Aluminum casting molds are a critical component in the manufacturing process across various industries. These molds play an essential role in shaping molten aluminum into desired forms, which are then used to create parts for industries such as automotive, aerospace, and electronics. But how exactly do these molds benefit manufacturing processes? The benefits are numerous, including increased efficiency, reduced costs, and enhanced precision. This article will explore how aluminum casting molds contribute to improving manufacturing processes, the types of molds available, and how to make the most of their advantages. Let’s dive into the details!
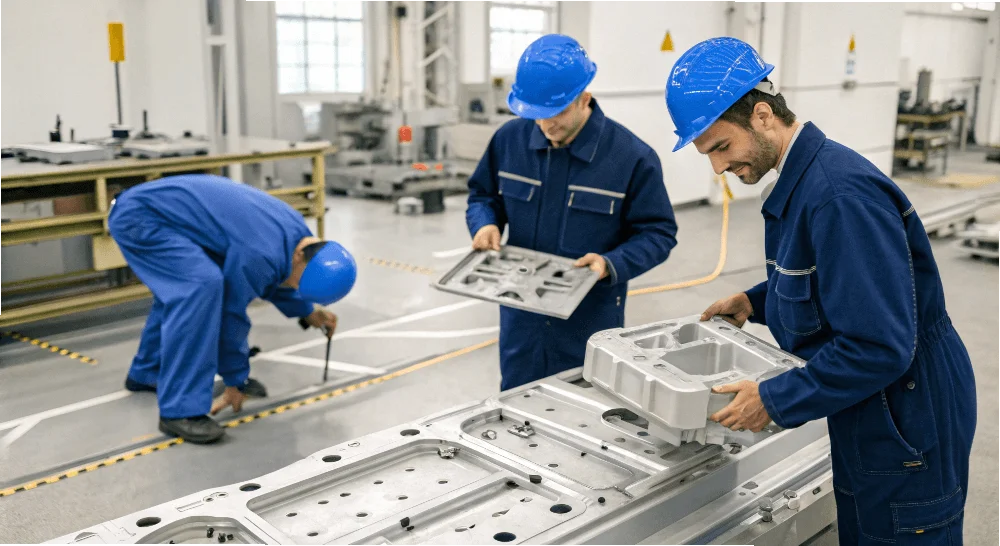
1. How Do Aluminum Casting Molds Work in Manufacturing?
Aluminum casting molds serve as the foundation for producing intricate parts used in manufacturing. The process starts by heating aluminum until it becomes molten. This molten metal is then poured into a mold cavity where it cools and solidifies, taking the shape of the mold. The key to understanding how aluminum casting molds work lies in recognizing their ability to create high-precision components quickly and efficiently.
But here’s the kicker—the quality of the aluminum mold significantly impacts the end product. A well-designed mold ensures that the final part is accurate and consistent, minimizing defects. Additionally, aluminum’s natural properties, such as its lightweight nature and excellent heat conductivity, make it an ideal material for mold production. This is where it gets interesting: the precision provided by aluminum molds helps reduce the amount of material waste, making them cost-effective.
A crucial aspect of using aluminum molds in manufacturing is their versatility. From automotive parts to aerospace components, the molds can handle a wide range of materials and processes. This flexibility makes them indispensable in industries requiring high-quality, complex shapes. By understanding how aluminum casting molds operate, manufacturers can leverage these benefits to create better, more efficient products at scale.
Aluminum Mold Benefit | Description | Impact on Manufacturing |
---|---|---|
Precision | Aluminum molds ensure high accuracy and consistency. | Reduces defects, enhancing part quality. |
Heat Conductivity | Aluminum cools quickly, improving cycle time. | Speeds up production, reducing overall manufacturing costs. |
Lightweight | Aluminum molds are lighter than steel. | Eases handling and reduces transportation costs. |
Material Waste Reduction | Aluminum molds minimize waste during the casting process. | Increases material efficiency, cutting costs. |
2. What Are the Different Types of Aluminum Casting Molds?
When it comes to aluminum casting, not all molds are created equal. There are several types of molds, each with its unique characteristics, advantages, and best-use scenarios. Here, we’ll explore the main types of aluminum casting molds and their applications in manufacturing.
