Investment casting alloys are a crucial element in manufacturing processes that require precision and durability. Selecting the right alloy can make all the difference in product strength, resistance to wear, and longevity.
In this article, we will explore the best investment casting alloys, what makes them exceptional, and how to choose the right one for your manufacturing needs.
If you are looking to improve the quality and reliability of your products, understanding the various investment casting alloys and their applications is essential. This article will guide you through the most popular options and help you decide which ones fit your specific needs.
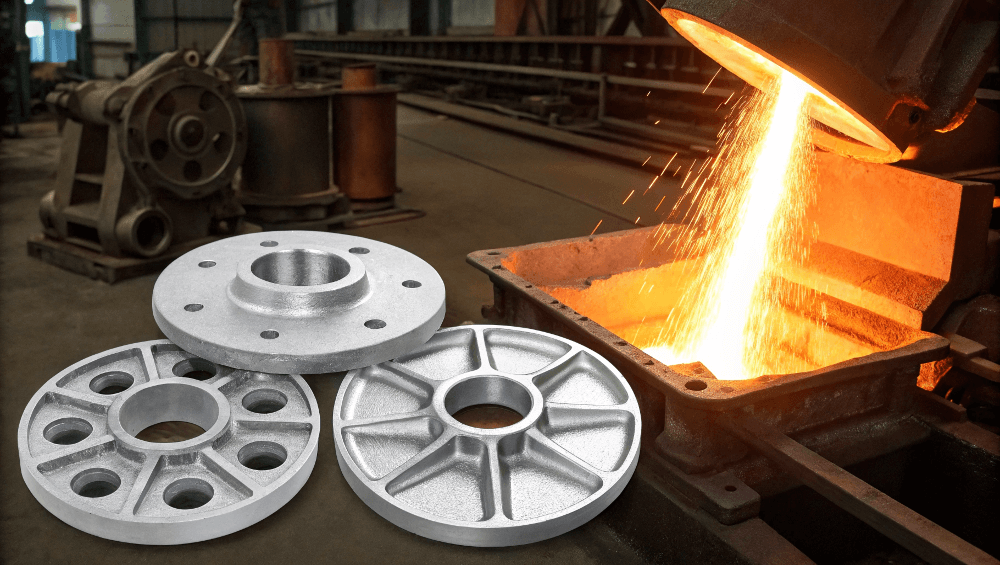
1. What Are Investment Casting Alloys?
Investment casting alloys are specially formulated metals that are used in the investment casting process to create precision parts for various industries. The process of investment casting involves pouring molten metal into a mold, which then hardens to form the desired shape. The alloy you choose can significantly affect the casting’s performance, cost, and quality.
Why Are Investment Casting Alloys Important?
Investment casting alloys are integral to producing parts that need high precision and performance under extreme conditions. These alloys can be tailored to meet specific needs such as corrosion resistance, heat resistance, and wear resistance. Whether you’re in the aerospace, automotive, or medical device industries, choosing the right alloy ensures that your products will withstand the test of time and perform optimally.
Investment casting alloys come in various types, each offering unique benefits. Below, we’ll look at some of the most commonly used alloys, including stainless steel, carbon steel, and high-temperature alloys, and break down their individual properties and applications.
Alloy Type | Strength | Heat Resistance | Corrosion Resistance | Best Application |
---|---|---|---|---|
Stainless Steel | High | Medium | Excellent | Food processing, pharmaceuticals |
Carbon Steel | Medium | Low | Moderate | Automotive, industrial parts |
Nickel-based Alloys | Very High | Very High | Excellent | Aerospace, high-performance turbines |
Titanium Alloys | High | High | High | Medical implants, aerospace |
2. Why Are Investment Casting Alloys Important in Manufacturing?
The use of the correct investment casting alloy is crucial in industries that require complex parts with precise dimensions. These alloys provide the strength, durability, and performance required in high-stakes manufacturing applications. From the aerospace industry, where parts need to withstand extreme temperatures and stresses, to the automotive industry, where durability is key, investment casting alloys are the backbone of precision manufacturing.
What Role Do Investment Casting Alloys Play in Manufacturing?
Investment casting alloys are essential in creating parts that are both durable and precise. This makes them especially valuable in industries like aerospace and automotive, where performance is critical. The alloys’ ability to resist high temperatures, corrosion, and wear extends the longevity of the parts they create, which in turn boosts the overall quality of the final product.
Industry | Alloy Type | Key Role |
---|---|---|
Aerospace | Nickel-based alloys | High heat resistance, performance under stress |
Automotive | Stainless steel | Durability and strength in engine components |
Medical Devices | Titanium alloys | Biocompatibility, corrosion resistance |
3. What Are the Different Types of Investment Casting Alloys?
There are several types of investment casting alloys, each designed to fulfill a specific role. Let’s dive into the main categories of alloys used in investment casting.
