Carbon and low-alloy steel castings are widely used in industries that require durable, strong, and cost-effective materials. These castings play a crucial role in various applications, from automotive components to industrial machinery. In this article, we will explore why these materials are essential and how their properties benefit different industries.
Carbon and low-alloy steel castings are versatile and reliable materials, ideal for industries requiring high strength and durability. These castings are widely used in manufacturing due to their cost-effectiveness and ability to withstand extreme conditions.
To understand the full potential of these materials, let’s dive into the key aspects of carbon and low-alloy steel investment castings. You’ll learn why they are used, how they are made, and the benefits they offer. Let’s get started.
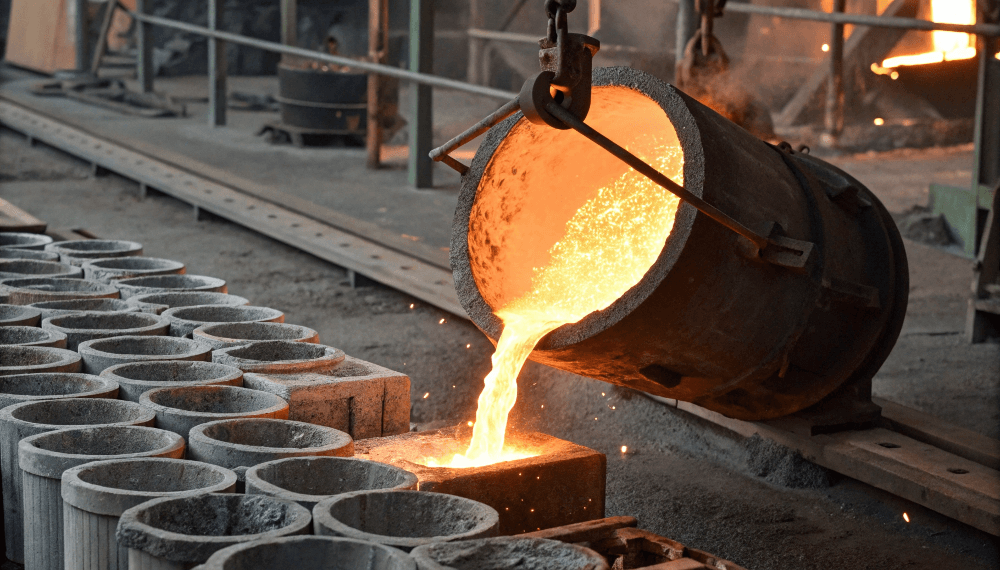
1. What Are Carbon and Low-Alloy Steel Investment Castings?
Carbon and low-alloy steel investment castings are parts made through the investment casting process, where molten metal is poured into a mold to create complex shapes. These materials are known for their strength and durability, which makes them suitable for a range of industrial applications.
Investment casting involves creating a mold, melting the metal, and then casting it into the shape of a part. Carbon and low-alloy steel castings are particularly useful because they offer excellent mechanical properties, cost-effectiveness, and versatility for high-stress environments.
In addition, the investment casting process allows for precise geometries, which is crucial for industries where dimensional accuracy and performance are paramount.
What Makes Carbon Steel Different From Low-Alloy Steel?
Carbon steel and low-alloy steel have distinct properties that make them suitable for different applications. Carbon steel is primarily made of iron and carbon, while low-alloy steel includes small amounts of other elements like manganese, chromium, or molybdenum to enhance its mechanical properties. Carbon steel is generally stronger but less resistant to corrosion, while low-alloy steel offers better toughness and heat resistance.
How the Investment Casting Process Enhances Steel Castings
The precision of the investment casting process allows for intricate designs with minimal waste. This results in a smoother finish and higher dimensional accuracy, which are essential for industries like aerospace and automotive manufacturing. The process also reduces the need for additional machining, which cuts down costs and production time.
