Introduction to High-Temperature Alloys
Understanding the Need for Stability in Extreme Conditions
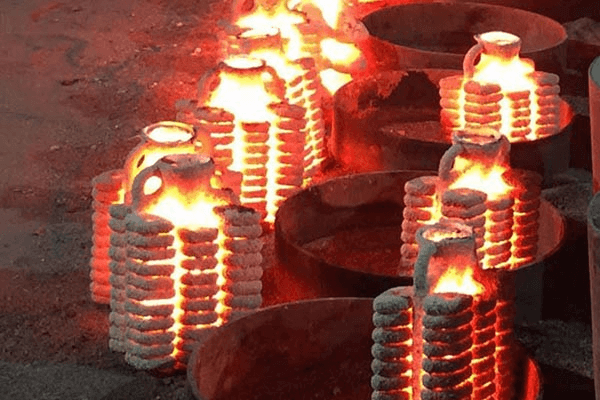
High-temperature alloys support many advanced industries that demand materials capable of enduring searing environments without breaking down. Imagine components placed near roaring jet engines or industrial furnaces where heat and stress constantly threaten to deform ordinary metals. You might be wondering: what makes these alloys stand apart from standard metals, and why do so many manufacturers insist on premium grades? It comes down to their specially engineered compositions and carefully controlled production methods. These alloys resist thermal creep, scaling, and oxidation in ways that lesser materials cannot. By maintaining their strength, shape, and properties at temperatures where others fail, premium high-temperature alloys deliver predictability and reliability. This is crucial since even a slight variance in performance can translate into costly downtime, safety concerns, or lower product quality. When organizations depend on consistent results, they turn to these specialized alloys, knowing they can operate under punishing conditions day after day. Here’s the deal: premium high-temperature alloys are engineered not just to survive but to help systems thrive when the going gets hot. That combination of strength, durability, and consistency empowers manufacturers to confidently push operational limits without compromising quality or safety.
The Importance of Consistency in High-Performance Industries
Why Material Reliability Matters to Critical Sectors
High-performance industries like aerospace, petrochemical, and power generation hinge on the unwavering quality of their components. Technicians, engineers, and managers need to know that each part will perform exactly as intended, no matter the temperature swings or mechanical stresses. You might be wondering: why does it matter if materials remain consistent throughout their operating life? Consider a turbine blade inside a jet engine. If that blade warps or weakens unpredictably at high temperatures, the entire system’s efficiency and safety come into question. Premium high-temperature alloys address this by providing materials that remain stable under extremes of heat, pressure, and chemical exposure. This stability directly impacts the reliability of an aircraft, a refinery, or a power plant.
Here’s the deal: a single inconsistent component can halt an entire production line, trigger expensive maintenance, or lead to lost revenue. Industries operating at these intensities cannot afford to take chances. They need materials that hold shape, don’t degrade prematurely, and maintain performance across long operational cycles. When high-temperature alloys prove consistent, they reduce downtime and maintenance costs. This reliability translates to safer working conditions for staff, improved product quality, and less risk of catastrophic failures.
In a competitive global market, maintaining high standards of quality and consistency becomes a key differentiator. Companies that invest in premium alloys show their commitment to delivering exceptional products. When clients know a supplier consistently provides materials that perform in harsh settings, trust grows. Guess what: trust and reliability open doors to new business opportunities, long-term contracts, and a solid reputation in the marketplace. In essence, consistency isn’t just a technical attribute; it’s a strategic advantage that keeps companies thriving in tough, high-performance arenas.
Key Properties of Premium High-Temperature Alloys
Strength, Stability, and Resistance to Harsh Elements
Premium high-temperature alloys exhibit several defining attributes that make them dependable in extreme operational conditions. You might be thinking: what properties ensure their stability and reliability even under punishing heat and pressure? First, these alloys maintain superior tensile strength at high temperatures. This strength prevents deformation and structural collapse when components experience tremendous mechanical stresses over prolonged periods.
Here’s the deal: oxidation and corrosion resistance also set premium alloys apart. Standard metals often form unwanted scales or weaken when exposed to high-temperature oxidizing atmospheres or harsh chemicals. Premium alloys incorporate elements like chromium, nickel, and cobalt to form stable oxides on their surfaces, effectively shielding underlying metal from further damage. This robust protective layer ensures the alloy’s core properties remain intact.
