Structural die casting plays a vital role in manufacturing industries like automotive, aerospace, and electronics. In this comprehensive guide, we will explore the intricacies of structural die casting, answering key questions and providing valuable insights for professionals looking to understand its processes, benefits, and applications. Whether you’re a manufacturer or a designer, knowing how to leverage the advantages of structural die casting can significantly improve your production processes. Let’s dive into the essential aspects of this crucial technology.
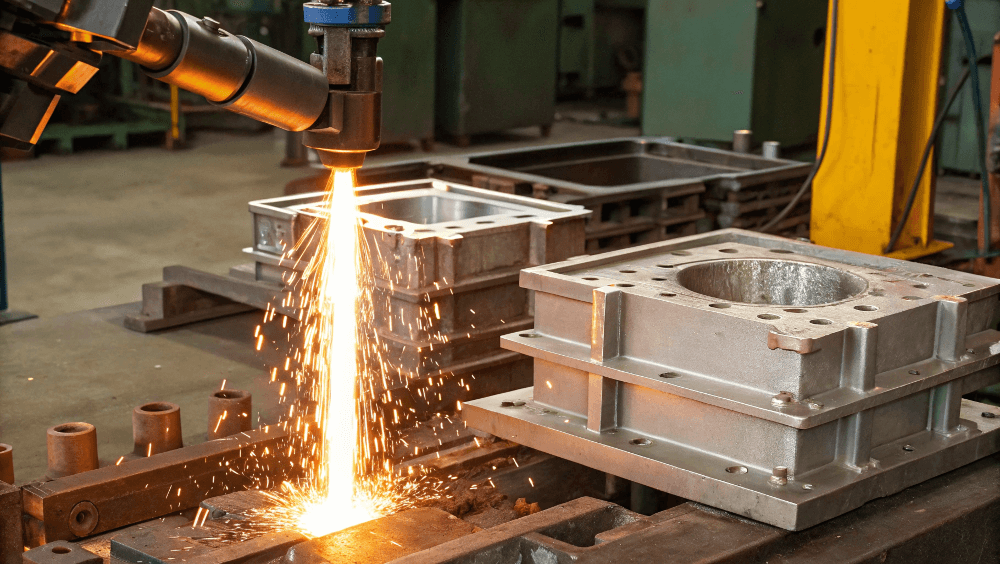
1. What is Structural Die Casting?
Structural die casting is a highly efficient manufacturing process used to create metal parts with complex shapes and high strength. The process involves injecting molten metal into a mold under high pressure, which then solidifies to form precise components. This technique is particularly beneficial when producing components that require high dimensional accuracy and excellent surface finish.
But here’s the kicker: structural die casting isn’t just about the precision of the parts. It’s about achieving strength and durability that can withstand heavy-duty applications. The types of metals typically used in this process include aluminum, zinc, and magnesium, each offering different properties depending on the application. Aluminum die casting, for instance, is renowned for its lightweight and strength, making it ideal for the automotive and aerospace industries.
What’s the real story? The main advantage of structural die casting is its ability to produce lightweight, high-strength components. This is why it’s preferred for manufacturing parts that need to be both strong and light, such as engine blocks, transmission housings, and structural supports in vehicles.
As industries push for more efficient and sustainable solutions, structural die casting stands as a leading method for producing parts that meet these demanding criteria.
Table: Comparison of Materials Used in Structural Die Casting
Material | Benefits | Common Uses |
---|---|---|
Aluminum | Lightweight, strong, corrosion-resistant | Automotive, Aerospace |
Zinc | High fluidity, low melting point | Small components, die casting |
Magnesium | Lightest metal, high strength-to-weight ratio | Aerospace, automotive |
2. How Does Structural Die Casting Work?
Ready for the good part? Let’s break down the process of structural die casting into simple steps. The procedure begins with the preparation of the die, which is typically made from steel and designed to create the desired shape of the component. Once the die is ready, the molten metal is injected into it under high pressure. This ensures that the molten metal fills every cavity and forms the component’s intricate design.
After injection, the molten metal cools and solidifies quickly, creating a near-perfect replica of the die’s shape. The die is then opened, and the solidified part is ejected. At this point, the part undergoes any necessary finishing processes, such as trimming excess material, polishing, or adding surface treatments.
