Steel casting is an essential process used to manufacture complex, durable parts across many industries. If you’re exploring steel casting for your business, understanding its fundamentals and applications is crucial.
Steel casting refers to the method of pouring molten steel into a mold to form specific shapes and components, typically for industries such as automotive, aerospace, and heavy machinery.
Steel casting allows businesses to create custom parts that are strong and precise, meeting specific needs in various sectors.
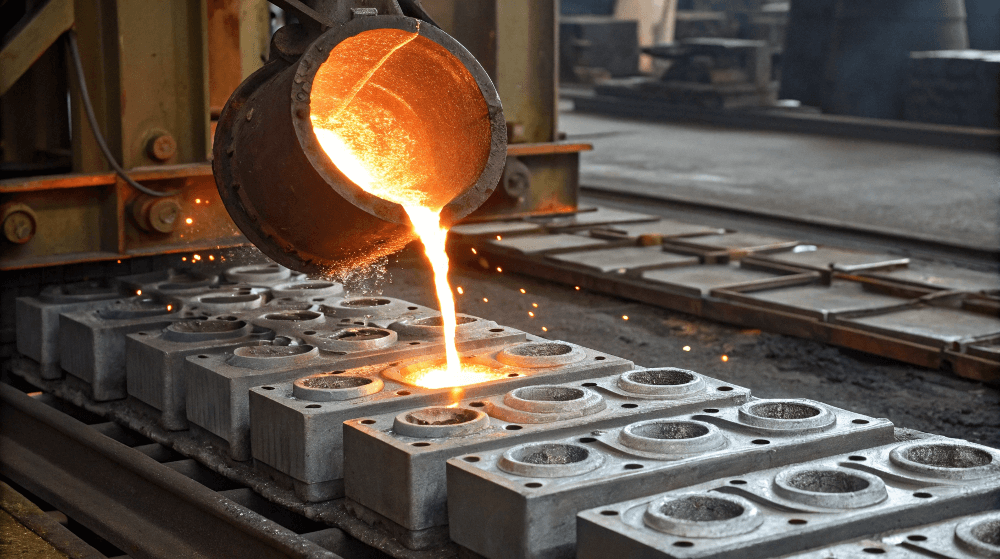
1. What Is Steel Casting?
Steel casting is one of the most important manufacturing techniques used to produce parts with intricate shapes and high durability. So, why is steel casting important? It’s essential for producing parts that other methods, like forging or machining, might not be able to create effectively.
Steel casting works by pouring molten steel into molds made from various materials, such as sand or metal, where it cools and hardens into the desired shape. Once the steel has solidified, the mold is removed, leaving behind the finished part, which can then be cleaned, tested, and used in its respective industry.
Steel casting has been a key manufacturing process for centuries, evolving over time to meet the increasing demands for more complex and larger components. From bridges and automotive parts to industrial machinery, steel casting has applications across almost every sector.
Types of Steel Castings
Steel castings come in various types, each suited for different applications based on the required strength, complexity, and precision. Here are the most common types:
- Investment casting: Used for highly intricate parts where precision is critical.
- Sand casting: Suitable for large parts, often used in construction and machinery.
- Shell molding: Provides a higher level of detail and is used in precision applications.
- Die casting: Typically used for small, mass-produced parts.
Each of these methods has its advantages depending on the part being produced and the requirements of the project.
Type of Steel Casting | Common Uses | Advantages |
---|---|---|
Investment Casting | Precision components | High accuracy, complex shapes |
Sand Casting | Large, heavy parts | Cost-effective, versatile |
Shell Molding | Small, intricate parts | High precision, good surface finish |
Die Casting | Small, mass-produced parts | High-speed production, excellent surface finish |
2. How Does Steel Casting Work?
The steel casting process involves multiple steps, starting with preparing the mold to the final inspection of the casted part.
Here’s a brief overview of the steps involved in steel casting:
- Pattern Making: The first step is to create a mold pattern, which will be used to shape the molten steel.
- Mold Preparation: Once the pattern is made, it’s placed in a mold made of sand, metal, or another material.
- Melting and Pouring: Steel is heated until it turns into molten form and is then poured into the mold.
- Cooling and Solidification: The molten steel cools and solidifies into the shape of the mold.
- Cleaning and Finishing: After the steel is cooled and hardened, the mold is removed, and the casting is cleaned and finished.
