When selecting materials for high-temperature applications, it’s essential to choose the best alloys that will perform effectively under extreme conditions. High-temperature alloys are engineered for use in environments where traditional metals would degrade or fail. These alloys are resistant to oxidation, corrosion, and high heat, making them crucial in industries such as aerospace, power generation, and chemical processing. In this article, we will explore the different types of high-temperature alloys, their properties, and how to choose the right one for your specific needs.
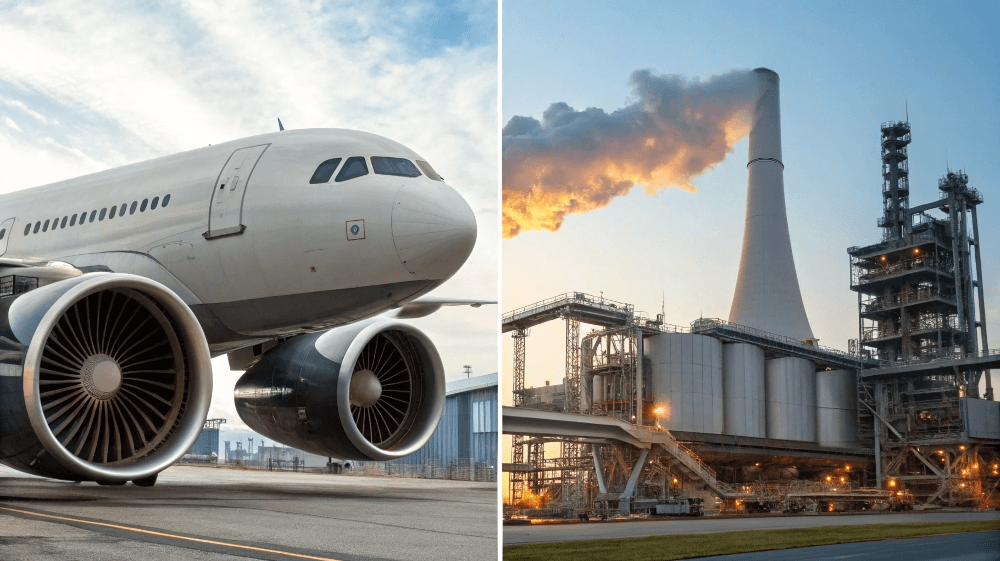
1. What Are High-Temperature Alloys?
High-temperature alloys are designed to withstand extreme temperatures without losing their strength or other mechanical properties. These materials are used in environments that exceed the limits of standard metals, often exceeding 500°C. But what makes these alloys so special?
High-temperature alloys are typically made from base metals like nickel, cobalt, and titanium, each offering unique advantages depending on the specific application. For example, nickel-based alloys are known for their high strength at elevated temperatures and resistance to oxidation, making them ideal for gas turbines and engine components. Cobalt-based alloys, on the other hand, are often used in environments with heavy oxidation and high wear rates. Titanium-based alloys, while lightweight, are favored for their excellent strength-to-weight ratio and resistance to corrosion at high temperatures.
These alloys are found in a wide range of industries, including aerospace, automotive, power generation, and even the medical field. The need for high-temperature alloys is growing as industries continue to push the limits of heat and stress resistance in components such as engine parts, turbines, and other critical machinery.
What’s the real story behind high-temperature alloys? They are essential in applications where failure could lead to catastrophic results, such as in aircraft engines or nuclear power plants. Choosing the right alloy can be the difference between a component’s reliable performance and a costly failure.
Alloy Type | Key Characteristics | Common Applications |
---|---|---|
Nickel-Based | High strength at elevated temperatures, oxidation resistant | Gas turbines, jet engines |
Cobalt-Based | Excellent wear resistance, oxidation resistant | Aerospace, medical devices |
Titanium-Based | Lightweight, high strength-to-weight ratio, corrosion resistant | Aerospace, automotive, medical |
2. Key Factors to Consider When Choosing High-Temperature Alloys
Choosing the right high-temperature alloy isn’t as simple as picking the most expensive or most well-known option. Ready for the good part? There are several key factors you need to consider to ensure that the alloy you choose will meet the demands of your specific application.
