The growth of light alloy foundry systems has been largely driven by recent developments in structural aluminum castings. These advancements have not only helped improve the efficiency of the foundry process but have also opened new avenues for growth in various industries, such as automotive, aerospace, and manufacturing. By understanding the connection between structural aluminum castings and the expansion of light alloy foundry systems, businesses can better position themselves in an increasingly competitive market.
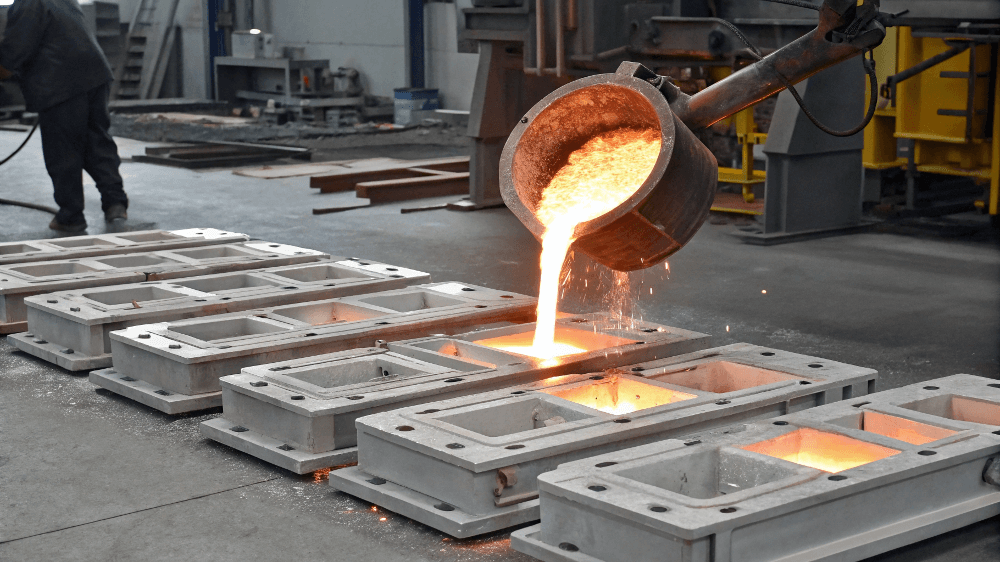
1. How Have Recent Developments in Structural Aluminum Castings Impacted the Industry?
Over the past few years, the aluminum casting industry has witnessed significant innovations that have reshaped its capabilities. What’s the real story? Structural aluminum castings have become more cost-effective, precise, and durable, thanks to advancements in manufacturing technology and material science. These developments have enabled foundries to produce lighter, stronger components at a faster rate, addressing the growing demand for materials that can withstand the rigorous demands of industries such as automotive and aerospace.
The integration of newer casting techniques, such as high-pressure die casting (HPDC) and sand casting, has streamlined production processes, reducing both costs and lead times. For instance, in the automotive industry, manufacturers have adopted aluminum castings for engine blocks, transmission housings, and chassis components, leading to substantial weight reductions. This has directly contributed to improving fuel efficiency and overall vehicle performance.
Moreover, innovations in aluminum alloys have enhanced casting quality, improving strength, corrosion resistance, and fatigue resistance. This has made aluminum a preferred material for structural components, particularly in sectors where durability and performance are critical. Ready for the good part? The increased use of aluminum in structural applications has boosted the demand for aluminum castings, further spurring growth in the light alloy foundry sector.
Table 1: Key Advantages of Structural Aluminum Castings
Feature | Impact on Industry | Example Applications |
---|---|---|
Strength-to-weight ratio | Increased efficiency and performance | Aerospace components, automotive frames |
Durability and corrosion resistance | Enhanced longevity and reliability | Marine equipment, automotive parts |
Cost-effectiveness | Lower production costs | High-volume manufacturing processes |
2. What Are the Key Drivers of Growth in the Light Alloy Foundry System?
The light alloy foundry system is growing at an accelerated pace, and several key drivers are fueling this expansion. What’s driving this change? One of the primary factors is the increasing demand for lightweight materials, especially in industries like automotive and aerospace, where weight reduction translates directly into improved fuel efficiency and performance.