Table 1: Comparison of Carbon and Low-Alloy Steel Properties
Property | Carbon Steel | Low-Alloy Steel |
---|---|---|
Composition | Iron + Carbon | Iron + Small Alloys (Mn, Cr) |
Strength | High tensile strength | Enhanced heat resistance |
Corrosion Res. | Lower resistance | Better corrosion resistance |
Toughness | Moderate | Higher toughness and impact |
Applications | Automotive, structural parts | Aerospace, industrial parts |
2. How Does the Investment Casting Process Work?
Investment casting, also known as the “lost-wax” process, is used to produce highly detailed and complex metal parts. This process involves creating a pattern, coating it with a shell, and then melting the pattern to form a mold. The molten metal is poured into the mold, allowed to cool, and then the cast part is removed.
The investment casting process is used to produce parts with tight tolerances and excellent surface finishes. Carbon and low-alloy steel are ideal for this process because they offer the necessary mechanical properties and cost-effectiveness for high-performance applications.
What Are the Steps in the Investment Casting Process?
- Pattern Creation: A pattern is made, often from wax or plastic, in the shape of the final part.
- Shell Building: The pattern is coated with a heat-resistant material, forming a shell around it.
- Pattern Removal: The pattern is melted or burned out, leaving the mold behind.
- Metal Pouring: Molten metal is poured into the mold.
- Cooling and Extraction: The metal is allowed to cool and solidify before being extracted from the mold.
Table 2: Key Stages in the Investment Casting Process
Stage | Description | Materials Used |
---|---|---|
Pattern Creation | A replica of the final part is made. | Wax, plastic, metal |
Shell Building | The pattern is coated with a shell. | Heat-resistant materials |
Pattern Removal | The pattern is removed using heat. | Heat or chemicals |
Metal Pouring | Molten metal is poured into the mold. | Carbon steel, low-alloy steel |
Cooling and Extraction | Metal cools and hardens, then part is removed. | Carbon steel, low-alloy steel |
Why is Investment Casting Preferred for Steel Alloys?
Investment casting is ideal for steel alloys like carbon and low-alloy steel because of its ability to create complex shapes with high precision. Steel castings produced this way maintain strong mechanical properties, which are crucial for components that need to endure high stresses and extreme conditions.
3. Why Are Carbon and Low-Alloy Steel Popular for Investment Casting?
Carbon and low-alloy steel are widely chosen for investment casting due to their excellent strength, durability, and affordability. These steels can withstand extreme environments and maintain their integrity under high stress, making them ideal for industries such as automotive, aerospace, and energy.
The popularity of carbon and low-alloy steel castings is attributed to their ability to provide high performance while remaining cost-effective. These materials offer good mechanical properties, making them suitable for critical applications where strength and reliability are essential.
What Makes Carbon and Low-Alloy Steel Suitable for High-Stress Applications?
Carbon steel is known for its tensile strength, which allows it to withstand heavy loads. Low-alloy steel, on the other hand, provides added resistance to heat and wear, which is especially valuable in industries like aerospace and energy. Both materials are versatile and can be tailored to specific needs through heat treatment and alloying.
Industries That Benefit from Carbon and Low-Alloy Steel Castings
- Automotive: Engine components, transmission parts, and structural elements.
- Aerospace: Turbocharger components, brackets, and turbine blades.
- Energy: Valve bodies, pump parts, and other critical components exposed to high temperatures and pressures.
Table 3: Industry Applications for Carbon and Low-Alloy Steel Castings
Industry | Applications | Benefits |
---|---|---|
Automotive | Engine blocks, suspension parts, structural components | Strength, durability |
Aerospace | Turbocharger components, turbine blades, brackets | Heat resistance, precision |
Energy | Valve bodies, pump parts, turbines | High-temperature durability |
4. What Are the Key Benefits of Carbon and Low-Alloy Steel Investment Castings?
The primary benefits of using carbon and low-alloy steel for investment castings include high precision, excellent surface finish, and minimal material waste. These benefits make investment casting an attractive option for manufacturers looking to produce high-performance components.
