356 alloy is a popular aluminum alloy known for its casting properties and excellent performance in various industries. It’s often used in manufacturing products that require high strength, durability, and resistance to wear. In this article, we’ll explore the composition, properties, uses, advantages, and challenges of 356 alloy, alongside comparisons to other alloys in the market. We’ll also look at how 356 alloy benefits industries like automotive, aerospace, and marine. By the end, you’ll understand why 356 alloy is a go-to choice for manufacturers worldwide.
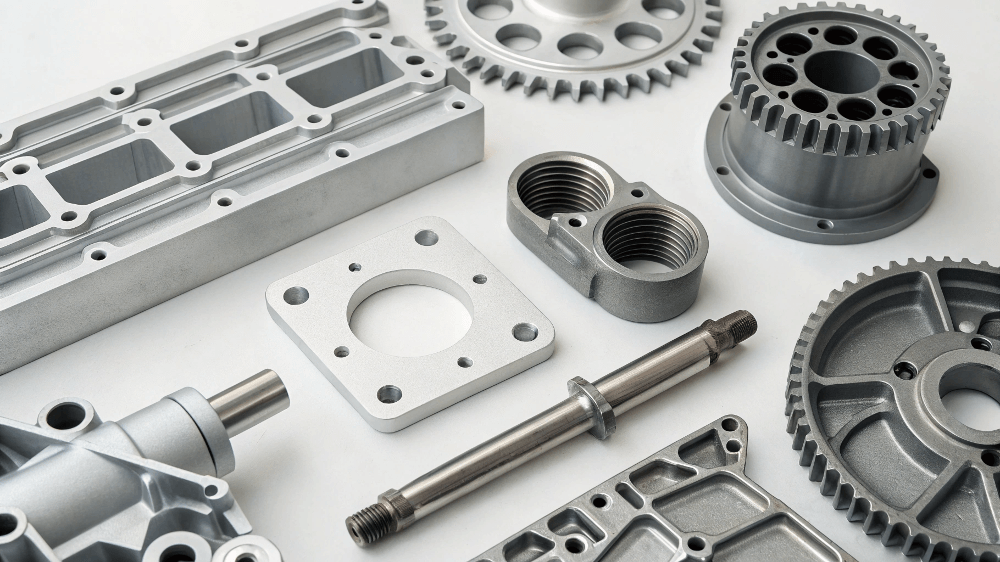
1. Introduction to 356 Alloy
356 alloy is a cast aluminum alloy widely used in manufacturing components that require high strength and excellent fluidity during the casting process. What’s the real story? Well, 356 alloy is favored in industries where complex shapes are required, and it’s often used in applications like automotive engine blocks, aerospace components, and marine parts. It has a great balance of mechanical properties, corrosion resistance, and lightweight characteristics, making it a preferred material for a range of products.
One of the standout features of 356 alloy is its impressive ability to withstand wear and tear, especially when used in high-stress environments. This alloy is composed primarily of aluminum, with key elements like silicon and copper, which enhance its performance. But here’s the kicker—its properties make it not only cost-effective but also a long-lasting solution for manufacturers.
Its main advantages are ease of casting, strength, and resilience. Whether it’s in a harsh automotive environment or an aerospace setting, 356 alloy holds up well under pressure. And the best part? It’s recyclable, contributing to its eco-friendly reputation. Ready for the good part? We’ll dive deeper into the specifics of its properties next, which will show just why it’s such a valuable material.
Property | Value |
---|---|
Composition | Aluminum, Silicon, Copper |
Key Benefits | High Strength, Corrosion Resistance |
Main Applications | Automotive, Aerospace, Marine |
2. Properties of 356 Alloy
When it comes to choosing materials for demanding applications, you might be wondering what makes 356 alloy stand out. The answer lies in its unique blend of physical and mechanical properties that set it apart from other alloys.
First, 356 alloy is known for its excellent fluidity in casting, which means it can easily fill intricate molds, making it ideal for complex parts. This property is essential in industries like automotive and aerospace, where precision is critical. This is where it gets interesting… 356 alloy is also highly resistant to corrosion, especially in harsh environments like marine and industrial settings. This corrosion resistance ensures that parts made from 356 alloy will last longer and require less maintenance compared to other metals.
The alloy’s mechanical properties, such as its tensile strength and hardness, are excellent as well. This makes 356 alloy a top choice for components that need to endure high mechanical loads, like engine parts and structural elements. Not only is it strong, but it is also lightweight, offering great advantages in industries like aerospace, where every ounce of weight counts.