Stainless Steel Alloys
Stainless steel is one of the most widely used materials in investment casting due to its excellent corrosion resistance and strength. It’s ideal for applications in the food, chemical, and pharmaceutical industries.
Carbon Steel Alloys
Carbon steel alloys offer a balance between cost and performance. They are used in applications where strength is required, but the parts will not be exposed to extreme conditions.
High-Temperature Alloys
Nickel-based and cobalt-based alloys are typically used for high-temperature applications, such as in turbine blades and aerospace components. These alloys are designed to withstand extreme heat and pressure.
Specialty Alloys
These alloys are often customized for specific industries or applications. They include materials like titanium alloys, which are often used in medical implants due to their biocompatibility.
Alloy Type | Best For | Temperature Range | Key Benefit |
---|---|---|---|
Stainless Steel | Pharmaceutical, Food processing | Medium range | Corrosion resistance |
Carbon Steel | Automotive, Heavy machinery | Low to medium range | Strength and cost-effectiveness |
Nickel Alloys | Aerospace, High-performance engines | Very high range | Extreme heat resistance |
Titanium Alloys | Medical implants, Aerospace | High range | Biocompatibility, corrosion resistance |
4. How Do Investment Casting Alloys Compare to Other Materials?
Investment casting alloys offer distinct advantages compared to other casting methods, such as sand casting or die casting. Alloys used in investment casting are more versatile and can produce parts with greater precision and higher strength.
How Do They Compare to Die Casting?
Die casting uses molten metal injected into a mold under high pressure, which results in a smoother finish but may not be suitable for highly intricate designs. Investment casting alloys, on the other hand, are more capable of producing complex geometries without the need for extensive machining. Additionally, the surface finish from investment casting tends to be superior to that of die casting.
Investment Casting vs. Sand Casting
While sand casting is less expensive and suitable for large parts, investment casting provides greater precision and a smoother surface finish. Sand casting also requires more post-processing to achieve the desired quality, which is not the case with investment casting alloys.
Casting Method | Precision | Surface Finish | Cost | Complexity of Part |
---|---|---|---|---|
Investment Casting | High | Excellent | Higher | Complex |
Die Casting | Medium | Good | Moderate | Moderate |
Sand Casting | Low | Rough | Lower | Simple |
5. What Are the Best Investment Casting Alloys for Different Applications?
Each application requires a specific set of properties from investment casting alloys. Let’s examine some of the best alloys for specific industries:
Aerospace
The aerospace industry demands alloys that can withstand high temperatures and extreme stress. Nickel-based alloys are commonly used in turbine blades, heat exchangers, and other aerospace components.
Automotive
The automotive industry benefits from stainless steel and carbon steel alloys. These alloys provide the necessary strength and durability for engine parts, transmission components, and exhaust systems.
Medical Devices
For medical devices, especially those used inside the human body, titanium alloys are often the material of choice. They are biocompatible, strong, and resistant to corrosion, making them ideal for implants and surgical instruments.
Industry | Preferred Alloy | Key Properties |
---|---|---|
Aerospace | Nickel-based | High heat resistance, strength |
Automotive | Stainless steel | Durability, resistance to corrosion |
Medical Devices | Titanium alloys | Biocompatibility, corrosion resistance |
6. How Do Investment Casting Alloys Improve the Final Product?
The quality of the alloy used directly impacts the final product’s performance, lifespan, and overall functionality. Investment casting alloys provide superior accuracy and smoother finishes, which results in parts that require less post-processing. These alloys also contribute to increased strength, reduced weight, and enhanced durability.
How Do Alloys Enhance Product Performance?
By selecting the right alloy, manufacturers can ensure the final product performs under the most demanding conditions. For example, alloys with higher tensile strength are perfect for parts exposed to stress and wear, while those with enhanced corrosion resistance are ideal for parts used in harsh chemical environments.
Alloy Type | Property Improved | Benefit to Final Product |
---|---|---|
Stainless Steel | Corrosion resistance | Longer lifespan in corrosive environments |
Carbon Steel | Strength | Increased durability in high-stress applications |
Nickel-based Alloys | Heat resistance | Improved performance in high-temperature environments |
Titanium Alloys | Biocompatibility | Suitable for medical implants and human contact |
7. What is the Process of Casting with Investment Casting Alloys?
Investment casting with alloys is a multi-step process that involves melting the alloy and casting it into intricate shapes. The detailed mold is created using a pattern, often made from wax, which is coated with a shell material. Once the pattern is solidified and the wax is removed, molten alloy is poured into the mold.
