Aluminum casting plays a crucial role in various industries, providing lightweight, durable, and corrosion-resistant components for a wide range of applications. In this guide, we’ll explore the intricacies of aluminum casting, including the different methods, benefits, and challenges, and offer practical insights for choosing the right approach for your needs. Whether you’re new to aluminum casting or looking to optimize your current processes, this guide has something for everyone.
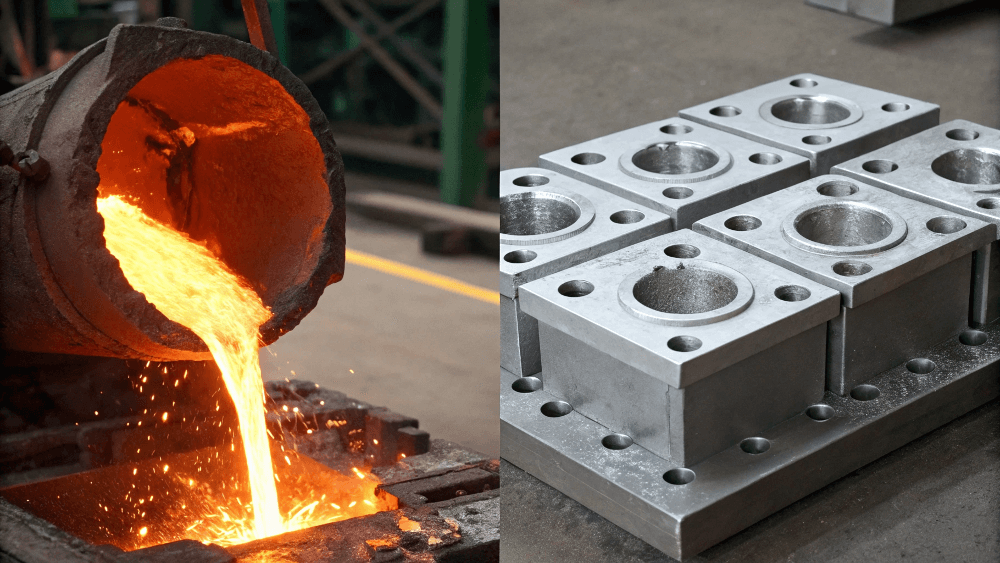
1. What is Aluminum Casting?
Aluminum casting refers to the process of pouring molten aluminum into molds to create a variety of shapes and parts used in industries such as automotive, aerospace, and electronics. This method is ideal for producing complex components with high precision, strength, and low weight. But here’s the kicker: aluminum casting not only provides a lightweight solution but also offers excellent corrosion resistance, making it an optimal choice for parts exposed to harsh environments.
Aluminum is a versatile metal, and when cast, it can be used in various industries to manufacture products ranging from engine blocks in vehicles to lightweight components for aerospace. The process involves melting aluminum at high temperatures and then pouring the liquid metal into molds designed to produce specific shapes. Once cooled, the aluminum solidifies, and the mold is removed, revealing the finished product. But that’s just the basics; the casting process itself is complex, with various factors influencing the quality of the final product.
One of the key advantages of aluminum casting is its ability to produce parts with intricate shapes that would be difficult or impossible to achieve using other manufacturing methods. This makes aluminum casting particularly valuable for industries that require highly customized, precision-engineered components. It’s no wonder that it’s a preferred choice for manufacturers worldwide.
Process Step | Description |
---|---|
Melting Aluminum | Aluminum is melted at high temperatures (1,200-1,400°F) |
Pouring into Mold | Molten aluminum is poured into a pre-designed mold |
Cooling & Solidifying | The aluminum cools and solidifies in the mold |
Mold Removal | Once cooled, the mold is removed, revealing the part |
2. What Are the Types of Aluminum Casting?
When it comes to aluminum casting, there are several methods to choose from, each offering different advantages depending on the application and requirements. Let’s break them down: sand casting, die casting, permanent mold casting, investment casting, and gravity die casting. Ready for the good part? Each of these methods has its own unique set of benefits that make it suitable for specific needs.
Sand Casting is one of the oldest and most widely used methods. It involves creating a mold from sand, which is then used to cast aluminum into the desired shape. This method is great for producing large, complex parts at a relatively low cost. However, it’s not ideal for high-precision or high-volume applications due to its limitations in accuracy.