Another key property involves thermal stability. Premium alloys resist grain growth and microstructural changes that might otherwise lead to brittleness or weakening. Consistent grain structures ensure uniform strength distribution and maintain predictable mechanical behavior. You might be wondering: how does this help in real-world applications? Consider components in a gas turbine engine. They must withstand repeated heating and cooling cycles without losing shape or integrity. Premium alloys’ inherent stability under thermal cycling fosters reliability and efficiency.
Moreover, these alloys maintain exceptional creep resistance. Over time, materials under constant stress at elevated temperatures may slowly deform, compromising the system’s performance. Premium alloys delay such creep, ensuring dimensional accuracy even after thousands of hours in operation. This translates to longer service intervals, reduced maintenance needs, and fewer costly replacements. Ultimately, these key properties—tensile strength, corrosion resistance, thermal stability, and creep resistance—function as the backbone that makes premium high-temperature alloys indispensable in demanding industrial scenarios.
Comparing Premium vs. Standard Alloys
Performance Differences and Long-Term Value
When comparing premium high-temperature alloys with standard options, the differences become clear. You might be wondering: why pay more for premium materials if standard alloys seem sufficient at first glance? It’s important to understand that while standard alloys can handle moderate heat and stress, they often falter when pushed closer to their operating limits. Components made from regular metals may deform, crack, or oxidize aggressively when exposed to extended high temperatures, leading to unpredictable outcomes and premature failures.
Here’s the deal: premium alloys cost more initially, but they provide significant long-term savings and fewer headaches. These materials maintain their mechanical properties under extreme heat, resisting distortion or breakdown. This stability leads to fewer replacements, less downtime, and reduced maintenance costs over the product’s lifecycle. Consider an industrial furnace that operates around the clock at high temperatures. Using standard alloys might lead to frequent shutdowns for repairs, lost productivity, and potential safety issues. Premium alloys, on the other hand, ensure the furnace runs more reliably, maintaining efficiency and cutting operating expenses.
Another stark difference lies in process control. Premium alloys undergo strict compositional control and rigorous testing. Manufacturers adhere to stringent quality standards to ensure the alloy’s chemistry remains consistent from batch to batch. This means buyers receive a predictable product every time. By contrast, standard alloys may come with greater variability, making performance harder to forecast. You might be asking: why risk unpredictable outcomes when the stakes are high? In the long run, premium alloys prove their worth by delivering stable, reliable service that justifies their initial investment. Simply put, premium beats standard whenever consistency, safety, and reliability are top priorities.
Metallurgical Composition and Control
How Elemental Precision Defines Superior Performance
High-temperature alloy composition isn’t guesswork; it’s a finely tuned science. You might be wondering: what exact blend of elements makes these premium alloys so exceptional? Engineers carefully select elements like nickel, chromium, cobalt, and molybdenum to achieve a desired balance of mechanical strength, oxidation resistance, and thermal stability. The precise proportions matter greatly. Even a slight variation can alter how an alloy responds to stress or reacts under intense heat.
Here’s the deal: manufacturing premium alloys often involves sophisticated melting and refining methods, such as vacuum induction melting, that minimize impurities and ensure a uniform distribution of alloying elements. These processes control the alloy’s grain structure and reduce unwanted segregation or defects that could weaken its properties. This meticulous attention to detail transforms a pile of raw materials into a flawless material whose characteristics remain consistent throughout its cross-section.
Advanced testing procedures play a crucial role. Manufacturers use tools like spectrometers and electron microscopes to verify chemical composition, microstructural uniformity, and overall quality. By adhering to strict metallurgical standards, producers guarantee that each batch of premium alloy meets or exceeds the specified mechanical and chemical properties. You might be asking: why is this so critical? Because when a component must endure scorching heat and relentless mechanical loads, any inconsistency in composition might lead to premature failure.
This unwavering commitment to metallurgical control distinguishes premium alloys from ordinary ones. With advanced production techniques and rigorous quality checks, the resulting product delivers dependable performance. In essence, the alloy’s composition and the engineering behind it form the foundation for consistent results. Companies can trust these materials to withstand the toughest conditions without surprise failures or unstable behavior.
Manufacturing Processes that Influence Consistency
Precision and Quality Control at Every Production Stage
Premium high-temperature alloys don’t simply appear; they emerge from meticulous manufacturing processes designed to eliminate guesswork. You might be wondering: how do these processes ensure every piece of alloy meets the toughest industry standards? The journey begins with careful selection of raw materials that adhere to strict composition guidelines. Manufacturers then rely on processes like precision casting and forging, which shape the alloy into components with uniform grain structures. This approach reduces internal stresses and helps maintain consistent mechanical properties.