How Does the Investment Casting Process Work with Alloys?
The process begins with the creation of a pattern, often made from wax, which is covered with a ceramic shell. After the shell hardens, the wax is removed by heating the mold. Next, molten alloy is poured into the cavity, and the mold is allowed to cool, solidifying the metal into the final shape. Once cooled, the casting is removed from the shell and cleaned.
Step | Description | Importance |
---|---|---|
Pattern creation | Wax or plastic pattern shaped as the part | Creates the foundation for the casting |
Shell coating | Ceramic slurry applied to the pattern | Provides the mold for the molten alloy |
Wax removal | Shell is heated to remove the wax | Prepares the mold for alloy pouring |
Alloy pouring | Molten alloy poured into the mold | Forms the part by filling the mold cavity |
Cooling and removal | Part is cooled and extracted from the shell | Solidifies and extracts the finished part |
8. How Do Investment Casting Alloys Influence Casting Costs?
The selection of investment casting alloys can significantly influence the overall cost of production. Higher-quality alloys typically cost more but result in better performance and fewer defects. On the other hand, less expensive alloys might reduce upfront costs but may increase long-term costs due to higher failure rates and increased maintenance.
What Are the Cost Implications of Alloy Selection?
Using high-performance alloys, such as those made from nickel or titanium, may incur higher material costs, but their ability to withstand extreme conditions can reduce maintenance costs and extend product lifespan. Choosing the right alloy is a balance between material cost and long-term performance benefits.
Alloy Type | Material Cost | Performance Benefit | Long-Term Savings |
---|---|---|---|
Stainless Steel | Moderate | Excellent corrosion resistance | Reduced maintenance costs |
Carbon Steel | Low | Strong and durable | Lower initial cost, higher post-processing costs |
Nickel-based Alloys | High | High heat resistance, strong | Increased performance, fewer failures |
Titanium Alloys | High | Excellent strength-to-weight ratio | Reduced part failure, longer lifespan |
9. How Can the Quality of Investment Casting Alloys Be Ensured?
Ensuring the quality of investment casting alloys involves monitoring the alloy composition, conducting thorough testing, and maintaining stringent quality control measures throughout the casting process. Testing methods such as tensile testing, metallography, and X-ray inspections help identify potential defects before the parts reach the customer.
What Are the Common Quality Assurance Methods?
Quality assurance in investment casting alloys often includes testing for material properties such as tensile strength, fatigue resistance, and ductility. These tests are performed during the production process to ensure that the alloys meet the necessary specifications for their intended application.
Test Method | What It Measures | Benefit to Quality Assurance |
---|---|---|
Tensile Testing | Material strength | Ensures the alloy can handle stress without breaking |
Metallographic Analysis | Microstructure and composition | Identifies defects in the material’s structure |
X-ray Inspection | Internal defects | Detects unseen cracks or voids in the alloy |
10. What Are the Latest Trends in Investment Casting Alloys?
The field of investment casting alloys is continually evolving as new materials and technologies are developed. The growing demand for lighter, stronger materials in industries such as aerospace and automotive has led to innovations in alloy formulations. Furthermore, advances in casting technology are improving alloy performance and reducing costs.
What Are the Innovations in Alloy Development?
In recent years, alloys with improved fatigue resistance, better corrosion performance, and lighter weight have been developed. These alloys are particularly valuable for industries that require both strength and weight optimization, such as aerospace and automotive manufacturing.
Alloy Type | Latest Innovations | Key Benefit |
---|---|---|
Nickel Alloys | Enhanced fatigue resistance | Longer part life in high-stress applications |
Stainless Steel | Improved corrosion resistance | Better performance in harsh environments |
Titanium Alloys | Lighter with higher strength | Reduced weight without compromising strength |
High-performance Alloys | Better heat and wear resistance | Ideal for extreme conditions |
11. How Do Investment Casting Alloys Impact Environmental Sustainability?
Sustainability is becoming a priority in all industries, and investment casting is no exception. By using alloys that are more efficient in production and can be recycled, manufacturers can reduce their environmental impact. Additionally, alloy improvements are being made to minimize waste during the casting process.
How Can Alloys Contribute to Sustainable Manufacturing?
Sustainable alloys, like those with recyclable properties or those that reduce emissions during production, help minimize the environmental footprint. Furthermore, reducing waste in casting and improving material usage efficiency plays a crucial role in sustainable manufacturing.
