Aluminum sand casting is a widely used technique in manufacturing that involves pouring molten aluminum into a sand mold to create complex parts and components. This method is highly regarded for its versatility, cost-effectiveness, and ability to produce high-quality castings. Whether you are a seasoned manufacturer or a newcomer, understanding the aluminum sand casting process is essential for optimizing production and ensuring the durability of your parts. In this article, we’ll delve into the process itself, its advantages, common applications, and some tips to improve efficiency.
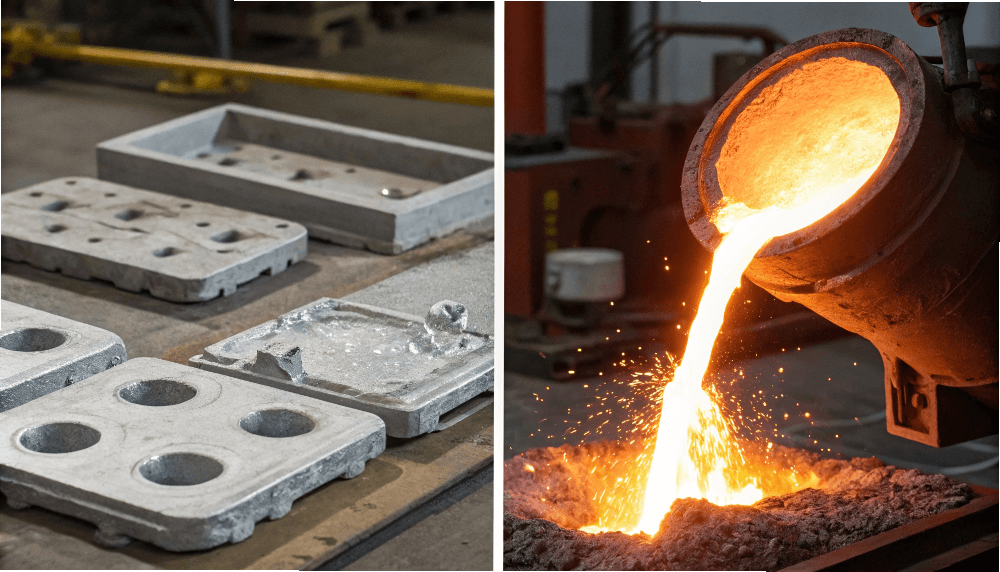
1. What is the Aluminum Sand Casting Process?
The aluminum sand casting process is one of the oldest and most widely used methods for producing aluminum parts. It involves creating a mold from sand, pouring molten aluminum into it, and allowing it to cool and solidify into the desired shape. The process has remained a staple in the casting industry due to its simplicity, affordability, and adaptability to various manufacturing needs. But here’s the kicker—despite its long history, sand casting continues to evolve, offering better results with each improvement in technique.
In the first step, a pattern of the part to be cast is made, typically from metal, wood, or plastic. This pattern is then placed into a sand mixture to create a mold. Once the mold is formed, molten aluminum is poured into the mold cavity and allowed to cool, forming the final cast product. This process allows for a wide range of designs, from simple geometric shapes to complex, intricate components.
Aluminum sand casting is favored in industries such as automotive, aerospace, and industrial machinery. Ready for the good part? Despite its simplicity, the process can create parts with excellent strength and durability, making it an attractive option for high-performance applications. Additionally, the flexibility of sand casting allows for the production of both large and small batches, making it ideal for manufacturers who require scalability in production.
Table: Key Steps in the Aluminum Sand Casting Process
Step | Description |
---|---|
Pattern Creation | A pattern is created from metal, wood, or plastic. |
Mold Formation | The pattern is placed into a sand mixture to form a mold. |
Molten Aluminum Pouring | Molten aluminum is poured into the mold cavity. |
Cooling and Solidifying | The mold is cooled, and aluminum solidifies into the shape. |
Mold Removal | Once solidified, the mold is removed, revealing the casting. |
2. What Are the Advantages of Aluminum Sand Casting?
Aluminum sand casting offers numerous advantages that make it a preferred choice in many manufacturing processes. One of the primary benefits is its cost-effectiveness. Unlike more advanced methods like die casting, which require expensive molds and machinery, sand casting requires relatively low initial investment in molds and equipment. This makes it an attractive option for companies looking to minimize overhead costs while maintaining high-quality production.