The most commonly used aluminum casting molds are permanent molds, sand molds, die-casting molds, and shell molds. Each type is suited for different manufacturing needs, making it important to choose the right mold for your specific project. Permanent molds, for example, are ideal for high-volume production as they offer durability and the ability to create complex shapes with precision.
What’s the real story here? Each mold type has its own set of strengths and limitations. For instance, while permanent molds can withstand multiple uses, they require high initial investment. On the other hand, sand molds are cost-effective and suitable for low-volume production. However, they may not offer the same precision as permanent molds.
Die-casting molds are another popular option, especially in high-precision industries like automotive and aerospace. These molds allow for mass production of aluminum parts with excellent detail and dimensional accuracy. Similarly, shell molds are used for casting complex geometries, offering high strength and surface finish.
Mold Type | Description | Advantages | Disadvantages |
---|---|---|---|
Permanent Molds | Molds used for high-volume, reusable casting. | Durability, high precision, cost-effective for mass production. | High initial setup cost. |
Sand Molds | Mold made from sand, used for low-volume production. | Low initial cost, flexible, easy to modify. | Lower precision, more material waste. |
Die-Casting Molds | Metal molds used for high-precision parts. | Excellent detail, fast production cycle, ideal for mass production. | Expensive equipment, requires specialized skill. |
Shell Molds | Thin ceramic molds used for complex shapes. | High strength, excellent surface finish. | Labor-intensive, limited production capacity. |
3. Why Are Aluminum Casting Molds Essential for Efficient Manufacturing?
In the world of manufacturing, efficiency is key to staying competitive. Aluminum casting molds help drive this efficiency by offering numerous benefits that streamline the production process. What’s the real advantage? Aluminum casting molds allow manufacturers to produce complex, high-quality parts quickly and at a lower cost.
Let’s take automotive manufacturing as an example. Aluminum casting molds are crucial for producing lightweight, durable components like engine blocks and transmission parts. Without these molds, the precision required for these complex shapes would be hard to achieve, leading to longer production times and increased costs. Aluminum molds also help reduce material waste by ensuring that the molten metal fills the mold cavity perfectly, which saves both time and resources.
What’s the kicker here? The combination of precision, speed, and cost-effectiveness makes aluminum casting molds an invaluable asset in any manufacturing process. They’re not just about creating parts—they’re about creating parts more efficiently and economically, driving down production costs while increasing output.
Benefit | Description | Impact on Manufacturing Efficiency |
---|---|---|
Cost Reduction | Aluminum molds reduce production costs. | More efficient material use and faster production cycles. |
Speed | Aluminum molds cool and set quickly. | Reduces production time, increasing throughput. |
Waste Minimization | Precision molds reduce excess material. | Saves costs on raw materials and reduces waste. |
High-Quality Parts | Aluminum molds maintain dimensional accuracy. | Reduces defects, leading to less rework and more reliable products. |
4. How Are Aluminum Casting Molds Manufactured?
The manufacturing process for aluminum casting molds involves several critical steps, each contributing to the mold’s accuracy and functionality. From design to production, the process ensures that the final mold can handle high temperatures and the precise casting of molten aluminum.
The first step in creating aluminum casting molds is the design phase. Here, manufacturers use advanced computer-aided design (CAD) software to create a detailed blueprint of the mold. Once the design is finalized, the mold is fabricated using materials such as high-strength steel or other alloys capable of withstanding the heat generated during casting.
Ready for the good part? The next phase involves the actual creation of the mold. Using specialized machinery, the mold is formed and refined until it meets the specifications required for casting. The mold is then thoroughly tested to ensure it can handle the stresses and temperatures involved in the casting process.
Additionally, manufacturers must ensure that the molds are capable of repeated use without degradation. This means that mold maintenance is crucial. Ensuring that molds are properly cared for extends their lifespan and ensures consistent results in every batch of production.
Step | Description | Critical Process in Manufacturing |
---|---|---|
Design | CAD software designs the mold blueprint. | Ensures precise mold specifications. |
Material Selection | High-strength alloys are chosen for durability. | Provides mold longevity and heat resistance. |
Fabrication | Molds are formed using specialized machines. | Creates the exact shape needed for casting. |
Testing | Molds undergo rigorous testing for quality. | Verifies mold integrity and ensures accurate production results. |
5. What Are the Advantages of Using Aluminum Casting Molds Over Other Materials?
Aluminum casting molds offer several advantages over molds made from other materials. From cost-effectiveness to durability, aluminum stands out as one of the best choices for mold production. But here’s the kicker—aluminum’s unique properties make it more versatile than many other materials, especially in high-precision manufacturing.