Here’s the deal: heat treatment steps such as solution annealing and precipitation hardening further stabilize microstructures. These controlled thermal treatments refine grain boundaries, improving toughness and minimizing the risk of creep and fatigue damage. Quality control measures like ultrasonic testing, X-ray inspection, and metallographic examinations catch any internal flaws, voids, or inconsistencies before they become problematic. Even a microscopic crack can grow into a major defect if unnoticed, so this level of scrutiny is crucial.
On top of that, powder metallurgy techniques help produce alloys with incredibly tight composition tolerances. Powder-based processes distribute alloying elements evenly, reducing hotspots or inconsistent regions. This leads to components that behave predictably, even under severe service conditions. You might be asking: does this attention to detail really matter? Absolutely. Industries that push materials to their limits can’t afford unexpected breakdowns. By investing in careful manufacturing steps, producers ensure the finished alloy consistently meets demanding performance standards.
Ultimately, these manufacturing methods form a chain of carefully managed steps. Any weakness in that chain threatens the final product’s quality. Skilled technicians, engineers, and quality control teams collaborate at every stage. This orchestration of expertise and technology ensures each component rolling off the production line can stand confidently in extreme environments without letting customers down.
Addressing Common Challenges at High Temperatures
Overcoming Stress, Oxidation, and Structural Degradation
When materials face blazing temperatures, they encounter a host of issues. You might be wondering: what challenges arise, and how do premium high-temperature alloys beat them? Let’s start with stress rupture and creep resistance. Under continuous load, metals can slowly deform over time. For standard alloys, this can mean parts lose shape or break unexpectedly. Premium alloys, however, combat creep through carefully balanced compositions and heat treatments that maintain structural integrity over long service intervals.
Here’s the deal: oxidation and corrosion present another hurdle. At high temperatures, standard metals form thick, flaky scales that eat away at their strength. Premium alloys incorporate elements like chromium and aluminum, which form stable oxide layers that shield the underlying metal. This protective barrier prevents further degradation and keeps components functioning reliably. The result is a cleaner, more stable surface that doesn’t chip or flake off easily.
Thermal fatigue also tests a material’s mettle. Rapid heating and cooling cycles induce stresses that eventually lead to cracks. Premium alloys excel at handling these cycles, resisting the formation of microcracks that would otherwise grow over time. This is critical in applications like gas turbine blades, which constantly experience temperature swings. By maintaining structural stability under thermal cycling, these alloys help ensure consistent performance.
You might be asking: is there more? Absolutely. Grain growth at high temperatures can weaken an alloy’s mechanical properties. Premium alloys resist this phenomenon, retaining fine, stable grains that translate into better strength and longer service life. In sum, premium alloys tackle high-temperature challenges head-on, offering solutions that keep systems running smoothly. Their ability to resist creep, oxidation, thermal fatigue, and grain growth sets them apart, ensuring consistent results in the hottest, toughest conditions imaginable.
Ensuring Product Uniformity Through Quality Assurance
Testing, Certifications, and Traceability
Quality assurance processes play a pivotal role in guaranteeing that every piece of premium high-temperature alloy meets the same exacting standards. You might be wondering: how do manufacturers verify that each batch remains consistent? Non-destructive testing methods like ultrasonic, X-ray, or magnetic particle inspections catch hidden flaws inside the material. These tests reveal internal cracks, voids, or inclusions that could compromise performance. By identifying and removing defective parts early, producers prevent substandard products from reaching the market.
Here’s the deal: standardized certifications provide confidence. Industry-recognized credentials like ISO or AS9100 confirm that a company’s production methods, quality controls, and documentation systems meet globally respected benchmarks. Customers gain assurance that the alloys they purchase have passed stringent evaluations. This trust in certified suppliers reduces uncertainty and risk, making it easier to select reliable partners.
Traceability is another crucial element. Premium alloy manufacturers maintain detailed records linking every component to its production batch, raw materials, and testing data. If an issue arises in the field, engineers can quickly trace the component’s origin, identify potential problems in the manufacturing process, and rectify them. This transparency not only ensures higher consistency but also demonstrates accountability.