But here’s the trick: the speed and precision of this process make it ideal for high-volume production. The pressure injection forces the metal to fill every corner of the die, ensuring a high level of detail in every cast part. As a result, structural die casting is often used to produce complex parts in large quantities, such as engine components, structural frames, and housing units for electronic devices.
3. Why is Structural Die Casting Used in Manufacturing?
What’s the deal with structural die casting in manufacturing? It’s all about efficiency and cost-effectiveness. One of the key reasons why manufacturers prefer this method is its ability to produce parts quickly and with high precision. The high-pressure injection method ensures that parts are made with minimal defects and that they fit perfectly into the assembly process, reducing the need for post-processing.
But here’s the kicker: it doesn’t stop at just speed. Structural die casting also allows for the production of lightweight, high-strength parts. This is essential in industries like automotive and aerospace, where performance and weight are crucial factors. Components such as transmission cases, engine blocks, and automotive body parts are all commonly produced using this technique.
Another compelling reason for using structural die casting is its versatility. With the right materials, this process can be used to create components for a wide range of applications. Whether you’re manufacturing parts for high-performance engines or durable machinery, structural die casting delivers the strength and quality needed.
Table: Advantages of Structural Die Casting
Advantage | Description |
---|---|
High Precision | Minimizes post-production adjustments |
Faster Production | Reduces lead times for manufacturing |
Lightweight & Strong Components | Ideal for automotive and aerospace industries |
Cost-Effective for High Volumes | Efficient production method for large orders |
4. What Types of Materials are Best for Structural Die Casting?
Ready to dive into materials? Structural die casting requires metals that offer a combination of strength, durability, and ease of casting. The most commonly used materials include aluminum, zinc, and magnesium, each with its unique set of benefits.
Aluminum is perhaps the most popular choice for structural die casting. It is lightweight, strong, and has excellent corrosion resistance, making it ideal for automotive and aerospace applications. The material is also highly versatile, able to be cast into intricate shapes with great precision.
Zinc, on the other hand, is often used for smaller components. It has excellent fluidity, allowing it to flow into complex mold shapes easily. Zinc die casting is commonly used for making components like connectors, housings, and other small precision parts.
Magnesium, the lightest structural metal, is often used for parts that need to be exceptionally light while maintaining strength. It’s ideal for aerospace components that require both low weight and high strength.
What’s the real story? The choice of material ultimately depends on the specific requirements of the part being produced. The goal is to balance strength, weight, cost, and durability.
5. What are the Common Industries Using Structural Die Casting?
What are the industries that benefit most from structural die casting? The answer is clear: automotive, aerospace, electronics, and defense. These sectors rely on high-performance parts that can withstand demanding conditions, and structural die casting is the go-to method for achieving that.
In the automotive industry, structural die casting is used to create engine blocks, transmission cases, and other heavy-duty components that require high strength and lightweight properties. Aluminum die casting is particularly popular in this field due to its excellent strength-to-weight ratio.
The aerospace industry also benefits from structural die casting. Parts such as wing brackets, engine components, and other structural elements are often produced using this method. The ability to produce lightweight yet durable parts is crucial in aerospace manufacturing, where weight savings can translate to fuel efficiency and performance.
Electronics manufacturers use structural die casting to create housings for electronic devices, as well as heat sinks for electronic components. This process ensures that the parts meet the required standards for durability and heat resistance.
Table: Industries Using Structural Die Casting
Industry | Applications |
---|---|
Automotive | Engine blocks, transmission cases, wheel rims |
Aerospace | Wing brackets, engine components |
Electronics | Housings, heat sinks, enclosures |
Defense | Military hardware, structural components |
6. How Are Structural Die Casting Molds Made?
This is where it gets interesting! The creation of structural die casting molds is a highly specialized process that requires precision engineering. Molds are typically made from steel due to its ability to withstand the high pressures involved in the casting process.
The mold design begins with a detailed blueprint of the part to be cast. Once the design is finalized, the mold is fabricated using advanced machining tools. The process involves carving out intricate cavities in the mold that will shape the molten metal.
What’s the kicker? The durability of the mold is a critical factor in the success of the die casting process. Molds are subjected to extreme pressure and temperature, so they must be able to withstand these conditions for extended periods. As such, manufacturers must invest in high-quality materials and precise manufacturing techniques to ensure that the mold can produce high-quality components consistently.
Choosing the right mold material and design is crucial to minimizing wear and maximizing mold life. For instance, harder steels may last longer but may be more difficult to machine, while softer steels may wear out faster but are easier to work with.
