Titanium investment casting is widely used in industries such as aerospace and medical devices because of the material’s strength, corrosion resistance, and ability to withstand high temperatures. However, the process can lead to a variety of defects that compromise the integrity of the final product. These defects can result from poor casting techniques, improper material handling, or insufficient quality control. In this article, we will explore the most common defects in titanium investment casting and discuss practical solutions to prevent them. Ready to learn how to perfect your casting process? Let’s dive in.
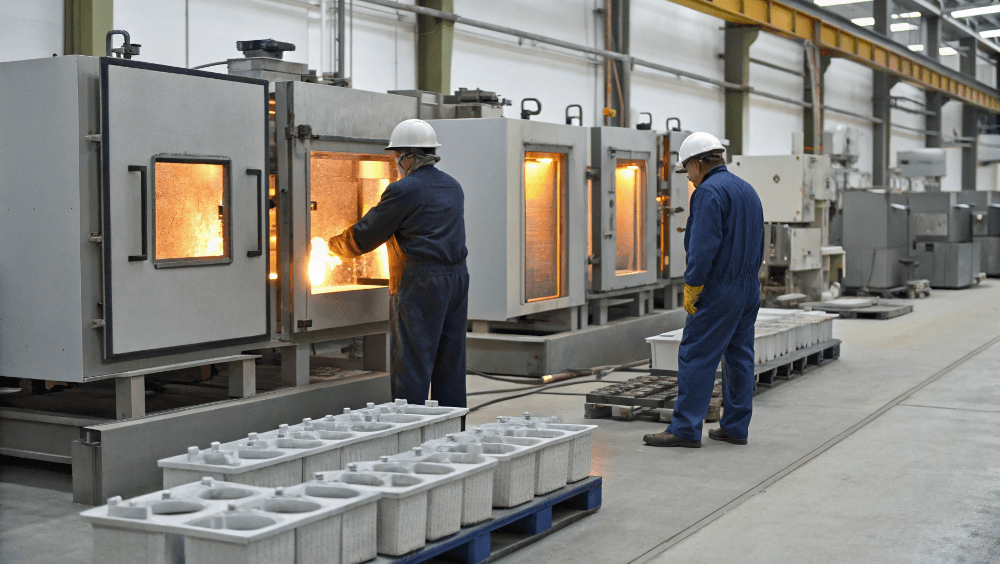
1. Introduction to Titanium Investment Casting Defects
Titanium investment casting is a specialized process that allows manufacturers to create highly intricate shapes with precision. Unlike traditional metalworking methods, investment casting involves creating a detailed mold, pouring molten titanium into it, and then removing the mold to reveal the finished part. While this method offers exceptional advantages, including the ability to produce complex geometries, it also presents challenges, particularly in ensuring the quality of the final product.
What’s the real story? The main issue with titanium investment casting lies in the defects that can arise during the process. These defects can impact the functionality and strength of the casting, leading to expensive rework and product failures. The most common defects in titanium castings include porosity, surface imperfections, dimensional inaccuracies, and cracks. These issues are typically caused by a variety of factors such as mold design, molten metal handling, and casting environment.
Let’s take a closer look at these defects and discuss how they can be addressed. The good news is that many of these issues are preventable with the right techniques and attention to detail.
Table 1: Common Titanium Investment Casting Defects
Defect | Description | Cause |
---|---|---|
Porosity | Air pockets trapped inside the casting. | Improper mold material, gas contamination. |
Surface Imperfections | Rough, uneven, or blemished surfaces. | Inadequate mold preparation or contamination. |
Dimensional Inaccuracies | Casting doesn’t meet specified dimensions. | Inaccurate mold design or temperature variations. |
Cracking and Brittleness | Cracks that weaken the structure. | Poor material handling or rapid cooling. |
2. What is Titanium Investment Casting?
Titanium investment casting, often referred to as lost-wax casting, is a highly versatile method of creating metal parts with exceptional precision. The process involves creating a detailed model, usually from a wax or plastic material, which is coated in a ceramic shell. After the shell hardens, it is heated to remove the wax, leaving a cavity in the shape of the desired part. The mold is then filled with molten titanium, and once it cools and solidifies, the ceramic shell is broken away to reveal the cast metal.