The most critical factor is temperature resistance. High-temperature alloys are designed to maintain their mechanical properties at elevated temperatures, but each alloy has a specific temperature range where it performs best. For example, some alloys can withstand temperatures up to 1,200°C, while others may only be suitable for applications up to 800°C.
Another important factor is mechanical properties, such as strength, ductility, and fatigue resistance. These properties determine how well the alloy can withstand not just heat, but also the stresses and strains that come with long-term use in demanding conditions. For instance, some alloys may be highly resistant to heat but brittle under mechanical stress, making them unsuitable for certain high-impact applications.
Lastly, corrosion resistance is crucial. High-temperature alloys are often exposed to harsh environments, including corrosive gases, chemicals, and moisture. The ability of the alloy to resist corrosion at elevated temperatures is vital for ensuring the longevity and reliability of components. Nickel-based alloys, for instance, are known for their excellent resistance to oxidation and corrosion, making them ideal for use in gas turbines.
Key Factor | Description | Example Alloy |
---|---|---|
Temperature Resistance | The alloy’s ability to withstand high temperatures | Nickel-based alloys |
Mechanical Properties | Strength, fatigue resistance, and ductility | Cobalt-based alloys |
Corrosion Resistance | Resistance to oxidation and degradation | Titanium-based alloys |
3. Common High-Temperature Alloys and Their Applications
High-temperature alloys are diverse and tailored to specific uses. But here’s the kicker… understanding the types of alloys and their best applications can make all the difference in the performance and longevity of critical components.
Nickel-based alloys are some of the most commonly used high-temperature materials. These alloys are used in extreme conditions such as gas turbines, jet engines, and chemical reactors. One well-known example is Inconel, a high-performance alloy that can withstand temperatures up to 1,000°C without losing its strength. It’s the go-to material for many high-temperature applications where both strength and oxidation resistance are required.
Cobalt-based alloys, while similar to nickel alloys, excel in environments where wear and tear are a concern. They are often used in applications such as turbine blades, medical implants, and other high-wear applications. The high wear resistance of cobalt alloys makes them ideal for parts subjected to constant friction and abrasion.
Titanium-based alloys, though lighter in weight, offer remarkable strength and corrosion resistance, making them suitable for applications where both heat resistance and weight are critical. These alloys are commonly used in the aerospace industry for aircraft components and automotive applications where fuel efficiency and performance are essential.
The key takeaway here? Each type of high-temperature alloy has unique properties that make it suited for specific applications. Understanding the differences can help you make the right choice for your needs.
Alloy Type | Temperature Range | Applications |
---|---|---|
Nickel-Based | Up to 1,200°C | Gas turbines, jet engines, chemical reactors |
Cobalt-Based | Up to 1,100°C | Turbine blades, medical implants |
Titanium-Based | Up to 800°C | Aerospace, automotive, medical |
4. How High-Temperature Alloys Are Tested
What’s the real story behind high-temperature alloys? Before any alloy is deemed suitable for high-temperature use, it must undergo rigorous testing. These tests simulate real-world conditions to ensure that the material will hold up under extreme conditions.
One of the most common tests for high-temperature alloys is heat resistance testing, which involves subjecting the material to high temperatures for extended periods to see how it reacts. This test helps determine the maximum temperature at which the alloy can maintain its strength and durability.
Fatigue tests are also important. These tests simulate the cyclical stress that materials experience over time, especially in high-stress environments like engines or turbines. High-temperature alloys are often subjected to thousands, if not millions, of cycles of thermal and mechanical stress to ensure they won’t fail prematurely.
Corrosion and oxidation tests are crucial, especially for alloys used in chemical processing or aerospace applications. These tests expose the alloys to corrosive environments at high temperatures to determine how well they resist degradation over time.
By understanding the types of tests high-temperature alloys undergo, you can make more informed decisions about the best material for your application.
