge is the complexity of creating molds for intricate parts, which requires high precision.
Additionally, inconsistent material quality and defects in the casting process can result in product rejection, leading to increased costs. To mitigate these challenges, manufacturers must maintain strict quality control standards throughout the entire process.
Common Challenges in Stainless Steel Investment Casting
Challenge | Impact | Solutions |
---|---|---|
Temperature Control | Cracking or porosity in cast parts | Precise temperature monitoring |
Mold Complexity | Difficulty in producing intricate designs | High-precision mold making |
Material Quality | Inconsistent casting results | Rigorous material testing and selection |
Defects in Casting | Increased rejection rates | Continuous quality control checks |
8. How to Choose the Right Stainless Steel for Investment Casting?
Choosing the right type of stainless steel for investment casting is critical to ensuring that the final product meets performance and durability requirements. It depends on factors such as the intended application, environmental conditions, and mechanical stress the part will endure.
Factors such as strength, corrosion resistance, and ease of fabrication should be considered when selecting stainless steel. For high-corrosion environments, austenitic stainless steel is preferred. For high-strength applications, martensitic stainless steel is typically used. It’s essential to balance the material properties with the performance requirements of the final product.
Factors to Consider When Choosing Stainless Steel
Factor | Importance | Best Stainless Steel Choice |
---|---|---|
Strength | Need for high mechanical strength | Martensitic stainless steel |
Corrosion Resistance | Resistance to environmental degradation | Austenitic stainless steel |
Fabrication Ease | Ease of processing and forming parts | Ferritic stainless steel |
Cost Efficiency | Balancing performance and cost | Mixed stainless steel grades |
9. What Are the Costs Associated with Stainless Steel Investment Casting?
The costs of stainless steel investment casting can vary depending on several factors, including the complexity of the part, material choice, and production volume. While investment casting can be more expensive upfront compared to other methods, it offers cost savings over time due to reduced material waste and minimal post-production work.
The initial setup costs for molds and patterns can be high, but the cost-per-unit decreases with larger production volumes. Labor costs also play a significant role, as skilled workers are required to oversee the process. For high-volume production, investment casting can become highly cost-efficient, especially for parts with intricate designs that would be difficult or expensive to produce using other methods.
Breakdown of Costs in Stainless Steel Investment Casting
Cost Factor | Description | Impact on Final Cost |
---|---|---|
Mold and Pattern Setup | Initial cost for creating molds and patterns | High upfront cost, but amortized over volume |
Material Costs | Cost of stainless steel used for casting | Varies based on type and quantity |
Labor Costs | Skilled workforce required for precision casting | Significant for smaller runs |
Production Volume | Number of parts produced | Cost-per-unit decreases with volume |
10. How Do You Maintain Quality Control in Stainless Steel Investment Casting?
Quality control is a crucial aspect of stainless steel investment casting. Defects in the casting process can result in costly rework and lost production time. To ensure the highest standards, manufacturers implement several quality control measures throughout the process.
The use of advanced inspection tools, such as x-ray or ultrasonic testing, ensures that parts are free of defects like cracks or porosity. Regular testing of materials before casting also helps identify any issues early on, ensuring consistent quality in the final product. Rigorous inspections after casting help verify that parts meet dimensional accuracy and mechanical properties.
Key Quality Control Methods in Stainless Steel Investment Casting
Method | Purpose | Tools Used |
---|---|---|
Visual Inspection | Checking for visible defects | Magnification tools, microscopes |
X-ray Testing | Detecting internal flaws like porosity | X-ray machines |
Ultrasonic Testing | Detecting subsurface defects | Ultrasonic probes |
Dimensional Check | Ensuring parts meet tolerance levels | Coordinate Measuring Machines (CMM) |
11. How is Stainless Steel Investment Casting Used in Aerospace Applications?
In the aerospace industry, stainless steel investment casting is crucial for producing components that require high strength, precision, and reliability. Parts such as turbine blades, housings, and engine components must endure extreme temperatures and mechanical stress, making stainless steel the material of choice.
The ability of investment casting to produce complex, intricate parts with minimal material waste makes it ideal for aerospace applications. Stainless steel’s strength and corrosion resistance ensure that parts remain functional even in harsh environments, making them reliable over the long term.
Key Aerospace Applications of Stainless Steel Investment Casting
Component | Application | Material Requirements |
---|---|---|
Turbine Blades | Used in engines to convert energy into motion | High strength, heat resistance |
Aircraft Structures | Parts of fuselage, wings, and landing gear | Lightweight, strong, fatigue-resistant |
Engine Components | Critical parts for jet engines | Resistance to high temperatures |
12. How is Stainless Steel Investment Casting Used in Medical Devices?
Stainless steel investment casting plays an important role in the medical device industry. It is used to produce surgical tools, implants, and diagnostic equipment. The precision and strength of stainless steel ensure that these devices meet stringent regulatory standards.
