Are you wondering how cast steel is made, its properties, and its composition? Cast steel is a versatile material used across industries due to its strength and durability. Let’s dive into how it’s produced, the elements that make it special, and how its composition impacts its performance.
Cast steel is made through a casting process, where molten steel is poured into molds to create different shapes. The production method plays a crucial role in determining the material’s properties. This article will guide you through cast steel’s production process, composition, and its key characteristics.
Now, let’s take a closer look at how cast steel is produced and what makes it stand out in various applications.
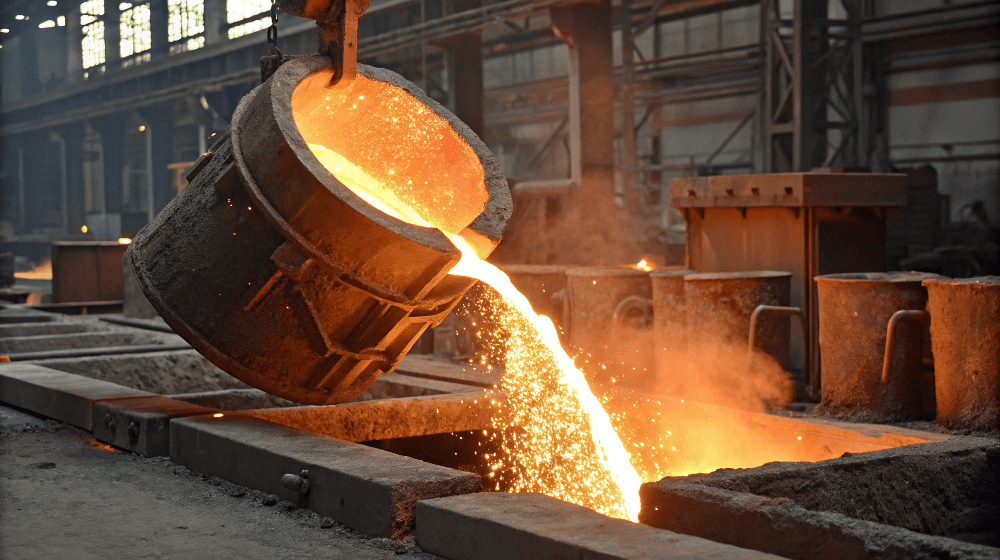
1. What is Cast Steel?
Have you ever wondered what exactly cast steel is and why it’s used in so many industries? Cast steel is a steel alloy made by pouring molten steel into molds to form shapes. It’s widely used for its strength and ability to be molded into complex forms.
Cast steel is typically created by heating steel to its molten state and then pouring it into a mold where it solidifies into the desired shape. The key benefit is its versatility and durability, making it ideal for heavy-duty applications.
What is the Difference Between Cast Steel and Wrought Steel?
- Cast steel is made by casting molten steel into molds. It is typically stronger and more durable due to its ability to handle high stresses.
- Wrought steel, on the other hand, is made by heating and hammering or rolling the steel into shape. It tends to be more ductile and less brittle than cast steel.
Common Applications of Cast Steel
Cast steel is used in a wide variety of applications due to its toughness and resistance to wear. Some examples include:
- Automotive parts, such as engine blocks
- Heavy machinery components
- Structural supports in construction
Key Characteristics of Cast Steel
- Strength: Cast steel can withstand heavy loads and is often used in construction and automotive applications.
- Durability: It is resistant to wear and can perform in harsh conditions.
- Versatility: Its ability to be molded into different shapes makes it ideal for complex designs.
Material | Strength | Durability | Flexibility |
---|---|---|---|
Cast Steel | High | Very Durable | Moderate |
Wrought Steel | Moderate | Durable | High |
2. How is Cast Steel Produced?
Are you curious about the process that turns raw steel into cast steel? The production of cast steel is a precise process that involves several steps. It’s important to understand these steps to appreciate how cast steel gets its strength and versatility.
The production of cast steel involves melting steel and pouring it into molds where it solidifies into the desired shape. This casting process ensures that the steel takes on the necessary properties for different applications.
