A356 Aluminum Alloy is a popular choice in various industries due to its excellent properties such as strength, corrosion resistance, and workability. It is commonly used in the manufacturing of critical parts and components for the automotive, aerospace, and industrial machinery sectors. This article will dive deep into the characteristics, applications, and benefits of A356 Aluminum, exploring its unique features and why it is often the material of choice in numerous manufacturing processes.
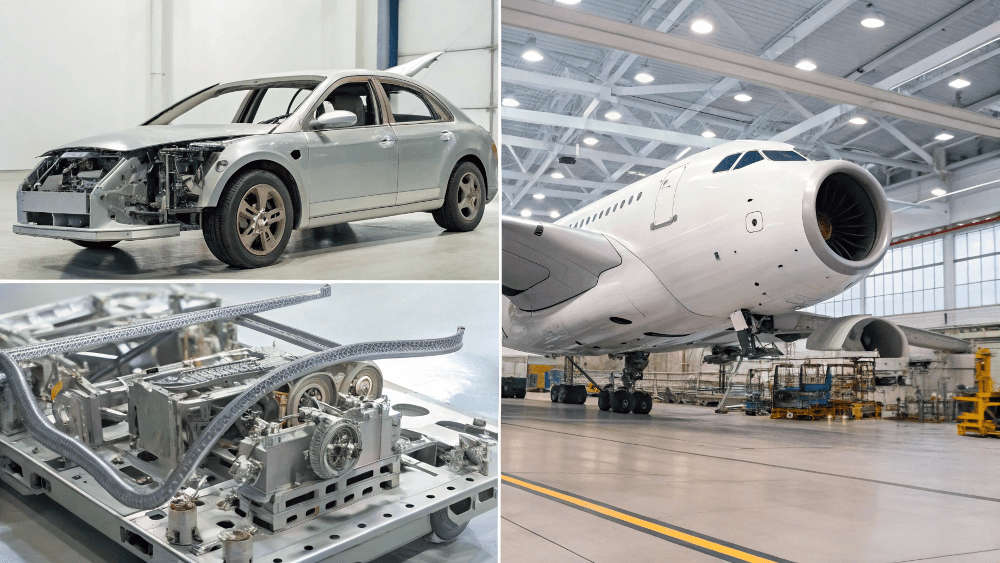
1. Introduction: Understanding A356 Aluminum
A356 Aluminum is a specific alloy used widely for casting applications. It is primarily made up of aluminum, silicon, and magnesium, and is known for its high-strength properties, durability, and excellent resistance to corrosion. This alloy is most commonly utilized in sand casting, die casting, and permanent mold casting, where its physical properties are highly valued.
But here’s the kicker—A356 aluminum isn’t just durable; it’s also highly versatile. This makes it the go-to choice for industries ranging from automotive manufacturing to aerospace. In this section, we will explore the key features of A356 Aluminum and its widespread use in the manufacturing industry.
Composition and Properties of A356 Aluminum
A356 Aluminum has a unique composition that gives it a strong balance of properties suitable for both lightweight and highly durable applications. The combination of aluminum with silicon and magnesium enhances the alloy’s casting characteristics and strength.
The aluminum content in A356 ensures lightness while silicon increases fluidity during the casting process. Magnesium is included to improve strength, especially under elevated temperatures. These properties make A356 ideal for producing complex parts that require both strength and lightness.
What’s the real story? The reason A356 aluminum is so widely used in the industry is that it provides manufacturers with a combination of lightweight properties, strength, and casting versatility.
Common Uses of A356 Aluminum
Some of the common applications of A356 aluminum include engine blocks, wheels, cylinder heads, and other automotive components. It’s also widely used in the aerospace industry for parts such as aircraft structural components, engine mounts, and landing gear parts. The material is chosen for these uses because it provides the necessary strength while being much lighter than other metals such as steel.