Stainless steel’s biocompatibility, combined with the precision of investment casting, makes it the perfect material for medical devices. Whether it’s a heart valve or a bone implant, these parts need to be reliable, strong, and safe for human use.
Medical Device Applications of Stainless Steel Investment Casting
Device | Use Case | Material Requirements |
---|---|---|
Surgical Tools | Used in surgeries for cutting, drilling, etc. | Precision, sterilization capabilities |
Implants | Bone, joint, or dental implants | Biocompatibility, corrosion resistance |
Diagnostic Devices | Used for imaging or testing | High precision, durability |
13. What Are the Environmental Impacts of Stainless Steel Investment Casting?
The environmental impact of stainless steel investment casting is a growing concern as industries aim to become more sustainable. Although the process is efficient in terms of material usage, there are still challenges regarding energy consumption and waste management.
While stainless steel is recyclable, investment casting requires a significant amount of energy to melt and cast the metal. However, efforts are being made to reduce the carbon footprint by improving energy efficiency and recycling waste materials during production. The overall sustainability of stainless steel investment casting depends on how manufacturers manage energy use and recycling.
Environmental Considerations in Stainless Steel Investment Casting
Factor | Environmental Impact | Mitigation Strategies |
---|---|---|
Energy Consumption | High energy use to melt metal | Use of energy-efficient furnaces |
Waste Management | Waste materials from casting process | Recycling scrap metal, reducing waste |
Emissions | Air and water emissions from casting | Implementing cleaner technologies |
14. How Can You Optimize the Stainless Steel Investment Casting Process?
To maximize the benefits of stainless steel investment casting, it’s important to focus on process optimization. By refining each stage of the process, manufacturers can reduce costs, improve quality, and increase production speed.
Optimizing the casting process involves improving mold design, refining material selection, and enhancing temperature control. Additionally, implementing automation and data analytics can lead to more consistent results, improving both efficiency and product quality.
Process Optimization Techniques in Stainless Steel Investment Casting
Optimization Strategy | Description | Potential Benefit |
---|---|---|
Mold Design | Improving mold quality and complexity | Better precision, reduced defects |
Temperature Control | Ensuring consistent pouring and cooling | Avoiding defects, better material properties |
Automation | Using robots for repetitive tasks | Increased speed, reduced human error |
15. What Are the Future Trends in Stainless Steel Investment Casting?
Stainless steel investment casting is constantly evolving with new technology and innovations. In the future, we can expect to see even more precise methods of casting, alongside more environmentally sustainable processes.
3D printing, for example, is expected to play a larger role in investment casting by enabling the creation of more complex molds and reducing production time. Furthermore, improvements in materials science will lead to stronger and more durable stainless steels, making investment casting even more efficient.
Future Trends in Stainless Steel Investment Casting
Trend | Impact on the Industry | Potential Benefits |
---|---|---|
3D Printing | Allows for more complex mold designs | Reduced production time, higher precision |
Advanced Materials | Stronger and more durable alloys | Increased performance and reliability |
Sustainability Efforts | Cleaner production methods | Lower carbon footprint, reduced waste |
Conclusion
Stainless steel investment casting offers immense advantages for industries requiring precision, strength, and corrosion resistance. From the aerospace sector to medical device manufacturing, this process helps create components that perform under extreme conditions. The ability to produce complex shapes with minimal waste and high precision makes it a valuable technique in modern manufacturing.
If you’re looking to learn more about the stainless steel investment casting process and how it could benefit your manufacturing operations, consider exploring further resources or contacting an expert in the field.
FAQ Section
Q1: What is stainless steel investment casting?
Stainless steel investment casting is a precision manufacturing process where molten stainless steel is poured into a mold to create complex parts with high accuracy and durability.
Q2: How does stainless steel investment casting work?
The process involves creating a model pattern, forming a mold around it, pouring molten stainless steel into the mold, and allowing it to cool and solidify. The mold is then broken to reveal the cast component.
Q3: What are the benefits of using stainless steel investment casting?
It offers high precision, reduces waste, and produces parts that are durable and resistant to corrosion, making it ideal for demanding applications.
Q4: What industries use stainless steel investment casting?
Industries such as aerospace, automotive, medical, and food processing rely on stainless steel investment casting due to its ability to produce strong and precise parts.
Q5: How do you choose the right stainless steel for investment casting?
Choosing the right stainless steel depends on factors like strength, corrosion resistance, and the specific needs of the application. Each type of stainless steel offers unique properties suited for different industries.