Introduction
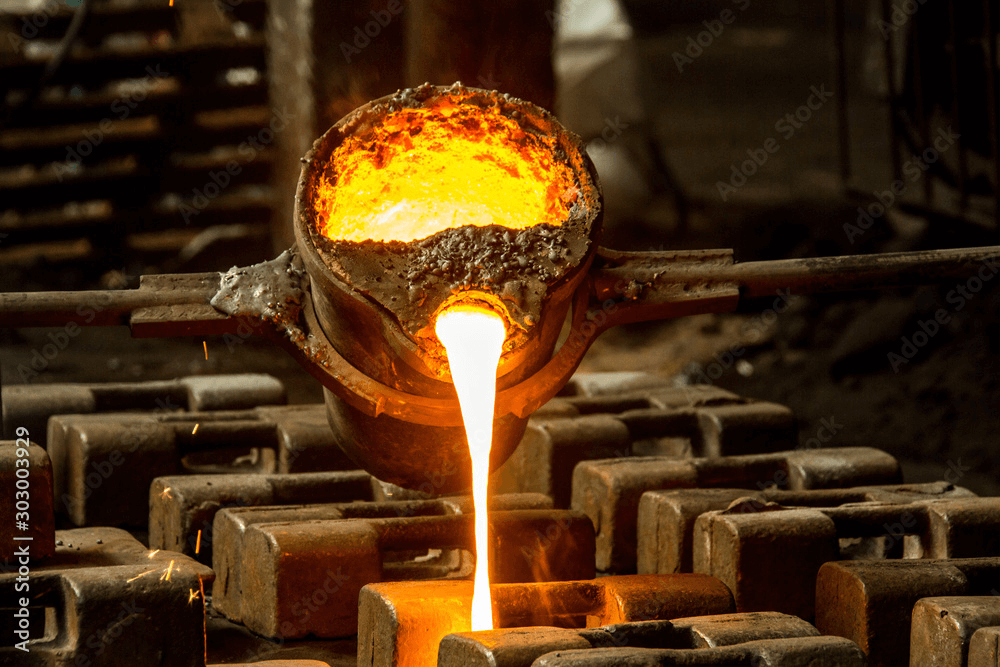
High-temperature alloys are the backbone of many advanced industries. They withstand extreme heat, resist corrosion, and maintain strength under immense stress. These materials drive innovation in fields like aerospace, automotive engineering, and energy. But what makes these alloys so extraordinary? In this guide, we will explore their composition, unique properties, and critical role in various industries. Whether you’re a technician, engineer, or simply curious, this comprehensive article will illuminate how high-temperature alloys are changing the game.
What Are High-Temperature Alloys?
High-temperature alloys, often referred to as superalloys, are materials designed to perform in extreme conditions. These alloys maintain exceptional strength, resist deformation, and endure elevated temperatures where standard materials fail. Their robust performance makes them indispensable for demanding applications.
Composition and Structure
High-temperature alloys typically consist of a blend of elements such as nickel, cobalt, and iron, which serve as the base. The addition of chromium, molybdenum, and aluminum enhances corrosion resistance, heat stability, and mechanical strength. The precise composition varies depending on the intended application, but the balance of elements ensures optimal performance under stress.
Key Characteristics
The defining traits of these alloys include their ability to endure extreme heat, resist oxidation, and maintain mechanical integrity. Unlike standard materials, high-temperature alloys are engineered with microstructural stability that prevents grain coarsening, a common issue at elevated temperatures.
Applications in Various Sectors
The versatility of high-temperature alloys stems from their adaptability. They are used in turbine blades, rocket engines, and industrial furnaces. Each application leverages the alloy’s unique properties to optimize performance, ensuring efficiency and longevity.
Historical Development
The evolution of high-temperature alloys is deeply tied to technological advancements. From the inception of early metallurgical techniques to today’s sophisticated alloy design, these materials have undergone remarkable transformations.