Below is a table summarizing the main uses of A356 Aluminum:
Uses of A356 Aluminum
Industry | Common Applications | Benefits |
---|---|---|
Automotive | Engine blocks, cylinder heads, wheels | Lightweight, strong, and durable |
Aerospace | Aircraft structural components, mounts | High strength-to-weight ratio, corrosion-resistant |
Industrial | Machinery parts, equipment housings | Excellent castability and strength |
2. The Composition of A356 Aluminum
Ready for the good part? The composition of A356 Aluminum is what makes it stand out from other alloys. A356 contains several key elements that determine its properties, such as its strength, resistance to corrosion, and casting behavior.
The primary components of A356 are:
- Aluminum (Al): The base metal that forms the majority of the alloy. It provides excellent lightweight properties.
- Silicon (Si): Silicon is added to enhance the fluidity of the molten aluminum, making it ideal for casting complex parts.
- Magnesium (Mg): This element increases the strength of the alloy, especially under high temperatures.
- Iron (Fe): Iron can be present in small amounts to increase the hardness of the alloy.
- Copper (Cu) and Zinc (Zn): These trace elements can sometimes be added to further improve the strength of the alloy.
The precise ratio of these elements makes A356 highly suited for casting, as well as for applications where strength and heat resistance are critical.
A356 aluminum’s composition is carefully engineered to optimize its properties, offering manufacturers the flexibility they need to create high-quality components. But here’s the kicker—this alloy can be tailored to meet specific requirements, such as varying degrees of strength or corrosion resistance, making it versatile for many industries.
Impact of Composition on Performance
The combination of these elements results in a metal that offers excellent mechanical properties. For example, the silicon content enhances fluidity and reduces shrinkage, making the alloy easier to cast. The addition of magnesium provides high strength and improved wear resistance, which is essential for automotive and aerospace applications.
Here’s a table that outlines the typical composition of A356 Aluminum:
Typical Composition of A356 Aluminum
Element | Percentage Range |
---|---|
Aluminum (Al) | 85-94% |
Silicon (Si) | 6-7% |
Magnesium (Mg) | 0.3-0.45% |
Iron (Fe) | 0.15-0.25% |
Copper (Cu) | 0.1-0.2% |
Zinc (Zn) | 0.1% |
3. Key Properties of A356 Aluminum
A356 Aluminum stands out due to its remarkable balance of strength, lightness, and durability. It is commonly used in industries that require high-performance materials for structural components and parts that are exposed to extreme conditions.
What’s the real story? The main properties that set A356 apart include its high strength-to-weight ratio, corrosion resistance, and excellent casting performance.
High Strength-to-Weight Ratio
One of the standout features of A356 Aluminum is its strength-to-weight ratio. This makes it particularly suitable for the automotive and aerospace industries where weight savings are critical. A356 offers comparable strength to steel, but at a fraction of the weight, making it an ideal choice for engine components and structural parts.
Corrosion Resistance
A356 Aluminum exhibits excellent resistance to corrosion, especially in harsh environments. Its high silicon content improves the alloy’s ability to resist oxidation, making it highly reliable in both marine and outdoor applications.
Workability and Castability
The high fluidity of A356 Aluminum in its molten state allows it to be cast into complex shapes with excellent surface finish. This makes it a favorite in the automotive and aerospace sectors, where intricate designs are often required.
Here’s the deal—A356 aluminum’s unique properties make it highly desirable in industries that demand precision and high performance from their materials.
Below is a table summarizing the key properties of A356 Aluminum:
Key Properties of A356 Aluminum
Property | Description |
---|---|
Strength-to-Weight Ratio | Comparable to steel, but lighter |
Corrosion Resistance | Excellent resistance to oxidation |
Workability | High fluidity for casting complex shapes |
Heat Resistance | Suitable for high-temperature applications |
4. Common Applications of A356 Aluminum
A356 Aluminum is extensively used in various industries that require lightweight, high-strength materials. From the automotive sector to aerospace, A356 is an ideal alloy for applications where both performance and durability are essential.