Die Casting, on the other hand, uses high-pressure to force molten aluminum into steel molds. This method is well-suited for mass production, offering high accuracy and consistency. It’s commonly used in industries like automotive and electronics for parts like housings and engine components.
Permanent Mold Casting uses reusable molds, typically made of metal, to cast aluminum. This method is more efficient than sand casting in terms of cost and production speed. It’s suitable for medium to high-volume production, offering improved surface finishes and dimensional accuracy compared to sand casting.
Investment Casting is another precision casting method, often referred to as lost-wax casting. It involves coating a wax model with a ceramic shell, then melting the wax and pouring molten aluminum into the shell. This process is excellent for creating complex and detailed parts but can be expensive and time-consuming.
Gravity Die Casting relies on gravity to fill molds with molten aluminum, making it a cost-effective method for medium- to high-volume production of complex parts. It is often used in automotive applications for casting engine blocks and other structural components.
Casting Method | Ideal Applications | Benefits |
---|---|---|
Sand Casting | Large, complex parts | Low cost, great for custom shapes |
Die Casting | Mass production, high-precision parts | High accuracy, consistency |
Permanent Mold Casting | Medium to high-volume production | Reusable molds, improved surface finish |
Investment Casting | Detailed, complex parts | High precision, excellent surface finish |
Gravity Die Casting | Automotive, structural components | Cost-effective, versatile for complex shapes |
3. Why Choose Aluminum for Casting?
Why is aluminum so widely chosen for casting? It’s not just about its lightweight nature—although that’s a major advantage. Aluminum offers a range of benefits that make it an ideal material for casting, including its strength, resistance to corrosion, and thermal conductivity. Let’s explore the reasons why aluminum stands out in the casting world.
Aluminum’s light weight is perhaps its most well-known benefit. It’s roughly one-third the weight of steel, making it an excellent choice for applications where weight reduction is crucial, such as in the automotive and aerospace industries. This weight reduction helps improve fuel efficiency and reduce overall operational costs. But here’s the kicker: the strength-to-weight ratio of aluminum makes it a versatile material for a wide range of components, from structural parts to intricate, high-strength components.
Aluminum also excels in corrosion resistance, which is essential in environments where parts are exposed to moisture, chemicals, or extreme weather conditions. Unlike steel, which can rust over time, aluminum forms a protective oxide layer that shields the material from further corrosion. This makes aluminum particularly valuable in outdoor and marine applications.
Thermal conductivity is another reason aluminum is a preferred material for casting. Aluminum’s ability to conduct heat efficiently makes it ideal for parts that need to withstand high temperatures or dissipate heat quickly, such as engine components or heat exchangers. The material’s versatility in various applications, from lightweight structural components to heat-sensitive parts, makes it a go-to choice for manufacturers across multiple industries.
Benefit | Description |
---|---|
Lightweight | Aluminum is about one-third the weight of steel |
Corrosion Resistance | Forms a protective oxide layer to resist rust and damage |
Thermal Conductivity | Efficient heat dissipation, ideal for high-temperature parts |
Strength-to-Weight Ratio | High strength for its low weight, suitable for various applications |
4. How is Aluminum Casting Done?
So, how exactly is aluminum casting done? In its simplest form, the process involves melting aluminum and pouring it into a mold, but there’s much more to it than meets the eye. Let’s break it down step-by-step and give you a better understanding of the complexities involved in this process.
First, aluminum is melted in a furnace at temperatures typically between 1,200 and 1,400 degrees Fahrenheit. Once molten, the aluminum is carefully poured into the chosen mold. Depending on the casting method, the mold could be made of sand, metal, or ceramic. Once the molten aluminum is in the mold, it cools and solidifies, forming the final part.
But wait—there’s more to the process than just pouring molten aluminum into a mold. For optimal results, factors like cooling rates, mold material, and alloy composition must be carefully controlled. The cooling rate, for instance, affects the crystallization of the aluminum, which in turn impacts the strength and durability of the final product. The mold material is also crucial in determining the finish and precision of the part. A high-quality mold will produce a smoother surface and more accurate dimensions.
Once the aluminum has cooled and solidified, the mold is removed, leaving behind the cast part. However, this is not the end of the process. The part may undergo additional steps like heat treatment, machining, or surface finishing to meet specific requirements.