Another key benefit of aluminum sand casting is its versatility. This process allows manufacturers to produce parts of varying sizes, shapes, and designs. The mold can be easily altered to accommodate changes in design, making it a flexible solution for custom parts. Furthermore, aluminum’s lightweight nature makes it ideal for applications in industries like automotive and aerospace, where reduced weight is essential for performance.
This is where it gets interesting—aluminum sand casting also offers excellent mechanical properties. Cast aluminum parts produced through this method are known for their strength, durability, and resistance to corrosion. These properties make them suitable for demanding environments such as automotive engines, industrial equipment, and even marine applications. Aluminum’s ability to maintain its structural integrity under high temperatures also makes it an excellent material for casting.
Table: Advantages of Aluminum Sand Casting
Advantage | Description |
---|---|
Cost-Effective | Lower investment in molds and equipment compared to die casting. |
Versatility | Suitable for a wide range of sizes, shapes, and designs. |
Excellent Mechanical Properties | High strength, durability, and resistance to corrosion. |
3. What Are the Different Types of Sand Used in Aluminum Casting?
In the world of aluminum sand casting, not all sand is created equal. The choice of sand can significantly impact the quality of the cast, the speed of production, and the final cost. There are several types of sand used in the casting process, each with its own unique properties. The three main types are green sand, resin sand, and silica sand.
Green sand is the most commonly used type of sand in aluminum casting. It consists of silica sand mixed with clay, water, and other additives. This mixture is easy to mold and provides good flexibility, making it ideal for producing a wide range of parts. What’s the real story? Green sand molds can be reused multiple times, which helps reduce costs and improve efficiency.
Resin sand is another type of sand used in aluminum casting. It is made by mixing silica sand with a resin binder that hardens the mold. This type of sand produces molds with better surface finish quality and is often used for casting intricate designs. Resin sand is particularly effective in creating high-precision molds for industries such as aerospace and automotive.
Silica sand is the base material for most sand casting molds. Silica sand is prized for its high melting point, which allows it to withstand the heat of molten metal without breaking down. This makes it a perfect choice for high-temperature applications like aluminum casting. The most significant advantage of silica sand is its ability to form solid molds that retain their shape under pressure.
Table: Types of Sand Used in Aluminum Casting
Type of Sand | Key Characteristics | Applications |
---|---|---|
Green Sand | Mixture of silica sand, clay, and water, reusable mold. | General manufacturing, large parts. |
Resin Sand | Silica sand mixed with resin binder for finer molds. | Aerospace, automotive, intricate designs. |
Silica Sand | High melting point, retains shape under pressure. | High-temperature applications, engine parts. |
4. How Does the Aluminum Sand Casting Process Work?
The aluminum sand casting process involves several steps that require careful attention to detail. Let’s break it down: first, a pattern is created, typically made of metal or another durable material, to serve as a model for the mold. This pattern is then placed into a sand mixture, creating a cavity in the sand that will eventually hold the molten aluminum.
Next, the sand mold is packed around the pattern to form a complete mold shell. Once the mold is prepared, the pattern is removed, leaving behind an empty cavity. Molten aluminum is then poured into the cavity, filling the space left by the pattern. The mold is allowed to cool, and once the aluminum solidifies, the mold is broken away, revealing the cast aluminum part.
This is where it gets interesting—after the casting is complete, the part may require additional cleaning, finishing, or machining to meet the desired specifications. These secondary processes help to refine the surface, remove any excess material, and ensure the final product meets the necessary standards for strength, durability, and precision.
The aluminum sand casting process offers great flexibility when it comes to producing parts of varying sizes, shapes, and complexities. But here’s the kicker—the use of sand molds also allows for the cost-effective production of small to medium-sized batches, making it ideal for manufacturers that don’t require mass production but still need high-quality parts.
Table: Steps in Aluminum Sand Casting
Step | Description |
---|---|
Pattern Creation | A pattern is created using durable materials like metal. |
Mold Formation | The pattern is placed into a sand mixture to form a mold. |
Mold Compaction | Sand is packed tightly to form a solid and durable mold. |
Pouring Aluminum | Molten aluminum is poured into the mold to fill the cavity. |
Cooling & Solidifying | Aluminum is allowed to cool and solidify inside the mold. |
Mold Removal | The mold is broken away, revealing the aluminum casting. |
5. What Are the Common Applications of Aluminum Sand Casting?
Aluminum sand casting is used across a variety of industries, each with its own unique requirements. One of the most prominent industries where this method is used is automotive manufacturing. Aluminum sand casting allows for the production of engine blocks, transmission housings, and other critical automotive components. These parts are essential to the performance and safety of vehicles, and aluminum’s lightweight yet durable properties make it an ideal material for these applications.
