Die casting tolerance standards are crucial for ensuring high-quality and precise parts in manufacturing. In 2024, these standards are more important than ever. As industries continue to demand precision, understanding these standards can save you time and resources.
In 2024, die casting tolerance standards are essential for maintaining high-quality manufacturing practices. These standards outline the acceptable levels of variation in dimensions, which helps manufacturers produce consistent and reliable parts.
Manufacturers must follow these standards closely to meet industry demands. Read on to explore why die casting tolerance matters and how it affects your production process.
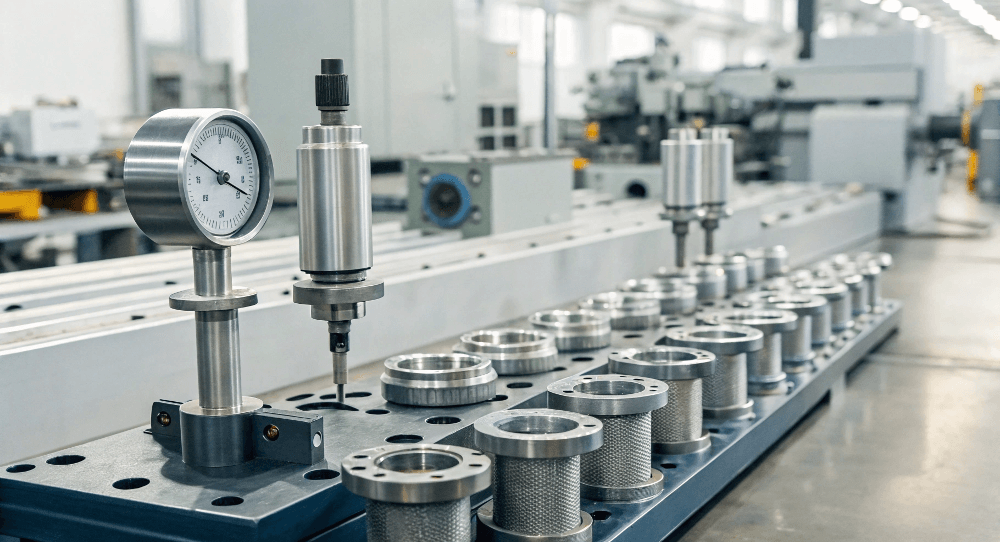
1. What Are Die Casting Tolerance Standards in 2024?
Die casting tolerance standards define the permissible variations in the dimensions and other physical properties of die-cast parts. These standards are crucial for ensuring that parts meet specific functional and aesthetic requirements. Without them, parts may not fit properly, which could lead to defects, increased costs, and production delays.
The die casting tolerance standards for 2024 have evolved to address the increasing demand for precision in manufacturing. These standards ensure that parts can be reliably produced within narrow tolerances, meeting the rigorous specifications of industries like automotive, aerospace, and electronics.
As we move further into 2024, the importance of these standards has increased, especially in industries where precision is critical. Let’s dive deeper into what makes up these standards and why they matter.
2. Why Are Die Casting Tolerance Standards Important?
Die casting tolerance standards are not just about meeting regulatory requirements; they also affect the overall quality of the product. Adhering to these standards ensures that parts fit together correctly, function as intended, and perform reliably over time. Without proper tolerance management, manufacturers risk producing parts that are too large, too small, or that fail to meet critical specifications.
In 2024, the pressure to meet higher precision levels has never been greater. With industries demanding more accurate parts, die casting tolerance standards help ensure quality, consistency, and the smooth functioning of complex assemblies.
What Are the Key Benefits of Die Casting Tolerance Standards?
Benefit | Explanation |
---|---|
Improved product quality | Reduces defects and rework |
Cost savings | Minimizes waste and scrap materials |
Enhanced customer satisfaction | Ensures products meet functional and aesthetic requirements |
Faster time-to-market | Streamlined production processes and fewer delays |
By ensuring accurate tolerances, manufacturers can improve their production efficiency, reduce costs, and enhance the final product’s quality. These benefits are critical in competitive industries that demand high standards.
