Steel casting is a critical part of modern manufacturing, playing a vital role in producing durable, high-quality components. If you’re looking to understand the basic steps involved in steel casting, you’re in the right place.
Steel casting involves several complex but essential stages. By mastering the basic steps in the process, manufacturers can produce steel parts that meet specific requirements for strength and durability.
Understanding how the steel casting process works is crucial. Let’s take a closer look at the steps involved and how they contribute to the production of cast steel components.
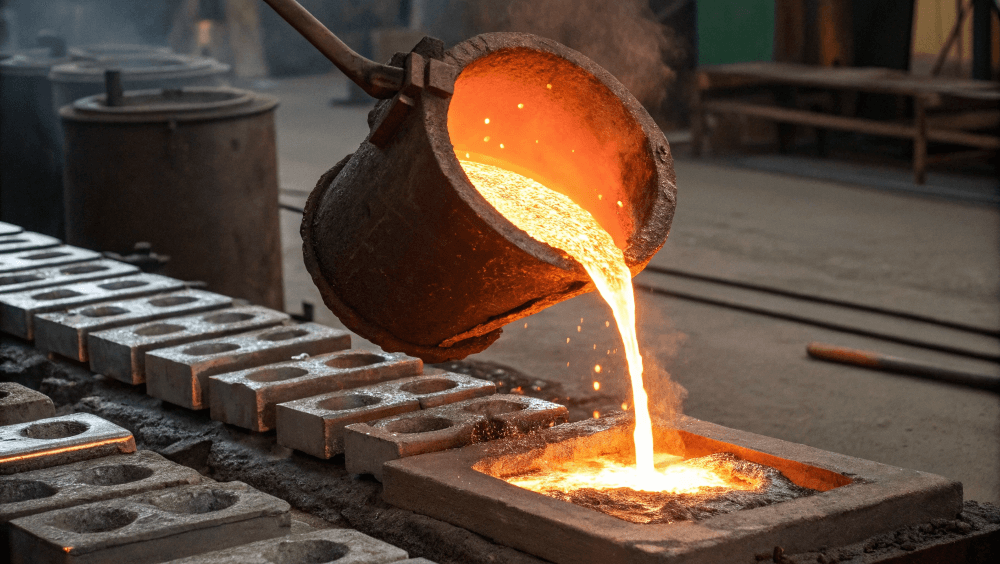
1. What Is the Steel Casting Process?
Steel casting refers to a process where molten steel is poured into a mold to form a specific shape. It’s used to create parts for a variety of industries, including automotive, construction, and energy.
The steel casting process involves melting steel and pouring it into a mold where it solidifies into the desired shape. These cast parts then undergo further finishing to meet specific requirements. Steel casting is often preferred due to its ability to produce complex parts that are durable and cost-effective.
Steel Casting Process Stages
Step | Description |
---|---|
Mold Preparation | Create and prepare a mold for molten steel. |
Melting the Steel | Heat steel to a molten state to make it ready for casting. |
Pouring the Steel | Pour molten steel into the mold to take its shape. |
Cooling & Solidification | Allow the steel to cool and harden in the mold. |
Finishing | Trim, grind, and inspect the casting to meet required standards. |
2. What Are the Key Materials Used in Steel Casting?
Steel casting requires specific materials, including steel alloys, to achieve the desired properties in the final product.
The materials used in steel casting include carbon steel, alloy steel, and stainless steel, each offering different advantages depending on the application. These materials must be carefully chosen based on their composition, as the alloy can significantly affect the strength, hardness, and other qualities of the final cast component.
- Carbon steel: Commonly used for general-purpose applications.
- Alloy steel: Offers superior strength and toughness for specialized applications.
- Stainless steel: Used when corrosion resistance is critical.
Steel Alloy Components
Alloy Type | Characteristics | Common Uses |
---|---|---|
Carbon Steel | Strong and ductile | Automotive parts, pipelines |
Alloy Steel | Tough, heat-resistant | Aerospace, industrial parts |
Stainless Steel | Corrosion-resistant | Marine, medical, food sectors |
3. What Are the Basic Steps in the Steel Casting Process?
The basic steps in steel casting involve preparing the mold, melting the steel, pouring the steel into the mold, and cooling it to solidify. These steps are essential for achieving the desired properties of the final product.
Each of the basic steps plays a crucial role in ensuring the quality of the final steel casting. Let’s break down each of these steps in more detail.
1. Mold Preparation
The first step is preparing the mold. This can be done using various materials, such as sand, metal, or ceramic, depending on the requirements of the casting.
- Mold Material Selection: Sand molds are often used for simpler, less complex shapes, while metal molds are chosen for high-precision and high-volume castings.
- Mold Coating: Applying a coating to the mold helps to prevent the molten metal from sticking to it and ensures the smooth surface of the casting.