One of the key benefits of aluminum casting molds is their lightweight nature. Unlike steel or iron, aluminum molds are easy to handle and transport, which reduces overall manufacturing costs. Additionally, aluminum has excellent heat conductivity, which means that it can cool more efficiently, allowing for faster production.
What’s the real story? Aluminum molds are also more reliable than molds made from other materials. This reliability translates into higher quality parts with fewer defects, which is crucial in industries like automotive and aerospace. In fact, the durability of aluminum casting molds means they can be reused multiple times, making them cost-effective in the long run.
Aluminum molds also offer better surface finishes than many other mold materials. This is particularly important when producing parts that require high precision and a smooth finish, like in the electronics or medical device industries.
Advantage | Description | Impact on Manufacturing |
---|---|---|
Lightweight | Aluminum molds are lighter than steel or iron. | Easier handling and transportation, lowering logistics costs. |
Heat Conductivity | Aluminum has superior heat conductivity. | Faster cooling, reducing cycle times and production costs. |
Durability | Aluminum molds last longer with proper maintenance. | Reduced costs over time due to fewer mold replacements. |
Better Surface Finish | Aluminum molds create smooth, precise surfaces. | Ideal for high-precision industries needing smooth parts. |
6. What Are the Main Applications of Aluminum Casting Molds?
Aluminum casting molds are used in a wide variety of industries to create high-quality parts and components. From automotive to aerospace, aluminum casting molds are essential for manufacturing durable, precise products. Ready for the good part? Here are some key industries that rely heavily on aluminum casting molds:
In the automotive industry, aluminum molds are used to produce engine parts, transmission components, and wheels. These parts require high precision, and aluminum molds offer the exacting standards needed for mass production. Aerospace manufacturers also rely on aluminum molds to create lightweight and durable parts, such as fuselage sections and wing components.
In electronics, aluminum casting molds are used to create parts for computers, smartphones, and other devices. The demand for lightweight, heat-resistant components in electronics is high, and aluminum molds help meet these needs efficiently.
What’s the kicker here? Even in industries like consumer goods and hardware, aluminum casting molds play a vital role in ensuring parts are strong, functional, and cost-effective. Whether it’s a small appliance or a large machine, aluminum casting molds are versatile and necessary for producing quality products.
Industry | Application | Key Benefits of Aluminum Molds |
---|---|---|
Automotive | Engine parts, transmission components. | Lightweight, durable, and precise. |
Aerospace | Aircraft components, fuselage sections. | High strength-to-weight ratio, precision in complex parts. |
Electronics | Computer parts, smartphone casings. | Heat resistance, high precision for intricate designs. |
Consumer Goods | Appliances, home hardware. | Cost-effective, reliable for mass production. |
7. How Do Aluminum Casting Molds Contribute to Product Quality?
Product quality is a top priority for any manufacturer, and aluminum casting molds play a significant role in ensuring that products meet high standards. The accuracy and consistency of aluminum molds lead to parts that are not only durable but also dimensionally precise. This is where it gets interesting: the precision offered by aluminum casting molds helps reduce defects and improve the overall quality of the final product.
What’s the real story? Aluminum molds are capable of creating components that fit together perfectly, with minimal finishing required after the casting process. This reduces the risk of errors during assembly and ensures that products function as intended. Additionally, aluminum molds are ideal for creating complex shapes that other materials might struggle with, making them crucial for industries that require intricate designs.
Ready for the good part? Using aluminum molds also helps prevent problems such as porosity or air pockets within the metal. This is particularly important in industries where strength and reliability are paramount, like aerospace or automotive manufacturing.