Another major industry that relies heavily on aluminum sand casting is aerospace. Aircraft components such as landing gear, turbine housings, and engine components benefit from aluminum’s high strength-to-weight ratio. Aluminum sand casting is used to create complex and lightweight parts that are essential for the safe operation of aircraft.
In industrial machinery, aluminum sand casting is used to produce heavy-duty components such as gear housings, valve bodies, and pump casings. These parts must withstand significant wear and tear, and aluminum’s corrosion resistance helps ensure that the parts remain functional over long periods of time.
Let’s take a closer look—aluminum sand casting is also used in the marine industry to create corrosion-resistant parts such as boat propellers and engine components. This application benefits from aluminum’s ability to resist saltwater corrosion, ensuring longevity and reliability in harsh marine environments.
Table: Common Applications of Aluminum Sand Casting
Industry | Application | Benefits |
---|---|---|
Automotive | Engine blocks, transmission housings | Lightweight, durable, and high performance. |
Aerospace | Aircraft parts (landing gear, turbine) | High strength-to-weight ratio, complex shapes. |
Industrial Machinery | Gear housings, pump casings | Corrosion-resistant and long-lasting. |
Marine | Boat propellers, engine components | Saltwater corrosion resistance. |
6. What Equipment is Needed for Aluminum Sand Casting?
To successfully execute aluminum sand casting, a variety of equipment is required. The first piece of equipment is the molding machine, which is used to form the sand molds. These machines are essential for creating molds that are accurate and consistent. Depending on the size and complexity of the part being produced, molding machines can range from small, manual models to large, automated machines capable of high-volume production.
Another critical piece of equipment is the melting furnace. These furnaces are used to melt aluminum to a specific temperature before pouring it into the molds. Furnaces can be powered by gas, electricity, or induction, with each type offering specific advantages depending on the scale of production and energy efficiency needs.
Ready for the good part? A core shooting machine is also necessary for creating complex molds with internal cavities. This machine injects a mixture of sand and binder into a mold to create precise core shapes, which are essential for parts with hollow interiors.
In addition to the primary machines, there are other tools and equipment required for post-casting processes such as cutting tools, polishing machines, and cleaning equipment. These are used to refine the casting and remove any imperfections or excess material.
Table: Essential Equipment for Aluminum Sand Casting
Equipment | Function |
---|---|
Molding Machines | Used to form sand molds, ensuring consistency. |
Melting Furnace | Melts aluminum to the correct pouring temperature. |
Core Shooting Machine | Creates molds with complex internal cavities. |
Finishing Tools | Includes cutting, polishing, and cleaning tools. |
7. How Do You Prepare the Mold for Aluminum Sand Casting?
Preparing the mold for aluminum sand casting is a critical step in ensuring the quality of the final product. The mold is essentially a negative replica of the part that will be cast, and it must be made with precision to achieve the desired shape and quality. First, a pattern of the part is created. This can be made from materials like metal, wood, or plastic, depending on the complexity of the part and the number of units being produced.
Once the pattern is ready, it is placed into a sand mixture to form the mold. The sand mixture usually consists of a combination of silica sand, clay, and water, with sometimes additional materials like carbon to enhance the mold’s performance. This mixture is carefully packed around the pattern to create a tight and durable mold. The molding process involves compacting the sand around the pattern to ensure it holds its shape.
But here’s the kicker—mold compaction is one of the most important steps. The sand must be packed tightly enough to withstand the pressure of the molten aluminum but loose enough to allow for easy removal of the pattern. The amount of compaction determines the overall quality of the casting, and inconsistent compaction can lead to defects such as rough surfaces or air pockets in the mold.
Once the mold is formed, it is allowed to harden. Depending on the type of sand used and the complexity of the mold, this can take anywhere from a few hours to a full day. After the mold has solidified, the pattern is removed, leaving a cavity in the sand that is the exact shape of the part. This cavity is where the molten aluminum will be poured to create the final casting.