This technique is especially useful for producing parts with complex geometries that would be difficult or impossible to create using other methods. Industries such as aerospace, medical devices, and automotive heavily rely on titanium investment casting due to the material’s high strength-to-weight ratio and resistance to corrosion and heat.
But here’s the kicker… even though titanium is an ideal material for casting, it is also one of the most challenging metals to work with. Its high melting point and reactivity with air and moisture mean that the casting process requires meticulous control over temperature and environmental factors. When defects occur, the consequences can be costly, leading to delays and compromised product quality.
Table 2: Applications of Titanium Investment Casting
Industry | Application Example | Why Titanium is Used |
---|---|---|
Aerospace | Aircraft engine components | High strength, light weight, heat resistance. |
Medical Devices | Prosthetics, surgical instruments | Biocompatibility, corrosion resistance. |
Automotive | Turbochargers, exhaust systems | Durability, high-temperature performance. |
3. Common Titanium Investment Casting Defects
When it comes to titanium investment casting, defects are a significant concern for manufacturers. Some of the most common defects include porosity, surface imperfections, dimensional inaccuracies, and cracking. These issues not only affect the final product’s appearance but can also compromise its mechanical properties, leading to potential failures in high-performance applications.
What’s the real story? The impact of these defects can be far-reaching. Porosity, for example, weakens the titanium casting and makes it prone to cracking under stress. Surface imperfections can interfere with the part’s fit and finish, while dimensional inaccuracies can result in parts that don’t meet specifications, rendering them useless for the intended purpose. Cracking and brittleness can significantly reduce the strength and durability of the castings, which is particularly problematic in industries like aerospace where safety is paramount.
Table 3: Causes and Solutions for Common Titanium Casting Defects
Defect | Cause | Solution |
---|---|---|
Porosity | Poor mold material, gas contamination | Improve mold material, control gas flow. |
Surface Imperfections | Inadequate mold preparation | Use better cleaning methods, avoid contamination. |
Dimensional Inaccuracies | Inaccurate mold design or temperature variations | Optimize mold design, control temperature closely. |
Cracking and Brittleness | Rapid cooling or improper material handling | Slow cooling, handle material carefully. |
4. Understanding Porosity in Titanium Castings
Porosity refers to the presence of small holes or voids within the material, often caused by trapped gases or moisture during the casting process. In titanium investment casting, porosity is particularly concerning because it can reduce the material’s strength and compromise its structural integrity. Even tiny pores can result in a failure under stress, making the part unsuitable for critical applications.
What’s the real story? Porosity in titanium castings is typically caused by a few key factors, including improper mold materials, poor handling of the molten titanium, and contamination of the mold by gases or moisture. These issues prevent the molten titanium from properly filling the mold and solidifying without air pockets.
To prevent porosity, manufacturers must take care to maintain a clean environment during the casting process. Using high-quality mold materials that are less prone to gas absorption, controlling the humidity and temperature in the foundry, and ensuring that the molten titanium is free from contaminants are all crucial steps in preventing porosity. Additionally, using vacuum-assisted casting techniques can help to reduce the occurrence of gas entrapment.
Table 4: Factors Contributing to Porosity in Titanium Castings
Factor | Contribution to Porosity | Prevention Method |
---|---|---|
Mold Material | Absorbs gases, leading to trapped air. | Use higher-quality, non-porous materials. |
Contaminants | Gases and moisture cause air pockets. | Maintain a clean, dry environment. |
Molten Titanium | Gas absorption during pouring. | Vacuum-assisted pouring techniques. |
5. Causes of Surface Defects in Titanium Investment Casting
Surface defects in titanium castings can range from minor blemishes to large-scale imperfections that significantly affect the part’s performance and appearance. These defects often arise from improper mold preparation, contamination during casting, or issues with the cooling process. Surface defects can make the final product unusable, especially in applications where aesthetics or smooth surfaces are essential, such as in medical devices or consumer electronics.