Aluminum, magnesium, and other light alloys are becoming essential in producing components that require high strength but minimal weight. In the automotive sector, the shift towards electric vehicles (EVs) has further intensified the need for lightweight materials to offset battery weight and improve energy efficiency. This is where structural aluminum castings come into play, as they are perfect for these applications due to their strength-to-weight ratio and cost-effectiveness.
Another significant driver is the advancement in casting technologies. For example, the adoption of computer-aided design (CAD) and computer-aided manufacturing (CAM) systems has led to more precise and efficient casting processes. These technologies have reduced material wastage and improved the overall quality of cast components, increasing the appeal of light alloys.
But here’s the kicker: environmental sustainability is playing an increasingly important role. As manufacturers face growing pressure to reduce their carbon footprints, the use of light alloys—particularly recycled aluminum—has become a more sustainable option. The environmental benefits of using recycled aluminum, which reduces energy consumption and greenhouse gas emissions compared to primary aluminum production, are not only contributing to the industry’s growth but also aligning with global sustainability goals.
Table 2: Drivers of Growth in Light Alloy Foundry Systems
Driver | Impact on Growth | Example Sector |
---|---|---|
Demand for lightweight materials | Increased adoption in automotive and aerospace industries | Electric vehicles, aircraft parts |
Technological advancements | Enhanced casting precision and efficiency | Aerospace, automotive industries |
Environmental sustainability | Reduced carbon footprint, energy savings | Recycling initiatives, eco-friendly production |
3. What Are the Key Advantages of Structural Aluminum for Foundries?
Structural aluminum offers several advantages that make it an ideal material for foundries, especially in industries requiring both strength and lightness. What’s the real story? Aluminum has a unique combination of properties that make it invaluable for a variety of applications.
One of the most significant advantages is aluminum’s excellent strength-to-weight ratio. This means that aluminum can deliver the required strength for structural components while keeping the overall weight low. This is particularly beneficial in industries like automotive, where reducing weight can lead to better fuel efficiency and performance. Structural aluminum is also highly durable and resistant to corrosion, making it ideal for harsh environments.
But here’s where it gets interesting: aluminum castings can be manufactured with a high degree of precision, reducing the need for additional machining and improving overall production efficiency. As a result, foundries can reduce costs and lead times, making aluminum castings a more attractive option for manufacturers looking to optimize their production processes.
Another key benefit is the recyclability of aluminum. Aluminum can be recycled indefinitely without losing its properties, making it a sustainable material choice. This is a critical factor as businesses look to adopt more eco-friendly manufacturing practices. In fact, recycled aluminum requires only a fraction of the energy used to produce primary aluminum, making it a more sustainable option for the environment.
Table 3: Advantages of Structural Aluminum
Advantage | Impact on Foundry System | Example Application |
---|---|---|
Strength-to-weight ratio | Improved performance, fuel efficiency | Automotive chassis, aerospace components |
Durability and corrosion resistance | Long-lasting and reliable components | Marine equipment, construction structures |
Recyclability | Sustainable manufacturing | Aluminum cans, automotive parts |
4. How Have Light Alloy Foundries Evolved in Recent Years?
The evolution of light alloy foundries is a direct response to the growing demand for higher quality, faster production, and more sustainable manufacturing practices. So, what’s changed? In recent years, foundries have incorporated new technologies and optimized processes to keep up with these demands.
One major change is the increased automation of foundry processes. Robots and automated systems are now used to perform tasks such as pouring molten metal, handling molds, and even finishing parts, which reduces human error and increases efficiency. Automation also allows for higher production rates, making foundries more capable of handling large-scale orders with short lead times.
Additionally, the integration of advanced data analytics has significantly improved process control. Foundries are now able to monitor variables such as temperature, pressure, and material composition in real-time, ensuring that the final products meet precise specifications. This level of precision and control reduces defects and scrap rates, resulting in more reliable and cost-effective aluminum castings.