But here’s the kicker—A356 aluminum’s versatility doesn’t stop at automotive and aerospace applications. It also has applications in the marine, military, and general manufacturing industries, where its corrosion resistance and strength make it a top choice.
Automotive Industry
A356 Aluminum is widely used in the automotive industry, particularly for engine blocks, cylinder heads, and wheels. The alloy’s light weight and excellent strength make it an ideal choice for automotive components that need to withstand high stresses and harsh operating conditions.
Aerospace and Military
In aerospace, A356 is used for structural components like aircraft wings, engine components, and other high-performance parts. Its high strength-to-weight ratio is a critical factor in the aerospace industry, as it helps reduce the overall weight of the aircraft without sacrificing strength or durability.
Industrial Machinery and Equipment
A356 Aluminum is also used in industrial machinery and equipment, particularly for parts that require precision and durability. Its excellent casting properties and resistance to wear and corrosion make it ideal for producing components used in harsh industrial environments.
Below is a table highlighting some of the key applications of A356 Aluminum:
A356 Aluminum Applications
Industry | Common Applications | Benefits |
---|---|---|
Automotive | Engine blocks, cylinder heads, wheels | Lightweight, strong, and durable |
Aerospace | Aircraft structural components, engine parts | High strength-to-weight ratio, corrosion-resistant |
Industrial | Machinery components, equipment housings | Excellent castability and strength |
5. Advantages of Using A356 Aluminum Alloy
A356 Aluminum is widely used for its numerous advantages, which include its strength, workability, and cost-effectiveness. Whether for casting or high-performance applications, A356 provides manufacturers with a reliable material that meets the demands of various industries.
What’s the real story? A356 aluminum offers the perfect balance of performance and cost, making it the top choice for industries that need a strong, lightweight material that won’t break the bank.
Cost-Effectiveness
Despite its superior properties, A356 Aluminum remains relatively cost-effective. It is cheaper to produce compared to other high-strength alloys, making it an attractive choice for manufacturers who want to reduce material costs without compromising on quality.
Excellent Castability
A356 Aluminum offers excellent castability, meaning that it can be easily molded into complex shapes without losing its structural integrity. This is essential for industries that need parts with intricate designs or tight tolerances.
Durability
A356 Aluminum’s durability is another key advantage. Its excellent corrosion resistance and high strength make it an ideal choice for parts that need to withstand harsh environments, such as automotive engine components or aerospace structural elements.
Here’s a table summarizing the main advantages of A356 Aluminum:
Advantages of A356 Aluminum
Advantage | Description |
---|---|
Cost-Effectiveness | Lower cost compared to other high-strength alloys |
Castability | Excellent flow properties for complex shapes |
Durability | High resistance to corrosion and wear |
6. Manufacturing A356 Aluminum: The Casting Process
Ready for the good part? The manufacturing process for A356 Aluminum involves a few key stages that are critical to ensuring the alloy retains its desired properties. The casting process is one of the most important steps in producing high-quality A356 components.
A356 Aluminum is primarily manufactured using the sand casting and die casting methods. Both processes offer unique benefits depending on the application, but they share the common goal of producing strong, durable parts.
Sand Casting
Sand casting involves pouring molten A356 Aluminum into a mold made of sand. This method is particularly effective for producing large and intricate parts that would be difficult to create using other methods. It’s widely used in the production of engine blocks and automotive components.
Die Casting
Die casting involves injecting molten A356 Aluminum into a steel mold under high pressure. This method is more suitable for producing high-volume parts with intricate details, such as aerospace and industrial components. The die casting process ensures that each part produced is highly precise, with excellent surface finish and minimal defects.
Below is a table summarizing the key casting methods used for A356 Aluminum:
Casting Methods for A356 Aluminum
Method | Advantages | Common Applications |
---|---|---|
Sand Casting | Suitable for large, complex parts | Engine blocks, automotive components |
Die Casting | Ideal for high-volume, detailed parts | Aerospace components, industrial machinery |
7. Heat Treatment of A356 Aluminum Alloy
A356 Aluminum’s heat treatment process plays a crucial role in optimizing its mechanical properties, making it suitable for demanding applications. This is where it gets interesting—by altering the temperature and cooling rate during heat treatment, manufacturers can significantly improve A356’s strength and hardness.
