Investment casting is a widely used process for creating metal parts with high precision. Whether you’re in the aerospace, medical, or automotive industry, selecting the right material is crucial for achieving the required quality and performance in your castings.
Choosing the correct material for investment casting can significantly affect the durability, strength, and surface finish of the final product. In this article, we will explore the different types of materials used in investment casting and their benefits.
Choosing the right material can be challenging, but understanding how different materials affect the process and the final product can make the decision easier.
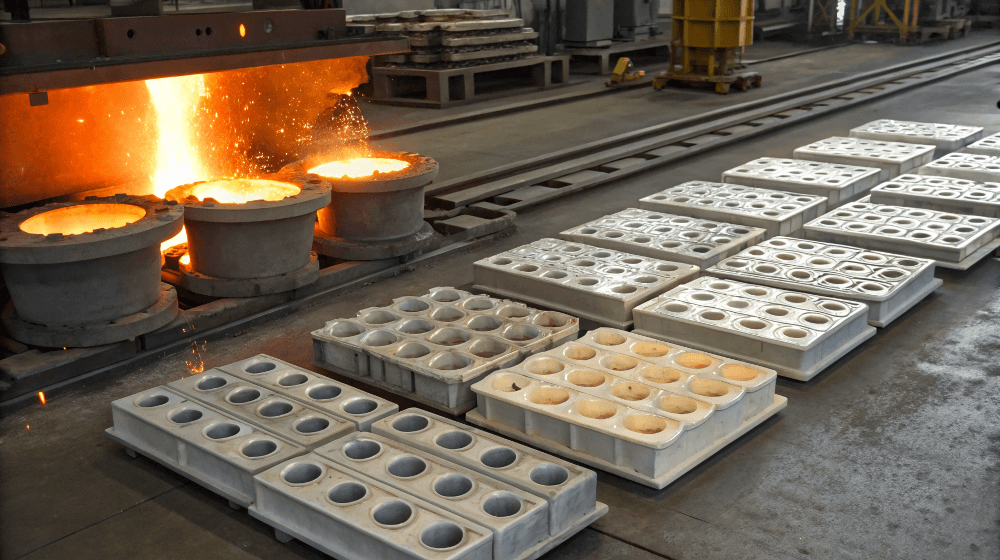
1. What are Investment Casting Materials?
Investment casting materials are those used to create both the molds and the final casting products. These materials are selected based on the intended use of the casting, the material properties needed, and the specific manufacturing process.
Investment casting materials can include metals, ceramics, and composites. These materials have unique properties that help achieve the desired characteristics in the final product.
Materials used in investment casting are critical as they affect the overall performance of the part being cast. The type of metal chosen, for example, plays a significant role in the mechanical properties of the cast product, such as strength and resistance to heat and corrosion.
1.1. Metals in Investment Casting
Metals such as stainless steel, aluminum, and titanium are commonly used in investment casting. Each metal has its own benefits, like resistance to high temperatures, corrosion, and strength.
1.2. Ceramics and Binders
Ceramics are used to make molds for investment casting. The mold material must be able to withstand the molten metal without breaking or deteriorating. A variety of binder materials are mixed with ceramics to improve mold strength and ease of removal.
1.3. Composite Materials
In some specialized applications, composite materials are used to offer both the heat resistance of ceramics and the strength of metals. Composites can be used for complex castings with specific performance needs.
Material Type | Examples | Benefits |
---|---|---|
Metals | Stainless Steel, Titanium | High strength, heat resistance, corrosion resistance |
Ceramics | Silica, Zircon | Molds withstand high temperatures |
Composites | Ceramic-Metal Composites | Enhanced durability and performance for specific applications |
2. Why is Material Selection Critical in Investment Casting?
Selecting the right material for investment casting is essential for ensuring the final product meets the required specifications, performance standards, and cost considerations.
Material selection impacts the strength, surface finish, and durability of the casting. Choosing the right material ensures that the casting will perform well under the conditions it will face during its life cycle.