Mold Material Comparison
Mold Type | Benefits | Common Applications |
---|---|---|
Sand Mold | Cost-effective, versatile | General-purpose castings |
Metal Mold | High precision, reusable | Automotive, aerospace |
Investment Mold | High accuracy, complex designs | Jewelry, aerospace components |
2. Melting Steel
Steel must be melted to a high temperature before it can be poured into the mold. This is typically done in a furnace using techniques like induction heating or electric arc furnaces.
- Heat Control: Proper temperature control is critical. Too much heat can lead to metal loss, while too little can result in an incomplete or weak casting.
Furnace Types for Melting Steel
Furnace Type | Benefits | Applications |
---|---|---|
Induction Furnace | Efficient, quick | Small to medium steel parts |
Electric Arc Furnace | Large scale, high quality | Steel refining, large castings |
3. Pouring Steel into the Mold
Once the steel is melted, it is carefully poured into the prepared mold.
- Pouring Speed: The speed at which the steel is poured can affect the quality of the casting. Pouring too fast can lead to defects like bubbles or uneven filling.
- Controlled Environment: Pouring in a controlled environment ensures that the steel cools at a uniform rate, minimizing the chances of cracks or defects.
Pouring Conditions
Condition | Effect | Best Practices |
---|---|---|
Pouring Speed | Affects uniformity | Maintain steady, controlled pour |
Pouring Temperature | Prevents premature cooling | Consistent high temperatures |
4. Cooling and Solidification
After pouring, the steel is left to cool and solidify. This is a delicate phase where the cooling rate must be controlled to ensure that the casting is strong and free from defects.
- Cooling Rate: Faster cooling can lead to brittleness, while slower cooling might cause the formation of unwanted microstructures.
- Solidification: As the steel cools, it begins to solidify, taking the shape of the mold. This phase must be carefully managed to avoid issues such as shrinkage or misalignment.
Cooling Rate and Its Impact
Cooling Rate | Impact on Casting | Recommended Cooling Practices |
---|---|---|
Fast Cooling | May cause brittleness | Gradual cooling in controlled environment |
Slow Cooling | Reduces defects | Use controlled cooling methods to prevent internal stresses |
5. Finishing the Castings
Once the casting has cooled and solidified, it is removed from the mold. This part of the process includes cutting, grinding, and finishing the steel casting to meet the required specifications.
- Surface Finishing: To improve the surface quality, processes like sandblasting, polishing, and coating are applied.
- Non-Destructive Testing: Castings are often subjected to non-destructive tests, such as ultrasonic testing or x-ray inspection, to ensure they meet the required strength and quality standards.
Surface Treatment and Testing
Method | Purpose | Common Uses |
---|---|---|
Sandblasting | Surface smoothing | Final finishing of castings |
Polishing | Glossy finish | Decorative or precision parts |
Ultrasonic Testing | Detects internal flaws | Structural and aerospace castings |
4. How Are Molds Created for Steel Casting?
Creating the right mold is a vital step in the steel casting process. The mold dictates the final shape and structure of the casted part.
Mold creation is a precise and detailed process, as the mold must withstand the high temperature of molten metal without degrading. There are several different types of molds used, each serving different needs in the casting process.
- Sand Molds: These are the most common type of molds and are made from a mixture of sand and binder materials. They are relatively cheap and ideal for producing large quantities of castings.
- Metal Molds: These are used for high-precision castings that require a fine finish and higher strength. They are reusable and can handle higher temperatures.
- Investment Molds: Often used for producing highly complex and intricate designs, investment casting molds are made by coating a wax pattern with a ceramic shell.
Mold Type | Benefits | Common Applications |
---|---|---|
Sand Mold | Cost-effective, versatile | General-purpose castings |
Metal Mold | High precision, reusable | Automotive, aerospace |
Investment Mold | High accuracy, complex designs | Jewelry, aerospace components |
5. How Is Metal Prepared for Steel Casting?
The preparation of metal before casting is essential to achieve the desired properties of the final product. This involves melting the metal, adjusting its composition, and ensuring that it is in the right state for pouring.
Proper metal preparation ensures that the steel maintains its integrity and meets the required specifications. Here are some key steps in metal preparation:
- Melting Techniques: Steel is melted in a furnace using different methods such as induction heating or electric arc furnaces.
- Alloy Composition: Steel alloys may be added to adjust the composition, providing specific properties like improved strength, corrosion resistance, or heat resistance.
Preparation Step | Method Used | Key Considerations |
---|---|---|
Melting | Induction Furnace, Arc Furnace | Control temperature precisely |
Alloying | Adding Carbon, Chromium, Nickel | Tailor strength, resistance |
6. What Happens During the Cooling and Solidification Phase?
Cooling and solidification is one of the most crucial steps in the steel casting process. It directly affects the mechanical properties and surface quality of the final casting.