Steps Involved in Heat Treating A356 Aluminum
The heat treatment of A356 Aluminum typically involves three main steps: solution heat treatment, quenching, and aging.
- Solution Heat Treatment: This step involves heating the aluminum to a high temperature (around 500°C), allowing the alloy to reach a solid solution. This ensures that the aluminum has a uniform microstructure.
- Quenching: After reaching the desired temperature, the aluminum is rapidly cooled, usually by immersion in water. Quenching locks the elements in place, preventing them from forming unwanted phases.
- Aging: The final step involves heating the material at a lower temperature to allow the alloy to mature, improving its strength and hardness. The aging process can be natural or artificial, depending on the application.
What’s the catch? While heat treatment enhances the strength and durability of A356 Aluminum, it’s important to carefully control the process. Improper heat treatment can lead to issues like warping or reduced material strength.
Effects of Heat Treatment on A356 Aluminum
Heat treatment can increase the tensile strength and yield strength of A356 Aluminum, making it more suitable for high-stress applications. It also improves the alloy’s wear resistance and reduces the likelihood of cracking during operation.
Below is a table that highlights the key changes in properties due to heat treatment:
Heat Treatment Effects on A356 Aluminum
Process | Property Improved | Effect on Performance |
---|---|---|
Solution Heat Treatment | Uniform microstructure | Improved strength and durability |
Quenching | Hardness | Higher resistance to wear and fatigue |
Aging | Strength, hardness | Enhanced strength for high-stress use |
8. A356 Aluminum in the Automotive Industry
Here’s the deal—the automotive industry has been one of the largest adopters of A356 Aluminum, particularly for components that require both high strength and low weight. A356 Aluminum is commonly used for engine blocks, cylinder heads, wheels, and other critical parts.
Why A356 Aluminum is Ideal for Automotive Parts
A356 Aluminum’s strength-to-weight ratio makes it a superior choice in automotive manufacturing. The lightweight nature of A356 helps improve fuel efficiency without sacrificing the strength needed for high-performance components. The alloy’s excellent casting properties allow manufacturers to create complex designs that wouldn’t be possible with other materials.
Examples of Automotive Components Made from A356 Aluminum
- Engine Blocks: A356 is commonly used for making engine blocks due to its excellent machinability and durability. It can withstand the high temperatures and pressures inside an engine.
- Cylinder Heads: A356’s thermal conductivity and strength make it ideal for cylinder heads, which must resist high stress and heat.
- Wheels: The alloy’s lightweight nature helps reduce the overall weight of the vehicle, improving fuel efficiency and handling.
Below is a table summarizing the automotive applications of A356 Aluminum:
A356 Aluminum in Automotive Applications
Component | Application | Benefits |
---|---|---|
Engine Blocks | Used in automotive engines | Lightweight, durable, high performance |
Cylinder Heads | Used in internal combustion engines | High heat resistance, machinable |
Wheels | Used in car wheels | Lightweight, strong, corrosion-resistant |
9. A356 Aluminum in Aerospace and Military Applications
A356 Aluminum’s properties make it a perfect fit for the aerospace and military industries, where performance and reliability are non-negotiable. This is where it gets interesting—A356 Aluminum’s strength-to-weight ratio is especially valuable in these industries, where reducing weight without compromising performance is crucial.
Aerospace Applications of A356 Aluminum
In the aerospace industry, A356 Aluminum is used to produce lightweight yet strong parts that are essential for aircraft performance. Components like wing spars, engine mounts, and fuselage parts often rely on A356 due to its high strength and ability to withstand extreme operating conditions.