Material selection influences several factors in the casting process, including its resistance to wear, thermal conductivity, and ability to handle specific stress loads. Materials with better performance characteristics may cost more initially but result in longer-lasting, more efficient products.
2.1. How Material Affects Strength and Durability
Material strength is essential for the product to withstand mechanical stress. The correct alloy or metal can greatly impact the load-bearing capacity and durability of the final product.
2.2. How Material Affects Surface Finish
The quality of the surface finish is crucial, especially for components used in industries like aerospace, where precision is key. The material selected directly influences the smoothness and precision of the final product.
2.3. Economic Considerations in Material Selection
Materials with better properties may come at a higher cost. Evaluating material costs against the final product’s requirements ensures the casting is both high-performing and cost-effective.
Material Type | Strength | Surface Finish | Cost |
---|---|---|---|
Stainless Steel | High | Smooth | Medium |
Aluminum | Medium | Rough | Low |
Titanium | Very High | Very Smooth | High |
3. What are the Different Types of Investment Casting Materials?
Investment casting uses a wide range of materials, including metals, ceramics, and other specialized compounds. Understanding the types of materials used helps in selecting the right one for specific applications.
Metals, ceramics, and composites are the most commonly used materials. Each material has unique properties that cater to different casting needs.
3.1. Metals in Investment Casting
Metals such as stainless steel, titanium, and aluminum are popular choices due to their mechanical properties. Stainless steel, for instance, is commonly used in automotive and medical applications because of its corrosion resistance and strength.
3.2. Ceramics Used in Investment Casting
Ceramics provide the high-temperature stability required to form molds that hold molten metal. They are also important in ensuring that the final product maintains the necessary detail and finish.
3.3. Specialized Alloys and Composites
Certain industries, such as aerospace, require materials that can withstand extreme conditions. For these applications, high-performance alloys and composites are used in investment casting to provide superior strength and durability.
Material Type | Examples | Key Uses |
---|---|---|
Ferrous Metals | Stainless Steel | Medical, Automotive, Industrial |
Non-Ferrous Metals | Aluminum, Brass | Aerospace, Defense, Consumer Goods |
Ceramics | Silica, Zircon | Mold making, Precision casting |
4. How Does the Metal Type Influence Investment Casting?
The metal used in investment casting determines many of the final casting’s properties, including its strength, durability, and heat resistance.
Metal types vary greatly in terms of their ability to withstand high temperatures, their resistance to corrosion, and their strength under stress.
Different metals are chosen for specific casting applications based on their unique characteristics. For example, titanium is selected for its excellent strength-to-weight ratio and ability to resist corrosion in extreme conditions.
4.1. Types of Ferrous Alloys in Investment Casting
Ferrous alloys, primarily made from iron, are used in investment casting due to their high strength and ability to withstand extreme conditions.
4.2. Non-Ferrous Metals in Investment Casting
Non-ferrous metals, such as aluminum and bronze, are used when casting requires lightweight materials with corrosion resistance.
4.3. Specialty Metals in High-Performance Applications
In applications like aerospace or military industries, specialized metals such as cobalt or nickel alloys are used to meet high-performance standards.
Metal Type | Key Characteristics | Applications |
---|---|---|
Ferrous Alloys | Strong, Heat-resistant | Automotive, Industrial, Medical |
Non-Ferrous Metals | Lightweight, Corrosion-resistant | Aerospace, Consumer Goods |
Specialty Metals | High performance, durable | Aerospace, Military, High-precision |
5. What Are the Key Properties of Materials Used in Investment Casting?
The key properties of materials used in investment casting directly affect the strength, durability, and overall performance of the final product. Each material must be carefully selected based on the application requirements.
The right material will enhance the casting’s ability to perform under stress, resist wear, and maintain its integrity in challenging environments.
Choosing a material with the correct mechanical properties is crucial, as it influences how the final product will react to external forces such as pressure, temperature, and corrosion.