Process Step | Temperature Range | Key Considerations |
---|---|---|
Melting Aluminum | 1,200–1,400°F | Ensuring proper temperature for uniformity |
Pouring into Mold | N/A | Mold type influences surface finish |
Cooling & Solidifying | Varies by method | Cooling rate affects material properties |
Mold Removal | N/A | Post-processing may include machining or finishing |
5. What Are the Common Applications of Aluminum Casting?
Aluminum casting is used in a wide range of industries, from automotive to aerospace, and is highly valued for its lightweight and durable properties. Let’s take a closer look at some of the common applications where aluminum casting plays a crucial role.
In the automotive industry, aluminum casting is used to produce engine blocks, cylinder heads, transmission housings, and other structural components. The lightweight nature of aluminum helps reduce the overall weight of vehicles, which improves fuel efficiency and performance. Additionally, aluminum’s ability to withstand high temperatures makes it ideal for engine parts exposed to heat.
The aerospace industry also heavily relies on aluminum casting for components such as aircraft structural parts, engine components, and landing gear. The need for lightweight yet strong materials in this industry makes aluminum casting a perfect fit, as it ensures the durability and performance of aerospace equipment while minimizing weight.
In the electronics industry, aluminum casting is used to produce heat sinks, casings, and other components for electronic devices. The excellent thermal conductivity of aluminum helps dissipate heat efficiently, preventing overheating and ensuring the longevity of electronic products.
In industrial machinery, aluminum casting is used to manufacture components like gears, brackets, and housings. The versatility of aluminum casting allows manufacturers to create intricate and complex shapes with high precision, making it an invaluable tool for various machinery applications.
Industry | Application Examples | Benefits |
---|---|---|
Automotive | Engine blocks, cylinder heads, transmission housings | Lightweight, high thermal stability |
Aerospace | Aircraft structural parts, engine components | Strength-to-weight ratio, corrosion resistance |
Electronics | Heat sinks, casings | Efficient heat dissipation, protection from overheating |
Industrial Machinery | Gears, brackets, housings | Precision, versatility in complex shapes |
6. How Does Aluminum Casting Compare to Other Metals?
When choosing a material for casting, aluminum often stands out compared to other metals. So, what’s the real story when it comes to aluminum versus steel, copper, and other materials?
Let’s start with aluminum vs. steel. While steel is stronger than aluminum in terms of tensile strength, it’s much heavier. In applications where weight is a concern, aluminum takes the lead. Aluminum also has superior corrosion resistance compared to steel, making it ideal for outdoor and marine environments. However, steel is often preferred for heavy-duty applications that require maximum strength, like construction and infrastructure.
Aluminum vs. copper is another interesting comparison. Copper offers superior conductivity, making it a preferred choice for electrical applications. However, copper is much heavier and more expensive than aluminum. Aluminum provides a good balance between conductivity and weight, which is why it’s often used in electrical wiring and components.
When comparing aluminum to zinc alloys, aluminum is typically more cost-effective and versatile. Zinc alloys have higher strength, but they are also more prone to corrosion, whereas aluminum is highly resistant to corrosion and provides better value for many applications.
Ready for the good part? Aluminum casting offers the best of both worlds: it combines strength, light weight, and excellent corrosion resistance, making it a go-to choice for a wide range of industries.
Metal Comparison | Strength | Weight | Corrosion Resistance | Cost | Best Application |
---|---|---|---|---|---|
Aluminum vs. Steel | Lower tensile strength | Lighter | Higher | Lower | Automotive, Aerospace |
Aluminum vs. Copper | Moderate | Lighter | Moderate | Lower | Electrical, Electronics |
Aluminum vs. Zinc Alloys | Moderate | Lighter | Higher | Lower | General manufacturing |
7. What Are the Advantages of Aluminum Casting?
Aluminum casting offers a range of advantages that make it an attractive choice for manufacturers across industries. So, what’s in it for you?
First, aluminum’s lightweight nature makes it an ideal material for applications where reducing weight is a priority, such as in the automotive and aerospace industries. This lightweight property also helps lower fuel consumption and improves the overall efficiency of products.
Second, aluminum is highly resistant to corrosion, which is a key consideration for parts exposed to harsh environments. The protective oxide layer that forms on the surface of aluminum helps it resist rust and deterioration, ensuring a long lifespan for cast components.