Table: Types of Molds Used in Structural Die Casting
Mold Type | Material Used | Benefits | Typical Use |
---|---|---|---|
Single-Cavity | Steel | High precision, low cost for small runs | Small parts, low volume runs |
Multi-Cavity | Tool Steel | Increased production efficiency, cost-effective for high volumes | Large production runs |
Die-Cast Die | Hardened Steel | Long-lasting, resistant to wear and tear | Heavy-duty parts, automotive components |
7. What are the Advantages of Structural Die Casting?
You might be wondering why structural die casting is so popular in manufacturing. The answer is simple: it offers numerous advantages over other methods of casting.
First, the process is incredibly fast. Parts can be produced in high volumes quickly, making it ideal for industries that need to scale production. The high-pressure injection method ensures that parts are made with minimal defects, which reduces the need for post-processing.
Second, structural die casting allows for the production of complex parts with intricate shapes and fine details. This makes it ideal for creating components that other casting methods might struggle to produce.
Lastly, die casting results in parts that are both strong and lightweight, offering the best of both worlds. The high strength-to-weight ratio is particularly important in industries like automotive and aerospace, where every ounce matters.
Table: Benefits of Structural Die Casting
Benefit | Description |
---|---|
Speed of Production | High-volume production with minimal delays |
Precision and Detail | Ability to create intricate shapes and details |
Lightweight, Durable Parts | Ideal for high-performance industries |
Cost-Effective for Large Orders | Suitable for mass production needs |
8. What are the Challenges in Structural Die Casting?
While structural die casting offers many advantages, it’s not without its challenges. One of the main issues manufacturers face is the potential for defects such as porosity and surface imperfections. These can occur if the mold isn’t properly filled, or if the molten metal cools too quickly.
Another challenge is the high cost of mold production. High-quality molds are expensive to manufacture, and the process of creating them requires a significant investment in time and resources.
What’s the real story? While these challenges can be significant, they are often mitigated by advancements in technology and better-quality materials. Manufacturers who understand these potential pitfalls can take steps to prevent issues and optimize their die casting processes.
Table: Common Challenges in Structural Die Casting
Challenge | Solution |
---|---|
Porosity and Surface Defects | Use better mold designs, improve cooling rates |
High Cost of Mold Production | Invest in high-quality, durable molds |
Material Selection | Choose the right material for the application |
9. How Do Quality Control Processes Work in Structural Die Casting?
What’s the deal with quality control? In structural die casting, ensuring that parts meet the required specifications is a top priority. Manufacturers use a variety of testing methods to inspect the quality of cast parts.
One common method is X-ray inspection, which helps detect internal defects such as porosity. Visual inspection is also crucial for identifying surface defects like cracks or misalignment. Additionally, mechanical testing is often performed to ensure the strength and durability of the parts.
But here’s the kicker: the process doesn’t stop with just inspections. Manufacturers also employ statistical process control (SPC) to monitor the production process and ensure that it remains consistent. This helps prevent defects from occurring in the first place.
Table: Quality Control Methods in Structural Die Casting
Method | Purpose |
---|---|
X-ray Inspection | Detects internal defects such as porosity |
Visual Inspection | Identifies surface defects and misalignment |
Mechanical Testing | Ensures strength and durability |
10. How Much Does Structural Die Casting Cost?
What’s the price tag? The cost of structural die casting depends on several factors, including the material used, the complexity of the part, and the volume of production.
For smaller production runs, the cost per part can be relatively high due to the expense of the mold. However, for large-volume orders, the cost per part decreases significantly, making structural die casting a cost-effective choice for mass production.
But here’s the kicker: while the initial setup cost can be expensive, the long-term savings in production speed and quality can make structural die casting an excellent choice for manufacturers.
Table: Factors Affecting the Cost of Structural Die Casting
Factor | Impact on Cost |
---|---|
Material Used | Different materials have different costs |
Mold Complexity | More complex molds are more expensive |
Production Volume | Higher volumes lead to lower costs per unit |
11. What are the Environmental Impacts of Structural Die Casting?
You might be wondering about the environmental implications of structural die casting. Like all manufacturing processes, die casting does have some impact on the environment. The main concerns are energy consumption and waste production.