Ready for the good part? The good news is that surface defects can be minimized or even eliminated with careful preparation and handling. One of the most common causes of surface imperfections is the presence of foreign materials, such as dust or moisture, in the mold. These contaminants can cause bubbles or rough patches on the surface of the cast. Another common issue is the cooling process. If the titanium cools too quickly, it can cause the surface to crack or warp.
To prevent surface defects, manufacturers need to ensure that the mold is thoroughly cleaned before use, that the molten titanium is free from contaminants, and that the cooling process is carefully controlled to prevent stress cracks. Using an appropriate surface treatment process, such as shot blasting or polishing, can also help to improve the final finish.
Table 5: Prevention Methods for Surface Defects in Titanium Castings
Defect | Cause | Prevention Method |
---|---|---|
Surface Imperfections | Contaminants in the mold | Thorough cleaning and proper handling. |
Cracking | Rapid cooling or improper mold material | Slow cooling, proper mold material. |
Blemishes | Foreign particles in molten titanium | Ensure clean, dust-free environment. |
6. Dimensional Inaccuracies in Titanium Castings
Dimensional inaccuracies are another common issue in titanium investment casting. These inaccuracies can range from slight variations in size to large discrepancies that make the part unusable. Dimensional issues are often caused by errors in the mold design, improper pouring temperatures, or inadequate cooling rates. The impact of dimensional inaccuracies is significant, as even small errors can result in parts that do not meet the required specifications.
What’s the real story? Dimensional inaccuracies often occur due to inconsistent temperatures during the casting process or errors in the mold design itself. If the mold is not properly calibrated or if the temperature of the molten titanium fluctuates too much, the final casting can end up being too large, too small, or misshapen. These dimensional problems can lead to costly rework, delays, and part failures.
To minimize dimensional inaccuracies, manufacturers need to focus on improving the mold design and closely controlling the pouring temperature and cooling rate. Using advanced measurement tools during the design phase and ensuring that the mold is accurately aligned during casting can help to maintain the desired dimensions.
Table 6: Causes and Solutions for Dimensional Inaccuracies
Cause | Impact on Dimensions | Solution |
---|---|---|
Mold Design | Incorrect design leads to size discrepancies. | Optimize mold design for better accuracy. |
Temperature Variations | Causes uneven expansion and contraction. | Maintain consistent pouring temperature. |
Cooling Rate | Fast cooling leads to warping and shrinkage. | Slow cooling and controlled environment. |
7. Cracking and Brittleness in Titanium Investment Castings
Cracking and brittleness are two of the most concerning issues when it comes to titanium investment casting. These problems occur when the titanium does not solidify properly or when the material becomes too fragile to withstand stress. Cracking can occur during cooling, while brittleness is often caused by poor material handling or improper temperature control during the casting process.
But here’s the kicker… Cracking and brittleness can lead to catastrophic failures, especially in high-stress applications like aerospace and medical devices. These issues can make the titanium casting unsuitable for its intended use, requiring expensive rework or replacement.
To prevent cracking and brittleness, it is essential to control the cooling process. Rapid cooling can create internal stresses in the casting that lead to cracks. Manufacturers should use a slower cooling rate and handle the material carefully to prevent damage. Additionally, proper alloy selection and heat treatment processes can improve the toughness of the titanium, reducing the risk of brittleness.
Table 7: Solutions to Prevent Cracking and Brittleness in Titanium Castings
Issue | Cause | Solution |
---|---|---|
Cracking | Rapid cooling, poor material handling | Slow cooling, proper material handling. |
Brittleness | Poor alloy selection, incorrect heat treatment | Use appropriate alloys, heat treatment. |
8. The Role of Mold Design in Minimizing Defects
The design of the mold plays a crucial role in the quality of the final titanium casting. A poorly designed mold can lead to a variety of defects, such as dimensional inaccuracies, surface imperfections, and cracking. Mold design must consider factors like material flow, temperature control, and ease of mold removal to ensure that the titanium casting is free of defects.
What’s the real story? Mold design is more than just creating a mold that fits the desired shape. It requires a deep understanding of how titanium behaves under various conditions and how the molten material will flow through the mold. Key elements such as venting, gating, and risers must be designed correctly to ensure the mold fills evenly and that any trapped gases can escape. The right mold material is also essential for preventing contamination and ensuring a smooth surface finish.