3. What Are the Key Components of Die Casting Tolerance?
When discussing die casting tolerance, it’s essential to understand the key components that make up the standards. Tolerance in die casting includes several aspects, such as dimensional tolerance, geometric tolerance, and material tolerance. These factors work together to ensure that the die-cast part meets the required specifications.
In 2024, the key components of die casting tolerance are more advanced, helping manufacturers achieve the highest possible precision. These components address everything from the size and shape of parts to the finish and material properties.
Types of Tolerances in Die Casting
- Dimensional Tolerances: These relate to the size and shape of the part, ensuring it matches the design specifications.
- Geometric Tolerances: These ensure the correct form, orientation, and location of features on the part.
- Material Tolerances: These include factors like material composition, surface finish, and density.
Type of Tolerance | Definition |
---|---|
Dimensional Tolerance | Variations in size and shape |
Geometric Tolerance | Variations in form, orientation, and location |
Material Tolerance | Variations in material properties, such as density and surface finish |
By understanding these components, manufacturers can better control the casting process, ensuring parts meet the required standards.
4. How Do Die Casting Tolerance Standards Vary by Industry?
Different industries have unique requirements when it comes to die casting tolerance standards. For instance, the automotive industry typically requires tighter tolerances for safety-critical components, while the consumer goods sector may allow for looser tolerances.
In 2024, industry-specific standards for die casting tolerance are becoming more refined to cater to the increasing need for precision. Automotive, aerospace, and electronics industries all require very specific tolerances to ensure the reliability of their components.
Tolerance Standards in Key Industries
Industry | Typical Tolerance Range |
---|---|
Automotive | ±0.5mm to ±2.0mm |
Aerospace | ±0.2mm to ±1.0mm |
Consumer Goods | ±1.0mm to ±3.0mm |
These variations depend on the function and criticality of the part. For example, automotive components must meet stringent safety standards, while consumer goods may not need as high a level of precision.
5. What Are the Tolerance Levels for Die Casting in 2024?
Die casting tolerance standards for 2024 are set at different levels, depending on the application and the complexity of the part. These levels have become stricter, with manufacturers pushing for higher precision to meet the growing demands of industries.
The tolerance levels for die casting in 2024 reflect the increasing complexity of parts and the precision required for modern manufacturing. These standards aim to ensure that parts are produced with minimal variation, even in highly detailed and intricate designs.
Tolerance Level | Tolerance Range |
---|---|
General Tolerance | ±0.5mm to ±1.5mm |
High Precision | ±0.1mm to ±0.5mm |
Ultra Precision | ±0.01mm to ±0.1mm |
By adhering to these stringent tolerance levels, manufacturers can produce high-quality parts that meet the expectations of even the most demanding customers.
6. How Can Manufacturers Achieve Precise Tolerances?
Achieving precise tolerances in die casting requires a combination of advanced technology, skilled workers, and strict quality control measures. Manufacturers use specialized machinery and casting techniques to minimize dimensional variations and improve the overall quality of the parts. By focusing on critical aspects like material selection, die maintenance, and optimal casting parameters, manufacturers can meet the required standards more consistently.
In 2024, manufacturers are using a range of advanced technologies to enhance precision in the die casting process. These include automated die casting machines, high-precision molds, and innovative cooling systems to control the temperature during the casting process.
Key Factors for Achieving Precise Tolerances
Factor | Description |
---|---|
Advanced Die Casting Machines | High-tech machines ensure tight tolerances and improved consistency. |
Skilled Workforce | Proper training and experience are essential for minimizing errors. |
Die Maintenance | Regular tool maintenance ensures consistent performance and reduces defects. |
Material Selection | Choosing the right material helps control shrinkage and ensures dimensional stability. |
Optimal Casting Parameters | Controlling temperature, pressure, and cooling rates during casting reduces variation. |
By implementing these factors, manufacturers can reduce dimensional discrepancies and improve the overall quality and consistency of die-cast parts.