Table: Steps in Mold Preparation
Step | Description |
---|---|
Pattern Creation | A pattern is created using durable materials like metal. |
Sand Mixture Preparation | A mixture of silica sand, clay, and water is prepared. |
Mold Compaction | Sand is tightly packed around the pattern to form a mold. |
Pattern Removal | After molding, the pattern is removed, leaving a cavity. |
Mold Hardening | The mold is left to harden before aluminum pouring. |
8. How to Ensure the Quality of Aluminum Sand Castings?
Ensuring the quality of aluminum sand castings is paramount for achieving reliable, durable parts. Several factors contribute to the overall quality of the casting, and paying attention to these details can help avoid costly mistakes and ensure the success of the project. First and foremost, proper material selection is essential. The quality of the sand, aluminum, and binders used in the casting process plays a significant role in the strength and durability of the final product.
What’s the real story? Temperature control is another critical factor that directly affects the quality of the aluminum sand casting. The aluminum must be heated to the proper temperature to ensure it flows smoothly into the mold and fills the cavity completely. If the temperature is too low, the aluminum may not properly fill the mold, leading to incomplete or weak castings. Conversely, if the temperature is too high, the aluminum may react with the mold material, causing defects.
Mold quality is equally important. The sand mixture used to create the mold must be of high quality and properly prepared. If the sand mixture is too dry, the mold may not hold its shape, resulting in defects. If the mixture is too wet, it can cause problems with the aluminum’s surface finish and result in porosity in the final casting.
Another important factor is the cooling process. Cooling should be controlled to ensure the casting solidifies at the correct rate, which helps reduce the chances of cracking or distortion. Cooling too quickly can lead to thermal stresses, while slow cooling can cause the casting to shrink unevenly, resulting in defects.
Table: Quality Control Factors in Aluminum Sand Casting
Factor | Importance |
---|---|
Material Selection | Choosing high-quality sand, aluminum, and binders. |
Temperature Control | Ensuring proper aluminum pouring temperature for complete filling. |
Mold Quality | Using the correct sand mixture and compacting properly. |
Cooling Process | Controlling cooling rate to prevent defects like cracking. |
9. What Are the Challenges of Aluminum Sand Casting?
While aluminum sand casting is a reliable and cost-effective method, it does come with its own set of challenges. One of the biggest challenges is managing the defects that can occur during the casting process. Common defects in aluminum sand casting include porosity, shrinkage, and surface imperfections. These defects can significantly affect the performance and aesthetic of the final part.
Porosity occurs when gas bubbles are trapped inside the casting, creating holes or voids in the metal. This can weaken the part and make it unsuitable for high-performance applications. Shrinkage is another common issue that occurs when the aluminum solidifies and contracts, causing the casting to shrink unevenly. This can result in cracks, warping, or incomplete parts. Surface imperfections, such as rough surfaces or mold marks, can also be a problem, especially for parts that require a smooth finish.
What’s the real story? Managing heat is another challenge in aluminum sand casting. Aluminum must be poured at the right temperature to ensure it fills the mold properly. If the temperature is too low, the molten metal may not fill the mold completely. On the other hand, if the temperature is too high, the aluminum can react with the sand mold, leading to defects such as surface roughness or contamination of the casting.
Mold integrity is also a critical factor. The sand mold must be strong enough to withstand the pressure of the molten metal without breaking down. If the mold is not sufficiently compacted or the sand mixture is too weak, it can collapse or deform during the pouring process, leading to defects.
Table: Common Defects in Aluminum Sand Casting
Defect | Description | Impact |
---|---|---|
Porosity | Trapped gas bubbles create holes or voids in the metal. | Weakens the part and reduces its structural integrity. |
Shrinkage | Aluminum contracts unevenly during cooling. | Leads to cracks, warping, or incomplete parts. |
Surface Imperfections | Rough surfaces or mold marks left on the casting. | Impacts part aesthetics and functionality. |
10. How Do You Improve Aluminum Sand Casting Efficiency?
Improving the efficiency of aluminum sand casting can have significant benefits for manufacturers, from reducing production costs to improving quality and turnaround times. One of the most effective ways to improve efficiency is by optimizing the melting process. By ensuring that the aluminum is melted to the optimal temperature and maintaining a consistent pouring rate, manufacturers can reduce waste and ensure that each cast is as accurate as possible.
Ready for the good part? Automation plays a significant role in improving efficiency. Automated molding machines, pouring systems, and finishing tools can help streamline the production process, reducing manual labor and increasing production speed. These automated systems also reduce the risk of human error, improving the overall consistency and quality of the castings.
Another way to improve efficiency is by reducing waste. This can be achieved by optimizing the mold design, using the right type of sand mixture, and carefully controlling the pouring process. Minimizing waste reduces the amount of material used, lowering overall costs and reducing the environmental impact of the casting process.