Alloy Type | Environmental Benefit | Sustainable Manufacturing Practice |
---|---|---|
Stainless Steel | High recyclability | Reduced waste, recyclable material |
Carbon Steel | Energy-efficient production | Less energy-intensive than other materials |
Titanium Alloys | Low material waste during casting | Efficient use of high-quality materials |
Nickel Alloys | Reduced emissions during production | Improved energy efficiency in casting |
12. What Are the Challenges in Working with Investment Casting Alloys?
Working with investment casting alloys presents several challenges, from the difficulty in sourcing high-quality alloys to maintaining the consistency of alloy composition. The complexity of alloy casting can also lead to issues like porosity, shrinkage, or cracking if not properly managed.
What Are the Common Problems with Alloy Casting?
Some of the most common problems include material defects, such as porosity, which occurs when gas bubbles are trapped in the alloy during casting. Additionally, controlling the alloy’s temperature during the casting process is critical to avoid issues such as cracking or incomplete solidification.
Problem | Cause of Problem | Solution |
---|---|---|
Porosity | Gas trapped during casting | Use proper venting and control of mold temperature |
Shrinkage | Inconsistent cooling rates | Adjust cooling procedures to ensure uniform solidification |
Cracking | High thermal stress | Ensure proper mold design and alloy selection for heat resistance |
13. How Do Investment Casting Alloys Meet Industry Standards?
Industry standards ensure that investment casting alloys meet the necessary specifications for strength, durability, and safety. These standards are set by various regulatory bodies, including ASTM, ISO, and SAE, to maintain consistency and quality across industries.
How Are Industry Standards Implemented in Alloy Selection?
Manufacturers must adhere to specific standards when selecting alloys for casting to ensure they meet the requirements for the intended use. For example, aerospace components require alloys that meet high performance and safety standards, while medical implants need to adhere to biocompatibility regulations.
Standard Organization | Standard Type | Industry Coverage |
---|---|---|
ASTM | Material specifications | Aerospace, automotive |
ISO | Quality management | General manufacturing |
SAE | Automotive and aerospace alloys | Automotive, aerospace |
14. What Are the Advantages of Customizing Investment Casting Alloys?
Custom alloys are tailored to meet the specific needs of the manufacturer and the final product. Customization allows for a more precise balance of material properties, ensuring that the alloy is optimized for its intended application.
How Can Custom Alloys Improve Performance?
By customizing the alloy composition, manufacturers can improve certain attributes, such as strength, corrosion resistance, or thermal stability. This leads to better product performance and fewer failures during use.
Custom Alloy Type | Application Customization | Key Benefit |
---|---|---|
Stainless Steel | Customized for strength and corrosion resistance | Improved performance in specific environments |
Titanium Alloys | Optimized for biocompatibility | Ideal for medical applications |
Nickel Alloys | Tailored for high-temperature resistance | Better durability in extreme conditions |
15. How to Choose the Right Supplier for Investment Casting Alloys?
Choosing the right supplier for investment casting alloys is essential for ensuring quality, reliability, and cost-effectiveness. It’s important to consider factors such as experience, customer service, and the supplier’s ability to meet your specifications.
What Should You Look for in a Supplier?
Look for suppliers that have a strong track record of providing high-quality alloys. Additionally, it’s beneficial to work with a supplier that offers flexibility in alloy customization and can meet tight deadlines.
Supplier Criteria | Key Considerations | Benefit |
---|---|---|
Experience | Proven track record in your industry | Ensures consistent quality |
Customization | Ability to tailor alloys to specifications | Better performance for your needs |
Customer Service | Responsive support and timely delivery | Reduces production delays |
Conclusion
Investment casting alloys play a vital role in manufacturing parts that need to meet high precision and performance standards. Whether you’re working in aerospace, automotive, or medical device manufacturing, choosing the right alloy is key to ensuring product quality and durability. By understanding the various types of alloys and their specific applications, you can make more informed decisions to meet your manufacturing needs.
FAQ
- Q1: What are investment casting alloys?
Investment casting alloys are specialized materials used in the investment casting process to create precise and durable parts for various industries like aerospace, automotive, and medical devices. - Q2: How does the investment casting process work?
Investment casting involves creating a wax model of the part, coating it with a ceramic shell, and then melting the wax away before pouring molten alloy into the mold to form the part. - Q3: What are the best applications for investment casting alloys?
Investment casting alloys are used in industries like aerospace, automotive, and medical devices, where precision and durability are crucial. - Q4: How do I choose the right alloy for investment casting?
Choosing the right alloy depends on the part’s required strength, heat resistance, corrosion resistance, and intended application. - Q5: What are the benefits of using investment casting alloys?
The benefits include high precision, durability, and the ability to produce complex parts with superior surface finishes.