Each of these steps requires precision and care to ensure the final product meets the necessary specifications.
Step | Description |
---|---|
Pattern Making | Creating the shape of the final part |
Mold Preparation | Preparing the mold to receive molten steel |
Melting and Pouring | Melting steel and pouring it into the mold |
Cooling and Solidification | Allowing steel to cool and solidify in the mold |
Cleaning and Finishing | Removing the mold and cleaning the casting |
3. What Are the Main Types of Steel Castings?
Steel castings can be classified based on the method used to create them, each method offering unique benefits depending on the application.
- Investment casting is used for small, complex parts where precision is paramount.
- Sand casting is a versatile and cost-effective method for creating larger parts.
- Shell molding offers improved detail and surface finish, ideal for intricate components.
- Die casting is efficient for producing small and mass-produced parts.
Each method has its pros and cons, and selecting the right one depends on factors such as part size, complexity, and production volume.
4. What Are the Materials Used in Steel Casting?
The materials used in steel casting are critical in determining the final properties of the casted parts. Steel alloys, particularly carbon steel and stainless steel, are commonly used due to their durability and ability to withstand extreme conditions.
The choice of material significantly influences the quality of the final product. For example, stainless steel is used for parts that require resistance to corrosion, while carbon steel is often used for its strength and cost-effectiveness.
Material | Benefits | Common Applications |
---|---|---|
Carbon Steel | Strong, affordable | Heavy machinery, automotive |
Stainless Steel | Corrosion-resistant | Medical equipment, aerospace |
Alloy Steel | High performance | Tooling, automotive parts |
5. What Are the Advantages of Steel Casting?
Steel casting has several key advantages, which is why it is commonly used in various industries.
- Strength and durability: Steel castings are known for their ability to withstand harsh conditions.
- Design flexibility: Steel casting allows for the creation of complex shapes that are difficult to achieve with other manufacturing methods.
- Cost-effectiveness: While the initial investment can be high, steel casting is often more cost-effective in the long run due to its ability to create durable, high-performance parts.
Steel casting is ideal for producing parts that must meet stringent performance and reliability standards.
Advantage | Description |
---|---|
Strength and Durability | Steel castings can handle heavy stress and high temperatures. |
Design Flexibility | Complex shapes can be easily formed. |
Cost-effectiveness | High initial costs but cost savings over time due to durability. |
6. What Are the Challenges in Steel Casting?
Despite the numerous advantages, steel casting does present some challenges that need to be addressed to ensure high-quality outcomes.
The process of steel casting can result in several common issues such as defects, dimensional variations, and issues related to the quality of the mold or the steel itself. For example, if the molten steel is not poured at the correct temperature, it can lead to cracks or inclusions in the final part.
Managing these challenges is critical to maintaining the efficiency and effectiveness of the steel casting process. Some of the most common issues in steel casting include:
- Defects like shrinkage or cracks: These can occur due to improper cooling or solidification processes.
- Dimensional issues: Inaccuracies in the mold or tooling can result in parts that do not meet the required specifications.
- Material issues: If the wrong type of steel is used or impurities are present, it can compromise the integrity of the casting.
These challenges can be mitigated with proper techniques, advanced technologies, and constant quality control throughout the casting process.
Challenge | Description | Solution |
---|---|---|
Defects (Shrinkage/Cracks) | Imperfections due to cooling and solidification issues. | Use controlled cooling processes and proper mold design. |
Dimensional Variations | Parts may not meet required specifications. | Improve tooling accuracy and mold design. |
Material Impurities | Impurities in the steel affect the casting quality. | Use high-quality materials and precise monitoring. |
7. How Do Steel Casting and Other Manufacturing Methods Compare?
Steel casting is just one of many manufacturing techniques, and it’s important to understand how it compares to other methods like forging or machining.
Steel casting has a distinct advantage when creating parts with complex geometries that other methods can’t easily achieve. While forging and machining have their own advantages, steel casting offers greater flexibility for certain applications. Let’s look at how steel casting compares to some of the other methods:
- Forging: Forging involves shaping metal using compressive force. It’s ideal for parts that need high strength but doesn’t allow for as much complexity in design.
- Machining: While machining offers high precision, it’s less effective when creating complex shapes and is usually more time-consuming.
For intricate and large parts that need to meet both durability and design requirements, steel casting remains a top choice.