5.1. Strength and Durability
Strength is a critical factor in ensuring the longevity and performance of the casting, especially in industries that demand high endurance, such as aerospace and automotive. Durability ensures the material can withstand long-term use without degradation.
5.2. Resistance to Heat and Corrosion
For many industries, resistance to heat and corrosion is vital. Materials used in investment casting must be capable of withstanding harsh environments, whether it’s extreme temperatures or exposure to chemicals and moisture.
5.3. Surface Finish and Precision
The surface finish of the casting is essential, especially in industries like medical or aerospace, where high precision is required. The material used should be compatible with surface treatment processes to achieve the desired finish.
Property | Impact on Performance | Material Examples |
---|---|---|
Strength | Provides load-bearing capacity | Stainless Steel, Titanium |
Heat Resistance | Ensures material stability under extreme conditions | Nickel Alloys, Cobalt |
Corrosion Resistance | Protects against environmental factors | Aluminum, Stainless Steel |
Surface Finish | Influences final product appearance | Titanium, Stainless Steel |
6. How Are Ceramic Materials Used in Investment Casting?
Ceramic materials play an essential role in creating molds that hold molten metal during the investment casting process. The material must withstand the high temperatures of the molten metal and maintain its shape under stress.
Ceramics are used to form the mold that shapes the metal, and the choice of ceramic material significantly impacts the mold’s ability to withstand thermal shock and produce precise castings.
Investment casting molds made from ceramics are highly detailed, allowing manufacturers to create complex parts with intricate designs and tight tolerances. Ceramics are also used for core-making, where hollow or internal structures are needed in the final product.
6.1. Role of Ceramics in Mold Making
Ceramics serve as the mold material in the investment casting process. The mold is created by coating a pattern (often made from wax) with a ceramic slurry, which hardens to form the outer shell.
6.2. Types of Ceramics Used in Investment Casting
Common ceramic materials include silica, zircon, and alumina. The selection of ceramic material depends on factors such as temperature resistance, mold strength, and compatibility with the metal being cast.
6.3. Advantages and Limitations of Ceramic Molds
Ceramic molds offer several advantages, including high precision and the ability to withstand high temperatures. However, they are fragile and can be costly and time-consuming to produce.
Ceramic Material | Key Characteristics | Applications |
---|---|---|
Silica | High temperature resistance | Aerospace, Industrial |
Zircon | Excellent mold strength | Medical, Defense |
Alumina | Strong at high temperatures | Aerospace, High-performance parts |
7. What Are the Benefits of Using Ferrous Alloys in Investment Casting?
Ferrous alloys, primarily made from iron, are commonly used in investment casting due to their excellent strength and ability to withstand extreme conditions. These alloys are critical in applications requiring durable and tough castings.
Ferrous alloys are highly favored for their strength, cost-effectiveness, and suitability for casting large, heavy parts used in automotive and industrial machinery.
Ferrous alloys are used in a wide range of investment casting applications due to their versatility. Common ferrous alloys include carbon steel, stainless steel, and cast iron. Each alloy type has specific benefits, such as corrosion resistance or high-temperature stability.
7.1. Types of Ferrous Alloys in Investment Casting
Stainless steel is one of the most commonly used ferrous alloys in investment casting. Its resistance to corrosion and high strength make it an ideal choice for industries like aerospace and medical.
7.2. Benefits of Ferrous Alloys
Ferrous alloys offer strength and toughness that is unmatched in many applications. They are also relatively cost-effective and readily available, making them an ideal choice for mass production.
7.3. Cost Considerations
Although ferrous alloys are often less expensive than some non-ferrous materials, they may require more advanced techniques for mold making and finishing, increasing the overall production cost.