Property | Value |
---|---|
Fluidity | High |
Corrosion Resistance | Excellent |
Tensile Strength | High |
Weight | Lightweight |
3. How 356 Alloy is Made
Now, let’s talk about how 356 alloy is made. What’s the real process behind its creation? The alloy is primarily created through casting, a process where molten metal is poured into molds to create the desired shape. The key ingredients, such as aluminum, silicon, and copper, are combined in a controlled environment to form the alloy. The purity and ratio of these elements significantly affect the final product’s properties.
Casting 356 alloy involves a precise process to ensure the metal maintains its strength, fluidity, and corrosion resistance. But here’s the kicker—356 alloy can be produced using different casting techniques, including sand casting and die casting. These methods are chosen based on the complexity of the part and the production volume. Sand casting is often used for large, complex parts, while die casting is employed for more precise, smaller components.
This alloy’s production process is relatively straightforward, yet it requires close attention to detail at each stage to ensure high-quality results. After casting, the alloy is heat-treated to enhance its mechanical properties. Ready for the good part? The final product is both strong and durable, making it an ideal choice for high-performance applications.
Casting Method | Application | Benefits |
---|---|---|
Sand Casting | Complex Parts | Low cost, flexible |
Die Casting | Small Components | High precision, fast production |
4. Common Uses of 356 Alloy
356 alloy is incredibly versatile, and this is where it gets interesting… It is used in a wide range of industries that require materials with high strength and excellent casting properties. One of the most prominent applications of 356 alloy is in the automotive industry, where it is used in the manufacture of engine blocks, cylinder heads, and other critical parts. These parts must endure extreme temperatures, high pressure, and mechanical stress, making 356 alloy an excellent choice.
In aerospace, 356 alloy is used for structural components and parts that need to be lightweight yet strong. Aircraft components made from 356 alloy contribute to reducing overall weight, which directly impacts fuel efficiency and performance. Similarly, in marine applications, 356 alloy is used for parts exposed to saltwater environments, where its corrosion resistance is vital.
But here’s the kicker—356 alloy is also utilized in consumer goods, particularly in products requiring high durability. For example, high-quality kitchen equipment, such as frying pans and cookware, benefits from the durability and lightweight characteristics of 356 alloy. Its ability to withstand wear and tear makes it a fantastic option for these high-use products.
Industry | Application | Key Benefits |
---|---|---|
Automotive | Engine Blocks, Cylinder Heads | High Strength, Durability |
Aerospace | Aircraft Parts, Structural Components | Lightweight, Strong |
Marine | Boat Parts, Engine Components | Corrosion Resistance |
Consumer Goods | Cookware, Kitchen Equipment | Durability, Lightweight |
5. 356 Alloy vs. Other Aluminum Alloys
When comparing 356 alloy to other aluminum alloys, you might be wondering how it stacks up. Let’s dive into a comparison between 356 alloy and two other popular aluminum alloys: 6061 and 7075.
Here’s the deal—356 alloy is excellent for casting due to its high fluidity, while 6061 is known for its weldability and versatility in various applications, such as structural components and pipelines. 6061 is often used in situations that don’t require the same casting abilities as 356 alloy, but it is still a solid choice for many manufacturing processes.
On the other hand, 7075 alloy is one of the strongest aluminum alloys available, making it ideal for aerospace and military applications where strength is paramount. Ready for the good part? While 7075 offers strength, it lacks the same fluidity in casting that 356 alloy boasts, which makes 356 alloy the better option for complex casting needs.
Each of these alloys has its own strengths, and the choice depends largely on the specific requirements of the project. Whether it’s casting, welding, or strength, each alloy has its place in modern manufacturing.
Alloy Type | Key Strengths | Ideal Applications |
---|---|---|
356 Alloy | High Fluidity, Corrosion Resistance | Casting, Automotive, Aerospace |
6061 Alloy | Weldability, Versatility | Structural, Piping |
7075 Alloy | High Strength, Durability | Aerospace, Military |
6. Advantages of Using 356 Alloy
The advantages of using 356 alloy are vast, and this is where it gets interesting… It is a great material for manufacturers who need strength, lightweight properties, and corrosion resistance. 356 alloy’s ability to be cast into complex shapes with high precision means that manufacturers can produce parts with less waste and lower cost. This directly translates to cost savings for both the producer and the consumer.
But here’s the kicker—356 alloy is also known for its excellent mechanical properties, especially in the aerospace and automotive industries. Its tensile strength, corrosion resistance, and durability in high-stress environments make it a standout choice. In addition, its recyclability helps companies reduce their environmental footprint, making it a win-win material for both production and sustainability.
Another key benefit is the versatility of 356 alloy. It can be used in a wide range of applications, from high-performance components to everyday consumer products. Whether you’re designing a lightweight aircraft or a durable cookware set, 356 alloy’s adaptability makes it an excellent choice.