Key Steps in Cast Steel Production
- Melting the Steel: Steel is melted in an electric arc furnace or induction furnace, where scrap steel is combined with alloying elements to achieve the desired composition.
- Pouring into Molds: Once molten, the steel is poured into pre-prepared molds that define the shape of the final product.
- Cooling and Solidification: The steel is cooled slowly to prevent cracking, ensuring that the solidified piece has the right density and strength.
- Finishing: After the casting has cooled, the final product undergoes finishing processes like grinding, machining, and heat treatment to enhance its properties.
Types of Casting Methods Used in Steel Production
- Sand Casting: Involves making molds out of sand, which can handle large components.
- Die Casting: Uses metal molds and is suitable for mass production of smaller components.
- Investment Casting: Often used for precision parts, where a wax pattern is coated with a ceramic shell.
Challenges in Cast Steel Production
One of the main challenges in cast steel production is ensuring uniformity and preventing defects like cracks or inclusions in the final product. The cooling process is especially critical in maintaining the quality of the steel.
Casting Method | Best Use | Advantages |
---|---|---|
Sand Casting | Large parts, low volume | Inexpensive, versatile |
Die Casting | Small parts, mass production | High precision, fast production |
Investment Casting | Complex shapes, precision | High accuracy, smooth surface finish |
3. What Are the Key Properties of Cast Steel?
What makes cast steel so unique and reliable? Cast steel has several important properties that make it ideal for industrial use. These properties are what set it apart from other materials and make it a go-to choice for engineers and manufacturers.
Cast steel is known for its high strength, wear resistance, and ability to handle high-stress conditions. It’s used in heavy machinery, automotive components, and many other industries that require durable materials.
Key Properties of Cast Steel
- Strength: Cast steel is stronger than many other materials, making it ideal for use in parts that need to bear heavy loads or handle stress.
- Ductility: Although cast steel is tough, it can also be slightly more brittle than wrought steel, so it is not as flexible under impact forces.
- Corrosion Resistance: Many types of cast steel are resistant to corrosion, making them suitable for use in harsh environments.
- Machinability: Cast steel can be easily machined into complex shapes, allowing it to be used in a variety of applications.
How Cast Steel Performs in Extreme Conditions
Cast steel’s toughness makes it ideal for applications that require resistance to wear, such as mining equipment, automotive parts, and heavy machinery components. The alloy can withstand extreme temperatures and pressure, ensuring long-term durability.
Heat Treatment of Cast Steel
Heat treatment processes can significantly improve the mechanical properties of cast steel, such as increasing its hardness and strength. Common heat treatment processes include quenching, annealing, and tempering.
Property | Impact on Performance | Ideal Application |
---|---|---|
Strength | Enhances load-bearing capacity | Heavy machinery, automotive parts |
Ductility | Determines flexibility | Construction, structural components |
Corrosion Resistance | Protects against degradation | Marine, industrial equipment |
4. What Are the Different Types of Cast Steel?
Do you know that there are different types of cast steel, each with its own strengths and uses? Cast steel can be classified into several types based on its composition and intended use. Understanding these types will help you choose the right steel for your application.
The different types of cast steel include carbon cast steel, alloy cast steel, stainless cast steel, and tool cast steel. Each type has unique properties that make it suitable for specific applications.
Types of Cast Steel
- Carbon Cast Steel: This is the most basic form of cast steel, made with carbon as the primary alloying element. It is strong but lacks corrosion resistance.
- Alloy Cast Steel: Alloy cast steel contains elements like chromium, manganese, and molybdenum to enhance specific properties such as strength and heat resistance.
- Stainless Cast Steel: Stainless steel is resistant to corrosion and oxidation, making it ideal for use in harsh environments like marine or food processing industries.
- Tool Cast Steel: This type of steel is used for making tools and dies. It has high hardness and wear resistance.
Choosing the Right Type of Cast Steel
When selecting cast steel for a project, it’s important to match the type of steel with the needs of the application. For instance, alloy cast steel is better for high-stress applications, while stainless cast steel is ideal for environments that require corrosion resistance.