Ferrous Alloy | Characteristics | Benefits |
---|---|---|
Stainless Steel | Corrosion-resistant, durable | High strength, resistant to heat |
Carbon Steel | Strong, affordable | Versatile, easy to work with |
Cast Iron | Good casting properties | Durable, cost-effective |
8. What Are the Advantages of Non-Ferrous Metals in Investment Casting?
Non-ferrous metals, which are metals that do not contain iron, have unique properties that make them ideal for specific applications in investment casting.
Non-ferrous metals are prized for their lightweight properties, excellent corrosion resistance, and ability to form complex shapes.
Aluminum, brass, and copper are some of the most commonly used non-ferrous metals in investment casting. These materials are chosen based on their suitability for lightweight castings that must also endure corrosion and heat.
8.1. Common Non-Ferrous Metals Used in Investment Casting
Aluminum is one of the most popular non-ferrous metals used in investment casting due to its light weight, ease of casting, and good corrosion resistance.
8.2. Benefits of Non-Ferrous Metals
Non-ferrous metals are ideal for applications where weight reduction is crucial, such as in the aerospace industry. They also offer superior corrosion resistance, making them perfect for marine and automotive applications.
8.3. Applications of Non-Ferrous Metals
Non-ferrous metals are commonly used in casting products that need to be lightweight but strong, such as engine components, electrical parts, and decorative items.
Non-Ferrous Metal | Characteristics | Applications |
---|---|---|
Aluminum | Lightweight, corrosion-resistant | Aerospace, Automotive, Electronics |
Brass | Malleable, durable | Marine, Automotive, Engineering |
Copper | Excellent heat conductivity | Electrical components, Heat exchangers |
9. What is the Role of Special Alloys in Investment Casting?
Specialty alloys, such as those used in the aerospace and medical industries, offer superior performance characteristics. These alloys are specially designed to perform in extreme environments, where typical metals may fail.
Specialty alloys provide high performance in terms of heat resistance, strength, and longevity, making them ideal for high-stress applications.
Alloys such as cobalt, nickel, and titanium are used in investment casting for industries where performance and precision are paramount. These materials are designed to meet the demanding requirements of sectors like aerospace, military, and medical devices.
9.1. High-Performance Alloys Used in Investment Casting
Nickel and cobalt-based alloys are often used for their excellent high-temperature properties and resistance to wear and corrosion. These alloys are ideal for aerospace and defense applications.
9.2. Trade-Off Between Cost and Performance
Specialty alloys often come at a higher cost due to their advanced material properties. However, the performance benefits they provide make them essential for critical applications.
9.3. Applications of Specialty Alloys
These alloys are used in high-performance engines, turbine blades, and other parts that are exposed to extreme temperatures and pressure.
Special Alloy | Characteristics | Applications |
---|---|---|
Nickel Alloys | High-temperature resistance, strong | Aerospace, Turbine blades |
Cobalt Alloys | High wear resistance, tough | Medical devices, Aerospace |
Titanium Alloys | Strong, lightweight, corrosion-resistant | Aerospace, Military, Medical |
10. How Do Material Properties Affect Surface Finish?
Material properties significantly impact the surface finish of investment castings. Achieving the desired surface quality is essential for parts used in industries where aesthetics and functionality are critical, such as medical, aerospace, and automotive.
Material properties such as smoothness, texture, and porosity determine how well the final product will meet the desired finish. Selecting the right material can help avoid defects like rough surfaces and improve the overall casting quality.
The material selected for the casting affects how the molten metal flows into the mold, how it solidifies, and how easily the mold can be removed. All of these factors contribute to the final surface texture.
10.1. The Importance of Smoothness
The smoother the surface of the material, the less post-processing is required. Materials with fine grains and good flow characteristics allow for a smoother final product with fewer defects.
10.2. Texture and Porosity
The texture of the surface, whether rough or smooth, depends on the material’s characteristics and the mold’s quality. Materials with higher porosity might result in surface defects that require additional finishing.
10.3. Final Surface Quality
A well-chosen material ensures the casting requires minimal finishing, saving both time and costs. In critical applications, high-quality surface finish is a must.
