Die casting is an essential manufacturing process used in automotive parts production. It involves injecting molten metal under high pressure into a mold to create parts with exceptional precision and durability. In this article, we will explore the benefits of die casting in the automotive industry, the types of parts produced, and how it compares to other manufacturing methods. We will also discuss the materials used, the challenges faced, and the future of die casting in automotive production.
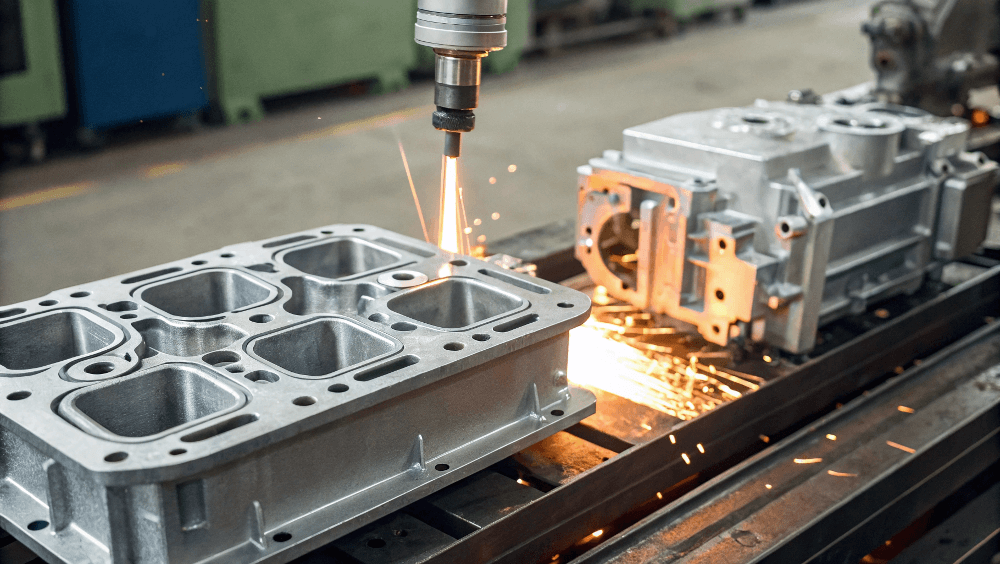
1. What is Die Casting in Automotive Parts Production?
Die casting is a highly efficient and precise method for creating automotive components. The process involves injecting molten metal into a mold under high pressure, allowing the material to cool and solidify into the desired shape. The main materials used for die casting in automotive parts are metals such as aluminum, magnesium, and zinc, which provide excellent strength, lightness, and resistance to wear. This manufacturing technique is widely used in the automotive industry due to its ability to produce high-quality, durable parts at a relatively low cost.
But here’s the kicker: die casting allows for complex geometries and intricate designs that are difficult to achieve using other manufacturing methods. The speed and consistency of the process make it ideal for mass production, where thousands or even millions of parts must be produced with identical specifications. The parts produced are typically lightweight, strong, and resistant to corrosion, making them perfect for use in automotive applications.
Table: Die Casting Process Overview
Step | Description |
---|---|
Material Selection | Choice of aluminum, magnesium, zinc, or copper alloys |
Mold Creation | A die (mold) is designed based on the desired part geometry |
Molten Metal Injection | Molten metal is injected into the mold at high pressure |
Cooling and Solidification | The molten metal cools and solidifies in the mold |
Ejection and Finishing | The part is ejected from the mold and any finishing processes are applied |
2. Why is Die Casting Used in Automotive Parts Production?
Die casting is a go-to method in automotive parts production due to its numerous advantages. Let’s break it down:
One of the key reasons die casting is used in automotive production is its cost-effectiveness. Compared to other manufacturing methods, die casting is relatively inexpensive in terms of both material and labor costs, particularly in high-volume production runs. The automated nature of die casting also reduces labor costs and minimizes human error, making it an efficient process for mass production.