During this phase, the molten steel cools in the mold and solidifies. Proper control of the cooling rate ensures that the casting is free of defects such as cracks or warping. If the cooling process is not properly managed, internal stresses can form, which may affect the casting’s overall strength and durability.
Cooling Rate and Its Impact on Solidification
Cooling Rate | Impact on Casting Quality | Cooling Method Used |
---|---|---|
Rapid Cooling | May cause brittleness and defects | Controlled environment cooling |
Slow Cooling | Enhances strength and reduces internal stresses | Air or furnace cooling |
The cooling rate can influence the structure of the steel and its final mechanical properties. Slow cooling often results in a more homogeneous microstructure, reducing brittleness and increasing strength. However, if the cooling is too slow, there may be problems like uneven shrinkage or distortion, which can lead to poor dimensional accuracy.
Furthermore, controlling the cooling phase can help avoid defects such as porosity and cracks that may weaken the casting.
7. How Are Steel Castings Finished?
Once the steel has cooled and solidified, the next step is finishing the casting. This step ensures that the casting meets both dimensional and surface quality requirements.
The finishing process includes several key activities like cutting, grinding, polishing, and sometimes coating, to improve the final product’s appearance and function. Steel castings often require surface treatments to enhance corrosion resistance and strength.
Common Steel Casting Finishing Techniques
Technique | Purpose | Common Applications |
---|---|---|
Grinding | Removes excess material | High-precision components |
Polishing | Enhances surface finish | Decorative parts, aerospace |
Sandblasting | Removes impurities | Automotive, industrial parts |
Coating | Provides corrosion resistance | Marine, construction industries |
Each of these finishing techniques plays a role in ensuring that the steel casting meets the required specifications, whether it’s for aesthetic purposes or functional performance in critical applications.
8. How Are Steel Castings Tested for Quality?
Quality control is essential in the steel casting process. The tests performed ensure that the steel casting meets the desired standards for strength, durability, and precision.
Quality control for steel castings involves various non-destructive tests (NDT), including ultrasonic testing, x-ray inspection, and visual inspections. These tests allow manufacturers to check for internal defects without damaging the part.
Key Quality Control Tests
Test Type | Purpose | Common Applications |
---|---|---|
Ultrasonic Testing | Detects internal flaws such as cracks | Aerospace, automotive parts |
X-ray Inspection | Checks for internal voids and porosity | Critical structural components |
Visual Inspection | Identifies surface defects or imperfections | General-purpose castings |
Through these tests, manufacturers can ensure the integrity of each steel casting before it reaches the customer.
9. What Are the Different Types of Steel Castings?
Steel castings can be categorized based on the alloy used, the complexity of the casting, and the specific application. The most common types of steel castings include carbon steel, alloy steel, and stainless steel.
Different types of steel castings offer unique advantages for specific applications, allowing manufacturers to select the right material for each casting based on the project’s requirements. Understanding the types of steel castings available is crucial for choosing the correct one for your needs.
Types of Steel Castings
Casting Type | Characteristics | Common Uses |
---|---|---|
Carbon Steel | Cost-effective, ductile | General manufacturing, pipes |
Alloy Steel | High strength, tough | Aerospace, automotive |
Stainless Steel | Corrosion-resistant | Food processing, marine parts |
Each of these casting types offers specific benefits, from general use to specialized applications. Carbon steel is widely used for general purposes, while alloy steel and stainless steel offer higher strength and resistance to corrosion.
10. How Does Steel Casting Compare to Other Metal Forming Processes?
Steel casting is one of several metal-forming techniques used in manufacturing, and it offers distinct advantages when it comes to producing complex parts. However, other methods such as forging, machining, and welding have their own benefits depending on the application.
Compared to other metal-forming processes, steel casting offers more flexibility in producing intricate shapes, though it may not be as fast or cost-effective as forging or machining for simpler parts. Understanding the differences between steel casting and other methods can help manufacturers decide which process is best for their needs.
Steel Casting vs. Other Methods
Process | Advantages | Disadvantages |
---|---|---|
Steel Casting | Complex shapes, high durability | Slower, higher cost for small runs |
Forging | Stronger, more precise | Limited to simpler shapes |
Machining | Highly precise, versatile | Material waste, slow for large quantities |
Welding | Strong, flexible | Requires more post-processing |
Each process has its pros and cons. Steel casting stands out for producing parts with complex geometries that would be difficult or expensive to achieve using other methods.
11. What Are the Common Defects in Steel Castings?
Even with meticulous care, defects can still occur during the steel casting process. Understanding common casting defects helps manufacturers improve the process and achieve higher-quality outcomes.
Common defects in steel castings include porosity, cracks, and misalignment, which can significantly affect the strength and integrity of the part. Identifying these defects early can save costs and reduce rework or scrap rates.