Type of Cast Steel | Key Characteristics | Best Applications |
---|---|---|
Carbon Cast Steel | Strong, but lacks resistance | General machinery and automotive |
Alloy Cast Steel | Enhanced strength, heat resistance | High-performance machinery |
Stainless Cast Steel | Corrosion-resistant | Marine, food industry, medical devices |
Tool Cast Steel | High hardness, wear-resistant | Tool manufacturing, dies |
5. What is the Composition of Cast Steel?
Do you know what exactly makes up cast steel? The composition of cast steel is crucial for determining its strength, hardness, and resistance to wear. Understanding the elements involved in cast steel composition can help you choose the right material for your application.
Cast steel is primarily composed of iron, carbon, and alloying elements like manganese, chromium, and molybdenum. The specific combination of these elements affects the material’s properties, such as its hardness, machinability, and resistance to corrosion.
Key Elements in Cast Steel
- Carbon: The primary element in cast steel, influencing hardness and strength. Higher carbon content increases strength but reduces ductility.
- Manganese: Enhances strength and hardness, while also improving wear resistance.
- Chromium: Increases corrosion resistance and hardness, often used in stainless cast steel.
- Molybdenum: Adds to the strength at high temperatures, making the steel more resistant to heat and wear.
How Alloying Elements Impact Cast Steel
- Carbon: Higher carbon content leads to stronger but more brittle cast steel, making it ideal for applications requiring high strength but less flexibility.
- Manganese: Manganese is added to improve the material’s resistance to wear and enhance its toughness, which is essential in applications like construction and automotive parts.
- Chromium and Molybdenum: These elements make cast steel more resistant to corrosion and oxidation, allowing it to perform well in harsh environments.
Element | Function | Impact on Cast Steel |
---|---|---|
Carbon | Increases hardness and strength | Higher strength, reduced ductility |
Manganese | Improves hardness and toughness | Enhanced wear resistance |
Chromium | Adds corrosion resistance | Increases durability in harsh conditions |
Molybdenum | Improves heat and wear resistance | Better performance at high temperatures |
6. How Does Carbon Content Affect Cast Steel Properties?
Did you know that carbon content plays a key role in the properties of cast steel? The amount of carbon in cast steel significantly impacts its hardness, strength, and ductility.
The higher the carbon content in cast steel, the harder and stronger it becomes, but at the cost of flexibility. It’s essential to balance the carbon content to achieve the desired properties for specific applications.
Relationship Between Carbon Content and Strength
- Higher Carbon Content: Increases the hardness and strength of the steel, making it ideal for applications that require load-bearing capabilities. However, this makes the steel more brittle and less ductile.
- Lower Carbon Content: Results in softer steel that is more flexible and ductile, making it suitable for applications where flexibility is more important than strength.
Impact on Ductility and Weldability
While higher carbon content makes cast steel stronger, it also reduces its ductility and weldability. This means that cast steel with high carbon content may crack or break under certain conditions, especially when subjected to bending or welding.
Carbon Content | Impact on Strength | Impact on Ductility |
---|---|---|
Low Carbon | Lower strength | Higher ductility |
High Carbon | Higher strength | Reduced ductility |
7. What Are the Benefits of Using Cast Steel in Manufacturing?
Are you wondering why so many industries prefer cast steel for manufacturing? Cast steel offers a range of benefits that make it a popular choice for manufacturing components that need to withstand high stresses and harsh environments.
The main benefits of cast steel include its durability, strength, and cost-effectiveness. Its versatility and ability to be molded into complex shapes make it a go-to material for manufacturing parts across various industries.
Durability and Reliability in Industrial Applications
Cast steel is highly durable and can withstand heavy loads, making it ideal for industries like mining, construction, and automotive manufacturing. Components made from cast steel have a long lifespan, which helps reduce maintenance and replacement costs.
Cost-Effectiveness Compared to Other Materials
When compared to other materials like stainless steel or alloy steel, cast steel is often more affordable. Its production process is cost-effective, especially for mass production, making it a budget-friendly choice for manufacturers.