Another advantage is aluminum’s thermal conductivity, which allows it to dissipate heat efficiently. This makes aluminum casting perfect for parts exposed to high temperatures, such as engine components and heat exchangers.
Finally, aluminum casting offers design flexibility, allowing manufacturers to create complex shapes and intricate details. This design freedom makes aluminum casting an ideal solution for a wide range of applications, from automotive parts to industrial machinery.
Advantage | Benefit |
---|---|
Lightweight | Reduces weight for improved fuel efficiency |
Corrosion Resistance | Provides durability in harsh environments |
Thermal Conductivity | Efficient heat dissipation for high-temperature parts |
Design Flexibility | Allows for complex shapes and intricate details |
8. What Are the Challenges of Aluminum Casting?
While aluminum casting has many advantages, it’s not without its challenges. Let’s dive into some of the common hurdles faced during the casting process and how they can impact the final product.
One of the main challenges in aluminum casting is shrinkage and porosity. When aluminum cools and solidifies, it tends to shrink, which can lead to voids or air pockets within the casting. These defects can compromise the structural integrity of the part and require costly rework or repairs.
Another challenge is controlling the cooling process. The rate at which aluminum cools can affect its final properties, including strength and surface finish. If the cooling rate is too fast or too slow, it can lead to defects like cracking or warping.
Complex mold designs can also pose difficulties. In some cases, intricate molds are required to produce parts with specific shapes or features. These molds can be expensive and time-consuming to create, adding to the overall cost of production.
Finally, aluminum casting can be costly and wasteful if not managed properly. Poor material management and inefficient processes can lead to material waste and higher operational costs. It’s essential to optimize production techniques to minimize these issues.
Challenge | Description | Mitigation Methods |
---|---|---|
Shrinkage & Porosity | Voids and defects from cooling shrinkage | Optimize cooling rate, control molten aluminum flow |
Cooling Process | Cracking or warping due to improper cooling rates | Control cooling rates, use molds designed for even cooling |
Complex Mold Designs | Costly and time-consuming to produce intricate molds | Use efficient design software, improve mold material selection |
Material Waste | Excessive waste and higher costs | Optimize casting techniques, reduce waste during production |
9. How Does the Aluminum Casting Process Affect Quality?
The quality of an aluminum casting is heavily influenced by the process itself. So, how do different factors impact the quality of the final product?
First, the temperature at which the aluminum is melted plays a crucial role in determining the quality of the casting. If the aluminum is overheated or underheated, it can affect the flow properties of the molten metal, leading to defects in the final product.
The cooling rate is also critical in aluminum casting. Rapid cooling can cause internal stresses that lead to cracks or warping. On the other hand, slow cooling can lead to poor surface finishes and dimensional inaccuracies. Achieving the right cooling rate is essential for producing high-quality castings.
The purity of the aluminum alloy used in the casting process is another key factor. Impurities in the metal can lead to weak spots, porosity, and other defects. Using high-quality alloys and ensuring proper material handling can help prevent these issues and ensure the final product meets specifications.
Quality Factor | Impact on Casting Quality | Recommended Practice |
---|---|---|
Temperature | Overheating or underheating affects metal flow | Monitor and maintain precise temperature during melting |
Cooling Rate | Rapid cooling leads to cracks; slow cooling impacts surface finish | Optimize cooling methods to control solidification rates |
Alloy Purity | Impurities cause defects like porosity and weak spots | Use high-quality alloys, control impurity levels |
10. What Are the Common Defects in Aluminum Casting?
Despite the best efforts to control the casting process, defects can still occur. Here are some of the most common defects seen in aluminum casting.
Cracking is one of the most common issues in aluminum casting. It can occur during cooling or due to improper handling of the mold. Cracks can weaken the casting and require rework or replacement.
Warpage happens when parts are subjected to uneven cooling or stresses during the casting process. This can cause parts to distort, leading to dimensional inaccuracies and issues with fit and function.
Surface defects such as roughness, pitting, or oxidation can also occur if the mold isn’t properly prepared or if the aluminum isn’t handled carefully during pouring. These defects can affect the aesthetic quality of the part and may require additional finishing steps.