Military Applications of A356 Aluminum
In military applications, A356 Aluminum is used for creating parts that need to endure high stress, fatigue, and exposure to harsh environments. It’s often found in vehicle components, weaponry, and aerospace defense applications, where both strength and weight reduction are vital.
Here’s a table summarizing aerospace and military applications for A356 Aluminum:
A356 Aluminum in Aerospace and Military
Industry | Applications | Benefits |
---|---|---|
Aerospace | Wing spars, engine mounts, fuselage parts | Lightweight, strong, fatigue-resistant |
Military | Military vehicle components, aerospace defense | High strength, corrosion-resistant |
10. Challenges with A356 Aluminum Alloy
You might be wondering—despite all its advantages, A356 Aluminum is not without its challenges. Like any material, it comes with its own set of difficulties that need to be managed during production and application.
Issues in the Casting Process
One of the biggest challenges with A356 Aluminum is its sensitivity to defects during the casting process. It can experience issues like porosity or shrinkage, which can affect the quality and performance of the final product. These issues arise when the material doesn’t flow properly or cools too quickly during casting.
Solutions to Overcome Casting Challenges
Manufacturers can overcome these challenges by using advanced casting techniques, such as controlled cooling and vacuum-assisted casting, to ensure the material is properly formed. Additionally, using precise mold designs and controlling the temperature of the molten aluminum can reduce defects.
Here’s a table highlighting common issues with A356 Aluminum and how to solve them:
Challenges and Solutions with A356 Aluminum
Issue | Solution | Description |
---|---|---|
Porosity | Use vacuum casting, controlled cooling | Reduces air pockets and improves casting quality |
Shrinkage | Precise mold design, temperature control | Minimizes shrinkage and ensures better product integrity |
11. A356 Aluminum Alloy vs. Other Aluminum Alloys
What’s the real story? How does A356 Aluminum compare to other popular aluminum alloys? In this section, we will compare A356 to alloys like A380 and 6061 Aluminum to understand why A356 is preferred in certain applications.
A356 vs. A380 Aluminum
A380 aluminum alloy is often used for high-volume casting because of its excellent castability. However, A356 aluminum is stronger and more durable, making it better suited for applications that require greater strength, such as engine components and aerospace parts. While A380 offers superior fluidity during casting, A356 is the better choice for high-stress environments.
A356 vs. 6061 Aluminum
6061 aluminum is known for its good mechanical properties and is often used in structural applications. However, A356 has better casting properties, making it the preferred choice for complex cast parts. While 6061 may outperform A356 in welded structures, A356’s casting characteristics make it ideal for industries like automotive and aerospace.
Below is a table summarizing the differences between A356 Aluminum and other alloys:
A356 Aluminum vs. Other Alloys
Alloy | Strength | Castability | Common Applications |
---|---|---|---|
A356 | High | Excellent | Engine parts, aerospace, automotive |
A380 | Moderate | Excellent | High-volume cast parts |
6061 | High | Moderate | Structural parts, welded joints |
12. Recycling A356 Aluminum Alloy
Ready for the good part? One of the great things about A356 Aluminum is its recyclability. Aluminum alloys, including A356, can be recycled without losing their properties, making them an environmentally friendly choice.
The Importance of Recycling A356 Aluminum
Recycling aluminum helps reduce the need for raw material extraction, which has a significant environmental impact. Recycling A356 Aluminum can reduce energy consumption by up to 95% compared to extracting virgin aluminum. This is crucial for industries looking to reduce their environmental footprint.
The Process of Recycling A356 Aluminum
The recycling process for A356 Aluminum involves melting down scrap aluminum and re-casting it into new parts. This is a closed-loop process that reduces waste and ensures that the alloy’s quality is preserved.
Here’s a table summarizing the benefits of recycling A356 Aluminum:
Benefits of Recycling A356 Aluminum
Benefit | Description |
---|---|
Reduced Energy Consumption | Recycling saves up to 95% of energy compared to virgin production |
Reduced Environmental Impact | Less need for raw material extraction |
Cost Savings | Recycling helps manufacturers save on raw material costs |
13. Quality Control in A356 Aluminum Production
Quality control is essential in the production of A356 Aluminum to ensure that the final product meets all required specifications. But here’s the kicker—ensuring consistent quality requires precision throughout the entire manufacturing process, from casting to heat treatment.
