In industries where extreme temperatures are a concern, selecting the right materials is crucial. Metals that can withstand high temperatures without compromising their structural integrity are essential. Heat resistant metals, such as alloys designed to resist temperature-induced damage, play a significant role in various industries, from aerospace to automotive. In this article, we will dive into the world of heat resistant metals, looking at their types, properties, applications, and how to choose the right metal for specific high-temperature conditions.
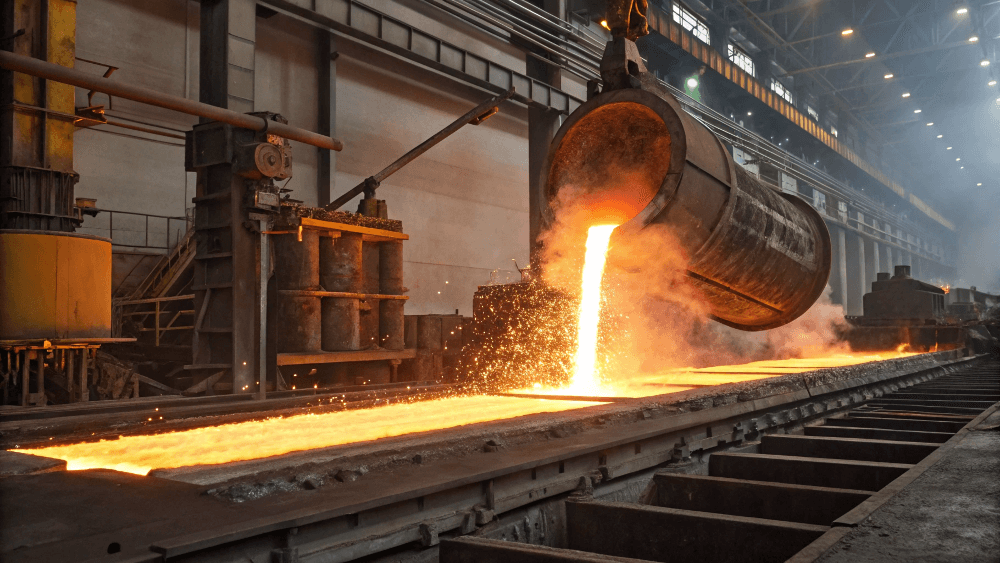
1. What is Heat Resistant Metal?
Heat resistant metal refers to materials designed to withstand high temperatures while maintaining their strength and functionality. These metals are used in applications where temperatures exceed the limits of standard materials, which would otherwise deform or fail under such conditions. Heat resistant metals are commonly found in industries that demand high performance and durability, including aerospace, automotive, manufacturing, and energy sectors.
What’s the real story here? Heat resistance in metals isn’t just about withstanding heat; it’s about maintaining performance even in extreme conditions. Metals like titanium, stainless steel, and Inconel are popular choices for applications that require resistance to heat, corrosion, and high-pressure environments. Their ability to resist high temperatures is due to their unique properties, such as high melting points, strong bonding between atoms, and advanced alloys that prevent oxidation.
Heat resistant metals come in various forms, including alloys, which are created by mixing different metals to improve the heat resistance of a base metal. For instance, Inconel, an alloy made primarily of nickel, chromium, and iron, is known for its excellent performance at high temperatures.
To better understand the relationship between metal resistance and temperature, let’s break down these metals into categories. Understanding these distinctions is crucial when choosing the right material for a high-temperature application.
2. Why is Heat Resistance Important for Metals?
Heat resistance in metals is vital for ensuring that materials maintain their structural integrity under extreme temperatures. In applications like engines, turbines, and furnaces, metals are exposed to intense heat, which can cause materials to expand, warp, or break. Without sufficient heat resistance, the performance and safety of these components could be compromised.
What’s the kicker here? Metals with high heat resistance can perform under conditions that would otherwise be impossible for less durable materials. This ensures that machinery and equipment continue to function properly, even in high-temperature environments. High-performance alloys, such as those used in the aerospace industry, are designed to handle these stresses, ensuring the safety and reliability of vehicles, equipment, and machinery.
The importance of heat resistance also extends to the longevity of the components. Heat causes metals to weaken over time, especially when subjected to continuous thermal cycling. Over time, even the strongest metals can suffer from fatigue, which can lead to cracks or failures. Metals with higher heat resistance are more resilient to these stressors, reducing the frequency of replacements and repairs.
3. What are the Best Types of Heat Resistant Metals?
When it comes to selecting the best heat resistant metals, several options stand out due to their performance in high-temperature environments. These include titanium, stainless steel, Inconel, and tungsten.