Test Type | Purpose | Example Application |
---|---|---|
Heat Resistance | Measures the ability to withstand heat | Gas turbines, jet engines |
Fatigue Resistance | Simulates cyclical stress | Turbine blades, reactors |
Corrosion Resistance | Assesses resistance to oxidation and corrosion | Aerospace, chemical reactors |
5. Industries That Rely on High-Temperature Alloys
High-temperature alloys are used across numerous industries, and their applications are essential to ensuring safety, performance, and efficiency. But here’s where it gets interesting… the demand for high-temperature alloys is only increasing as industries continue to push the boundaries of technology and performance.
In the aerospace industry, for example, high-temperature alloys are used extensively in jet engines, where they need to withstand the extreme heat generated by combustion. Components like turbine blades and engine nozzles are often made from nickel-based alloys, as they offer exceptional heat resistance and strength at high temperatures.
Power generation is another key industry where high-temperature alloys are critical. Gas turbines and other equipment in power plants rely on high-temperature alloys to maintain performance in extreme heat conditions. The ability of these alloys to perform under high stress and temperature is crucial to the efficiency and reliability of power generation.
The automotive industry also benefits from high-temperature alloys, especially in performance vehicles and engines. Titanium alloys, for example, are used in exhaust systems due to their high strength-to-weight ratio and resistance to heat and corrosion.
High-temperature alloys are also indispensable in the chemical processing industry, where they are used in reactors, heat exchangers, and other equipment exposed to high temperatures and corrosive substances. Without these specialized alloys, many processes would be inefficient or impossible.
Industry | Applications | Common Alloys Used |
---|---|---|
Aerospace | Jet engines, turbine blades | Nickel-based alloys |
Power Generation | Gas turbines, reactors | Cobalt-based alloys |
Automotive | Exhaust systems, engine components | Titanium-based alloys |
Chemical Processing | Heat exchangers, reactors | Nickel-based alloys |
6. Advantages of Using High-Temperature Alloys
Ready for the good part? High-temperature alloys offer a variety of advantages that make them indispensable for industries requiring extreme heat resistance. The most significant benefit is their ability to maintain structural integrity at elevated temperatures, making them ideal for high-performance applications.
One of the main reasons high-temperature alloys are so beneficial is their resistance to oxidation and corrosion. Many alloys, particularly nickel-based alloys, are highly resistant to oxidation, ensuring they won’t degrade over time, even in harsh conditions like high-pressure environments and exposure to corrosive gases.
Another advantage is their strength under stress. High-temperature alloys maintain their strength and mechanical properties even at extreme temperatures, unlike standard metals, which can become brittle and fail. This is particularly important in industries like aerospace, where failure can result in catastrophic consequences.
Finally, the longevity of high-temperature alloys makes them a cost-effective solution in the long run. While they may have a higher initial cost compared to standard metals, their durability and resistance to failure can reduce maintenance costs and downtime, leading to significant savings over time.
Advantage | Description | Example Alloy |
---|---|---|
Oxidation Resistance | Prevents degradation in high-temperature environments | Nickel-based alloys |
Strength Under Stress | Maintains mechanical properties at extreme temperatures | Cobalt-based alloys |
Longevity | Reduces maintenance costs and downtime | Titanium-based alloys |
7. Potential Challenges with High-Temperature Alloys
While high-temperature alloys offer numerous benefits, they are not without their challenges. So, what’s the deal with these materials? While they provide unmatched strength and heat resistance, they come with some drawbacks that must be considered before making a choice.
First and foremost, high-temperature alloys are often significantly more expensive than other materials. The production processes for these alloys are complex and require specialized equipment, which increases costs. This can make high-temperature alloys a less attractive option for companies on a tight budget or for applications that don’t require extreme heat resistance.
Another challenge is the difficulty in processing and machining these alloys. High-temperature alloys are often harder and more brittle than other materials, which makes them difficult to shape and machine. This can increase production time and cost, making them less practical for some applications.
Material availability is also a concern. Some high-temperature alloys, especially those based on rare metals like cobalt and titanium, may not be readily available in large quantities, making it harder to source the necessary materials for large-scale production.