Key Quality Control Measures
Some of the key quality control measures for A356 Aluminum production include:
- Visual Inspections: To detect defects like cracks, porosity, or other visible flaws.
- Tensile Testing: To measure the strength of the alloy under different conditions.
- Microstructure Analysis: To ensure the alloy has the correct composition and grain structure for optimal performance.
Importance of Quality Control
Inconsistent quality can lead to significant failures in parts made from A356 Aluminum. Therefore, manufacturers must implement stringent quality checks at every stage of production to ensure the final product meets the required standards.
Here’s a table summarizing the main quality control measures used in A356 Aluminum production:
Quality Control Measures for A356 Aluminum
Measure | Description | Purpose |
---|---|---|
Visual Inspections | Checking for visible defects | Ensures part integrity |
Tensile Testing | Measuring material strength | Confirms the alloy’s strength under stress |
Microstructure Analysis | Analyzing the alloy’s composition and grain | Ensures proper microstructure for performance |
14. Future Trends in A356 Aluminum Alloy
A356 Aluminum is likely to see continued improvements and innovations as manufacturing processes evolve. What’s the real story? Future trends in A356 Aluminum alloy could lead to even better performance, efficiency, and sustainability in manufacturing.
Technological Advancements
Advancements in casting techniques, heat treatment, and alloy design could further enhance A356 Aluminum’s properties, such as strength, durability, and recyclability. This could make A356 even more suitable for next-generation automotive, aerospace, and industrial applications.
The Role of Sustainability
As manufacturers continue to focus on sustainability, A356 Aluminum will play an important role. The alloy’s recyclability and energy-efficient production process make it an attractive material for companies looking to reduce their environmental impact while maintaining high performance.
Here’s a table summarizing future trends in A356 Aluminum:
Future Trends in A356 Aluminum
Trend | Description |
---|---|
Advanced Casting Techniques | Improvements in mold design and casting precision |
Increased Sustainability | More focus on recycling and reduced energy consumption |
Enhanced Alloy Properties | Better strength, durability, and resistance to extreme conditions |
15. Conclusion: Why A356 Aluminum is a Superior Choice
In conclusion, A356 Aluminum offers an ideal combination of strength, lightweight properties, and excellent casting capabilities, making it a preferred choice across a variety of industries. Its versatility and durability make it a superior material for automotive, aerospace, and industrial applications.
But here’s the kicker—the ongoing development of A356 Aluminum ensures that it will remain a top material in the future. Whether you’re looking to reduce weight in your product designs or need a material that can handle high-stress environments, A356 Aluminum remains one of the most reliable and cost-effective choices available.
FAQ Section
Q1: What is A356 aluminum?
A356 aluminum is a high-performance alloy known for its excellent casting properties, strength, and corrosion resistance. It is commonly used in the automotive, aerospace, and industrial sectors.
Q2: How does A356 aluminum work in casting?
A356 aluminum is highly fluid when molten, making it ideal for casting into complex shapes. Its excellent flow properties allow it to fill molds with intricate details and fine surface finishes.
Q3: What industries use A356 aluminum alloy?
A356 aluminum is widely used in the automotive, aerospace, military, and industrial machinery industries. Its strength, durability, and casting properties make it ideal for critical components in these sectors.
Q4: How does heat treatment affect A356 aluminum?
Heat treatment improves the strength, hardness, and wear resistance of A356 aluminum. It also enhances the alloy’s performance under high-stress conditions.
Q5: What makes A356 aluminum a good choice over other alloys?
A356 aluminum offers a unique balance of strength, lightness, corrosion resistance, and casting ability. These properties make it a versatile and reliable choice for demanding applications across various industries.