Investment castings made from carbon and low-alloy steel offer multiple advantages, including complex shape creation, reduced waste, and superior mechanical properties. These factors significantly contribute to the casting’s performance, making it ideal for demanding applications.
Advantages of High Precision and Dimensional Accuracy
Investment casting allows for the production of parts with high dimensional accuracy. This is essential in industries like aerospace, where even the smallest deviation can result in failures. The ability to produce precise components reduces the need for further machining, saving time and money.
Reduced Material Waste and Cost-Effectiveness
The investment casting process is highly efficient because it uses less material than traditional casting methods. Since the process creates fewer defects and requires less finishing, manufacturers can save on material costs while ensuring that the final product is of high quality.
Excellent Surface Finish
Investment castings have a superior surface finish, which reduces the need for further finishing processes. This is beneficial for industries that require components with smooth surfaces, such as in aerospace and automotive manufacturing.
Table 4: Key Benefits of Carbon and Low-Alloy Steel Castings
Benefit | Description |
---|---|
High Precision | Allows for complex and intricate part designs. |
Reduced Waste | Investment casting uses less material compared to traditional casting. |
Excellent Surface Finish | Reduces the need for additional finishing work. |
5. What Are the Common Applications of Carbon and Low-Alloy Steel Investment Castings?
Carbon and low-alloy steel investment castings are commonly used in various industries, including automotive, aerospace, and industrial equipment. These materials provide the necessary strength, heat resistance, and precision for components that undergo high stress.
Carbon and low-alloy steel investment castings are used in critical applications such as engine components, turbine blades, and structural parts. These materials are chosen for their excellent mechanical properties and ability to perform well in harsh environments.
Common Automotive Applications
In the automotive industry, carbon and low-alloy steel investment castings are used for engine blocks, suspension parts, and structural components. The durability and high strength of these materials make them ideal for parts that need to withstand continuous stress.
Aerospace Applications
In aerospace, these castings are used in turbochargers, turbine blades, and brackets that need to endure high temperatures and stresses. The ability of low-alloy steel to resist heat and corrosion makes it suitable for these demanding applications.
Energy Industry Applications
Carbon and low-alloy steel castings are also used in the energy sector, where components such as valve bodies, pump parts, and turbines require high strength and heat resistance. These materials are critical for machinery that operates under extreme conditions.
Table 5: Applications in Different Industries
Industry | Applications | Material Requirements |
---|---|---|
Automotive | Engine blocks, suspension parts, structural components | High strength, durability |
Aerospace | Turbocharger components, turbine blades, brackets | Heat resistance, precision |
Energy | Valve bodies, pump parts, turbines | High temperature resistance |
6. What Are the Challenges of Using Carbon and Low-Alloy Steel for Investment Casting?
While carbon and low-alloy steel offer numerous advantages, there are some challenges associated with using them for investment casting. These challenges can affect the production process and the final product’s performance, but they can often be mitigated with careful planning and advanced techniques.
Challenges such as material consistency, potential cost implications, and limitations in high-temperature applications should be carefully considered when selecting carbon and low-alloy steel for investment casting. Understanding these challenges helps manufacturers choose the right material for their needs.
What Are the Main Challenges in Using Carbon and Low-Alloy Steel?
- Material Consistency: Variations in material composition can impact the casting process and the final product. Ensuring consistent material quality across large batches is crucial to avoid defects.
- Cost Implications: Low-alloy steel, while offering superior properties like heat resistance and toughness, can be more expensive than carbon steel. This price difference needs to be factored into the manufacturing cost.
- High-Temperature Limitations: While low-alloy steel is resistant to heat, there are still limitations in extremely high-temperature environments, particularly when exposed to prolonged stress.