Moreover, die casting ensures that parts are produced with high precision. This precision results in parts that fit together seamlessly, reducing the need for additional machining and ensuring high-quality finished products. The parts produced are also durable, offering resistance to impact, wear, and corrosion, which is essential for automotive applications.
What’s the real story? Die casting is also highly scalable. Whether you need to produce a small batch or millions of parts, die casting can accommodate a wide range of production volumes, making it ideal for both small and large automotive manufacturers.
Table: Cost Comparison of Die Casting vs. Other Methods
Manufacturing Method | Cost (per unit) | Efficiency | Precision | Material Waste |
---|---|---|---|---|
Die Casting | Low | High | High | Low |
Injection Molding | Moderate | High | Moderate | Low |
Sand Casting | High | Low | Moderate | High |
Forging | High | Low | High | Moderate |
3. What Are the Main Advantages of Die Casting in Automotive Parts?
The advantages of die casting in automotive parts production are numerous and far-reaching. One of the primary benefits is the ability to produce complex and intricate parts with tight tolerances. Unlike other manufacturing methods, die casting allows manufacturers to create parts with fine details that would otherwise require additional machining. This not only saves time but also reduces the risk of defects, ensuring parts meet stringent quality standards.
Furthermore, die casting offers excellent material efficiency. The process generates minimal waste, as the excess metal is usually recyclable. This makes it an environmentally friendly option for automotive manufacturers looking to minimize their carbon footprint.
Another significant advantage of die casting is its ability to create lightweight parts without compromising on strength. This is particularly important in the automotive industry, where reducing vehicle weight can improve fuel efficiency and reduce emissions. By using materials such as aluminum and magnesium, die casting helps create lightweight but strong parts that are essential for modern automotive design.
Ready for the good part? Die casting also allows for the integration of multiple functions into a single part. This reduces the need for additional components and assembly processes, leading to lower production costs and faster manufacturing times.
Table: Advantages of Die Casting in Automotive Parts
Advantage | Description |
---|---|
High Precision | Allows for tight tolerances and complex geometries |
Cost-Effective | Low production cost, especially in high-volume runs |
Material Efficiency | Minimal waste, recyclable materials used |
Lightweight | Parts are lightweight without compromising strength |
Function Integration | Multiple functions combined into a single part |
4. What Types of Automotive Parts Are Made Using Die Casting?
Die casting plays a pivotal role in the production of a wide variety of automotive components. These parts are typically used in the engine, transmission, and structural components of vehicles. Some of the most common automotive parts made using die casting include:
- Engine components: Die casting is used to manufacture parts such as engine blocks, cylinder heads, and valve bodies. These parts require high strength, heat resistance, and precision, all of which die casting can provide.
- Transmission parts: Die-cast parts such as gearboxes, shift forks, and housings are essential for the smooth operation of a vehicle’s transmission system. Die casting allows for the production of parts with tight tolerances and high durability.
- Structural components: The automotive industry also relies on die casting for the production of structural components like chassis parts, brackets, and supports. These parts must be strong enough to withstand stress and impact, which makes die casting a perfect choice.
What’s the real story? Die casting is used not only for small and medium-sized parts but also for larger, more complex components that require high strength and precision. The versatility of die casting makes it a go-to option for producing a wide range of automotive parts, both big and small.
Table: Common Automotive Parts Made Using Die Casting
Automotive Part | Example | Materials Used |
---|---|---|
Engine Components | Engine Blocks, Cylinder Heads | Aluminum, Magnesium |
Transmission Parts | Gearboxes, Shift Forks | Aluminum, Zinc |
Structural Components | Chassis, Brackets | Aluminum, Zinc |
Body Parts | Housings, Brackets | Aluminum |
5. How Does Die Casting Compare to Other Manufacturing Methods?
When it comes to manufacturing automotive parts, die casting has a distinct edge over other methods. Let’s compare it to some of the other most common manufacturing techniques:
- Die casting vs. injection molding: While both methods involve injecting molten material into a mold, die casting typically uses metals such as aluminum and zinc, while injection molding uses plastic. Die casting produces parts that are stronger, more durable, and able to withstand higher temperatures than those made by injection molding.