Quality Factor | Description | Impact on Product Quality |
---|---|---|
Dimensional Precision | Aluminum molds maintain tight tolerances. | Reduces defects, ensuring parts fit and function correctly. |
Surface Finish | Aluminum molds provide a smooth finish. | Minimizes rework and improves the final product’s appearance. |
Porosity Control | Aluminum molds reduce air pockets in castings. | Increases strength, especially in critical applications. |
Complexity Handling | Aluminum molds can handle intricate shapes. | Enables the production of complex, high-precision components. |
8. What Are Common Challenges in Using Aluminum Casting Molds?
Aluminum casting molds, while highly beneficial, do come with some challenges. The most significant challenge manufacturers face with aluminum molds is thermal expansion. When aluminum is heated, it expands, and this expansion can cause distortions in the mold and the final casted part. This can lead to dimensional inaccuracies, which are unacceptable in industries like aerospace, where precision is paramount. What’s the real story? By controlling the temperature during the casting process, manufacturers can minimize the effects of thermal expansion. A carefully managed cooling process ensures that aluminum cools at a consistent rate, preventing warping and maintaining accuracy.
Another common issue is mold defects, such as cracks or surface imperfections. These defects may occur due to improper cooling rates, poor mold design, or contamination during casting. Ready for the good part? To combat these defects, manufacturers can invest in high-quality mold materials, design the mold for uniform cooling, and implement strict quality control processes to identify and correct any issues before the parts reach the customer.
Aluminum casting molds can also suffer from porosity—the formation of small gas pockets within the cast aluminum. Porosity can weaken the final product, making it unsuitable for use in critical applications. The best way to handle this issue? By using vacuum-assisted casting or improving mold venting to eliminate trapped gases. These solutions can help ensure that the final product is free of porosity and meets the required strength standards.
Challenge | Description | Solution |
---|---|---|
Thermal Expansion | Aluminum expands when heated, causing distortions. | Control cooling rates and temperatures to reduce thermal issues. |
Mold Defects | Cracks and surface imperfections can arise. | Use high-quality materials and monitor cooling rates. |
Porosity | Air pockets can form inside the aluminum casting. | Use vacuum-assisted casting and improve mold venting techniques. |
9. How Can You Optimize Aluminum Casting Mold Performance?
To achieve the highest quality parts and maximize the life cycle of aluminum casting molds, it’s essential to optimize their performance. Ready for the good part? There are several strategies manufacturers can use to enhance the effectiveness of aluminum molds.
The first step in optimizing mold performance is design optimization. Using advanced CAD software, manufacturers can ensure the mold is designed for optimal material flow and cooling. This reduces potential defects and ensures that the final product will be precisely what is needed. What’s the kicker here? Simulation tools can predict how the molten aluminum will behave within the mold, allowing adjustments to be made before any metal is poured.
Another key aspect of optimization is material selection. The right aluminum alloy can make all the difference in mold performance. For example, alloys like Aluminum 356 are known for their excellent casting properties, including high strength and resistance to corrosion. By choosing the right alloy, manufacturers can increase the mold’s durability and its ability to withstand high temperatures, reducing wear and tear during casting cycles.
Temperature control is another crucial factor. The mold should be heated to the appropriate temperature before pouring molten aluminum into it. Maintaining consistent temperatures throughout the mold ensures that the casting process is stable, which results in better quality parts. Ready to dive into this? Investing in high-precision cooling systems can improve cooling rates, reduce cycle times, and prevent overheating, which in turn leads to better overall casting quality.
Optimization Strategy | Description | Benefits |
---|---|---|
Design Optimization | Use CAD and simulation software for mold design. | Enhances mold accuracy and predicts potential issues. |
Material Selection | Choose alloys with high strength and thermal resistance. | Increases mold longevity and casting quality. |
Temperature Control | Implement precise heating and cooling systems. | Prevents overheating, reduces cycle times, and improves part quality. |
10. What Are the Best Practices for Aluminum Casting Mold Maintenance?
Maintaining aluminum casting molds is essential for ensuring that they perform at their best over time. Proper maintenance can significantly extend the lifespan of the molds and improve the consistency of the parts they produce. Let’s dive into the best practices for mold maintenance, starting with regular cleaning.
After each casting, molds should be cleaned thoroughly to remove any aluminum residue, dust, or debris. This prevents material buildup that could interfere with the casting process or degrade the quality of the next batch. But here’s the kicker—using abrasive cleaning techniques such as shot blasting can help remove stubborn residues without damaging the mold surface.
Another best practice is inspection. Regular inspections should be conducted to check for signs of wear or damage, such as cracks or warping. This ensures that any issues are detected early, preventing further damage and costly repairs. Ready for the good part? It’s also important to inspect the mold’s cooling and heating systems, ensuring that they’re working properly and effectively managing temperature during the casting process.