Advantage | Benefit |
---|---|
High Fluidity | Ideal for complex parts and casting |
Corrosion Resistance | Long-lasting in harsh environments |
Lightweight | Reduced material weight for better performance |
Recyclability | Environmentally friendly option |
7. Challenges of Working with 356 Alloy
Like any material, 356 alloy has its challenges, and you might be wondering what these are. While 356 alloy is known for its excellent casting properties, one of the main challenges comes during the casting process. This is where it gets interesting… Variations in temperature, mold quality, and alloy composition can lead to defects like porosity or cracks in the final product.
Another issue with 356 alloy is its susceptibility to certain types of corrosion, particularly in environments where the alloy is exposed to moisture for prolonged periods. Although 356 alloy is resistant to corrosion in most environments, certain applications, such as marine components, may require additional protective coatings to ensure long-term durability.
Ready for the good part? The casting defects can be minimized by controlling the quality of the mold and the alloy composition, but this requires specialized knowledge and experience. Manufacturers must ensure that their suppliers understand the nuances of working with 356 alloy to prevent defects during the casting process.
Challenge | Solution |
---|---|
Casting Defects | Control mold quality and alloy composition |
Corrosion in Specific Environments | Use additional protective coatings |
8. 356 Alloy and Environmental Considerations
In today’s world, environmental impact is a big concern for manufacturers, and what’s the real story? 356 alloy is actually a relatively eco-friendly material compared to others. This is where it gets interesting… 356 alloy is recyclable, and its use in manufacturing can contribute to reducing waste and energy consumption. Once a product made from 356 alloy reaches the end of its life cycle, it can be melted down and repurposed for new products.
The environmental footprint of producing 356 alloy is also lower compared to other metals like steel, which require more energy to produce. By choosing 356 alloy, companies can help reduce their carbon footprint and promote sustainability in their manufacturing processes.
But here’s the kicker—the fact that 356 alloy is lightweight means that products made from it, like vehicles or aircraft, require less fuel to operate, contributing to reduced emissions. It’s a sustainable material that helps save energy both in production and in use.
Environmental Factor | Impact |
---|---|
Recyclability | Reduces waste and energy consumption |
Production Energy | Lower compared to steel |
Lightweight | Contributes to energy savings in use |
9. 356 Alloy in Automotive Manufacturing
356 alloy is widely used in the automotive industry, and you might be wondering what makes it such a great choice. Here’s the deal—automotive manufacturers choose 356 alloy for engine blocks, cylinder heads, and other critical engine parts because it offers a perfect balance of strength, lightweight properties, and durability. These parts must endure extreme temperatures, mechanical stresses, and frequent vibrations, all of which 356 alloy can withstand without cracking or deforming.
One of the reasons 356 alloy is so effective in automotive parts is due to its high fluidity during the casting process. This property allows manufacturers to create intricate and precise parts that fit into complex engine systems. Additionally, the alloy’s lightweight nature helps reduce the overall weight of the vehicle, which can improve fuel efficiency and performance.
Ready for the good part? By using 356 alloy, automakers can create high-performance components at a relatively low cost compared to other materials. The versatility and strength of the alloy ensure that manufacturers get the best of both worlds—high-performance parts and cost-effectiveness.
Automotive Component | Material Choice | Benefit |
---|---|---|
Engine Blocks | 356 Alloy | High Strength, Durability |
Cylinder Heads | 356 Alloy | Lightweight, Precision Casting |
Other Engine Parts | 356 Alloy | Cost-effective, High Performance |
10. 356 Alloy in Aerospace and Aviation
In the aerospace industry, 356 alloy plays a critical role in producing lightweight yet strong components. Aircraft components, such as wing structures, landing gear, and engine parts, benefit from the lightweight and corrosion-resistant properties of 356 alloy. These materials help reduce the overall weight of aircraft, which directly translates to improved fuel efficiency and performance.
What’s the real story? Aerospace manufacturers need to strike a balance between strength and weight, and 356 alloy is one of the best materials for achieving this. Its strength-to-weight ratio makes it ideal for critical aerospace components that require both durability and reduced weight to maximize fuel efficiency.
In addition to strength and weight, 356 alloy is also resistant to the harsh conditions encountered in the aerospace environment. Its ability to resist corrosion in high-temperature, high-pressure environments makes it perfect for engine components and other parts that are exposed to extreme conditions.
Aerospace Component | Material Choice | Benefit |
---|---|---|
Wing Structures | 356 Alloy | Lightweight, Strong |
Landing Gear | 356 Alloy | Corrosion Resistance |
Engine Parts | 356 Alloy | Durability, Precision Casting |
11. The Future of 356 Alloy
The future of 356 alloy looks promising, with new advancements in both the alloy’s formulation and manufacturing processes. Here’s the deal—356 alloy is becoming more refined as manufacturers experiment with different alloying elements to further enhance its properties. This is where it gets interesting… Innovations in 3D printing and other manufacturing technologies may allow for even more intricate and precise parts made from 356 alloy.