Ready for the good part? The use of 3D printing in foundry operations has also gained traction. 3D-printed molds and patterns enable faster prototyping and more intricate designs that would be difficult or impossible to achieve using traditional methods. This has opened up new opportunities for custom, low-volume casting, allowing foundries to cater to niche markets and specific client needs.
Table 4: Technological Advancements in Foundries
Advancement | Benefit to Foundry System | Example Application |
---|---|---|
Automation | Increased efficiency, reduced labor costs | Casting production, finishing processes |
Data analytics | Improved precision and process control | Quality assurance, defect reduction |
3D printing | Faster prototyping, custom designs | Low-volume production, custom parts |
5. What Is the Current Market Outlook for the Aluminum Casting Industry?
The aluminum casting industry has a bright future, with significant growth projected in the coming years. What’s the real story? Global demand for aluminum castings continues to rise, driven by industries like automotive, aerospace, and construction, all of which are increasingly reliant on lightweight, durable materials.
Market research indicates that the aluminum casting industry is expected to grow at a steady rate, with a particularly strong uptick in demand for aluminum components used in electric vehicles (EVs). As EV adoption continues to accelerate, the need for lightweight materials like aluminum to offset battery weight will grow, providing a substantial boost to the market.
The Asia-Pacific region is poised to be the largest market for aluminum castings, with China being the primary contributor due to its significant automotive and manufacturing sectors. However, North America and Europe are also witnessing substantial growth, particularly in the aerospace and automotive industries. Manufacturers are focusing on enhancing production capacity and optimizing supply chains to meet the rising demand.
But here’s the kicker: aluminum is also gaining popularity in non-traditional sectors, such as renewable energy. Wind turbines, solar panels, and energy storage systems increasingly use aluminum castings, contributing to the expansion of the aluminum casting market. As these industries continue to grow, they will further fuel demand for aluminum casting technologies.
Table 5: Market Outlook for Aluminum Castings
Region | Projected Growth Rate | Key Industry Drivers |
---|---|---|
Asia-Pacific | 6% annually | Automotive, manufacturing |
North America | 4% annually | Aerospace, electric vehicles |
Europe | 5% annually | Automotive, renewable energy |
6. How Is the Adoption of Green Manufacturing Practices Affecting Light Alloy Foundries?
The drive for sustainability is influencing every aspect of modern manufacturing, and light alloy foundries are no exception. Ready for the good part? The adoption of green manufacturing practices is helping these foundries reduce their environmental impact, improve efficiency, and align with global sustainability goals.
One of the most significant green practices in aluminum casting is the increased use of recycled materials. The recycling of aluminum requires only a fraction of the energy needed for primary production, making it a more environmentally friendly option. Additionally, aluminum is infinitely recyclable without losing its properties, making it a sustainable material choice for manufacturers.
What’s the real story? The move towards energy-efficient processes has been another game-changer. New technologies, such as electric furnaces, have replaced traditional gas-powered models, reducing the carbon footprint of the foundry process. These electric furnaces are not only more energy-efficient but also reduce the emission of greenhouse gases, making them an attractive option for companies aiming to meet stringent environmental regulations.
On top of that, light alloy foundries are investing in cleaner technologies to reduce their water consumption, waste generation, and air pollution. These measures contribute to reducing the overall environmental footprint of foundries, which is crucial in today’s market. By adopting greener manufacturing practices, light alloy foundries are able to appeal to environmentally conscious consumers and meet increasingly strict regulatory requirements.
Table 6: Green Manufacturing Practices in Light Alloy Foundries
Practice | Environmental Benefit | Example Application |
---|---|---|
Recycled aluminum | Reduced energy consumption, less waste | Automotive parts, packaging |
Energy-efficient furnaces | Lower carbon footprint, reduced emissions | Aluminum casting processes |
Water and waste management | Reduced resource consumption, minimized pollution | Foundry cooling, casting processes |
7. What Are the Challenges Faced by the Light Alloy Foundry System?
Despite its growth, the light alloy foundry system faces a number of challenges that can hinder its progress. So, what’s holding the industry back? One of the most significant obstacles is the high initial investment required for modernizing casting technologies and upgrading equipment. Automation, robotics, and advanced data analytics systems are expensive to implement, and not all foundries can afford to make the necessary changes. However, those that can make the investment will ultimately see greater returns in the form of increased efficiency, reduced labor costs, and improved product quality.