Incomplete filling happens when the molten aluminum doesn’t fully fill the mold cavity. This can lead to gaps or voids within the part, compromising its structural integrity.
Porosity is another common defect caused by trapped air or gases during the casting process. Porous aluminum parts may be weaker and less durable, making them unsuitable for certain applications.
Defect | Description | Impact on Final Product |
---|---|---|
Cracking | Cracks form due to cooling or mold issues | Weakens casting, may require rework or replacement |
Warpage | Distortion from uneven cooling or stress | Affects dimensional accuracy and part fit |
Surface Defects | Roughness, oxidation, pitting | Requires additional finishing, affects aesthetic quality |
Incomplete Filling | Molten aluminum doesn’t fill mold cavity completely | Causes voids and weak spots in the final casting |
Porosity | Trapped air or gases cause air pockets | Reduces strength, makes parts unsuitable for critical applications |
11. How Can You Improve the Aluminum Casting Process?
Improving the aluminum casting process is essential for achieving higher-quality products and minimizing defects. Let’s take a closer look at some of the methods used to improve the casting process.
One of the most effective ways to improve aluminum casting is by optimizing cooling rates. By controlling the rate at which aluminum cools, manufacturers can reduce the risk of defects such as cracking and warping. Using advanced cooling systems or techniques, such as chills or controlled mold temperatures, can help achieve better results.
Choosing the right mold material is also important. The material used for the mold can affect the surface finish and precision of the cast part. High-quality molds made from durable materials, such as steel or ceramic, can improve the final product’s quality.
Using high-quality aluminum alloys and ensuring proper material handling can also help improve the casting process. Alloys with better flow properties and lower impurity levels are less likely to produce defects, ensuring a smoother casting process.
Incorporating automated processes into the casting line can further improve efficiency and reduce human error. Automation allows for greater consistency, reduced waste, and faster production cycles.
Improvement Method | Benefit | Impact on Casting Quality |
---|---|---|
Optimizing Cooling Rates | Reduces risk of defects like cracking and warping | Consistent cooling, better final part quality |
Using High-Quality Molds | Improves surface finish and dimensional accuracy | Smoother surfaces, more accurate parts |
Choosing High-Quality Alloys | Minimizes impurities and defects | Stronger, more durable castings |
Incorporating Automation | Improves consistency, reduces human error | Faster production, fewer defects |
12. What Are the Environmental Benefits of Aluminum Casting?
Aluminum casting isn’t just about performance—it also offers significant environmental benefits. Let’s explore some of the key ways in which aluminum casting is a sustainable choice.
One of the biggest environmental advantages of aluminum casting is its recyclability. Aluminum can be recycled multiple times without losing its properties, making it an environmentally friendly material for manufacturing. Recycling aluminum also uses far less energy than producing new aluminum from raw materials, which helps reduce carbon emissions.
Energy savings in the aluminum casting process are another significant environmental benefit. Aluminum casting requires less energy than many other casting processes, particularly when using efficient casting methods like die casting. This lower energy consumption helps reduce the environmental impact of production.
Finally, aluminum casting can reduce waste by producing near-net-shape parts that require little to no additional machining. This reduces material waste and the need for further processing, making it a more sustainable manufacturing option.
Environmental Benefit | Description | Impact on Sustainability |
---|---|---|
Recyclability | Aluminum can be recycled without losing quality | Reduces resource consumption and carbon emissions |
Energy Savings | Casting methods like die casting are energy efficient | Decreases overall energy usage and environmental impact |
Waste Reduction | Near-net-shape casting reduces material waste | Minimizes waste and the need for additional processing |
13. How Do You Choose the Right Aluminum Alloy for Casting?
Choosing the right aluminum alloy for casting is crucial to achieving the desired properties in your final product. So, how do you pick the right one?
There are several factors to consider, including the strength requirements, corrosion resistance, and casting method. For parts exposed to harsh environments or extreme temperatures, alloys with enhanced corrosion resistance or heat resistance are ideal.
Another factor to consider is the alloy composition. Aluminum alloys are made by mixing aluminum with other metals, such as copper, magnesium, or silicon. Each alloy has different properties that make it suitable for specific applications. For example, aluminum-silicon alloys are great for casting parts with complex shapes, while aluminum-magnesium alloys are ideal for parts requiring high strength and corrosion resistance.