- Die casting vs. sand casting: Sand casting is another method used to produce automotive parts, but it tends to be slower and less precise than die casting. Sand casting also produces more waste material, making it less efficient in terms of cost and environmental impact.
- Die casting vs. forging: Forging involves shaping metal through the application of heat and pressure. While forging produces very strong parts, it’s generally less efficient and more expensive than die casting, particularly for high-volume production runs.
But here’s the kicker: die casting excels when it comes to mass production. Its speed, precision, and cost-efficiency make it the preferred choice for producing thousands or even millions of parts in a short period.
Table: Die Casting vs Other Manufacturing Methods
Method | Production Speed | Precision | Material Type | Waste |
---|---|---|---|---|
Die Casting | Fast | High | Metals (Aluminum, Zinc, Magnesium) | Low |
Injection Molding | Moderate | Moderate | Plastics | Low |
Sand Casting | Slow | Low | Metals (Various) | High |
Forging | Slow | High | Metals (Various) | Moderate |
6. What Materials Are Commonly Used in Die Casting for Automotive Parts?
The materials used in die casting play a crucial role in determining the performance and properties of the final part. The most common materials used in automotive die casting include:
- Aluminum alloys: Aluminum is the most widely used material in automotive die casting due to its lightweight properties, excellent corrosion resistance, and good thermal conductivity. It is commonly used for engine components, transmission parts, and structural elements.
- Magnesium alloys: Magnesium is even lighter than aluminum and is used in parts where weight reduction is critical, such as in chassis components and interior parts.
- Zinc alloys: Zinc offers excellent strength and durability and is often used for smaller parts such as connectors, housings, and brackets.
- Copper alloys: Copper is used for parts that require high electrical conductivity, such as electrical connectors and terminals.
What’s the real story? Each material has its own set of advantages, and the choice of material depends on the specific requirements of the automotive component being produced. Die casting allows manufacturers to select the material that best suits the performance and weight requirements of the part.
Table: Common Die Casting Materials in Automotive Parts
Material | Key Properties | Common Applications |
---|---|---|
Aluminum Alloys | Lightweight, Corrosion-resistant | Engine Blocks, Transmission Parts |
Magnesium Alloys | Very lightweight, High strength | Chassis, Interior Components |
Zinc Alloys | Strong, Durable | Connectors, Housings |
Copper Alloys | High electrical conductivity | Electrical Connectors |
7. What Are the Challenges in Die Casting Automotive Parts?
While die casting offers numerous advantages, it is not without its challenges. One of the main issues faced by manufacturers is the high tooling costs associated with the process. Die casting molds can be expensive to produce, especially for complex or large parts. However, these costs can be offset by the high volume of parts produced, making die casting a cost-effective solution in the long run.
Another challenge is material limitations. Some materials, such as certain alloys, may not be suitable for the die casting process due to their melting points or flow characteristics. Additionally, die casting can sometimes result in shrinkage and porosity in the final part, which may require additional finishing or quality control to address.
What’s the real story? Despite these challenges, die casting remains one of the most efficient and cost-effective manufacturing methods for automotive parts. Manufacturers are continuously working to improve the process, reducing tooling costs and addressing material limitations through new technology and innovations.
Table: Common Challenges in Die Casting
Challenge | Solution |
---|---|
High Tooling Costs | Offset by high-volume production runs |
Material Limitations | Select appropriate alloys and treatments |
Shrinkage and Porosity | Implement better cooling and mold design |
8. How Does Die Casting Contribute to Automotive Industry Sustainability?
In an era where sustainability is a growing concern, die casting plays a significant role in helping the automotive industry reduce its environmental impact. The process itself is energy-efficient, with the high pressure used to inject molten metal reducing the energy needed to cool the metal quickly. Additionally, the metal used in die casting is highly recyclable, which helps minimize waste and reduce the demand for raw materials.