Challenge | Description | Example Impact |
---|---|---|
High Cost | Expensive production processes | Higher upfront costs |
Difficult Processing | Harder to machine and shape | Increased production time |
Material Availability | Limited availability of some alloys | Challenges in sourcing |
8. How to Ensure You Are Choosing the Right Alloy for Your Needs
Choosing the right high-temperature alloy for your application is critical, and there are several steps you can take to ensure you make the right decision. But here’s where it gets interesting… understanding the factors that matter most will make the selection process easier and more efficient.
Start by evaluating the environmental conditions your alloy will be exposed to. Are you working with high-pressure gases? Will the alloy be subjected to corrosion or oxidation? These factors will help you narrow down the types of alloys you should consider.
Next, consult with engineers and suppliers who have experience with high-temperature alloys. Their knowledge and expertise can guide you toward the best material for your needs, ensuring that you choose an alloy that will perform well over time.
Comparing performance data from different alloys is also essential. Look for materials with strong track records in similar applications, and review test data and case studies to see how they have performed in real-world conditions.
Selection Factor | Importance | Example Action |
---|---|---|
Environmental Factors | Determines alloy suitability for specific conditions | Temperature, corrosion |
Expert Consultation | Provides guidance on material choice | Consult engineers |
Performance Data | Helps assess long-term reliability and suitability | Review case studies |
9. The Role of High-Temperature Alloys in Future Technology
High-temperature alloys are constantly evolving to meet the needs of new technologies and industries. But what’s the future of high-temperature alloys? As industries like aerospace and power generation continue to develop new, more efficient systems, the demand for advanced high-temperature alloys is only expected to grow.
Innovations in materials science are leading to the development of even more advanced alloys with improved properties, such as higher heat resistance, better oxidation resistance, and increased strength. These advancements will enable industries to push the limits of performance, efficiency, and reliability.
Processing techniques are also improving, making it easier and more cost-effective to produce high-temperature alloys in large quantities. These innovations will likely drive down costs and make high-temperature alloys more accessible to a wider range of industries.
The key takeaway? The future of high-temperature alloys is bright, with ongoing research and development pushing the boundaries of what’s possible in extreme environments.
Trend | Description | Example Impact |
---|---|---|
Material Innovation | Development of advanced high-temperature alloys | Improved performance |
Processing Advances | Enhanced methods for producing alloys | Reduced production costs |
Market Expansion | Growing demand for high-temperature alloys | More industries using alloys |
10. How High-Temperature Alloys Impact Sustainability
Ready for the good part? High-temperature alloys can have a significant impact on sustainability, both in terms of their production and their use. These materials are designed to last longer than standard metals, reducing the need for frequent replacements and lowering overall material waste.
Many high-temperature alloys are also recyclable, which helps reduce the environmental impact of mining and material processing. Recycled alloys maintain their properties and can be reused in manufacturing, making them a more sustainable option than virgin materials.
Moreover, the development of more efficient alloys and production techniques is leading to less waste and energy consumption during manufacturing. These advancements contribute to the overall sustainability of high-temperature alloys, making them a more eco-friendly choice for industries with stringent environmental standards.
Sustainability Factor | Description | Example Alloy |
---|---|---|
Longevity | Reduces material waste by lasting longer | Nickel-based alloys |
Recyclability | Many alloys can be recycled to reduce waste | Cobalt-based alloys |
Production Efficiency | Improved manufacturing reduces energy usage | Titanium-based alloys |
11. The Importance of Proper Alloy Maintenance
What’s the real story behind alloy maintenance? Choosing the right alloy is just the first step; maintaining it properly ensures that it performs at its best over time. Proper alloy maintenance is crucial for extending the lifespan of high-temperature components, especially those used in high-stress environments.
Preventive maintenance is the best approach. Regular inspections and cleaning can prevent the buildup of contaminants that could lead to corrosion or oxidation. For alloys exposed to extreme temperatures, checking for early signs of fatigue or cracking is vital to avoid catastrophic failure.