But here’s the kicker: labor shortages are also a significant issue. The foundry industry relies heavily on skilled workers, but the demand for experienced technicians and engineers is growing faster than the supply. As older workers retire, there is a shortage of younger workers with the necessary skills to operate advanced machinery and manage complex processes. This lack of skilled labor can lead to delays in production and errors in casting, ultimately affecting the bottom line.
Additionally, the light alloy foundry system is not immune to supply chain disruptions. The global nature of the aluminum market means that foundries are vulnerable to fluctuations in raw material prices and delays in receiving necessary components. Supply chain challenges can lead to production stoppages and increased costs, affecting the competitiveness of foundries in the global market.
Table 7: Key Challenges in Light Alloy Foundries
Challenge | Impact on Foundry Operations | Example Consequences |
---|---|---|
High initial investment | Increased operational costs | Slow adoption of new technologies |
Skilled labor shortages | Reduced production efficiency | Delays in production, errors in casting |
Supply chain disruptions | Increased costs, delays | Delays in materials, higher production costs |
8. How Does Structural Aluminum Casting Benefit the Automotive and Aerospace Industries?
Structural aluminum casting has had a significant impact on the automotive and aerospace industries, helping both sectors reduce weight and increase performance. What’s the real story? The automotive industry, in particular, has embraced aluminum castings as part of its move toward lighter vehicles that consume less fuel and have improved overall efficiency. Aluminum is the material of choice for manufacturers looking to reduce the weight of engine components, transmission housings, and chassis.
Aluminum castings are also playing a major role in the aerospace sector. The material’s lightweight yet durable properties make it ideal for producing parts that need to withstand extreme conditions. In aircraft, structural aluminum castings are used for everything from wing spars to fuselage components. The lightweight nature of aluminum allows manufacturers to create fuel-efficient airplanes while maintaining the strength and performance needed for flight.
But here’s where it gets interesting: aluminum castings help manufacturers meet regulatory and safety standards. The stringent regulations imposed by the National Highway Traffic Safety Administration (NHTSA) and the Federal Aviation Administration (FAA) require manufacturers to produce components that are both lightweight and strong enough to ensure safety. Structural aluminum castings help meet these standards by providing the necessary balance between performance and durability.
Table 8: Benefits of Structural Aluminum in Automotive and Aerospace
Industry | Application | Benefit |
---|---|---|
Automotive | Engine blocks, chassis | Reduced weight, improved fuel efficiency |
Aerospace | Aircraft components (wings, fuselage) | Fuel efficiency, structural integrity |
9. How Do Technological Advancements in Casting Processes Contribute to Efficiency?
Technological advancements have played a critical role in improving the efficiency of aluminum casting processes. So, what’s the story here? Automation and robotics have revolutionized the way aluminum castings are produced. Automated systems allow for the rapid production of complex components with minimal human intervention. This not only increases the speed of production but also reduces the likelihood of human error, ensuring that each casting meets the necessary specifications.
What’s the real story? The integration of computer-aided design (CAD) and computer-aided manufacturing (CAM) systems has further enhanced precision and accuracy in aluminum casting. These systems allow for better control over mold design, material composition, and the casting process itself, leading to improved product quality and reduced waste. With CAD and CAM, foundries can make adjustments in real-time, reducing the need for costly rework and scrap materials.
Additive manufacturing, or 3D printing, has also made its mark on the aluminum casting process. By enabling the creation of complex mold designs and prototypes, 3D printing allows for faster product development and testing. This technology helps foundries reduce lead times and improve overall production efficiency.