Material Type | Surface Smoothness | Post-Processing Requirements |
---|---|---|
Stainless Steel | Very Smooth | Minimal |
Aluminum | Smooth | Moderate |
Titanium | Very Smooth | Minimal |
Cast Iron | Rough | Extensive |
11. What Are the Challenges with Material Selection in Investment Casting?
Material selection in investment casting comes with its own set of challenges. Understanding and overcoming these challenges is key to ensuring the final product meets all design and performance requirements.
Challenges include material shrinkage, porosity, mold compatibility, and cost concerns. Overcoming these challenges requires careful material selection and process optimization.
These challenges are further compounded when working with advanced materials or specialized alloys. Every step in the process, from mold preparation to casting solidification, must be carefully controlled to minimize defects.
11.1. Material Shrinkage
As molten metal cools and solidifies, it shrinks. This shrinkage can lead to dimensional inaccuracies. Material selection can help minimize these issues, but it requires precise calculations.
11.2. Porosity Issues
Porosity, or the presence of air pockets within the casting, is a common challenge in investment casting. Porosity can weaken the structure of the part and is more likely to occur with certain materials.
11.3. Mold Compatibility
The material chosen for casting must be compatible with the mold material to avoid reactions that can compromise the mold’s integrity and the final casting.
Challenge | Cause | Solution |
---|---|---|
Shrinkage | Cooling and solidification | Use of alloys with lower shrinkage rates |
Porosity | Air pockets in the mold | Optimizing the pouring technique |
Mold Compatibility | Reaction between mold and metal | Using compatible materials for mold and casting |
12. How Do Materials Affect the Casting Process?
Materials selected for investment casting play a pivotal role in how the casting process proceeds. They affect the mold creation, pouring, cooling, and solidification of the molten metal.
Material selection influences key aspects of the casting process, including how the material flows into molds, its cooling time, and its ability to withstand the thermal shock of the casting environment.
Selecting a material with the right thermal properties and flow characteristics ensures a smoother casting process and helps avoid defects like cracking or improper filling of the mold.
12.1. Mold Creation and Material Flow
The flow of molten metal into the mold is a critical part of the process. Materials that have better fluidity and lower viscosity help fill the mold more completely, reducing the chance of voids.
12.2. Cooling and Solidification Rates
Different materials cool at different rates, which affects the solidification process and can lead to shrinkage or warping. Materials with faster cooling rates tend to result in denser, stronger castings.
12.3. Material Thermal Properties
Thermal conductivity is a crucial property that affects how quickly a material can handle temperature changes during the casting process.
Material Type | Cooling Rate | Mold Compatibility | Thermal Conductivity |
---|---|---|---|
Stainless Steel | Moderate | Good | Low |
Aluminum | Fast | Moderate | High |
Titanium | Slow | Excellent | Low |
Cast Iron | Moderate | Good | Moderate |
13. How Do Environmental Factors Impact Material Selection?
Environmental factors such as temperature, humidity, and exposure to chemicals can have a significant impact on the performance of investment castings. Materials must be selected to withstand the specific conditions the product will face in its end use.
Materials must be able to endure the environmental conditions they will be exposed to without losing their integrity or performance.
When casting components that will be used in harsh environments, such as marine or chemical processing industries, the material chosen must be resistant to corrosion, extreme temperatures, and pressure.
13.1. Impact of Temperature on Materials
High-temperature applications require materials that can withstand heat without deforming. Metals like titanium and nickel are often used in these environments because of their excellent heat resistance.
13.2. Resistance to Humidity and Corrosion
Corrosive environments, such as marine or chemical processing settings, require materials that are resistant to rust and degradation. Stainless steel is commonly chosen for its high resistance to corrosion.
13.3. Material Performance in Extreme Conditions
For extreme conditions, such as aerospace or high-performance automotive parts, specialized alloys and composites are used to meet the extreme physical and chemical demands.