Early detection of wear and tear can save businesses significant costs by avoiding unscheduled downtime and expensive repairs. Proper maintenance routines ensure that high-temperature alloys continue to perform reliably, even in the most demanding applications.
Maintenance Practice | Importance | Example Alloy Usage |
---|---|---|
Regular Inspections | Identifies early signs of wear and damage | Aerospace components |
Cleaning | Prevents buildup of contaminants | Power generation parts |
Fatigue Detection | Ensures alloys don’t fail prematurely | Chemical reactors |
12. Comparing High-Temperature Alloys to Other Metals
Ready for the good part? Comparing high-temperature alloys with other metals, like stainless steel and aluminum alloys, is key to understanding their unique benefits. While these other metals have their uses, high-temperature alloys offer unparalleled performance in extreme conditions.
For example, while stainless steel is corrosion-resistant, it tends to lose strength at high temperatures, making it unsuitable for applications where heat resistance is paramount. Aluminum alloys are lightweight but lack the high-temperature strength and durability required for demanding industrial applications.
High-temperature alloys, on the other hand, are specifically engineered to maintain strength, resist corrosion, and perform under extreme conditions, making them the superior choice for industries like aerospace, power generation, and chemical processing.
Metal Type | Advantages | Limitations |
---|---|---|
Stainless Steel | Corrosion-resistant | Loses strength at high temperatures |
Aluminum Alloys | Lightweight | Poor performance at high temperatures |
High-Temperature Alloys | High strength, corrosion-resistant, durable | Higher cost, difficult processing |
13. Buying High-Temperature Alloys: What to Look For
When buying high-temperature alloys, it’s important to keep a few key considerations in mind. Ready for the good part? Price is a factor, but quality should be your top priority. High-temperature alloys are expensive, so choosing a reputable supplier is essential to ensure you’re getting the right material for your application.
Certifications are another important factor. Look for alloys that meet industry standards, such as those set by ASTM (American Society for Testing and Materials) or ISO (International Organization for Standardization). These certifications ensure that the alloy meets the necessary performance criteria.
Lastly, understanding the specific alloy’s performance data is crucial. The supplier should be able to provide detailed test results and specifications to help you make an informed decision about the alloy’s suitability for your needs.
Consideration | Description | Example Action |
---|---|---|
Price | Ensure you’re getting a good deal without compromising quality | Compare suppliers |
Certifications | Look for industry certifications like ASTM or ISO | Check supplier credentials |
Performance Data | Ensure the alloy performs well in your application | Request test results |
14. Conclusion
In conclusion, choosing the right high-temperature alloy is a critical decision that impacts the performance and reliability of your equipment. From nickel-based alloys to cobalt and titanium, each type of high-temperature alloy offers unique advantages depending on your specific needs. Understanding the properties, applications, and challenges of each alloy type ensures that you can make an informed decision that maximizes performance and minimizes costs.
Take your time to evaluate the environmental conditions, consult with experts, and review performance data before making your final choice. With the right high-temperature alloy, you’ll ensure that your components perform at their best, even in the most extreme conditions.
FAQ Section
Q1: What is a high-temperature alloy?
A high-temperature alloy is a material designed to perform under extreme heat conditions, maintaining its strength and durability even at temperatures above 500°C.
Q2: How does high-temperature alloy work?
High-temperature alloys work by maintaining their mechanical properties, such as strength and resistance to corrosion, at elevated temperatures. They are engineered for use in demanding environments where traditional metals would fail.
Q3: What are the common types of high-temperature alloys?
The most common high-temperature alloys are nickel-based, cobalt-based, and titanium-based alloys. Each has unique properties suited for different industrial applications.
Q4: Why are high-temperature alloys important for aerospace applications?
High-temperature alloys are essential in aerospace applications because they can withstand the extreme heat generated by jet engines, ensuring safe and reliable performance of critical components.
Q5: Can high-temperature alloys be recycled?
Yes, many high-temperature alloys are recyclable. This helps reduce material waste and supports sustainability in industries that rely on these alloys.