Ready for the good part? The increased focus on sustainability and reduced environmental impact is likely to further boost the popularity of 356 alloy. Its recyclability and energy-efficient production processes position it well for a future that prioritizes sustainability.
Future Trend | Impact |
---|---|
3D Printing | Allows for more complex designs |
Sustainability | Reduced environmental impact |
New Alloy Formulations | Enhanced properties |
12. How to Choose the Right 356 Alloy for Your Project
Choosing the right 356 alloy for your project is crucial, and you might be wondering what factors you should consider. What’s the real story? When selecting 356 alloy, it’s important to consider factors like the required strength, the casting process, and the environmental conditions the part will be exposed to.
The casting method plays a significant role in determining the properties of the final product. Sand casting, for example, is ideal for larger parts, while die casting is more suitable for smaller, high-precision components. Manufacturers should also consider the alloy’s composition and ensure that it meets the specific needs of the application.
But here’s the kicker—working with an experienced supplier who understands the nuances of 356 alloy is key to ensuring you get the highest quality product for your project.
Factor to Consider | Importance |
---|---|
Strength | Determines durability and performance |
Casting Method | Affects precision and cost |
Supplier Experience | Ensures quality control and reliability |
13. Casting and Manufacturing Methods for 356 Alloy
The casting process plays a pivotal role in the production of 356 alloy, and you might be wondering which methods are most commonly used. Ready for the good part? The two main methods used for 356 alloy casting are sand casting and die casting, each offering distinct benefits depending on the size and complexity of the part.
Sand casting is typically used for larger, more complex parts, as it allows for a great deal of flexibility in design. However, it may not offer the precision of die casting, which is often used for smaller, high-precision components. But here’s the kicker—die casting is faster and more cost-effective for high-volume production, making it a popular choice for industries like automotive.
Casting Method | Application | Benefits |
---|---|---|
Sand Casting | Large, Complex Parts | Flexible, Low cost |
Die Casting | Small, Precise Parts | Fast, High Volume |
14. 356 Alloy’s Role in High-Performance Products
356 alloy is often used in high-performance products due to its exceptional mechanical properties and versatility. What’s the real story? The alloy’s high strength, lightweight, and corrosion-resistant properties make it ideal for products like performance vehicle parts, military components, and sports equipment.
The automotive industry uses 356 alloy to create parts that need to withstand extreme conditions, while the aerospace industry relies on the alloy for structural components that need to be both strong and lightweight. Its versatility ensures that it is used in everyday products as well, such as cookware, which requires durability and lightweight characteristics.
But here’s the kicker—356 alloy’s ability to perform in high-stress environments while maintaining a lightweight profile is what makes it stand out in high-performance applications.
Industry | Application | Benefit |
---|---|---|
Automotive | Performance Parts | Durability, Strength |
Aerospace | Structural Parts | Lightweight, Strong |
Consumer Goods | Cookware, Tools | Durability, Lightness |
15. Conclusion
In conclusion, 356 alloy offers significant advantages for various industries, from automotive to aerospace. Its high fluidity, excellent corrosion resistance, and lightweight properties make it an ideal choice for manufacturing high-performance components. As industries continue to prioritize sustainability and durability, the demand for 356 alloy will likely increase, especially as manufacturing processes become more advanced.
What’s the real story? When selecting 356 alloy for your next project, keep in mind the casting method, desired mechanical properties, and specific environmental conditions the part will face. With its versatility and proven benefits, 356 alloy remains a top choice for manufacturers around the globe.
FAQ Section
Q1: What is 356 alloy?
356 alloy is an aluminum alloy primarily used for casting. It is known for its excellent fluidity, high strength, and corrosion resistance.
Q2: How does 356 alloy compare to other aluminum alloys?
356 alloy is superior to alloys like 6061 and 7075 in casting applications due to its high fluidity and corrosion resistance. However, 7075 is stronger for structural uses.
Q3: What industries use 356 alloy?
356 alloy is used in automotive, aerospace, marine, and consumer goods industries due to its high strength, lightweight, and durability.
Q4: How is 356 alloy made?
356 alloy is made through casting processes, typically sand casting and die casting, where aluminum, silicon, and copper are combined to create the alloy.
Q5: How do I choose the right 356 alloy for my project?
When selecting 356 alloy, consider factors such as strength, the casting method, and environmental conditions. Working with an experienced supplier ensures you get the best results.