Common Defects and Causes
Defect | Cause | Prevention Methods |
---|---|---|
Porosity | Gas trapped during pouring | Control pouring speed and temperature |
Cracks | Cooling stresses, thermal shock | Slow, controlled cooling |
Misalignment | Mold errors or improper pouring | Use precise mold preparation |
Preventing these defects requires a detailed understanding of the casting process, including pouring, cooling, and mold preparation.
12. How Is Steel Casting Used in Various Industries?
Steel casting is a versatile manufacturing method used across multiple industries. It provides parts that are critical in industries such as automotive, aerospace, and energy.
Steel castings are ideal for applications that require high strength and durability under extreme conditions. From large engine parts to structural components, steel casting is relied upon for producing components that can withstand wear, pressure, and temperature.
Steel Casting Applications by Industry
Industry | Application | Example Castings |
---|---|---|
Automotive | Engine blocks, transmission parts | Automotive components |
Aerospace | Structural components | Turbine blades, frames |
Energy | Pressure vessels, turbines | Power plant components |
Marine | Ship hulls, engine parts | Ship structural components |
Steel casting plays a significant role in ensuring the reliability and longevity of critical components used in various industries.
13. How Is Steel Casting’s Environmental Impact Managed?
The steel casting process can have environmental impacts, particularly in terms of emissions and waste materials. However, modern casting techniques have become more environmentally friendly through advancements in technology and sustainable practices.
Reducing the environmental footprint of steel casting involves controlling emissions, recycling materials, and improving energy efficiency. These improvements help reduce the overall impact on the environment while maintaining the efficiency and cost-effectiveness of the process.
Environmental Best Practices in Steel Casting
Practice | Benefit | Impact on Environment |
---|---|---|
Emission Control | Reduces harmful gases | Improves air quality |
Recycling Materials | Reduces waste and material costs | Conserves natural resources |
Energy Efficiency | Decreases energy consumption | Lowers greenhouse gas emissions |
By adopting these best practices, steel casting can be more sustainable and contribute less to pollution while maintaining high production quality.
14. What Are the Benefits of Steel Casting in Manufacturing?
Steel casting offers several advantages in manufacturing, particularly in producing complex and durable components at a cost-effective price.
The benefits of steel casting include the ability to produce intricate parts, its cost-effectiveness for large-scale production, and the high durability of the final products. These advantages make steel casting a go-to method for many industries, from automotive to aerospace.
Benefits of Steel Casting
Benefit | Description | Common Applications |
---|---|---|
Complex Shapes | Enables the creation of intricate designs | Aerospace, automotive |
Cost-effective | Lower cost for mass production | Construction, automotive |
Durability | Strong, long-lasting parts | Structural components, energy |
Steel casting remains one of the most valuable techniques for creating parts that need to be strong, durable, and complex in design.
15. How Is the Future of Steel Casting Shaping Up?
The future of steel casting looks promising, with ongoing innovations improving efficiency, sustainability, and the range of applications.
The future of steel casting includes advancements in automation, 3D printing, and AI integration, making the process even more precise and efficient. These developments are pushing the boundaries of what can be achieved with steel casting, opening doors to new possibilities for manufacturers.
Emerging Trends in Steel Casting
Trend | Description | Potential Impact |
---|---|---|
Automation | Robotics and automated processes | Increased precision, reduced labor costs |
3D Printing | Rapid prototyping and complex part creation | More design flexibility, faster turnaround |
AI Integration | AI-driven optimization of casting processes | Improved quality control, reduced waste |
With these trends, the future of steel casting holds great potential for greater productivity, lower costs, and more sustainable practices.
Conclusion
Steel casting is a critical process used to create high-quality, durable steel parts for various industries. By understanding the basic steps involved, manufacturers can produce parts that meet the required standards for strength and durability. The process involves careful preparation, precise pouring, and cooling to ensure that each cast part is reliable and defect-free.
FAQ
- Q1: What is the steel casting process?
Steel casting is the process of pouring molten steel into a mold where it solidifies into the desired shape. It’s used to create parts for various industries. - Q2: How does the steel casting process work?
The process includes preparing the mold, melting the steel, pouring it into the mold, allowing it to cool and solidify, and finishing the casting by cutting or grinding it. - Q3: What materials are used in steel casting?
Steel casting uses materials such as carbon steel, alloy steel, and stainless steel, each selected based on the application’s requirements. - Q4: How can defects in steel castings be avoided?
Defects can be avoided by controlling the pouring speed, temperature, and cooling process, as well as ensuring the mold and steel composition are correct. - Q5: What are the benefits of steel casting in manufacturing?
Steel casting offers cost-effectiveness, the ability to create complex shapes, and provides durable, strong parts suitable for demanding applications.