Finally, improving quality control throughout the casting process is essential for boosting efficiency. By regularly inspecting the molds, monitoring temperature levels, and checking the castings for defects, manufacturers can catch potential issues early and address them before they result in costly delays or rework.
Table: Efficiency Improvement Strategies in Aluminum Sand Casting
Strategy | Description |
---|---|
Optimizing Melting Process | Maintaining the right temperature and consistent pouring. |
Automation | Using automated systems to speed up production and reduce errors. |
Waste Reduction | Optimizing mold design and sand mixture to reduce material waste. |
Quality Control | Implementing regular inspections and defect monitoring. |
11. What Are the Best Practices for Aluminum Sand Casting?
To achieve the best results in aluminum sand casting, there are several best practices that manufacturers should follow. First and foremost, proper mold preparation is crucial. This includes ensuring the mold is properly compacted, the pattern is accurate, and the sand mixture is of high quality. Mold preparation is the foundation of a successful casting process, and cutting corners here can lead to defects down the line.
But here’s the kicker—using the right alloy for the specific application is just as important. The alloy used in the casting process should be chosen based on the desired mechanical properties, such as strength, corrosion resistance, and thermal conductivity. The wrong alloy can result in poor casting quality and performance.
Post-casting cleaning and finishing are also vital. After the aluminum has cooled and solidified, the casting must be cleaned to remove any sand, mold residues, or excess material. This can be done through a variety of methods, such as sandblasting, tumbling, or chemical cleaning. Once cleaned, the casting may need to be finished using machining, polishing, or coating to achieve the desired surface quality and dimensions.
What’s the real story? Ensuring proper cooling is another best practice that cannot be overlooked. Cooling the casting at a controlled rate prevents issues like cracking, distortion, or uneven shrinkage. Controlled cooling also improves the structural integrity of the final part, making it more reliable for its intended use.
Table: Best Practices in Aluminum Sand Casting
Practice | Description |
---|---|
Proper Mold Preparation | Ensure mold is well-compacted and the sand mixture is of high quality. |
Correct Alloy Selection | Choose alloys based on the desired mechanical properties. |
Post-Casting Cleaning | Clean the casting to remove sand and other residues. |
Controlled Cooling | Cool the casting at a controlled rate to avoid defects. |
12. How Does Aluminum Sand Casting Compare to Other Casting Methods?
When it comes to casting aluminum parts, manufacturers often face the decision of choosing between aluminum sand casting, die casting, and investment casting. Each method has its own set of advantages and disadvantages, and the choice largely depends on the specific requirements of the part being produced.
Aluminum sand casting is generally more cost-effective for producing low to medium-volume parts, making it a great choice for custom or small-batch production. This method also allows for greater flexibility in the types of parts that can be produced, making it ideal for complex or irregular shapes. Sand casting also allows for a wider variety of materials and is easier to adjust to new designs or modifications, making it an excellent choice for prototype work or niche applications.
On the other hand, die casting is typically used for high-volume production runs. Die casting offers superior surface finish quality and tighter tolerances compared to sand casting. However, it requires more expensive molds and equipment, making it less cost-effective for small batches. Ready for the good part? Die casting is also more limited when it comes to part size and complexity compared to sand casting. Large or complex parts often require the use of sand casting to achieve the desired result.
Investment casting, also known as the lost-wax process, is used for producing parts with intricate geometries and high precision. Investment casting offers superior surface finishes and is ideal for parts that require complex designs. However, it is more expensive than both sand casting and die casting, making it better suited for high-precision, high-value parts.
In short, the best casting method depends on your specific needs—whether it’s cost, complexity, or production volume.
Table: Comparison of Aluminum Casting Methods
Casting Method | Ideal For | Advantages | Disadvantages |
---|---|---|---|
Sand Casting | Low to medium volume, complex shapes | Cost-effective, flexible, and versatile | Lower surface finish, larger tolerances |
Die Casting | High-volume production | High precision, excellent surface finish | Expensive molds, limited complexity |
Investment Casting | High-precision, intricate parts | Superior surface finish, high precision | High cost, limited material choices |
13. How Do You Handle and Transport Aluminum Sand Castings?
Handling and transporting aluminum sand castings require careful consideration to prevent damage and ensure the parts arrive at their destination in good condition. Once the castings are finished, they must be handled with care to avoid chipping, cracking, or scratching the surface. One key step in handling is the use of protective packaging. Castings are often wrapped in foam, bubble wrap, or custom-fitted padding to minimize the risk of damage during handling and transportation.