Ready for the good part? Die casting also supports sustainability by enabling the production of lightweight parts. Lighter components reduce the overall weight of vehicles, which leads to improved fuel efficiency and lower emissions. As the automotive industry continues to focus on reducing its carbon footprint, die casting will play a crucial role in meeting these sustainability goals.
Table: Sustainability Benefits of Die Casting
Benefit | Description |
---|---|
Energy Efficiency | Reduced energy required for cooling |
Recyclable Materials | Metals used are highly recyclable |
Weight Reduction | Lighter parts reduce vehicle emissions |
Material Efficiency | Minimal waste generated during production |
9. How Can Die Casting Improve the Safety and Performance of Automotive Parts?
Die casting helps improve the safety and performance of automotive parts in several key ways. First, it allows for the production of parts that are both lightweight and strong, such as engine components and structural parts. This reduces the overall weight of vehicles without compromising on strength, leading to better performance and fuel efficiency.
Another way die casting improves automotive safety is by enabling the production of complex geometries that provide additional strength and protection. For example, die-cast parts can be designed with internal structures that absorb impact energy, providing additional safety in the event of a collision.
What’s the real story? The precision and quality of die-cast parts ensure that they fit perfectly in the vehicle, reducing the risk of failure and improving the overall reliability of the automotive system.
Table: Safety and Performance Benefits of Die Casting
Benefit | Example |
---|---|
Lightweight | Reduces vehicle weight and increases fuel efficiency |
Impact Absorption | Parts designed with internal structures for added safety |
Precision | Ensures perfect fit, improving overall reliability |
10. What Are the Innovations in Die Casting for Automotive Applications?
Innovation in die casting is constantly evolving, and the automotive industry is no exception. One of the most significant innovations in recent years is the use of 3D printing to create prototypes and molds for die-cast parts. This technology enables manufacturers to create more complex designs more quickly and at a lower cost than traditional methods.
Additionally, the use of robotics and automation in die casting is transforming the industry. Automated systems can handle tasks such as loading and unloading molds, reducing human labor costs and improving the efficiency and consistency of the production process.
What’s the real story? These innovations are enabling automotive manufacturers to produce die-cast parts that are more precise, cost-effective, and environmentally friendly.
Table: Innovations in Die Casting Technology
Innovation | Impact on Automotive Industry |
---|---|
3D Printing | Faster prototype creation and mold design |
Robotics & Automation | Improved efficiency, reduced labor costs |
Advanced Alloys | Stronger, lighter parts with better performance |
11. What Role Does Die Casting Play in Reducing Costs in Automotive Manufacturing?
Die casting plays a vital role in reducing costs in automotive manufacturing, particularly in high-volume production. The automation involved in the process reduces labor costs, while the high precision of die casting minimizes the need for additional machining or finishing. This cuts down on the time and cost required to produce each part.
Moreover, die casting’s ability to create lightweight and strong parts reduces the number of components needed for the final assembly, which further reduces costs. By integrating multiple functions into a single part, die casting simplifies the manufacturing process, leading to faster production times and reduced costs.
What’s the real story? Die casting’s efficiency and cost-effectiveness make it a key player in reducing overall manufacturing expenses, especially in the highly competitive automotive industry.
Table: Cost Reduction Through Die Casting
Factor | Impact on Manufacturing Costs |
---|---|
Automation | Reduces labor costs and errors |
Precision | Minimizes the need for additional machining |
Material Efficiency | Reduces waste and scrap material |
12. How Does Die Casting Help Meet Industry Standards and Regulations?
The automotive industry is subject to strict regulations and standards, particularly when it comes to safety, performance, and environmental impact. Die casting helps manufacturers meet these standards by producing parts with high precision and quality. The consistency of die-cast parts ensures that they meet the required specifications and performance standards, reducing the risk of defects or failures.
Moreover, die casting supports compliance with environmental regulations by enabling the use of recyclable materials and reducing material waste. The energy-efficient nature of the process also helps reduce the carbon footprint of automotive manufacturing.