Table 8: Key Elements in Mold Design for Titanium Casting
Element | Role in Defect Prevention | Best Practices |
---|---|---|
Venting | Allows gases to escape, preventing porosity. | Design vents to let air flow freely. |
Gating | Controls the flow of molten material. | Ensure gates are appropriately placed. |
Risers | Supplies additional molten metal during cooling. | Use risers to prevent shrinkage defects. |
9. Quality Control Measures for Titanium Investment Castings
Quality control is critical in ensuring that titanium castings meet the required standards. Several techniques are employed during the casting process to inspect for defects and ensure that the final product is of the highest quality. One of the most important quality control methods is X-ray inspection, which can detect internal defects such as porosity and cracks that are not visible on the surface.
What’s the real story? Quality control is a multi-step process that starts with inspecting raw materials and continues through every stage of the casting process. In addition to X-ray inspection, manufacturers may use ultrasound testing, visual inspection, and dye penetrant testing to identify surface and internal defects. Ensuring that all parts are thoroughly tested before shipment helps to avoid costly rework and product failures.
Table 9: Common Quality Control Methods for Titanium Castings
Method | Purpose | When to Use |
---|---|---|
X-ray Inspection | Detects internal defects like porosity. | During casting inspection and post-casting. |
Ultrasound Testing | Identifies cracks and voids inside the metal. | For thicker parts or complex geometries. |
Visual Inspection | Detects surface flaws. | For final inspection before shipment. |
10. Preventive Measures to Avoid Titanium Investment Casting Defects
Preventing defects in titanium investment casting requires a combination of proper planning, attention to detail, and the right technology. By taking proactive steps, manufacturers can reduce the likelihood of common defects such as porosity, cracking, and surface imperfections.
What’s the real story? Prevention starts with proper material selection and preparation. Using high-quality titanium alloys and ensuring the molds are free from contaminants is essential. Moreover, controlling the temperature of the molten titanium and the cooling rate of the casting can help prevent defects such as cracking and brittleness. Implementing these best practices ensures that the final product is defect-free and meets all the required specifications.
Table 10: Preventive Measures for Titanium Casting Defects
Defect | Prevention Method | Importance |
---|---|---|
Porosity | Use high-quality mold material, control gas flow. | Reduces air pockets and strengthens casting. |
Cracking | Slow cooling, proper material handling. | Prevents internal stresses. |
Surface Imperfections | Clean molds, control pouring temperature. | Ensures smooth, blemish-free finish. |
11. Post-Casting Treatment to Fix Defects
While preventive measures can significantly reduce defects, some issues may still arise after the casting is completed. In these cases, post-casting treatments can be used to correct defects and improve the overall quality of the part. Heat treatment, shot blasting, and polishing are common methods used to fix or improve castings.
But here’s the kicker… post-casting treatments can not only repair defects but also enhance the mechanical properties of the titanium castings. Heat treatment, for example, can relieve internal stresses and improve the strength of the part, while shot blasting and polishing can remove surface imperfections and improve the aesthetic quality.
Table 11: Post-Casting Treatment Methods
Treatment | Purpose | Best Practice |
---|---|---|
Heat Treatment | Relieves internal stresses, improves strength. | Use annealing or stress-relieving heat treatments. |
Shot Blasting | Removes surface imperfections. | Use appropriate grit size for titanium. |
Polishing | Improves surface finish, removes rough spots. | Ensure even pressure and temperature. |
12. Choosing the Right Foundry for Titanium Investment Casting
Choosing the right foundry for titanium investment casting is critical to ensuring the quality of the final product. When selecting a foundry, there are several factors to consider, including the foundry’s experience, reputation, and the quality of their equipment.
Ready for the good part? The ideal foundry will have experience in casting titanium and an understanding of the specific challenges associated with this material. They should also be able to demonstrate a commitment to quality control and provide evidence of their ability to consistently produce defect-free castings. Additionally, the foundry should use state-of-the-art equipment and employ skilled personnel who can handle the intricacies of titanium casting.