Early Discoveries
The origins of high-temperature alloys trace back to the early 20th century when engineers sought materials capable of withstanding the heat generated by internal combustion engines. Nickel-based alloys emerged as a solution, offering both durability and thermal stability.
Milestones in Development
Key breakthroughs occurred during World War II with the development of jet engines. Engineers faced the challenge of creating turbine blades that could endure the intense heat and stress of jet propulsion. This demand led to innovations such as the introduction of chromium and aluminum into alloy compositions, which significantly improved oxidation resistance.
Modern Innovations
Today, advances in computational modeling and material science have revolutionized alloy design. High-entropy alloys and additive manufacturing techniques are pushing the boundaries, enabling precise customization for specific applications. These innovations ensure that high-temperature alloys remain at the forefront of industrial progress.
The Science Behind High-Temperature Alloys
Understanding the science of high-temperature alloys requires exploring their behavior under extreme conditions. Their performance is a result of careful engineering at the atomic level.
Thermal Stability
The hallmark of high-temperature alloys is their ability to retain mechanical properties at high temperatures. This stability is achieved through the presence of precipitates within the alloy’s matrix, which act as barriers to dislocation movement, thereby maintaining strength.
Microstructural Engineering
Microstructural stability is key to preventing grain growth and degradation. The inclusion of elements like niobium and tantalum promotes the formation of gamma-prime (γ’) and gamma-double-prime (γ”) phases, which are essential for strengthening.
Relationship Between Composition and Properties
The properties of high-temperature alloys are intricately linked to their composition. For instance, nickel-based alloys excel in oxidation resistance due to the formation of a stable oxide layer, while cobalt-based alloys offer superior wear resistance. Engineers can tailor these properties to meet specific needs by adjusting the elemental makeup.
Applications Across Industries
The impact of high-temperature alloys spans multiple industries, each relying on their unique properties for critical functions.
Aerospace
In the aerospace sector, high-temperature alloys are indispensable. They are used in turbine blades, combustion chambers, and exhaust nozzles, where extreme heat and stress are constants. The alloys ensure reliability and performance, enabling safe and efficient flight.
Automotive
Automotive applications include turbochargers and exhaust systems. These components must withstand high thermal loads and corrosive environments. High-temperature alloys extend the lifespan of these parts, contributing to enhanced vehicle performance.
Energy Sector
In power generation, high-temperature alloys are crucial for gas turbines and nuclear reactors. Their ability to operate efficiently in extreme conditions improves energy output and reduces maintenance costs, driving sustainability.
How High-Temperature Alloys Differ From Conventional Alloys
High-temperature alloys outshine conventional materials in performance and reliability. Their unique properties allow them to excel where traditional alloys fail.
Performance Under Stress
While conventional alloys may deform or lose strength at high temperatures, high-temperature alloys maintain structural integrity. This makes them ideal for applications involving extreme thermal and mechanical stress.
Corrosion Resistance
High-temperature alloys offer superior resistance to oxidation and chemical degradation. This property is essential in environments like chemical processing plants, where exposure to corrosive agents is common.
Economic Implications
Although high-temperature alloys are more expensive upfront, their durability and efficiency provide significant cost savings over time. Reduced maintenance and longer service life offset the initial investment, making them a cost-effective choice.
Critical Properties That Enable Enhanced Performance
High-temperature alloys derive their remarkable capabilities from specific properties engineered through meticulous design.
Heat Resistance
These alloys resist softening and deformation at elevated temperatures, making them indispensable for high-heat environments. Applications like jet engines rely on this characteristic to function efficiently under extreme conditions.
Corrosion Resistance
Oxidation and chemical stability are achieved through the inclusion of chromium and aluminum. These elements form protective oxide layers that shield the material from degradation, ensuring longevity.
Mechanical Strength
The inherent strength of high-temperature alloys comes from their microstructure. Elements like molybdenum and tungsten reinforce the matrix, enabling the material to endure mechanical loads without failure.