Customization for Specific Applications
Cast steel can be easily molded into a variety of shapes and sizes, allowing manufacturers to create complex components that meet specific requirements. This level of customization is one of the main reasons cast steel is used in so many industries.
Benefit | Impact on Manufacturing |
---|---|
Durability | Long-lasting components, reduced maintenance costs |
Cost-effectiveness | More affordable than alternative materials |
Customization | Ability to mold into complex shapes for specific needs |
8. How Are Cast Steel Alloys Created?
Do you know how alloying elements are mixed into cast steel to create different types of cast steel? The process of creating cast steel alloys involves adding specific elements to enhance the material’s properties.
Cast steel alloys are created by adding elements like chromium, manganese, and molybdenum to the base steel. These elements give the cast steel specific properties, such as increased strength, corrosion resistance, and heat resistance.
The Role of Alloying Elements in Steel
- Chromium: Adds corrosion resistance and improves hardness, making the steel suitable for harsh environments.
- Manganese: Enhances strength and toughness, particularly in applications requiring resistance to wear.
- Molybdenum: Improves resistance to heat and enhances strength, making the steel more reliable under high-temperature conditions.
Process of Alloy Creation and Mixing
Alloying elements are added to molten steel in precise amounts to ensure that the final product has the desired properties. The steel is thoroughly mixed, and then it is poured into molds to form the final shapes.
Alloying Element | Function | Benefits in Cast Steel |
---|---|---|
Chromium | Increases corrosion resistance | Durable in harsh environments |
Manganese | Enhances strength and toughness | More resistant to wear and tear |
Molybdenum | Improves heat resistance | Reliable in high-temperature use |
9. What Are the Challenges in Cast Steel Production?
What are some of the challenges manufacturers face when producing cast steel? Cast steel production is not without its difficulties, and addressing these challenges is crucial for ensuring high-quality products.
The main challenges in cast steel production include maintaining quality control, preventing defects, and managing the cooling process. Let’s dive deeper into how these challenges affect the production process and the final product.
Quality Control and Defect Prevention
Maintaining quality control is one of the biggest challenges in cast steel production. Defects like cracks, inclusions, and air pockets can compromise the strength and reliability of the final product.
Cooling and Solidification Issues
The cooling process is critical in ensuring that the steel solidifies properly. If the cooling rate is too fast or too slow, it can cause defects like shrinkage or cracking. Manufacturers must carefully control the cooling process to prevent these issues.
Environmental Concerns in Production
Steel production, including the casting process, generates emissions and consumes significant energy. Manufacturers are increasingly focused on improving sustainability and reducing their environmental impact.
Challenge | Impact on Production |
---|---|
Quality Control | Risk of defects that compromise product strength |
Cooling Issues | Cracking or shrinkage of cast steel components |
Environmental Concerns | High energy consumption and emissions |
10. How Are Cast Steel Properties Tested?
How do manufacturers test the properties of cast steel to ensure they meet required standards? Testing cast steel properties is essential to ensure the material will perform as expected in its intended application.
Cast steel properties are tested using mechanical testing, chemical analysis, and non-destructive testing methods. These tests help verify that the material meets the necessary strength, hardness, and resistance to wear.
Mechanical Testing Methods
Mechanical testing is used to determine the material’s strength, hardness, and toughness. Common tests include tensile testing, impact testing, and hardness testing. These tests provide valuable information about how the cast steel will perform under various loads and conditions.
Chemical Analysis
Chemical analysis is performed to determine the composition of the cast steel and ensure it contains the correct elements in the right proportions. Techniques like spectroscopy and X-ray analysis are often used for this purpose.
Non-Destructive Testing
Non-destructive testing methods, such as ultrasonic and radiographic testing, allow manufacturers to detect internal defects without damaging the steel. These tests are crucial for ensuring the material’s integrity before it is used in production.
Testing Method | Purpose |
---|---|
Mechanical Testing | To determine strength, hardness, and toughness |
Chemical Analysis | To verify composition and element proportions |
Non-Destructive Testing | To detect internal defects without damaging the steel |
11. What Are the Common Applications of Cast Steel?
Where is cast steel used in real-world applications? Cast steel’s strength and versatility make it ideal for a wide range of industries and applications, from heavy machinery to automotive manufacturing.