Here’s the good part. Each of these metals offers unique properties suited to different applications. Titanium, for instance, is known for its lightweight nature and high strength, making it ideal for aerospace and high-performance engineering. On the other hand, stainless steel, particularly its high-temperature variants, offers excellent corrosion resistance and is commonly used in heat exchangers and power plants.
Inconel, a nickel-chromium alloy, is widely regarded for its excellent resistance to oxidation and thermal fatigue, making it suitable for gas turbines and jet engines. Lastly, tungsten, with its extraordinarily high melting point, is used in applications requiring extreme heat resistance, such as rocket nozzles and military applications.
It’s important to note that while these metals offer superior heat resistance, their cost can vary significantly depending on the metal and its specific alloy composition.
Let’s take a look at some of the key differences between these metals in the following table, comparing their properties and applications.
Metal | Melting Point | Typical Applications | Advantages | Cost Estimate |
---|---|---|---|---|
Titanium | 1,668°C | Aerospace, Medical Devices | Lightweight, corrosion-resistant | High |
Stainless Steel | 1,510°C | Power Plants, Heat Exchangers | Corrosion-resistant, durable | Medium |
Inconel | 1,300°C–1,400°C | Gas Turbines, Jet Engines | High oxidation resistance, thermal fatigue resistance | Very High |
Tungsten | 3,422°C | Rocket Nozzles, Military | High melting point, excellent heat resistance | Very High |
4. How Do Heat Resistant Metals Perform in Extreme Temperatures?
Heat resistant metals are specifically engineered to perform under extreme temperature conditions, from those encountered in industrial processes to those found in deep space. But how exactly do they perform in such environments?
Here’s where it gets interesting. Heat resistant metals maintain their strength and structure even when temperatures exceed the normal limits for other materials. For example, titanium alloys maintain their integrity at temperatures as high as 600°C, while Inconel can handle temperatures over 1,300°C without suffering from oxidation or thermal fatigue.
The thermal properties of these metals, such as their ability to expand and contract without losing strength, play a critical role in their performance. When a metal is exposed to heat, it expands. If it expands too much or too quickly, it can crack or warp. Heat resistant metals are designed to resist these changes, ensuring their structural stability in extreme conditions.
The type of alloy also plays a role in how a metal performs in high temperatures. For instance, Inconel’s high nickel content allows it to maintain strength and flexibility under heat, while also resisting corrosion. This makes it ideal for use in environments with extreme heat and corrosive conditions, like jet engines or gas turbines.
5. What are the Applications of Heat Resistant Metals?
Heat resistant metals are used in a variety of applications across different industries, from aerospace to manufacturing. In the aerospace industry, for example, heat resistant metals are used in turbine blades, exhaust systems, and aircraft engines. These components are exposed to extreme temperatures during operation, and without the use of heat resistant metals, they would quickly fail under the intense conditions.
Ready for the good part? Heat resistant metals are also essential in automotive manufacturing, particularly in engine components that operate at high temperatures. Parts such as exhaust systems, engine blocks, and catalytic converters all rely on the durability of heat resistant metals to perform efficiently and safely.
In the energy industry, heat resistant metals are used in power plants, where they are exposed to extreme temperatures in boilers, heat exchangers, and reactors. The high-temperature stability of these materials ensures that equipment can operate at optimal levels without the risk of failure or overheating.
Industry | Application Example | Heat Resistant Metal Used | Key Benefits |
---|---|---|---|
Aerospace | Turbine Blades, Exhaust | Inconel, Titanium | High strength at extreme temperatures |
Automotive | Engine Components, Exhaust | Stainless Steel, Titanium | Durability, corrosion resistance |
Energy | Heat Exchangers, Boilers | Stainless Steel, Inconel | Temperature stability, reliability in power generation |
6. What Makes a Metal Heat Resistant?
Heat resistance in metals is primarily determined by the material’s composition, crystal structure, and ability to resist thermal expansion. Metals with high heat resistance often have a crystalline structure that allows them to maintain their integrity at elevated temperatures.
But here’s the kicker. It’s not just about the metal itself; it’s about how the metal is alloyed with other materials. For example, nickel alloys, like Inconel, are designed to improve heat resistance by enhancing the metal’s ability to resist oxidation and maintain strength at high temperatures.
The physical properties of the metal also play a crucial role in its ability to resist heat. For instance, the higher the melting point of the metal, the better it can resist heat. Metals like tungsten, with an exceptionally high melting point, are ideal for applications where extremely high temperatures are common.