You might be asking: can these measures truly guarantee uniformity? While no system is perfect, robust quality assurance frameworks drastically reduce variability. They ensure that what you specify is what you get, time after time. For industries demanding unwavering reliability, these procedures form the backbone of trust. Premium high-temperature alloys aren’t just about engineered perfection at the atomic level; they also rely on rigorous testing, certification, and traceability that signal a promise of consistent quality.
Real-World Applications and Case Studies
From Aerospace Turbines to Petrochemical Reactors
Premium high-temperature alloys thrive in settings where ordinary metals buckle under pressure. You might be wondering: where do these alloys prove their worth? Consider aerospace turbine blades spinning at thousands of rotations per minute in scorching jet engines. Premium alloys ensure these blades maintain shape and strength through countless high-speed flights. The result is consistent thrust, improved fuel efficiency, and fewer unexpected maintenance stops.
Here’s the deal: petrochemical reactors also benefit. Harsh chemicals, extreme heat, and corrosive environments punish materials. Premium alloys hold up, preventing leaks and cracks that might shut down production lines or risk operator safety. The payoff: stable output, reliable operation, and minimized downtime.
Automotive industries rely on these alloys for turbochargers and exhaust systems that face fluctuating heat loads. By resisting thermal fatigue, premium alloys enable stable engine performance, better emissions control, and an extended component lifespan. This keeps vehicles running smoothly over time, reducing environmental impact and saving money on repairs.
Power generation turbines represent another classic use case. Reliable alloys help maintain constant power output, preventing corrosion and scaling that degrade efficiency. This leads to stable energy production and fewer costly outages. You might be asking: do these applications scale to other industries? Absolutely. From high-temperature furnaces in manufacturing plants to specialized medical equipment that endures sterilization cycles, premium alloys provide a foundation of reliability. They foster confidence in complex systems, allowing businesses to operate closer to their limits without introducing unnecessary risk. When a component needs to last longer, perform better, and deliver consistent results in punishing conditions, premium alloys answer the call.
Selecting the Right Alloy for Specific Applications
Matching Material Properties to Operational Needs
Choosing the proper high-temperature alloy involves more than picking a name from a catalog. You might be wondering: how do engineers ensure the material precisely meets an application’s demands? They start by evaluating the required temperature range, mechanical loads, and environmental factors. Different alloys excel in different areas. Some offer outstanding creep resistance at slightly lower temperatures, while others maintain stability even beyond 1000°C. The goal is to match alloy capabilities with the specific challenges a component will face.
Here’s the deal: working closely with suppliers and experts makes a huge difference. These professionals guide engineers through available grades, highlight performance trade-offs, and help interpret datasheets. A supplier’s technical support team can recommend alloys suited for gas turbine blades, for instance, or for furnace fixtures exposed to corrosive gases. By selecting an alloy tailored to the conditions, companies minimize risk and maximize reliability.
Cost considerations also come into play. Premium alloys are investments. But when balanced against reduced maintenance, fewer replacements, and extended service life, they often prove more economical in the long run. Engineers must consider the total lifecycle cost rather than just the upfront price. This holistic perspective encourages the selection of materials that deliver consistent results year after year.
You might be asking: can a single alloy handle every scenario? Rarely. Different applications call for nuanced solutions. The best approach involves careful analysis, clear communication with suppliers, and thorough testing. By understanding the operating environment and making informed choices, organizations ensure they get the most from their premium alloys. This thoughtful selection process ensures maximum consistency, safety, and efficiency in even the harshest conditions.
Economic Impact of Using Premium Alloys
Balancing Upfront Costs and Long-Term Gains
Investing in premium high-temperature alloys is a strategic decision that often pays dividends over the long haul. You might be wondering: why spend more at the start when budget constraints loom? Consider the bigger picture. Premium alloys slash downtime due to unexpected component failures, reduce costly repairs, and prevent production halts. Over the lifespan of a complex system, these savings can outweigh the initial expense.
Here’s the deal: imagine a power plant turbine made from standard alloys that routinely requires maintenance shutdowns. Each shutdown costs money, disrupts supply, and may even damage the operator’s reputation. Now picture using premium alloys that maintain stable performance under identical conditions. Maintenance intervals lengthen, parts last longer, and fewer interventions are needed. All this leads to higher productivity and smoother operations.
Additionally, premium alloys can boost energy efficiency. Stable components help machines run at optimal conditions, reducing fuel consumption and emissions. This can translate into lower operational costs and environmental benefits. When investors, stakeholders, or regulatory bodies look at a company’s long-term sustainability, decisions that favor premium alloys stand out as wise moves.