Table 6: Challenges of Carbon and Low-Alloy Steel in Investment Casting
Challenge | Impact | Mitigation Strategies |
---|---|---|
Material Consistency | Can lead to defects and dimensional issues | Use controlled material suppliers, regular testing |
Cost Implications | Higher costs for low-alloy steel | Choose appropriate alloys based on application needs |
High-Temperature Limits | Potential failure under extreme heat | Use advanced alloys for high-heat applications |
7. What is the Importance of Heat Treatment in Carbon and Low-Alloy Steel Investment Castings?
Heat treatment plays a crucial role in enhancing the properties of carbon and low-alloy steel castings. This process is designed to improve the strength, hardness, and durability of steel, making it more suitable for high-stress applications.
Heat treatment can significantly improve the mechanical properties of carbon and low-alloy steel castings. By adjusting the heat treatment process, manufacturers can achieve the desired balance of strength, toughness, and wear resistance.
How Does Heat Treatment Affect Steel Castings?
Heat treatment alters the structure of steel alloys, optimizing their properties for specific applications. Depending on the process used, heat treatment can:
- Increase Strength: Steel castings undergo a process like quenching to enhance their strength by rapidly cooling them.
- Improve Toughness: Tempering can help reduce brittleness, providing greater impact resistance.
- Enhance Wear Resistance: Heat treatment techniques such as carburizing increase surface hardness, improving the material’s wear resistance.
Table 7: Heat Treatment Processes for Carbon and Low-Alloy Steel
Process | Purpose | Result |
---|---|---|
Quenching | Rapid cooling after heating | Increases hardness and strength |
Tempering | Reheating after quenching | Increases toughness and reduces brittleness |
Carburizing | Adding carbon to the surface | Improves wear resistance and surface hardness |
8. How to Choose the Right Carbon or Low-Alloy Steel for Investment Casting?
Choosing the correct type of carbon or low-alloy steel for investment casting depends on several factors, including the application’s requirements, the material’s properties, and cost considerations.
Selecting the right steel alloy is essential to ensure the casting performs well under stress and in specific environmental conditions. It’s crucial to balance the desired properties with budgetary constraints.
What Factors Should Be Considered When Choosing Steel for Investment Casting?
- Mechanical Properties: The required strength, hardness, and toughness of the casting will dictate the type of steel used.
- Application: Consider the application’s environment, such as exposure to high temperatures or corrosive elements, and choose an alloy that can handle these conditions.
- Cost: Low-alloy steel can offer superior properties, but it might be more expensive than carbon steel. Evaluate whether the added cost justifies the performance benefits for the specific application.
Table 8: Factors to Consider When Choosing Steel
Factor | Carbon Steel | Low-Alloy Steel |
---|---|---|
Mechanical Properties | Stronger tensile strength | Better toughness and heat resistance |
Application | Automotive, structural parts | Aerospace, energy, high-stress applications |
Cost | More affordable | Higher cost due to added alloys |
9. What Are the Key Quality Control Processes for Carbon and Low-Alloy Steel Castings?
Quality control is a critical part of the manufacturing process for carbon and low-alloy steel investment castings. Ensuring the castings meet the required standards and specifications is crucial for the performance of the final product.
Using various inspection methods and following industry standards ensures the castings meet stringent quality requirements. This guarantees that parts will perform reliably under their intended operational conditions.
What Are the Most Common Quality Control Techniques?
- Ultrasonic Testing: Used to detect internal flaws in the casting.
- X-Ray Inspection: Helps to identify internal voids or cracks that could affect the part’s integrity.
- Dimensional Inspection: Ensures the casting meets the specified tolerances and fits the intended design.
- Surface Finish Inspection: Ensures the casting has the required surface quality, which is critical for certain applications like aerospace.