Ready for the good part? Die casting provides a reliable solution that helps automotive manufacturers meet stringent standards while keeping production costs under control.
Table: Compliance Benefits of Die Casting
Compliance Area | Benefit |
---|---|
Safety Standards | High precision meets performance specifications |
Environmental Impact | Reduces waste and uses recyclable materials |
Energy Efficiency | Energy-efficient manufacturing reduces carbon footprint |
13. What Are the Key Considerations When Choosing Die Casting for Automotive Parts?
When choosing die casting for automotive parts production, there are several factors to consider. The first is the material. Die casting can accommodate a wide range of metals, but the choice of material will depend on the performance requirements of the part being produced. Aluminum, magnesium, and zinc are the most commonly used materials in automotive die casting, but other metals may be used for specific applications.
Another important consideration is the complexity of the part. Die casting excels at producing complex parts with intricate details, but the more complex the part, the higher the tooling costs. Manufacturers must weigh the benefits of precision and complexity against the cost of producing the molds.
What’s the real story? Die casting is ideal for high-volume production, but manufacturers need to assess the part’s material requirements, complexity, and production volume before committing to this method.
Table: Key Considerations for Die Casting Selection
Consideration | Impact on Die Casting Selection |
---|---|
Material | Determines strength, weight, and durability |
Complexity | Affects tooling costs and design flexibility |
Production Volume | Impacts overall cost-efficiency in mass production |
14. How Does Die Casting Fit into the Overall Automotive Manufacturing Process?
Die casting plays an integral role in the overall automotive manufacturing process. It is often used in conjunction with other manufacturing methods such as stamping, welding, and assembly to produce finished vehicle components. Die-cast parts are typically integrated into the vehicle at various stages of assembly, where they serve critical functions such as providing structural support or housing important engine components.
Moreover, die casting is highly scalable, which allows manufacturers to adapt their production process based on demand. Whether producing a limited run of high-performance parts or mass-producing components for standard vehicles, die casting can accommodate a range of production needs.
What’s the real story? Die casting fits seamlessly into the overall manufacturing process, complementing other methods and ensuring the efficient production of high-quality automotive parts.
Table: Die Casting Integration in Automotive Manufacturing
Stage | Role of Die Casting |
---|---|
Engine Assembly | Parts like engine blocks and cylinder heads |
Transmission | Gearboxes and shift forks |
Chassis and Body | Brackets, supports, and other structural parts |
15. What Does the Future Hold for Die Casting in Automotive Parts Production?
The future of die casting in automotive parts production is bright. As the automotive industry evolves, die casting will continue to play a crucial role in meeting the demand for lighter, stronger, and more precise components. Innovations in materials, automation, and 3D printing are expected to further enhance the capabilities of die casting, making it even more efficient and cost-effective.
What’s the real story? As the push for electric vehicles grows and new technologies emerge, die casting will remain a vital process for producing the components needed for tomorrow’s cars.
Table: Future Trends in Die Casting for Automotive
Trend | Impact on Die Casting |
---|---|
Electric Vehicles | Increased demand for lightweight, high-performance parts |
3D Printing | Faster mold creation and more complex designs |
Automation | More efficient production processes and lower costs |
FAQ Section
Q1: What is die casting?
Die casting is a manufacturing process in which molten metal is injected into a mold under high pressure, allowing the material to cool and form precise parts.
Q2: How does die casting work in automotive parts production?
Die casting involves injecting molten metal into molds to create automotive parts with high precision, durability, and strength. The process is ideal for mass production.
Q3: What materials are used in automotive die casting?
Common materials include aluminum, magnesium, zinc, and copper alloys, each selected based on the specific performance requirements of the part.
Q4: What are the advantages of die casting in automotive manufacturing?
Die casting offers high precision, reduced material waste, complex part creation, and cost-effective high-volume production, making it ideal for the automotive industry.
Q5: How does die casting improve automotive part performance?
Die casting produces lightweight yet strong parts that improve fuel efficiency, safety, and overall vehicle performance. The process allows for complex designs that enhance functionality.