The die casting process requires significant amounts of energy, especially when melting metal. However, manufacturers are taking steps to reduce their energy usage and minimize waste. One way to do this is by using recycled metals, which not only reduces the demand for raw materials but also cuts down on energy consumption.
What’s the real story? As industries continue to focus on sustainability, advancements in die casting technology will help reduce its environmental footprint.
Table: Environmental Impact of Structural Die Casting
Impact | Mitigation Method |
---|---|
High Energy Consumption | Use energy-efficient equipment |
Metal Waste | Recycle materials and improve processes |
Carbon Emissions | Implement sustainable practices |
12. How Can You Improve the Efficiency of Structural Die Casting?
Here’s where it gets interesting: improving the efficiency of structural die casting involves optimizing the process, reducing defects, and maximizing throughput. The key to better efficiency lies in adopting new technologies and improving existing processes.
For example, manufacturers can use automated systems to monitor and control the die casting process in real-time. This allows them to adjust parameters on the fly, ensuring that the process remains optimal and efficient.
What’s the kicker? By incorporating better cooling systems, more advanced molding techniques, and robotic automation, manufacturers can achieve higher efficiency and lower production costs.
Table: Methods to Improve Die Casting Efficiency
Method | Benefit |
---|---|
Automation and Robotics | Increases precision and reduces human error |
Advanced Cooling Systems | Reduces cycle times and improves quality |
Better Molding Techniques | Ensures higher-quality parts with fewer defects |
13. How Long Does it Take to Produce Structural Die Cast Parts?
What’s the real story behind production time? The time required to produce a structural die cast part depends on several factors, such as the complexity of the part, the material used, and the size of the production run.
For simple parts, the die casting process can be completed in just a few minutes. However, more complex parts may take longer, especially if the mold needs to be replaced or adjusted during the production process.
What’s the kicker? Despite the complexity, the efficiency of the die casting process often results in faster production times compared to other manufacturing methods.
Table: Time Required for Structural Die Casting Production
Factor | Production Time (Approx.) |
---|---|
Simple Parts | 5–15 minutes |
Complex Parts | 20–30 minutes |
Custom Molds | Additional 30 minutes or more |
14. What Innovations Are Shaping the Future of Structural Die Casting?
What’s the future look like? The future of structural die casting is being shaped by several innovations in technology and material science. New alloys are being developed that offer even greater strength and durability, while advancements in automation and robotics are improving the efficiency of the die casting process.
What’s the kicker? As industries push for more sustainable and efficient solutions, innovations in die casting technology will continue to drive progress. The use of 3D printing for mold design and the integration of artificial intelligence in production systems are two examples of how technology is reshaping the industry.
Table: Innovations in Structural Die Casting
Innovation | Benefit |
---|---|
3D Printing for Mold Design | Reduces lead times and mold costs |
Artificial Intelligence | Optimizes production and reduces defects |
New Alloys | Enhances strength and durability |
15. How Do You Choose a Reliable Structural Die Casting Supplier?
Choosing a reliable supplier for structural die casting is crucial for ensuring quality and timely delivery. The best suppliers have a proven track record of producing high-quality parts, a clear understanding of your requirements, and the capability to meet deadlines.
What’s the kicker? It’s essential to choose a supplier who understands your industry and can provide expert advice on material selection, mold design, and production optimization.
Table: Key Factors for Choosing a Die Casting Supplier
Factor | Importance |
---|---|
Quality Control Processes | Ensures high-quality parts |
Experience and Reputation | A proven track record builds trust |
Technical Expertise | Helps in selecting materials and designs |
FAQ Section
Q1: What is structural die casting?
Structural die casting is a manufacturing process where molten metal is injected into a mold under high pressure, resulting in precise, strong, and durable components.
Q2: How does the structural die casting process work?
In structural die casting, molten metal is injected into a mold, where it cools and solidifies. The mold is then opened to release the part, which is trimmed and finished as needed.
Q3: What materials are best for structural die casting?
Aluminum, zinc, and magnesium are the most commonly used materials in structural die casting. Each material offers distinct benefits such as lightweight, strength, and corrosion resistance.
Q4: How long does it take to produce structural die cast parts?
The production time depends on the complexity of the part, but simple parts can be cast in as little as 5–15 minutes, while complex components may take up to 30 minutes.
Q5: How do I choose a reliable structural die casting supplier?
Look for suppliers with a proven track record, strong quality control processes, technical expertise, and the ability to meet your production deadlines.