Proper storage is also a key factor in maintaining mold performance. When molds are not in use, they should be stored in a dry, cool environment to avoid corrosion or damage. Molds should be stored vertically to prevent deformation. Regular maintenance and careful handling will help keep aluminum molds in top shape for years to come.
Maintenance Practice | Description | Benefits |
---|---|---|
Cleaning | Remove aluminum residue after each casting. | Prevents material buildup and ensures smooth casting. |
Inspection | Check for cracks, warping, or other damage. | Identifies issues early to prevent further damage and costly repairs. |
Storage | Store molds in a dry, cool place. | Prevents corrosion and deformation, extending mold life. |
11. How Do Aluminum Casting Molds Impact the Environment?
As sustainability becomes more important, manufacturers are looking for ways to reduce their environmental impact. Aluminum casting molds offer several environmental advantages that can help companies make greener choices without sacrificing quality. What’s the kicker here? Aluminum is one of the most recyclable metals available, and aluminum casting molds can be reused for multiple production cycles.
In fact, aluminum recycling has a low environmental impact compared to extracting new aluminum from bauxite ore. What’s the real story here? Recycled aluminum requires only 5% of the energy needed to produce new aluminum, making it a more sustainable option for casting. By utilizing aluminum molds, manufacturers reduce the amount of waste generated during the production process.
Additionally, aluminum molds contribute to energy efficiency. They cool more quickly than molds made from other materials, which reduces the energy needed to maintain consistent temperatures during casting. This not only saves on energy costs but also helps reduce the carbon footprint of the manufacturing process.
What’s the kicker here? Aluminum molds are also lightweight, which reduces transportation costs and the associated environmental impact. The ease with which aluminum can be handled, transported, and recycled makes it a more eco-friendly choice for mold production.
Environmental Benefit | Description | Impact on Sustainability |
---|---|---|
Recyclability | Aluminum can be recycled with minimal energy usage. | Reduces the need for new materials, lowering environmental impact. |
Energy Efficiency | Aluminum molds cool quickly, saving energy. | Reduces the carbon footprint and lowers energy consumption. |
Lightweight | Aluminum is lighter than steel or iron. | Reduces transportation costs and environmental impact. |
12. How Can Aluminum Casting Molds Reduce Costs in Manufacturing?
Cost reduction is always a top priority in manufacturing. The good news is that aluminum casting molds can significantly lower production costs while maintaining high-quality output. First, aluminum molds offer superior durability compared to molds made from other materials. This means that manufacturers can use the same molds for longer periods, reducing the need for frequent replacements. Over time, this leads to cost savings.
What’s the real story? Aluminum casting molds also help reduce material waste. Since aluminum is highly conductive, it cools faster, allowing manufacturers to produce parts with greater precision and less scrap material. This not only improves the quality of the products but also minimizes the cost of raw materials.
Another significant way aluminum molds reduce costs is by speeding up production times. Aluminum molds can be designed to cool quickly and uniformly, allowing for faster cycle times in casting. This is particularly beneficial in industries that require high-volume production, such as automotive and electronics.
What’s the kicker here? The cost-efficiency of aluminum casting molds means that manufacturers can produce high-quality products at a lower overall cost, leading to a more profitable operation.
Cost Reduction Strategy | Description | Benefits |
---|---|---|
Durability | Aluminum molds last longer than other materials. | Reduced costs for mold replacements. |
Material Efficiency | Faster cooling rates reduce waste. | Less scrap material, saving on raw materials. |
Faster Production | Quick, uniform cooling reduces cycle times. | More parts produced per hour, lowering overall production costs. |
13. What Technologies Are Improving Aluminum Casting Mold Design?
Advancements in technology have significantly improved the design and production of aluminum casting molds. One of the key developments in this area is the use of 3D printing. 3D printing allows for rapid prototyping of mold designs, enabling manufacturers to test and refine their molds before committing to full-scale production. This not only saves time but also reduces costs associated with traditional mold-making processes.
But here’s the kicker—simulation software has revolutionized the way molds are designed. These software programs allow manufacturers to simulate the casting process and predict potential issues, such as porosity or uneven cooling. This predictive capability helps manufacturers create better molds that are less prone to defects, resulting in higher-quality castings.