Common applications of cast steel include the automotive, mining, construction, and aerospace industries. Cast steel’s ability to withstand heavy loads and perform well under extreme conditions makes it indispensable in these sectors.
Cast Steel in the Automotive Industry
Cast steel is used in manufacturing components like engine blocks, suspension parts, and gears. Its durability and strength make it ideal for parts that need to endure high stress.
Cast Steel in Mining and Construction
Mining equipment, like crushers and excavators, is often made from cast steel due to its toughness and resistance to wear. Cast steel is also used for structural supports in construction, where high load-bearing capacity is required.
Cast Steel in Aerospace and Marine Industries
In the aerospace industry, cast steel is used for parts that need to withstand high temperatures and stresses. Similarly, cast steel components are used in marine applications, where corrosion resistance and strength are crucial.
Industry | Application |
---|---|
Automotive | Engine blocks, suspension parts |
Mining | Crushers, excavation machinery |
Aerospace | High-temperature parts |
Marine | Marine components, corrosion-resistant parts |
12. How Can Cast Steel Be Heat Treated for Optimal Performance?
How does heat treatment improve the properties of cast steel? Heat treatment is a vital process that can enhance the strength, hardness, and performance of cast steel.
Heat treatment processes like quenching, annealing, and tempering are used to improve the mechanical properties of cast steel. These processes can make the steel more durable, resistant to wear, and capable of withstanding high temperatures.
Common Heat Treatment Methods
- Quenching: Rapid cooling of cast steel in water or oil to increase hardness.
- Annealing: Slow heating and cooling to improve ductility and reduce internal stresses.
- Tempering: Reheating quenched steel to a specific temperature to reduce brittleness.
Effects of Heat Treatment on Cast Steel
Heat treatment can enhance the material’s performance in various ways. For example, tempering can reduce the brittleness of quenched steel, while annealing improves its workability.
Heat Treatment Method | Effect on Cast Steel |
---|---|
Quenching | Increases hardness, makes steel more brittle |
Annealing | Reduces internal stress, increases ductility |
Tempering | Reduces brittleness, increases toughness |
13. How Do You Choose the Right Type of Cast Steel for an Application?
Are you wondering which type of cast steel is best for your specific needs? Selecting the right type of cast steel can be a daunting task, but it’s essential to ensure that the material you choose meets the specific requirements of your application.
The right type of cast steel depends on factors like strength, durability, temperature resistance, and cost. By considering the intended use, you can determine which type of cast steel will perform best in your project.
Factors to Consider When Choosing Cast Steel
- Strength Requirements: If the application involves heavy loads or high stress, you’ll need cast steel with a high tensile strength, such as carbon or alloy cast steel.
- Temperature Resistance: For applications exposed to high temperatures, you’ll need cast steel with heat-resistant properties, such as molybdenum or chromium alloys.
- Corrosion Resistance: For use in harsh environments, stainless cast steel is a great option due to its ability to resist corrosion and oxidation.
Matching Steel Properties to Project Requirements
Each type of cast steel offers a unique set of properties. By understanding your project’s demands, you can match the material to the right application. For instance, stainless steel is best for corrosion-resistant applications, while tool steel is ideal for high-wear parts like molds and dies.
Cost Considerations
While high-performance cast steels offer excellent durability and resistance to wear, they can also be more expensive. When selecting cast steel, consider the balance between cost and performance. For less demanding applications, carbon cast steel may be sufficient, offering a lower cost without compromising much on strength.
Factor | Consideration |
---|---|
Strength | Required for heavy load-bearing applications |
Temperature Resistance | Needed for high-temperature applications |
Corrosion Resistance | Crucial for marine, food processing, and harsh environments |
Cost | Balancing performance with material cost |
14. What Are the Environmental Impacts of Cast Steel Production?
Did you know that steel production, including the casting process, has a significant environmental impact? Understanding the environmental aspects of cast steel production is important for both manufacturers and consumers who are committed to sustainability.