Table 9: Common Quality Control Techniques for Steel Castings
Inspection Method | Purpose | Benefits |
---|---|---|
Ultrasonic Testing | Detects internal defects | Provides clear identification of flaws |
X-Ray Inspection | Detects cracks or voids inside the part | Ensures part integrity and safety |
Dimensional Inspection | Verifies that part matches design specs | Guarantees accuracy and fit |
Surface Inspection | Checks for surface quality | Ensures quality for high-performance applications |
10. What Are the Environmental Considerations for Carbon and Low-Alloy Steel Investment Casting?
The environmental impact of investment casting, particularly when using carbon and low-alloy steel, is a growing concern. Manufacturers must take steps to minimize waste, reduce energy consumption, and address other sustainability issues.
Sustainable practices and innovations in casting technology are increasingly important for reducing the environmental footprint of carbon and low-alloy steel castings.
What Are the Key Environmental Considerations?
- Energy Consumption: The investment casting process requires significant energy, especially during the melting and cooling stages. Using energy-efficient technologies can help reduce carbon emissions.
- Material Waste: Though investment casting is efficient, there is still some material waste during the process. Recycling scrap metal and optimizing production methods can help minimize waste.
- Emissions: Manufacturers must comply with environmental regulations regarding emissions from furnaces and other equipment used in casting.
Table 10: Environmental Impact of Investment Casting
Environmental Factor | Impact | Mitigation Strategies |
---|---|---|
Energy Consumption | High energy use in melting and cooling | Implement energy-efficient systems |
Material Waste | Small amounts of waste generated | Optimize material use, recycle scrap |
Emissions | Emissions from furnace operations | Use cleaner technologies and comply with regulations |
11. How Are Carbon and Low-Alloy Steel Investment Castings Manufactured Globally?
Global manufacturing of carbon and low-alloy steel castings involves a complex supply chain that includes raw material suppliers, foundries, and final product manufacturers. The process is influenced by local regulations, technology availability, and production capabilities.
Manufacturing locations like China, the USA, and Europe dominate the global casting industry. Understanding regional differences in production can help manufacturers choose the best suppliers for their needs.
Which Regions Are Leaders in Casting Production?
- China: The world’s largest producer of steel castings, offering cost-effective solutions.
- USA: Known for high-quality precision castings, particularly in aerospace and energy sectors.
- Europe: Specialized in high-performance alloys for demanding applications like automotive and aerospace.
Table 11: Key Manufacturing Regions for Steel Castings
Region | Leading Industries | Advantages |
---|---|---|
China | Automotive, industrial equipment | Cost-effective, large-scale production |
USA | Aerospace, energy, automotive | High-quality standards, precision casting |
Europe | Automotive, aerospace, industrial tools | Advanced technologies, high performance alloys |
12. How Do Carbon and Low-Alloy Steel Investment Castings Impact the Bottom Line for Manufacturers?
Using carbon and low-alloy steel investment castings can have a significant impact on the cost and efficiency of manufacturing. These materials offer performance benefits that can lead to long-term savings and competitive advantages.
Carbon and low-alloy steel castings are a cost-effective solution for manufacturers, providing high-quality components that can enhance product performance and reduce costs in the long run.
How Do These Castings Affect Manufacturing Costs?
- Reduced Waste: Investment casting minimizes material waste, which lowers costs.
- Fewer Machining Steps: The precision of the process reduces the need for additional machining, saving time and labor.
- Long-Term Durability: The superior performance of these materials means less downtime and fewer repairs.
Table 12: Impact of Carbon and Low-Alloy Steel on Manufacturing Costs
Factor | Effect | Financial Benefit |
---|---|---|
Reduced Waste | Less material used in the casting process | Lower material costs |
Fewer Machining Steps | Reduced need for additional machining | Time and labor savings |
Long-Term Durability | Increased product lifespan | Reduced maintenance and repair costs |
13. What Are the Latest Innovations in Carbon and Low-Alloy Steel Casting Technology?
Advancements in casting technology are continually improving the quality and efficiency of carbon and low-alloy steel castings. New techniques and innovations in alloy composition are helping manufacturers meet the demands of modern industries.