Method | Advantages | Disadvantages | Best Use Case |
---|---|---|---|
Steel Casting | Complex shapes, high durability | Potential defects, longer lead times | Large, complex parts |
Forging | High strength, high density | Limited design complexity | Parts requiring high strength |
Machining | High precision | Time-consuming, limited for large parts | Fine-tuning parts for exact specifications |
8. Where Is Steel Casting Used?
Steel casting is employed in numerous industries due to its ability to create highly durable and precisely shaped components.
This manufacturing process is essential in industries such as automotive, aerospace, and heavy machinery, where strength and durability are critical. The parts produced are used in everything from car engines to turbines.
Common applications include:
- Automotive Industry: Steel castings are used for engine components, transmission parts, and exhaust systems.
- Aerospace: Components for aircraft engines, landing gear, and structural parts are made using steel casting.
- Heavy Machinery: Parts for construction equipment, mining machines, and industrial machinery are cast using steel.
Steel casting also plays a role in the production of medical equipment, valves, and pumps.
Industry | Common Applications | Benefits |
---|---|---|
Automotive | Engine blocks, transmission parts | High strength, complex shapes |
Aerospace | Aircraft engine parts, landing gear | Durability, reliability |
Heavy Machinery | Construction equipment, mining machines | High wear resistance, cost-effectiveness |
9. What Are the Key Steel Casting Industries?
Several industries rely heavily on steel casting for the production of high-quality parts. These industries require parts that meet stringent performance standards for durability, strength, and precision.
Some of the most significant industries include:
- Automotive and Transportation: Steel castings are crucial for making engine components, brake systems, and structural parts.
- Oil and Gas: Parts used in pumps, valves, and drilling equipment are commonly produced using steel casting.
- Aerospace: The aerospace industry relies on steel casting for parts that need to withstand extreme conditions, such as turbine blades and engine components.
Each of these industries benefits from the versatility of steel casting, which allows for the creation of durable, high-performance parts.
Industry | Common Steel Casting Parts | Requirements |
---|---|---|
Automotive | Engine components, brake systems | Durability, high performance |
Oil and Gas | Pumps, valves, drilling equipment | Strength, corrosion resistance |
Aerospace | Turbine blades, engine parts | High heat resistance, reliability |
10. How Is Steel Casting Tested for Quality?
Testing is an integral part of ensuring the quality of steel castings.
Several methods are used to test steel castings for defects and performance, including visual inspections, ultrasonic testing, and mechanical testing. These tests ensure that the parts meet the necessary standards before being sent to the customer.
Common testing methods include:
- Ultrasonic testing: Used to detect internal defects.
- Visual inspection: Ensures there are no surface defects.
- Mechanical testing: Assesses the strength, flexibility, and durability of the casted part.
Quality control processes in steel casting include continuous monitoring of temperature, material composition, and mold integrity.
Test Type | Purpose | Common Use Case |
---|---|---|
Ultrasonic Testing | Detects internal defects | Critical components like turbine blades |
Visual Inspection | Identifies surface defects | Final checks before shipment |
Mechanical Testing | Measures strength and durability | Testing for automotive and aerospace parts |
11. What Is the Future of Steel Casting?
Steel casting is evolving with advancements in technology and manufacturing techniques.
The future of steel casting involves increased automation, advanced material alloys, and the integration of more efficient production processes. Automation is particularly important, as it can reduce labor costs and improve precision.
Another major trend is the development of sustainable practices within the industry. Many companies are seeking ways to reduce energy consumption, minimize waste, and lower their carbon footprints.
Emerging technologies, such as 3D printing, could further revolutionize steel casting, allowing for more complex designs and quicker production times.
Future Trend | Description | Benefits |
---|---|---|
Automation | Increased use of robotics and automated systems | Reduced labor costs, increased precision |
Sustainable Practices | Focus on eco-friendly production methods | Reduced environmental impact, cost savings |
3D Printing | Integration of 3D printing in steel casting | Complex designs, faster production |
12. What Are the Environmental Considerations in Steel Casting?
Environmental sustainability is becoming a growing concern in the steel casting industry.
Steel casting operations can be resource-intensive, leading to high energy consumption and waste generation. However, many companies are adopting green initiatives to minimize their environmental impact. These include reducing energy usage, recycling materials, and reducing emissions from the casting process.