What’s the real story here? The integration of robotics and automation in mold production is also improving efficiency. Automated systems can handle tasks like mold cleaning, inspection, and maintenance, reducing labor costs and ensuring that molds are consistently maintained to high standards.
Technology | Description | Impact on Mold Design and Production |
---|---|---|
3D Printing | Allows rapid prototyping of mold designs. | Saves time and reduces costs by testing designs before full production. |
Simulation Software | Predicts potential issues like porosity and uneven cooling. | Helps optimize designs and improve casting accuracy. |
Robotics and Automation | Automates cleaning, inspection, and maintenance tasks. | Reduces labor costs and ensures consistent mold quality. |
14. How Do Aluminum Casting Molds Affect the Automotive Industry?
The automotive industry is one of the largest consumers of aluminum casting molds, and for good reason. Aluminum casting molds play a critical role in producing lightweight yet durable components for cars, trucks, and other vehicles. So, why are these molds so important for the automotive industry? The lightweight nature of aluminum helps manufacturers produce fuel-efficient vehicles by reducing the overall weight of the vehicle.
Ready for the good part? Aluminum molds are used to create essential automotive parts, such as engine blocks, transmission housings, and wheels, all of which require high precision and strength. By using aluminum casting molds, manufacturers can achieve the level of accuracy needed for complex parts while keeping production costs in check.
What’s the kicker here? Aluminum casting molds also support faster production cycles, which is vital in the highly competitive automotive industry. The ability to produce parts quickly and efficiently helps manufacturers meet demand and maintain a competitive edge.
Application | Description | Benefits to the Automotive Industry |
---|---|---|
Engine Blocks | Aluminum molds create lightweight engine blocks. | Reduces vehicle weight, improving fuel efficiency. |
Transmission Housings | Molds used for transmission parts. | High precision ensures proper fit and functionality. |
Wheels | Aluminum molds are used for wheel production. | Lighter wheels improve vehicle performance and fuel economy. |
15. What Are the Future Trends in Aluminum Casting Molds?
As technology continues to evolve, so does the field of aluminum casting. The future of aluminum casting molds looks promising, with several exciting trends on the horizon. One of the most significant trends is the increased use of smart manufacturing technologies. These technologies use sensors and data analytics to monitor the casting process in real-time, providing valuable insights into mold performance and product quality.
What’s the kicker here? 3D printing is also set to revolutionize the design and production of aluminum molds. As 3D printing technology continues to improve, manufacturers will be able to create more complex and customized molds with greater precision and at lower costs.
What’s the real story here? The continued development of sustainable practices in aluminum casting will likely lead to even more eco-friendly production methods. As manufacturers strive to reduce their environmental impact, innovations in mold design and materials will make aluminum casting even more sustainable and cost-effective.
Future Trend | Description | Impact on Aluminum Casting Molds |
---|---|---|
Smart Manufacturing | Use of sensors and data analytics for real-time monitoring. | Improves mold performance and part quality. |
3D Printing | Revolutionizes mold design and production. | Allows for more complex, cost-effective, and customized molds. |
Sustainability | Increased focus on eco-friendly practices in casting. | Reduces environmental impact and improves overall cost-efficiency. |
FAQ Section
Q1: What are aluminum casting molds?
Aluminum casting molds are specialized molds used to shape molten aluminum into specific forms. These molds are crucial for creating high-precision components used in industries like automotive, aerospace, and electronics.
Q2: How do aluminum casting molds improve manufacturing?
Aluminum casting molds improve manufacturing by enhancing precision, reducing production costs, and speeding up the casting process, all while ensuring the quality of the final product.
Q3: What types of aluminum casting molds are commonly used?
The most common types of aluminum casting molds are permanent molds, sand molds, die-casting molds, and shell molds. Each type is chosen based on the requirements of the specific manufacturing process.
Q4: How can I maintain my aluminum casting molds?
To maintain aluminum casting molds, ensure regular inspection, cleaning, and proper storage to prevent damage and wear. Proper care extends the lifespan of the molds and ensures high-quality production.
Q5: What industries benefit the most from aluminum casting molds?
Industries such as automotive, aerospace, electronics, and household appliances benefit greatly from aluminum casting molds, as they provide precision, durability, and cost-effectiveness in manufacturing.