Table 9: Technological Advancements in Aluminum Casting
Advancement | Impact on Casting Efficiency | Example Application |
---|---|---|
Automation and robotics | Faster production, reduced labor costs | High-volume casting production |
CAD and CAM systems | Improved precision, reduced errors | Mold design, process control |
3D printing | Faster prototyping, complex designs | Custom casting, rapid product testing |
10. What Are the Environmental Benefits of Using Structural Aluminum?
The use of structural aluminum in casting has significant environmental benefits that contribute to sustainability goals in manufacturing. What’s the real story? Aluminum is one of the most environmentally friendly metals used in manufacturing due to its recyclability. Unlike many other materials, aluminum can be recycled indefinitely without losing any of its properties. Recycling aluminum saves up to 95% of the energy required to produce new aluminum from raw materials, making it a highly sustainable option.
Moreover, the production of aluminum from recycled materials reduces the need for mining, which can have negative environmental impacts, such as habitat destruction and water pollution. This makes aluminum a more sustainable choice compared to other metals that rely heavily on raw material extraction.
Another key environmental benefit is the lower carbon footprint of aluminum production. Modern casting technologies have significantly reduced the energy required to produce aluminum, making the overall production process more efficient and less harmful to the environment.
Table 10: Environmental Benefits of Structural Aluminum
Benefit | Environmental Impact | Example Application |
---|---|---|
Recyclability | Reduces waste and energy consumption | Automotive parts, packaging |
Reduced carbon footprint | Less energy consumption, lower emissions | Aluminum production processes |
Reduced need for mining | Minimizes environmental damage | Mining, raw material extraction |
11. How Can Foundries Keep Up with Industry Demand and Technological Changes?
The constant evolution of technology and increasing market demands present both opportunities and challenges for light alloy foundries. But here’s where it gets interesting: foundries must evolve alongside these changes to stay competitive and meet the needs of industries that require high-quality, precision-engineered components. So, how can they keep up?
One of the most important strategies is the continuous investment in technology. As automation and digitalization take center stage, adopting Industry 4.0 solutions has become essential. For example, foundries are integrating smart sensors, data analytics, and predictive maintenance systems into their operations. This allows them to identify potential issues before they cause disruptions, leading to increased uptime and production efficiency. Furthermore, the real-time monitoring of processes enhances the ability to maintain consistent quality, reducing scrap rates and ensuring customer satisfaction.
Another strategy is to optimize workforce development. The shortage of skilled labor in the foundry industry is an ongoing challenge. By investing in employee training and development, foundries can ensure that their workforce is equipped with the necessary skills to operate new technologies effectively. Cross-training employees in different aspects of the foundry process can also increase flexibility and reduce the impact of labor shortages.
But here’s the kicker: collaboration is also a key factor in staying ahead of industry trends. Foundries that work closely with suppliers, technology providers, and even customers are able to stay informed about new materials, casting techniques, and design specifications. This collaboration enables foundries to adopt innovations more quickly and deliver the high-performance products that their customers expect.
Table 11: Strategies for Keeping Up with Industry Demand
Strategy | Impact on Foundry Operations | Example Application |
---|---|---|
Technology investment | Enhanced production efficiency, better quality control | Automation, smart sensors, predictive maintenance |
Workforce development | Improved skillsets, increased flexibility | Employee training, cross-training programs |
Collaboration with suppliers | Faster adoption of innovations, better customer alignment | Material sourcing, casting design feedback |
12. What Are the Economic Impacts of the Growth in Light Alloy Foundries?
The growth of light alloy foundries has significant economic implications, not just for the foundries themselves but also for the broader manufacturing sector. What’s the real story? The expansion of the aluminum casting industry creates jobs, stimulates technological innovation, and strengthens global supply chains.
For instance, as foundries increase their production capabilities to meet rising demand, they are contributing to the creation of new jobs across multiple sectors. The demand for skilled workers in areas like casting design, machining, and quality control is on the rise, and this is positively impacting local economies. Additionally, suppliers of materials, equipment, and technology also benefit as foundries increase their purchasing power.