The casting method also influences the choice of alloy. Some alloys flow better during casting, making them suitable for methods like die casting or sand casting. Choosing the right alloy for the casting method can help minimize defects and improve the overall quality of the final product.
Alloy Type | Key Properties | Ideal Applications |
---|---|---|
Aluminum-Silicon | Good flow, low shrinkage | Complex shapes, high-performance parts |
Aluminum-Magnesium | High strength, corrosion resistance | Structural components, marine applications |
Aluminum-Copper | High strength and hardness | Aerospace, high-temperature parts |
Aluminum-Zinc | Excellent castability, good corrosion resistance | Die casting, automotive components |
14. What Are the Costs Involved in Aluminum Casting?
The costs associated with aluminum casting can vary widely depending on factors such as the casting method, alloy choice, and part complexity. So, what should you expect when it comes to costs?
The primary costs involved in aluminum casting include the cost of raw materials, tooling, labor, and energy. Raw materials, such as aluminum alloys, can be a significant cost, particularly for high-performance alloys with specific properties.
Tooling costs can also be substantial, especially for complex molds or custom designs. Molds need to be durable and precise, which often requires significant investment. However, these costs can be offset by the efficiency and repeatability offered by certain casting methods, such as die casting.
Labor and energy costs are another factor to consider. Casting processes that require manual labor or extensive machining will increase the overall production cost. On the other hand, automated processes can reduce labor costs and improve production efficiency.
To reduce costs, manufacturers can focus on optimizing the casting process, reducing waste, and choosing cost-effective alloys and methods. But here’s the thing: while aluminum casting may seem expensive upfront, the long-term benefits in terms of durability, strength, and performance make it a worthwhile investment.
Cost Factor | Description | Methods to Reduce Costs |
---|---|---|
Raw Materials | Cost of aluminum alloys, especially high-performance types | Optimize alloy selection, bulk purchasing |
Tooling | Expense of custom molds or complex designs | Use efficient mold designs, select cost-effective materials |
Labor & Energy | Labor-intensive casting and machining processes | Automate processes, reduce manual labor |
Overall Production | Total cost of production per unit | Optimize cooling, reduce waste, streamline operations |
15. What Are the Future Trends in Aluminum Casting?
The aluminum casting industry is constantly evolving. As technology advances and manufacturers demand more efficient and sustainable solutions, new trends are emerging in the field. What are these trends, and what do they mean for the future of aluminum casting?
Automation and AI are increasingly playing a role in aluminum casting. Automated casting lines help improve consistency, reduce labor costs, and increase production speed. AI is also being used to optimize the casting process by predicting defects and improving quality control.
Sustainability is another key trend in aluminum casting. As manufacturers strive to reduce their environmental impact, there is a growing focus on using recycled aluminum, reducing energy consumption, and minimizing waste. This trend is driven by both environmental concerns and economic factors.
Finally, advancements in casting technology are opening up new possibilities for aluminum casting. Innovations in mold materials, casting methods, and alloy compositions are improving the efficiency and versatility of aluminum casting, making it possible to produce even more complex and high-performance parts.
Trend | Description | Potential Impact |
---|---|---|
Automation & AI | Integration of automated processes and artificial intelligence | Improved consistency, reduced errors, faster production |
Sustainability | Focus on using recycled aluminum and reducing environmental impact | Reduced resource consumption, lower carbon emissions |
Advancements in Technology | Innovations in mold materials, casting methods, and alloys | Increased versatility, improved quality, efficiency |
FAQ Section
Q1: What is aluminum casting?
Aluminum casting is the process of pouring molten aluminum into molds to create parts used in various industries, including automotive, aerospace, and electronics.
Q2: How does aluminum casting work?
Molten aluminum is poured into a mold, where it solidifies into a specific shape. The mold is then removed, revealing the finished part.
Q3: What are the types of aluminum casting?
The main types of aluminum casting are sand casting, die casting, permanent mold casting, investment casting, and gravity die casting.
Q4: What are the advantages of using aluminum in casting?
Aluminum offers several advantages, including lightweight, corrosion resistance, thermal conductivity, and design flexibility.
Q5: How can the aluminum casting process be improved?
Improvements can be made by optimizing cooling rates, using high-quality molds and alloys, and incorporating automation to reduce defects and improve consistency.