7. What Challenges Do Manufacturers Face with Die Casting Tolerance?
Manufacturers face several challenges when trying to meet strict die casting tolerance standards. These challenges include variability in material properties, complexity in part design, and the effects of tool wear. Even slight imperfections in the die casting process can result in significant deviations from the desired tolerances, leading to rework, additional costs, and delays.
In 2024, the challenges are becoming more complex as manufacturers push the boundaries of precision. Factors like material variability, tool wear, and intricate designs can all impact the ability to maintain tight tolerances.
Common Challenges in Die Casting Tolerance
Challenge | Explanation |
---|---|
Material Variability | Different batches of materials can have varying properties, affecting the final part dimensions. |
Tool Wear | The wear and tear on dies and molds can cause deviations in part size and shape. |
Complexity of Part Design | More intricate parts require more precise tolerances, making the casting process harder to control. |
Temperature Fluctuations | Inconsistent temperatures during the casting process can lead to material shrinkage or expansion. |
Addressing these challenges requires a combination of advanced technology, expert handling, and continuous monitoring of the casting process to maintain consistent quality.
8. How Do Tolerance Variations Affect Product Performance?
Tolerance variations can significantly impact the fit, form, and function of die-cast parts. Even small deviations from the intended dimensions can cause parts to misalign, affecting the performance of the final product. For example, in the automotive industry, slight tolerance variations can result in parts that don’t fit together correctly, leading to operational failures or safety risks.
In 2024, the increasing demand for high-performance products has made tolerance variations more critical than ever. Manufacturers must ensure that every part meets the exact specifications to avoid performance issues.
Impact of Tolerance Variations on Performance
Performance Issue | Description |
---|---|
Fit and Function Issues | Parts that don’t fit properly can lead to misalignments and mechanical failures. |
Reduced Durability | Tolerances outside the specified range can result in weaker parts, leading to premature failure. |
Assembly Problems | Incorrect dimensions can cause issues during assembly, requiring rework and additional time. |
Increased Wear and Tear | Parts that don’t meet exact tolerances wear out faster, reducing their lifespan and functionality. |
Maintaining strict tolerance standards is crucial to ensuring that parts perform as expected over time and meet customer requirements.
9. What Role Does Quality Control Play in Die Casting Tolerance?
Quality control is integral to ensuring that die-cast parts meet the required tolerance standards. By using advanced inspection methods, such as Coordinate Measuring Machines (CMM) or laser scanning, manufacturers can quickly detect any deviations from the specified tolerances. Consistent and effective quality control processes help identify problems early in the production process, reducing the risk of defects and improving overall efficiency.
In 2024, quality control technologies are more advanced than ever, providing manufacturers with real-time data on part dimensions. These technologies enable quicker decision-making, reducing rework and ensuring that parts are within acceptable tolerance ranges.
Quality Control Methods in Die Casting
Method | Description |
---|---|
Coordinate Measuring Machine (CMM) | Provides precise 3D measurements of parts to check dimensional accuracy. |
Laser Scanning | Uses laser beams to measure part dimensions and detect surface variations. |
Visual Inspection | Manual inspection to detect visible defects and discrepancies. |
X-Ray or Ultrasonic Testing | Used for internal defects that are not visible on the surface. |
Quality control plays a critical role in maintaining consistent quality, reducing defects, and improving customer satisfaction.
10. What Are the Most Common Mistakes in Managing Tolerances?
Despite the importance of die casting tolerance standards, many manufacturers still make common mistakes that compromise part quality. Some of these mistakes include over-tightening tolerances, underestimating the effects of tool wear, and failing to maintain clear communication between design and manufacturing teams. These errors can lead to defects, delays, and increased production costs.