The environmental impact of cast steel production includes energy consumption, emissions, and the use of natural resources. Manufacturers are increasingly focusing on reducing their environmental footprint through more sustainable production methods and recycling efforts.
Emissions and Energy Consumption in Steel Production
Steel production requires a substantial amount of energy, especially during the melting and casting stages. This results in greenhouse gas emissions and air pollution. Efforts are being made to reduce energy consumption by adopting more efficient furnaces and using alternative energy sources.
Recycling Options for Cast Steel
One of the most significant advantages of cast steel is its recyclability. Cast steel can be recycled multiple times without losing its properties, making it a sustainable choice. Recycling reduces the need for raw materials and lowers the environmental impact associated with mining and processing new steel.
Strategies for Reducing Environmental Footprint
Manufacturers are adopting various strategies to reduce the environmental impact of steel production. These include:
- Implementing energy-efficient technologies
- Increasing the use of recycled steel
- Reducing emissions through cleaner production techniques
Environmental Impact | Solution |
---|---|
Energy Consumption | Use of energy-efficient technologies |
Emissions | Cleaner production methods, reduction in carbon footprint |
Raw Material Use | Increased recycling and use of scrap steel |
15. What is the Future of Cast Steel Production?
What does the future hold for cast steel production? As industries evolve, so do the technologies and techniques used to produce cast steel. Innovations are continuously shaping the future of cast steel manufacturing.
The future of cast steel production is moving toward greater efficiency, sustainability, and technological advancements. These changes promise to further enhance the material’s performance and reduce its environmental impact.
Emerging Technologies in Cast Steel Manufacturing
- 3D Printing: Additive manufacturing, or 3D printing, is beginning to play a role in the production of cast steel parts. This allows for the creation of complex geometries that would be difficult or impossible with traditional casting methods.
- Automation and AI: Automation in the production process, combined with AI-driven systems, is improving the speed, precision, and efficiency of steel casting, reducing human error and material waste.
Trends in Alloy Development
The development of new alloys will continue to shape cast steel production. Researchers are working on alloys that offer improved strength, corrosion resistance, and wear resistance while maintaining a low environmental impact. This is critical for applications in industries like aerospace, automotive, and marine engineering.
The Impact of Sustainability in Steel Production
Sustainability will continue to be a driving force in the evolution of cast steel production. Companies are adopting green practices, including energy-efficient furnaces, carbon capture technologies, and increased use of recycled materials, to meet growing environmental demands.
Future Trend | Impact on Cast Steel |
---|---|
3D Printing | Enables complex shapes and reduces waste |
Automation and AI | Improves efficiency and reduces human error |
Alloy Development | Stronger, more resistant materials |
Sustainability | Reduces environmental impact through greener practices |
Conclusion
Cast steel is a vital material in various industries due to its strength, durability, and versatility. By understanding its production process, composition, and key properties, you can make better decisions about how to use cast steel in your projects. Whether you’re in manufacturing, construction, or another field, cast steel is a reliable choice that can withstand the toughest conditions.
FAQ Section
Q1: What is cast steel?
Cast steel is a type of steel that is formed by pouring molten steel into molds, allowing it to solidify into different shapes. It is used for its strength, durability, and versatility in various industries.
Q2: How does the casting process work?
The casting process involves melting steel, pouring it into molds, and allowing it to cool and solidify into the desired shape. This process is crucial for achieving the strength and properties of cast steel.
Q3: What is the difference between cast steel and wrought steel?
Cast steel is made by casting molten steel into molds, while wrought steel is shaped by heating and working the metal. Cast steel is generally stronger, while wrought steel is more flexible.
Q4: Why is cast steel used in heavy machinery?
Cast steel’s strength, durability, and ability to handle high-stress conditions make it ideal for heavy machinery, where parts are subjected to extreme loads and wear.
Q5: Can cast steel be recycled?
Yes, cast steel is recyclable, and its recycling process helps reduce the environmental impact of steel production. It is often reused in new cast steel production or other manufacturing processes.