Property | Influence on Heat Resistance | Example Metal |
---|---|---|
Melting Point | Higher melting point improves heat resistance | Tungsten |
Thermal Expansion | Less expansion means less deformation at high temperatures | Titanium |
Oxidation Resistance | Prevents corrosion at high temperatures | Inconel |
7. How Can You Choose the Right Heat Resistant Metal?
Choosing the right heat resistant metal for a specific application involves considering several factors. These include the temperature range, the metal’s ability to withstand thermal cycling, its resistance to oxidation, and its cost.
What’s the real story? Different applications require different types of heat resistant metals. For instance, in aerospace applications, weight is often a concern, so titanium is preferred for its combination of strength and low density. On the other hand, for components that experience high stress and high temperatures, such as gas turbines, Inconel’s superior heat resistance and durability make it the go-to choice.
Additionally, cost plays a significant role in selecting the appropriate metal. While Inconel offers unmatched heat resistance, it’s also one of the most expensive options. For less demanding applications, stainless steel or titanium may provide adequate performance at a fraction of the cost.
8. How Are Heat Resistant Metals Tested for Durability?
Heat resistant metals are subjected to rigorous testing to ensure that they can withstand extreme conditions without failing. One of the most common testing methods is thermal cycling, where the metal is repeatedly heated and cooled to simulate real-world operating conditions.
Ready for the good part? These tests allow engineers to observe how metals react to temperature fluctuations and assess their resistance to fatigue. Metals that can endure these conditions without significant degradation are considered durable and reliable for high-temperature applications.
Other testing methods include exposure to corrosive environments to determine how metals perform when subjected to extreme temperatures and chemicals. Metals like Inconel are often tested for oxidation resistance in environments where heat and corrosive gases are present.
Testing Method | Purpose | Metal Tested | Results |
---|---|---|---|
Thermal Cycling | Simulate temperature fluctuations | Inconel, Titanium | Resistance to thermal fatigue |
Corrosion Testing | Assess performance in extreme environments | Stainless Steel, Inconel | Resistance to oxidation and corrosion |
9. What Are the Limitations of Heat Resistant Metals?
While heat resistant metals offer superior performance in high-temperature environments, they do have limitations. One of the main challenges is that these metals can still suffer from fatigue over time. Even the best heat resistant metals can degrade under extreme thermal cycling or prolonged exposure to high temperatures.
What’s the kicker here? Not all heat resistant metals are suitable for every high-temperature application. For example, while tungsten performs exceptionally well in extreme heat, it’s brittle and may not be the best choice for applications where impact resistance is required. Similarly, Inconel’s high cost makes it impractical for some projects, especially those that do not require the highest level of heat resistance.
The limitations of heat resistant metals underscore the importance of choosing the right material for the specific demands of the application. In many cases, a combination of metals or coatings may be used to enhance heat resistance and address these limitations.
10. How Can Heat Resistant Metals Be Maintained?
Maintaining heat resistant metals involves regular inspections to check for signs of wear and tear, such as cracks, corrosion, or discoloration. Proper maintenance can help extend the lifespan of these metals and ensure they continue to perform optimally under high temperatures.
Ready for the good part? One of the most common maintenance practices for heat resistant metals is applying protective coatings, such as thermal barrier coatings, which reduce the risk of oxidation and thermal degradation. Additionally, routine cleaning to remove dirt and debris can help maintain the metal’s performance and prevent buildup that could lead to overheating.
Maintenance Task | Purpose | Metal Affected | Recommended Action |
---|---|---|---|
Thermal Barrier Coatings | Protect against oxidation and heat damage | Inconel, Titanium | Apply coatings to components exposed to high heat |
Regular Inspections | Detect cracks, corrosion, or wear | All Heat Resistant Metals | Perform visual inspections and non-destructive testing |
11. How Does Heat Resistance Affect the Cost of Metals?
The cost of heat resistant metals is directly influenced by their performance capabilities. Metals with higher heat resistance, such as Inconel, are typically more expensive due to the advanced alloys and manufacturing processes required to produce them. However, the investment in high-quality heat resistant metals can be justified by their longevity and reduced maintenance costs over time.
What’s the real story? While the initial cost of heat resistant metals can be higher than standard materials, they can save businesses money in the long run by improving the efficiency and durability of components. For example, replacing a part made of low-cost steel with one made of a heat resistant metal might involve a higher upfront cost but can lead to fewer repairs and longer service life.
In many industries, the benefits of using heat resistant metals far outweigh the added cost, especially in applications where failure is not an option.