Manufacturing and Processing Techniques
The production and processing of high-temperature alloys involve intricate methods to achieve their unique properties. These techniques ensure that the alloys meet the stringent demands of their applications.
Casting and Forging
Casting and forging are traditional methods for shaping high-temperature alloys. Precision casting, such as investment casting, creates complex shapes with excellent surface finish, vital for aerospace components like turbine blades. Forging improves mechanical properties by refining the grain structure, which enhances strength and durability.
Additive Manufacturing
Additive manufacturing, commonly known as 3D printing, has revolutionized the production of high-temperature alloys. By using powder bed fusion and laser sintering, engineers can create intricate designs that were previously impossible. This method minimizes material waste and allows for rapid prototyping, making it ideal for custom applications in industries like aerospace and healthcare.
Heat Treatment Processes
Heat treatment plays a crucial role in optimizing the properties of high-temperature alloys. Processes like solution annealing, aging, and stress relief enhance strength, hardness, and corrosion resistance. Heat treatment also tailors the microstructure, enabling the material to perform exceptionally under high thermal and mechanical stress.
Advanced Research in High-Temperature Alloys
Ongoing research in high-temperature alloys focuses on pushing the boundaries of their performance. New developments are redefining what these materials can achieve.
High-Entropy Alloys
High-entropy alloys (HEAs) are at the forefront of material science. Unlike traditional alloys, which are based on one or two primary elements, HEAs consist of multiple principal elements in near-equal proportions. This unique composition results in exceptional mechanical properties, including high strength and thermal stability.
Computational Modeling
Advancements in computational modeling and artificial intelligence (AI) enable researchers to predict alloy behavior under various conditions. By simulating stress, temperature, and corrosion, scientists can design alloys with optimal properties faster and at a lower cost.
Nano-Engineering
Nano-engineering techniques are being explored to enhance the performance of high-temperature alloys. By manipulating the material’s structure at the atomic level, researchers aim to improve wear resistance, reduce grain growth, and increase creep strength, making these alloys even more versatile.
The Role of High-Temperature Alloys in Sustainability
High-temperature alloys contribute significantly to sustainability by improving efficiency and reducing waste across various sectors.
Enhancing Energy Efficiency
In power generation, high-temperature alloys enable turbines to operate at higher temperatures, increasing efficiency. This reduces fuel consumption and greenhouse gas emissions, aligning with global sustainability goals.
Longevity and Durability
The durability of high-temperature alloys minimizes the need for frequent replacements. This longevity reduces material waste and maintenance costs, making them an environmentally friendly choice for industries like automotive and aerospace.
Recycling and Reuse
Efforts to recycle high-temperature alloys are gaining traction. By reclaiming valuable elements like nickel and cobalt, manufacturers can reduce reliance on mining and lower the environmental impact of production processes.
Challenges in Using High-Temperature Alloys
Despite their remarkable properties, high-temperature alloys face challenges that can limit their application or increase costs.
Cost Considerations
The production of high-temperature alloys involves expensive raw materials and complex manufacturing processes. While their performance justifies the cost in critical applications, affordability remains a challenge for widespread use.
Processing Difficulties
The high melting points and complex compositions of these alloys make processing challenging. Specialized equipment and techniques are required, adding to production costs and time.
Potential Limitations
High-temperature alloys are not a one-size-fits-all solution. Their properties must be carefully matched to the application, as they may exhibit limitations in environments outside their optimal performance range, such as extreme chemical exposure.
Case Studies
Real-world applications of high-temperature alloys showcase their transformative impact across industries.
Aerospace Success Stories
In the aerospace sector, nickel-based superalloys like Inconel 718 are used in jet engine turbines. These alloys withstand temperatures exceeding 1,000°C while maintaining structural integrity, enabling efficient and reliable propulsion.