You might be asking: what about smaller businesses on tight budgets? Even they reap benefits. Smaller operations must be particularly careful with resources. By choosing premium alloys, they establish stability, reduce risk, and ultimately improve their bottom line. Over time, the premium investment becomes a strategic shield against unpredictable costs. In sum, premium alloys represent more than just a material upgrade. They embody a forward-looking approach that values reliability, reduces total expenses, and builds a platform for steady growth.
Environmental Considerations and Sustainability
Durable Materials that Minimize Waste
Sustainability isn’t just a buzzword; it’s a growing priority for global industries. You might be wondering: how do premium high-temperature alloys factor into environmental goals? One key advantage lies in their durability. If components last longer and require fewer replacements, the need for constant new material production diminishes. This reduces resource consumption and lowers the carbon footprint associated with manufacturing and transporting new parts.
Here’s the deal: efficient alloys that maintain stable performance also enhance energy usage. Whether in power generation, automotive engines, or industrial furnaces, stable materials help machines run at peak efficiency. Improved efficiency conserves fuel, trims emissions, and aligns with sustainability targets. Over time, businesses that embrace premium alloys can highlight their environmental stewardship, appealing to customers who value green credentials.
Another factor involves material recyclability. Many premium alloys retain their properties even after multiple recycling cycles. This closed-loop approach reduces waste and the need for mining raw materials. As environmental regulations tighten, the ability to repurpose materials responsibly becomes an advantage. By turning to alloys designed for longevity and stability, companies can claim a more sustainable approach to industrial operations.
You might be asking: does this actually matter to bottom lines? Increasingly, yes. Customers and investors often prefer businesses that prioritize sustainability. Regulatory bodies may reward companies that meet environmental standards with easier permitting or incentives. With premium alloys, organizations build reliability into their operations while simultaneously contributing to broader eco-friendly initiatives. Sustainability, cost savings, and consistent performance can coexist. Premium alloys serve as a tool that helps industries achieve that delicate balance.
Working with Trusted Suppliers and Partners
Building Relationships for Long-Term Success
Selecting premium high-temperature alloys isn’t a one-time transaction. You might be wondering: why focus on supplier relationships? Trusted suppliers bring more than just materials to the table. They offer technical expertise, after-sales support, and in-depth understanding of evolving industry needs. Partnering with such suppliers ensures that buyers always have someone to turn to for guidance, troubleshooting, and advice.
Here’s the deal: suppliers with strong track records often hold certifications and maintain strict quality assurance programs. They can produce consistent alloys that meet specified requirements time after time. This reduces uncertainty and frees buyers to focus on innovation and growth rather than worrying about material quality. Over the long term, stable supplier relationships streamline procurement processes and reduce administrative burdens.
Good suppliers also keep pace with technological advances. They may introduce new alloy grades or manufacturing techniques that improve performance and reduce costs. This ongoing collaboration helps customers stay ahead of the competition, adapt to changing market conditions, and solve emerging challenges. You might be asking: how do you find these suppliers? Start by checking certifications, seeking referrals, and evaluating their responsiveness and technical capabilities. Clear communication and transparency are critical. When both parties understand each other’s goals, the partnership can thrive.
Ultimately, working with reputable partners transforms alloy procurement from a transactional process into a strategic advantage. The right supplier relationship not only delivers top-quality alloys but also enhances a company’s ability to achieve consistent results, reduce risks, and build a more resilient business model.
Future Trends in High-Temperature Alloy Development
Innovations Paving the Way for Next-Gen Materials
The world doesn’t stand still, and neither do premium high-temperature alloys. You might be wondering: what’s on the horizon as industries demand even more from these materials? Researchers and engineers continue pushing boundaries. They explore new alloy chemistries that offer exceptional strength-to-weight ratios or withstand even higher temperatures without losing stability. Advanced coatings, nanomaterials, and composite approaches promise next-level corrosion resistance and longevity.
Here’s the deal: additive manufacturing, also known as 3D printing, plays a growing role. By layer-by-layer building complex alloy components, manufacturers gain unprecedented design flexibility. This method can optimize grain structures, reduce waste, and speed up production. As these techniques mature, they’ll likely lead to customized alloys that fit specific applications perfectly, further improving consistency.