But here’s the kicker: economic growth doesn’t just come from within the foundry itself. The light alloy foundry industry plays an essential role in supporting industries that rely heavily on high-quality, lightweight materials. For example, as the automotive and aerospace industries grow, they create more demand for aluminum castings, which, in turn, leads to increased revenue for foundries. This ripple effect helps sustain economic activity not just in manufacturing but in related sectors as well.
Another important factor is the contribution to global supply chains. Aluminum foundries play a critical role in ensuring the timely delivery of key components to manufacturers worldwide. By maintaining high standards of quality and efficiency, light alloy foundries ensure that the entire supply chain remains intact, reducing delays and ensuring that manufacturers meet their production deadlines.
Table 12: Economic Impact of Growth in Light Alloy Foundries
Economic Impact | Effect on Local and Global Economies | Example Sector |
---|---|---|
Job creation | Increase in employment opportunities | Casting design, machining |
Revenue growth | Boost in foundry and supplier income | Aluminum suppliers, equipment providers |
Strengthened supply chains | Increased stability and efficiency | Automotive, aerospace, renewable energy |
13. How Does the Light Alloy Foundry System Contribute to Global Supply Chains?
The light alloy foundry system is a crucial link in the global supply chain, providing the materials and components needed for a wide range of industries. So, what’s the real story? The demand for lightweight, durable materials like aluminum continues to grow in industries such as automotive, aerospace, and construction. Foundries that produce high-quality aluminum castings are essential in meeting this demand and ensuring that production schedules are met across the globe.
One key contribution of light alloy foundries is the timely delivery of components. Because industries such as automotive and aerospace rely on cast parts for vehicle frames, engine components, and aircraft structures, any delay in the supply of these parts can lead to production halts and supply chain disruptions. Light alloy foundries are critical to avoiding such disruptions by maintaining high production rates and quick turnaround times.
But here’s where it gets interesting: light alloy foundries also contribute to supply chain resilience. By using flexible manufacturing processes and maintaining relationships with multiple suppliers, foundries can adapt quickly to fluctuations in demand, material availability, and market conditions. This flexibility ensures that global supply chains remain strong, even during times of economic uncertainty or material shortages.
Moreover, foundries that invest in sustainable practices and ethical sourcing play a key role in promoting responsible supply chains. With increasing pressure from both consumers and governments to adopt more sustainable practices, foundries that prioritize recycling and reduce their carbon footprint contribute to a more eco-friendly global supply chain.
Table 13: Contributions of Light Alloy Foundries to Global Supply Chains
Contribution | Impact on Global Supply Chains | Example Industry |
---|---|---|
Timely delivery of components | Reduces production delays and disruptions | Automotive, aerospace |
Supply chain resilience | Enhances ability to adapt to market fluctuations | Manufacturing, renewable energy |
Sustainable and ethical practices | Promotes responsible sourcing, reduces environmental impact | Automotive, construction |
14. What Innovations Are Shaping the Future of Aluminum Casting?
The aluminum casting industry is undergoing a wave of innovations that are pushing the boundaries of what’s possible. What’s the real story? From automation and robotics to additive manufacturing, new technologies are reshaping the future of casting and making it more efficient, sustainable, and precise than ever before.
One of the most exciting developments is the integration of 3D printing into the casting process. 3D printing allows foundries to create complex molds and patterns quickly, without the need for traditional tooling. This not only reduces lead times but also enables the production of highly customized parts for niche markets. The ability to create intricate, one-of-a-kind components is a game-changer for industries like aerospace, where precision and customization are critical.
Another breakthrough technology is artificial intelligence (AI). AI is being used to optimize casting processes by predicting defects, improving material flow, and monitoring quality control. With AI, foundries can detect anomalies in the casting process in real-time, leading to fewer defects and higher-quality products. By integrating AI with machine learning, foundries can also improve operational efficiency and reduce downtime, making them more competitive in a fast-paced market.
But here’s the kicker: sustainability innovations are also playing a key role in shaping the future of aluminum casting. From energy-efficient furnaces to the use of recycled materials, these innovations are helping reduce the environmental footprint of aluminum production. As the global demand for sustainable manufacturing practices continues to rise, aluminum foundries that prioritize eco-friendly technologies will have a significant competitive advantage.