Automotive Advancements
High-temperature alloys have revolutionized automotive engineering, particularly in racing. For example, titanium aluminides are used in exhaust valves to reduce weight and enhance performance, allowing race cars to achieve higher speeds with greater efficiency.
Energy Sector Breakthroughs
In the energy sector, high-temperature alloys are integral to the efficiency of gas turbines. Alloys like Hastelloy improve the performance of turbine blades, enabling power plants to generate more electricity with less fuel.
The Economic Impact of High-Temperature Alloys
The economic implications of high-temperature alloys are profound, influencing industries and global markets.
Cost-Benefit Analysis
While high-temperature alloys come with a higher initial cost, their durability and efficiency lead to long-term savings. Reduced maintenance, extended lifespans, and enhanced performance outweigh the upfront investment.
Driving Innovation
The versatility of high-temperature alloys drives innovation in critical industries. By enabling cutting-edge designs and applications, these materials open new markets and create economic opportunities.
Strategic Importance
High-temperature alloys are vital for industries critical to national security and technological leadership, such as aerospace and defense. Investing in their development ensures a competitive edge in these sectors.
Future Prospects
The future of high-temperature alloys is bright, with emerging technologies and applications set to expand their capabilities.
Innovations in Alloy Design
Researchers are exploring novel alloy compositions to further improve performance. High-entropy alloys and other experimental materials promise breakthroughs in strength, durability, and thermal resistance.
Emerging Applications
New applications in fields like space exploration and advanced manufacturing are on the horizon. High-temperature alloys will play a pivotal role in enabling technologies like hypersonic travel and energy storage.
Overcoming Current Limitations
Efforts to address the cost and processing challenges of high-temperature alloys are ongoing. Advances in manufacturing techniques, such as additive manufacturing, are expected to make these materials more accessible.
Comparison of Leading High-Temperature Alloys
Different high-temperature alloys offer unique benefits, making them suitable for specific applications.
Inconel Alloys
Inconel alloys are known for their exceptional oxidation and corrosion resistance. They are widely used in jet engines and industrial furnaces where high thermal stability is essential.
Hastelloy Alloys
Hastelloy is prized for its resistance to chemical corrosion, making it ideal for applications in chemical processing and marine environments.
Titanium Aluminides
Titanium aluminides offer a balance of lightweight properties and high-temperature performance, making them suitable for aerospace and automotive applications.
Practical Tips for Engineers and Technicians
Selecting and maintaining high-temperature alloys requires expertise and careful planning.
Choosing the Right Alloy
Understand the specific demands of your application, including temperature, stress, and environmental conditions. Consult material experts to select an alloy that meets your needs.
Maintenance and Inspection
Regular maintenance and inspection are essential to ensure the longevity of high-temperature alloys. Monitor for signs of wear, corrosion, or thermal degradation, and address issues promptly.
Partnering with Experts
Collaborate with trusted suppliers and manufacturers to access high-quality alloys and technical support. Their expertise can help optimize performance and minimize costs.
Conclusion
High-temperature alloys are indispensable for industries that demand exceptional performance under extreme conditions. From aerospace to energy, these materials enable innovation and sustainability. As technology advances, their role will only grow, shaping the future of engineering and manufacturing. To learn more or explore alloy solutions for your projects, reach out to industry experts and unlock the potential of high-temperature alloys today.
FAQ
What are high-temperature alloys made of?
They are composed of elements like nickel, cobalt, and iron, with additional elements like chromium and molybdenum for enhanced properties.
What industries use high-temperature alloys?
They are widely used in aerospace, automotive, energy, and chemical processing industries.
Are high-temperature alloys recyclable?
Yes, many high-temperature alloys can be recycled to recover valuable elements like nickel and cobalt.
What is the biggest challenge in using high-temperature alloys?
Their high cost and processing complexity are significant challenges, although their performance often justifies the investment.
What are the future trends for high-temperature alloys?
Advancements in alloy design, additive manufacturing, and emerging applications like space exploration will shape the future of these materials.