Table 12: Factors to Consider When Choosing a Foundry
Factor | Why It Matters | What to Look For |
---|---|---|
Experience | Ensures familiarity with titanium casting. | Proven track record in titanium casting. |
Reputation | Reflects the quality and reliability of the foundry. | Positive customer reviews and referrals. |
Equipment | Ensures precision and quality in casting. | Modern, well-maintained casting equipment. |
13. Case Studies: Common Defects and Their Solutions
Case studies provide valuable insight into how defects in titanium investment casting can be identified, addressed, and prevented. By analyzing real-world examples, manufacturers can learn from past mistakes and improve their casting processes.
What’s the real story? Let’s look at a few case studies to see how different defects have been handled in titanium casting. For example, a major aerospace company once faced significant issues with porosity in their castings. The solution was to implement vacuum-assisted casting techniques and improve their mold materials. In another case, dimensional inaccuracies were corrected by redesigning the mold and improving temperature control during the pouring process.
Table 13: Case Study Summary: Solutions to Defects
Defect | Company | Solution |
---|---|---|
Porosity | Aerospace Manufacturer | Vacuum-assisted casting, better mold material. |
Dimensional Inaccuracy | Automotive Company | Improved mold design, better temperature control. |
Surface Imperfections | Medical Device Maker | Enhanced mold cleaning, controlled pouring. |
14. Advanced Techniques for Improving Titanium Casting Quality
While traditional casting methods are effective, advanced techniques are continuously being developed to improve the quality and efficiency of titanium investment casting. Technologies such as 3D printing for mold design and the use of advanced alloys are leading the way in reducing defects and improving the overall performance of titanium castings.
What’s the real story? 3D printing has revolutionized mold design by allowing for more complex and precise mold geometries. This not only reduces the likelihood of defects but also speeds up the production process. Additionally, advancements in alloy development have led to the creation of titanium alloys that are more resistant to common casting issues, such as porosity and cracking.
Table 14: Advanced Techniques for Titanium Casting
Technique | Benefit | Application |
---|---|---|
3D Printing | Allows for complex, precise mold designs. | Faster production, fewer defects. |
Advanced Alloys | Reduces susceptibility to porosity and cracking. | Aerospace, medical devices. |
Vacuum Casting | Minimizes gas entrapment in the molten metal. | Prevents porosity in titanium castings. |
15. Conclusion and Best Practices
In conclusion, titanium investment casting is a powerful technique that allows manufacturers to create highly precise and durable components. However, as we have discussed, it is not without its challenges. The most common defects include porosity, surface imperfections, dimensional inaccuracies, and cracking, all of which can have serious consequences if not addressed properly.
What’s the real story? The key to success in titanium investment casting lies in understanding the causes of these defects and implementing preventive measures. Whether it’s improving mold design, controlling temperature, or using advanced materials, manufacturers have a range of tools at their disposal to ensure high-quality castings. By applying best practices, companies can minimize defects and produce titanium parts that meet the highest standards.
Table 15: Summary of Best Practices for Titanium Casting
Best Practice | Benefit | Application |
---|---|---|
Mold Design | Reduces defects by improving material flow. | Aerospace, automotive, medical devices. |
Temperature Control | Prevents cracking and dimensional inaccuracies. | Ensures high-quality, accurate castings. |
Material Selection | Prevents porosity and brittleness. | Enhances strength and durability. |
FAQ Section
Q1: What is titanium investment casting?
Titanium investment casting is a process used to create precise and complex metal parts by pouring molten titanium into a mold and allowing it to solidify.
Q2: How does porosity affect titanium castings?
Porosity causes tiny holes within the casting, weakening its structure and making it prone to failure under stress, particularly in high-performance applications.
Q3: What are the causes of surface defects in titanium castings?
Surface defects can be caused by contamination during the mold preparation process, poor mold material, or improper handling of the molten titanium.
Q4: How can dimensional inaccuracies be reduced in titanium investment casting?
Dimensional inaccuracies can be minimized by improving mold design, controlling the pouring temperature, and ensuring proper mold alignment.
Q5: What is the role of heat treatment in preventing casting defects?
Heat treatment, such as annealing, helps relieve internal stresses in the material, improving the overall strength and reducing the likelihood of cracks.