Environmental Factor | Material Impact | Recommended Materials |
---|---|---|
Temperature | Affects material stability | Titanium, Nickel Alloys |
Humidity & Corrosion | Causes degradation | Stainless Steel, Aluminum |
Chemical Exposure | Material degradation | Stainless Steel, Coated Alloys |
14. What Are the Economic Considerations in Choosing Casting Materials?
Material selection is not only influenced by performance requirements but also by the cost of the materials and the casting process. Balancing cost with performance is a key consideration when choosing materials for investment casting.
Economic factors include the initial cost of materials, the availability of raw materials, and the overall cost of the casting process.
Some materials, like high-performance alloys, come with a higher price tag, while others, like aluminum, are less expensive but may not offer the same level of durability or strength.
14.1. Cost vs. Performance Trade-Offs
The trade-off between cost and performance is a common challenge in material selection. High-performance materials often come with a higher initial cost but can provide long-term savings by enhancing product durability and reducing maintenance.
14.2. Availability and Sourcing of Materials
The availability of certain materials can influence their cost. Materials that are rare or require specialized processing are typically more expensive and harder to source.
14.3. Lifecycle Costs
In addition to initial material costs, lifecycle costs must be considered, including the longevity of the product and the potential for replacements or repairs.
Material Type | Initial Cost | Lifecycle Cost | Performance |
---|---|---|---|
Stainless Steel | Medium | High | Excellent |
Aluminum | Low | Medium | Good |
Titanium | High | Very High | Superior |
Cast Iron | Low | Low | Moderate |
15. How Can New Materials Impact the Future of Investment Casting?
New materials and advancements in material science have the potential to transform the investment casting process. Innovations can lead to stronger, lighter, and more cost-effective castings.
The development of new materials will allow industries to create more complex parts, with better performance and reduced environmental impact.
Researchers are continually developing new alloys and composites that offer improved strength, heat resistance, and corrosion protection. These advancements will allow for greater innovation in fields like aerospace, medical, and defense.
15.1. Innovations in Alloy Design
Alloying techniques have advanced, allowing for the creation of materials that are both lightweight and high-strength. For example, titanium alloys have evolved to offer better heat resistance and toughness.
15.2. Advancements in Composite Materials
Composites combine the best features of different materials, offering high performance at lower costs. The development of new composite materials will continue to improve the casting process.
15.3. Environmental Considerations in Material Selection
As industries move toward more sustainable manufacturing practices, the use of eco-friendly materials and processes will become increasingly important. Developing recyclable and renewable materials will play a key role in the future of investment casting.
Innovation | Impact on Casting | Applications |
---|---|---|
Alloy Advancements | Higher strength, heat resistance | Aerospace, Military, Medical |
Composite Materials | Improved performance at lower costs | Automotive, Aerospace, Consumer Goods |
Eco-friendly Materials | Sustainable, recyclable | Automotive, Consumer Products |
Conclusion
Choosing the right materials for investment casting is key to producing high-quality, durable parts that meet the specific needs of industries. With proper understanding of material properties, manufacturers can ensure that the castings perform well under various conditions. The materials used can significantly impact the product’s strength, surface finish, and cost-effectiveness.
FAQ Section
- Q1: What is investment casting?
Investment casting is a metal-forming process where a pattern is made from a wax material, coated with ceramic, and then filled with molten metal to create a casting. - Q2: How does material selection affect investment casting?
Material selection is crucial as it directly influences the mechanical properties, strength, surface finish, and overall performance of the final casting. - Q3: What are the most common materials used in investment casting?
The most common materials include stainless steel, aluminum, and titanium, as well as ceramics for mold-making. - Q4: How do ceramics help in the casting process?
Ceramics are used to create molds that can withstand high temperatures, ensuring the final product retains its precise shape and strength. - Q5: What are the challenges in selecting materials for investment casting?
Challenges include balancing performance with cost, managing material shrinkage, and ensuring the right material properties for specific applications.