Another emerging trend involves predictive maintenance. With sensors embedded in critical components, operators can monitor material performance in real time, identifying potential issues before they escalate. Imagine knowing precisely when a turbine blade approaches its safe service limit and scheduling maintenance accordingly. This proactive approach ensures consistent results and longer component life.
You might be asking: how does sustainability factor in? Researchers also focus on developing eco-friendly alloys that reduce the use of critical elements or energy-intensive production methods. These new materials must deliver top-notch performance while aligning with global environmental goals.
As these innovations advance, premium alloys will only become more reliable and accessible. Buyers who stay informed and engage with the latest developments position themselves at the leading edge of their industries. In the future, premium high-temperature alloys may not just meet expectations—they may redefine them entirely.
Conclusion and Key Takeaways
Making Informed Choices for Stable, Reliable Performance
In environments where heat rises and conditions challenge every component, premium high-temperature alloys emerge as champions of consistency. They deliver reliable performance, resisting creep, oxidation, and structural changes that could derail critical operations. You might be wondering: why invest in these alloys now? The answer is straightforward. Premium alloys reduce long-term costs, boost efficiency, and enhance sustainability. They protect reputations by preventing catastrophic failures and maintaining stable output. They also give companies a competitive edge, reassuring clients that every product, turbine blade, or reactor component will function as intended. With stringent quality controls, meticulous composition, and advanced manufacturing methods, premium high-temperature alloys reflect engineering excellence at its peak.
By embracing these materials, organizations take a proactive stance against unpredictable outcomes. They build trust with customers, streamline processes, and cultivate safer, more efficient workplaces. In short, these alloys aren’t just about surviving intense conditions. They’re about thriving in them.
Frequently Asked Questions (FAQ)
What industries commonly use premium high-temperature alloys?
Aerospace, power generation, petrochemical, and automotive sectors frequently rely on these alloys. Any industry facing prolonged exposure to extreme heat and stress benefits from their stability, including manufacturing operations where furnace components, turbine blades, and other critical parts must remain dependable under punishing conditions.
How do premium alloys differ from standard alloys?
Premium alloys undergo strict composition control and advanced processing methods to ensure superior properties at high temperatures. They maintain their mechanical strength, resist oxidation, and remain dimensionally stable in ways standard alloys cannot match, leading to more consistent performance over their service life.
Are premium alloys worth the higher initial cost?
Yes. Though premium alloys often cost more upfront, the long-term savings are substantial. Their durability reduces downtime, maintenance expenses, and component replacements. This, in turn, lowers total operating costs and enhances productivity, making them a strategic investment.
How are these alloys tested for quality and consistency?
Manufacturers employ non-destructive testing methods like ultrasonic, X-ray, and magnetic particle inspections. They also rely on standardized certifications and detailed documentation to track each batch’s properties. This level of scrutiny ensures that every product meets or exceeds specified quality standards.
Can premium alloys improve environmental sustainability?
Yes. Longer-lasting components mean fewer replacements, which reduces resource consumption. Premium alloys often enable machines to run more efficiently, cutting fuel use and emissions. Additionally, many of these alloys are recyclable, aligning with sustainable industry practices.
How do I choose the right alloy for my application?
Begin by assessing your operating conditions—maximum temperature, chemical exposure, stress levels. Consult with suppliers or technical experts who can recommend specific alloy grades. Consider long-term performance and lifecycle costs rather than focusing solely on initial price.
Are there emerging trends in high-temperature alloy development?
Absolutely. Researchers explore advanced coatings, composites, additive manufacturing, and eco-friendly production methods. Innovations aim to enhance creep resistance, improve corrosion protection, and refine grain structures. The goal is to push the limits of reliability and efficiency even further.
What role do suppliers play in ensuring consistent results?
Trusted suppliers offer technical support, certifications, and quality controls. They maintain stable alloy compositions and provide ongoing guidance as your operational needs evolve. This partnership ensures that you receive top-grade products and expert advice whenever required.
Can these alloys handle rapid temperature changes?
Yes. Premium alloys resist thermal fatigue and maintain structural integrity even when exposed to cyclical heating and cooling. This stability prevents cracking or warping, ensuring that critical components last longer and perform more reliably under fluctuating conditions.
How do premium alloys enhance operational safety?
Consistent materials reduce the risk of unexpected failures that can lead to accidents, production halts, or equipment damage. By improving reliability and predictability, premium alloys contribute to a safer working environment and more stable operational workflows.