Table 14: Innovations Shaping the Future of Aluminum Casting
Innovation | Impact on Aluminum Casting Industry | Example Application |
---|---|---|
3D printing | Faster production, more complex designs | Custom parts, low-volume production |
Artificial intelligence (AI) | Improved efficiency, reduced defects | Quality control, predictive maintenance |
Sustainability innovations | Reduced environmental impact, energy savings | Recycling, energy-efficient furnaces |
15. What Are the Long-Term Prospects for Structural Aluminum in Light Alloy Foundries?
The long-term prospects for structural aluminum in light alloy foundries are incredibly positive, thanks to the material’s unique properties and increasing demand across various industries. So, what’s the real story? As global industries continue to prioritize lightweight, durable, and cost-effective materials, the demand for structural aluminum is expected to rise steadily.
One of the most promising trends is the growing use of aluminum in electric vehicles (EVs). As the automotive industry shifts towards EVs, the need for lightweight materials to offset battery weight is becoming more important. Structural aluminum castings offer the perfect solution, enabling automakers to reduce vehicle weight while maintaining safety and performance standards. This trend is expected to drive significant growth in the aluminum casting market over the next few decades.
In addition, sustainable construction practices are likely to increase the demand for aluminum castings in the building industry. Aluminum’s strength, corrosion resistance, and recyclability make it an ideal choice for constructing energy-efficient buildings, bridges, and infrastructure. As the world moves towards greener construction practices, the role of structural aluminum in these projects will continue to grow.
But here’s where it gets interesting: as global supply chains continue to evolve, foundries that can adapt to changing market conditions, meet new regulatory requirements, and incorporate emerging technologies will thrive. The future of structural aluminum in light alloy foundries looks promising, with continued demand, technological innovation, and sustainability at the forefront.
Table 15: Long-Term Prospects for Structural Aluminum in Light Alloy Foundries
Trend | Long-Term Impact on Foundry Market | Example Application |
---|---|---|
Electric vehicle adoption | Increased demand for lightweight materials | EV chassis, battery casings |
Sustainable construction | Growth in demand for eco-friendly materials | Energy-efficient buildings, infrastructure |
Technological advancements | Improved efficiency, precision, and sustainability | Advanced casting techniques, smart foundries |
Conclusion
Structural aluminum castings are playing an increasingly important role in the growth of light alloy foundry systems. With key drivers such as technological advancements, environmental sustainability, and the rising demand for lightweight materials, the aluminum casting industry is poised for continued growth. The automotive, aerospace, and renewable energy sectors are among the industries benefiting from aluminum’s unique properties, and the adoption of green manufacturing practices is further accelerating the growth of light alloy foundries. As these trends continue, businesses in the foundry industry must adapt to stay competitive and capitalize on emerging opportunities.
FAQ Section
Q1: What are light alloy foundries?
Light alloy foundries specialize in casting components made from lightweight metals such as aluminum, magnesium, and titanium. These metals are used in industries like automotive, aerospace, and construction due to their strength-to-weight ratio and durability.
Q2: How do aluminum castings benefit industries like automotive and aerospace?
Aluminum castings help industries like automotive and aerospace reduce the weight of their components, which in turn enhances fuel efficiency, performance, and safety.
Q3: What is the impact of technological advancements on light alloy foundries?
Technological advancements like automation, data analytics, and 3D printing have improved efficiency, precision, and quality control in foundries, allowing them to meet the increasing demand for lightweight, high-performance components.
Q4: What are the main challenges faced by light alloy foundries?
Light alloy foundries face challenges such as high initial capital investment, skilled labor shortages, and the need to comply with environmental regulations while maintaining production efficiency.
Q5: How can light alloy foundries contribute to sustainability goals?
By using recyclable materials like aluminum, reducing energy consumption, and minimizing emissions, light alloy foundries can significantly contribute to sustainability in manufacturing processes.