What’s the real story? Weight and size of the casting should also be considered when transporting. Large and heavy parts may require special equipment such as cranes or forklifts to handle safely. Additionally, using sturdy shipping containers and rigid packaging ensures that the castings are well-protected during transit.
Temperature control during transportation is also crucial, especially when shipping large quantities or fragile parts. Aluminum castings should be kept at a stable temperature to prevent warping or distortion, particularly if the castings have intricate shapes or thin sections. Proper storage conditions can significantly reduce the risk of quality issues that arise from transport.
Table: Handling and Transport Considerations for Aluminum Castings
Factor | Considerations |
---|---|
Protective Packaging | Use foam, bubble wrap, or custom packaging for damage prevention. |
Weight and Size | Use cranes or forklifts for large/heavy parts. |
Temperature Control | Ensure stable temperature during transportation. |
Sturdy Shipping Containers | Use rigid containers to protect castings during transit. |
14. What Are the Cost Factors in Aluminum Sand Casting?
Several cost factors come into play when determining the overall price of aluminum sand casting. First, there’s the cost of materials. The quality of the sand, the aluminum alloy, and other components like binders or coatings directly affect the cost. Choosing a higher-quality material can increase the overall cost of production but may result in a more durable and precise casting.
Next, the labor cost must be considered. Aluminum sand casting requires skilled labor to oversee the entire process, from mold preparation to finishing. Labor costs can vary depending on the complexity of the casting and the level of automation in the process.
Another cost factor is the equipment cost. Investment in high-quality machinery, such as molding machines, melting furnaces, and core shooting machines, adds to the overall expense of the process. However, the right equipment can increase production speed and efficiency, reducing costs in the long run.
Table: Key Cost Factors in Aluminum Sand Casting
Cost Factor | Description |
---|---|
Material Costs | Sand, aluminum alloy, binders, and coatings. |
Labor Costs | Skilled labor for mold preparation, casting, and finishing. |
Equipment Costs | Molds, furnaces, core shooters, and finishing machinery. |
15. How Can You Make Aluminum Sand Casting More Sustainable?
Sustainability is an increasingly important concern for manufacturers across industries, and aluminum sand casting is no exception. One of the primary ways to make aluminum sand casting more sustainable is by recycling materials. Sand can often be reused for multiple casting cycles, reducing the need for new sand and minimizing waste.
Energy efficiency is another area where sustainability can be improved. Optimizing the melting process can help reduce energy consumption, making the casting process more environmentally friendly. This can be achieved by using electric induction furnaces or other energy-efficient technologies.
Finally, reducing emissions from the casting process is another key sustainability consideration. Manufacturers can adopt cleaner technologies or implement stricter controls to reduce the environmental impact of their operations.
Table: Sustainability Considerations in Aluminum Sand Casting
Sustainability Factor | Practices to Implement |
---|---|
Recycling Materials | Reuse sand for multiple casting cycles. |
Energy Efficiency | Use electric induction furnaces to reduce energy consumption. |
Reducing Emissions | Implement cleaner technologies to minimize environmental impact. |
Conclusion
Aluminum sand casting is a versatile and cost-effective manufacturing process that is used in a wide range of industries, including automotive, aerospace, and industrial machinery. The process involves pouring molten aluminum into a sand mold to create complex parts, and its benefits include cost-effectiveness, versatility, and strength. By following best practices and optimizing the process, manufacturers can improve efficiency, reduce costs, and ensure high-quality castings.
FAQ Section
Q1: What is aluminum sand casting?
Aluminum sand casting is a process where molten aluminum is poured into a sand mold to create various metal parts, often used for complex shapes.
Q2: How does aluminum sand casting work?
The process involves creating a sand mold, pouring molten aluminum into the mold, and allowing it to cool and solidify into the desired shape.
Q3: What are the advantages of aluminum sand casting?
Aluminum sand casting is cost-effective, versatile, and provides strong, durable parts suitable for many industrial applications.
Q4: What equipment is required for aluminum sand casting?
Key equipment includes molding machines, melting furnaces, core shooters, and various finishing tools to shape the castings.
Q5: How do you ensure the quality of aluminum sand castings?
Ensuring quality involves controlling mold preparation, selecting the right materials, and maintaining proper temperature during pouring to avoid defects.