Common environmental considerations include:
- Energy consumption: Steel casting is energy-intensive, but advancements in technology aim to reduce energy use.
- Waste management: Waste products from the casting process can be recycled or disposed of more efficiently.
Sustainability is becoming a core focus for the steel casting industry, and companies that embrace these practices will likely have a competitive edge in the future.
Environmental Factor | Solution | Impact |
---|---|---|
Energy Consumption | Use of energy-efficient technologies | Lower operating costs, reduced carbon footprint |
Waste Management | Improved recycling and disposal methods | Less waste, reduced environmental harm |
13. How Can Steel Casting Costs Be Reduced?
Steel casting can be expensive, but there are several strategies to reduce costs without sacrificing quality.
One of the most effective ways to lower costs is by improving efficiency in the production process. This includes reducing waste, using more cost-effective materials, and optimizing mold design to reduce material usage.
Other strategies to reduce costs:
- Investing in automation: Automated processes can reduce labor costs and increase precision.
- Optimizing the supply chain: Streamlining the procurement of materials and components can reduce expenses.
- Improving quality control: Preventing defects early on reduces the need for rework and waste.
By focusing on efficiency and innovation, companies can reduce the overall costs of steel casting.
Cost Reduction Strategy | Description | Benefit |
---|---|---|
Efficiency Improvements | Optimize production processes and reduce waste | Lower costs, faster production times |
Automation | Invest in automated systems to replace manual labor | Reduced labor costs, better precision |
Quality Control | Prevent defects and rework through rigorous testing | Reduced material waste, fewer production delays |
14. How Do Steel Castings Contribute to Safety in Manufacturing?
Steel castings play a crucial role in ensuring safety across various industries.
By providing strong, durable components for critical machinery, steel castings contribute to safety by preventing equipment failure. For instance, the use of high-quality steel castings in automotive and aerospace industries ensures that vehicles and aircraft remain safe under extreme conditions.
Steel castings are also used in manufacturing machinery that handles heavy loads, such as cranes or mining equipment. These components must meet strict safety standards to avoid accidents.
Industry | Application | Safety Benefit |
---|---|---|
Automotive | Engine blocks, brake systems | Prevents failure, ensures safety |
Aerospace | Aircraft engine components | Reliable under extreme conditions |
Heavy Machinery | Cranes, lifting equipment | Prevents machinery malfunction, reduces risk |
15. How Does Steel Casting Compare Globally?
Steel casting is a global industry, with major producers located around the world.
Countries like China, the USA, and India are leading producers of steel castings, benefiting from large-scale manufacturing capabilities and access to raw materials. The global demand for steel castings is increasing due to their widespread use in key industries like automotive, energy, and construction.
The global nature of the steel casting market means that companies are increasingly competing for customers. Trade regulations, tariffs, and supply chain disruptions can all affect the global market for steel castings.
Country | Steel Casting Production | Global Impact |
---|---|---|
China | Largest producer | Dominates global market, cost advantages |
USA | High-quality production | Focuses on precision and high-performance castings |
India | Growing steel casting market | Cost-effective solutions, increasing demand |
Conclusion
Steel casting is a versatile and highly effective method used in manufacturing a wide range of parts for various industries. Understanding the different types of steel castings, the materials used, and the process itself can help you make informed decisions when selecting this manufacturing technique. With its numerous advantages, steel casting remains a vital process in the production of high-performance, durable parts. If you’re considering steel casting for your next project, it’s essential to understand the nuances of the process to ensure the best results.
FAQ Section
Q1: What is steel casting?
Steel casting is a process where molten steel is poured into a mold to create parts with complex shapes and high durability. It is widely used in industries like automotive, aerospace, and heavy machinery.
Q2: How does the steel casting process work?
The steel casting process involves creating a mold, melting the steel, pouring it into the mold, allowing it to solidify, and then cleaning and finishing the final product.
Q3: What are the main types of steel casting?
The main types of steel casting include investment casting, sand casting, shell molding, and die casting. Each method offers unique benefits based on the part’s requirements.
Q4: What are the advantages of steel casting?
Steel casting offers strength, design flexibility, and cost-effectiveness. It is ideal for producing durable parts that can withstand extreme conditions and have complex shapes.
Q5: How is steel casting tested for quality?
Steel casting is tested using methods like visual inspection, mechanical testing, and non-destructive testing to ensure that the final product meets the required standards.