In 2024, manufacturers need to pay closer attention to tolerance management to prevent these common mistakes. Addressing these issues early in the process can save time, money, and resources.
Common Mistakes in Tolerance Management
Mistake | Explanation |
---|---|
Over-tightening Tolerances | Setting unnecessarily tight tolerances increases production costs without improving quality. |
Underestimating Tool Wear | Failing to account for tool wear can lead to dimensional variations and defects. |
Lack of Communication | Poor communication between design and manufacturing teams can result in parts that don’t meet specifications. |
Not Adjusting for Material Variability | Ignoring material properties can cause inconsistencies in the final product. |
Avoiding these common mistakes requires careful planning, clear communication, and attention to detail throughout the manufacturing process.
11. How Are Tolerances Measured in Die Casting?
Measuring tolerances accurately is essential in die casting to ensure that parts meet design specifications. Various tools and techniques are used to measure the dimensions and properties of cast parts, including Coordinate Measuring Machines (CMM), optical scanners, and calipers. These measurements ensure that the tolerances are within acceptable limits and that parts will function as intended.
In 2024, the use of advanced measurement tools and technologies has made it easier to measure die casting tolerances with higher precision. Manufacturers now have access to real-time data and measurement systems that improve the accuracy and speed of the inspection process.
Key Measurement Tools for Die Casting Tolerances
Measurement Tool | Description |
---|---|
Coordinate Measuring Machine (CMM) | A 3D measurement tool that scans the part to measure its dimensions accurately. |
Laser Scanning | A non-contact method that uses laser beams to measure part dimensions and detect surface defects. |
Calipers and Micrometers | Traditional tools used for measuring external and internal dimensions, ensuring tight tolerances. |
Optical Scanners | Used for measuring surface features and detecting any variations in the part’s shape or surface finish. |
By using these tools, manufacturers can ensure that each die-cast part is within the required tolerance range, improving product quality and reducing defects.
12. How Can Tolerances Be Improved in Die Casting Processes?
Improving die casting tolerance requires optimizing various aspects of the casting process. Factors like die design, material selection, machine settings, and cooling processes can all impact the precision of the final product. By refining these areas, manufacturers can produce parts with tighter tolerances and fewer defects.
In 2024, advancements in die casting technologies and process optimization techniques allow manufacturers to achieve better tolerances with higher consistency. This has resulted in fewer defects, reduced rework, and improved product quality.
Strategies for Improving Die Casting Tolerances
Strategy | Description |
---|---|
Optimizing Die Design | Designing dies with features that control metal flow and reduce material stress, improving part precision. |
Controlling Cooling Rates | Proper cooling reduces shrinkage and distortion, which helps maintain dimensional stability. |
Using Advanced Materials | Selecting materials with consistent properties can minimize variations and improve tolerance accuracy. |
Machine Settings Adjustments | Fine-tuning machine parameters such as pressure, temperature, and injection speed can lead to better consistency in part dimensions. |
These strategies help manufacturers create more accurate and reliable die-cast parts that meet stringent tolerance standards.
13. What Are the Economic Impacts of Tolerance Variations?
Tolerance variations can have significant economic impacts, both in terms of increased production costs and potential customer dissatisfaction. When tolerances are not met, manufacturers may need to rework parts, scrap defective products, or delay shipments. These factors can lead to higher costs and longer production times.
In 2024, the pressure to meet tight deadlines and lower costs means that tolerance variations must be minimized to ensure profitability and customer satisfaction. By reducing tolerance errors, manufacturers can lower costs and improve their competitive edge.
Economic Consequences of Tolerance Variations
Economic Impact | Description |
---|---|
Increased Production Costs | Rework, material waste, and delays increase manufacturing costs. |
Reduced Profit Margins | Lower-quality parts lead to higher scrap rates and decreased profits. |
Customer Dissatisfaction | Parts that do not meet tolerances may result in returns, lost business, and damage to brand reputation. |
Extended Lead Times | Tightening tolerances requires additional time for measurements, adjustments, and inspections. |
Minimizing tolerance variations helps manufacturers reduce waste, avoid rework, and meet customer deadlines, ultimately improving profitability.