Technological innovations in casting methods and alloy development are enhancing the performance and cost-efficiency of carbon and low-alloy steel castings. These improvements are opening up new possibilities for industries that rely on high-performance materials.
What Are the New Trends in Casting Technology?
- 3D Printing for Molds: 3D printing is being used to create molds for investment casting, which reduces lead times and increases design flexibility.
- Advanced Alloys: The development of new alloys with superior properties, such as higher heat resistance, is allowing for even more demanding applications.
- Automation: Automation in the casting process is helping reduce human error, improve efficiency, and lower costs.
Table 13: Emerging Technologies in Steel Casting
Technology | Description | Benefits |
---|---|---|
3D Printing for Molds | Use of additive manufacturing to create molds | Faster production, more design flexibility |
Advanced Alloys | New steel alloys with enhanced properties | Higher performance and durability |
Automation | Use of automated systems in the casting process | Improved efficiency and reduced costs |
14. What Are the Future Trends for Carbon and Low-Alloy Steel Investment Castings?
The future of carbon and low-alloy steel investment castings looks promising, with continued advancements in materials and technology. As industries evolve, these castings will play a vital role in supporting new applications and meeting increasing performance demands.
Emerging trends suggest that carbon and low-alloy steel castings will continue to advance, providing even more value to manufacturers and industries around the world.
What Are the Key Future Trends in Casting?
- Increased Use of High-Performance Alloys: As industries demand even more robust materials, advanced alloys will become increasingly popular.
- Sustainability: Manufacturers will focus on sustainable practices, including using recycled materials and reducing emissions.
- Digital Manufacturing: The integration of digital technologies in casting processes will help streamline operations and improve quality.
Table 14: Future Trends in Steel Casting
Trend | Description | Expected Impact |
---|---|---|
High-Performance Alloys | Use of advanced alloys for demanding applications | Improved product performance |
Sustainability | Focus on eco-friendly practices and materials | Reduced environmental impact |
Digital Manufacturing | Use of digital tools and automation in casting | Enhanced quality and efficiency |
15. Conclusion
Carbon and low-alloy steel investment castings are essential materials for industries requiring high strength, durability, and precision. With benefits such as excellent surface finish, reduced material waste, and the ability to withstand high temperatures, these castings play a crucial role in manufacturing components for automotive, aerospace, and energy sectors. By understanding the advantages and applications of carbon and low-alloy steel castings, manufacturers can make informed decisions about their production needs.
Conclusion
Carbon and low-alloy steel investment castings are essential materials for industries requiring high strength, durability, and precision. With benefits such as excellent surface finish, reduced material waste, and the ability to withstand high temperatures, these castings play a crucial role in manufacturing components for automotive, aerospace, and energy sectors. By understanding the advantages and applications of carbon and low-alloy steel castings, manufacturers can make informed decisions about their production needs.
FAQ Section
Q1: What are carbon and low-alloy steel investment castings?
Carbon and low-alloy steel investment castings are parts created through the investment casting process using carbon and low-alloy steel, known for their strength and durability in high-stress environments.
Q2: How does the investment casting process work?
Investment casting involves creating a pattern, coating it with a shell, and then melting the pattern away to form a mold. Molten metal is poured into the mold to create the final part.
Q3: What are the benefits of using carbon and low-alloy steel in investment casting?
These materials offer high precision, excellent surface finish, reduced material waste, and the ability to withstand extreme conditions, making them ideal for critical applications in various industries.
Q4: How does heat treatment affect the properties of carbon and low-alloy steel castings?
Heat treatment enhances the strength, hardness, and fatigue resistance of carbon and low-alloy steel castings, making them suitable for demanding applications where durability is essential.
Q5: How do carbon and low-alloy steel castings compare to other materials?
Carbon and low-alloy steel offer superior strength, durability, and cost-effectiveness, making them better suited for high-performance components compared to materials like aluminum or copper alloys.