12. What Are the Environmental Impacts of Using Heat Resistant Metals?
The production and use of heat resistant metals have some environmental implications, particularly due to the energy-intensive processes involved in creating the alloys. However, these metals are often highly durable, reducing the need for replacements and repairs, which can have a positive environmental impact by lowering waste and resource consumption.
But here’s the kicker. The recyclability of heat resistant metals like stainless steel and Inconel further helps mitigate their environmental footprint. Many of these metals can be recycled multiple times without losing their properties, making them a sustainable choice in certain applications.
Metal | Environmental Impact | Recycling Capability | Use in Sustainable Practices |
---|---|---|---|
Stainless Steel | Energy-intensive production | High | Widely recycled |
Inconel | Energy-intensive production | High | Can be recycled with minimal property loss |
13. How Do Heat Resistant Metals Compare to Other Materials?
When compared to other materials such as ceramics and composites, heat resistant metals offer a range of advantages. Metals like titanium and Inconel combine heat resistance with strength and durability, making them suitable for applications that require both high temperature resistance and mechanical performance.
Ready for the good part? While ceramics may offer higher heat resistance in certain cases, they are often more brittle and less versatile than metals. Composites, on the other hand, offer flexibility and can be engineered for specific applications but may lack the overall strength of metals.
The choice between metals and other materials depends on the specific requirements of the application, including temperature ranges, strength, weight, and durability.
14. What Are the Future Trends in Heat Resistant Metals?
The future of heat resistant metals looks promising, with ongoing advancements in alloy composition and manufacturing processes. Emerging technologies are enabling the development of metals that offer even better heat resistance and durability while reducing weight and cost.
But here’s the kicker. New innovations in 3D printing and additive manufacturing are opening up new possibilities for producing custom heat resistant components with highly specific properties. This could revolutionize industries like aerospace and automotive, where precision and performance are paramount.
The trend towards sustainable materials and manufacturing processes will also continue to shape the future of heat resistant metals, as companies seek to reduce the environmental impact of production.
15. How Can You Improve the Heat Resistance of Metals?
There are several ways to improve the heat resistance of metals, including heat treatments, alloying, and surface coatings. Heat treatments, such as carburizing and quenching, alter the metal’s structure to improve its performance at high temperatures. Alloying, by combining different metals, can also enhance heat resistance by adding elements that improve the metal’s ability to withstand heat.
Ready for the good part? Coatings like ceramic or thermal barrier coatings can be applied to heat resistant metals to further improve their performance by reducing the risk of oxidation and thermal damage. These methods can help enhance the longevity and functionality of heat resistant metals in extreme conditions.
Improvement Method | Effectiveness | Metal Affected | Recommended Use |
---|---|---|---|
Heat Treatments | High | All Heat Resistant Metals | Enhance heat resistance and strength |
Alloying | High | Inconel, Titanium | Increase heat resistance |
Thermal Barrier Coatings | High | Stainless Steel, Inconel | Reduce oxidation and thermal damage |
Conclusion
In conclusion, choosing the right heat resistant metal is essential for any application exposed to extreme temperatures. Metals like titanium, stainless steel, Inconel, and tungsten each offer unique properties that make them suitable for different industries and applications. While heat resistant metals are more expensive than standard materials, their long-term benefits in performance and durability often make them worth the investment.
Remember, the best choice depends on the specific demands of your application, including temperature range, material strength, and budget. By understanding the properties of these metals and their applications, you can make an informed decision that ensures the longevity and efficiency of your high-temperature components.
FAQ Section
Q1: What is heat resistant metal?
Heat resistant metal refers to metals designed to withstand high temperatures without losing structural integrity or strength. These metals are essential in industries that require components to endure extreme heat, such as aerospace and automotive industries.
Q2: How does heat resistance work?
Heat resistance in metals is achieved through their composition and structure. Metals with high melting points and strong atomic bonds are more capable of withstanding elevated temperatures without undergoing significant deformation or damage.
Q3: What types of metals are heat resistant?
Common heat resistant metals include titanium, stainless steel, Inconel, and tungsten. These metals are chosen based on their specific properties, such as high melting points and resistance to oxidation and thermal fatigue.
Q4: Can heat resistant metals be used in extreme temperatures?
Yes, heat resistant metals can be used in extreme temperatures. The ability of these metals to maintain structural integrity in high heat makes them ideal for applications such as jet engines, turbines, and high-performance machinery.
Q5: How can I maintain heat resistant metals?
Maintaining heat resistant metals involves regular inspections, cleaning, and applying protective coatings like thermal barriers. This helps prevent oxidation and thermal degradation, ensuring the longevity and reliability of the metal.