14. What Innovations Are Shaping Die Casting Tolerances in 2024?
In 2024, several innovations are helping manufacturers improve die casting tolerance standards. These innovations range from advanced simulation software to the introduction of AI-powered machines that can adjust processes in real time. These technologies allow manufacturers to predict potential defects, optimize casting parameters, and increase production efficiency.
As technology continues to evolve, die casting tolerance standards are becoming more precise and easier to control. Innovations like automated quality control systems, 3D printing, and advanced die design software are revolutionizing the way manufacturers approach tolerance management.
Innovations in Die Casting Tolerance Technology
Innovation | Description |
---|---|
AI-Powered Machines | Machines equipped with AI that can automatically adjust casting parameters to meet tight tolerances. |
Advanced Simulation Software | Software that predicts potential defects in the die casting process, allowing manufacturers to adjust parameters before production. |
3D Printing of Molds | The ability to print molds for die casting with precise tolerances, reducing errors and improving efficiency. |
Automated Quality Control | Systems that use real-time data to monitor part dimensions and make adjustments, ensuring parts meet tolerance standards. |
These innovations are pushing the boundaries of die casting tolerance, enabling manufacturers to achieve higher precision and reduce costs.
15. How Can Companies Stay Updated on Die Casting Tolerance Standards?
Die casting tolerance standards are constantly evolving, and manufacturers must stay updated to remain competitive. Companies can stay informed about the latest standards by attending industry conferences, participating in online forums, and subscribing to publications that focus on manufacturing processes. Additionally, industry organizations and standards-setting bodies regularly publish updates on tolerance standards that manufacturers should follow.
In 2024, staying updated on the latest tolerance standards is crucial for maintaining high-quality production and meeting the increasing demands for precision. Companies that keep up with industry changes are better equipped to deliver consistent, reliable parts.
Ways to Stay Updated on Tolerance Standards
Method | Description |
---|---|
Industry Conferences | Conferences are an excellent way to network and learn about the latest developments in die casting. |
Online Forums and Communities | Participate in online discussions to learn about new practices and tools in the die casting industry. |
Subscriptions to Industry Publications | Read industry journals and newsletters for the latest standards and research. |
Membership in Standards Organizations | Join groups that focus on developing and updating die casting standards. |
By staying connected with industry developments, manufacturers can ensure that they are always operating according to the most current and relevant tolerance standards.
Conclusion
Understanding die casting tolerance standards is crucial for any manufacturer looking to maintain high-quality production and stay competitive. The standards for 2024 ensure precision, reduce waste, and improve overall product performance. By adhering to these standards, manufacturers can meet industry demands, avoid costly errors, and deliver parts that meet customer expectations.
To stay ahead, it’s important for companies to continuously update their processes to align with evolving tolerance standards. Embracing these changes will help ensure success in an increasingly precision-driven world.
FAQ Section
- Q1: What are die casting tolerance standards?
Die casting tolerance standards define the permissible variations in the dimensions and properties of die-cast parts to ensure they meet specific functional and quality requirements. - Q2: How do die casting tolerance standards impact product quality?
These standards help ensure that parts fit together correctly, function as intended, and perform reliably over time, leading to higher product quality and fewer defects. - Q3: How do manufacturers achieve precise tolerances in die casting?
Manufacturers use advanced machines, precise tooling, material selection, and skilled labor to ensure that die casting tolerances are met during production. - Q4: Why are die casting tolerance standards different for various industries?
Different industries, such as automotive, aerospace, and consumer goods, require varying levels of precision for their components based on functionality and safety requirements. - Q5: How do tolerance variations affect the cost of production?
Tolerance variations can lead to rework, material waste, and defects, which increase production costs. Stricter tolerances often require more advanced machinery and skilled labor, raising production costs.